Применяемые станки, станочное приспособления и инструменты
Министерство образования и науки Российской Федерации
Федеральное государственное бюджетное образовательное учреждение
высшего образования
«Владимирский государственный университет
Имени Александра Григорьевича и Николая Григорьевича Столетовых»
(ВлГУ)
Колледж инновационных технологий и предпринимательства
Кафедра «Технология машиностроения»
Отчет о прохождении учебной практики
Выполнил:
Ст. гр. ТСП-115
Балдин Д. С.
Руководитель практики:
Новикова Ю. А.
Принял:
Новикова Ю. А.
Владимир 2018
Содержание
Введение. 3
Техника безопасности. 4
Деталь и заготовка. 9
Применяемые станки, станочное приспособления и инструменты.. 11
Заключение. 18
Список литературы.. 19
Введение
Сегодня технологиямашиностроения – это сложный, но интересный процесс. Работа технолога является важным элементом современного общества. Обеспечение потребителя итогом работы предприятия (изделиями) – один из основопологающих элементов обеспечения удобства жизни людей.
Технолог – машиностроитель в XI веке – это многоцелевой специалист, который должен уметь работать в разных сферах связанных с получением деталей. Оформление технологической документации – одно из главных занятий технолога. Правильный расчёт режимов резания на прямую влияет на качество получаемого изделия и скорости его получения. Так же это является “планированием” операций, что позволяет начать работу и избежать ошибок.
|
|
Сегодня количество инструментов, станочного приспособления и самих станков, очень обширно. Умение правильно подбирать их для определённых работ, сортировать в соответствии с ГОСТами и правильно составлять документы на новые виды, должно быть настолько же важным, как и само умение работать на новых станках для машиностроителей сегодня.
Цель: Составить технологическую документацию для определённой детали.
Задачи: 1. Выполнить чертёж детали и 3D модель в программе КОМПАС 3D.
2. Составить маршрут механической обработки детали.
3. Подобрать технологическое оборудование и инструмент для соответствующих видов обработки.
4. Разработать технологический процесс изготовления детали.
5. Выполнить эскизы последовательной обработки.
Техника безопасности
Техника безопасности - это система организационных и технических мероприятий и средств, предотвращающих воздействие на работающих опасных и вредных производственных факторов. Основное содержание мероприятий по технике безопасности и производственной санитарии заключается в профилактике травматизма, т. е. предупреждении несчастных случаев на производстве, и в частности в период прохождения учебной практики.
|
|
Техника безопасности при работе на токарном станке: Перед началом работы: привести в порядок рабочую одежду; застегнуть или обвязать обшлага рукавов, заправить халат (комбинезон), чтобы не было развевающихся концов, убрать волосы под головной убор; небрежно надетая одежда может привести к травме; убедиться в исправности станка; осмотреть ограждение зубчатых колес, приводных ремней и гитары станка; проверить, не оборван или заземляющий провод;проверить установку светильника местного освещения (свет не должен слепить глаза); проверить станок на холостом ходу и убедиться в исправности кнопок «пуск» и «стоп», органов управления, тормоза, систем смазки и охлаждения, подъемных и загрузочных устройств; работать на неисправном станке опасно; привести в порядок рабочее место: убрать все лишнее со станка и площади рабочего места; осмотреть и подготовить к работе приспособления, режущий и измерительный инструмент и крепежные детали; удобно установить тару для заготовок и деталей; проверить, исправна ли подножная деревянная решетка; порядок на рабочем месте — залог безопасности работы;
|
|
о неисправностях станка и электрооборудования немедленно сообщить мастеру или дежурному слесарю (электрику) и до устранения неисправности к работе не приступать.
Во время работы станка: при установке и съеме заготовок и деталей массой более 20 кг пользоваться подъемными устройствами, при этом надежно стропить заготовку (деталь). Освобождать от подвески заготовку (деталь) только после ее установки и надежного закрепления на станке; прочно закреплять обрабатываемые заготовки на станке (в патроне, центрах или на оправке). Не наращивать рукоятки ключа для закрепления заготовок в патроне, не применять подкладок между зевом ключа и гранями гайки. Не оставлять ключ в патроне после закрепления или освобождения заготовки; правильно и надежно закреплять инструмент. При установке резца применять минимальное число подкладок, перед включением станка убедиться в том, что пуск его никому не угрожает опасностью.
Перед тем как остановить станок, выключить подачу и отвести инструмент от заготовки; работать на режимах резания, указанных в справочнике или операционной карте; обязательно отключить станок при временном прекращении работы:
|
|
— измерении обрабатываемой заготовки, наладке и ремонте станка,
— уборке рабочего места, смазке станка и регулировке, при перерывах в подаче электроэнергии;
— не снимать и не открывать ограждений и предохранительных устройств; не снимать футляров с электрооборудования, не открывать дверей электрошкафов, не прикасаться к клеммам; не тормозить станок нажимом руки на патрон или заготовку, работать с отрегулированным тормозом;
— во время работы перекрывать зону резания защитным щитком; на станке, не оснащенном защитным устройством, работать в защитных очках или использовать индивидуальный защитный щиток, применять предохранительный щиток над патроном; при скоростном точении стали пользоваться резцами с накладными стружколомателями или стружколомающими канавками, при обработке чугуна — стружкоотражателями. Не убирать стружку на ходу станка. После остановки станка удалять стружку крючком и щеткой;
— в кулачковом патроне без поддержки центром задней бабки закреплять только короткие заготовки, более длинные поддерживать центром задней бабки;
— нежесткие валы обрабатывать в люнетах: не отрезать прутковый материал при большом вылете из шпинделя. Выступающий из нерабочей стороны шпинделя конец прутка ограждать трубчатым кожухом;
— не производить никаких измерений универсальными измерительными инструментами или калибрами на ходу станка;
— не раздвигать кулачки патрона до выхода их из корпуса;
— не работать на станке в перчатках или рукавицах; если палец забинтован, поверх бинта надевать резиновый Напальчник; вытирать руки чистой ветошью, не использовать для этой цели обтирочный материал, которым вытирают станок, так как можно поранить руки мелкой стружкой; следить, чтобы охлаждающая жидкость или масло не попадали на решетку и на пол в зоне рабочего места токаря. При обнаружении утечки масла из картеров станка немедленно вызвать слесаря;
— не облокачиваться на станок во время работы;
— при работе с невращающимся задним центром своевременно заполнять смазкой центровые от верстия заготовок; периодически проверять,
— не отходит ли задний центр. Не допускается работа с жестким центром при частоте вращения шпинделя свыше 150 об/мин;
— при обработке тяжелых заготовок (массой свыше 30 кг) применять самосмазывающийся центр; если патрон крепится к шпинделю на резьбе, применять стопорное устройство, предохраняющее патрон от самоотвинчивания; не допускать чрезмерного зажима кулачкового люнета на заготовке, периодически смазывать кулачки, своевременно заменять сработанные кулачки;
— работать только исправным инструментом; при получении инструмента из кладовой проверять, нет ли забоин на конусных хвостовиках инструмента, трещин в твердосплавных пластинках, сколов или выкрошившихся участков на режущих кромках. При получении резца проверять надежность механического крепления пластинки;
— если при прикосновении к станку ощущается удар тока, немедленно выключить станок и сообщить об этом мастеру или дежурному электромонтеру;
— при затачивании не подводить инструмент к торцу плоского круга; не допускать большого зазора между пЪдручником и кругом; не прижимать инструмент с большим усилием к кругу; пользоваться защитным щитком или очками.
После окончания работы: — выключить электродвигатель станка; привести в порядок рабочее место, очистить и смазать станок;
— аккуратно сложить на рабочем месте заготовки и детали.
Техника безопасности при работе на фрезерном станке:при фрезеровании можно травмироваться при неправильной установке детали и фрезы, неправильном управлении станком во время работы, попадании отлетаемой стружки на руки, лицо и глаза, затягивании пальцев под фрезу и т.д.
До начала работы: — приведи в порядок рабочую одежду (застегни обшлага рукавов, одень головной убор);
— проверь наличие рабочего и режущего инструмента и их исправность;
— проверь наличие защитного экрана и заземления;
— проверь исправность станка на холостом ходу.
Во время работы: — не пользуйся неисправным инструментом и тупой фрезой;
— не убирай излишки стружек руками или ветошью, не сдувай их, а удаляй стружку щеткой-сметкой;
— не отходи от работающего станка, не занимайся посторонними делами;
— не производи замер обрабатываемой детали при вращающейся фрезе;
— не подводи пальцы рук близко к вращающейся фрезе;
— не меняй скорости вращения шпинделя без разрешения учителя.
По окончании работы: — выключи станок от общей силовой сети;
— сними обрабатываемую деталь и фрезу, убери фрезу и рабочий инструмент на свое предназначенное место;
— убери станок щеткой-сметкой или ветошью;
— смажь машинным маслом все направляющие станка;
— убери рабочее место.
Техника безопасности при работе на сверлильном станке: опасности в работе: — Ранение глаз отлетающей стружкой при сверлении металла;
— Ранение рук при плохом закреплении деталей.
До начала работы: — наденьте спецодежду;
— проверьте надежность крепления защитного кожуха ременной передачи;
— надежно закрепите сверло в патроне;
— проверьте работу станка на холостом ходу и исправность пусковой системы путем включения и выключения кнопок;
— прочно закрепите деталь на столе станка в тисках или кондукторе. Поддерживать руками при сверлении незакрепленную деталь запрещается;
— перед самым началом работы наденьте защитные очки;
Во время работы: — не пользуйтесь сверлами с изношенными хвостовиками;
— сверло к детали подавайте плавно, без усилий и рывков, и только после того, как шпиндель станка наберет полную скорость;
— перед сверлением металлической заготовки необходимо накернить центры отверстий. Деревянные заготовки в месте сверления накалывают шилом;
— особое внимание и осторожность проявляйте в конце сверления. При выходе сверла из материала заготовки уменьшите подачу;
— во избежание травм в процессе работы на станке: а) не наклоняйте голову близко к сверлу;
б) не производите работу в рукавицах;
в) не кладите посторонние предметы на станину станка;
г) не смазывайте и не охлаждайте сверло с помощью мокрых тряпок. Для охлаждения сверла нужно пользоваться специальной кисточкой;
д) не тормозите руками патрон или сверло;
е) не отходите от станка, не выключив его.
— перед остановкой станка поднимите сверло от детали, после чего выключите электродвигатель.
После окончания работы: — после выполнения работы удалите стружку со станка с помощью щетки. Из пазов станочного стола стружку уберите металлическим крючком;
—не сдувайте стужку и не сметайте ее руками;
— освободите сверло из патрона и сдайте его учителю;
— приведите себя в порядок.
Деталь и заготовка
В этой работе мы рассмотрим деталь типа корпус (СПИН. 294. 276. 318. 14. 004). Тип производства – единичный\ мелкосерийный. Деталь имеет среднюю сложность.Габариты детали 135х99.Она имеет пазы, фаски и отверстия с маленьким диаметром. Обработка ведется с применением токарных, фрезеровочных, сверлильных операций, а так же производится развёртывание отверстия для получения меньшей его шероховатости. Деталь подвергается улучшению, а именно – термообработке (при закалке (в воде) при температуре 800°С и отпуске при температуре 350°С прочность стали будет примерно 40-45 HRC, что удовлетворяет условиям). Изделие применяется для закрепления валов в сложных конструкциях.
Рис. 1: Схема базирования детали Корпус СПИН. 294.276.318.14.004
Материал, применяемый для этого изделия – сталь 45 (Сталь конструкционная углеродистая качественная).
Расшифровка марки стали: марка 45 означает, что в стали содержится 0,45% углерода, а остальные примеси крайне незначительны.
Свойства: Удельный вес: 7826 кг/м3
Твердость материала: HB 10 -1 = 170 МПа
Температура критических точек: Ac1 = 730 , Ac3(Acm) = 755 , Ar3(Arcm) = 690 , Ar1 = 780 , Mn = 350
Свариваемость материала: трудносвариваемая. Способы сварки: РДС и КТС. Необходим подогрев и последующая термообработка.
Температура ковки, °С: начала 1250, конца 700. Сечения до 400 мм охлаждаются на воздухе.
Обрабатываемость резанием: в горячекатаном состоянии при HB 170-179 и σв=640 МПа, К υ тв. спл=1 и Кυб.ст=1
Использование в промышленности: вал-шестерни, коленчатые и распределительные валы, шестерни, шпиндели, бандажи, цилиндры, кулачки и другие нормализованные, улучшаемые и подвергаемые поверхностной термообработке детали, от которых требуется повышенная прочность.
Табл. 1: Химический состав стали 45
Методы получения заготовки: Выбраны приблизительные методы получения заготовки: это прокат и литье в землю. Сравним их: деталь в итоге весит 1,69 килограммов. Круг стали 45 диаметром 135 миллиметров весит 11,19 килограммов, а в случае с литьем – 2,5 килограммов. Расcчитаем КИМ (коэффициент использования материала):
Где: – масса детали;
– масса заготовки.
Протяжка:
Литьё:
При обработке заготовки полученной методом литья будет тратится меньше материала чем при протягивании, но КИМ 0,15 – тоже допустим в рамках мелкосерийного или единичного производства.
Сравним экономический показатель: Круг стали 45 будет стоить 240 рублей за килограмм, а литье – 500 рублей за килограмм. Если учесть этот фактор, то получится, что литьё более дешёвый метод(11,19 килограмм = 2685,6 рублей; 2,5 килограмм = 1250 рублей).
Но протяжка позволит нам получить оптимальную точность внешней поверхности для наибольшего диаметра детали, тем самым сократив время обработки и количество операций.
Выбираем метод получения протяжкой, так как этот метод сможет помочь достичь оптимальной точности поверхности.
Применяемые станки, станочное приспособления и инструменты
При обработке нашей детали задействуются два станка: Токарно-винторезный станок 16К20Ф3С32 – для выполнения токарных работ и для развёртывания; Сверлильно-фрезерный станок 2C150ПМФ4 – для выполнения фрезеровочных и сверлильных операций.
Табл. 2: Характеристика станка 16К20Ф3С32
Табл.3: Характеристика станка 2С150ПМФ4
Рис.2: Пример вида станка 16К20Ф3С32
Рис.3: Пример вида станка 1С150ПМФ4
Инструменты, применяемые для обработки детали:
При токарной обработке: Резец 2101-0007Т15К6 ГОСТ 18879-73 (h*b=16*16;L=80); Резец 2141-0056Т15К6 ГОСТ 18883-73(h*b=16*12;L=170;l=80;m=6,0); Резец 2130-0251 Т15К6 ГОСТ 18884-73(h*b=16*10;L=100;l=20;a=3); Резец 2130-0517 Т15К6 ГОСТ 18874-73(h*b=16*16;L=80;l=15;l1=30;a=8); Резец 2141-0201 ГОСТ 18883-73 (h*b=12*12; L=100; l=20; d=6; m=2,5).
При сверлении: Сверло 2300-2269 ГОСТ 886-77 (d=7,5;L=156;l=102) Сверло 2301-3568 ГОСТ 10903-77 (d=8;l=75;L=156).
При развёртывании: Развертка 2363-0068 H9 ГОСТ 1672-80 (d=7,0;d1=7,1;L=109;l=31).
При фрезеровании: Фреза 2214-0351 ГОСТ 26595-85 (D=50;d=22;d1=11,0;d2=18;d3=41;H=40;l1=20;l2=33); Фреза 2220-0217 ГОСТ 17025-71 (d=25,0;l=45;L=121); Фреза 2234-0355 ГОСТ 9140-78 (d=6;d1=6;L=52;l=8;l1=36;R=0,2).
Рис. 4: Сверло 2300-2269 ГОСТ 886-77
Рис.5: Резец 2101-0003 Т15К6 ГОСТ 18879-73
Рис.6: Развертка 2363-0068 H9 ГОСТ 1672-80
Станочное приспособление: Патрон 7100-0003 ГОСТ 2675-80; Тиски 7200-0209 ГОСТ 16518-96; Неподвижные опоры диаметром 29,7и 34, 9 миллиметров.
Рис.7: Тиски 7200-0209 ГОСТ 16518-96
Измерительные приборы: Штангенциркуль ШЦ-I-125-0,05 ГОСТ 166-89; НутрометрНИ 6-10-1 ГОСТ 868-82.
Табл. 4. Измерительные приборы
Тип | Модель | Цена деления, мм | Диапазон измерения, мм | Допускаемая погрешность, мм |
Штангенциркуль | Двухсторонние с глубиномером | 0,05 | 0-125 | 0,05 |
Нутрометр | Индикаторный | 0,01 | 6-10 | 0,005 |
Принцип работы нутрометра: Нутромер индикаторный вводится в измеряемое отверстие и устанавливается там перпендикулярно. После этого нужно отмечать отклонение стрелки на шкале. Если она склоняется влево от нуля, то размер на самом деле больше настроенного, если вправо – то меньше. Таким образом, если установить номинальный размер в 10 мм, а стрелка при этом сдвинется вправо на 15 делений, то фактически размер будет 9,85 мм, если же стрелка отойдет на такое же количество делений влево, то размер составит 10,15 мм.
Принцип работы штангенциркуля: - Измерение наружных поверхностей: для того, чтобы получить данные о внешних размерах изделия, его требуется зафиксировать в нижних губках инструмента. Для этого требуется развести его немного больше, чем сама измеряемая заготовка, а потом свести губки до упора. После этого можно снимать показания по основной и дополнительной шкале.
- Измерение внутренних поверхностей: для данной операции инструмент следует переместить в нулевое положение, после чего поместить губки для внутреннего измерения в заготовку, параллельно измеряемой плоскости. Далее следует разводить их до упора, что поможет зафиксировать их в одном положении и избежать больших погрешностей. Это подходит также для определения диаметра.
Заключение
Практическая работа выполнена путем решения поставленных задач. Нами были высчитаны оптимальные режимы резания и оформлена технологическая документация. Документарная часть подготовки операции является неотъемлемым элементом работы технолога. Правильный выбор оборудования и точный расчёт режимов резания может кардинально повлиять на ход работы, вплоть до серьёзных повреждений станка или инструмента.Так же правильность их выбора влияет на итоговое качество изделия: неправильно подобранные режимы или инструменты могут привести как к несовпадающим требованиям шероховатости, так и кполомки инструмента или станка, непоправимому браку детали. Про технику безопасности тоже забывать не стоит: её соблюдение поможет избежать повреждения при работе.
Список литературы
1. Режимы резания при фрезеровании. Фрезерование металла [Электронный ресурс]. – URL: http://metalcutting.ru.
2. Расчет норм времени при сверлении [Электронный ресурс]. – URL:https://studopedia.su/19_105223_raschet-norm-vremeni-pri-sverlenii.html
3. Расчет подготовительно-заключительного времени [Электронный ресурс]. – URL:https://lektsii.org/3-85274.html
4. Расчет норм времени. Расчет основного времени. Расчет вспомогательного времени [Электронный ресурс]. – URL:https://studopedia.su/19_105223_raschet-norm-vremeni-pri-sverlenii.html
5. Каталоги станков и кузнечно-прессового оборудования [Электронный ресурс]. – URL:http://stanki-katalog.ru/
6. Справочник технолога-машиностроителя. В 2 т. Т. 1 / под ред. А. Г. Косиловой и Р. К. Мещерякова. – 4-е изд., перераб. и доп. – М. : Машиностроение, 1986. – 656 с.
7. Справочник технолога-машиностроителя. В 2 т. Т. 2/ под ред. А. Г. Косиловой и Р. К. Мещерякова. – 4-е изд., перераб. и доп. – М. : Машиностроение, 1985. – 496 с.
Дата добавления: 2018-08-06; просмотров: 385; Мы поможем в написании вашей работы! |
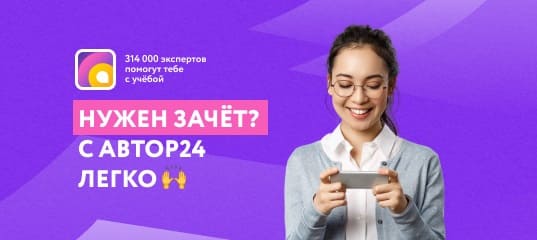
Мы поможем в написании ваших работ!