Выбор оптимального резерва производственной мощности АРП
Nbsp; Проектирование авторемонтного предприятия
Задание на курсовую работу
Модель автомобиля ПАЗ-3205.
Годовая программа ремонта: Wгод=650; Кта1=2,0; Кта2=1,4; Кта3=1,8; Кта4=2,0.
Технологическая планировка участка восстановления основных и базовых деталей.
Аннотация
В данной курсовой работе рассмотрены вопросы проектирования авторемонтного предприятия.
Курсовая работа состоит из девяти разделов.
В первом разделе проводится расчёт трудоёмкости годовой программы проектируемого ремонтного предприятия.
Во втором разделе рассматриваются вопросы о наличии оптимального резерва производственной мощности.
В третьем разделе проводится расчёт трудоёмкости годовой программы по цехам и участкам предприятия.
В четверном разделе производится расчет числа рабочих по цехам и участкам.
В пятом разделе производится расчет площадей участков АРП.
В шестом разделе проводится расчёт числа единиц технологического оборудования для производственного корпуса по участкам.
В седьмом разделе производится планировка генерального плана АРП.
В восьмом разделе проводится проектирование участка восстановления.
В девятом разделе производится экономическое обоснование проекта и расчёт планируемых технико-экономических показателей предприятия.
Пояснительная записка курсовой рабоы содержит ___ листов, ___ таблиц, ___ рисунка.
Курсовая работа содержит два листа графической части:
|
|
Приложение А - Планировка участка восстановления,
Приложение Б - Планировка генерального плана АРП.
авторемонтный показатель экономический
Содержание
Введение
1. Расчет годового объема работ
2. Выбор оптимального резерва производственной мощности АРП
3. Распределение трудоёмкости по цехам и участкам
4. Расчет количества рабочих по цехам и участкам
5. Определение площадей участков АРП
6. Расчет числа единиц технологического оборудования для производственного корпуса по участкам
7. Планировка генерального плана АРП
8. Проектирование участка восстановления основных и базовых деталей
8.1 Определение трудоемкостей работ, выполняемых на участке по одному ремонтируемому объекту
8.2 Такт производства и количество рабочих на рабочих местах
8.3 Расчёт потребности в технологическом оборудовании по трудоёмкости объёктов ремонта
8.4 Назначение основного и вспомогательного оборудования
8.5 Определение площади участка по площади, занимаемой оборудованием
8.6 Планировка, расстановка, привязка оборудования
9. Экономическое обоснование проекта
Заключение
Список использованных источников
Введение
В процессе эксплуатации автомобиля его рабочие свойства постепенно ухудшаются из-за изнашивания деталей, а также коррозии и усталости материала, из которого они изготовлены. В автомобиле появляются отказы и неисправности, которые устраняют при техническом обслуживании и ремонте.
|
|
Исправным считают автомобиль, который соответствует всем требованиям нормативно-технической документации. Работоспособные автомобиль в отличие от исправного должен удовлетворять лишь тем требованиям, выполнение которых позволяет использовать его по назначению без угрозы безопасности движения.
Повреждением называют переход автомобиля в неисправное, но работоспособное состояние; переход его в неработоспособное состояние называют отказом.
Ремонт представляет собой комплекс операций по восстановлению исправности или работоспособности изделий и восстановлению ресурсов изделий и их составных частей.
Необходимость и целесообразность ремонта автомобилей обусловлены, прежде всего, неравнопрочностью их составных частей. Известно, что создать равнопрочный автомобиль, все детали которого изнашивались бы равномерно и имели бы одинаковый эксплуатационный срок службы, невозможно. Поэтому в процессе эксплуатации автомобили проходят на автотранспортных предприятиях периодическое ТО и при необходимости ТР, который осуществляется путём замены отдельных деталей и агрегатов. Это позволяет поддерживать автомобиль в технически исправном состоянии.
|
|
При длительной эксплуатации автомобили достигают такого состояния, когда их ремонт в условиях АТП становится технически невозможным и экономически нецелесообразным. В этом случае они направляются в централизованный текущий или капитальный ремонт на авторемонтное предприятие.
Капитальный ремонт должен обеспечивать исправность и полный (или близкий к полному) ресурс автомобиля или агрегата путём восстановления и замены любых сборочных единиц и деталей, включая базовые. Базовой называется деталь, с которой начинают сборку изделия, присоединяя к ней сборочные единицы и другие детали.
Основным источником экономической эффективности КР автомобилей является использование остаточного ресурса их деталей. Около 70…75 % деталей, поступивших в КР, могут быть использованы повторно без ремонта, либо после небольшого ремонтного воздействия.
Расчет годового объема работ
Годовой объем работ - суммарная трудоёмкость (станкоёмкость) выполнения годовой производственной программы. Годовые объемы работ предприятия (Тг) и производственных участков определяются по формуле
|
|
Тг = ∑ Ті Νі, (1)
где Тi - трудоемкость ремонта i-го изделия; Ni - годовая производственная программа ремонта i-х изделий.
Для авторемонтных предприятий разработаны значения удельных технико-экономических показателей для эталонных условий и коэффициенты корректирования, учитывающие производственные условия проектируемого предприятия.
Определение трудоемкости ремонтных работ выполняется по методике укрупненных показателей для эталонных условий и корректирующих коэффициентов ([1], стр.440). Трудоемкость ремонта автомобиля включает ремонт на базе готовых агрегатов и входящих в автомобиль агрегатов. Программа по товарным агрегатам определяется умножением программы по автомобилю на коэффициент агрегата Кта1, указанным в задании. Годовая трудоемкость определяется:
Тг = (Таг. а. + Тс. а. + Тпроч. а.) Wа + ∑Тт. а. i Wт. а. i, (2)
где, Таг. а - трудоемкость ремонта автомобилей на базе готовых агрега-
тов, чел. - ч;
Тс. а. - трудоемкость ремонта автомобиля, чел. - ч;
Тпроч. а. - трудоемкость агрегатов, входящих в состав автомобиля,
чел. - ч;
Тт. а. i - трудоемкость i-ого товарного агрегата автомобиля, чел. - ч;т. а. i - годовая программа по i-ому агрегату
Wт. а. i = Wа Кт. а. i, (3)
где, Кт. а. i - коэффициент по i-ому товарному агрегату.
Значение Таг. а определим по следующей формуле:
Таг. а = tэk1k2k3k4k5, (4)
где tэ - трудоемкость для эталонных условий, чел. - ч; k1 - коэффициент приведения, учитывающий годовую производственную программу АРП, в соответствии с заданной годовой программой и справочными данными [1, с.441] принимаем k1=1,06; k2 - коэффициент приведения, учитывающий типы, модели и модификации автомобилей или агрегатов, принимаем k2=0,8; k3 - коэффициент приведения, учитывающий количество ремонтируемых на предприятии моделей агрегатов (автомобилей), принимаем k3=1,0; k4 - коэффициент приведения, учитывающий соотношение в программе предприятия полнокомплектных автомобилей и комплектов агрегатов (только для предприятий, ремонтирующих полнокомплектные автомобили), принимаем k4=1,0; k5 - коэффициент приведения, учитывающий соотношение между трудоемкостями капитального ремонта агрегатов, входящих в силовой агрегат и комплект прочих агрегатов.
Значения коэффициентов приведения принимаем в соответствии с заданной годовой программой и справочными данными [1].
Подставим известные значения в формулу (4):
Таг. а = 650∙1,06∙0,8∙1∙1∙1= 551,2 чел. - ч.
Значение Тс. а. определим по следующей формуле:
Тс. а. = tэk1k2k3, (5)
где tэ - трудоемкость эталона, чел. - ч.
Принимаем tэ =32. Тогда:
Тс. а. =32∙1,06∙1∙1= 33,92, чел. - ч.
Трудоемкость агрегатов, входящих в состав автомобиля Тпроч. а определяется по формуле:
Тпроч. а. = Тс. а. (1 - ηi. а.) / ηс. а., (6)
где, ηi. а. - доля i-ого агрегата;
ηс. а. - доля силового агрегата. Принимаем значение ηс. а. =0,555, (табл.34,3 [1]). Тогда:
Тпроч. а. =33,92∙ (1-0,555) /0,555=27,2 чел. - ч.
Трудоемкость i-ого агрегата Тт. а. i определяется по формуле:
Тт. а. i = Тс. а. ∙ ηi. а. / ηс. а. (7)
Значения ηi. а. для переднего моста, КПП и заднего моста принимаем по табл.34,3 ([1]).
Тпм=33,92∙0,12/ 0,555=7,33 чел. - ч.
Ткпп=33,92∙0,1/ 0,555=6,11 чел. - ч.
Тзм=33,92∙0, 19/ 0,555=11,61 чел. - ч.
Годовую программу по i-ому агрегату Wт. а. i определим по формуле (3):
т. а.1=650∙2,0=1300т. а.2=650∙1,4=910т. а.3=650∙1,8=1170т. а.4=650∙2,0=1300
Вычислим значение годовой трудоемкости, подставив известные данные в формулу (2):
Тг = (551,2+33,92+27,2) ∙650+33,92∙1300 + 7,33∙910 + 6,11∙1170 + +11,61∙1300 =471016 чел. - ч.
Определим годовую трудоемкость двигателя:
Тг. дв. = Тс. а. ∙ (Wа + Wт. а.1) =33,92∙ (650+1300) =66144 чел. - ч. (8)
Годовая трудоемкость полнокомплектных автомобилей равна:
ТПА= Тг - Тг. дв=471016 - 66144=404872 чел. - ч. (9)
Выбор оптимального резерва производственной мощности АРП
Ремонтный фонд для АРП поступает неравномерно, это приводит к образованию очереди и увеличения времени ожидания ремонта.
Потери от простоев автомобилей можно значительно уменьшить, создавая резерв производственной мощности.
Дата добавления: 2018-09-22; просмотров: 431; Мы поможем в написании вашей работы! |
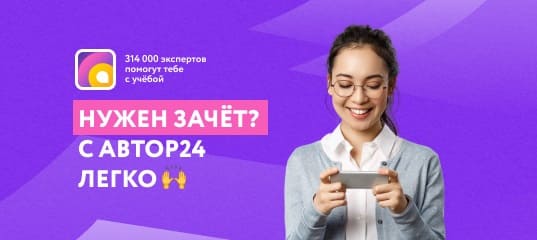
Мы поможем в написании ваших работ!