Применяемых при производстве силикатного кирпича и камней
Искусственные материалы и изделия на основе минеральных вяжущих.
Строительные материалы и изделия на основе минеральных вяжущих веществ называют безобжиговыми, так как в процессе производства их не обжигают. Необходимую прочность они приобретают в результате затвердевания вяжущего вещества.
Материалы на основе минеральных вяжущих веществ включают в себя материалы на основе:
гипса (гипсокартон, гипсовые декоративные украшения и др.);
извести (кирпич и камни силикатные, ячеистые бетоны);
материалы на основе цемента (листы асбестоцементные (шифер), трубы асбоцементные, цементно-песчаные изделия (блоки стеновые и фундаментные, облицовочные, плиты перекрытий, тротуарная плитка и др.).
Изделия из гипса и гипсобетона
Изделия на основе гипса получают как из гипсового теста (т. е. из смеси гипса и воды), так и из смеси гипса, воды и заполнителей.В первом случае изделия называют гипсовыми, во втором - гипсобетонными.
В качестве заполнителей при изготовлении гипсобетонных изделий используют кварцевый песок, пористые заполнители (керамзит, шлаковую пемзу), опилки, стружки, льняную костру, макулатуру и т. п. Для уменьшения плотности к гипсовым смесям добавляют вспенивающие вещества.
Гипсовые и гипсобетонные изделия применяют в основном для внутренних частей зданий, не несущих больших нагрузок. Изделия из гипса могут быть сплошными и пустотелыми, армированными и неармированными. Имеют невысокую плотность (1100... ...1400 кг/м3), несгораемы, хорошо изолируют от шума, поддаются механической обработке и легко пробиваются гвоздями.
|
|
У гипсовых изделий есть и существенные недостатки: низкая водостойкость, гигроскопичность, хрупкость и малая прочность при изгибе.Изделия из гипса нельзя применять в помещениях с влажностью воздуха более 60 %.
Из гипсобетонов изготовляют различные строительные изделия - от мелких камней до крупных панелей. Мелкие стеновые камни выпускают из чистого гипса плотной или ячеистой структуры и из легких гипсовых бетонов. Широко применяются камни с тремя рядами щелевидных пустот по ширине, расположенных в шахматном порядке. Гипсовые камни выпускают размерами 250x120x140 мм, 390x190x140 мм и др. Средняя плотность гипсобетонных пустотелых камней - 1000... 1350 кг/м3, влажность - не более 8 %, морозостойкость - не менее 10... 15 циклов.
Гипсобетонные панели выпускают размером на комнату (высотой - до 3 м, длиной - до 6 м, толщиной - 60... 100 мм), сплошными и с проемами для дверей и фрамуг. Панели, предназначенные для помещений с влажностью не более 60 %, изготовляют из бетона на строительном гипсе прочностью при сжатии не менее 3,5 МПа, для санузлов и вентиляционных коммуникаций - на ГЦПВ прочностью 7 МПа и более.
|
|
Получают гипсобетонные панели методами непрерывного проката или вертикального формования в кассетах.
Плиты для перегородок могут быть гипсовыми, гипсобетонными и гипсоволокнистыми. Большей частью плиты имеют паз и гребень, что облегчает монтаж перегородок. Технология их изготовления состоит из следующих операций: дозирования компонентов, перемешивания смеси, формования плит и высушивания.
Для отделочных работ и устройства перегородок в помещениях с влажностью не более 60 % применяют гипсокартонные листы (сухую штукатурку). Они состоят из затвердевшего гипсового сердечника, прочно соединенного с картонной оболочкой. Технологический процесс производства гипсокартонных листов включает приготовление формовочной массы, подготовку картона, формование непрерывной ленты штукатурки, разрезание ее на отдельные листы после схватывания гипса и сушку в многоярусных туннельных сушилках. Гипсоволокнистые плиты без оболочки размерами 1000x1200x10 (12) мм используют для устройства полов (вместо стяжки).
Материалы и изделия автоклавного твердения на основе извести и кремнеземистого компонента
|
|
Силикатные материалы и изделия автоклавного твердения представляют собой искусственные строительные конгломераты на основе известково-кремнеземистого (силикатного) камня, синтезируемого в процессе автоклавной обработки под действием пара при высокой температуре и повышенном давлении.
К числу автоклавных силикатных изделий относят силикатный кирпич, крупные силикатные блоки, плиты из тяжелого силикатного бетона, панели перекрытий и стеновые, колонны, балки и пр. Легкие заполнители позволяют понизить массу стеновых панелей и других элементов. Силикатные изделия выпускают полнотелыми или облегченными со сквозными или полузамкнутыми пустотами. Особое значение имеют силикатные ячеистые бетоны, заполненные равномерно распределенными воздушными ячейками, или пузырьками. Они могут иметь конструктивное и теплоизоляционное назначение, что обусловливает форму и размеры изделий, их качественные показатели.
Также к изделиямавтоклавного твердения на основе извести и кремнеземистого компонента можно отнести ячеистые бетоны с применением извести в качестве вяжущего.
Из ячеистого бетона изготавливают следующую продукцию:
ü Плиты перекрытия, плиты покрытия;
|
|
ü Блоки крупноразмерные армированные и неармированные;
ü Блоки стеновые мелкие;
ü Мелкие теплоизоляционные изделия;
ü Звукопоглощающие изделия;
ü Межкомнатные перегородки;
ü Стеновые панели;
ü Перемычки лотковые и брусковые;
ü Теплоизоляционную засыпку.
Кирпич и камни силикатные
Сырье.
Перечень материалов,
применяемых при производстве силикатного кирпича и камней
Наименование материалов | Нормативный документ |
1 Песок для производства силикатных изделий | По действующим нормативным документам |
2 Известь строительная | ГОСТ 9179-79 |
3 Белитовый (нефелиновый) шлам | По действующим нормативным документам |
4 Золы уноса тепловых электростанций | ГОСТ 23818-91 |
5 Смеси золошлаковые | ГОСТ 25592-91 |
6 Щебень и песок шлаковые | ГОСТ 3344-63 ГОСТ 26644-85 |
7 Щебень и песок из шлаков | ГОСТ 3344-63 ГОСТ 26644-85 |
8 Щелочеустойчивые пигменты | ГОСТ 2912-79 ГОСТ 8135-74 |
9 Известесодержащие вяжущие | По действующим нормативным документам |
10 Краска сухая поливинилбутирольная, П-ВЛ, П-ВЛ-212, редоксайд, фталоциониновый зеленый, паропроницаемые эмали, эмали кремний органические КО-174 разных цветов, органосиликатные композиции и др. | По действующим нормативным документам |
Производство.Изготавливается способом прессования увлажненной смеси из кремнеземистых материалов и извести или других известесодержащих вяжущих с применением пигментов и без них с последующим твердением под действием насыщенного пара в автоклаве.
Для современного производства силикатного кирпича используют сырьевую смесь, в состав которой входит 90…95% песка, 5…10% молотой негашеной извести и некоторое количество воды.
Общая технология получения силикатных материалов
Технология получения силикатных изделий обычно складывается из следующих этапов:
1. Получение сырьевой смеси.
2. Прессование изделий.
3. Обработка в автоклаве изделий.
4. Выдержка готовых изделий.
В данном производстве большой объем работ составляет процесс получения извести для сырьевой смеси. В технологический процесс производства извести входят следующие операции: добыча известкового камня в карьерах, дробление и сортировка его по фракциям, обжиг в шахтных вращающихся и других печах, дробление или помол комовой извести (получение негашеной извести).
Начинается все с подготовки, обработки и дозировки сырья, которое необходимо для производства силикатного кирпича. Песок, который используют для производства силикатного кирпича, тоже должен быть соответствующего качества, т.е. примеси не должны превышать необходимый предел.
В песок добавляют необходимый объем извести и воды. Вода необходима для окончательного завершения химического процесса и формирования пластичной силикатной смеси.
Для производства силикатных кирпичей используют два способа: силосный и барабанный. Они различаются способом приготовления известково-песчаной смеси.
Наиболее экономически выгоден силосный способ. Его технология производства гораздо проще и не требует больших затрат.
Подготовленные составляющие ингредиенты перемешивают и увлажняют. После чего полученную смесь направляют в герметичный резервуар – силос. Там, при непрерывно вращающемся резервуаре, происходит гашение извести. Этот процесс занимает от 4 до 8 часов.
Далее смесь подвергается дополнительному увлажнению и прессованию под большим давлением. Это позволяет получить кирпич высокого качества. Чем больше давление, тем плотность готового силикатного кирпича будет выше, меньше останется отверстий и пустот в структуре.
Полученный сырец, направляется для тепло-влажной обработки и твердения в автоклав.
Барабанный способ предполагает использование измельченной, тонкомолотой негашеной извести. Песок и известь подают в специальные бункера, а оттуда в необходимом количестве подаются в гасильный барабан. Там, в герметически закрытой емкости, происходит перемешивание ингредиентов и гашение извести. Этот процесс происходит под давлением и подаче пара при вращающемся барабане, и занимает около 40 минут.
Технология производства силикатного кирпича, в отличие от производства глиняного кирпича, имеет ряд преимуществ. Это и короткий цикл производства, более простое технологическое оборудование, высокая степень механизации и сравнительно небольшой расход топлива.
Автоклав представляет собой горизонтально расположенный стальной цилиндр с герметически закрывающимися с торцов крышками. В автоклаве в атмосфере насыщенного пара при давлении 0,8-1,3 МПа и температуре 175-200°С кирпич твердеет 8…14ч.
Прочность автоклавных материалов формируется в результате взаимодействия двух процессов: структурообразования, обусловленного синтезом гидросиликатов кальция, и деструкции, обусловленной внутренними напряжениями.
Для снижения внутренних напряжений автоклавную обработку проводят по определенному режиму, включающему постепенный подъем давления пара в течение 1,5-2 ч, изотермическую выдержку изделий в автоклаве при температуре 175-200°С и давлении 0,8-1,3 МПа в течение 4-8 ч и снижение давления пара в течение 2-4 ч. После автоклавной обработки продолжительностью 8-14 ч получают силикатные изделия.
Из автоклава выгружают почти готовые изделия, которые выдерживают 10…15дней для карбонизации непрореагировавшей извести с углекислым газом воздуха, в результате чего повышается водостойкость и прочность изделий. Температура обработки и общие энергозатраты при производстве силикатного кирпича существенно ниже, чем при производстве керамического, поэтому силикатный кирпич экономически эффективнее.
К числу автоклавных силикатных изделий относят силикатный кирпич, крупные силикатные блоки, плиты из тяжелого силикатного бетона, панели перекрытий и стеновые, колонны, балки и пр. Легкие заполнители позволяют понизить массу стеновых панелей и других элементов. Силикатные изделия выпускают полнотелыми или облегченными со сквозными или полузамкнутыми пустотами.
Область применения и технические требования. Кирпич и камни применяют для кладки каменных и армокаменных наружных и внутренних стен зданий и сооружений, а также для их облицовки из лицевых изделий.
Основные параметры и размеры.Кирпич и камни силикатные зготавливают в форме прямоугольного параллелепипеда с номинальными размерами, указанными в таблице 1.
Лицевые поверхности могут быть рифлеными, или иметь колотую фактуру.
Таблица 1В миллиметрах
Вид изделия | Длина | Ширина | Толщина |
Кирпич одинарный | 250 250 | 120 88 | 65 54 |
Кирпич утолщенный | 250 | 120 | 88 |
Камень | 250 | 120 | 138 |
Камень модульных размеров укрупненный | 252 | 248 | 88 |
Камень укрупненный | 252 252 | 248 248 | 138 188 |
Камень перегородочный | 512 250 | 120 248 | 188 188 |
Камень перемычечный | 250 250 | 248 120 | 138 88 |
Предельные отклонения от номинальных размеров и геометрической формы изделий не должны превышать, мм:
— по длине, толщине и ширине — ±2;
— по толщине для колотых изделий — ±10;
— по непараллельности граней — 2.
Одинарный и утолщенный кирпич изготавливают полнотелым и пустотелым, камни — только пустотелыми.
Технические характеристики
1)По прочности изделия изготавливают марок 75, 100, 125, 150, 175, 200, 250, 300.
2) По морозостойкости изделия изготавливают марок F15, F25, F35, F50. Морозостойкость лицевых изделий должна быть не менее F35.
3) Водопоглощение изделий должно быть не менее 6 %.
4) Масса утолщенного кирпича в высушенном состоянии не должна превышать 4,3 кг, камня — не более 21,0 кг. По согласованию с потребителем допускается выпускать утолщенный кирпич массой более 4,3 кг, а камней — массой более 21,0 кг.
5) Коэффициент теплопроводности силикатного кирпича полнотелого, равен 0,7. Пустотелого силикатного кирпича – 0,66 Вт/м*К.
Для сравнения: коэффициент теплопроводности газобетона – 0,11 – 0,30, клинкерного кирпича – 0,8 – 0,9, керамического кирпича полнотелого – 0,5 – 0,8 Вт/м*К.
Дата добавления: 2018-08-06; просмотров: 228; Мы поможем в написании вашей работы! |
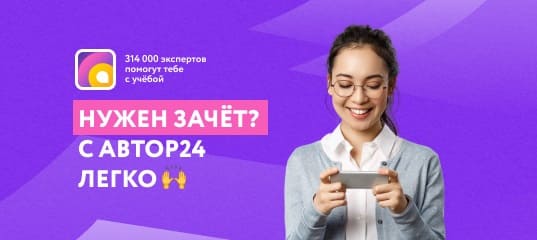
Мы поможем в написании ваших работ!