Самораспространяющийся высокотемпературный синтез (СВС)
Новый процесс получения нитридов, получивший название самораспространяющийся высокотемпературный синтез (СВС), был открыт в 1967 году академиком А. Г. Мержановым и профессорами И. П. Боровинской и В. М. Шкиро [7-20]. В основе метода лежит экзотермическая реакция, протекающая в режиме направленного горения. Процесс осуществляется в тонком слое смеси исходных реагентов после локального инициирования реакции и самопроизвольно распространяется по всей системе благодаря теплопередаче от горячих продуктов к ненагретым исходным веществам. В качестве исходных веществ используются металлы (неметаллы) II, III, IV, V, VI, VIII групп периодической системы в смеси с неметаллами. Возможно также в качестве исходных компонентов систем СВС использовать не только порошки металлов или неметаллов, но также и их соединения. Схематично процесс можно представить в виде:
; (1.1)
где – металл (неметалл) в твердом состоянии;
– неметалл в твердом, жидком или газообразном состоянии;
Z – твердый или жидкий продукт реакции;
X(i) – Mg, B, Al, Ti, Zr, Hf, V, Nb, Ta, W, Cr, Mo, Mn, Fe, Ni;
Y(j) – C, B, N2, Si, O2, S, Se;
Z – карбиды, бориды, нитриды, силициды, оксиды, сульфиды, селениды, интерметаллиды, твердые растворы, сложные композитные системы.
Процесс СВС характеризуется высокой температурой (2000-4000 ºС) и большой скоростью распространения фронта горения (0,5-15 см/с). Высокие температуры горения обеспечивают полноту превращения исходных элементов в конечные продукты и способствуют испарению примесей, поэтому целевые продукты имеют высокую чистоту. Большие скорости горения обеспечивают высокую производительность процесса [7, 21, 22]. Процесс СВС легко управляем. Имея ряд общих черт с технологическими процессами традиционной порошковой металлургии, самораспространяющийся высокотемпературный синтез характеризуется такой уникальной особенностью, как существование в течение протекания взаимодействия высокотемпературной среды, допускающей различные типы дополнительных внешних воздействий, посредством которых возможно регулирование структуры и свойств целевых продуктов. Изменяя условия горения (температуру, давление, соотношение исходных реагентов), можно в широких пределах регулировать химический и фазовый состав получаемых продуктов [7, 14-17].
|
|
Технология СВС относится к порошковым технологиям, но она принципиально отличается от технологии порошковой металлургии тем, что для осуществления синтеза и (или) спекания в первом случае исходные порошки сжигают, а не нагревают в печи. Ближе всего к СВС находятся металлотермические процессы [7, 20, 23-26].
|
|
При решении задач синтеза основное внимание должно уделяться нахождению условий, обеспечивающих полноту реакции и получение однофазных продуктов. Трудности связаны с тем, что нитридные пленки, покрывающие частицы исходного порошка азотируемого элемента в ходе синтеза, являются защитными и сильно тормозят процесс, что приводит к недогоранию. Вследствие этого, процесс СВС проходит в две стадии: распространение волны горения и объемное догорание [11]. Для получения однофазных нитридов необходимо обеспечить полноту процесса на стадии догорания. Так, при преодолении фильтрационных затруднений при подводе азота, возникла необходимость смягчения режима синтеза, для чего исходный порошок азотируемого элемента разбавляют одноименным нитридом.
Технология СВС нитридов устраняет многие недостатки, присущие технологиям печного и плазмохимического синтеза: высокая скорость, приводящая к высокой производительности процесса; отсутствие энергетических затрат на нагрев до высоких температур и выдержки при этих температурах из-за больших внутренних тепловых ресурсов системы; простота аппаратурного оформления; отсутствие сложного электротермического оборудования [7, 12, 15]. При этом чистота целевых нитридов не хуже чистоты исходных реагентов, так как загрязнения при синтезе не возникает [12, 15-17]. Кроме того, вследствие высоких температур горения происходит частичная самоочистка нитридов из-за испарения легкоплавких примесей.
|
|
Вместе с перечисленными преимуществами, технология СВС имеет и существенные недостатки, главным из которых являются фильтрационные затруднения, связанные с подводом внешнего азота в центральную часть образца, что приводит к неполному азотированию [23-27]. Кроме того, разбавление исходной шихты конечным продуктом синтеза, снижает производительность процесса. Так же, как и для технологии ПС, здесь, в большинстве случаев, также возможно получение целевого продукта в виде спека, который подвергается дроблению и измельчению для перевода в порошкообразное состояние. В добавление к сказанному необходимо отметить, что при использовании в качестве исходного сырья порошков азотируемых элементов, становится проблематичным получение наноразмерных структур, так как в этом случае размер частиц синтезируемого нитрида будет соизмерим или больше размера частиц исходных порошков азотируемых элементов.
|
|
О получении порошков нитридов вольфрама по классической технологии СВС информация отсутствует. По технологии СВС с использованием азида натрия получен не нитрид, а карбид вольфрама [28].
При этом использовалось следующее уравнение реакции [2]:
WiO3+2NaN3+0,75C→
→0,25WC+0,75Na2WO4+0,5NaCN+2,75N2; (1.2)
Как уже отмечалось выше, порошки в технологии СВС получают обычно путем дробления и размола первичного продукта горения, который чаще всего представляет собой пористый спек. При неполном измельчении продукта горения получают агломератные СВС-порошки, состоящие из частиц, образованных отдельными кристаллитами, т.е. монокристаллами с неправильной внешней огранкой, между которыми наблюдается значительное сращивание. Размеры частиц агломератных порошков обычно варьируются в пределах 10-200 мкм. Эти частицы могут быть пористыми.
Наибольший интерес представляет получение очень мелких монокристальных порошков, как микронных и субмикронных с размером частиц от нескольких мкм до 0,1 мкм, так и нанопорошков с размером частиц менее 0,1 мкм (100 нм).
Авторы [7, 29, 30] сформулировали обобщенные принципы уменьшения размера кристаллитов продуктов СВС:
– уменьшение размера частиц исходных реагентов, процессов рекристаллизации и агломерации зерен продуктов горения за счет: уменьшения температуры горения;
– увеличения скорости охлаждения продуктов горения;
– разделения частиц целевого продукта газовыми или конденсированными промежуточными слоями побочного продукта или разбавителя, замена исходных реагентов из чистых элементов, в частности, металлов, на их химические соединения, которые разлагаются в волне горения, превращение твердых реагентов в пар или газ в процессе горения;
– использование газофазных реакций в горении, процессов химической конденсации, растворение исходных реагентов и реализация реакций СВС в жидкой фазе, активация процесса СВС за счет: механических воздействий; ударных волн; гравитации; нагрева и закалки; электрических и магнитных полей, химическое диспергирование продукта СВС.
Дата добавления: 2018-08-06; просмотров: 436; Мы поможем в написании вашей работы! |
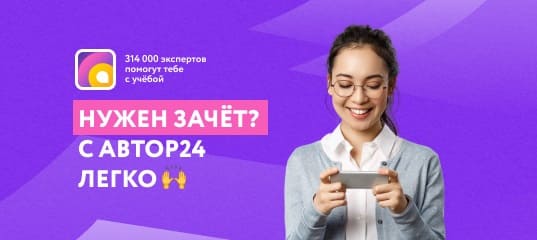
Мы поможем в написании ваших работ!