Последовательная схема производства
Рекристаллизационный отжиг необходим для снятия напряжений возникших после холодной прокатки, восстанавливает пластичность деформированного материала, способствует получению определенной величины зерна.
Рекристаллизационному отжигу в колпаковых печах подвергают холоднокатаный металл толщиной 0,50–2,50 мм марок сталей 08Ю, 08кп, 08пс, 08ЮПР, 08ЮП, 08ЮР, 08ЮТР, поставляемой по действующим стандартам и техническим условиям (ТУ) и зарубежные аналоги указанных марок сталей для производства экспортных заказов.
Технология рекристаллизационного отжига сталей в колпаковых печах производится по следующей схеме:
1. В отделение металл поступает со склада холоднокатаных рулонов на основании технологического паспорта.
2. Осуществляется подготовка стенда к отжигу. При подготовке стенда необходимо проверить:
а) величину зазора между верхним срезом крыльчатки и малым подовым кольцом;
б) состояние направляющего аппарата;
в) исправность стендового термоэлектрического преобразователя;
г) газопровод защитного газа, состояние выхлопа защитного газа;
д) поступление воды на охлаждение двигателя циркуляционного вентилятора;
е) состояние огнеупорной кладки;
ж) исправность ЦВ;
з) чистоту и количество песка для затвора.
3. Загрузка стенда металлом. Загрузка производится электромостовым краном с помощью клещей. Между рулонами укладываются конвекторные кольца для увеличения площади колпака защитного газа с металлом. Отверстия верхнего рулона закрывается крышкой. В стопе 4 рулона, общая высота стопы не превышает 5000 мм. Стопа накрывается муфелем с помощью клещевого захвата для транспортировки муфелей. Муфель должен быть исправен (наличие трещин и прочих дефектов не допускается). Оператор ПУ и термист проката заполняют карточку отжига.
|
|
4. Пуск печи. Перед пуском печи проверяют на герметичность стенд, муфель, песочный затвор. Для удаления воздуха из под муфеля производится холодная продувка защитным газом, затем производится продувка холодильников защитного газа.
Состав защитного газа: водород 100 %
Только после этого на стенд устанавливается колпак (желательно горячий), производится подключение колпакового термоэлектрического преобразователя, исполнительного механизма МЗО101125, включение 2-х штекерных разъемов. Затем осуществляется пуск печи.
5. Рекристаллизационный отжиг металла в печи.
Отжиг металла ведут в защитной среде 100 % водорода по одноступенчатому или двухступенчатому режимам в зависимости от марки стали, требуемых механических свойств, толщины полосы и массы садки.
Температура отжига при рекристаллизационном отжиге должна быть не более 850 °С.
|
|
Режим термической обработки
Режим термической обработки садки холоднокатаного металла, состоящей из 3-4 плотно смотанных рулонов, должен обеспечить их нагрев до заданной температуры с оптимальной скоростью, которая определяется требованиями к микроструктуре и свойствам готовой продукции. По мере увеличения скорости нагрева наклепанного металла увеличивается число зародышей новых зерен, возникающих в единицу времени, а следовательно, структура его к концу первичной кристаллизации становится все более мелкозернистой.
При отжиге в металле происходит рекристаллизация деформированного зерна феррита, коагуляция и сфероидизация цементита и рост зерен феррита до оптимальной величины. У нестареющих сталей при отжиге должны быть созданы условия для связывания свободного растворенных углерода и азота в стабильные нитриды и карбиды, а у стали, раскисленной алюминием, – для роста рекристаллизованных зерен сплющенной формы. Величина и форма зерна феррита после отжига определяется, кроме химического состава стали, еще и степенью холодной деформации, температурой отжига, скоростью нагрева, временем выдержки при температуре отжига и условиями охлаждения.
|
|
Оптимальная структура низкоуглеродистой листовой стали после отжига – феррит с однородными по размеру зернами с небольшим количеством мелкозернистого цементита и зернами округлой формы. С увеличением размера зерен феррита штампуемость стали улучшается, но ухудшается качество поверхности штампованных изделий. При этом поверхность приобретает шероховатость. В нестареющих сталях зерна феррита имеют несколько вытянутую форму (влияние алюминия). Такая микроструктура в плоскости листа крупнозернистая, а в плоскости, перпендикулярной листу – относительно мелкозернистая. Это обусловливает высокую штампуемость и хорошее качество поверхности листа.
Теорией и практикой выработаны два варианта термообработки холоднокатаных рулонов в колпаковых печах:
1. Садку рулонов нагревают с малой скоростью 50–150 °С/ч до температуры 680–700 °С для кипящих и полуспокойных сталей и до 700–720 °С для спокойных. Далее охлаждение со скоростью не более 40 °С/ч до температуры 120–180°С под муфелем (во избежание образования цветов побежалости на поверхности полосы) и окончательное остывание рулонов на воздухе.
2. Нагрев садки рулонов со скоростью 50–250 °С/ч, далее выдержка при температуре 450–600 °С, потом нагрев до температуры отжига (см. вариант 1), выдержка при этой температуре и охлаждение со скоростью 40 °С/ч.
|
|
При отжиге автомобильного листа режим нагрева с промежуточной выдержкой благоприятно сказывается на формировании микроструктуры и кристаллографической текстуры металла. Ферритные зерна получаются с большой (1,5–2,8) степенью вытянутости. Структура характеризуется однородным по ширине и толщине полосы большим (12–13,5) отношением компонентов кристаллографической текстуры {111}/{100}. Коэффициент нормальной анизотропии металла, отожженного по двухступенчатому режиму, составляет 2,3–2,45 (при непрерывном нагреве этот показатель 1–1,5).
Отжиг 2-х, 3-х и 4-х рулонных садок стали марки 08Ю толщиной 0,7-2,5 мм включительно способности к вытяжке ВОСВ по ГОСТ 9045-93 производиться по одноступенчатым режимам программ указанным в таблице 2 с регулируемой по этапам скоростью нагрева.
Таблица 2 – Режим отжига 2-х, 3-х и 4-х рулонных садок проката стали 08Ю толщиной 0,7–2,5 мм способности к вытяжке ВОСВ
Толщина полосы | Масса садки | Время нагрева до температур промежуточных этапов без выдержки (по стендовой термопаре) | Время нагрева до температуры выдержки (по стендовой термопаре) и время выдержки | Время регулируемого охлаждения до температуры | Общее время отжига | Номер программы | ||||||||
Этап №1 | Этап №2 | Этап №3 | Этап №4 | |||||||||||
мм | т | ч | °С | ч | °С | ч | °С | ч | °С | ч | ч | °С | ч | |
0,7-0,99 | до 65 | 3 | 460 | 3 | 520 | 5 | 550 | 4 | 690 | 12 | 2 | 670 | 29 | 65 |
66–70 | 3 | 460 | 3 | 520 | 5 | 550 | 4 | 690 | 13 | 2 | 670 | 30 | 66 | |
71–75 | 3 | 460 | 3 | 520 | 5 | 550 | 4 | 690 | 14 | 2 | 670 | 31 | 67 | |
76–80 | 4 | 460 | 3 | 520 | 5 | 550 | 4 | 690 | 14 | 2 | 670 | 32 | 68 | |
81–85 | 5 | 460 | 3 | 520 | 5 | 550 | 4 | 690 | 15 | 2 | 670 | 34 | 69 | |
86–90 | 5 | 460 | 3 | 520 | 5 | 550 | 5 | 690 | 15 | 2 | 670 | 35 | 70 | |
91–95 | 6 | 460 | 3 | 520 | 5 | 550 | 5 | 690 | 15 | 2 | 670 | 36 | 71 |
Примечание:
1. Температура отжига (термоэлектрический преобразователь, установленный на колпаке) не более 850°С.
2. Время выдержки под нагревательным колпаком с выключенными горелками – 1 час.
3. Скорость нагрева рулонов: на первом этапе – 73-147 °С/ч, на втором этапе – 20 °С/ч, на третьем этапе – 6 °С/ч, на четвертом этапе – 28-37 °С/ч.
График режима термообработки стали 08Ю представлен на рисунке 2.
Рисунок 2 – Режим термической обработки стали 08Ю
Переотжиг (повторный отжиг) проводят после отжига в колпаковых печах холоднокатаной стали, с целью восстановления поверхности от окисной пленки, ликвидации дефектов "ржавчина", "загрязнение" и "окисление". Производится в зависимости от массы садки в среде 100 % водорода при температуре под муфелем (690 ± 10) °С, программами отжига в соответствии с таблицей 3 (с произвольным нагревом до температуры выдержки).
Повторная обработка является отклонением от штатной технологии и может привести к получению несоответствующей продукции.
Таблица 3 – Режим переотжига (повторного отжига) стали
Масса садки, т | Общее время отжига, ч | Максимальный расход 100 % водорода, м3 | Номера программ отжига в среде отжига 100% водорода |
до 65 | 14 | 220 | 80 |
66–70 | 15 | 250 | 81 |
71–75 | 16 | 260 | 82 |
76–80 | 17 | 270 | 83 |
81–85 | 18 | 275 | 84 |
86–90 | 19 | 290 | 85 |
91–95 | 20 | 300 | 86 |
Автоматизация и механизация
Управление тепловым и режимным режимом печи осуществляется с помощью комплексом технических средств на базе ЭВМ типа СМ–2, установленной в вычислительном центре системой дистанционного регулирования, которая устанавливается в помещении тепловых щитов.
В систему автоматического дистанционного регулирования входит:
− стендовые хромель-алюмелевые термопары типа ТХА (преобразователь термоэлектрический);
− колпаковые хромель-алюмелевые термопары типа ТХА (преобразователь термоэлектрический);
− самопишущий токовый преобразователь Ш72;
− самопишущий токовый прибор КСУ–2–0,24;
− амперметры и вольтметры постоянного тока, типа М–1731;
− блоки двух- и трехпозиционные сигнализации и регулирования П1731, П1730;
− пускатели бесконтактного типа;
− исполнительные механизмы;
− исполнительные переключатели выбора рода работы.
На местных пунктах установлены приборы типа ДН для контроля падения давления газов, смешанного и защитного, лампочки аварийной сигнализации.
Контроль подогрева стопы рулонов осуществляется по стендовой термопаре, измеряющей температуру защитного газа в подмуфельном пространстве (5 ± 2 мм ниже подовой плиты). Контроль температуры рабочего пространства печи между колпаком и колпаковыми термоэлектрическими преобразователями, его горячий слой должен выступать из кладки на 50 мм ±1 мм.
В аварийную сигнализацию термического отделения входят:
падение давления смешанного газа, предел срабатывания ниже 588,0 Па (на каждые 2 стенда);
падение давления защитного газа (на 10 стендов). Предел срабатывания ниже 931,6 Па/ч;
падение давления эжекторного воздуха на группу из 40 стендов, предел срабатывания ниже 2 942,0 Па;
снижение потока воды через холодильник;
повышение температуры охлаждающей воды до и после АВЗ выше 60 °С, самопишущий прибор КСМ–2;
снижение расхода циркуляционной воды после насосов, 400 м3/ч, самопишущий прибор КСД–2;
снижение давления циркуляционной воды, 0,147 м3/ч, самопишущий прибор КСД–2;
верхний и нижний аварийные уровни воды в расширительном баке ВЧ 760 мм, НУ 1670 мм;
повышение объемной доли кислорода в защитном газе, прибор КСА–2, ЗУ–05.
Регулирование давления защитного и смешанного газа осуществляется на общем входе регуляторами РП–П, установка заданного давления осуществляется задатчиками типа установленными на тепловом щите № 2.
Для перевозки рулонов в другое отделение предусмотрены стальные тележки грузоподъемностью 240 т, скорость движения 0,6 м/с. Все средства измерения контроля представлены в таблице 4.
Таблица 4 − Перечень средств измерения, подключенных для контроля технологического процесса
Измеряемый параметр | Кол-во | Наименование | Предел измерения | Класс точности | Примечание |
Стендовая температура | 80 | 1)термоэлектрический преобразователь | 0–900 °С | 1 % | – |
2)нормирующий преобразователь | 0–900 °С | 0,4 % | – | ||
3)электронный прибор | 0–900 °С | 1 % | – |
Окончание таблицы 4
Зональная температура | 36 | 1) термоэлектрический преобразователь | 0–900 °С | 0,4 % | – |
2) нормирующий преобразователь УВИ | 0–900 °С | 0,4 % | – | ||
Давление коксодоменного газа | 16 | 1) дифманометр | 0–1569 °С | 1 % | – |
2) вторичный прибор | 0–1569 °С | 0,5 % | – | ||
Давление защитного газа | 3 | 1) дифманометр | 0–2451 °С | 1 % | – |
2) вторичный прибор | 0–2451 °С | 0,5 % | – | ||
Массовая доля кислорода в защитном газе | 80 | газоанализатор на кислород | 0–50 % О2 | 5 % | ‒ |
Массовая доля водорода в защитном газе | 10 | газоанализатор на водород | 0–6 % О2 | 2,5 % | ‒ |
Влажность защитного газа | 80 | 1) измеритель влажности | 0–100 | 0,5 % | ‒ |
2) потенциометр | 3,6–70 °С |
Транспортировка конверторных колец осуществляется электромостовым краном при помощи электромагнита.
К теплоэнергетическому силовому оборудованию относятся газо– и воздухопроводы колпаковых печей, которые подразделяются на:
− газо- и воздухопроводы нагревательного колпака;
− газопроводы смешанного и защитного газов, подводящие газ к стендам.
Инжектирующий воздух подается от вентиляционной станции, в которой установлены 2 вентилятора типа В14, В15.
Вспомогательное оборудование, служащее для получения защитной атмосферы, находится за пределами отделения.
Дата добавления: 2018-08-06; просмотров: 533; Мы поможем в написании вашей работы! |
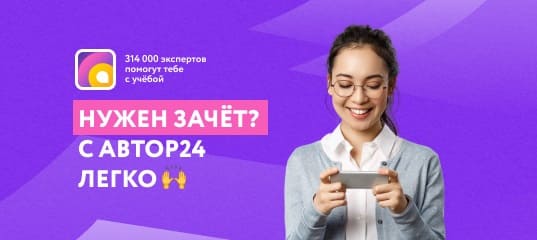
Мы поможем в написании ваших работ!