РАСЧЕТ КАЧЕСТВЕННО-КОЛИЧЕСТВЕННОЙ СХЕМЫ ПОДГОТОВИТЕЛЬНЫХ ОПЕРАЦИЙ
Курсовой проект
По дисциплине: «Основы обогащения полезных ископаемых»
Тема курсового проекта:Рассчитать качественно-количественные показатели подготовительных и основных операций обогащения железной руды
Выполнила: ст. гр ОПИ-10
Сватовская Дарья
Проверила: Николаева Т.С.
Москва 2011 г.
Содержание курсового проекта:
1.Задание на курсовую работу.
2.Введение.
3.Расчет качественно-количественной схемы подготовительных операций дробления, грохочения железной руды (выбор и обоснование схемы, расчет выхода продуктов).
4.Расчет качественно-количественных показателей по двум предлагаемым варрантам технологии обогащения:
- выход коллективного, магнетитового и гематитового концентратов, а также хвостов обогащения;
- содержание компонентов (общее и по отдельным минералам) в продуктах обогащения;
- извлечение компонентов в продукты обогащения;
- степень сокращения и концентрации;
- технологическая эффективность процессов обогащения (точная и приближенная).
5. Вывод.
6. Список использованной литературы.
7.Графическое представление предлагаемых технологических схем рудоподготовки и обогащения железной руды.
|
|
Исходные данные:
1. Железосодержащая руда добывается открытым способом.
2. Производительность фабрики 25 тысяч тонн в сутки.
3. Характеристику крупности исходной руды, поступающей на грохочение, можно принять прямолинейной.
4. Циркулирующая нагрузка в замкнутом цикле операции дробления
с = 110%
5. Содержание железа в руде:
Магнетитового αм = 28%
Гематитового, αг = 7%
породообразующий минерал – кварц
6. Содержание железа в концентрате:
Магнитного обогащения βм = 66%
Гравитационного обогащения βг = 68%
Флотационного обогащения βф = 64%
7. Извлечение магнетитового железа при магнитном обогащении
εм = 90%
8. Извлечение гематитового железа при гравитационном обогащении εг = 85%
9. Извлечение железа магнетитового и гематитового при флотации
εф = 87%.
Задание курсового проекта:
1. Расчет качественно-количественной схемы дробления – грохочения (выбор схемы, определение крупности продуктов, расчет выхода продуктов).
2. Расчет качественно-количественных показателей обогащения (выход коллективного, магнитного и гематитового концентратов, а также хвостов обогащения; содержание компонентов (общее и по отдельным минералам) в продуктах обогащения; извлечение компонентов в продукты обогащения; степени сокращения и концентрации; технологическая эффективность процессов обогащения).
|
|
Введение.
Обогащением полезных ископаемых называется процесс
первичной обработки сырья с целью разделения минерала,
отделение вредных примесей и получение кондиционного продукта-
концентрата, с повышенным содержанием ценного компонента
(достаточным для последующей эффективной переработки).
Обогащению подвергаются все руды цветных и редких металлов,
Руды черных металлов обогащаются около 90%,все коксующиеся
угли, энергетические угли- около 50%.
Задачи обогащения:
Повышение качества полезного ископаемого.
Удаление вредных примесей.
Достижение однородности сырья по крупности и вещественного состава.
Только при обогащении возможно комплексное использование вещества.
Все процессы на обогатительной фабрике можно разделить на три группа:
Подготовительная: грохочение, дробление, измельчение, классификации по крупности, усреднение.
|
|
Основная (собственно обогащение ):гравитационный метод обогащения, флотация, магнитный метод обогащения, электрический и специальные методы обогащения.
Вспомогательные: обезвоживание, пылеулавливание, обеспыливание, транспортирование, складирование, очистка сточных и кондиционирование оборотных вод.
Схема рудоподготовки, включающая операции дробления, грохочения
и измельчения, намечается исходя из свойств руды на основе результатов исследований обогатимости, технологических характеристик оборудования, которое возможно применить, и опыта переработки аналогичных по свойствам и составу руд. Крупность материала подаваемого на фабрику, определяется проектом горной части, крупности материала, поступающего в первый прием обогащения, и сам способ обогащения устанавливаются в зависимости от испытаний на обогатимости. Физические свойства руды:
крепость, гранулометрический состав, влажность, содержание глины, дробимость, грохочения и измельчения и тип аппаратов для выполнения этих операций. На выбор схемы оказывают влияние и общие условия проектирования: климатические условия района, производительность предприятия, способ разработки месторождения, способов подачи
|
|
руды на фабрику и многие другие, например, при глинистой, влажной руде, липкой и нетранспортабельной, возможно, потребуется промывка руды, а иногда, по условиям смерзаемости и подсушка руды. Иногда требуются выделение мелочи и отдельное складирование кусковой руды. Для проектировщика оченьважно знать данные эксплуатации обогатительных фабрик, работающих на рудах, подобных исследуемым.
Применение в проекте проверенных решений позволит избежать ошибок, которые трудно исправить на построенной фабрике, а перестройка некоторых технологических узлов потребует больших затрат и вызывает потерю времени на освоение производственной мощности предприятия.
Операции дробления применяются для подготовки полезного ископаемого к измельчению в мельницах или подготовки его непосредственно к операциям обогащения, в случае, если руда с крупной вкрапленностью полезного минералов. На дробильно-сортировочных фабриках операции дробления имеют самостоятельное значение.
В схемы дробления обычно включают операции предварительного и поверочного грохочения. Их принято относить к той операции дробления, в которую поступает верхний продукт грохота.
Операция дробления вместе с относящимися к ней операциями грохочения составляет стадию дробления, а совокупность стадий дробления – схему дробления.
РАСЧЕТ КАЧЕСТВЕННО-КОЛИЧЕСТВЕННОЙ СХЕМЫ ПОДГОТОВИТЕЛЬНЫХ ОПЕРАЦИЙ
ДРОБЛЕНИЯ И ГРОХОЧЕНИЯ РУДЫ)
Выбор схемы
При выборе схемынеобходимо решить вопрос о числе стадий дробления и необходимости операций предварительного и контрольногогрохочения.
Число стадий определяется крупностью исходного и конечного продуктов дробления. Начальная крупность, т.е. максимальный размер кусков руды, поступающей из рудника на обогатительную фабрику Dmax, определяется в зависимости от производительности горного цеха и принятой на нем системы горных работ (табл. 3).
Таблица 3
«Зависимость максимального размера кусков руды от характера горных работ»
Производительность горного цеха, т/сут | Максимальный размер кусков руды Dmax, мм | |
Открытые работы | Подземные работы | |
Малая, до 300 | 350-500 | 250 |
Средняя, 300-6000 | 700-1000 | 400 |
Большая, 6000-15000 | 900-1200 | 600-700 |
Очень большая, >15000 | 1200-1300 | - |
Крупность конечного дробленого продуктаdmax, получаемого в цехе дробления – грохочения и поступающего в цех измельчения – классификации, зависит в основном oт производительности обогатительной фабрики. Ввиду того, что операция измельчения является наиболее дорогой в технологической схеме, необходимо получить возможно более мелкий дробленый продукт, стараясь при этом излишне не усложнять схему дробления. По указанным причинам экономически выгодно получать мелкий дробленый продукт лишь при высокой производительности предприятия. При выборе оптимальной крупности дробленого продукта можно руководствоваться данными табл. 4.
Таблица 4
«Зависимость оптимального размера кусков руда в питании мельниц от производительности фабрики»
Производительность фабрики, т/сут | < 500 | < 2500 | < 10000 | < 40000 |
Оптимальная крупность питания мельниц, мм | 10 – 15 | 6 – 12 | 5 – 10 | 4 – 8 |
Общая степень дробления составит
Sобщ = Dmax / dmax =
Общая степень дробления всей схемы равна произведению степеней дробления в отдельных стадиях, т. е.
Sобщ = S1*S2*…*Sn = 5*6*8 = 240
Оптимальные значения степени дробления для дробилок различного типа при дроблении в одну стадию следующие:
- конусные крупного дробления (ККД) – до 5;
- щековые со сложным качанием щеки (ЩДС) – до 8;
- щековые с простым качанием щеки (ЩДП) – до 5;
- конусные среднего дробления (КСД) без контрольного грохочения – до 6;
- конусные в замкнутом цикле с контрольным грохочением – до 8 – 10;
- конусные мелкого дробления (КМД);
- без контрольного грохочения – до 3 – 5;
- в замкнутом цикле с контрольным грохочением – до 8.
Практика проектирования и эксплуатации Обогатительных Фабрик, а также учет технических возможностей современного дробильного оборудования показывают, что одностадиальная схема неосуществима. Наиболее часто принимают двух – трехстадиальные схемы. При этом каждой операции дробления может предшествовать предварительное грохочение. Операции предварительного грохочения применяются для сокращения количества материала, поступающего в дробление и увеличения подвижности материала в рабочей зоне дробилки. Последнее особенно необходимо при дроблении в конусных дробилках среднего в мелкого дробления, склонных к забиваниюих рабочей зоны рудной мелочью.
Решение вопроса о необходимости предварительного грохочения осуществляется по данным ситовой характеристики дробимого материала. Предварительное грохочение применяется, когда выход отсеиваемого класса крупности, т. е. продукта, соответствующего по крупности размеру разгрузочного отверстия дробилки, составляет не менее 20 – 28 %.
Максимальная крупность материала, поступающего на обогатительную фабрику, 900 мм, следовательно, необходимо применить крупное дробление (S1=5).Условная максимальная крупность продуктов дробления равна D1 = Dmax / S1, D1 = 180 мм. Перед этой операцией надо решить вопрос о применении предварительного грохочения. Составим прямолинейную, суммарную характеристику крупности материала по минусу для первой стадии.
Из диаграммы 1 видно, что при D1 = 180 мм, выход отсеваемого
класса крупности составляет 20%. Целесообразно применить перед
первой стадией дробления предварительное грохочение.
Максимальная крупность материала, поступающего на вторую стадию
дробления, будет равна 180 мм. Условная максимальная крупность продуктов дробления второй стадии D2 = D1/ S2, где S2 = 6. Составляем прямолинейную суммарную характеристику крупности материала по минусу для второй стадии.
Из диаграммы 2 следует, что при D2 = 30 мм, выход отсеваемого класса крупности равен 16 %. Следовательно, грохочение для второй стадии применять не нужно.
Операция контрольного грохочения применяется только в последней (третьей) стадии дробления, так как введение в схему дробления контрольного грохочение вызывает необходимости установки большого числа грохотов, конвейеров и питателей, что приводит к увеличению капитальных затрат и усложняет эксплуатацию цеха дробления. Максимальная крупность материала, поступающего на третью стадию дробления, будет равна D3 = D2 / S3 ; где S3 = 8; D3 = 4 мм. Эта крупность будет соответствовать крупности конечного дробленого продукта. Составляем прямолинейную суммарную характеристику крупности материала по минусу для третьей стадии.
Ширина разгрузочного отверстий для каждой стадии определяется выражением in = D/Zn , in – ширина разгрузочного отверстия дробилки на n – ой стадии. Zn – отношение размера максимального куска дробленной руды , к ширине разгрузочного отверстия. Величина Zn определяется по типовым характеристикам дробленой руды.
Для замкнутого цикла величину Z принимают равно 1,25.
i1 = 180/1, 25 = 144 мм. i2 = 180/6 / 1, 25 = 20 мм. i3 = 30/8/1, 25 = 3 мм.
Размеры отверстий грохотов назначаются в пределах между размером разгрузочного отверстия дробилки (для предварительного расчета можно принять размеры отверстий грохотов равным размером максимальных кусков дробленой руды).
1.2. Расчет выхода продуктов.
Расчет качественно-количественной схемы заключается в определении выхода продуктов по выбранной схеме.
В первой стадии обычно устанавливают неподвижные колосниковые грохоты, эффективность (Е) которых принимают равной 0,6 – 0,7. Количество подрешетного продукта, образующегося при грохочении по крупности D, равно
Qn = Q* α *E, т/ч,
где Q – количество руды, поступающей на грохочение, т/ч;
α – содержание в руде класса крупности –d, доли единицы;
Е – эффективность грохочения, доли единиц.
Величинаα определяется графическим методом по суммарной гранулометрической характеристике.
Рассчитаем количество подрешетного продукта, образующего при предварительном грохочении по крупности D1 = 180 мм.
Содержание в руде класса крупности D1 находим из диаграммы 1 (a = 20%). Скорость подачи питания на грохот рассчитаем исходя из производительности обогатительной фабрики: 1000 т/сут = 416,7 т/ч.
Q1 n = 416,7 * 0,2 * 0,7 = 58,3 т/ч
Рассчитаем выход подрешетного продукта, который определяется выражением:
γ п1 = 58,3/ 416,7 * 100% = 14%
Количество руды ( Qn ) и выходпродукта поступающего в операции дробления составляют соответственно:
Qдр = Q – Qп, т/ч;
γ п = 100 - γ п %
Для первой стадии Q1 n и γ п1 будут равны:
Q1 n = 416,7 – 58,3 = 358,4 т/ч;
γ п1 = 100 – 14 = 86%.
Рассчитаем эти же показатели для третьей стадии. В третьей стадии устанавливают грохоты с подвижной поверхностью с эффектностью 0,8 – 0,85. Количество и выход продуктов в последней стадии дробления в замкнутом цикле определяется с учетом циркулирующей нагрузки. Величину а находим из диаргаммы 3 (а = 12%).
Для третьей стадии будут равны:
Q3 n = 416,7 * 0,12*0,8 = 40т/ч;
γ п3 = 40/416,7 * 100% = 9,6%;
Q3 n = 416,7 -40= 376,7 т/ч;
γ п3 = 100 – 9,6 = 90,4%;
Нагрузка на грохоты в третьей определяется выражением:
Qс = Q + Qn * С = 100+110=210%
где С – циркулирующаянагрузка в замкнутом цикле операции дробления.
γ = γ n+ γ nC = 100 + 90,4 * 1,4 = 226,56
Qс = 416,7 + 376,7 * 1,4 = 944,08
Дата добавления: 2018-09-22; просмотров: 369; Мы поможем в написании вашей работы! |
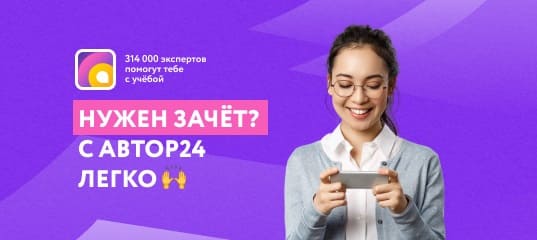
Мы поможем в написании ваших работ!