Силикоалюминий технологиясы (SiAl)
Металдардың жіктелуі Химиялық қослыстар мен физика-химиялық қасиеттерге тәуелді металдарды темір және темір емес деп топтарға бөлуге болады. Металдардың темір тобына әдетте табиғатта оксидтер түрінде кездесетін темір, марганец, хром, ванадий жатады. Темір емес тобына келесі металдарды жатқызамыз: мыс, қорғасын, мырыш, никель, қалайы, кобальт, кадмий, сурьма, висмут, сынап, алюминий, титан, магний, алтын, күміс, платина, цирконий, ниобий, тантал, молибден, вольфрам, литий, рубидий, цезий, бериллий, бұлар көбінесе табиғатта сульфидтер түрінде кездесді. Тотыққан қышқылды дайындау жұмыстары сульфидті кендерді даярлаудан айрықша ерекшеленеді. Мұнымен қоса, бастапқы шикізаттағы металл қосылыстарының концентрациясы да айтарлықтай мәнге ие. Темір емес топтағы металдар өз кезегінде төмендегіше жіктеледі: 1) ауыр (мыс, қорғасын, мырыш, қалайы, кобальт, кадмий, никель, сурьма, висмут, сынап); 2) жеңіл (алюминий, магний, титан); 3) асыл (алтын, күміс, платина); 4) сирек және радиоактивті (цирконий, ниобий, тантал, молибден, вольфрам, литий, рубидий, цезий, германий және т.б.). 2.Металдар мен қорытпаларды өндіруге арналған материалдар Шойын, болат және түсті металдар өндірісі үшін кен, флюстер, отын және отқа төзімді материалдарды қолданылады. Өнеркәсіптік кен – метал және оның қоспаларын (темір үшін металдың кендегі үлесі 30…60%-дан төмен болуы керек, мыс үшін 3..5%, молибден үшін 0,005…0,02%) тиімді бөліп алуға болатын, тау жынысы. Кен металл және оның қоспаларынан және бос жыныстан құралған минералдардан тұрады. Кенді бір немесе бірнеше металл аттарымен атайды, мысалы олардың құрамына темір және мыс-никельді кендер кіреді. Қазып алынатын элементтің құрамына байланысты бай және кедей кендер болып екіге бөлінеді. Кедей кендерді байытады – бос жыныстың бөлігін алып тастайды. Флюстер – балқыту пештеріне кеннің бос жыныстарынан жеңіл балқитын қоспаларды немесе дайын өнімді және отын күлділігін қалыптастыруға арналған материалдар. Әдетте, қож металға қарағанда төмен тығыздыққа ие, сондықтан, ол метал астында орналасады және балқыту үрдісі кезінде алынып тасталынады. Қож пеш газдарынан және ауадан металды қорғайды. Егер қождың құрамы қышқыл тотықтардан (SiO2, P2O5) тұрса, және оның құрамында негізгі тотықтар (CaO, MgO, FeO) көп болса, қышқыл деп аталады. Агломерат және шекемтас түрінде салынады. Отын – металлургия пештеріндегі кокс, табиғи газ, қара май, домналы (колошникті) газ. Коксты кокстелетін сұрыптағы тас көмірлерден (ауасыз) құрғақ айдаумен 1000○С температурада алады (2-сурет). Кокста 80…88% көміртек, 8…12% күлділік, 2…5% ылғалдылық болады. Кокстың түйіршіктері 25…60 мм өлшемінде болуы керек. Бұлар – берік балқымайтын отындар, тек қыздыру үшін жанғыш ретінде ғана емес, кеннен темірді өңдеп алу үшін химиялық реагент ретінде қызмет етеді. Отқа төзімді материалдарды металлургиялық пештердің ішкі қаптама бетін (футеровка) және еріген металдарға арналған шөміштерді дайындау үшін қолданады. Олар жоғары температурада жүктеулерге төтеп бере алады, қождың және пештік газдардың химиялық әсеріне, температурасының өзгеруіне қарсы тұра алады. Химиялық қасиеттеріне байланысты отқа төзімді материалдарды келесі топтарға бөледі: қышқыл (кварцті құм, династы кесек), негізгі (магнезитті кірпіш, магнезитті-хромитті кірпіш), нейтральды (шамотты кірпіш). Негізгі отқа төзімді материалдармен қышқыл қождардың әрекеті және керісінше, пештің бұзылуына әкелуі мүмкін. Көміртекті кірпіш және блоктар графит түріндегі көміртектің 92%-на және жоғары отқа төзімді қасиетке ие. Домна пешінің алюминий алуға арналған электролизді ванналарды, мыс құймаларын балқытуға және құюға арналған тигельдерді қалауға қолданылады. 3. Шойын өндірісі Шойын – темір және көміртектің сәйкес элементтермен (көміртектің мөлшері 2,14 %-дан жоғары) құймасы. Шойынды домна пешінде балқыту үшін темір кендерін, отын және флюстерді қолданады. Темір кендеріне жатады: - құрамында 55…60% темір бар магнитті темір (Fe3O4), кен орны – Соколовск, Курск магнитті аномалия (КМА); - құрамында 55…60% темір бар қызыл темір (Fe2O3), кен орны – Кривой Рог, КМА; - құрамында 37…55% темірі бар қоңыр темір (темір тотықтарының гидраттары 2Fe2O3 · 3H2O и Fe2O3 · H2O) – Керчь. Марганецті кендер темірдің марганецпен құймасын – ферромарганецті (10…82% Mn) балқытуға, сондай-ақ құрамында 1%-ға дейін марганец бар қайта өңдеуші шойынды балқыту үшін қолданады. Марганец кендерде тотық және карбонаттар түрінде болады: MnO2, Mn2O3, Mn3O4, MnCO3 және т.б. Хром кендері феррохром, металдық хром және отқа төзімді материалдар – хроммагнезиттер өндірісі үшін қолданылады. Домна өндірісіне отын ретінде кокс қолданылады, оны газбен, қара маймен аздап алмастыруға болады. Флюс ретінде әктас CaCO3 немесе CaCO3 мен MgCO3тұратын доломиттелген әктас алынады, себебі қожға негіздік оксидтер енуі керек, олар металдан күкіртті жою үшін керек. Домналық балқытуға кендерді дайындау домна пешінің өнімділігін жоғарылату, кокс шығынын азайту және шойын сапасын жоғарылату мақсатында жүргізіледі. Дайындау әдісі кеннің сапасына байланысты болады. Кендерді ірілігі бойынша сұрыптау және ұсақтау оңтайлы іріліктегі кендерді алу үшін жүргізіледі және ұсақтағыштар мен сұрыптағыштардың көмегімен жүргізіледі. Кендерді байыту минералдардың әртүрлі физикалық қаситеттеріне негізделген: а) жуу – бос борпылдақ жыныстан тығыз құрамдыларды бөліп алу; б) гравитация (шөктіру) – кенді бос жыныстардан су қабатын дірілді тесіктен өткізу арқылы бөлу: бос жыныс беткі қабатқа түседі де сумен бірге шығарылады, ал кен минералдары тұнады; в) магнитті сепарация – ұнтақталған кенді магнитпен әрекеттестіреді, темір құрамды минералдарды өзіне тартып, оларды бос жыныстардан алыстатады. Кесектеуді қажетті өлшемдегі кесекті материалдар алу үшін дайын өнімді қайта өңдеуде қолданады. Кесектеудің екі әдісі қолданылады: агломерация және жентектеу. Агломерация кезінде темір кенінен (40…50%), әктен (15…20%), ұсақ агломерат қайтымынан (20…30%), кокс ұнтағынан (4…6 %), ылғалдылықтан (6…9 %) тұратын шихтаны 1300…1500○С температурада агломерациялы машиналарда қайнатады. Қайнату кезінде кеннен зиянды қоспалар (күкірт, мышьяк) алынып тасталынады, карбонаттар ыдыратылып кесектелген кеуекті флюстелген агломерат түзіледі. Шекемтастау кезінде шихтаға ұнтақталған концентраттан, флюстен, отыннан тұратын шихтаны ылғалдандырады және айналмалы барабандарда өңдеу кезінде шар тәрізді формаға енеді – олар 30мм-ге дейінгі диаметрге ие шекемтастардан тұрады. Оларды кептіреді және 1200…1350○С температурада күйдіреді. Агломерат пен шекемтастарды қолдану іктас-флюсті жекелей қосуды қажет етпейді. 4. Жану үрдістеріне жалпы сипаттама Жану – бұл жылудың интенсивті бөлінуімен және түзілетін жану өнімдерінің температураларының тез жоғарлауымен бірге жүргізілетін, отын құрамдылардың қышқылсыздандырғышпен химиялық қосылу үрдісі. Ережеге сай, көптеген металлургиялық агрегаттарда жалынды жану қолданылады. Жалын - жану үрдісі жүретін қозғалмалы газдардың жарқырау көлемімен сипатталады. Нақты құрылымды және кескінді жалынды, әдетте, факел деп атайды. Жалын және факел гомогенді және гетерогенді болады. Гомогенді жалын бір ғана газды фазадан тұрады және газ түріндегі қышқылсыздандырғышта газ түріндегі отындарды жағу кезінде түзіледі. Алайда бұл жағдайда күрделі көп сатылы жану үрдісіне жалыны бар камера қабырғалары, немесе жану жүретін металлургиялық агрегаттың жұмысшы кеңістіктеріндегі өзге де қатты беттері қатысады. Гетерогенді (екі немесе көп фазалы) жалын шаң тәрізді қатты немесе шашыраңқы сұйық отынды жаққан кезде түзіледі. Бұл жағдайда, сондай-ақ, факел түзілуі мүмкін, бірақ өте қиын құрылымды болады. Қатты кесекті отынның жануы кезінде, әдетте, жалғыз факел түзілмейді, ол жалын жанып жатқан кесектердің маңында түзіледі және макроқұрылым осындай әрбір кесектің маңында байқалуы мүмкін. Қабатта жану, әдетте, отынның мөлшері артық болғанда жүруі мүмкін, сондықтан да қабаттың бөлімшелеріндегі қышқылсыздандырғышты жіберу орнынан алыс және жоғары жерлерде химиялық әрекеттесу үрдісі тек бос қана емес байланысқан оттекпенде аяқталады. Реакциялар бірінен соң бірі жүріп отырады: 1) С + О2 = СО2 (толық жану); 2) 2С + О2 = 2СО (толық емес жану) 3) 2СО + О2 = 2СО2 (СО жанғанға дейін);СО2 + С = 2СО (СО2 көміртегінің газификациясы). Металлургиялық агрегаттарда жану кезіндегі қабат немесе факелдің кескіні агрегаттың пішіні және кескінімен, қышқылсыздандырғыш үрлеуді беру әдісі және бағытымен байланысты. Жалынды шашыраңқы пештерде (мартенді, екі ванналы болат балқытқыш, қыздырғыш илемді) факел, оның ұзындығы ең негізгі өлшем ретінде анықталуы мүмкін, көлденең қимада түзіледі. Конвертерлерде ұшқын жалынды жоғары және әсіресе донды немесе кешенді үрлеу, тік және көп жағдайда тиемелі, яғни әрекеттесу бос газ фазасында емес, қож-металдық эмульсия (жоғары үрлеу) немесе сұйық метал (отын қосылыстарын қолдана отырып, донды немесе кешенді үрлеу) маңында жүреді. Домна пештерінде мойындықта отын (кокс) қабығы үрлеуді беру бағыты бойынша көлденең бойлыққа ие, ал пеш осіне факел біртіндеп жоғары бағытталады. Газ генераторларында газ түріндегі отынды (генераторлы газды) алу үшін отын қабаты (тас көмірдің) үрлеуді беру бағыты бойынша тік бойлықтың төмен жоғарысына бағытталады. Көп жағдайларда, металлургиялық агрегаттарға үрлеуді беру жылдамдығы жоғары мөлшерге дейін жетеді, мысалы, домна пешіне 150 – 200 м/с, ал конвертерлерде жоғары үрлеу 700 – 800 м/с-ке дейін. Соңғысында, ол дыбыстың жылдамдығын біршама жоғарылатады. Металлургиялық агрегаттарда отынның жануы үшін газ түріндегі реагенттердің конвективті масса тасымалдау, соның ішінде атмосферадан жоғары болатын қысым кезінде қысымды ағын түрінде болады. Алайда, газ түріндегі реагенттерді микро көлемдерде және соның ішінде газ түріндегі қышқылсыздандырғыштарды отынның қатты немесе сұйық бөліктеріне жеткізу кезінде жіңішке шектеулі қабаттардың бетінде, молекулалық диффузияға осы қабаттың сыртқы шегінде және беттің өзінде заттардың әр түрлі концентрациясының әсерінен, тасымалдау жүреді. 5. Газ қоспаларында жанудың жалпы кинетикасы мен механизмі Отынның жылу жұтқыш қабілеті деп оның салмағының (немесе газдарға арналған көлем) толық жануы кезіндегі бөлінетін жылу мөлшерін атайды. Сұйық және қатты отын үшін жылу жұтқыштық қасиет ккал / кг – мен, ал газ түріндегілер үшін – ккал / нм2 түрінде болады. Гесс заңы бойынша, органикалық қосылыстардың жану жылуы, оған кіретін көміртек және сутектің және қоспа молекулаларын түзу жылуының жиынтығы арасындағы айырмашылыққа тең. Отындағы негізгі жанғыш ретінде көміртек саналады. Көміртектен тұратын кез келген қосылысты түзетін жылу көміртектің жану жылуымен салыстырғанда айтарлықтай аз. Сондықтан да, отындағы көміртектің қосылу пішініне тәуелсіз, жану кезінде бос көміртек келесі реакция бойынша қанша жылу берсе, сонша береді: С + О2 = СО2 + 97650ккал / г · моль, немесе 97650 / 12 = 8137ккал / кг. Сутекті қарастырғанда, оның оттек (0 / 8) отынының органикалық массасына эквивалентті кіретін бөлігі Н2О-мен байланысты болады және жану жылуын бөлу кезінде қатыспайды деп есептелінеді. Тек сутектің көміртекпен және органикалық массадағы басқа қосылыстармен байланысқан бөлігі ғана жылу бөлу арқылы жанады. Сутекті қоспалардың жылу түзуі жеткіліксіз болғандықтан, жану кезінде бұл сутек бөлетін жылу, қышқылсыздандыру кезіндегі бос сутек бөлетін жылумен келесі реакциядағыдай болады деп есептелінеді: H2 + 1 / 2О2 = H2О(ж) + 68360ккал / кг · моль, немесе келесі реакция бойынша H2 + 1 / 2О2 = Н2О(пар) + 57810ккал / кг · моль, Яғни, егер сутек түзілсе 57810 / 2 = 28905ккал және егер бу түзілсе, 1 кг сутек береді 68360 / 2 = 34180ккал. Отындағы үшінші жылу түзгіш элемент болып, сульфид (FeS, FeS2), сульфат (CaSО4) және күкіртті – органикалық қоспа түріндегі күкірт саналады. Отындағы барлық күкірт бос элемент ретінде SО2-ге дейін жанады деп есептелінеді, яғни келесідей жылу бөле отырып жүреді: Келтірілген болжамдар бойынша отынның жылу жұтқыш қасиеті келесідей мағынаға ие болады: Qв = 81,37 · Cp + 341,8(Нр - Op / 8) + 21,81Sp ккал / кг, (1) мұндағы, Ср, Нр, Op, Sp – отынның жұмысшы массасындағы көміртек, оттек, сутек және күкірттің мөлшері, %. Осы формула бойынша отынның жұмысшы массасында (Qн), гигроскопиялық ылғалдылықсыз және сутек сұйық судың түзілуі арқылы қышқылсызданады деген шартпен, жоғары жылу жұтқыштық қасиетті анықтайды. Отынды жағу кезінде, жалпы, су бу түрінде шығарылады, сәйкесінше әрбір қышқылсыздандырылатын сутекке 289,05 ккал жылу бөлінеді, гигроскопиялық ылғалдылықтың жоғалуына шамамен 600 ккал / кг жылу бөлінеді. Осы түзетулерді енгізіп, жанудың тәжірибелік шартын өрнектейтін, отынның төменгі жылу жұтқыштық қасиетін есептеуге арналған формуланы аламыз: Qв = 81,37 · Cp + 289,05(Нр - Op / 8) + 21,81Sp - 6Wp ккал / кг, (2) мұндағы, Wp – отынның жұмысшы массасындағы гигроскопиялық ылғалдылықтың пайызы. Осы формулалар бойынша отынның жылу жұтқыштық қасиетін есептеу калорометриялық анықтамалармен өте жақын сәйкес келеді, соның ішінде тас көмірлердің. Сондай-ақ, Д.И.Менделеевтің, Д.П.Коноваловтың, Фондрачектің эмперикалық форулаларының есептерінде де ұқсастық бар. 6. Тығыз қабаттағы газ бен шикіқұрам арасындағы жылу алмасу заңдылықтары Қыздырылған ауаны үрлеу кезінде енгізілетін жылудан басқа шикіқұрам мен газды қыздыруға, шойын мен қождың балқуына қажетті, жылу жоғалтулардың тотықсыздану мен компенсациясы үрдістерін қамтамасыз ету үшін керек жылу көздеріне келесілер жатады: отынның (кокстың және оның орнына кокстың бір бөлігі үшін қолданылатын табиғи газдар, мұнай өнімдері мен көмір ұнтақтары) жануы кезінде көріктің жоғарғы жағында пайда болатын жылу. Ыстық газ тәрізді жанғыш өнімдер төмендегі салқын шикіқұрам материалдарына өз жылуларын бере отырып, көріктен жоғары қарай көтеріледі де, өздері салқындай бастайды. Сондықтан, пеш көрігінен жоғарыға қарай колошникке шығар кезде пеш температурасы 1400 - 1600○С - тан 200 - 350○С - қа дейін төмендейді. Мұнымен қоса, көлденең қимада пештің бірдей ендіктерінде температуралар тұрақты болмайды да, айтарлықтай кең ауқымда өзгеріске ие болады. Бұл пеш қимасы бойымен көтеріліп келе жатқан ыстық газдардың біртексіз таралуымен түсіндіріледі, газдардың максималь көп мөлшері көлденең қима аумағында шикіқұрамның аз қарсыласуымен өтіп кетеді де мұнда ең жоғарғы температуралар байқалады. 7 Домна пешіндегі тотықсыздану үрдістері Темір домна пешіне тотықтар түрінде енеді, агломератта Fе2О мен аздаған Fе2О3 және FeO болады, шекемтастарда - Fе2О3 және Fе2О, темір кені, егер оны қолданса - Fе2О3 және Fе2О, мұнымен қоса бұл тотықтардың бір бөлігі өздге де тотықтармен байланысқан түрде кездеседі. Домна үрдісінің негізгі мақсаты - осы тотықтардан оларды тотықсыздандыра отырып мүмкіндігінше көп мөлшерде темірді бөліп алу. Тотықсыздану тотықтардан оттегіні бөліп алып олардан элементті алуға негізделген (немесе оттегі мөлшері аз тотықтар алуға). Оны тотықсыздандырғаш көмегімен жүзеге асырады - ол тотықсызданатын элементпен салыстырғанда, оттегімен көп ұқсастығы бар болуына байланысты оттегі бөлініп байланыс түзе алатын заттар. Осылайша, тотықсыздану үрдісінде бір зат оттегіден ажырайды, ал екіншісі оны өзіне алады (тотығады). Жалпы алғанда тотықсыздану үрдісі келесі теңдеумен жазылады: МО + В = М + ВО, (3.1) мұнда, М - тотықсыданатын металл; В - тотықсыздандырғыш; МО - тотықсызданатын тотық; ВО - тотықсыздандырғыш тотығы. Академик А.А. Байковтың тұжырымдамасына сай, темір тотықтарының тотықсыздануы сатылай жоғарыдан төмен орындалады: Fе2О3 - Fе2О - FeO - Fe. (3.2) 3Fе2О3 + СО = 2Fе2О + CO2 + 53740, Fе2О + СО = 3FeO + CO2 + 36680, FeO + СО = Fe + CO2 + 16060. Осылайша, жанама тотықсызданудан тікелей тотықсызданудың айырмашылығы көміртегінің шығындалуында, ал бұл дегеніміз - тікелей тотықсыздану үрдісінің дамуымен фурмаға берілетін көміртегі мөлшері азаяды. Домна пешінің атмосферасында 8 - 12% - ға дейін жетуі мүмкін сутегімен жанама тотықсыздану келесі реакциялармен жүреді: 3Fе2О3 + Н2 = 2Fе3О4 + Н2О - 4200, Fе3О4 + Н2 = 3FеО + H2O - 62410, FеО + Н2 = Fе + H2О - 27800. 8. Пештің жоғарғы бөлігінде гидраттар мен карбонаттардың ыдырауы Домна пешіне енгізілетін шикіқұрам гидроскопиялық ылғалдылыққа ие болады (мысалы, кокста 0,5 - 5%), ал кейде гидратты ылғалдылықта болады. Гидроскопиялық ылғал колошникте жеңіл буланады және оның шығып кетуі үшін қосымша жылудың қажеті болмайды, себебі колошникті газдардың температурасы ылғалдың булану температурасынан жоғары болады. Гидратты ылғал тек темір кенін пешке енгізгенде ғана пайда болады, ол Fе2О3 - пен (қоңыр теміртаспен) немесе Аl2О3 - пен (каолиниттерде Аl2О3 · 2SiО2 · 2Н2О) байланыс түзеді. Бұл қосылыстар жылуды жұта отырып, 400 - 1000○С - та ыдырайды. Алайда, қазіргі уақытта шикізатты кендер қолданылмайтын болғандықтан, гидратты ылғалдар балқыту үрдісіне айтарлықтай әсер етпейді. Карбонаттар (көмірқышқылды қосылыстар) домна пешіне әктас түрінде СаСО3 (кейде ол біршама СаСО3 мен біршама МgСО3 құрамдас болуы мүмкін), кабонатты темір кені түрінде (FеСО3) және марганец кені түрінде (МnСО3) түсуі мүмкін. Қыздыру кезінде карбонаттар жылуды жұта отырып, СО2 мен металл тотығына ыдырайды. Қазіргі таңда шикізатты кендер домна пешіне салынбайды, домна қожына қосуға міндетті СаО - ны енгізу үшін салынатын әктасты агломерат шикіқұрамына қосып жібереді және қождың негізділігін жоғарылату үшін пешке аздаған мөлшерде әктас салынады. Мұнда әктас келесі реакциямен температурада қарқынды ыдырайды: СаСО3 = СаО + СО2 - 178500Дж. Ыдырауға жұмсалатын жылу шығындарынан басқа, кері әсер ететін факторға 1000○С - тан жоғары температурада СО2 + С = 2СО реакциясының жылуды жұту арқылы жүруі мен кокс көміртегісінің жұмсалуы жатады. Қождамаланған агломератты қолдану мен (яғни агломерат шикіқұрамына әктас қосу арқылы алынған) және домна шикіқұрамынан әктастың толықтай алынуы коксты үнемдеуге мүмкіндік береді. Агломерация кезінде әктастың ыдырау үрдісі қымбат тұратын қоры аз металлургиялық кокстың емес, төмен сортты отынның (кокс ұнтағы, антрацитті үгінді) жануы кезінде жүзеге асады. 9. Шикіқұрам қабатына қойылатын талаптар Дәстүрлі металлургиялық үрдіс, ең алдымен, газды өңдегіш реагент және энергия тасымалдағыш ретінде қолданылуына негізделген. Шикіқұрам берілген температураға дейін қыздыру және химиялық реакциялар, соның ішінде, газдардың тотықтары газдың шикіқұрамның бірлігіне 1000 – 1200 м3 / т аралығында жұмсалуы кезінде түзіледі. Агрегаттың берілген өнімділігін қамтамасыз ету т / тәул немесе т / сағ бірлігінде бағаланады. Онда газ шығыны өнімділікті меншікті шығынға көбейту арқылы табылуу мүмкін: Көріп отырғанымыздай, 1 сағатта шикіқұрам материалдары арқылы газдың мөлшері υΓ өтуі қажет. Металлургиялық агрегатта газ ағыны өтетін, шикіқұрамның діңгегінің қимасы бар болғандықтан, олардың қатынасы арқылы газ ағынының қозғалу жылдамдығын есептеп шығаруға болады, яғни. ωГ = , , немесе (2) ωГ = . (3) Бұл теңдеу арқылы шикіқұрамның қабатына негізгі талаптар қойылады. Шикіқұрамның қабаты өзінің берік күйін сақтауы және (3) қатынасымен анықталатын жылдамдық бойынша газды ағынды өткізуі қажет. Бұл талапқа газ өткізгіштік деп аталатын қабаттың қасиеті сәйкес келеді. Қабаттың газ өткізгіштігін қамтамасыз ету үшін соңғысы кесектілікке ие болуы керек. Кесекті материалдардан тұратын қабат газ ағыны өтетін, бос кесек аралық аумаққа ие. Бір жағынан бай темір кенді кен орындарының таусылуы, өте кедей темір кенді кен орындарды қайта дамыту шикізатты дайындау алдында кен шикізатын, ұсақ және дисперсті материал түрінде болатын, темір кеннің дайын өнімін міндетті түрде байытуды алға қойды. Сондықтан да, оны дәстүрлі металлургиялық үрдісте тікелей қолдану, мүлдем мүмкін емес және тек одан кесектелген шикізатты өндіру арқылы жүргізіледі. Домналы шахталы пешке кесектелген шикізатты тығыз шикіқұрам діңгегі түрінде тиелгеннен кейін қысылған жағдайда төменге жайлап түсіріледі. Пештен жоғарыдан төмен қарай қозғалу кезінде қабат түйіршіктері қысымға, тазалауға, тегістеуге беріледі. Мұндай қозғалыс кезінде кесектелген кеннің ұнтақталуы сондай-ақ жағымсыз нәтижелерге әкеледі. Шикіқұрамның түсу шамасы бойынша ұнтақтарды ұлғайту колошникті шаңның шығарылып тасталуын жоғарылататын газ өткізгіштікті төмендетеді. Сондықтан, шикізатты кесектеудің маңызды талаптарының бірі болып кесектердің тығыздығы саналады. Кесектеу үрдісі үш негізгі әдістен тұрады. Шикізатты кесектеудің ең кең таралған әдісі болып агломерация саналады. 10 Агломерациялық үрдіс Үрдісті жүзеге асыру үшін, агломерациялық шикіқұрамды құрастыру керек. Агломерациялық шикіқұрамның негізі ретінде темір кенінің дайын өнімі және ұсақ аглокен саналады. Дайын өнім және кеннің негізгі құраушысы ретінде, әдетте, шамамен 80 - 85% құрайтын темір тотығы саналады. Дайын өнімдер және кендер, әдетте, қышқыл болып келеді. Металл емес тотықтарда SiO2 тотығы кездеседі. Шикіқұрамды дайындау кезінде күтілетін қождың негізін және құрамын болжамдайды. Қож шикіқұрамының негізі келесі қатынаспен сипатталады: Бастапқы дайын өнім және кендегі СаО жетіспейтіндіктен, шикіқұрамға, әдетте негізі ретінде әк қолданылатын, флюсті қосу қажеттігі туындайды. Әк белгілі бір негізділіктегі В флюстық қабілетпен сипатталады. ФС = СаО(Ф) - ВSiO2(Ф) (5) Мысалы, В = 1,2 болған кезде: ФС = 54,0 - 1,2 ∙ 1,45 = 52,26. Шикіқұрамның кендік бөлігініің бірлігіне қажет флюстің шамасын келесі формуламен анықтауға болады: мұндағы, SiO2, CaO – шикіқұрамның кендік бөлігіндегі осы тотықтардың құрамы, %: SiO2(ф), CaO(ф) –флюстегі осы тотықтардың құрамы, %. (6) теңдеу бойынша шикіқұрамның екінші қоспасының – флюстің (әктің) шамасын анықтаймыз. Шикіқұрамның үшінші қоспасы болып < 8 мм фракциядағы кокс ұнтағы саналады. Оның шамасын шикіқұрам қабатын еріту температурасына дейін қыздырудың жылулық теңдеуі бойынша анықтауға болады. Бұл шама әдетте белгілі және оны толығымен шикіқұрамның кендік бөлігінің массасынан 4 - 6% аралығында алуға болады. Осылайша, аглокеннің барлық үш қоспасында көрсетуге болады. Кокс қосылысының негізделуі жылу бөлінумен сипатталады. Бұл үрдіс аглокен қабатындағы кокс түйіршіктерінің жану нәтижесінде жүргізіледі. Бұл үшін шикіқұрам қабаты арнайы мойындық арқылы өтеді, бұл аумақта қыздырғыш немесе форсунка арқылы газ түріндегі немесе сұйық өнімдерді жағып, жанғыш газды 1200○С температурада ауа қоспасымен жылдамдығы 1,1 - 1,4м / мин қозғалғыш конвейерде аглокен қабаты арқылы сорады. Осыған байланысты аглокеннің жоғарғы қабаты кептіріліп, қыздырылады әрі қарай кокс түйіршіктерінің жануы жүреді: СК + О2 = СО2 + Q. (7) Жылудың шығарылатын бөлігі шикіқұрам түйіршіктерін балқу температурасына дейін қыздырады және оның қайнауын тудырады. Газ үздіксіз сорылатындықтан, қайнайтын қабат жазық түрде түзіледі. Қабаттың қайнауы аяқталғаннан кейін, ауа әрі қарай сорыла береді. Қайнаған қабат салқындатылады да жазық пирог түрінде қалады. Осылайша, аглокеннің басынан бастап төмеңгі қабатына дейін қозғалғыш конвейерде түзіліп бкеиді: 1) кептіру аймағы, 2) қайта ылғалдандыру аймағы, 3) қыздыру аймағы (кокс түйіршіктерін қыздыру), 4) қайнау аймағы, 5) суыту аймағы. 11. Домна пешінің құрылымы Домна пеші (1-сурет) дөңгелек қималы шахталы пештен тұрады, оттөзімді құрылыммен футеревкаланған (жоғарғы жағы шамотты кірпішпен, ал төмеңгі жағы – көміртекті блоактармен). Құрылымның жанып кетуін тоқтату мен пеш қаптамасын жоғарғы температуралардан қорғау үшін су айналымды тоңазытқыштар қолданылады. Пеш қаптамасы мен колошникті құрылғы табанына орнатылған бағаналармен бекітіледі. Пеш колошнигіне шихта скиптермен, кейде ленталы конвейерлермен беріледі. Скиптер пешке қабылдау воронкасы және колошникке орнатылған себу аппараты арқылы беріледі. Ауа үрлеуші машиналардан ауа пешке ауа қыздырғыштар (мұнда ауа 1000 - 1200°С-қа дейін қыздырылады) және көрік бойымен орнатылған фурмалы аспаптар арқылы беріледі. Фурма арқылы мұнымен қоса қосымша отын да енгізіледі (табиғи газ, мазут немесе көмір шаңы). Балқыту өнімдері көріктің төмеңгі бөлігіндегі ағынөзектер арқылы шойын тасымалдаушы және қожға арналған шөміштерге шығарылады. Пеште түзілетін колошникті газ пеш күмбезіндегі газ бөлгішке шығарылады. 12. Домна шикіқұрамының құрамы Домна өндірісінде бастапқы материал болып саналады: темір кені, марганец кені, агломерат, шекемтастар, сонымен қатар жанғыш заттар мен флюстер. Домна пешінің шихтасы ретінде негізділігі 1,1-1,3 болатын 50-60% Ғе құрамды флюстелген агломерат қолданылады, флютелген шекемтастарды қолдану да даму үстінде. Темір құрамды шихта материалдарының домнада балқытудың технико-экономикалық көрсеткіштерін анықтайтын негізгі қасиеттері: темір мөлшері, бос жыныс құрамы, зиянды қоспалар мөлшері, сонымен қатар гранулометриялық құрам, беріктік пен тотықсыздану қабілеті. Домна өнідірісіндегі негізгі жанғыш затқа көміртасты коксты жатқызуға болады. Кокстың біраз бөлігін домна пешінің көрігіне үрленетін газ тәрізді, сұйық және қатты отынмен алмастырып балқыту кең тараламға ие болып келе жатыр. Флюстер ретінде әктас, кейде доломит қолданылады. 13. Домна пешіндегі шикіқұрам мен газ қозғалысы Қазіргі заманғы домна пештерінде онда материалдың болу ұзақтығы 4-6 сағат, ал газдар – шамамен 3-12 секунд. Балқытудың жоғарғы көрсеткіштері газдардың пеш қимасы бойымен жақсы таралуы кезінде алынуы мүмкін. Тек осы жағдайда газдар максимал дәрежеде материалдарға физикалық жылу бере алады және олардың тотықсыздану қабілеті толығымен қолданылуы мүмкін. Белгілі болғандай, пеш қимасы бойымен газ ағынының таралымы газ өтетін шихта діңгегінің қарсыласуына тәуелді болады. Газдардың әрқашан аумақта шихтамен аз қарсыласа қозғалатынын ескере отырып, оны жүктеу үрдісінде пеш қимасы бойымен агломераттың коксқа қарағанда газөткізгіштігі аз екенін есепке ала агломерат пен коксты белгілі бір қатынаста тарата отырып, реттеуге болады. Егер мұны жасамайтын болсақ, онда газдардың негізгі бөлігі шихтамен аз қарсыласа отырып қозғалады да, пештен жоғарғы температурада шығып кетеді, яғни эжылу энергиясын толық қолданбайды және тотықсыздану қабілетін толықтай орындалмайды. Мұнымен қоса газдың штхтамен жоғарғы қарсыласуы туындаған кезде газ аз енетін болады, сондықтан шихта аз қыздырылып, нашар тотықсызданады, бұл пешгтің төмеңгі жағынан қосымша энергия көзін, яғни кокс шығынын арттыруды талап етеді. Жүктеу кезінде ең алдымен келесіні есепке алады: үрлеу пешке қабырғалардан келеді, тегіс қабырғалардың газбен қарсыласуы шихта көлеміне қарағанда төмен болады, осыған байланысты газдар қабырғада қозғалуға ұмтылады. Сондықтан, қабырғаларда газөткізгіш агломераттан аз қалыңдықтың болуы, ал центрінде кокс қалыңдығынан қалыңырақ болуы қабылданған, бұл газ ағынының центрге қарай таралуына мүмкіндік береді. Пеш бойымен де материалдар бірегей орналасуы керек. Екі конусты сеппелі аппараты бар пештерде шихтаны пешке жекелей бөліктеп енгізеді. Жүктеу бірнеше скипті құрайды (көбінесе төрт, ал кейде үш, төрт, алты) және кенді бөліктен (негізінен агломераттан) және шихтаны есептеудегі қатынаспен алынатын кокстан тұрады. Жүктеу біріккен,бөлшекті және ажыратылған болуы мүмкін, біріншісінде оған енетін барлық агломерат пен кокс скиптері кіші конусті айналдырмай жіберу арқылы үлкен конусқа жинақталады, одан кейін пешке бір үлкен конусты жібере отырып, жүктелінеді (оны белгілеу мысалы: ААКt); екіншісінде агломератты үлкен конусты бір рет түсіру арқылы жүктейді, ал коксты – екінші ретте (ААtККt) және үшіншісінде беріліс екі қабылдағышпен жүзеге асады, бірақ әрқайсысында кокс та, агломерат та болады (ААК, ККАt). Берілген белгілеулерде t белгісі үлкен конустың жіберілуін, А – агломерат скипін, К – кокс скипін білдіреді. (Берілісті жинау реті мен колошник бойымен берілістердің таралуы сеппелі аппаратты суреттеуде жоғарыда келтірілген). Колошник қимасы бойымен агломерат пен кокстың таралымын басқару үшін келесілер қолданылады: үлкен конустағы агломерат пен кокс скиптері жинағының реттілігін өзгерту, бөлек және ажыратылған берілістерді қолдану, беріліс массасын өзгерту, колошниктегі сеппе деңгейін сатылы өзгерту, пешке берілісті жүктеу кезінде үлкен конусты толық емес түсіру, колошник қабырғаларында қозғалмалы плиталарды қондыру. Шихта таралымын осы әдістерді қолдана отырып реттеуде сеппелі материалдарды енгізудің келесі белгілі заңдылықтарын есепке алады: - үлкен конустан келіп түсетін материалдар колошникте жота бойымен тік орналасады; - жота қабырғаларда орналасқанда бір, ал қабырғалардан алынғанда екі сырғымаға (скат) ие болады; - шихта құлаған орында көп мөлшерде ұнтақ материал жинақталады, ал ірі кесектер айтарлықтай шамада жотаның табанында жиналады, сондықтан да жота аумағында шихтаның газөткізгіштігі төмен болады. Осы кезде ұнтақтың негізгі бөлігі агломерат болып есептеледі; - жотаның орналасуына колошниктегі сеппе деңгейіне тәуелді болады, сеппенің деңгейі H1-ден H3-ке төмендегенде жота колошник қабырғаларына жақындайды; - жотаның орналасуы үлкен конус пен колошник қабырғасы арасындағы саңылауға да тәуелді болады, саңылау кіші болғанда жота қабырғада, ал үлкен болғанда қабырғадан тыс орналасады; - шынайы еңіс (естественный откос) бұрышы еркін орналастыру кезінде жоғарыдан құлап келе жатқан кокста агломератпен салыстырғанда кіші болады, сондықтан үлкен конус себу кезінде пеш қабырғасында агломераттың қалың қабаты, ал ортасында кокстың қалың қабаты пайда болады; - осындай еңіс бұрыштарының айырмашылығына орай беріліс массасын азайту пеш ортасында агломерат қабаты қалыңдығының кемуіне алып келеді, және аумақ ортасында агломератсыз жақсы газөткізгіштікті қалыптастыруға мүмкіндік береді; - үлкен конусты толық емес түсіру материал жоталарының колошник қабырғаларына қарай орналасуына және ұһнтақтың көп мөлшерінің периферияға түсуіне мүмкіндік туғызады; - беріліс үлкен конустан жүргізілгенде оның төмеңгі бөлігі қабырғада жаьады, бұл кезде центрге берілістің соңғы бөлігі түірілетін жота түзіледі, яғни пеш центріне негізінен үлкен конусқа соңынан жүктелген скип материалдары түсіп отырады. Сәйкесінше, ААКК агломератпен беріліс кезінде пеш центріне көп мөлшерде кокс, ал кері бағытта KKAAt берілген кезде көп мөлшерде агломерат беріледі. 14. Мартен пешінің құрылысы 1864 жылы Пьер Мартен пеште ең алғаш болат балқытуды жүргізді. Ол өз құрылымында және толықтай ғасыр бойы әлемде болаттың көп мөлшері мартендік пештерде балқытылған. Өндірістің бұл әдісі өзінің әмбебаптылығымен байланысты – олардың алынуы болаттың әр маркасын даярлау үшін сұйық пен қатты металдың кез келген қатынасында әр түрлі шойын типтерін қолдана отырып және бұрыңғы бақылау мен талдау кезінде мүмкін болады. Ал қазіргі таңда мартендік пештерден әлем металлургтарының барлығы бас тартты, тек ТМД елдерінде мартендік өндіріс үлесі шамамен 30%-ды құрайды (әлем бойынша бұл 3%), ТМД елдерінде мартендік пештер қолданыстан жайлап шығарылуда, оның ішінде, Ресейде 2010 жылы мартендік болаттар үлесі 10%-дан аспайды деп күтілуде. 15. Мартендік әдіспен болат өндіру Мартендік әдіспен болат өндіру негізгі пештерде жүзеге асқан болатын. Пеш енгізбесін жылуға төзімді магнезит хромитті немесе динансты кірпіштен жасайды. Басшалар арқылы отын мен ауа беріледі. Ванна үстімен газ қозғалысының бағытын периодты өзгерте отырып, жану өнімдерін жояды. Жұмысшы кеңістігі басшадан тік каналдар арқылы және қож шығарғыштар регенератормен жалғанған. Регенераторлар мартендік пештердің негізгі міндетті элементі болып саналады, онсыз қажетті температураға қол жеткізу және балқыған түрдегі болат алу мүмкін емес. Қож шығарғыштар ірі шаңдарды шөктіре отырып, шығарылатын газдарды бірніші ретті тазалауға арналған. Регенераторлардан соң бу газдары бу құбырына түседі, немесе ауаға жіберілмес бұрын газды тазалаудан өтеді. Түтін құбыры газды байланыс қақтығысын қамтамасыз ететін ауырлыққа қабілетті болу керек. Сондықтан ірі мартендердің түтін құбыры 100 м болады. Жоғары фосфорлы шойындарды өңдеу үшін цилиндрлік төмеңгі бөлікке ие және тігінен ажыратылатын айналмалы мартендік пештер қолданылған болатын, бұл қожды білікті терезелер арқылы көпретті айналдыруға мүмкіндік береді. Мұндай пештер құймалы цехтарда қолданылады, мұнда сұйық болатты жиі аз үлестермен беріп отыру керек болады. Орташа мартендердің сыйымдылығы 125-300 т, ал үлкен жүктілерде 900 т болады. Мартендік балқытудың ерекшелігі оның металл ваннасына жылу мен оттегінің қож қабаты арқылы жоғарыдан берілуінде. Сондықтан, үрдістің керекті жылдамдығына ие болу үшін пеш ваннаның аз тереңдігінде (~ 1м) балқыған металдың үлкен бетке (0,5м2 / т) ие болады. 16. Мартен пешінің жұмысы Пеш жұмысының қағидасы келесіге негізделген: шихтаны жүктегеннен кейін басшалардан отын (мазут, табиғи газ) регенераторда ~ 1200°С-қа дейін қыздырылған ауа желдеткіштен беріледі, бұл жалын температурасын туғызады - 1900°С. Тиімді жылу берілісі үшін жалын ваннамен жанасуы және оның бетімен өтуі керек. Жалын жылуы ваннадан шамамен 85% сәулеленумен, ал 15% - конвекциямен беріледі. Шыққан газ пештен басша арқылы пештің өзге аяғында 1500°С температурамен беріліп, жылудың негізгі бөлігі қарсы регенератордағы оттөзімді енгізбе арқылы беріледі. Регенератор «үрлеу арқылы» суыған соң және «газ арқылы» қыздырылған соң клапандарды ашады, мұның нәтижесінде газ ағынының бағыты қарама-қарсы өзгереді. Мартендік үрдісте ваннаның ұзындығы мен тереңдігі бойынша температуралық біртексіздік пайда болады, бұл кезде қож температурасыәрқашан металл темперасынан жоғары болады. Температураның айшықталуына көміртегі қышқылданғанда түзілетін СО көпіршіктерінің есебінен ваннаның «қайнауы» мүмкіндік береді. Оттегі көзі болып үрленетін ауа, жану өнімдері (СО2, Н2О),сонымен қатар қосымша енгізілетін қатты тотықтырғыштар табылады. Керекті құрам мен металл тепмературасы орнағаннан кейін легирлеуші мен қышқылсыздандырғыштар қосу арқыл қайнауды тоқтатады. Мартендік балқытудың жалпы ұзақтығы 6 сағаттан астам, жылудың қолданылу коэффициенті 50%-дан аз емес. Шихтаның құрамына байланысты мартендік үрдіс екі түрлі болады: кенді-скрап және үрдіс-скрабы. Кең таралған скрап-кенді үрдіс кезінде шихтадағы сұйық шойын үлесі 60%-ды құрайды (скраптағы үлесі небәрі 30%), бұл қатты тотықтырғыштардың – кен, агломерат, шекемтастардың жоғары мөлшерін - шамамен 10%, сонымен қатар флюстердің жоғарғы шығнын қажет етеді. Скрап-үрдісте шихта негізін болат сынықтары құрайды, және тек металды ғана балқыту керек болады. Бұл үрдісті қышқыл футеревкада жүзеге асыруға мүмкіндік береді, ол газды және бейметалдық қоспалары бойынша таза болат алуға мүмкіндік береді. Ваннаның «қайнауы» үшін шихтаға арнайы карбюризаторлар – көміртек құрамды қоспалар қосады (қатты шойын, кокс және т.б.). Соңында айта кетерлік жай, жақсы өңделген технологиялық үрдіске ие болуына қарамастан мартендік үрдіс барлық жағынан конвертерлі және электрлі болат балқыту өндірістерінен артта қалып отыр. Сондықтан, мартендік пештер және балқыту технологиялары пудлингті үрдістер секілді металлургия саласының тарих беттеріне жақынырақ. 17. Үздіксіз әрекетті агрегаттардағы болат өндіру Бұдан бұрынырақ айтып өткендей, қазіргі бар болат өндіру агрегаттары (конвертерлер, мартендік, доғалы, индукциялы пештер) периодты сипатте жұмыс жасайды және осыған орай, бірқатар кемшіліктеге де ие. Заманауи болат балқыту өндірісінің жоғары деңгейде болуына қарамастан, агрегаттардың тоқтап тұру уақыттарының үлесі балқыту мен циклдің барлық уақытының жартысын құрайды екен. Меншікті өнімділікті одан әрі арттыру көмекші жұмыстарға жұмсалатын уақытты азайту есебінен ғана мүмкін болады. Осы мезетте үздіксіз әрекетті болат балқыту агрегаттарын жасап шыңару мәселенің шешімін табуға мүмкіндік береді. Үздіксіз әрекетті болат балқыту агрегаттарының құрылымын асап шығару және осы агрегаттарда болат балқыту үрдісін өңдеумен әлемдегі көптеген елдер мамандары шұғылдануда, бірақ әзірге еш сенімді нәтиже табылған жоқ. Біріншіден, бұл шойыннан бір уақытта термохимиялық қасиеттері жағынан әр текті қоспаларды шығрып алу үшін әр түрлі жағдайларды жасай білудің қажеттілігмен байланысты. Екіншіден, болат балқыту үрдісінің бұл сұлбасы бір уақытта жүргізілуі мүмкін емес сатылар қатарынан тұрады. Үшіншіден, қажетті технологиялық операциялар реттілігін қамтамасыз ететін және жоғары температуралар кезінде жөндеу мүмкіндігі болмаған жағдайда жоғары төзімділікке ие агрегат құрылымын жасау күрделі болып табылады. Ақырында, техникалық шешім қазіргі қолданыстағы заманауи үрдістермен салыстырғанда экономикалық тұрғыдан тиімді болуы керек Мұнымен қоса, қазіргі таңда ҮӘБА-ның бірнеше үлгілері ұсынылып келеді, оларды келесідей топтарға бөлуге болады: - үрдіс сатысының санына қарай: көпсатылы, яғни агрегаттың жеке бөлігінде бір не бірнеше технологиялық операциялар жүреді; бір сатылы, бұл кезде барлық саты қоысылып кеткен, және барлық қоспалар бір уақытта жойылады; - агрегат құрылымы бойынша: жалпақ, оларда газ тәрізді және қатты реагенттер жалпақ және желобты реакторларға түседі; ағысты реакторлар, мұнда барлық материалдар ілінбелі ұнтақталған тамшы тәрізді күйде болады; тек металл сынықтарын өңдеуге арналған шахталы пештер; - балқу өнімдерінің қозғалыс бағытына байланысты: тік ағынды, яғни қож бен металдың қозғалысы бір бағытта жүреді; ағынға қарсы, яғни қож бен металл қарсылас бағытта жүреді. Сұйық шойынды болатқа айналдыруға арналған ҮӘБА-ның көбісі жалпақ агрегат түрінде болады. Металл сынықтарының үздіксіз өңделуі доғалы, немесе шахталы пештерде жүзеге асады. Айта кетерлік жай, сұйық шойынды өңдеуге арналған ҮӘБА жартылай өнеркәсіптік сыналу деңгейінде, мұнымен қоса олар метал сынықтарын өңдеуде бірқатар танымалдылыққа ие. Бірақ соңғы жағдайда алынатын металл жартылай өнім болып саналады және көмекші агрегаттарда болат қылып дайындауды қажет етеді, бұл дегеніміз мұндай үрдіс қазіргі таңдағы болат балқыту тиехнологияларының толыққанды орны басушысы бола алмайды. Осылайша, бүгінде жоғарғы сапалы болат алуға мүмкіндік беретін және қазіргі болат балқыту технологиясының орнын алмастыра алатын оңтайлы ҮӘБА құрылымы әзірше табыла қойған жоқ. Бұл мәселенің шешімін болат балқыту үрдістеріне басқаша көзқараспен қарау арқылы табуға болатын болар. Кез келген үздіксіздік бұл белгілі жиіліктегі үзіктілердің жиынтығы болып саналады. Мысалы, домна үрдісі үздіксіз болып саналады, алайда балқу өнімдерін енгізу де , шығару да периодты режимде жүзеге асады. Болат балқыту үрдісі қатыстық үздіксіз шарттарына қазіргі технологияларына жақын бағытта дами түседі. Тек бір мәселенің шешімін табу үздіксіз үрдісті қалыптастыруды айтарлықтай қысқартады. Жалпы алғанда, бұл тікелей болат балқыту агрегаттарының қызметін қысқарту есебінен жүргізіледі, атап айтқанда:: шойынды домнадан тыс күкіртсіздендіру, оны домнаның негізгі желобында кремнийсіздендіру, белсенді миксерлер қолдану, болатты шығу алдында қышқылсыздандыру, шөмішті металлургия, пештен тыс өңдеу және т.с.с. 18. Болаттардың жіктелу Жіктеудің әлемдік бірегей жүйесі қазірде жоқ. Біршама факторларға тәуелді және қасиеттерін тез меңгеру мақсатымен болатты келесі белгілері бойынша жіктейді: тағайындалуы, сапасы, құрамы, өндірілу әдісі. Ресейде бұдан өзге де жіктеу әдістері бар. Тағайындалуы бойынша болат, құрылымдық, аспаптық, мойынтіректі болып бөлінеді. Сапасы бойынша үш топқа бөлуге болады: жоғарғы сапалы, сапалы, қарапайым сападағы. Қышқылсыздануы бойынша – қайнаған, жартылай тыныш, тыныштықтағы. Өндірілу әдісіне қарай болат конвертерлі, электрлі болуы мүмкін, мұнымен қоса, осы кездердегі нақты алу шарттарының болуына байланысты. Көбінесе болаттың сапасының көрсеткіші болып табылатын құрамына сай оны екі негізгі сұрыпқа бөледі: көміртекті, оның ішінде аз көміртекті, орта көміртекті және жоғарғы көміртекті; легирленген, оның ішінде аз легирленген және жоғарғы легирленген. Жоғарғы легирленген болаттарда темір мен көміртегіден басқа бір не бірнеше элементтердің біршама мөлшері болады: никель, марганец, кобальт, молибден. Жоғарғы легирленген болаттар қатарына тот баспайтын, аспаптық болаттар қатары енеді. Маркаларда шамамен химиялық құрамды өрнектеу үшін Ресейде металдағы элементтерді кириллица әріптерімен белгілеу қабылданған (мысалы, Мn - Г; Сr - X; Ni - Н; V - Ф; Ti - Т), ал олардан кейін тұратын сандар олардағы пайыздық дәлдікпен құрамындағы мөлшерін көрсетеді. Әріптен кейін тұратын сандар болмаса, сол элементтің 1%-дан аз екенін көрсетеді. Легирленген болаттарды белгілеуде алғашқы сандар көміртегі мөлшерін пайыздың жүзден бір үлесімен көрсетеді. Мысалы, 30Х2Н болатта 0,3% С, 2% Cr және 1%-дан аз Ni құрамды. 19 Үрдістің негізі мен жалпы сұлбасы Оттегілі-конверторлы үрдіс – бұл сұйық шойыннан металл сынығын қосу арқылы конвертерде негізгі футеревкамен және сумен салқындатылатын фурма арқылы оттегімен үрлеу көмегімен болат балқыту үрдісі. Шойынды жоғарыдан оттегімен үрлеуге қатысты алғашқы тәжірибелерді инженер Н. И. Мозгов жылы жүргізген болатын. Одан әрі бірқатар елдерде жаңа үрдіс технологиясын өңдеу бойынша зерттеулер жүргізілді. Өнеркәсіптік ауқымда оттегілі-конверторлы үрдіс алғаш 1952-1953 жылдары Австрияда Линце және Донавице қалаларындағы зауыттарда жүргізілді. Қысқа мерзімде оттегілі-конверторлы үрдіс барлық елдерде кеңінен таралып кетті. Сонымен, егер 1960 жылы оттегілі-конверторлы болаттың үлесі әлемдік болат балқытудың 4%-ын құраса, 1970 жылы - 40,9%, ал 1980 жылы - шамамен 65%-ды құрады. Оттегілі-конверторлы үрдістің тез дамуы оның басқа конверторлы үрдістер секілді мартендік және электрлік болат балқыту үрдістерімен салыстырғанда бірқатар артықшылықтарға ие болуымен түсіндіріледі. Ол артықшылықтардың негізгілері келесілер: 1) бір жұмыс істеп тұрған болат балқыту агрегатының өнімділігінң жоғарылау болуы (мартендік және электр доғалы пештердің сағаттық өнімділігі 100т / сағ, ал үлкен жүктемелі конверторларда 400 - 500т / сағ); 2) әлдеқайда аз капиталдық шығындар, яғни цех ғимаратына жұмсалатын шығындар, бұл конвертор құрылғысы құрылымының қарапайымдылығымен және цех балқыту агрегаттарының аз санын қондыра алц мүмкіндігімен түсіндіріледі; 3) өңдеуге қатысты шығындардың аз болуы, оларға электр энергиясының құны, жанармай, оттөзімділер, ауыспалы жабдықтар, еңбек ақы құндары енеді; 4) үрдіс балқыту үрдісін басқаруды автоматтандыруға ыңғайлы болып табылады. Үрлеу үшін таза оттегі қолданылатын болғандықтан, оттегілі-конверторлы болатта азот мөлшері мартендікімен салыстырғанда азырақ, және сапасы жағынан мартендік болаттан алда тұр. Шойын құрамдылардың тотығуы кезінде бөлінетін жылу болатты шығару температурасына дейін қыздыруға жеткілікті. Әрдайым бөлініп отыратын артық жылу мөлшері конверторда металл сынықтарының толығымен өңделуіне септігін тигізеді. Бұл үрдістің ең негізгі артықшылығы болып табылады, себебі металл сынықтарының құны арзан болғандықтан, балқытылатын болат құны да төмендейді. Шетелдерде оттегілі-конверторлы үрдіс ЛД үрдісі деген атау алған. 20 Балқыту технологиясы Балқытуды конверторға металл қалдықтарын жүктеуден бастау керек. Жүктеуді металл қалдықтары салынған қалақтарды еңкейген конверторларға салып отыратын аудару машиналары немесе крандарының мойыншалары арқылы жүзеге асырады (3-сурет, а). Одан кейін аудару көмішінен көпірлі кран көмегімен еңкейген конвертор мойыншасы арқылы сұйық шойын құяды (3-сурет, б). Шойын құйылғаннан кейін конверторды тік жұмысшы бағытқа бұрады. Конвертор ішіне оттегі үрлей отырып, фурманы енгізеді (3-сурет, в). Одан кейін (3-сурет, г) қож түзушілердің бірінші үлесін салады (шпатпен кейде кен қосу арқылы әк, отқабыршық, шекемтас, боксит). Бірінші үлеске 1 / 2 - 2 / 3 қож түзушілер енеді, қалған мөлшерін бірнеше үлеспен үрлеу ұзақтығының алғашқы үштен бір ұзақтығында салып отырады. Сеппелі қож түзушілер сеппелілерді сақтауға арналған бункерден, қоректендіргіштен, конвертор мойыншасына материалдады енгізуге арналған таразылар мен қалақтардан құралған автоматтандырылған жүйе көмегімен салады. Жүйе конверторды басқару пультімен оператор орнатқан бағдарлама бойынша үрлеуді тоқтаусыз жүргізуге мүмкіндік береді. Оттегілі фурманы қатаң анықталған, бекітілген қалыпта орнатады. Фурма басынан тыныштықтағы ванна деңгейіне дейінгі арақашықтық конвертор сыйымдылығына және берілген цех технологиясына байланысты 0,8-3,3 м-ді құрайды. Әдетте қождың түзілу жылдамдығын арттыру үшін үрлеуді фурма қалпы жоғары болған кезде бастайды, ал 2-4 минуттан соң оны әдеттегі оңтайлы қалыпқа дейін жібереді. Оттегіні берудің қарқындылығы фурма құрылымына және қабылданған технологияға байланысты 2,5-тен 5 - 7м3 / (т · мин)-қа дейінгі мәнде болады. 23 Оттегілі-конверторлы балқытудың үрлеу режимі Конверторлы ваннаға оттегіні беру режимі үрлеу ұзақтығына, қож түзілу барысына, сұйық болат шығымының шамасына және оның сапасына, конвертор футеревкасының төзімділігіне айтарлықтай әсер етеді. Үрлеу режимінің маңызды параметрлері болып қысым мен оттегіні үрлеу қарқындылығы, оттегілі ағындар мөлшері, фурманың орналасу биіктігі мен ваннаға ағындарды енгізу биіктігі, оттегі жиілігі болып саналады. Оттегінің меншікті шығыны 47-57 м3 / т болатқа дейін өзгереді, шойындағы тотығатын қоспалар мөлшері ұлғаяды және шихтада болат сынықтарының үлесінің өсуімен төмендейді, себебі шойынға қарағанда сынықтарында тотыққан элементтер көбірек болады. Фурма алдында оттегі қысымы белгілі бір аралықта болуы керек. Шығатын Лаваля шоқылары газ қысымы энергиясын кинетикалыққа айналдырады. Ваннағы оттегі ағындарының терең енуі үшін және металдың оттегіге толығымен қанығуы үшін ағынның жоғарғы кинетикалық энергиясының жоғары болуы керек, сондықтан шоқы өлшемдері ағынның олардан шығу кезінде 450 - 500м / с болатындай етіп алынуы керек. Бұл кездегі фурма алдындағы қысым 1,2 - 1,6МПа болуы тиісті, қазіргі жұмыс жасап тұрған цехтарда 0,9-дан 1,4МПа-ға дейін өзгеруі мүмкін. 24. Оттегімен донналы үрлеу Конверторда ең алғашқы рет шойынды таза оттегімен үрлеу Ресейде 1945 жылы сынақтан өткізілді. Оның көрсетуінше, тотығу нәтижесінде фурмада шойын қоспаларында жоғарғы температура түзіледі және осы себеппен футеревка түбі бірнеше минутта бұзылады. Бірқатар елдерде жүргізілген зерттеулер өнеркәсіпте қолдануға жарамды көмірсутектерден жасалған сақиналы қорғаныш қаптамасымен қоршалған ағындар түрінде оттегіні төменнен енгізудің жаға технологиясын жасап шығаруға жетелейді. Сақиналы қаптама фурмадағы шойынмен оттегінің байланысын бодырмайды, мұнымен қоса сұйық металмен әрекеттесу кезінде көмірсутектер ыдырайды, бұл жылудың жұ ылуына алып келіп, фурма аумағының салқындауына тудырады. Бұл жағдайларда түпкі бөлік футеревкасының төзімділігі бірнеше жүздеген балқытуға шыдамды болады. Оттегі ағындарының айналасында қорғаныс қаптамасын орнату үшін табиғи газдың, кейде сұйық жанармайдың жұқа қабатын қолданады. Олардың ыдырауы кезінде сутегі мен оттегі бөлінеді. Табиғи газдың шығыны 6-8, ал пропанның шығыны жұмсалатын оттегінің шамамен 3,5%-ын құрайды. Өндіріс аясында донналы үрлеу үрдісі ГФР зауыттарының бірінде ең алғаш 1967-68 жылдары енгізілген және ОБМ атауына ие болған, бұл үрдістің түрлері АҚШ-та КУ-БоП, Францияда – ЛВС, ГДР – КЕК атауларын алған. 1980 жылы осы үрдіспен болат өндіру әлемде 38-40 млн. т құрады. 25. Үрлеудің аралас әдістері Донналы үрлеу конверторларының қолдану тәжірибесі мен ваннаның қарқынды аралас білуімен байланысты осы үрдістің технологиялық артықшылықтары соңғы жылдары аралас – төменнен және жоғарыдан үрлеу жүзеге асатын конверторлы үрдіс технологиясын жасап шығаруға мүмкіндік берді. Бұл технологиямен жұмыс жасауға оттегілі конверторлардың көп мөлшері өтуде. Оттегіні фурма арқылы жоғарыдан беру келесіерді қамтитын аралас үрлеудің алуан түрлері кең таралуда: - түпкі бөлікке кеуекті оттөзімді элементтер арқылы (LBE үрдісі) немесе түп футеревкасындағы каналдар, я болмаса құбырлар арқылы (LD = KG, LD = AB, LD = BC, TBM үрдістері) инертті газдарды үрлеу,көмірсутекті немесе бейтарап газдардан құралған сақиналы қаптамада оттегі мен инертті газдар қоспасы донналы фурмалар арқылы үрлеу (STB үрдісі) немесе қорғаныс қаптамасынсыз (LD = OTBүрдісі); - инертті газдарды сақиналы қаптамадағы ауа донналы фурмасы арқылы үрлеу (ВАР үрдісі); - көмірсутекті немесе бейтарап газдардан жасалған сақиналы қаптамадағы донналы фурмалар арқылы оттегі бөлігін үрлеу (LD = OB, LD = HC үрдістері); - түп арқылы әктасты қосымша үрлеу арқылы жоғарыда көрсетілген әдістер (мысалы, К – ВОР үрдісі, бұл кезде әктасты қорғанысты қаптамадағы оттегі ағындарымен енгізіледі). Аралас үрлеуді негізінен оттегілі үрлеу жоғарыдан жүргізілетін үрдіспен жұмыс жасаушы цехтарда қолданады. Тәжірибелер көрсеткендей, төменнен үрлеу салыстырмалы аздаған газ мөлшерінде (мысалы, 0,01 - 0,3м3 / (т · мин) аргон не азот) ваннаның араласуын қарқынын айтарлықтай жоғарылатады. Осының нәтижесінде тек жоғарыдан үрлеумен салыстырғанда келесідей артықшылықтарға қол жеткізіледі: - үрлеу ваннаны көп көпіршіктендірмей әлдеқайда тыныш өтеді; - металл мен қождың тотығуын төмендетеді; - жарамды металл шығыны артады, нәтижесінде темірдің қожбен бірге жоғалуы азаяды; - әктастың еруі жылдамдайды, яғни қождың түзілуі артады; - үрлеу кезінде тотығатын марганец мөлшері азаяды, қож түзгіштер шығынын азайта отырып, фосфорсыздану мен күкіртсіздену дәрежесі жоғарылайды. Бұл артықшылықтар фурманың болуы немесе түпте кеекту төсемелердің болуымен байланысты конвертордың пайдаланылуы мен құрылымының күрделенуін туғызады. Мұнымен қоса донналы үрлемелі конверторларды аралас үрлеумен ауыстыруға қатысты да жағдайлар кездескен. Бұл кезде қол жеткізілетін жалғыз артықшылық - кесекті әктасты қолдану арқылы жұмыс істеу кезінде негізгі қождың ертерек қалыптасуы жүзеге асады. 26. Болаттың мартендік өндірісі Мартендік үрдістің жүзеге асу бастамасын 1864 жылдың 8 сәуірінен бастауға болады, бұл кез Пьер Мартиннің француз зауыттарының бірінде алғашқы балқытуды жүргізген кезі болатын. Мартендік үрдіс регенераторлармен жабдықталған жалынды балқымалы пеш кеңістігінде жүргізіледі. Пешке жағылатын отын жалынымен біртіндеп балқитын шихта (шойын, скрап, металл сынықтары және өзге де құрамбөліктер) енгізіледі. Балқығаннан кейін ваннаға керекті температура мен құрамдағы металл алу үшін әр түрлі қоспалар қосылады, одан кейін дайын металды шөмішке салып құйып алады. Алғашқы мартендік пештердің өнімділігі жоғары болмаған. Алайда өзінің сапасы мен арзан болуына байланысты мартендік болат өте кең қолданыс тапқан. ХХ ғасырдың басында-ақ әлемдік болат өндірісінің жартысы мартендік пештерде өндіріле бастады. 27. Мартендік үрдістің жалпы сипаттамасы Мартендік пештерде шойын мен кез келген құрамдағы және пропорциядағы скрап көмегімен болат алуға болады. Шихта құрамына байланысты мартендік үрдісті бірнешетүрге бөліге болады: 1. Скрап-үрдіс – бұл шихтаның негізгі құрамдас бөлігі болат скрабы болып саналатын үрдіс. Скрап-үрдіс әдетте құрамында домна пеші жоқ және көп металл сынықтары кездесетін өндірістік ірі орталықтарда орналасқан металлургиялық және машина жасау зауыттарында қолданылады. Скраптан басқа шихтаға шойынның біршама мөлшерін қосады (25 - 45%). 2. Скрапты-кенді үрдіс – бұл қатты құраушылары скрап пен темір кені болып саналатын шихтаны мартендік пештерде өңдеу үрдісі. Шихтаның негізгі құраушысы (55 - 75%) – сұйық шойын. Металдық шихта 100% сұйық шойыннан тұрғанда, ал пешке қатты күйде тек темір кенін салатын болсақ үрдіс кенді деп аталады. Қож құрамы мен түбінің материалына байланысты мартендік үрдістер «негіздік» және «қышқылдық» болып бөлінеді. 28 Негізгі мартендік үрдіс Жалпы болаттың жартысынан көбісі негіздік мартендік пештерде өндіріледі. Пеш сыйымдылықтары 10-нан 900 т-ға дейін ауыспалы. Негіздік мартендік үрдістердің мұндайкең қолданыс табуы үрдістің жоғары технико-экономикалық көрсеткіштерімен (өнімділігі, отын шығыны, оттөзімділер шығыны) және оның әмбебаптылығымен түсіндіріледі. Негіздік мартендік пештерде кез келген құрамдағы және кез келген пропорциядағы скрап пен шойынды балқытуға болады, сонымен қатар осылайша кез келген құрамдағы сапалы болат алуға болады (электр пештерінде алынатын жоғары легирленген болаттар мен қорытпалардан басқа). Негіздік мартендік пештерде негізінен шойын мен скраптан тұратын шихтадан болат балқытылады. Қолданылатын металдық шихтаның құрамы шойын мен скрап құрамына және 1 т болат алу үшін жұмсалатын шойын мен скрап мөлшеріне байланысты болады. Темір мен өзге де қоспалардың түтінін есепке ала отырып, 1 т балқытылатын болат үшін шамамен 1100 кг металдық шихта шығындалады. Шойын мен скрап шығындарының арасындағы қатынас әр елде көптеген шарттарға тәуелді болады (металл өнеркәсібінің даму дәрежесі, тиемір кендері қорының болуы, шойын өндірісінің көлемі). Мысалы, 1 т мартендік болат үшін орта есеппен 575-585 кг шойын және 490-515 кг болат сынықтары жұмсалады. Алайда, жекелей зауыттар үшін бұл шамалар өзгешеліктерге ие, 1 т болат үшін домналы цехтары бар зауыттарда 300-400 кг шойын жұмсалады, ал толық металлургиялық циклдан тұратын зауыттар үшін бұл шама 550-700 кг-ға дейін болады. 29 Қышқылды мартендік үрдіс Қышқылды мартендік үрдіс деп «қышқылдық мартендік пештерде», яғни түбі қышқыл материалдардан жасалған пештерде болат балқыту үрдісі аталады. М. Партен 1864-1865 жылдары тұрғызылған алғашқы мартендік пештерде түпкі бөлік қышқылды болатын, оны кварц құмынан жасаған болатын. Мартендік үрдіс 1878 жылға дейін қышқылды үрдіс ретінде қолданылып келді. Пеш астында таза жоғары кремнийлі құм, ұнтақталған кварцит немесе кварцитпен бірге ақырғы қышқыл қож қоспалары қайнатылады. Қышқыл пештің түбі ванна түбінде жүретін үрдістер үшін белсенді рөл атқарады, қышқыл болаттың жоғары сапасы белгілі дәрежеде металдық ваннамен қышқыл түп материалының әрекеттесу дәрежесімен анықталады. Сондықтан қышқыл пеш күйіне аса назар аударылады. Қышқыл түптің дайындалуы мен оны баптау өте күрделі және жауапкершілікті талап етеді, оны әдетті жоғары мамандандырылған шеберлер жүзеге асырады. Қышқыл пешті толтыру ұзақтығы жоғары, және түптің күйіне байланысты 1,5-2,5 сағатты құрайды. Негіздік мартендік скрап-үрдістегі секілді пешке салынатын шойын мен скрап қатынасы металдағы берілген көміртегі мөлшеріне тәуелді. Әдетте, балқығанннан кейін металда талап етілетін дайын болаттан0,5 - 0,6%-ға көп мөлшерде көміртегі болатындай етіп жүргізіледі. Негіздік мартендік үрдіспен салыстырғанда скрап-кенді үрдіске темір кені де қосылады, ал қышқылдық үрдісте қож түзілуіне қажетті мөлшер аз болады. Металл қождың жеткіліксіз қабатымен жабылуы мүмкін және осының әсерінен қарқынды тотығып, газбен қанығады. Мұндай құбылыстардың алдын алу үшін кейде түпке шихтаны құйғанға дейін ақырғы қышқыл қож, шамотты бой және кварц құмы – металл массасының 2 - 4% мөлшерінде салынады. Дуплекс-үрдіспен жұмыс жасау кезінде ваннаның қайнай бастауын жылдамдату үшін пешке темір кенінің біраз мөлшерін енгізеді. 30. Екі ванналы болат балқыту пештері Екі ванналы пеш құрылысына алғашқы патент осыдан 70 жыл бұрын берілген болатын көп түпті пеш құрылысына КСРО-да патенттер мен төлқұжаттар қатары соңғы жылдары беріліп келеді. Алайда, ұсынылған жобалардың бірі де жүзеге асқан емес. Жұмысқа қабілетті заманауи екі ванналаы пештерді жасау үшін мартендік үрдіс оттегімен қарқынды ету әдісін, қазіргі технологияларды өңдеу, балқытуды автоматты бақылау мен басқру әдістерін, ваннаға оттегі беру үшін фурма құрылымын қайта өңдеуді, сонымен қатар отын-оттегілі жандырғыш құрылымын қайта өңдеуді жақсы игеруді талап етеді. Екі ванналаы пештердің кең таралауын үдеткен қазіргі жағдай болып ваннаны оттегімен үрлеу арқылы жұмыс жасайтын мартендік пештердің регенераторлық төсемелерін жөндеу мен қызмет көрсету күрделілігі табылады. Ваннаны үрлеуді арттыруға байланысты балқыту пештерінің саны да артады, төсеме мен төсеме астындағы кеңістікті жиі-жиі тазалап отыру қажеттілігін туғызады, бұл пешке қызмет көрсетуді күрделендіріп, қымбаттадаы, және жөндеуге жұмсалатын ең бек шығынын арттырады. Төсемелерді тазарту әдістері жетілмеген және тиімсіз болғандықтан әр жөндеген сайын барлық дерлік пештердің регенератор төсемелерінің ұяшықтары кеңейіп кетеді (120 х 120-дан 460 х 220мм-ге дейін). Алайда, ұяшықтардың қиылысы үлкен болған сайын регенераторлардың қолданылу тиімділігі де азаяды, ауаның қызу температурасы да төмендейді. Нәтижесінде, мұндай тиімділігі төмен регенераторлардың құрылуына, жөндеуі мен қызмет көрсетуге кететін шығындардың отын үнемдеу жағынан тиімсіз екендігі белгілі болады. Мұнымен қоса, үрлеуді оттегімен байыту дәрежесінің артуымен шығатын газдардың температурасы артады, және сәйкесінше регенератор төсемелерінің жоғарғы жағының температурасы артады, бұл да олардың пайдаланылу шарттарын күрделендіреді. Мартендік пештерде регенераторлардың болуы олардың дайындағу шығындалатын оттөзімділердің көп мөлшерін білдіреді, бірақ олардың қондырылуы мен жөнделуі үлкен мөлшерде физикалық еңбекті талап етеді. Осыған байланысты регенераторлардан бас тарту тек оттөзімділер шығынын төмендетуге ғана емес, агрегат жөнделуіне шығындалатын еңбек күшінің де төмендетуге де бағытталған. Екі ванналы пештер (2-сурет) екі ваннадан, екі басшадан, екі тік каналдан, екі қож түсірушіден және борова жүйесі мен алынбалы клапандардан тұратын агрегат болып саналады. Екі ванналы пеш жұмысы мынада: бір ваннада металды оттегімен үрлеу жүрып жатқанда, екіншісінде қатты шихта бірінші ваннадан шығып жатқан газдар жылуы әсерінен қызады (2-сурет, стрелкалармен газдардың бағыты көрсетілген). Пеш өнімділігі мұндай жұмыс әдісінде артады. Ваннаны қарқынды үрлеу арқылы жұмыс жасайтын мартендік пештерде оттегімен сұйық шойынды құйып алғаннан кейінгі балқытуды шартты түрде екі бөлікке бөлуге болады: а) «қатты» - түпті қарап шығу, металл сынықтарын, кен, әктас құю және оларды қыздыру, б) «сұйық» - шойын құю, ваннаны үрлеу және олардың қоспаларының тотығуы, қышқылсыздану, легирлеу және шығару. 31. Электпештерінде болат өндіру, электрпештері жөніндегі жалпы мағлұматтар, болат балқытуға арналған электр пештерінің жіктелуі Электрпештерінде болат балқыту(жалпы мағлұматтар) – бұл электр энергиясын жылу энергиясына айналдырып, үрдістің қажетті температурасына қол жеткізу мен оны ұстап тұру үшін қолданылатын болат өндіру үрдістері.
|
|
|
|
|
|
|
|
Жіктелуі
Электрпештері доғалы, индукциялы, графитті қарсылық элементтері бар пештер болып бөлінеді.
32. Болат балқытуға арналған доғалы пештер, үрдіс технологиясы мен әртектілігі
Доғалы пештерде болат балқыту
Қағидалары
а) Доғалы пештерде электр энергиясы жылуға айналдырылады, бұл жылу тікелей жылу өткізу және сәулелену арқылы металл мен қожға беріледі.
б) Доғаның жоғарғы температурасы және электр энергиясының жақсы реттелуі балқыту режимінің кез келген температурасын қалыптастурыға мүмкіндік береді.
в) Пештегі таңдалған қож құрамына байланысты тотықтыру, немесе тотықсықдану үрдістерін де жүргізуге болады.
г) Жанғыш газдардың зиянды әсері болмайды.
д) Тотығу үрдістерінің жылдамдығын арттыру үшін оттегілі үрлеуді қолдана алу мүмкіндігі.
е) Қождың ауысуы оңай жүзеге асады.
ж) Легирлеуші элементтер жақсы қолданылады.
з) Жүктеу тікелей қатты шихта арқылы жүзеге асады.
Балқыту электр пештері басқа балқыту агрегаттарымен салыстырғанда бірқатар артықшылықтарға ие:
а) ток параметрлерін өзгерте отырып, жылулық үрдісті реттеу жеңіл;
б) металдың жоғарғы температурасын алуға болады;
в) қышқылдық, тотықсыздандырғыш, бейтарап атмосфера мен вакуум құру мүмкіндігі, бұл аз мөлшерде бейметалл қоспалар түзе отырып, металды қышқылсыздандыруға мүмкіндік береді.
Электрпештер құрылымдық, жоғары легирленген, аспаптық, арнайы қорытпалар мен болаттар алу үшін қолданылады.
Доғалы және индукциялық электр пештері бар.
1-суретте доғалы пеш жұмысның қағидасын көрсететін сызба берілген. Доғалы пеш үш фазалы ауыспалы токпен қоректенеді. Электр тогы сымдармен 7 өтетін электр ұстағыштарда 8 бекітілген графиттелген массадан жасалған үш цилиндрлік электродтан тұрады. Электрод пен металдық шихта 3 арасында электр доғасы пайда болады. Пеш корпусы цилиндр формасына ие. Сыртынан ол берік болат қаптамамен 4 қапталған, ішкі жағынан негіздік немесе қышқылды кірпішпен 1 футеревкаланған. Балқыту кеңістігі қабырғамен 5, түппен 12 және енгізбемен 6 шектелген. Алынбалы енгізбе 6 электродтарға арналған саңылаудан тұрады. Корпус қабырғасында балқыту кезінде қабықшамен жабылып тұратын жұмысшы терезе 10 бар. Дайын болатты құйылмалы желобты 2 құйып алу саңылауы арқылы жүзеге асырады. Пеш секторларға тірелген және жұмысшы терезесін немесе желобты еңкейтуге арналған жетекке 11 ие. Пешті жүктеу енгізбенің ашық күйінде жүзеге асады.
Пеш сыйымдылықтары 0,5-400 тоннаға дейін болады. Металлургиялық цехтарда негіздік футеревкалау қолданылады, ал құймалы цехтарда – қышқылдық.
Негіздік доғалы пеште балқытудың екі түрі жүргізіледі:
а) легирленген қалдықтардан дайындалған шихтада (қайта балқыту әдісімен), б) көміртекті шихтада(қоспаларды тотықтыру арқылы).
Легирленген қалдықтардан жасалған шихтадабалқыту қоспаларды тотықтырусыз жүзеге асырылады. Шихтаны балқытқаннан кейін металдан күкіртті жояды, керек болса, көміртексіздендіреді және металды берілген химиялық құрамға дейін жеткізеді. Қожға ұнтақталған ферросилиций, алюминий, ұнталған кокс сала отырып, дуффузиялық қышқылсыздандыру жүргізіледі. Солайша машина жасау зауыттарының қалдықтарынан легирленген болаттар балқытылады.
Көміртекті шихтада балқытуқұрылымдық болаттар өндірісі үшін қолданылады. Пешке шихта салынады: болат сынықтары, қайта өнделетін шойын, электродты бой немесе кокс, кейде металды күкіртсіздендіру үшін әк те қосылады. Электродтарды салып, ток қосылады. Шихта электродтар әсерінен балқиды, металл пеш түбінде жинала бастайды. Ауадағы көміртегімен, шихта тотықтарымен және отқабыршықтармен балқуы кезінде темір, кремний, фосфор, марганец, кейде көміртегі де тотығады. Әктен алынған кальций оксиді мен темір оксидтері негізгі темірлі қож түзеді, ол металдан фосфорды жоюға қабілетті. 1500 - 1540○C-қа дейін қыздырған соң кен мен әк салынады, металдың «қайнау» режимі орын алады, көміртегінің одан әрі тотығуы жүреді. Қайнау тоқтағаннан кейін қожды жояды. Одан кейін күкіртті жоюға және берілген құрамдағы металды қышқылсыздандыруға кіріседі. Қышқылсыздандыру шөктіру және диффузиялық әдіспен жүзеге асады. Металдың химиялық құрамын анықтау үшін сынама алынады және керек болған кезде пешке берілген химиялық құрамдағы металл алу үшін ферроқорытпалар салынады. Одан кейін алюминиймен және силикокальциймен ақырғы қышқылсыздандыру жүргізіледі, болатты шөмішке шығарып алады.
Доғалы пештерде легирленген болат балқыту кезінде болатқа ферроқорытпалар түрінде легирлеуші элементтер қосылады.
Доғалы пештерде жоғары сапалы көміртекті болаттар балқытылады – құрылымдық, аспаптық, ыстыққа төзімді және ыстыққа берік.
Технология
Шихта – балқыту әдісіне байланысты легирленген немесе легирленбеген скрап болып саналады. Егер балқыту тотықтыру режимінсіз жүргізілсе, фосфор мөлшері төмен болуы керек.
Салқындату – шығару алдында температураны түзету үшін скрап көмегімен жүзеге асырылады.
Балқытудағы тотықтыру кезеңі
Темір қоспаларын С, Si, Mn, P, S жою. Газсыздандыру мен бейметалл қоспалардың түзілуі. Бұл үрдістерге балқыманың энергетикалық қайнауы жағымды әсер етеді. Бұл үшін ваннада көміртегі мөлшерінің көп болуы, кен мен әкті шөктіру, сұйық ағынды тотықтырғыш қождың түзілуі, температураның жылдам көтерілуі, балқыманы оттегімен үрлеу жүргізілуі керек.
Балқыманы тотықсыздандыру кезеңі
Мақсаты – оттегі мен күкірт мөлшерін азайту. Тотықтырғыш қож жүктеу, қайтара қышқылсыздандыру, әк пен шпаттан тұратын тотықсыздандырғыш қож енгізу арқылы жүзеге асады. Тотықсыздандырғыш қождан қосымша түйіршіктелген FeSi, CaSi немесе А1 қосылғанда ақ қож, ал кокс косар болсақ – карбидті қож түзіледі. Металда еріген тотықтар мен күкірт қожға қосылады, мұнда тотықсызданып байланысады. Тотықсыздану кезеңінің созылуымен қождағы сутегінің мөлшері ұлғаяды.
Легирлеу
Оттегігі ұқсастығы аз элементтер пешке салынады, ал оттегіге жақындығы жоғарылары –металл қышқылсызданғаннан кейін (мысалы, Si, Al, Ti, Zr, Mo) салынады. Көміртегі тотықтырғыш қож жүктелгеннен кейін қосылады.
Қышқылсыздану
Балқытудың тотықтыру кезеңінен кейінгі қайтара қышқылсыздану, тотықсықдану кезеңіндегі диффузиялық қышқылсыздандыру, ақырғы қышқылсыздандыру.
Үрдіс нұсқалары
Балқытудың бастапқы кезеңі
Әлдеқайда энергетикалық тотығу балқыту кезінде немесе тікелей балқытудан соң жүзеге асады. Құрам легирлеуші төсемелер арқылы түзетіледі.
Қайта балқыту
Тікелей балқыту немесе қысқаша қайнау кезеңінен кейін тотықсыздандыру шартында легирленген скраптан металды максимал бөліп алу жүзеге асады.
Дуплекс - үрдіс
Балқыту пештерінің бірінде балқыту, тотығу, жекелей не жалпы фосфорсыздану және әдетте қышқылсыздану жүргізіледі. Одан кейін металды доғалы пештерде қайта балқытады, мұнда балқыған легирленген скрап болады және ол осында нақты балқып дайын болады.
Аралас үрдіс
Әр түрлі пештерде металлургиялық өңделген және балқытылған қорытпаларды араластырамыз. Араластыру шөміште не пештердің бірінде жүргізіледі.
Доғалы пештердегі қышқыл үрдіс
Болаттық қалыпталған құймалар және қайта балқыту үшін айтарлықтай маңызды болып саналады. Қышқыл футеревка және қышқыл қож (60%-ға дейін SiO2). Кенді салу балқыманың қайнауына алып келеді. Одан кейін қышқылсыздандыру, легирлеу және шығару.
Қара қожбен жүретін үрдіс
Сыйымдылығы жоғары доғалы пештерде жүргізіледі (500т-ға дейін). Ақырғы тотықсыздандырусыз балқыту мен тотықтыра өңдеу жатады. Болаттың ауқымды сұрыптарын өндіруде қолданылады.
33. Индукциялық балқыту пештері, қарсылық пештері
Индукциялық араластыру
Балқытудың тотықсыздандыру кезеңінде күкіртті жою және қышқылсыздандыру үрдістерін жеделдету үшін электромагниттік аумақ әсерінен балқыманың қозғалысы орнатылады. Осы мақсатпен ванна астында индуктор орнатылады. Тотықсыздану кезеңіндегі уақытты үнемдеу 30 минутқа дейін жетеді. Балқыма бойымен легирлеуші элементтердің жылдам әрі біртекті таралуына қол жеткізіледі. Температураның айшықталуы тотықтыру кезеңінен кейінгі қождың жүктелуін жеңілдетеді.
Қуаттылығы жоғары УВМ пештері(ультра жоғары қуатты) – бұл өте күшті қуат берілетін пештер. Қуаттылығы бойынша доғалы пештердің жіктелуі (2-сурет), кВт / т. Қуаттылығы жоғары пештерде балқыту үрдісі 1-1,5 сағатты құрайды.
Болат өндірудің электрометаллургиялық әдістерінің ішінде басым орын алатыны болатты негіздік доғалы пештерде балқыту болып саналады. Бұл жоғары сапалы болаттарды балқытудың ең жақсы әдісі болып саналады. Пеш сыйымдылығын арттыра отырып, ауқымды қолданыстағы болат өндірісіндегі мартендік үрдіске бәсеке бола алады. Электроболаттардың әлемдік өндірісі тұрақты өсіп келеді, бірақ оның жалпы болат өндірісіндегі үлесі баяу ұлғаюда.
Индукциялық тигельді балқыту пештеріндеәлдеқайда сапалы, коррозияға төзімді, ыстыққа берік және басқа да болаттар мен қорытпалар балқытылады.
Сыйымдылық ондаған килограммнан 30 тоннаға дейін болады. Индукциялық тигельдік пештің сұлбасы 3-суретте берілген.
Пеш суды салқындататын индуктордан 3, оның ішінде орналасатын металдық шихтасы бар тигельден 4 тұрады, индуктор арқылы жоғары жиіліктегі генератордан бір фазалы жоғары жиіліктегі ауыспалы ток өтеді (500 - 2000Гц).
Ток жіберілген кезде тигельде орналасқан металдағы 1 индуктор арқылы қуатты құйынды токтар индукцияланады, бұл металдың қызуы мен оның балқуын қамтамасыз етеді. Жылу жоғалтуды азайту үшін пеште алынбалы енгізбе 2 болады.
Тигель қышқыл не негіздік оттөзімділерден дайындалады. Балқыманы шығару үшін пешті құймалы желобқа қарай еңкейтіледі.
Индуктордың электромагниттік аумағы әсерінен балқыту кезінде сұйық металдың қарқынды циркуляциясы пайда болады, бұл химиялық реакциялардың жеделдеуіне, химиялық құрамы жағынан біртекті метал алуға, бейметал қоспалардың тез қалқып шығуына, температуаның анықталуына алып келеді.
Индукциялық пештерде болат балқытады және қайта балқыту әдісімен легирленген қалдықтардан, немесе таза шихталық металдан және ферроқорытпалар қоса отырып скраптан қорытпалар балқытылады.
Шихта балқытылғаннан кейін металл бетіне металдың жылулық жоғалымдарын төмендету және легирлеуші элементтердің түтінін азайту үшін, олардың газбен қанығуынан қорғану үшін қож қоспасы енгізіледі.
Қышқыл пештерде балқытудан кейін және балқыту қождарын жою үшін шыныдан жасалған қож құйылады (SiO2). Ақырғы қышқылсыздану үшін металды шөмішке шығару үшін оған ферросилиций, ферромарганец және алюминий енгізіледі.
Негіздік пештерде қышқылсыздандыру ұнтақ тәрізді әктен, кокстан, ферросилицийден, ферромарганецтен және алюминийден жасалған қоспалар салынады.
Негіздік пештерде марганец, титан, никель, алюминий мөлшері жоғары болатын жоғары сапалы легирленген болаттар, ал қышқыл футеревкалы пештерде – өзге элементтермен легирленген құрылымдық болаттар балқытылады.
Пештерде аз мөлшерде көміртегісі бар және көміртексіз қорытпалар алынады, себебі көміртектендіру ортасы болмайды.
Вакуумдық индукциялық балқыту кезінде индуктор, тигель, шихта мөлшерлегіші мен металл қалыптар вакуумдық қалыптарға орналастырылады. Бұл кезде газ, бейметалл қоспаларының аз мөлшері бар қорытпалар мен кез келген элементпен легирленген қорытпалар алынады.
Графитті қыздырғыштары бар қарсылық пештері
Қағидасы
а) Ауыспалы ток жүретін графитті стерженьде қорытпаға сәулелену арқылы беріле отырып электр энергиясы жылу жнергиясына айналдырылады (4-сурет).
б) Тотықсыздандырғыш атмосферасында металдың жедел еруі жүреді.
в) Осының нәтижесінде металдың түтінмен жоғалуы азаяды.
г) Пештер өткір және аспаптық болаттар, таттанбайтын және ыстыққа төзімді болаттар, сонымен қатар магниттік болатта балқыту үшін қолданылады. Одан артық қайта балқыту жүзеге асады, балқытуды қожбен бірге жүргізу мүмкін емес.
34. Ферроқорытпалардың жіктелуі мен тағайындалуы
Қазіргі заманғы ферроқорытпа электр-металлургиясы кендерден, концентраттардан және техникалық таза оксидтерден металдарды біріншілік шығаруға маманданған. Ферроқорытпаларға лигатуралар мен модификаторлар жатады, олар тағайындалу бойынша ажыратылады.
Лигатураны кендер мен концентраттардан оның компоненттерінің құраушыларын балқыту немесе оларды тотықсыздау арқылы алады. Лигатураның балқу температурасы оның құрамына кіретін кез келген металдікінен төмен, қоспалау кезінде тезірек ериді және элементтердің қалдықтарын азайтады.
Модификатор – бұл аз мөлшері онымен өңделген металдың немесе қорытпаның құрылымы мен қасиеттерін айтарлықтай өзгертетін зат. Бұл эффект түрлендіру деп аталады. Академик П.А. Ребиндер (1898-1972 жж.) классификациясы бойынша модификаторлар екі топқа бөлінеді: бірінші текті – беттік-белсенді заттар (ББЗ) және екінші текті - инокуляторлар.
Бірінші текті модификаторлар кристалданған металл балқытпаларының ұрықтарында адсорбцияланады, олардың өсуін тежейді және құрылымды ұсақтайды.
Екінші текті модификаторлар балқытпада кристалдану орталықтарының түзілуін жеңілдетеді және конструкциялық болаттардың және қорытпалардың микроқұрылымын ұсақтайды.
Металдар екі негізгі топқа бөлінеді: қара және түсті. Бірінші топқа темір жатады, мұнда ол негізгі металл болып табылады – шойын, химиялық құрамы әртүрлі болаттар және ферроқорытпалар. Екінші топ келесі топшаларға бөлінеді: 1) жеңіл (Al, Ba, Be, K, Ca, Li, Mg, Na, Rb, Si, Sr, Ti, Cs); 2) сирек (V, W, Ga, Hf, Y, Ge, Mo, Re, РЗМ, Se, Ta, Te, Zr); 3) ауыр (As, Bi, Cd, Co, Cu, C, Fe, Hg, Ni, Sb, Pb); 4) асыл (Au, Ag, Ir, Os, Rt, Rd, Ru); 5) радиоактивті (Pu, Po, Ra, Np, U).
Ферроқорытпаларда қара және түсті металдар (Fe, Mn, Si, Cr, Ca, Al, Be, РЗМ және басқалары) болуы мүмкін. Ферроқорытпалар ретінде S, P, Cu, Sn, Sb және басқа элементтер болады.
Ферроқорытпалар үлкен қорытпаларға және өндірістің жалпы көлемінде негізгі орын алатын және аз таралған кіші қорытпаларға бөлінеді. Үлкен ферроқорытпалардың тобы 1-топ (немесе массалық қолданыстағы): 1) кремний қорытпалары (FeSi, барлық маркасы, кристалды Si); 2) марганецті ферроқорытпалар (жоғары; орта; және төмен көміртекті FeMn; тауарлық және қайта қорыту SiMn; металдық, силикотермиялық және электротермиялық марганец). 3) хромды ферроқорытпалар (жоғары; орта; және төмен көміртекті FeCr; тауарлық және қайта қорыту FeSiCr; металдық хром; азотталған феррохром).
Кіші ферроқорытпалардың 2-тобы: 1) FeW және вольфраммен қорытпалар (W - Cr, W - Ni); 2) FeMo және Мо-мен лигатуралар Mo (Mo - Al - Ti, Mo - Al - Ni, Mo - Al - Cr - Fe); 3) FeV және ванадиймен қорытпалар (Fe - Si - V, Fe - Mn - V, V - Ca - Si); 4) сілтілі жер металдар қорытпалары СЖМ (SiCa, SiBa, SiMg, Si кешенді қорытпалары Fe - Si - Mg - Ca, Si - Ca - Ba - Fe, Si - Ba - Fe, Si - Ba - Sr және басқалары; 5) FeNb және Ni - Nb, Nb - Ta - Fe, Nb - Ta - Mn - Al - Si - Ti, Nb - Ta – Al жүйелерімен қорытпалары; 6) FeTi және Fe - Si - Ti, Ti - Cr - Al, Ti - Cr - Al - Fe, Ti – Ni жүйелерімен қорытпалар; 7) FeB, бормен лигатуралар (Ni - B, Cr - B, грейнал B - Si - Al - Ti - Zr; 8) алюминиймен қорытпалар (SiAl, FeAl, FeSiAl, Fe - Al - Mn - Si, Fe - Mn – Al жүйелерінің қорытпалары); 9) СКМ жүйелерімен қорытпалар РЗМ - Si, Ge - Si - Fe, РЗМ - Al - Si, РЗМ - Ni - Si; 10) FeSiZr, FeAlZr; 11) FeNi, FeCo.
Ферроқорытпалардың негізгі компоненттері жетекші элементтер деп аталады. Металға өту және тотықсыздану немесе жетекші элементті алу деңгейі технологияның пайдалылығын және техника-экономикалық тиімділігін анықтайды. Конструкциясы мен қуаты әртүрлі пештерде шығу тегі мен құрамы әртүрлі шикізаттардан ферроқорытпаларды өндіру көрсеткіштерін талдау және салыстыру ферроқорытпалар мөлшерін базалық тоннаға қайта есептеу жағдайында жүргізіледі.
Базалық тонна – бұл жетекші элементтің немесе оның қосылысының белгілі бір мөлшері қатаң сақталған кеннің, ферроқорытпаның, концентраттың бір тоннасы.
Мысалы, ФС45 маркілі FeSi құрамында 41-47% Si болуы мүмкін, ал базалық тоннаға 45% Si-мен қорытпаның бір тоннасы қабылданады.
Ферроқорытпалардың негізгі бөлігі болат балқыту өндірісінде болаттарды қоспалау және қышқылсыздандыру үшін, сонымен қатар шойын мен қорытпаларды қоспалау және түрлендіру үшін қолданылады.
Көптеген ферроқорытпаларда темірдің мөлшері айтарлықтай жоғары болады. Өйткені бастапқы шикізатта жетекші элементпен бірге темір оксидтері болады, олар көптеген ферроқорытпалар үшін зиянды қоспа болып табылады. Сонымен қатар темір жетекші элементті еріте отырып, соңғысының белсенділігін және ферроқорытпаның балқу температурасын төмендетеді, бірқатар ферроқорытпалардың тығыздығын өсіреді және болаттар мен қорытпаларды қышқылсыздандыруда және қоспалауда пайдалануды арттырады.
35. Ферроқорытпа үрдістерінің әр түрлі типтерінің ерекшеліктері
Ферроқорытпалар өндірісінде кез келген элементтерді тотықсыздандыруға қабілетті көміртегі кең қолданыс тапқан. Жоғары температураларда металдарды көміртекпен тотықсыздандыру көміртекті термиялық тотықсыздандыру деген атау алған. Жалпы түрде реакция келесідей болады:
2 / у МехОу + 2С = 2х / у Ме + 2СО - Q,
2 / у МехОу + (2 + 2х / z)С = 2х / уz МеzCy + 2CO - Qc.
Оттектің тотықсыздандыру реакциясының өнімдерінің бірі көміртегінің монооксиді болып табылады, оны реакция аймағынан жою шихтадан металға жетекші элемент шығуының жоғары дәрежесін қамтамасыз етеді.
Көміртегінің артықшылықтары: оның бағасы жоғары емес, бұл ретте шығу тегі әртүрлі көміртекті материалдарды қолдануға болады. Көміртегінің кемшіліктері: 1) оксидтерді тотықсыздандыруда карбидтер түзіледі, сондықтан Si аз концентрациясында қорытпаларда көміртегі мөлшері жоғары болады, 2) оксидтердің тотықсыздандыру реакциялары көп мөлшерде қуат жұмсаумен жүреді, сондықтан қуаты үлкен пештер қажет.
Металл тотықтарын силикотермиялық тотықсыздандыру мына реакция бойынша жүреді:
2 / у МехОу + Si = 2x / y Me + SiO2 + QSi.
Тотықтарды кремниймен тотықсыздандыру кешенді қайта қорытылған ферроқорытпаларды (SiMn, FeSi, FeSiCr және басқалары) пайдаланумен жүреді, бұлар кремнеземді көміртекпен тотықсыздандыру арқылы алынады.
Кремний оттегімен химиялық жағынан өте ұқсас, бұл қуаты үлкен емес электрпештерде (2700-7000 кВА) әртүрлі оксидтердің (Cr2O3, MnO, MoO3, WO3 және басқалары) тотықсыздандырғышы қызмет атқаруы мүмкін.
Кремний тотықсыздандырғыштың келесідей кемшіліктері бар: 1) кремнеземнің түзілуі әсерінен қож мөлшері артады, бұл ретте SiO2 белсенділігі артып, жетекші элементтің төменгі оксидтерінің берік силикаттары пайда болады, 2) ферроқорытпаларды қорытуда кремний металдармен идеалды ерітінді қасиеттерінен кері ауытқуларға ие ерітінділер түзеді және кремнийдің концентрациясы төмен қорытпаларды алуды қиындатады, 3) құнының жоғары болуы.
Металдардың тотықтарын алюмотермиялық тотықсыздандыру мына реакция бойынша жүреді:
2 / у МехОу + 4 / 3Al = 2x / y Me + 2 / 3Al2O3 + QAl,
және Гибс энергиясының айтарлықтай өзгеруімен жүреді, бұл ретте үрдіс жетекші элементтің жоғары шығымымен өтеді. Алюмотермиялық үрдістің ерекшелігі: жылудың үлкен мөлшерінің бөлінуі және жылуды алусыз, пеш сыртында үрдістерді жүргізу мүмкіндігі бар. Бұл кезде кристалданудың басталуынан жоғары температурамен қож бен металл алуды, металл мен қождың жақсы бөлінуін, үрдістің жылдамдығын қамтамасыз ететін өте жоғары темеператураларға (2400-2800 К) дейін жетеді.
Тотықсыздандырудың экзотермиялық реакциялары нәтижесінде бөлінетін Qэкз жылу мөлшеріне байланысты алюмотермиялық үрдістерді 3 топқа бөлуге болады:
1) өздігінен жүретін (Qэкз ≥ Qр + Qп), мұндағы Qэкз – тотықсыздандырғыштың жылулық эффектісі, Qр – металл мөлшері;
2) Qп жылулық шығымдардың тиісті компенсациясы, (Qэкз - Qр < Qп);
3) Q сырттан керекті жылу мөлшерін енгізу, (Qэкз < Qр).
Алюмотермиялық (пештен тыс) үрдісті екі тәсілмен жүргізуге болады: шихтаның жоғарғы немесе төменгі тұтандырғышымен көрікте (шахтада, шөміште).
Жоғарғы тұтандырғышпен көрікте (шахтада) немесе шөміште пештен тыс балқыту – балқыту үрдісі көріктің жоғарғы бөлігінде басталады, балқытпа айнасы астындағы шихта қатты және ұнтақ тәріздес. Жоғарғы тұтандырғышпен балқыту кезінде үрдіс қарқындылығын реттеуге болмайды, себебі бұл балқытпа шығарылуына әкелуі мүмкін. Металл тамшысының пайда болуы шихтаның барлық биіктігінде оның жанама шөгуімен жүреді, бұл қож бен металл королькаларының жоғалуымен байланысты.
Төменгі тұтандырғышпен пештен тыс балқыту көрік табанында балқытпа түзіліп, үрдістің басталуымен сипатталады. Шихта қажетті қарқындылықпен балқытпаға беріледі. Металл бірден көріктің төмеңгі бөлігінде түзіледі және королькамен металдың жоғалуы 2-5%-ға төмендейді. Жылу жоғалымы төмендейді, себебі балқытпа шихта қабатымен жабылған. Балқытуды тек блокқа қана емес, қожды немесе қож бен металды шығарумен жүргізуге болады, бұл көрікті келесі балқыту үшін бірден пайдалануға мүмкіндік береді. Алюмотермиялық үрдістің артықшылықтары: 1) беріктігі жоғары металдар оксидтерін шихтадан қажетті мөлшерде шығара отырып, оларды тотықсыздандыру, өйткені алюминий оттегіге өте ұқсас, 2) түсті металдардың қоспаларымен және көміртегі концентрациясымен техникалық таза металдар және қорытпалар алу және оксидтерді тотықсыздандыру, 3) үрдісті жабдықтау қарапайымдылығы, аз қаржылық шығындар, 4) металл мен қожды шығара отырып, көлбеу көрікте үрдісті жүргізу, 5) синтетикалық қождар, сонымен қатар жоғары глиноземді цементтің клинкерін алу үшін жоғары глиноземді қождарды пайдалану, 6) шихтада металдар мен қорытпалардың металл қалдықтарының үлкен мөлшерін қолдану мүмкіндігі, 7) кальций мен магнийдің қымбат ұнтақтарына қарағанда алюминий ұнтағын алу, сақтау жәіне пайдалану қарапайымдылығы.
Үрдіс кемшіліктері: 1) біріншілік алюминий тапшылығы және бағасының жоғары болуы, 2) королькалар түрінде тотықсызданған металдың жоғалуына алып келетін, жоғары тұтқырлықты жоғары глиноземді қож түзілуі, 3) жетекші элементтердің төмеңгі оксидтердің түзілуі, оксидтердің тотықсыздану және шихтадан металдардың шығуы төмендейді.
36. Ферроқорытпа үрдістерінің түрлеріФерроқорытпа үрдісінің түрлері
Қолданылған агрегат түріне байланысты ферроқорытпаларды алу. Қорытпалардың жіктелуі
Қазіргі уақытта ферроқорытпалар өндірудің 4 негізгі тәсілдері бар: 1) электротермиялық, 2) металлотермиялық, 3) домналық 4) электролиттік.
Электротермиялық тәсіл металдар мен қорытпаларды тотықсыздандыру, балқыту, қыздыру және оларды тазарту үшін электрлік энергияны жылулық энергияға түрлендіруге мүмкіндік беретін энергетикалық қондырғыларда жүзеге асырылады. Өнімдерді қолдану облыстары: 1) ферроқорытпалардың электрометаллургиясы, 2) болат электрометаллургиясы, 3) карбидтерді алу (Si, B, Ca және басқалары), 4) оксидтерді электрлік балқыту (ақ электрокорунд, кварцты құм, балқытылған магнезит және т.б.), 5) айналдыру және конденсация (фосфор, күкіртсутек CS және т.б.), 6) электрлік разряд көмегімен газды фазада заттар синтезі және крекингі (озон, азот оксидтері және басқалары).
Металлотермиялық тәсіл оксидтерді алюминиймен, кремниймен, кальциймен тотықсыздандыру химиялық реакциялар жылуын пайдалануға негізделген (алюминотермия, силикотермия, кальциетермия).
Металлотермиялық тәсілмен балқытылған ферроқорытпалар, қорытпалар және металдар Cr, Fe, Ni және басқа металдар негізінде темірдің төмен мөлшерімен сипатталады.
Металлотермиялық тәсілмен блокқа пештен тыс балқыту, қож бен металды шығарып балқыту және т.б. алынады. Бұл тәсіл өнеркәсіптің отқа берік, болат балқыту, құрылыс салаларында ысырма қождарды пайдалануға мүмкіндік береді.
Электролиттік тәсіл сулы ерітінділердің немесе ерітілген тұздардың электролизіне негізделген және аса таза металдарды алу үшін қолданылады.
Домналық үрдісте көміртегі мөлшері жоғары (FeMn, FeCr, FeSi және басқалары) ферроқорытпалар (Mn, Si, Cr) алынады.
Домендік пештерде ферроқорытпаларды қорыту кокстің жоғары шығынынан көміртекпен қаныққан, олар күкіртпен және фосформен ластанған. Бұл тәсілмен өндіру көлемі қысқартылған. Мысалға, домналық пештерде FeSi өндіру тоқтатылған.
Ферроқорытпалық үрдістер үздіксіз және периодты болып бөлінеді. Үздіксіз үрдістер жабық мойынды кен тотықсыздандыру пештерінде шихтаны үздіксіз жүктеумен, периодты түрде қож бен ферроқорытпа шығарумен сипатталады. Шихта пеште барлық уақытта белгілі бір деңгейде орналасады. Электродтар әрқашан шихтаға батырылған, ал металл мен қожды шығару периодты немесе үзіліссіз жүреді. Периодты үрдіспен ферроқорытпалар өндірісінде балқымаға батырылған барлық шихта балқытылады және сосын қорытпа мен қож шығару жүргізіледі. Периодты үрдіске блокқа балқыту, қорытпаны сарқып алу, балқытпаларды араластыру тәсілдері жатады. Периодты үрдіс арқылы оттекті конвертерде үрлеумен, қатты және сұйық күйде вакуумдық өңдеумен ферроқорытпаларды алу, азотталған қорытпаларды алу және т.б. жүзеге асырылады.
Түзілген қождың меншікті мөлшеріне байланысты ферроқорытпаларды өндіру үрдістерін қожды және қожсыз деп бөлуге болады. Түзілген қож мөлшері пештен шығарылған қож бен қорытпа массасының арақатынасымен (қож еселігі) сипатталады. Қожсыз үрдісте қож еселігі 0,05-0,1 аралығында болады. Қожсыз үрдістің мысалы – бұл барлық маркалы FeSi, кристалды кремнийді және басқаларын өндіру. Қожды үрдіспен FeCr, FeMn, FeW және басқалары балқытылады. Қож еселігі кендегі (концентраттағы) бос жыныстың мөлшері мен құрамына байланысты 0,4-тен 2,5-ке дейін және одан жоғары болады.
Флюсті және флюссіз үрдістер
Ферроқорытпаларды үздіксіз үрдіспен қорыту кезінде балқыманы флюсті тәсілмен жүргізеді. Флюстер ретінде құрамында компоненттері тотықсыздандыру реакциясы оксидті өнімдерімен берік химиялық қосылыстар түзетін CaO, MgO және басқалары бар материалдар пайдаланылады. Бұл кезде қож тұтқырлығы азаяды, қождың балқу темперратурасы (То) төмендейді (немесе артады), ферроқорытпалардағы қоспалар концентрациясы төмендейді, бұл жетекші элементтің толығырақ бөлінуіне және ферроқорытпа сапасының артуына әкеледі.
Флюссіз тәсілмен қорытуда электроэнергия шығыны төмендейді және пеш өнімділігі артады, бірақ жетекші элементті тотықсыздандыру дәрежесі төмендейді. Қожда жетекші элемент оксидтерінің үлкен мөлшері болады және оны әдетте көміртекпен тотықсыздандыруға қабілетті ферроқорытпаларды қорыту үшін қолданады. Бұл кезде флюс шығыны азаяды және жетекші элементті үздіксіз пайдалану жоғарылайды. Бірақ флюссіз тәсіл жоғары сапалы кендер мен концентраттарды пайдалануда ғана қолданылады.
Ферроқорытпалар өндірісі көміртекті термиялық (КТӨ), силикотермиялық (СТӨ) және алюмотермиялық (АТӨ) болып жіктеледі.
37 Ферроқорытпа сапасына қойылатын жалпы талаптар
Ферроқорытпалар жетекші элементтің өзгеру шектерімен және мөлшерімен, қоспалар концентрациясымен (C; S; P; түсті металдар, N және басқалары), түйіршіктік құрамымен, тығыздықпен, балқу температурасымен, O2, H2 және басқа бейметалл қоспаларының мөлшерімен сипатталады. Ферроқорытпалар сапасының негізгі көрсеткіші жетекші элементтің жоғары концентрациясы мен жетекші элементі мөлшері, химиялық құрамы болып табылады. Ферроқорытпалардың химиялық құрамының біртектілігі қорытпадағы жетекші элементтің орташа мөлшерінен шекті максимал ауытқуымен сипатталады. Ауытқу ± 2% деп қабылданады, бұл қоспалаушы элементтердің берілген тар мөлшерімен болатты алуды қамтамасыз етеді.
Зиянды қоспалар мөлшеріне шектеу (P, S, C). Ферроқорытпалардағы зиянды қоспалар болып балқыту үрдісінде металдан алынбайтын түсті металдардың (Cu, Pb, Zn, Sn, As, Bi, Gd) қоспалары табылады. Түйіршіктік құрам маңызды сипаттама болып табылады. Кесектердің рұқсат етілген өлшемі кесектердің максимал массасымен (5-45) немесе габариттерімен (≤ 300мм) сипатталады. Жоғары сапалы ферроқорытпаларда тотыққан беттер, қождың пісірілген орындары және құйма қалыптардың сылақтары болмауы керек. Қоспалаушы қоспалар негізінде қорытпалардың берілген түйіршіктік құрамын алу үшін ұнтақтау қондырғыларын таңдау жүргізіледі.
Осылай ферроқорытпалар сапасына қойылатын талаптар олардың технологиялық тағайындалуына байланысты орнатылуы қажет.
38. Шикізат материалдарын дайындау және пирометаллургиялық тәсілмен мыс алу
Мыс алу үшін мыс кендері, сонымен қатар түсті металдардың өнеркәсіптік және тұрмыстық қалдықтары қолданылады. Мыстың кендердегі мөлшері өте төмен және 1-6% құрайды. Құрамында 0,5 Cu бар тау жыныстары олардан мыс бөлу үрдісінің тиімсіздігінен қайта өңделмейді. Көптеген жағдайларда мыс кендерінде басқа түсті металдар: мырыш, қорғасын, никель, алтын, күміс, селен, теллур және басқалары болады. Мыс кендерде сульфидтер (сульфидті кендер) немесе оксидтер (тотыққан кендер) түрінде болады. Мыс кендері байытуға, әдетте флотацияға ұшырайды. Байыту нәтижесінде мысты концентрат және қалдық алынады. Кендерді байытуда мыс концентратымен қатар басқа да концентраттар, мысалы, мырыш, қорғасын, пиритті және басқалары, алынады. сульфидті кендерден алынатын мыс концентраты құрамында: 10-35% Cu, 30-35% Fe және 20-24% S болады. Бос жыныстың мөлшері (көбіне SiO2, сонымен қатар Al2O3және CaO) 3-15% аралығында болады.
Мыс кендері мен концентраттарын қайта өңдеудің екі тәсілі бар: пиро- және гидрометаллургиялық. Күйдіруді, штейнге балқытуды, штейнді айырбастау, отпен және электролиттік тазартуды қамтитын пирометаллургиялық тәсіл көбірек таралған (1-сурет).
Концентраттарды күйдіруді күкірт мөлшерін азайту және мыс пен темір сульфидтерінің бір бөлігін оксидтерге ауыстыру үшін жүргізеді. Бұл жеткілікті мысқа бай сульфидтер қорытпаларын (штейн) алу үшін қажет.Штейнге балқыту сульфидтер (штейн) мен оксидтер (қож) балқымаларын алуды қарастырады. Сұйық штейн айырбастауға ұшырайды, яғни конвертерде ауамен үрленеді, бұл ретте сульфидтердің тотығуы, темірдің қождануы және қара мыстың алынуы жүреді. Қара мысты алдымен отпен, сосын электролиттік тәсілмен тазартады (қоспаларды жояды).
39 Концентраттарды күйдіру
Күйдіруге көбіне құрамында 8-25% Cu бар кедей концентраттар ұшырайды. Бай мыс концентраттары күйдірусіз балқытылады. Ең жетілген тәсіл қайнаушы қабатта күйдіру болып табылады. Қайнаушы қабат құбылысының мәні келесіде: егер түйіршікті материал қабаты арқылы газдың өршуші ағынын жіберсек, онда аз жылдамдықтарда қатты бөлшектер қозғалмайды, бұл ретте қабат көлемі өзгермейді, бұл шахталық пештерде өтетін үрдістерге тән. Егер жылдамдықты арттырсақ, онда оның қандай да бір мәнінде материал бөлшектері еркін болады және қарқынды қозғалады: қабат көлемі ұлғаядыжәне ол қайнап жатқан сұйықтыққа ұқсас болады. Қайнаушы қабат түзуге қажетті газды ағынның жылдамдығы күйдірілетін материал бөлшектерінің диаметрі мен тығыздығына тәуелді.
Қайнаушы қабатта күйдіруге арналған пештің төмеңгі бөлігінде табаны бар, қимасы тікбұрыш, тігінен орналасқан камера болады. Камераның түбінен күмбез арқылы сығылған ауа беріледі. Шихталық материалдар (7080%мыс концентраттары, 15-20% кварцты флюстер, 2-3% әктастар және 2-3% айналмалы материалдар) жүктеу құрылғысы көмегімен пеш табанына беріледі. Күйдіру 850°С-та өтеді, бұл ретте мыс пен темір сульфидтерінің ауа оттегісімен өзара әсерлесуі жүреді. Күйдіру кезінде жүретін негізгі реакциялар келесілер болып табылады:
3FeS + 5O2 = Fe3O4 + 3SO2,
Cu2S4 + 2O2 = 2CuO + SO2.
Күйдіру нәтижесінде өртенділер (огарок) алынады, олардың құрамындағы күкірт мөлшері 10-12% құрайды, ал бастапқы концентратта ол 24-28% болады. Күйдіру үшін механикалық қыздырумен көп табанды пештер қолданылады. Пеш отқа төзімді кірпіштермен шегенделген цилиндр болып келеді. Пеште отқа төзімді кірпіштерден салынған 8-13 табан-сөрелер бар. Пеш осімен қалақ тәріздес ескектер бекітілген ескек ұстағыштары бар бос денелі тік білік өтеді.Ескектер білік айналғанда (2-3 айн/мин) олар материалдың бір сөрелерде периферияға, басқаларында кері бағытта жылжуын қамтамасыз ететіндей орналасқан. Жоғарыдан жүктелетін шихта біртіндеп төмен қарай иек тәріздес жолмен табаннан табанға жылжиды. Сульфидтерді ішінара тотықтыруға қажетті ауа цилиндр құраушысы бойында орналасқан терезе арқылы сорылады. Ауа төменнен жоғары қарай шихтаға қарсы қозғалады. Күйдіру температурасы шихтаның бірігуін болдырмау үшін 850°С-тан артпауы керек. Осы себептен шихтадағы күкірт мөлшері 27%-дан артық болмауы қажет. Пештен шығарылатын газдар күкірт қышқылын өндіру үшін пайдаланылады. Алдын ала олар шаңнан тазартуға ұшырайды.
40. Шағылдыру және электрлік пештерде штейнге балқыту
Шағылдыру пештерінде, сонымен қатар пештердің басқа түрлерінде мыс концентраттарын штейнге балқытудың негізгі мақсаты екі сұйық өнімді – штейн мен қожды ала отырып, шихтаны балқыту болып табылады. Бұл ретте мыс пен басқа бағалы элементтерді, мысалы, асыл металдарды, штейнге толығырақ ауыстыру, ал бос жынысты қождау мәселесі қойылады.
Шағылдыру балқытуының мәнісі жүктелген шихтаның көміртекті отынды пештің көлденең жұмысшы кеңістігінде жағудан бөлінетін жылу есебінен балқитындығында. Отын жанғанда пайда болатын факел балқытпа бетінде орналасады.Ылғалды және кептірілгенконцентраттарды балқытуда жүктелген шихта пештің бүйір қабырғалары бойында құламалар түзеді, өртендіні (огарок) балқытуда ол қожды балқытпа айнасының бетімен ағады.
Шағылдыру пештерінде шихта және балқытпа беті күмбездің ішкі бетінен шағылысқан жылулық сәулелердің және ыстық жағу газдарының факелінің сәуле шығару есебінен қыздырылады. Жылу беруде күмбездің жылулық сәулеленуді шағылдыру арқылы қатысуы пештерді шағылдырушы деп атауға себепші болды.
Шихта қабаты ішінде жылу беру тек жылу өткізгіштік есебінен ғана жүзеге асуы мүмкін. Шағылдыру пештерінде балқытпа ішінде масса алмасудың болмауы балқытпаның төмеңгі қабаттарына жылудың берілуі тек жылу өткізгіштік есебінен жүретіндігін білдіреді. Бұл кезде шихта мен қожды балқытпаның жылу өткізгіштігі төмен екенін ескерген жөн.
Шағылдыру пешінде балқыту механизмін келесі түрде айтуға болады. Факелден шығарылатын жылу есебінен құламалар бетінде жатқан шихтаны қыздырумен материалды кептіру және жоғары сульфидтер мен басқа тұрақсыз қосылыстардың термиялық диссоциациясы бірге жүреді. Қыздыру шамасына байланысты шихталық құламалардың беткі қабаттарында шихтаның жеңіл балқитын құраушылары – сульфидті және оксидті эвтектикалар балқи бастайды. Бұл кезде түзілетін біріншілік балқытпа құламалар бетімен ағады, өзінде қиын балқитын компоненттерді ерітеді және қожды балқытпа қабаттарына түсіреді. Осы кезден бастап қожды және штейнді фазалардың бөлінуі басталады, оксидті фазаның тамшылары пештегі қождың жалпы массасында ериді, ал штейн тамшылары қож қабаты арқылы өтеді және ваннаның төмеңгі бөлігінде өзіндік штейндік жентек түзеді.
Штейн тамшыларының тұну жылдамдығы олардың өлшемдері үлкен болған сайын, соншалықты жоғары болады. Шағылдыру пештері жағдайында (тыныш ванна) өте ұсақ штейндік қоспалар пеште балқытпаның болу уақытында (10-14 сағ) толықтай тұнып үлгермейді және қожбен бірге шығарылады.
Шағылдыру пештерінде термиялық дайындықтан өткен, күйдірілген концентраттарды қайта өңдеуде балқыту механизмі басқаша болады. Өртенді (огарок) бөлшектері қожды ванна бетімен аға отырып, онымен байланысады, осының нәтижесінде бөлшектердегі оксидті қабыршақтар қожда ериді, ал сульфидті түйіршіктер штейн түзе отырып, балқытпа түбіне тұнады.
Шикі және күйдірілген концентраттарды балқытуда балқыту механизмі де әртүрлі болады. Шикі концентраттарды балқыту кезінде негізгі химиялық үрдістер болып жоғары сульфидтердің ыдырауы және темір сульфидтерінің айналмалы конвертерлік қожбен пешке келіп түсетін магнетитпен төмендегі реакция бойынша өзара әсерлесуі болып табылады:
FeS + 3Fe3O4 +5SiO2 = 5(2FeO · SiO2) + SO2.
Бұл жағдайда жалпы дусульфуризация әдетте 45-55%құрайды. Өртендіні (огарок) балқыту (күйдіру кезінде жоғары сульфидтердің ыдырауы толықтай біткендіктен)оксидтер мен сульфидтер арасында химиялық өзара әсерлесуге келтіріледі. Бұл балқытуда негізгі реакциялар:
Cu2O + FeS = Cu2S + FeO,
10Fe2O3 + FeS = 7Fe3O4 + SO2,
сонымен қатар кремнезем болғандағы FeS Fe3O4-пен өзара әсерлесу болып табылады.
Күйдірілген мыс концентраттарын балқытуда десульфуризация 20-25%-дан аспайды. Мыс концентраттарын балқытуға арналған шағылдыру пеші – көлденең жұмысшы кеңістігі бар балқыту агрегаты. Заманауи шағылдыру пештерінің ішкі өлшемдері келесідей: ұзындығы 28-35м, ені 6-10м, күмбезден табанға дейінгі биіктігі 4-4,5м. Мұндай пештердің табанының ауданы 180-350м2 аралығында болады.
Конструкциялық шағылдыру пеші фундаменттен, қабырғалардан, табаннан (пештабан), күмбезден, қаңқасынан, балқыту өнімдерін шығару және шихтаны жүктеуге арналған құрылғылардан, отынды жағуға арналған оттықтардан (форсункалардан) тұрады.
Пеш фундаменті (негізі) құйма қождан, бетоннан, кірпіштен немесе кесек тастан дайындалған. Фундаментте пісіру пештабаны орналасқан. Пісіруді құрылыс және отқа төзімді кірпіштердің бірнеше қабаттарында кварцты құмды балқытумен жүргізіледі. Пештабанның жалпы қалыңдығы 0,61,5м.
Шағылдырып балқытудың өнімдері штейн, қож, шаң және газдар болып табылады. Оларды шығару және жою арнайы қондырғылар арқылы жүзеге асырылады.
Шағылдырып балқытудың зауыттық мыс штейндері қайта өңделетін шикізат және балқыту тәсіліне (күйдірусіз немесе күйдірумен) байланысты құрамында 15-60% Cu, 6%-ға дейін Zn, 0,5%-ға дейін Ni, 1%-ға дейін Pb, 3040% Fe, 23-26% S болады. Бұдан басқа олардың құрамында асыл металдар, селен, теллур және басқа бағалы және зиянды қоспалар болады.
Штейнді шығару пеш табаны үстіндегі ванна түбінен периодты жұмыс істейтін шпурлар арқылы немесе байланыстырушы ыдыстар принципі бойынша жұмыс жасайтын сифондық құрылғылар арқылы жүргізіледі. Штейндік сифон үзіліссіз режимде жұмыс жасай алады. Шпурды сазды тығынмен, ал сифонды сазды тығызағыш көмегімен бітейді.
Шағылдырып балқыту қожтарының жеке қож түзуші компоненттерінің мөлшері бойынша құрамы үлкен аралықтарда өзгеруі мүмкін. Ол бірқатар жергілікті жағдайлардан – қайта өңделетін шикізат құрамы мен түрінен, арзан және қол жетімді флюстердің бар болуынан, технологиялық факторлардан тәуелді. Флюстеуші қоспалардың минимал рұқсат етілген шығысында, бірақ сол кәсіпорын үшін аударма қожтың оңтайлы құрамынан қашықтамай жұмыс істеуге ұмтылады. Шағылдырып балқытудың нақты қожтарындағы жеке қож түзуші компоненттердің мөлшері келесі аралықтар өзгереді, %: Cu 0,3-0,8; SiO2 32-46%, FeO 35-55, CaO 1,5-22, Al2O3 3-10%, Zn 6-8 дейін, S 0,5 - 1,5.
Шағылдырып балқыту штейнінің құрамында 80-90%мыс және темір сульфидтері болады, ал олардың құрамына 15-55% Сu, 15-50% Fе, 20-30% S, 2% Zn, сонымен қатар асыл және басқа металдар кіреді. Қож кремний, темір, кальций және алюминий (SiO2, FeO, CaO, және 0,5% Cu) оксидтерінен тұрады.Мыс пен асыл металдарды штейнге шығару дәрежесі96-99,5%-ға жетеді.
Штейн қорытуға арналған жетілген агрегат электрлік пеш болып табылады. Онда жоғары өнімділікке қол жеткізіледі, пеште балқытумен қарағанда шығарумен жоғалтулар төмендейді. Бірақ шағылдыру және электрлік пештерде балқытудың бірқатар кемшіліктері бар. Бірінші кезекте олардың қатарына төмен меншікті өнімділік жатады. Шағылдыру пештерін ол 4,0-4,5т/тәул, ал электрлік пештерде аздап жоғары құрайды. Электрлік пешке шикізатты пайдаланудың айтарлықтай төмен кешенділік тән, яғни біраз бағалы металдар (қорғасын, мырыш, кадмий, германий, рений және басқалары) штейнге шықпайды және барлығы дерлік жоғалады.
ТМД елдерінде сұйық ваннада балқыту деп аталатын балқытудың жаңа сызбасы ұсынылды. Бұл тәсіл 50-60т/(м2·тәул)-ке дейінгі өте жоғары меншікті өнімділікке, отынның төмен шығысына ие (шағылдыру деңгейімен салыстырғанда шамамен үш есе кем), бұдан басқа мыстың және басқа түсті металдардың шығу дәрежесі артады. 20-40% күкіртті ангидридтен тұратын шықпа газдар күкірт қышқылын өндіру үшін қолданылады.
Сұйық ваннада балқытуға арналған пеш ұзындығы 10м, ені 2-3м және биіктігі 6-6,5м болатын тікбұрышты шахта болып келеді (2-сурет). Пештің бүйір қабырғаларында үрлеуге арналған сумен суытылатын үрлегіштер орналасқан. Шахта қабырғалары сумен салқындатылатын кессондар түрінде орындалған. Пештің төменгі бөлігі (көміш) отқа төзімді кірпіштермен шегенделген. Балқыту үзіліссіз жүргізіледі. Қож пен штейнді шығару көмішпен тоғыцсқан және қосылған қожтық және штейндік сифондар арқылы жүреді. Шихталық материалдар күмбездегі тесіктер арқылы жүктеледі, олар ленталық қоректендіргіштер көмегімен бункерден беріледі.
41. Шахталық пештерде штейнге балқыту
Мыс кендерін шахталық балқыту бірнеше ғасыр сақталған және қазіргі уақытқа дейін практикалық маңызы жойылмаған штейнге балқытудың ескі тәсілі болып табылады. Шахталық пеш шахтаға ұқсас тік жұмысшы кеңістігі бар балқыту аппараты болып келеді. Түсті металлургияның шахталық пештерінің көлденең қимасының формасы тікбұрышты. Кен мен флюстерден тұратын шихтаны және отынды периодты түрде салысдар деп аталатын жеке порциялармен мойындық алаңшаға жүктейді. Пештің төменгі бөлігіне үрлегіш арқылы ауа үрленеді. Үрлегіш маңында отын (қайта өңделетін шихтаның сульфидтері немесе кокс) жанады және сол жерде өте жоғары температуралар дамиды (1300-1600°С-қа дейін). Жоғары температуралар зонасы пеш фокусы деп аталады. Бөлінетін жылу есебінен пеш фокусында шихтанфың балқуы жүреді және балқыту өнімдерінің түзілуі аяқталады.
Балқытудың сұйық өнімдері (қож бен штейн) ішкі көмішке ағады, одан олар қату үшін алдыңғы көмішке сифондық астауша арқылы бірге беріледі. Штейн мен қожтың бөлек шығуы алдыңғы көміштен жүзеге асырылады. Балқыту шамасы бойынша шихта төмен түседі, ал оның орнына жаңа порциясы жүктеледі. Үрлегіш маңында және одан жоғарыда пайда болған газдар жоғары қарай көтеріледі, түсуші шихта бағанынан өтіп, оған өзінің бар жылуын береді. Қарсы ағын принципі бойынша газдар мен шихта арасындағы жылу алмасу металлургиялық пештерде байқалатын және шахталық пештерде 80-85%-ға жететін жылуды пайдаланудың өте жоғары коэффициентін қамтамасыз етеді.
Көптеген басқа балқыту пештерімен салыстырғанда шахталық пештерде тек ірілігі 20-100мм кесекті материалды балқытуға болады. Ұсақ шихтаны (кенді немесе концентраттарды)қайта өңдеу жағдайларында оны агломерация немесе брикеттеу тәсілдерімен алдын ала кесектеу қажет. Мыс кендері мен концентраттарын қайта өңдеуге шахталық балқытудың төрт түрі қолданылады: тотықсыздандыру, пиритті (тотықтандыру), жартылай пиритті және жетілдірілген пиритті немесе мысты-күкіртті. Қазіргі заманғы мыс металлургиясында кенді шикізатты өқайта өңдеуде тек екі соңғы тәсіл ғана практикалық маңызын жоғалтқан жоқ. Тотықсыздандырып шахталық балқыту қазіргі уақытқа дейін екіншілік шикізаттан қара мыс алудың негізгі тәсілі ретінде қолданылады.
Тотыққан немесе екіншілік шикізатты қайта өңдеуге жарамды тотықсыздандырып балқытуда үрдіске қажетті барлық жылу шығысы қатты шихта массасының 15%-нан кем емес болатын коксты жағу есебінен алынады.
Пиритті балқыту тотықсыздандырып балқытуға қарағанда жану жылуы 5000-6000 кДж/кг болатын сульфидті шихтаның тотығуынан (жануынан) бөлінентін жылу есебінен теориялық толығымен жүре алады. Өте шиелініскен жылулық баланс әсерінен практикада пешке 2%-ға дейіне кокс енгізілді. Құрамында 75%-дан кем емес пирит (~42% күкірт) болатын жоғары күкіртті кендерді ғана қайта өңдеуге жарамды пиритті балқыту таза күйінде практикалық мәнін жоғалтты.
Бастапқы шихтадағы сульфидтер шахталық балқытуды автогенді ендіруге жеткіліксіз болған жағдайларда жылу жетіспеушілігі көміртекті отын жағумен толықтырылады. Жылу сульфидтердің жануынан да, отын жағудан да алынатын шахталық балқытудың бұл түрі жартылай пиритті деген атауға ие болды. Шахталық балқытудың бұл түріндегі кокс шығысы 512% аралығында өзгереді. Осылай жартылай пиритті балқыту тотықсыздарып және пиритті балқытулары арасында аралық орын алады.
Жартылай пиритті балқыту барысын және сипатын анықтайтын негізгі үрдістер пеш фокусында дамиды, мұнда максимал температураға (1600оСқа дейін) қол жеткізіледі және кесекті костер мен сульфидтердің (қатты және сұйық күйінде) жану, шихта компоненттерінің, штейндік және қожтық түзілімдерді балқыту үрдістері жүреді.
Клаасикалық нұсқадағы мысты-күкіртті балқыту күкіртті қарапайым күйде алу мақсатында пеш газдарын өңдеудің жетілдірілген тәсілімен бірге, құрамында 40-42%-дан кем емес күкірт бар жоғары күкіртті кендерді пиритті балқыту болып келеді. Ол үшін кокстың артқан мөлшерімен (12%-ға дейін) және кварцты флюспен сульфидті кенді биіктігі өсірілген герметизацияланған шахталық пеште балқытады.
Мысты-күкіртті балқыту үшін пеште биіктік бойынша үш анық көрінетін: тотықтырып балқыту (төменгі), тотықсыздандыру (ортаңғы) және дайындық (жоғарғы) зоналарының болуы тән.
Үрлегіш маңында орналасқан және өте шектелген өлшемдерге ие тотықтырып балқыту зонасында пештегі жоғары температуралар (1200-1450оС) орын алады.Балқытуға қажетті жылу пиритті балқытудың негізгі реакциясы жүруі нәтижесінде бөлінеді:
2FeS + 3O2 + SiO2 = 2FeO · SiO2 + 2SiO2 + 1030290кДж.
Классикалық пиритті балқытуда реакция реагенттерінің стехиометриясынан ешқандай ауытқуларға жол берілмейді. Кез келген бастапқы реагенттің артық болуы немесе жетіспеуі балқытудың жылулық режимінің, пеш фокусының қысқаруына немесе созылуына әкеледі. Пиритті балқытуда теория жүзінде үрілген барлық оттегі үрлегіш маңында толығымен шығындалуы қажет және фурмаға децйін кокс жетпеуі керек. Кері жағдайда пиритті эффект жоғалады және пеш «теке» түзе отырып қата бастайды.
Пиритті балқытудың сұйық өнімдері пештің ішкі көмішіне және ары қарай сыртқы тұндырғышқа ағады, ал толығымен дерлік күкірт ангидриді мен азоттан тұратын газдар жоғары ұмтылады және қызған кокспен толған ортаңғы, тотықсыздандывру зонасына келіп түседі.
Концентраттарды шағылдыру немесе электрлік пештерде штейнге балқытылады. Шағылдыру пеші ұзындығы 30-40м, ені 8-10м және табаннан күмбезге дейінгі биіктігі 3,5-4,5м болатын тікбұрышты камера болып келеді.пештің жұмысшы кеңістігі династық немесе хромомагнезиттік кірпішпен шегенделген. Күмбез династық кірпіштен жасалған аркалы немесе магнезиттен жасалған аспалы болып келеді. Пеш мазутпен, табиғи газбен немесе көмір шаңымен қыздырылады. Оттықтар немесе форсункалар пештің алдыңғы торцтық қабырғасында бір қатарда орналасады. Жанудың газ тәріздес өнімдері шихтаны шаяды, артқы қабырғаға өтеді және газ өткізгіштен пеш көмейіне жіберіледі.
Пештің бүйір қабырғаларына жақын орналасқан күмбездегі тесіктер арқылы шихта жүктеледі. Қож пен штейн пештің бүйір қабырғаларындағы арнайы есіктер арқылы периодты түрде шығарылып отырады. Штейнге балқытуда келесі реакциялар жүреді. Алдымен шихтаны қыздыру шамасына байланысты мыс оксидінің темір сульфидімен өзара әрекеттесуі жүреді:
6CuO + Fe = 3Cu2O + SO2 + FeO.
Түзілген мыс оксиді темір сульфидімен мына реакция бойынша өзара әрекеттеседі:
Cu2O + FeS = Cu2S + FeO.
Бұл реакция штейнге балқытуда негізгі болып табылады. Бұл ретте мыс пен темір сульфидтері балқып, сұйық штейн түзеді. Бір уақытта темір силикаттары мен басқа оксидтерден сұйық қож қалыптасады.
Шағылдырып балқыту штейнінің құрамында 80-90%мыс және темір сульфидтері болады, ал олардың құрамына 15-55% Сu, 15-50% Fе, 20-30% S,2% Zn, сонымен қатар асыл және басқа металдар кіреді. Қож кремний, темір, кальций және алюминий оксидтерінен тұрады.Мыс пен асыл металдарды штейнге шығару дәрежесі96-99,5%-ға жетеді.
Мысты штейндерді айырбастау
Бастапқы кен шикізатынан құрамына және түріне байланысты, құрамында 10 - 12ден70 - 75%-ға дейінгі Сu бар, мыс штейндерін барлық жерде конвертірлеу әдісімен өңдейді. Конвертірлеуге мыс штейндерінен басқа, балқытылған немесе қатты күйде бай мыс кендері, кварцты флюстер (көбінесе алтын құрамдылар) және басқада материалдар келіп түседі. Мыс штейндері негізінен мыс сульфидінен (Cu2S) және темірден (Fe2S) тұрады.
Конвертірлеу үрдісінің негізгі мақсаты – темір мен күкіртті және тағы басқа қатысатын компоненттердің әсерінен қара мысты алу. Асыл металдар толығымен дерлік (сондай ақ селен және теллур) қара металда қалады. Экзотермиялық әсерге байланысты конвертірлеудің көптеген реакциялары артық отын шығынын тудырмайды, бұл дегеніміз тікелей автогенді үрдіс болып саналатындығын көрсетеді.
Мыс штейнін конвертірлеу кезінде сульфидтердің тотығуы, темірдің қожсыздануы қара мысты бөлуі жүреді. Конвертірлеуді бұрыштық үрлеу арқылы конвертірде көлденең орналастыру арқылы жүргіземіз (3-сурет). Конвертер ішінен магнезитті немесе хромомагнезитті кірпішпен қаланған, болатты цилиндр түрінде болады. Конвертердің сыртқы диаметрі 3-4, ұзындығы 6-10м. Конвертердің сиымдылығы 8-100т құрайды. Корпустың ортанғы бөлігінде конвертерге, темір тотығынын қожсыздандыруға арналған, кварцты флюсті беретін және балқытылған штейнді құятын мойындық орналасқан. Мойындық арқылы қара мысты және қожты шығарады. Конвертердің ось бойымен айналуы электр өткізгіш арқылы жүреді. Балқыманы ауамен үрлеу конвертердің бойымен орналасқан фурма арқылы беріледі. Фурманың санына (40 тан 50 ге дейін) конвертердің сиымдылығына байланысты өзгереді.
Конвертер көлденең ось бойымен айналады. Конвертердің барлық қызметі (тиеу, балқыма қоймалжыңдары, газдарды шығару) корпустың ортаңғы бөлігінде орналасқан мойындық арқылы жүзеге асады. Конвертерге ауаны корпустың бір жақ шетінде орналасқан фурма арқылы береді. Соңғы кездерде конвертерлерде коллектор – фурманы қолдану кеңінен таралған. Бұл құрылғыда, ауалы коллектор, өзінің корпусында орналасқан фурмалы түтіктердің деңгейінде орналастырылады. Коллектордың қарама қарсы жағында фурмалы түтіктердің ось бойымен, жұмыс жасап тұрған конвертерге үрлеуді тоқтатпай ақ, фурманы тазартуға мүмкіндік беретін, шарлы бекітілген клапандар жасалған.
Көлденең конвертерлер – үздіксіз жұмыс жасайтын аппараттар. Конвертордың негізгі жұмысшы аймағы болып, көлднең ось бойымен айналу бұрышына байланысты: штейнді құю, штейнді үрлеу (фурма балқымаға жүктелген), қож қоймалжыңы, қара мыс қоймалжыңы түрлерінде болады. Штейнге үрлеу кезінде түзілетін, газдар, конвертерде орналасқан герметикалық тозаңдатқышқа мойындық арқылы, арі қарай газ ағымының жүйесіне беріледі.
Мыс штейндерін конвертірлеудің ұйымдастырылған үрдістері екі кезеңге бөлінеді. Бірінші кезең – сульфидті массалар жиынтығы. Оның негізінде темір сульфидтерін тотықсыздандыру және осы кезде түзілетін тотықтардың қожқа өтуі жатыр. Темір сульфидтерін тотықсыздандырудың ерекшелігі, бірінші кезеңде мыспен салыстырғанда темірдің оттекке жоғары жақындығымен анықталады.
Бірінші кезеңде сульфидтердің тотықсыздандырылуы ауа оттегісен жүзеге асады. Осыған байланысты темір сульфидінің штейндегі концентрация төмендеп, сәйкесінше мыс сульфиді жоғарылайды, бұл дегеніміз, негізгі құрамы мыс сульфидінен тұратын және 78 - 80% Cuжәне20 - 21% S құрайтын ақ штейнге дейін түзілуі.Темірдің қожка өтуіне кварцтты (SiO2) флюс әсер етеді. Бірінші кезеңнің негізгі реакциялары болып келесілер саналады:
2FeS + O2 + SiO2 = 2FeO · SiO2 + 2SO2,
2Cu2S + 3O2 = 2Cu2O + 2SO2,
Cu2O + FeS = Cu2S + FeO.
Бірінші кезең штейндегі мыстың құрамына байланысты 6 дан 25 сағатқа дейін созылады.
Реакциялы деп аталатын, екінші кезеңде, нәтижесінде қара мыс алынатын ақ штейнде ауамен үрлеу жүреді. Бұл кезеңнің негізгі реакциялары болып келесілер саналады:
Cu2S + 3O2 = 2Cu2O + 2SO2,
Cu2S + 2Cu2O = 6[Cu] + SO2.
Екінші кезең 2-3 сағатқа созылады. Екінші кезеңнің аяқталуына қарай мысты конвертерден алып тік бұрышты болатты шөміштерге құяды. Қара мыстың құрамында: 97,5 - 99,5% Cu, 0,01 - 0,1% Fe, ≤ 0,3% Sb, ≤ 0,05% Bi, сондай ақ никельдің, мышьяктың, күмістің, алтынның және т.б. біршама мөлшері бар. Мысты және асыл металдарды жиынтықты бөліп алу 95 - 99% құрайды.
Конвертордың өнімділігі жалпы балқуға кеткен уақыт ұзақтығына бюайланысты 1 сағатта қара мысты өндіруге 4-12т құрайды. Тұтынушыларға қара мысты тікелей қолдану, оның құрамындағы электрлік, механикалық және басқада мыстың маңызды қасиеттерін және бағалы элементтерін – бағыттарын нашарлататын, құрамындағы зиянды қоспалардың әсерінен мүмкін емес.
Қара мысты рафинерлеуді экономикалық жағдайларға байланысты екі сатыда жүргізеді. Алдымен мысты зиянды қоспалардан оттық рафинерлеу әдісімен, содан кейін электролитті әдіспен тазартады. Бір ғана электролитті рафинерлеу қарастырылуы мүмкін. Алайда алдын ала мысты тазартусыз электролизді жүргізу қымбатқа соғуы мүмкін.
Мысты тазарту
Қара мысты рафинерлеу (қоспаларды алып тастау) алдымен оттық, электролиттік әдіспен өндіреді. Осыған сәйкес тек қана қоспаларды ғана емес, сондай ақ мыстан алтын металдарды және басқада бағалы қоспаларды алуға болады. Оттық рафинерлеуді құрылысы жағынан штейнді балқытуға арналған пештерге ұқсас, шағылыстырғыш пештерде жүргізеді. Пештердің сиымдылығы 200-400т құрайды. Пештерді табиғи газбен, мазутпен және көмір шаңымен қыздырады. Балқыту үрдісіндегі температура 1130 - 1150°С болады.Балқу ұзақтығы 20 сағат құрайды және қара мысты конверторден алғаннан кейін бірден пешке құятын болса 6-8 сағатқа төмендейді.
Балқыту үрдісі кезінде темір түтіктері арқылы балқымаға ауа оттегісімен
үрілетін қоспаларды тотықсыздандыру жүреді. Мысқа қарағанда оттекке химиялық қасиеті жағынан ұқсас қоспалар тотықсызданады. Оларға темір, никель, мырыш, мышьяк, сурма жатады. Асыл металдар тотықсызданбайды және мыста қалып қояды. Соның ішінде селен және теллур толығымен дерлік тотықсызданбайды , ал висмут шамалы дәрежеде тотықсызданады. Тотықсыздандыру кезеңінің негізгі реакциялары болып келесілер саналады:
4[Cu] + O2 = Cu2O,
[Me](қоспа) +Сu2O = MeO + 2[Cu].
Тотықсыздандыру кезеңінен кейін пештен қожты алып балқытылған мыстан еріген газдарды шығарып тастайды. Бұл операцияны тығыздығына байланысты дразнерлеу деп атайды, ол металдық ваннаға шикі қоспаларды салуды қарастырады. Осыған сәйкес ваннаның араласуына және одан күкіртті ангидрит және тағы басқа газдар түріндегі күкіртті алып тастауға әсер ететін, газ түсгіш көмірсутектілер және су бүркемесін интенсивті түрде шығару жүреді. Содан кейін созылымдылыққа дразнерлеу операциясын жүргізеді, бұл операция мысты қышқылсыздандыруға , яғни одан ерітілген оттекті алып тастауға қажет. Ол үшін ваннаның жоғарғы бетіне көмірдің бір бөлігін тастайдыда оған қайтадан шикі қоспаларды тиейді. Оттық рафинерлеу нәтижесінде құрамында 9,0 - 99,5% Сu және 0,5 - 1,0% мысты алады. Мысты жазық шөміштерге құйып, электролиттік рафинерлеуге жіберетін анодтарды алады.
Электролиттік рафинерлеуді жоғары деңгейдегі таза мыстарды алу үшін және асыл металдарды, басқада бағалы қоспаларды алып тастау үшін жүргізеді. Электролизді күкіртті қышқыл қоспасы бар күкіртқышқылды мыс ерітіндісімен толтырылған, электролиттік ванналарда жүргізеді. Ванналарды ішкі жағы қорғасынмен немесе винипластпен қапталған, темір ветоннан немесе ағаштан жасайды. Цехта 1500-2000 ваннан орналасқан. Анодтарды ванналардың шетіне іліп катодтармен (мыстың немесе тотықпайтын болаттың жұқа түрі) алмастырады. Электролиз үрдісінде мыс аноды еріп кетеді, яғни мыс еритіндіге өтеді, сосын катодта шығарылады. Катодта мыс иондарының зарядталуы жүреді. Үрдіс 5-12 күнге созылады. Таза мыстан алынған катодтарды ваннадан шығарып әбден жуады, сосын электр пештерінде қайта балқытады. Бұндай қоспалар, алтын, күміс, селен, теллур, электролиз үрдісінде ерімейді және тұнбаға (шлам) түседі. Шламды одан бағалы элементтерді алу мақсатында қайта өңдейді. Тұнбаға сондай ақ қорғасын, қалайы, сурма түседі.1 тонна мыс катодына кететін электр шығыны құрайды:200 - 300кВт · сағ, тоқ бойынша шығын 98%. МО маркасындағы таза мыс шамамен 99,95% Сu құрайды.
44. Алюминий және оның қосылыстарының қасиеттері
Алюминий оттекке жоғары химиялық қатыста болады, ол оның болат өндірісінде қышқылсыздандырғыш ретінде кең қолданысқа ие болуын анықтайды:
2[Al]Fe + 3[О]Fe = (Al2O3),
lnKal = ln([aAl]2 · [ao2]3 = (- 59560 / T) + 17,71.
1873К lnKal = - 14,09 болған кездеоның қышқылсыздандыру қасиеті сәйкесінше жоғары. Алюминийдің атомдық массасы 26,98, tпл = 933,23К, tкип = 2773К. 70 - 90% дейінгі Al ауа оттегі және шлак арқылы қышқылсыздандырылады, ал қалған құрамы болатта тиімсіз, сондықтанда болатты қоспалау кезінде қышқылсыздандыру үшін ферроалюминий және басқада балқымаларды (Fe - Mn - Al, Fe - Al - Mn - Si, Fe - Cr - Al және т.б.) қолданады. Бұл алюминий ферроқорытпаларын алу үшін алюминий шикізатын алюмасиликаттарға алмастырып қымбат және ақаулы бокситтерді алып тастау арқылы пештерде алюминийді электротермиялық әдіспен өңдеуді алюминий ферроқорытпаларын алуда мүмкіндік береді. Болатты қышқылсыздандыру үшін 10 - 30% Al бар ферроалюминийді қолдану алюминийді тиімді пайданануды 50 - 90% Al дейін жоғарылатады және ол біртіпдеп өседі. Алюминий (ФСА, ФАМС) және басқада қоспалардың қышқылсыздандыру қасиеттері таза элементтердің қышқылсыздандыру қасиеттерін жоғарылатады. Al2O3 - тің жоғары тотығы 2326К температурада балқиды. Жоғары температураларда AlO, Al2O, Al2O3. tкип Al2O3 = 3930К тотықтары үлкен роль атқарады. С мен қосылысы кезінде алюминийдің берік тотық карбиттері Al4O4C және Al2OC түзіледі. Al4O3 SiO2 мен және басқада металдармен қосылып Al4O4C tплав = 1873К түзіледі.
45. Глинозем құрамды кендер және минералдар
Алюминийді алу үшін шикізат ретінде глиноземгидратынан (бір сутекті гидраттан), глинозем моногидратынан – диаспор және бемиттен тұратын тау жынысы түріндегі боксит саналады. AlOOH үш сутекті гидраттан, гиббстан Al(OH)3 және басқада гидрооксил (гетит, гидрогетит, гидрогематит)және темір тотығынан тұрады.
Бокситтің үш түрі ажыратылады: 1)моногидратты (диаспор, бемит), 2) үш гидратты (гиббс), 3) екі минералдың да пішінін құрайтын араластар.
Зиянды қоспа ретінде SiO2 саналады. Бокситтің негізгі химиялық қоспасы болып Al2O3 саналады. Өнеркәсіптік бокситтердегі глиноземнің құрамы 28 - 60% аралығында болады. Глиноземнің 10 маркасы қарастырылады: ЭБ - 1, ЭБ - 2 маркасы электрлі коронд өндірісі үшін, ЦБ - 1 ЦБ - 2 цемент үшін, ОБ – отқа төзімділер үшін, ГБ - глинозем, МБ – мартен өндірісі үшін. Al2O3 тің бокситтің МБ , ГБ маркаларында шамамен 28%, ал ЦБ – 1 де - 34%, ЭБ – 2 де - 43%.
БҰҰ да бокситтің кен орындары: Оралда, (Қазақстанда, Торғай бокситтік ауданы), Кросноярск ауданында және Украинада. Жер шарында боксит кен орындарын жасаудың ең тиімді жолы болып тропиктермен (әлемдік қордың 80%) Альп және Гимолай тау жүйелерінің жазықтары саналады. Алюминий күн энергиясын қолдануда жиынтықты қондырғыларды жасау арқылы құрылымды материал ретінде қолданылады. Алюминийді және оның органикалық қоспаларын қолдануды жоғары дәрежеде болғандықтан әлемнің барлық елдерінде алюминий және оның қоспаларын глинозем құрамды бокситтерден әр түрлі әдістер электр балқыма, химиялық, микробиологиялық, сілтісіздендіру және т.б. арқылы алу технологиясы бойынша жұмыстар жүргізуде.
Осыған байланысты БҰҰ және басқада елдерде құрамында ферроқорытпа бар жиынтықты алюмнийді алудың жаңа технологиялық үрдістері қарастырылуда, оларды қара металлургияда болатты қышқылсыздандыру үшін, қара және түсті металлургияда біріншілік алюминий шығынын төмендетуге мүмкіндік береді.
Ферроалюминий технологиясы
FeAl дің химиялық құрамы келесі маркалар үшін: ФА - 10: 8 - 11,9% Al, ФА - 15: 12 - 16,9% Al, ФА - 20: 17 - 21,9% Al және ФА - 23: 22 - 24% Al. Келесі маркалар үшін қоспалардың құрамы: 4% Si, 4% C, 0,06% S, 0,06% P. FeAl балқытуды үлкен қуаттылықты жабық электр пештерінде жүргізеді, балқыту технологиясы совролитті концентраттың (48 - 50%; Al2O3; 34 - 36% SiO2 және ≈ 15% Fe2O3 немесе басқа алюмосиликатты шикізаттардан (силимоноит, дистен, каолин және т.б.) боксит агломераттарынан алынатын электрлі корундтан алюминийді өңдеуден тұрады. Осылайша қарапайым әдіспен (SiO2 және Fe, өндірілуімен, кен өндіргіш пештерде кедей бокситтерден көміртек алумен ) алынған электрлі корунд құрайды: 91 - 96% Al2O3, 1 - 3% SiO2, 1 - 2% TiO2, ≈ 0,5% MgO; 0,8 - 3% CaO. Осыған байланысты ферросилиций (ФС20 - 25) алынады.
Бірінші сатыда 1т электрлі корундқа және 500 - 800кг FeSi ге кедей бокситтің 1600 - 1700кг, кокстың 250 - 300кг-ы, болаттың 600 - 850 шамасы электр энергия 5000кВт / ч болғанда агломераты алынады.
Екінші саты металды үздікті шығару арқылы және шлактың аздаған мөлшері жүретін үздіксіз үрдіс. Шихта ретінде электрлі корунд, кокс, болат қолданылады. Шихтаны дұрыс таңдап алу және құрау арқылы және электрлік режимді таңдау арқылы үрдіс қиындықсыз жүреді. Металды шығаруды әрбір екі сағат сайын жүргізеді. 1 т құймаға шлактың 1 - 3% өтеді. Шлак біршама жақсы жүреді. FeAl дің құрамы: 8 - 20% Al, 2 - 3,5% Si, 1 - 3% С, н.б. 0,03% S және 0,04% Р. 1т FeAl ге кететін шығын (ФА15) 3900кВт / ч.
Азотталған FeAl-ді (8 - 28% Al, 4 - 10% N2, н.б. 4% Si, 1 - 3% C қалғандары Fe) алу тиімдірек. Құймаларды ауада азоттандыру арқылы азот немесе алюминийді 1473 - 1553К жүргізеді. Алюминий нитридін құрайтын құймаларды қолдану олардың құрамына кіретін азотты толығымен пайдалануға мүмкіндік беріп марганец немесе хромның азотталған құймаларын пайдаланбайды. Барлық алюминий қорытпаларын алу кезінде алюминий шикізаттарын жоғары температура кезінде сұйық фаза түзілуі арқылы өндіріледі, сондай ақ металдық құрамдағы өндірілген алюминийдің ерітіндісімен.
Бұл қағидаға алюминийді басқада құймалармен алу технологиясы сүйенеді. Ол құймаларға, мысалы, ферромарганец, ферроалюминий және ФАМС жатады. ФМнА-ның құймасын балқыту үшін электрлі корунд, қайта өңделген көміртекті FeMn, болат струшкасы және кокс жанғағы. Балқыманы металды әрбір екі сағат сайын шығару арқылы үздіксіз жүргізеді. ФмнА-ның 1т құймасына (8 - 11% Al, 35 - 40% Mn және 2 - 4% Si) шығындалады: 400кг т электрлі корунд, 440кг жоғарыкөміртекті FeMn, 340кг болат стружкасы, 160кг кокс электр энергия шамасы 3600кВт / сағ. болғанда. Металдың массасына байланысты шлактың құрамы 1 - 3% болады. Fe - Al - Mn - Si (ФАМС) жиынтықты құймасы тиімді болат қышқылсыздандырғыш болып саналады және одан әр түрлі шикізаттар алуға болады. БҰҰ – ның аумағындағы Оңтүстік Еуропада ставролитті концентратты – тау металлургиялық комбинатының өндісіндегі қалдықтарды қолдану тиімді. Ставролит 46 - 50% Al2O3, 36 - 38% SiO2, 13 - 15% Fe2O3құрайды. Концентратты брикеттейді немесе агломерациялайды. Үрдісті шлаксыз әдіспен үздіксіз түрде жүргізеді. Пештің колошнигі салқын, шихта еркін түрде болады, ағынөзек жақсы ашылады, ал шлактың құрамы 2% -дан (металдың массасынан) төмен. Құйманың құрамында: 10 - 14% Al, 22 - 94% Mn, 10 - 15% Si, н.б. 0,06% Р, 0,03 - 0,05% Zr, 1 - 2% С бар. Бұндай құрамдағы құйма сақтау кезінде сеппеленбейді. 1т ФАМС-ке (10% Fe, 25% Mn, 13% Si) 700кг ставролит, 400кг - тауарлы SiMn, 630кг болат стружкасы электр энергия 5200кВт / сағ.болғанда шығындалады. FeMnAl-дің 1т құймасының өзіндік құны 180 - 210$, ФАМС-те 300$ құрайды. ФАМС құймасын Si және Al көміртегін боксит агломератынан және кремнийдің төменгі құрамымен жоғары көміртекті FeMn немесе FeSiMn-ті метал ретінде енгізгендегі кварцитті алуға болады. Металдық қоспаны марганецті концентратпен алмастыру ертеректегі шлак түзумен және температураны пештің ваннасында төмендетумен байланысты. Бұл алюминий және кремнийдің жаксы өндірілуіне мүмкіндік бермейді.
Силикоалюминий технологиясы (SiAl)
Al – Si жүйесіндегі құймалар 577○С 12,3% Si болған кезде эвтетикамен кез келген қатынаста түзіле алады. Si - Al жүйесіндегі құймаларды құю саласында (қозғалтқыш блоктары, арматура, авияциялы қозғалтқыштар, дөңгелек дискілері т.б.) қолданылады. Осы жүйенің негізінде біріншілік алюминий және кристалдылық кремнийді балқыту әдістеріндегі әр түрлі элементтермен қоспаланған 5 - 33% Si құймаларды алады.
ТМД-да қуатты кен түзгіш пештерде электртермиялық әдістерді қолданып, әр түрлі алюмосиликатты шикізаттардың көміртектерімен кремний және алюминий тотықтарын шығарады. Электротермиялық әдіспен Al-ді SiAl түрде алу және оны біріншілік және екіншілік алюминийдің орнына болатты қышқылсыздандыру үшін қолдану келесідей артықшылықтарға ие:
1) электролизер қуаттылықтарымен өлшенбейтін, кен түзгіш пештердің жеткілікті бастапқы қуаттылығы;
2) ауыспалы тоқты тұрақты тоққа алмастыру және электрлік шығындарды азайту қажеттіліктерін болдырмау;
3) бокситтен глиноземді гидрометаллургиялық әдіспен алу қажеттілігінің жетіспеушілігі;
4) қымбат фторлы тұздарды қолдануды болдырмау;
5) әр түрлі алюмосиликаттарды (ставролитті, дистенді, силимонитті және басқада концентраттардан) және қазіргі кезде глинозем өндірісіне қолданылмайтын кедей бокситтерді қолдану арқылы кен базасын кеңейту мүмкіншілігі;
6) шикізаттан Al-ді арзан және кең таралған көміртекті қоспалармен өңдеу;
7) цехтерді тұрғызу кезінде глиноземді және электролизді цехтердің шығындарымен салыстырғанда қуатты кен түзгіш пештер мен есептегендегі төмен капиталды шығындар;
Al2O3 -ті көміртекпен қайта өңдеу кезінде Al - O2 - C:
Al2O3 → Al4O4С → Al2OС → Al4С3 → Al.
Al2O3 Al4С3 Fe, Si. SiAl Al и Si (3Al2O3 · 2SiO2).
SiO2(ж) + 2С = Si(ж) + 2СО,
2 / 3Al2O3 + 2С = 4 / 3Al + 2СО.
Жоғары қуаттылықты кен өңдегіш пештерде Al - Siқұймасын балқыту кезінде 59 - 64% Al құймасын алу тиімді. Бұл жағдайда құймадағы Al және Si активтілігі төмен және екіншілік карбид үрдістері Si + 2СО = SiС + СО2, 2Al + СО = Al2OC төмен деңгейде өтеді. SiAl-дің өндірісінің және оның негізіндегі литилі алюминий құймаларының (силумин АК12М2 және т.б.) технологиялық сұлбасы негізделген. Құю балқымаларының автомобиль өнеркәсібінде келесі құрамдағы түрі кең таралған: 11 - 12,5% Si, Cu - 1,75 - 25%, Fe - 0,6 - 0,9 %, Mg ≤ 0,2, Mn ≤ 0,5, Ni н.б. 0,3%, Ti ≤ 0,2, Zn ≤ 0,8%, Pb ≤ 0,15, Sr ≤ 0,1%.
Шикіқұрамның тотықты бөлігі глиноземнің алюмосиликатынан және басқада жоғары глиноземді минералдардан, ал Ni, Cu және т.б. элементтерді шикіқұрамға тотық немесе метал түрінде беруге болады. Олардың химиялық құрамына қойылатын негізгі талап темір тотығының төмен құрамы саналады. Өңдегіш ретінде газды көмірді (2,5 - 4,5% күлділік, 32 - 37% ұшқыш заттар, 78 - 80% С) және мұнайлы коксты (0,3 - 0,9% күлділік, 7 - 17% ұшқыш заттар, 88 - 90% С) береді, оларды шикіқұрамға Al және Si өңдеуге қажетті теориядан шамамен 94 - 98% енгізеді. Өңдегіштерді үсақ жіңішке тотықтармен бірге де ұнтақтайды да шнекті араластырғышта байланыстырғыш қоспасымен араластыруға жіберіледі. Содан кейін араласқан және ылғалдандырылған шикіқұрамды брикеттейді, оларды кептіреді және пешті бункерлерге бағыттайды. Балқытуды жабық колошникте және шикіқұрамның үнемі беріліп тұратын үйіндісімен жүргізеді. Колошникті арнайы мырышталған машинамен электродтардың жанында конустың пайда болуы үшін және шикіқұрамның жүрісін қамтамасыз ету үшін үйеді.құйма және қождың шығатын бөлігін бір уақытта құйманы рафинерлеп, үздіксіз футерленген қожда жүргізеді.
Алынған рафинерленген құйманың құрамында 59 - 63% Al, 38 - 39% Si және темірдің, титанның және калциймен басқада элементтердің қоспалары бар. Құйма балқыту миксеріне, ал қожды қайта өңдеуге жібереді. Құйманың рафинерленуінің металлургиялық өңделуі оны электролизді цехтан берілетін сұйық алюминиймен еріткеннен кейін басталады. Қыздырылатын миксерге құйма, салқындатылған қалдықтар және флюстерді береді. Содан кейін ерітілген құйманы кварц тығынының қабаты арқылы филтрлейді және газды қыздыратын филтрлегіш пешке бағыттап, конвейерлі түрдегі машинада қоспалайды және аралстырады
48. Титанның және оның қоспаларының қасиеттері
Титан, тығыздығы 4,5г / см3, tпл = 1670ºС, tкип = 3170ºСэлемент. Көміртекпен титан карбид TiC (tпл = 3177ºС) түзеді. Кремниймен силицид Ti5Si3, TiSi, TiSi2 түзеді, олардың ішінде ең қаттысы Ti5Si3, (tпл = 2120ºС). Алюминиймен – интерметалдық қоспалар TiAl және TiAl3 оттекпен титан, балқу температуралары tпл - 195ºС, 2130ºС, 2020ºС болатын, келесі қатар тотықтарын TiO2, Ti2O3 және TiO, түзеді. Титан темірмен титанның интерметалдық қоспасын TiFe (46,2% Ti) түзеді, TiFe2-нің балқу температурасы өнеркәсіптік құймаға жақын және 1430ºС құрайды. Стандартты түрде FeTi өзінің құймасындағы құрамға негізделген: әр түрлі маркалар үшін оның минимальды құрамы 20-дан (ФТи 20, 25, 30, 40, 65) 68% - ға (ФТи 68) дейін болады.
Al-дің құрамы 3%-дан бастап, Si 0,5-тен 8%-ға дейін, көміртек 0,1-ден 0,4% және зиянды қоспалармен шектелетіндермен (Р, Cu, S және т.б. элементтермен).
49. Шикіқұрам материалдары
Титан әр түрлі минералдардың құрамына кіреді: ильмениттің (FeO · TiO2 53%-дан жоғары емес TiO2), рутилдің (TiO2 - 90 - 95%), ферровскиттің (СаO · TiO2 58,4% TiO2) және сфенның (C2Ti(SiO4)O 40,7% TiO2).
FeTi-ді алудың негізгі шикізаты ретінде, ильмениттің дайын өнімі қолданылады. FeTi өндірісінде қолданылатын, ильмениттің титанды дайын өнімінің құрамында 50 - 64% TiO2, 0,08 - 0,20% P, 0,05 - 0,10% Cr2O3, и 1,5% Н2О болуы керек. Оны 1100 - 1150ºС температурада, S-ті 0,1 - 0,5%-дан 0,04%-ға дейін төмендету үшін және FeO-ның Fe2O3-ке өтуімен ильмениттің кристалдық торын бұзу мақсатында қышқылсыздандырғыш күйдіреді, бұл дегеніміз үрдістің термиялығын арттырып, титанның қолданылуын жоғарылатады және алюминийдің шығын төмендетеді.
2(FeO · TiO2) + 1 / 2О2 = Fe2O3 + 2TiО2
FeTi өндірісі үшін, сондай-ақ, металдық титанның қалдықтарында қолданады. Қалдықтар, құрғақ, брикеттеудің жоңқасы немесе темір ыдыста қапталған болуы қажет.
Өңдегіш ретінде, екіншілік альминий (0,1 - 1мм фракциясы 55%-дан төмен емес, 1 - 3мм 25% -дан төмен емес және 0 - 0,1мм 30%-дан төмен емес) сеппесін қолданады. Алюминий сеппесін, алюминийдің форсунка арқылы қысылған ауамен еруі арқылы немесе дұрысы Ar немесе N-ның инертті газдарымен алады.
Пульверизацияның ең жоғары өнімділігі 710 - 750 ºСтемпературада қарастырылады.
Г.Ф. Игнатенкомен арнайы араластырғышта сұйық алюминий әктасымен және темір қабыршағымен дайын өнімді араластыру арқылы алынатын, кен өңдегіш қоспаны алу технологиясы жасалған, ол өндірістің технико-эканомикалық көрсеткіштерін жоғарлатуды қаматамасыз етеді. Шикіқұрамға берілетін алюминийдің ең жоғарғы шамасын, егер алюминийдің (температура 50ºС-тан астам емес) салқын дайын өнімі 660 - 680ºС-қа дейін қыздырылған болса. Өте жоғары температура кезінде, араластырғышта, араласу үрдісін бұзатын настылдар түзіледі. Моношикіқұрамға қолданылатын температура 100 - 200ºС.
Титанның қатты силицидінің Ti5Si3 түзілуне байланысты құймадағы кремнйдің 5 - 5,5% - ға дейінгі мөлшері титанның біршама бөліп алынуына % және құймада қалған алюминийдің мөлшерінің азайуына әкеп соғады.
Құймадағы титанның қатынасы Ti / (Si + Al), құйманың құрамның айтарлықтай өзгерістері кезінде тұрақты болып қалады, сондықтан да шикіқұрамдағы кремнйдің құрамын арттырған тиімдірек. Бұл сеппені (3 мм-ден астам емес) 45 - 75% FeSi-ге беру арқылы жүреді..
Флюс ретінде балғалы (3 мм) әкті қолданады, құрамында 90% СаО және 1%-дан астам емес С бар.
Темір термиялық тұнбасында бай темірлі аз фосфоритті (Р 0,017% - дан астам емес), ірілігі 5 мм-ден астам емес кенді қолданады. Кенді, ылғалдылықты алып тастау үшін кептіріп алады, құймада қолданылатын кварциттің құрамында SiO2 95%-дан аспауы керек және 5 мм фракцияға дейін ұнтақталуы керек.
Кварцит, қайнатылған тұз сияқты (5 мм-ден астам емес фракциядағы) үрдіс жағдайын алюминийі көпіршігінің түйіршіктерінде глиноземді қабық еруі нәтижесінде және қождың тұтқырлығын азайту үшін балқыту алдында кептіреді.
Титанның қалдығын кептіреді және 100 - 150ºС температурада балқыту алдында балқымалы құйманы қояды.
50. FeTi - ды карботермиялық балқыту
Титанның екі тотығын өңдеу жылудың біраз шығынын қажет етеді. Қуатты электр пештерде титанды көміртекпен өңдеуге болады, алайда осыған байланысты қолданыс таппаған, титан құймасының темірмен және көміртекпен құймасы алынады.
Электр пештерінде карботермиялық өңдеу арқылы тек қана келесі титан құймаларын алады:
1)Феррокарботитан (20 - 25% Ti, 5 - 8% С, 1 - 2% Si, 1 - 2% Al, остальное железо). Әдетте, феррокарботитанды қуаттылығы 500кВт – ке дейінгі пеште жүргізеді. Ережеге сай, электродпен бір фазалы пешті қолданады. Пешке ильмениттің және активті өңдегіштің қоспасын, мысалы, жартылай кокс немесе ағаш көмірді тиейді. Пештегі жылу концентрациясы өте жоғары болуы керек, яғни тигельді мүмкіндігінше өте жіңішке етіп таңдап алады. Жұмысшы кернеу, ережеге сәйкес, 50 - 75В құрайды. Тигельдің материалы – көміртек. Өңдеу үрдісі кезінде басында, титан еритін, сұйық темір ваннасы түзіледі. Титанның ек тотығын өңдеу жай жүреді, және қождар титанның ек тотығының ≈ 20%-ын құрайды. Қождың сұйық қозғалмалылығын жақсарту үшін, оған күйдірілген әкті қосады. Көміртектің шығымы артқан кезде, титанның екі тотығына жақсы әсер ететін, кальций карбидінің түзілуі жүреді. Бірақ бұл жағдайда да көміртек 5 - 8% болған кезде құрамында Для улучшения жидкоподвижности шлака в него добавляют обожженную известь. При 25% - дан кем емес титан бар құйм қиын алынады.
Қождағы SiO2-нің құрамын рутилді беру арқылы жоғарлату өңдеу шартын жақсартпайды, керісінше, қож тұрақты болып, сәйкесінше, өңдеу жағдайы нашарлайды. Алайда, тәжірибелік түрде сәйкес келетіндер бұл әдіс бойынша жарияланбаған.
Силикотитанға қатысты келесіні айтуға болады:титан құймаларындағы көміртекті азайту бойынша жүргізілген көптеген жұмыстардан кейін, кремний көміртекті қысатыны, оған ұқсас жағдайда алюминий қоспасы әсер ететіні белгілі. Бұны төмен көміртекті титан құймаларын балқыту кезінде қолданады. Мұндай құймалар үшін пештердің қуаттылығы 500кВттан аспайды, тигель көміртекті болып келеді. Мұндай құйманы алуға арналған шикіқұрамның құрамы келесідей: 47% (51,2% TiO2) ильменит, 28,5% кварцит, 24,5% ұсақталған кокс. Мұндай шикіқұрамнан алынған құйма келесілерден тұрады: 29 - 30% титан, 17 - 20% кремний, 1,8 - 2% көміртек, қалғаны темір. Кернеу 50 Вт құрайды, 1 кг құймаға кететін элект энергиясы ≈ 12кВт / сағ. Шикіқұрамдағы кварциттің шамасын жоғарлату кезінде құрамында 30% кремний және 0,1 - 0,3% көміртек бар құйманы алуға болады. Сәйкесінше кремний қышқылын толық немесе аздаған шамада бокситпен алмастыру арқылы құрамында төмен көміртек бар кремний – алюминий – титанды құйманы алуға болады. Шикіқұрамнан 35% ильменитті (51,2% TiO2, 26,5% кварцит, 13% боксит, 25,5% ұсақталған кокс) үздіксіз әдіспен құйманы 31,5% титанмен балқытқан, 12 - 14% алюминиді, 8 - 10% кремнийді, ≈ 1% Mn, ≈ 2% С, қалғаны темір алынған. Екі құйманы да төмен шикіқұрамды пеште үздіксіз балқытады, осыған орай титанның бөліп алу дәрежесі 70 - 75%-ға жеткен, шикіқұрамдағы кремнийдің немесе алюминийдің жоғары мөлшерін көміртектің төмен шамасында осы элементтердің құймадағы сәйкесінше жоғарлауымен береді. Электр энергияның шығыны пештің қуаттылығына байланысты 10 - 14кВт · сағ / кг құрайды.
51. FeTi - ды алюмотермиялық балқыту
БҰҰ-да FeTi –ді алудың ең кең таралған әдісінің бірі болып, дайын өнім тотықтарын келесі реакциялар бойынша алюмотермиялық өңдеу саналады:
TiO2 + 4 / 3Al = Ti + 2 / 3Al2О3 = 2495кДж / кг оксида
SiO2 + 4 / 3Al = Si + 2 / 3Al2О3 = 4074кДж / кг оксида
2FeO + 4 / 3Al = 2Fe + 2 / 3Al2О3 = 4003кДж / кг оксида
2 / 3Fe2O3 + 4 / 3Al = 4 / 3Fe + 2 / 3Al2О3 = 5359кДж / кг оксида.
Темір тотықтары толық 99% өңделеді, кремнезем 90%-ға дейін, ал титан тотығы 75 - 80%-ға. Қожда қалған титан, қиын өңделетін, төменгі тотықтар (шамамен Ti және Ti2O3 арасында) түрінде болады. FeTi өндірісінің технологиялық тізбегі 1 суретте көрсетілген.
FeTi-ды ажырамалы жартыдан немесе бірнеше бөлімшелерден тұратын, жиналмалы шойынның мойындығында балқытады. Мойындық, аумағы отқа төзімді кірпіштермен жабдықталған, арбада орналастырылады. Мойындықтың қабырғаларын қыздырылған күйде балғалы магнезит (95%), сұйық шыны (0,7%) және отқа төзімді саздың (4,3%) қоспаларымен су ерітіндісімен торкретирлеу әдісімен футерлейді. Футеровканың ені 10-15 мм. Футеровканың басқа да әдістерін қолданады, мысалы, еденге магнезитті көпіршіктің қабатын себедіде, ал мойындық қабырғаларын асбестпен жасап үстіне саз жағады. Торкретирлеу – футеровканың ең дамыған әдісі.
Арбадағы дайындалған мойындық, шикіқұрамға арналған бункерлермен, мойындыққа беруге арналған шнектермен, шаң ұстау және вентиляцияға арналған қондырғымен жабдықталған, балқыту камерасына беріледі.
Балқыту үрдісін төменгі үйіндімен жүргізеді, бұл дегеніміз балқыту үрдісінің алдында мойындыққа шамамен 200 кг шикіқұрам себеді, оның үстіне үйілген қоспаны (селитр + магнит жоңқасы). Үйілген құйманы арнайы электрлі үйіндімен немесе магнит жоңқасымен өртейді. Экзотермиялық үрдістер қарқынды болған кезде, мойындыққа шнектің көмегімен бункерде дайындалған шикіқұрамды береді. Шикқұрамның алдын ала балқу жылдамдығы әдетте шамамен минутына 300 кг құрайды, ваннаның беті 1м2 болғанда. Мұндай жылдамдық ваннаны балқу кезінде жылу шығынын азайтатын, шикіқұрамның жіңішке қабатымен, қапталуын қамтамасыз етеді.
Титан технологиясы
Титанды жоғары жиілікте құрылымды материал ретінде қолданады, титанның дайын өнімін қиын көп сатылы қайта өңдеу технологиясы бойынша алады. Алғашында дайын өнімдерді қуаттылығы 10 – 15 МВА кен өңдегіш пештерде жоғары титанның қожын алу үшін жүргізеді.
Шикіқұраммен берілетін коксик ильменит құймасынан темір тотығын өңдеуді қамтамасыз етеді, нәтижесінде титан тотығының құрамы TiО2 шамасында 82 - 84%-ға жетеді, ал FeО-ның құрамы 3 - 4%-ға дейін төмендейді. Қождың шығатын кездегі температурасы шамамен 1700ºС.
Екінші сатыда титан қожын, титанның төрт валентті хлоридін TiCl4 алу үшін, көміртектің қатысуымен газ түріндегі хлормен хлорлауға түсіреді.
Титан қожының артықшылығы ретінде, оны, титанның төменгі тотықтарын ауның жоғары тотығына дейін қышқылсыздандыру әсерінен салқындату кезінде өздігінен сеппеленуіне икемділгі саналады.
Ti3+ - ді қышқылсыздандыру келесі реакция бойынша жүруі мүмкін:
Fe2+ + 2Ti3+ = Feo + 2Ti4+,
Канададағы төмен сортты ильменит кендерін өңдеумен алынатын қожды зерттеу кезінде электр пешіндегі антрцитпен жасалған.
Қождың негізгі фазасы: (71 - 72% TiО2) олардың ішінде 12% Ti2О3, 9% FeО, 1% Fe – жер бетінде жоқ элемент армалит, ол тек айлы грунтта (Апполо - 11) бар.
Арамалколит темір марганецті титанод Mg0,5Fe0,5TiO5 түрінде болады. Қождың көпіршігін хлорламас бұрын көміртекті қосылыстармен брикеттейді. Брикеттерді хлорлауды, шахталы электрлі қарсыласу электрлі пеші түрінде болатын, арнайы реактор – хлораторда жүргізеді. Брикеттердің құрамындағы көміртекті оттекпен байланыстырады, төмен температурада хлорлау реакциясының өтуін, бұл реакцияны қайтымсыз қылатын, қамтамасыз етеді:
TiО + C + 2Cl2 → TiCl4 + CO,
Ti2O3 + 3C + 4Cl2 → 2TiCl4 + 3CO,
TiO2 + 2C + 2Cl2 → TiCl4 + 2CO.
Титан тотықтарын хлорлаумен қатар, хлоридтердің түзілуіне әкелетін, басқа да тотықтармен өзара әрекеттесу реакциясы жүреді: SiCl4, FeCl2, AlCl3 және т.б.хлоридтердің айтарлықтай артықшылығы болып, тотықтағыларға қарағанда, балқудың температурасы және қайнаудың төмен температурасы. TiCl4 - tпл = 249К, tкип = 409К.
Бірінші сатыда TiCl4 келесі реакция бойынша Mg – мен өңделеді:
TiCl4 + 2Mg = Ti + 2MgCl2.
Бұл үрдісті температурада қарсыласу пештерінде жүргізеді, осы сатыда алынатын титанның ысқышы, кейін вакум пештерінде кешенді титанның құймасын алу үшін қайта балқытылады. Өзіндік құн құрылымында әрбір сатыдағы шығындар құрайды: титан қождарының өндірісі 6%, шикіқұрам дайындау 5%, брикеттерді хлорау және TiCl432%-ке дейін тазарту, TiCl4 – ті магнимен 57% өңдеу.
53 Ферровольфрам өндірісі
FeW және оның қосылыстарының қасиеттерін қолдану аумағы
Вольфрам – жылтыр – ақ түсті металл ρ = 19,3гр / см3, tплав = 3380○С, tкип = 5400○С. Вольфрам көміртекпен карбидтер түзеді W2C, WC, tплав = 2550○С, tкип = 2870○С. Кремниймен W3Si және WSi2 түзеді балқу температурасы2327, 2165○С Қышқылсыздандырғыштармен WO2, W4O11, WO3 тотықтарын түзеді, түзілу жылуы 56,5, 3110, 840МДж / моль, tплав = 1327,800, tвозг = 1377○С. Темірмен ферровольфрам (62,2% W) және Fe7W6 (73,8% W). Болат балқыту өнеркәсібінде вольфрамды құйма түрінде темірмен қоспалаушы элемент ретінде қолданады. Стандарт W құрамының 65% - дан төмен болмауына негізделген. FeW – ның өнеркәсіптік түрлерінің температурасы 2500○С – тан астам емес.
Вольфрам, 1781 жылы химик Карл Шеелемен тунгстен (швед тілінен аударғанда ауыр тас) минералынан, кейіннен шеелит деп аталған, вольфрамды ангидрид ашылды және ұсынылды.
FeW алғаш рет 1892 жылы алюминотермиялық әдіспен, металдық вольфрамды электрлі шамдарда жіптерді дайындау үшін, қолдану арқылы, алынды және А.Н.Ладыгинмен ұсынылды. 1990 жылы вольфрам карбидінің негізінде қатты құймалар алына бастады. FeW түріндегі вольфрам құрылымды және құрал-сайманды болатты (Кесте 1) қоспалау үшін қолданылады.
W және Mo, темірге қарағанда, оттекке химиялық ұқсастығы аз. Сондықтан да олар, ұшқыш заттардың , дистиляциялы қышқылсыздандырудың түзілуі әсерінен қышқылсыздандырғыш (вакуумда W Ғе-ді қышқылсыздандыра алады) ретінде қолданылмайды. ФВ70, 65 маркаларындағы FeW – ді қуаттылығы 2,5 – 5 МВа кен өңдегіш пештерде С и Si – ді сарқып алу арқылы өңдеп алады. Негізгі маркалардың құймаларын алюмотермиялық әдіспен балқытады.
Вольфрам болаттың беріктілік және ағындық аралықтарын жоғарлатады, соққыға және тозуға қарсы тұрады, жоғары температурада тығыздықты және қаттылықты жоғарылатады және өздігінен шынығу қасиетін тудырады, магнитті болаттарда жанғыш ақаулардың түзілу мүмкіндігін азайтады. Болатты қоспалау үшін барлық W – ның 80%-дан астамы қолданылады. W концентрациясының жоғарылауымен соққының тұтқырлығы, қайта қызуға қарсы тұрақтылық жоғарылайды және шынықтырылу тереңдігі төмендейді, яғни бұл кезде берік WС түзіліп, болат С және W – мен қосылып жылу өткізудің және пісірудің жұмсақ морт сынғыштығы төмендейді. Құю немесе көбікті металлургия әдісімен алынған, карбидтер түрінде, W, жоғары қаттылыққа және тозуға төзімділікке ие металлокерамикалық құймалардың (мысалы, 85 – 90 % WC, 5 – 15 % Co) құрамына кіреді. Бұл құймалар кесетін және бұрғылы құрал – саймандарды, сымдарды орауға арналған біліктерді және т.б. жасау үшін қолданылады. Мұндай құймаларға Mo, Nb, Ta, Ti карбидтері кіреді.
Вольфрам, хром, никель және т.б. жоғары электр өткізгіштік, жылу өткізгіштік және тозуға төзімділік қасиетке ие және турбин жинақтарын, поршендердің тез тозатын қақпақтарын жабу үшін қолданылатын, элементтер құрамына кіреді. Шет елдік зерттеулер негізінде құрамында Fe, Cu 3 -10 % Ni бар вольфрамды құймаларды қапталған снарядтардың ұштарын жасау үшін қолданады. Бұл құймалардың сапасы, урандыкімен салымтырғанда жоғары болады: 2% Мо и 0,75% Ti. Өте жоғары бұзылу қасиеттерін сипаттайтын, W құймасының ұштары, уранның негізіндегі құймаларға қарағанда улы және радиоактивті емес. W бұл жиналу шамындағы жіптер және спиралдарды алуға арналған негізгі метал. Бұл дегеніміз жұмысшы температура 2100○C - 2800○С болғанда өте жоғары беріктілікке ие. W қосылуы химия және мұнай өндірісінде катализаторлармен жұмыс жасайды. Құрамында 0,05 - 1% қоспа бар таза W – ні алады, WO2 – ні сутекпен өңдеу, қатты W – ні құю оның балқу температурасының жоғары болуына байланысты шектелген, бұйымдарды қолдану үшін W – ні қолданады. Қытайда, БҰҰ – сіз 232,5 · 103тонн, әлемдік қор бойынша жалпы 957 · 103тонн құрайтын, шеелиттің CaWO4, вольфрамиттің (FeMn)WO4, ең үлкен қорлары бар. КНР – де, W өндірісі бойынша барлық қуаттылықтар бағынатын, «Huaxing» вольфрам бірлестігі ұйымдастырылған. АҚШ-тың тау бюро болжамдарының негіздері бойынша, стратегиялық металдардың зерттелген қорлары, капиталдық тұрғыдан 37 жылға жетеді. Mo - 93 жылға, Nb - 220 жылға, Mn - 147 жылға, Ni - 87 жылға, Со - 77 жылға, Cr - 537 жылға.
Осыған байланысты, Mo – ның 86,7% - ы Чилиде және АҚШ – та, W – ның 56,1% - ы Канадада, Түркияда және АҚШ-та орналасқан. W – ның жылдық өсімі 6 – 10% Cr – дыкі 58%, Co –ныкы 10 – 20 %, Mn – дыкы 6 – 12 %, Mo - ныкы 1%, FeSi 5 – 8%, кристалдық кремнидәкә 4 – 7%-ға күтілуде.
54 W қасиеті
Реттік саны 74, ат.массасы 183,85 ρмонокристалл = 19,3 - 19,2гр / см3 = 3683К, tкип = 6203К, балқу жылуы = 8,05кДж / моль булану жылуы = 775кДж / моль. Балқу энтропиясы 2,19, буланудыкы 118,9Дж / моль К.
W оттекпен WO2, W4O11, WO3, W18O49, W20O58 тотықтарын және т.б. қатарын түзеді.
W – ғы оттектің ең жоғарғы еруі - 0,005% температура 1973К болған кезде. Түзілу жылуы WO3 ΔН0298 = 831,7кДж / моль. 1073 К кезінде оның сублимациясы біліне бастайды. WO3 – тегі жиынтықты қысым температураға байланысты (1273 К – ге дейін) келесі шамамен анықталады. кПа.
PWO3 = (- 27400 / T) + 14,03. W3O – ның кристалдануы кезінде W және WO2 диссосацияланады. W, WO2 диоксидтері 873 К температурада түзіледі. Ол күкіртті және тұзды қышқылдарда ерімейді. Азотты қышқыл оны WO3 – ке дейін қышқылсыздандырады. Соңғы тотықта берілген қышқылда және суда ерімейді, балқымалы қышқылда сілтінің ерітіндісі, тотығы және фторидінің түзілуімен ериді. Тотықты түзу реакциясы үшін: W(тв) + 3 / 2О2 = WO3(ж), W(тв) + 3 / 2О2 = WO3(т), W(тв) + О2 = WO2(тв).
55 Вольфрам жүйелері
а) W - Fe жүйелері
W – ның массалық құрамы 60% - дан астам болғанда, құйманың балқу температурасы 2850 К, сондықтан да W – ны пештен сұйық құйманың шығуымен бірге алу мүлдем мүмкін емес, кремнийдің құрамы шамамен 4% болғанда, құйманың балқу температурасы 2500 К – нен кем емес. Шынықтырылу тереңдігінің тығыздығы 13,8 – 15,5 гр / см3құрайды. Al, W –мен WAl12, WA5, WA4 алюминидтері түзіледі.
б) W - C жүйелері
Бұл жүйеде карбидтер түзіледі: 2W + C = W2C, W + C = WC. Температура 1300К болған кезде келесі реакция жүреді: 2W + 2CO = W2C + CO, W + 2CO = WС3 + CO2 С болған кезде С монооксидінің регенерациясымен. ρW2C = 17,15гр / см3, WC = 15,5гр / см3, tплав = 3068 и 3078К.
в) W - Si жүйелері
W - Si жүйесінде силицидтер W3Si2, WSi2, 3W(тв.) + 2Si(тв.)= W3Si(г), W(тв.) + 2Si(тв.) = WSi2(тв) түзіледі, tплав W3Si2 = 2583K. WSi2 = 2338K. WSi2 үшін энтальпия температураға байланысты өзгереді.
56. Вольфрамның кендері және дайын өнімдері
Құрамында W бар шамамен 15 минерал белгілі, бірақ өнеркәсіптік мағынада 4-еу: ферберит, гюбнерит, вольфрамит және шеелит. Сондай-ақ, тунгстенит (WS2), тунгститтер [WO2 (OH)2], антуанит (Al2W2O9 · 3H2O), мпоророит [(Al,Fe)2 W2O9 · 6H2O], гюбнерит және ферберит жеке кездеседі, әдетте олар Mn және Fe бір бірін минерал торында толықтыра алатын изоморфті қоспа (вольфрамит) түзеді.
W кендері орташа шамамен 0,2 - 0,5% WO3 құрауы мүмкін, сирек 1%-дан асады. Олар жиі Al, Sn, Cu, Asминералдарын және т.б. элементтерді қосады. Вольфрамды кендердің негізгі кен орындары солтүстік Кавказда, Оралда, Алыс Шығыста, Орта Азияда, Қазақстанда орналасқан. Вольфрамның негізгі бай кендері АҚШ-та, Испанияда, Португалияда, Боливияда, Австрияда, Қытайда, Бирмада қазып алынады.
Барлық кендер байытуға гравитациялық әдіспен, соның ішінде отсадкада, концентрациялық үстелдерде және шлюздерде жүргізіледі. Концентрациялар WO3-тің 55%-дан астамын құрайды. Fe-ге бай кендер электромагнитті сепараторларда жоғары тиімділікті магнитті өрістерде қосымша байытудан өтеді. Шеелитті флотациямен немесе электростатикалық сепарациямен бөледі. Мұндай түрдегі кендерді флотациялау сульфидтерді бөлу үшін және концентраттарды енгізу үшін қызмет етеді.
Шеелитті кендер майлы қышқылдарда ( олеинды қышқыл, натрий олеаты, сұйық сабын) флотациямен байытылады. Көбіктендіргіш ретінде қарағай майы немесе креозол қолданылады.
57. FeW - ді көміртек - силикотермиялық әдіспен алу
FeW – ді алу үшін ЧЭМК-да В.Л.Гусаровпен жасалған, болатты пештен сорып алу арқылы балқытудың көміртекті – силикотермиялық әдісі қолданылады. Вольфрам O2 – ге аздаған химиялық ұқсастыққа ие, тотықтардан кремний, көміртек және алюминиймен өңделуі мүмкін:
2 / 3WO3 + Si = 2 / 3W + SiO2,
2 / 3WO3 + 2C = 2 / 3W + 2CO,
2 / 3WO3 + 4 / 3Al = 2 / 3W + 2 / 3Al2O3.
Пештің ваннасын магнезитті кірпішпен футерлейді (қаптайды). Балқыту үрдісі кезінде магнезитті футеровка беті арқылы біртіндеп FeW – ды орналастырады және жұмысшы футеровканың мәні бойынша металдық гарнисаж болып саналады. Қожды шығарып тастағаннан кейін ваннаны еденде орналасқан тұтқыр болатпен және дайын құймадағы ұсақтаудың қатты қалдықтарымен толтырады. Балқыту үшін, вольфрамның дайын өнімін, мұнайлы және құмды кокс, грануляцияланған FeSi (ФС 65 - 75), болат жоңқасын және шаңды және қалдықтарды қайта балқыту арқылы алынатын құрамында W бар қожды қолданған. Шикіқұрамның құрамын қоспалардың құймаға өтуі арқылы келесі шамада есептейді: Mo - 100%, P - 100%, Al - 15%, S - 15%, Sn - 15%. Ағып өту сипаттамасына бойынша физико-химиялық айналу және операцияларды қолдану арқылы сәйкесінше балқыманы 3 кезеңге бөлуге болады. Алайда кезеңдердің айырмашылығы жоқ. Соңғы үшінші кезеңнен кейін пеш ваннасында 3 - 8%, Mn - 1,7 - 4,5%, C - 0,2 - 2% байланысты жоғары Si құрамды FeW бар, ал ондағы вольфрамның концентрациясы 50 - 55% - ға дейін төмендеген. Бірінші кезеңде құйманы, оған қожды қосу кезінде өтіп, оларды оттекпен қышқылсыздандыру нәтижесінде, дайын өнімді пешке тиейтін, Si, Mn, С байланысты рафинирлеу:
2 / 3WO3 + Si = 2 / 3W + SiO2,
2 / 3WO3 + 2Mn = 2 / 3W + 2MnO,
2 / 3WO3 + 2C = 2 / 3W + 2CO,
2FeO + 2Mn = 2Fe + 2MnO,
2FeO + 2C = 2Fe + 2CO.
Кезеңнің басында пешті электрофильтрлерде шаңдарды қайта балқыту кезінде алынғанымен, құрамында жоғары мөлшерде W бар қожбен және батарейялы циклонның шаңымен толтырады. FeW – ның тұтқырлығын азайту үшін, пешке балқыту температурасын төмендететін, болат жоңқасын салады, сосын дайын өнім үйіле бастайды.
Пеште қышқылсыздандырғыш қож түзіледі, құрамында: 16 - 23% WO3, 15 - 20% FeO, 28 - 32% SiO2, 10 - 15% MnO, 8 - 10% CaO, 1 - 3% MgO, 2 - 4% Al2O3 бар. Рафинирлеу жылдамдығын жоғарылату үшін, қож және металдың температурасын, пешті жоғары қуаттылыққа қойып жоғарылатады. Электродтар пештің жұмысы кезінде қожға тиелген. Егер олар жоғарыласа, қождың электрлік қарсыласуын, оны кокс жүктемесімен көпіршіктендіре отырып, арттырады. Осыған орай, электродтар шығарылады да қожға тиеледі және метал жақсы қыздырылады. Бірінші кезеңнің жалпы ұзақтығы 4-4,5 сағат, кезеңнің соңында дайын өнім кокспен, екінші кезеңнің 10 - 12% WO3мөлшердегі жұмысшы қожын алу мақсатында, көміле бастайды. Бірінші және екінші кезеңде дайын өнімнен W және Fe – ді өңдеу кокс көміртегінің әсерінен жүреді:
2 / 3CaWO4 + 2C = 2 / 3W + 2 / 3CaO + 2CO,
1 / 2FeWO4 + 2C = 1 / 2(W + Fe) + 2CO.
W және Fe – ді өңдеу кезінде, үшінші кезеңде қожды өңдеуге дейінгі металда қалған, Si және Mn қатысады:
2 / 3CaWO4 + Si = 2 / 3W + 2 / 3CaO + SiO2,
2 / 3CaWO4 + 2Mn = 2 / 3W + 2 / 3CaO + 2MnO,
1 / 2FeWO4 + Si = 1 / 2(W + Fe) + (SiO2),
1 / 2FeWO4 + 2Mn = 1 / 2(W + Fe) + 2(MnO).
Бірінші кезеңнің соңына қарай метал вольфрам және оның қосылыстарының стандартты мөлшеріне ие болады. Құйманы талдаудан кейін екінші кезең құйманы сорып алуға көшеді, екінші кезең шамамен 1-1,5 сағат құрайды, жұмысшы кернеуді 179 - 180В, 149В-қа дейін төмендетеді. Яғни металды неғұрлым көп қыздыру үшін және оның тест түріндегі жағдайын қамтамасыз ету үшін. Дайын өнімнің үйіндісін аздаған көлемде береді. W және Fe-ді өңдеу үшін, коксты үйеді, алынған қож келесі құрамға ие, %: WO3 - 10 - 12, FeO 24 - 26, SiO2 32 - 34, CaO 10 - 12, MgO 14 - 16, MgO 2 - 4, Al2O3 2 - 4.
Қожды көбіктендіргіш жағдайда ұстайды. Тиелетін кокстың мөлшерін төмендету керек болған жағдайда, электродтар жоғары жаққа орналасуы мүмкін, яғни ашық электродты доға пайда болады. Металдың қайнауы төмендейді, сорып алу кезінде оның тұтқырлығы жайлы сөз болған кездегі. Пешке дайын өнімнің үйіндісін бірінші және екінші кезеңдерде үйме машиналардың көмегімен береді. Қалтадағы дайын өнім бұрылғыш лотка арқылы машинаның хоботты лотогына беріледі, оның бұрылысынан кейін қалтаны қождың бетіне қарай түсіріп жайлап қожға береді.
Екінші кезеңдегі құйманы сорып алуды жұмысшы аймақта орналасқан ЧЭМК жүйесімен арнайы машинада жүргізеді (1 Сурет).
Пештегі құйма арнайы қасықпен көміртекті болаттан батырып алынады. Сыйымдылығы шамамен 50кг. Қасықты металмен суы бар бакқа тиейді, арнайы қондырғыда салқындатады және құйманы қаққылайды. Қасықтарды алмастыру құйманы суда салқындату кезінде жүргізіледі. Құйманы тегіс сорып алу үшін пештің ваннасын 180мин -1 жиілікте айналдырады. Дайын өнімнің әрбір қабатына металддың қатаң анықталған шамасы сорып алынады. Үшінші кезеңнің негізгі мақсаты ретінде WO3-ті қождан кремниймен қайта өңдеу, FeSi-ді 0,25% WO3-қа дейін. Метал, қож және марганецтен өңделетін кремниймен байытылады. Құймадағы концентрация W үнемі 65 - 72 до 52 - 54%-бен төмендеп отырады. FeSi-ді кокспен қоспасы бойынша 30-40 мин бойына үлеспен береді, жалпы шығын кезінде соңғыныкы 100 кг-дан кем емес, WO3 концентрациясын төмендеткен кезде сынықтағы қож жарықтанады, ашық-жасыл түске еніп. Тағы да бір құрамы 0,25% WO3 –тен кем емес (әдетте 0,05 - 0,15%) сынамаға талдау жүргізгеннен кейін, оны пеште 10-15 минут бойына ұстап тұрады. Сосын құрамында 0,05 - 0,2% WO3, 0,3 - 2% FeO, 45 - 50% SiO2, 15 - 20% MnO, 25 - 32% CaO болатын соңғы қож шығарылады. Қож шығарылғаннан кейін пеште келесі құрамдағы метал қалады, %: W 66 - 70, Si 5 - 7, Mn 0,7 - 2,5, S - 0,03 - 0,14, C 0,1 - 0,2. Егер қождың құрамында WO30,3%-дан астам болса, онда оны қайта балқытуға жібереді. Балқыту үрдісі кезінде қалыпты технологиялық үрдістің бұзылуы қарастырылуы мүмкін, оларды болдырмау үшін белгілі бір шараларды қолдануды қажет етеді. Егер, сорып алу алдында жоғары құрамдағы С, Si, Mn құйма алынса, онда пеште үйілетін дайын өнімнің мөлшерін арттыру керек. Концентрацияның WO3 мөлшері жоғары болған кезде, қож және металдың температурасын, пешке кокстың аздаған құрамын сала отыра, жоғарылату керек. Қож бұл кезде көпіршіктенеді, электродтар тереңге түседі. Қышқылсыздандыру С, Si, Mn жылдамдығы артады. Бірінші және екінші кезеңдерде қожбен WO3 жоғары мөлшерімен жұмыс жасау кезінде гарнисаждың қатты бұзылуы жүреді. Бұл жағдайда, WO3-ті өңдеуге арналған кокстың мөлшері артады, ал пештің баурайларын құйма қалдықтарымен немесе тұтқыр құймамен толтырады. FeW өзіндік құнының негізгі бөлігін дайын өнім (жалпы құнның 96 - 98%-ы) құрайды, сондықтан да құйманы алу үрдісі кезінде, вольфрамның қалдық газдар және шаңдар қожымен шығынын төмендету үшін арнайы шаралар қолданады. Буланатын вольфрамды ұстап алу үшін, WO3 және WO2түрінде дайын өнімнің үйілуі кезінде шаң түзіледі. Пештерді батареялы циклондармен және электрофильтрлермен жабдықтайды, возгондар салқындату кезінде конденсацияланады және жинағыш электрофильтрлерде құрайды: 1,7% Bi, 0,4% Cu, 0,4% As, 1,4% Zn, 0,25% P, 0,3% S, 7 - 8% CaO, 0,2 - 0,3% MgO, 9 - 10% SiO2, 10 - 14% FeO, 3 - 4% Al2O3, 10 - 12% MnO және сілтілі металдардың тотықтары. Бұл шаңды арнайы электр пеште қайта балқытады және түсті металлургия зауытына қайта өңдеу үшін жіберілетін құйманы 40 - 50% Pb, 5 - 8% Sn алады, ал қожды 35 - 40% WO3 –пен FeW балқытатын пешке қайтарады. Батареялы циклондарда ұстап алынған шаңдар, пешке тиелетін шикіқұрамның құрамына ұқсас, оларды сондай-ақ брикеттегеннен кейін балқымада да қолданады.
Алынған FeW-ның орташа шынайы құрамы келесідей, %: W - 74,3%, Si - 0,22, Mn - 0,16, C - 0,14, S - 0,07, P - 0,028, Cu - 0,11, Sn - 0,1, Pb - 0,001, Mo - 1,45, V - 0,001, As - 0,01. FeW – ның 1 тоннасына шамамен 1530 кг вольфрамның дайын өнімі (60% WO3), 108кг, FeSi (ФС 75), құм кокс 85 кг, болат жоңқасы 102 кг, SiCa 44кг, электродты масса электр энергия шығыны 3550 кВт/сағат болғанда 40 кг шығындалады. Вольфрамды бөліп алу, әдетте, 99% құрайды. Кейбір жағдайларда, FeW-ді 2 пешті қолдана отырып, 2 сатылы сұлба бойынша балқытады. Бірінші пештің қуаттылығы жоғары емес 1000 - 3000квА. WO3 және FeO – ны ағаш көмірдің көміртегімен өңдеу шикіқұрамға қождың тұтқырлығын төмендету үшін әкті беру арқылы және келесі құрамдағы металды алу үшін: 81% W, 0,4% С, 0,2% Si, 0,4% Mn, 0,03% P, ал қожды 10 - 15% WO3 бірінші пешке қайта балқытуға үшін қайтарады, вольфрамның шаңмен және газбен шыққан артық шығыны 3 - 4%-ға жетеді.
58. FeW - ді және лигатураны алюминотермиялық әдіспен алу
В.Г.Елютинмен жасалған алюминотермиялық әдіспен FeW – ді жоғары құрамды вольфраммен алады, сондай-ақ вольфрам лигатурасын хроммен және никельмен алуға болады:
2 / 3WO3 + 4 / 3Al = 2 / 3W + 2 / 3Al2O3.
FeW – ді алуға қолданылған шикіқұрам сондай-ақ Mo, Fe, Si тотықтарына ие. Сондықтан да негізгі реакция ретінде келесі үрдіс қарастырылады:
2 / 3MoO3 + 4 / 3Al = 2 / 3Mo + 2 / 3Al2O3,
SiO2 + 4 / 3Al = Si + 2 / 3Al2O3,
2 / 3Fe2O3 + 4 / 3Al = 4 / 3Fe + 2 / 3Al2O3.
Балқыту үшін, көп жағдайда, КМШ – 1 маркалы шеелитті дайын өнімді қолданады, КМШ - 2, КМШ – 3 дайын өнімінің шамасы, кремнийдің стандартты құрамын FeW алу үшін, оларда кремнеземнің құрамы жоғарлайтындықтан, шектеледі. Көрсетілген реакция бойынша бөлінетін жылудың мөлшері құйманы балқытудың жоғары температурасының және оның қожбен жақсы бөлінуінің әсеріне құйманың қалыпты өтуін қамтамасыз етпейді. Сондықтан да, балқыманы 3 фазалы магнезитті футеровкамен жабдықталған 1000кв · А температуралы ДСП – 1,5 түріндегі электр пешінде жүргізеді. Пеш ваннасының диаметрі 800 – 1000 мм, биіктігі 1200 мм түсірілімді ванна, қожға арналған шығару тесігіне ие, электродтар графиттелген диаметрі 200 мм. Келесі құрамдағы шикіқұрам қолданылады: шеелиттің дайын өнімі 100кг, біріншілік Al - 23кг, темір айналмасы 3кг, темір қабыршағы 4 - 5кг, әктас 1кг. Вольфрамды бөліп алуды жоғарылату үшін шикіқұрамға қождың қабығын, алдыңғы балқытудың металдық қалдықтарын және ұстап алынған шаңды қосады. Тигельдің көлеміне байланысты балқытуға дайын өнімнің 2500 – 5000 кг жұмсалады. Зерттеулер, балқыманы көбіктендіргіштің орнына брикеттелген шикіқұрамды қолдану арқылы беру тиімді екенін көрсетті, яғни дайын өнім түйіршіктерінің өлшемі 0,5 мм – ден аспайтындықтан және осыған орай вольфрамды бөліп алу шамамен 4%-ке жоғарылайды. Қождағы WO3-ның құрамы, W-нің қожбен 0,7 - 0,3% жоғалуы кезінде, төмендейді. Брикеттеуді, әдетте, байланысушы қоспалармен, жүргізеді, дайын өнімнің ылғалдылығы дайын өнім 81% және алюминий көпіршігі 19% болғанда 1,5 - 2,6% құрайды және басқа да қоспаларды пеш бункеріне бөлек салады. Пештегі балқыту пешке 100 – 150 кг брикетті бергеннен кейін басталады, жағуды 3 кг темір қабыршағының, электр пештерінде брикеттерге себетін алюминий көпіршігін 1 кг оталдырғышпен тұтатады. Ішінде құйма түзілгеннен кейін, электродтарды түсіріп электрлі жүктемені жинайды. Алдын ала балқыту үрдісінде шикіқұрамды 50 - 55кг / мин көлемде тиейді, 65Вольт кернеу кезінде ең жоғарғы жүктеу 6 кА, осыған орай электродтар қожға төмен түсіріледі. Шикіқұрамды пешке тиеу ұзақтығы 36 – 60минут (балқытуға берілетін шикіқұрамға байланысты, пешке берілетін қалдықтардың саны балқытуда 300 кг-нан аспауы керек) құрайды. Егер, балқыту кезінде қож көпіршіктенсе, онда 20 кг темір қабыршағын салады. Шикіқұрам үйіліп болғаннан кейін, тигель жасалады, сосын қожды өңдейді, оған 10 – 15 минут бойына аздаған құрамда алюминий іріліктерін 5 – 10 кг салады. Сосын үзінді жасап (10 – 15 минут) қожды шығарады. Егер қожда WO3 0,5%-тен астам болса, онда оны қайта балқытуға жібереді. Әдетте, құйма қалдықтарын және бай қождарды қайта өңдеуді арнайы балқытуда жүргізеді. Балқымалы камерада жүргізілетін балқыту үрдісінде шаң және возгондарды электрофильтрмен ұстап алады. Брикеттеуді дозалау және балқыту бөлімшелерінде газдарды соруға және барлық шаңдарды жинауға арналған жүйе бар, бұл дегеніміз вольфрамның тиімді қолданылуымен анықталады. Пеште FeW құймасы қалады. Сонымен қатар, W 45 - 48% болған кезде, W-нің жоғары құрамымен (Mo 8 - 10%, Si 2 - 4,5%, Al 5 - 8%) құйма қабаттары түзіледі. Құймадағы қабатты бөлгеннен кейін оны қайта балқытады және темір кені және әк пен рафинирлейді, алынған құйманың құрамында: 25 - 30% W, 5 - 6% Mo, 0,2 - 0,6% Si, 0,4 - 0,6% Al болады. Үйінді қождардағы WO3 – тің орташа құрамы, көбік түзгіш шикіқұраммен жұмыс жасағанда 0,38% және брикеттелген шикіқұраммен 0,073% құрайды.
FeW – нің 1 тоннасына 1555 кг шеелиттің дайын өнімі, біріншілік алюминийдің 345 кг көпіршігі, 20 кг әк, 80 кг темір қабыршағы, 45 кг темір қимасы электр энергия шығын 425 кВт · сағат болғанда шығындалады. Вольфрамды бөліп алу 99%, жоғарылатады, дайын құйма құрайды: 83,15% W, 4 - 4,7% Mo, 1,25 - 1,28% Si, 6,9 - 7,5% Fe, 0,026 - 0,047% Cu.
Отандық және шет елдік зауттарда вольфрамды бөліп алуды жоғарылату үшін және алюмотермиялық әдіспен құйманы балқыту температурасын төмендету үшін (ХВ - 1, ХВ - 2) маркасындағы хром-вольфрамитті лигатураны балқытады, 30% вольфрамның құрамы 1 - 4% Mo, 0,5 - 0,8%Si, 1,2 - 6% Al, 0,1% C, 0,01% S, 0,02% P, қалғаны хром. Лигатура технологиясы Ni (ЭМН-нің құрамында 25 - 30%W, 0,5 - 3% Al, 1,5%-дан кем емес Si және 0,1% С) негізінде. Оны электр пештерінде алюмотермиялық әдіспен құймада араластыру арқылы алады. Қождың балқу температурасы 1573К.
59. Ванадий және оның темірмен қоспалары
Ванадий жылтыр – ақ түсті, нығыз, өте қатты метал, атомдық массасы 50,942, tпл = 1912○С, tкип - 3000○С-тан астам, тығыздығы 6,11г / см3, балқу жылуы 17,59кДж / моль, булану жылуы 444,14кДж / моль. Ванадий көміртекпен келесі карбидтер қатарын түзеді: V5C, V2C, V4C3, VC, V2C3, мұнда ең қаттысы болып 2830ºС температурадағы
VC карбид саналады. Si-мен ванадий силицидтерде V3Si, V5Si3, VSi2 қосылады, мұнда қиын балқитын болып 2147ºС балқу температурасында қиын балқитын V5Si3 саналады.
О2 мен ванадий келесі тотықтар қатарын VO, V2O3,V3O4, V2O5 1970ºС, 1967ºС, 1545ºС және 675ºС-да түзеді.
Ванадийда Al 35% -ға дейін ериді. V5Al8, VAl3химиялық қоспалары және басқалары орналасумен балқытылады. S –мен ванадий келесі сулфидтер қатарынV2S3, V2S5, VS, түзеді, мұнда балқу температурасы 1179 К төмен емес VS ең берік болып саналады.
V2O5 – CaO жүйесінде келесі құрамдағы ванадаттар бар: Ca · V2O5, 2CaO · V2O5, 3CaO · V2O5.
Температураны жоғарылатқан кезде FeO –мен ванадий тотығы V - V2O3 орнығып FeO · V2O3, 2FeO · V2O3 түзеді. V2O5 –ті алу кезінде қиын балқитындардың қосылуы ең негізгі рөл атқарады. Бұл қоспалардың түрінде V , оларды V2O5-ке дейін есептегенмен, кенде және қожда кездеседі.
V темірмен сұйық және қатты күйде де толық өз ара еріту қасиетіне ие. Құрамында 31% V бар құйманың температурасы 1468ºС.
FeV- ны болат балқыту өндірісінде қолдану үшін балқытады, оның құрамы: ФВд - 75 А және Б (V - 75%, C - 0,1 - 0,15%, Mn - 0,4 - 0,6%, Si - 0,8 - 1%, Al - 2 - 2,5%, P - 0,05 - 0,1%, S - 0,05 - 0,10%, Cu - 0,1%, As - 0,05%). ФВд 50А және Б: V - 50%, C - 0,15 - 0,3%, Mn - 0,2%, Si - 2%, Al - 2,5%, P, S - 0,10%, Cu - 0,2%. ФВд 35А және Б, С: V - 35%, C- 0,75 - 0,1%, Si - 2,5 - 3,5%, Al - 1,5 - 2,0%, P - 0,1 - 0,2%, S - 0,10%, Аs - 0,05%.
60. Ванадий кендері және кендерді бөліп алу
Жер шарындағы ванадийдің орташа қоры 0,015%құрайды, бұл дегеніміз мыс, қорғасын, молибден, вольфрамның және басқада сирек металдардың мөлшерінен асады деген. Ванадийдің ең кең таралған минералдары болып: урановандонат K2 · [UO2] · [VO4] · 3H2O · V2O5, ванадит Pb5 (VO4)3 · Сl, партронит V2S, деклаузит (Zn, Cu) P(VO4)ОH, ванадийсодержащий титаномагнетит - (Fe, V, Ti)3O4, кульсонит (Fe, V)3O4 саналады.
Өнеркәсіптік кендер келесі топтарға жіктеледі:
1) Жеке ванадийлі кендер - V2O5 3% -тен астам емес(кең таралған кендер),
2) түсті және сирек металдардың кешенді ванадийлі кендері - V2O5 1% -тен астам емес (карнотиттер, ванадиттің бокситтері),
3) Қара металдардан - V2O5 1% -тен астам емес (магнетиттер, титаномагнетиттер, шпатты қоңыр темірлер),
4) Жанғыш және басқа қазбалар - V2O5 1% -тен астам емес (асфальтиттер, битумдар, сланецтер, көмірлер, фосфаттар).
БҰҰ-дағы ванадийдің негізгі қорек көздері болып, құрамында 0,5 - 0,8% V2O5, 21 - 30% FeO, 32 - 60% Fe2O3, 2 - 5% TiO2, 4 - 16% SiO2, 2 - 7% CaO, 2 - 12% Al2O3, 0,03 - 0,08% S бар, Кусинск Орал, Бірінші Орал, Кашканар титан-магнитті кен орындары саналады.
61. Өндіру технологиясы
Кендегі ванадийдің төменгі мөлшері және оның құрамы, металдық және химиялық қайта өңдеу қатары түрінде болатын, өндірістің қиын технологиялық үрдісін анықтады (сурет 1).
БҰҰ-да пирометаллургиялық қайта өңдеу кең таралған:
1)агломерация немесе кесектеу әдістерімен құрамында ванадий бар кендерді балқытуға дайындау, 2) Домналық балқыту, 3) Шойынды деванациялау, 4) Ванадийді қождан бөліп алу.
Домналық қайта өңдеудің мақсаты – ванадийдің жоғары бөліп алу дәрежесі кезінде ≈ 83% кеннен ванадийлі шойынды алу.
Ванадийдің шойынға толық өтуі үшін үрдісті t = 1300 - 1350ºС –та және қождың негізінде 0,8 - 0,9 жүргізеді. Келесі құрамдағы шойынды алады: 0,5 - 0,6% V, 0,31% Si, 0,40% Mn, 0,07% P, 0,23% Ni, 0,04% S, 0,62% Cr және 4,2% С.
Содан кейін шойынды оттекті конвертерде диванацияға жібереді. Конвертерлі ванадий қожы 11 - 18% V2O5 ванадий құймасының Mn, Si-мен және басқада элементтермен өндірісі үшін немесе V2O5 өндірісі үшін химиялық қайта өңдеуге жібереді. Шойыннан ванадийдің қожға бөліп алу 88 - 90%. Конвертерлі қожды қайта өңдеу гидрометаллургиялық әдіспен жүргізіледі. Алынған тұнбаны филтрлейді, кептіреді 1000ºС-та жалынды пеште балқытады және металдық паддондарға құяды. Балқытылған ванадийдің техникалық пентоксидінің құрамында 87 - 97% V2O5 бар. Қождан ванадийді бөліп алу 80 - 85% құрайды. FeV өндірісі үшін негізгі түр ретінде, конвертерлік қождардан алынатын, техникалық пентоксид V2O5 саналады, оның құрамында 83%-дан аспайтын V2O5(марка 1) және 75%-дан аспайтын V2O5 (марка 2) бар. Қоспа ретінде: 1 - 2,5% SiO2, 1 - 1,8% TiO, 5,5 - 7% Fe2O3, 0,2 - 0,4% Al2O3, 1,5 - 2% CaO, 0,3 - 0,6% МgO, 2 - 3,5% (Na2O + H2O), 0,04 - 0,07% P, 0,1 - 0,3% S кездеседі.
Химиялық қайта өңдеуге түсірілетін қож ұсақтауға түседі, сосын, содамен бірігіп тартуға және әрі қарайғы күйдіруге (1123 - 1173К) жібереді. Күйдіру ұзақтығы – 3 сағат. Пештің барлық ұзыныдығы бойымен температураны жоғарлату, қожды жоғары температуралы аймаққа үздіксіз қожды тез суыту арқылы бері бойынша. Шикіқұрамның қышқылсыздандырғыш күйдіруінің мақсаты болып, темір, марганец, ванадий тотықтарын жоғарыға ауыстыру және ванадийдің еріткіш қоспаларын түзі.
Қожды қышқылсыздандыру үрдісі келесі түрде жүруі мүмкін:
2FeO · Fe2O3 + 1 / 2О2 → Fe2O3 · V2O3,
Fe2O3 · V2O3 + O2 → Fe2O3 + V2O5.
FeV- ны ванадийдің көміртекпен, кремниймен, алюминиймен пентаксидінің өндірілуімен алынуы мүмкін.Көміртекпен өңдеу, термодинамика заңына сәйкес екі реакция бойынша, кең таралған жоқ:
2 / 5V2O5(ж) + 2С(граф) = 4 / 5V(тв) + 2СO(г),
2 / 5V2O5(ж) + 14 / 5С(гр) = 4 / 5V(тв) + 2СO(г).
Ең тиімдісі болып, карбидті түзу арқылы реакция алу саналады. Егер, құйма 4 - 6% С құраса және оны көптеген қоспаланған V болаттарды балқыту кезінде қолдану мүмкін болмаса.
V2O5 – ті кремнймен өңдеу келесі реакция бойынша жүреді:
2 / 5V2O5 + Si = 4 / 5V + SiO2.
Біруақытта қиын өңделетін төмен тотықтарды V2O3 және VO түзе алады. Ванадийдің төмен тотықтарын өңдеу, ванадийдің силикатымен өңдеудегі сияқты қиын, сондықтан да шикіқұрамға, кремнеземмен байланысатын және ванадий силикаттарының түзілуін болдырмайтын, әкті береді. СаО болған кезде өңдеу реакциясы келесі түрге ие болады: 2 / 5V2O5 + Si + 2СаО = 4 / 5V + 2СаО · SiO2.
V2O5 алюминимен өңдеу келесі реакция бойынша жүреді:
2 / 5V2O5 + 4 / 3Al = 4 / 5V + 2 / 3Al2O3.
Ванадиі тотықтарын алюмотермиялық өңдеу үш үрдіс бойынша, ванадийдің жоғарғы бөліп алу дәрежесін қамтамасыз ететін, бұған балқытудың төменгі температурасы әсер етеді V2O5 (675ºС), бос энергияның үлкен өзгерісімен сипатталады.
FeV – ны БҰҰ-да, V2O5 – ті кремнимен өңдеу арқылы, FeSi және алюминиде қуаттылығы 3000кВА ДСП пешінде әк болғанда жүргізеді. V2O5 –ті кремнимен СаО-ның қатысында өңдеу келесі түрге ие болады:
2 / 3V2O5 + Si + 2СаО = 4 / 5V + 2СаО · SiО2,
2 / 3V2O3 + Si + 2СаО = 4 / 3V + 2СаО · SiО2.
FeV – ны балқыту үш кезеңнен тұрады:
Балқытудың бірінші кезеңінде V-ны балқытудың қайтымды өнімдерімен балқытады, құрамында жоғары кремний бар метал алады, оны екінші рекезеңнің өңдеу реакцияларын жақсы жүргізу үшін қыздырады. Құрамында төмен ванадий бар қожды пештен шығарып тастайды. ҚҰрамында жоғары ванадий бар қожды балқытудың бірінші кезңінде қолданады.
1 – ші кезеңдепеште, қайтымды қождан(1400кг), әктен (600кг), FeSi-ден (630кг), алюминиден (60кг), ванадий пентоксидінен (100кг), метал сеппелерінен және болат қималарынан (800кг) тұратын, шикіқұрамды бұзады. Өңдеу үрдістерінің нәтижесінде қождағы V2O5 –тің құрамы 0,25 - 0,35%-ке дейін төмендейді, ал металдыкі кезеңнің соңына қарай 25 - 30% ванади, 20 - 24% кремни, 0,3 - 0,5% С құрайды. Балқыту үрідісінің кезеңі 1сағ 20 мин – 1сағ 40 мин құрайды.
2 – ші кезеңденегізгі операциялар болып: V2O5 – ті кремнимен және алюминиймен өңдеу, құрамында 35%-дан аспайтын ванадий және 10 - 12% кремний бар металды алу, үйінді қожды беру және алып тастау. Екінші кезеңде пешке тиейді: ванадий пентаксидін (800кг), әкті (1400кг), 75% FeSi (150кг), алюминий (80кг). Шикіқұрам еріп болғаннан кейін метал мен қожды, ванадийді өңдеуді жылдамдату үшін, араластырады. Осы кезде металдың құрамында 6 - 8% кремний, ал қожда - 8 - 10% V2O5 болады. Содан кейін, ванадийді қождан өңдеп, FeSi және алюминийді тиейді. Кезеңнің аяқталуына 15 – 20 минут қалғанда метал сынамасын алады. Металдың құрамында 35 - 40% ванадий, 9 - 12% кремний және 0,4 - 0,6% С болуы керек. Екінші кезеңнің үйінді қождарында V2O5 0,35% -дан аспайды. Мұндай талдауды алу кезінде қожды пештен шығарады. Бұл кезеңнің ұзақтығы – 1сағат.
Үшінші (равинирленген) кезең – металда кремнимен ерітілген, V2O5 – тенванадийді өңдеуді, оның құймадағы мөлшерін төмендету арқылы және берілген құрамдағы металды алу арқылы жүргізеді. Үшінші (рафинирленген) кезеңнің басында пешке ванадийдің 700 кг пентоксидін және 700 кг әкті үйеді. Кезеңнің соңында метал мен қожды араластырады. Метал сынамасын алып, құрамындағы кремний 2% болған кезде, оны, әк сүтінен жасалған, магнезитті сыламамен шамот арқылы футерленген шөмішке түсіреді. І-ІІІ балқымаларының металдарының құрамы келесідей:
Кезеңнің ұзақтығы 40 - 60 минут. Үшінші кезеңдегі қождың құрамы 12 - 16% V2O5. Оны қождағышқа түсіреді және келесі балқытуда қолданады. FeV-ны құюды, салқындатудан кейін бұзып тастайтын, тік шойын шөмішінде жүргізеді. Құймаларды тазартады, ұсақтайды және металдық банкаларға жинайды. Шикіқұрам материалдарының шығыны 1 т 1т 40% FeV келесідей:
Ванадий пентаксидінде - 1,75% V2O5 - 860кг;
Металдық қалдықтарда - 340кг;
75% FeSi - 400кг;
Алюминийде - 80кг;
Әкте - 1350кг;
Болат қималарында - 20кг;
Графитты электродтарда - 30кг;
Электр энергия шығыны - 1500кВт.
FeV – ны балқыту кезінде ванадийді бөліп алу 98,9 - 99,85% құрайды, ал ванадийді тура бөліп алу дәрежесі, әдетте, 54 –тен 60% аралығында болады. Балқыманың алюмотермиялық әдісті қолдану, төмен құрамдағы С (0,02 - 0,06%) FeV – ны алуға мүмкіндік береді. Балқыту үрдісінің қалыпты жүруіне қажет, жылудың шамасын төмендету үшін, шикіқұрамға әкті салады. Шикіқұрам ірілігі 1 – 3 мм ванадий пентоксидінен, Аl көпіршігінен, болат жоңқасынан және әктен тұрады. Металдың ең жоғарғы алынуы ванадий пентоксидінің массасына байланысты әктің 30 - 40% - да жүреді. Нәтижелер, Мg тотығын аздаған көлемде қосу арқылы жақсарады. Металдың құрамында 82 - 84% V, 1 - 2% Si, 0,05%-дан аспайтын Р, 0,1% Ti, 1,5% Mn, 0,1% -дан аспайтын S, 0,06% С бар. Қожда 4,5% V2O5 бар. Құймадағы ванадийдің бөліп алу дәрежесі 90 - 96% құрайды.
Қайтымды қождағы ванадийдің құрамы ДСП – да қыздыру арқылы балқыту кезінде төмендеуі мүмкін. Үрдісті қуаттылығы 350кВА ДСП-да берілген электродтарда шикіқұрамдағы алюминийдің жетіспеушілігімен жүргізеді. Үрдіс аяқталғаннан кейін, қожды қыздыру арқылы, ванадийді өңдеу жағдайларын жақсарта отыра және металды тұндыру арқылы пешті қосады. Ванадийдің құрамы 1%-дан аспағандағы қожды құяды, ал металды V2O5 немесе FeO – мен алюминиймен рафинирлейді. Мұндай әдіс кезінде ванадийді бөліп алу 95 - 97%-ға дейін электр энергия шығыны 4,1 - 4,5кВт / сағ болған кезде шығындалады. (алюминий шығыны 1 - 1,2кг). Металлдың құрамында 80%-дан аспайтын ванадий және 0,25% С бар.
Алюмотермиялық әдіспен техникалық таза ванадийді (90%-ға дейін), таза пентаксидті V2O5 слюминиймен флюс СаО және СаF2 қосу арқылы алуға болады. БҰҰ зауыттарында құрамында 40 - 48% V, 1,2 - 2,8% Al, 1,8 - 4,6% Fe, 0,9 - 1,8% S, 0,06 - 0,1% С бар, Ni - V лигатураны алады, қалғаны никель электр пеште алюмотермиялық әдіспен алынады.
Дата добавления: 2018-08-06; просмотров: 868; Мы поможем в написании вашей работы! |
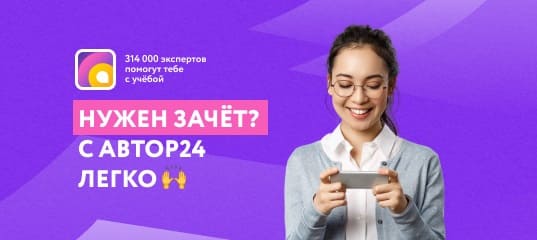
Мы поможем в написании ваших работ!