Механические и физические свойства деформируемых алюминиевых сплавов (ГОСТ 4784)
МИНОБРНАУКИ РОССИИ
Федеральное государственное бюджетное образовательное учреждение
Высшего образования
«Ижевский государственный технический университет имени М.Т. Калашникова»
(ФГБОУ ВО «ИжГТУ имени М.Т. Калашникова»)
Чайковский технологический институт (филиал) Федерального государственного бюджетного образовательного учреждения высшего образования
«Ижевский государственный технический университет имени М.Т. Калашникова»
(ЧТИ (филиал) ФГБОУ ВО «ИжГТУ имени М.Т. Калашникова»)
Кафедра «Промышленных технологий»
С.Н. Красильников
Материаловедение. ТКМ
Методические указания к выполнению контрольной работы
для студентов направления подготовки 23.03.03 «Эксплуатация транспортно-технологических машин и комплексов»
заочной формы обучения
Чайковский, 2018
8УДК 621.184.64
Материаловедение. ТКМ
Составитель: к.т.н., доцент С.Н. Красильников
2018 год
© С.Н. Красильников
Утверждено на заседании кафедры «Промышленных технологий» Чайковского технологического института (филиал) ФГБОУ ВО
«ИжГТУ имени М.Т. Калашникова»
Протокол № 6 от 29.03.2018 г.
Электронная версия в Word 2000 находится в Чайковском технологическом институте (филиал) ФГБОУ ВО «ИжГТУ имени М.Т. Калашникова»
Методические указания составлены в соответствии с программой курса «Материаловедение. Технология конструкционных материалов» для технических специальностей вузов. Методические указания предназначены для студентов заочнойформы обучения по направлению подготовки23.03.03«Эксплуатация транспортно-технологических машин и комплексов».
|
|
Методические указания являются руководством при выполнении контрольной работы.Приведены основные сведения о конструкционных материалах и их свойствах, методические указания содержат задания к контрольным работам и примеры выполнения заданий.
Работа № 1.
Основные механические свойства материалов.
Основные положения и расчетные формулы.
Прочность материала, его твердость,упругость, пластичность, ударная вязкость, выносливость относятся к механическим свойствам. Они являются основными свойствами конструкционных материалов и определяются по результатам испытаний.
Упругость, прочность и пластичность определяются при статических испытаниях на растяжение. Пример диаграммы такого испытания приводится на рисунке 1. Здесь по оси абсцисс откладывается продольная относительная деформация образца:
;
по оси ординат откладывается нормальное напряжение в поперечном сечении образца
|
|
,МПа.
В формулах использованы следующие обозначения: l0– длина ненагруженного измеряемого участка (начальная длина образца), мм; l – его длина при действии нагрузки, мм; P – нагрузка, Н; F0 – площадь поперечного сечения ненагруженного образца (начальная площадь), мм2.
Упругость – способность материала возвращаться к первоначальной форме после прекращения действия сил. Упругость характеризуется модулем упругости при растяжении (модулем жесткости) – свойство материала, характеризующее его жесткость
, МПА.
Прочность – способность материала сопротивляться разрушению или появлению остаточных деформаций под действием внешних сил. Прочность материала определяют параметры:
- предел пропорциональности – наибольшее напряжение, до которого сохраняется прямая пропорциональность между напряжением и деформацией
, МПа;
- предел текучести – напряжение, при котором рост деформации происходит без заметного увеличения нагрузки
, МПа;
Если площадка текучести по диаграмме растяжения данного материала отсутствует, то определяется условный предел текучести s0,2 – напряжение, вызывающее пластическую деформацию, равную 0,2%. Если масштаб диаграммы не позволяет определить напряжение, соответствующее деформации 0,2%, тогда установим пределы, в которых заключена искомая величина: sпц<s0,2<s1,0, где s1,0 – напряжение, которому соответствует, остаточная деформация, равная 1,0% (смотри рисунок 1). Можно определить величину s0,2,полагая, что кривую на участке от sпцдоs1,0 можно заменить отрезком прямой. При этом предположении приблизительное значение условного предела текучести можно получить при помощи формулы:
|
|
.
- предел прочности (временное сопротивление разрушению) – напряжение, которое равно отношению наибольшей нагрузки, предшествующей разрушению образца, к первоначальной площади его сечения
, МПа.
Предел прочности является обязательной характеристикой в стандартах классификации марок материалов.
Рисунок 1 –Определениеsпц,sв,s1,0
Пластичность – свойство материала изменять свои размеры и форму под действием внешних сил, не разрушаясь при этом. Показатели пластичности:
- относительное удлинение рассчитывается как отношение прироста длины образца после разрыва к его первоначальной расчетной длине, выраженное в процентах
,
где l1 – длина образца после разрыва, мм.
|
|
- относительное сужение определяется отношением уменьшения площади поперечного сечения образца после разрыва к первоначальной площади его поперечного сечения, выраженным в процентах
,
где F1 – площадь поперечного сечения образца в месте разрушения, мм2.
Твердость – способность материала сопротивляться поверхностной деформации под действием более твердого тела. Твердость определяют путем статического вдавливания в испытуемый материал стандартного тела. Существуют различные способы испытания на твердость. Наиболее распространенными из них являются (рисунок 2):
- твердость по БринеллюНВ. Испытания проводят с помощью стального закаленного шарика стандартного диаметра. Значение твердости вычисляют по формуле
, кгс/мм2
где P – прилагаемая нагрузка, кгс, D и d – диаметры шарика и отпечатка, мм.
По твердости, измеренной этим методом, можно судить о прочности при растяжении, так как между твердостью и прочностью существует следующая зависимость: для стали sв» (0,34 … 0,36)×НВ, для алюминиевых сплавов sв» 0,362×НВ, для медных сплавов sв»0,55×НВ.
- твердость по Роквеллу. Измерение осуществляют путем вдавливания в испытуемый материал стального шарика (HRB) или алмазного конуса (HRC). При испытании очень твердых материалов твердость обозначают HRА. Значение твердости в единицах HRCпримерно в 10 раз меньше, чем в единицах НВ, т.е. твердость 30HRCпримерно соответствует 300НВ. Между значениями твердости HRC и HRА имеется следующая зависимость:HRC = 2´HRА – 104.
Рисунок 2 – Методы определения твердости
- твердость по Виккерсу HV. В этом случае для определения твердости применяют четырехгранную алмазную пирамиду с углом между противоположными гранями, равным 136°. Значения твердости по Виккерсу и Бринеллю практически равны.
Вязкость – способность материала поглощать механическую энергию внешних сил за счет пластической деформации. Ударнаявязкость – способность материала сопротивляться разрушению под действием динамической нагрузки
,
,
где U(V) – форма надреза в образце; A – работа, затраченная на разрушение, кг×м; F – площадь поперечного сечения образца в месте надреза, см2 (рисунок 3, в формулу необходимо подставить площадь заштрихованного участка).
Рисунок 3 - Схема действия копра при разрушении образца
Выносливость – свойство металла сопротивляться усталости. Усталость – это процесс постепенного накопления повреждения металла под действием повторно-переменных напряжения, приводящих к образованию трещин и разрушению. Предел выносливостиs-1 – это наибольшее напряжение, которое выдерживает материал без разрушения при бесконечно большом числе циклов нагружения. Для определения предела выносливости стали можно воспользоваться зависимостью s-1» 0,43sв.
Испытание на выносливость (усталость) чаще всего осуществляют на вращающемся образце с приложенной постоянной изгибающей нагрузкой.
Задание на работу № 1.
Задача 1(по вариантам). Определить основные свойства стали: модуль упругости Е; относительное удлинение d; относительное сужение y; параметры прочностных свойств материала (пределы пропорциональности sпц, текучести s0,2, прочности sв) по заданной диаграмме (рисунок 4); твердость НВ; предел выносливости s-1.
Исходные данные:
№ варианта | l0, мм | F0, мм2 | P, Н | Dl×103, мм | F1, мм2 | l1, мм | № диаграммы |
1 | 125 | 490 | 3090 | 3,7 | 392 | 150 | I |
2 | 100 | 320 | 1680 | 2,5 | 272 | 130 | II |
3 | 80 | 180 | 810 | 2,0 | 135 | 104 | III |
4 | 75 | 80 | 530 | 2,6 | 57 | 84 | IV |
5 | 50 | 50 | 360 | 1,7 | 35 | 56 | V |
6 | 40 | 30 | 190 | 1,6 | 24 | 50 | VI |
7 | 30 | 20 | 160 | 1,2 | 18 | 39 | VII |
8 | 25 | 12 | 82 | 1,0 | 10 | 35 | VIII |
9 | 20 | 10 | 72 | 0,6 | 7,5 | 24 | IX |
10 | 15 | 8 | 24 | 0,5 | 6,2 | 18 | X |
11 | 80 | 180 | 810 | 2,0 | 135 | 104 | II |
12 | 50 | 50 | 360 | 1,7 | 35 | 56 | III |
13 | 25 | 12 | 82 | 1,0 | 10 | 35 | VI |
14 | 15 | 8 | 24 | 0,5 | 6,2 | 18 | VIII |
15 | 125 | 490 | 3090 | 3,7 | 392 | 150 | X |
16 | 120 | 450 | 3000 | 3,5 | 352 | 145 | I |
17 | 110 | 350 | 1880 | 3,1 | 302 | 135 | IV |
18 | 95 | 220 | 1120 | 2,4 | 172 | 125 | V |
19 | 70 | 75 | 510 | 1,9 | 52 | 79 | VII |
20 | 65 | 70 | 430 | 1,8 | 47 | 74 | IX |
21 | 45 | 50 | 275 | 1,6 | 44 | 55 | I |
22 | 85 | 200 | 910 | 2,1 | 155 | 109 | II |
23 | 35 | 25 | 175 | 1,3 | 23 | 45 | III |
24 | 115 | 315 | 1980 | 3,3 | 267 | 140 | IV |
25 | 105 | 300 | 1780 | 3,0 | 252 | 135 | V |
26 | 60 | 60 | 400 | 1,8 | 45 | 66 | VI |
27 | 55 | 45 | 380 | 1,7 | 30 | 61 | VII |
28 | 110 | 320 | 1885 | 3,1 | 272 | 139 | VIII |
29 | 70 | 80 | 550 | 1,9 | 57 | 78 | IX |
30 | 90 | 300 | 1580 | 2,3 | 255 | 120 | X |
31 | 125 | 490 | 3090 | 3,7 | 392 | 150 | I |
32 | 100 | 320 | 1680 | 2,5 | 272 | 130 | II |
33 | 80 | 180 | 810 | 2,0 | 135 | 104 | III |
34 | 75 | 80 | 530 | 2,6 | 57 | 84 | IV |
35 | 50 | 50 | 360 | 1,7 | 35 | 56 | V |
36 | 40 | 30 | 190 | 1,6 | 24 | 50 | VI |
37 | 30 | 20 | 160 | 1,2 | 18 | 39 | VII |
38 | 25 | 12 | 82 | 1,0 | 10 | 35 | VIII |
Рисунок 4 – Условные диаграммы растяжения материалов
(диаграммы I, IV, V, VII, VIII, IX – имеют выраженную площадку текучести, а у диаграмм II, III, VI, X – площадка текучести отсутствует)
Задача 2.Для разрушения на маятниковом копре стандартного образца стали сечением 1,0 ´1,0 см и длиной 5,5 см была затрачена работа А = 12,21кг×м. Удар произведен по надрезу в образце, глубина которого 0,2 см. Определить ударную вязкость стали.
Задача 3.Образец углеродистой стали испытывался на твердость на прессе Бринелля шариком D = 10 мм под нагрузкой Р = 3000 кгс. Получены три отпечатка с диаметрами 5,09 мм; 5,15 мм; 5,12 мм. Определить средние значения твердости и предела прочности.
Задача 4.На сколько удлинится стержень длиной 4 м из стали с пределом текучести s0,2= 285 МПа, если внутреннее напряжение s (s= P/F0) составит 0,62 от предела текучести.
При решении задачи необходимо воспользоваться формулой для определения модуля упругости. Значение модуля упругости принять из 1 задачи.
Задача 5. Растянутый элемент металлической балки в форме швеллера № 30 (F = 40,5 см2) изготовлен из стали Ст3. При какой нагрузке в данном элементе конструкции появятся остаточные деформации.
Пример решения задачи 1.
Определить основные свойства материалов: модуль упругости Е; относительное удлинение d; относительное сужение y; параметры прочностных свойств материала (пределы пропорциональности sпц, текучести sт (s0,2), прочности sв) по заданной диаграмме; твердость НВ, предел выносливости s-1.
Исходные данные:
l0, мм | F0, мм2 | P, Н | Dl×103, мм | F1, мм2 | l1, мм | № диаграммы |
70 | 85 | 520 | 2,4 | 67 | 78 | рисунок 1 |
Решение:
1. Определение модуля упругости:
.
2. Определение показателей пластичности:
- относительное удлинение ;
- относительное сужение .
3. Определение параметров прочности по диаграмме (см. рис. 1)
- предел пропорциональности характеризует конец прямолинейного участка диаграммы: sпц= 270 МПа, т.к. до этой точки график прямолинеен, далее он искривляется.
- поскольку на диаграмме нет явно выраженной площадки текучести, то определяем условный предел текучести s0,2. Для этого определим напряжение, соответствующее 1,0% деформации s1,0 =350 МПа, т.е.
270<s0,2<350,
.
(Если диаграмма имеет площадку текучести, то необходимо определить предел текучести s0,2, значение которого соответствует горизонтальному прямолинейному участку диаграммы (площадке текучести).)
- прослеживая характер кривой при возрастании нагрузки, доходим до точки экстремума (наивысшая точка диаграммы), которая и характеризует предел прочности (временного сопротивления) – sв = 460 МПа..
4. Определение твердости: sв = (0,34 … 0,36)НВ;
sв = 0,35 ×НВÞ НВ = sв /0,35 = 460 /0,35 = 1314 МПа.=131,4 кгс/мм2.
5. Определение предела выносливости: s-1=0,43sв=0,43×460 =197,8МПа.
Ответ. Е = 178,4× 103 МПа; d = 11,4%; y = 21,2%; sпц= 270 МПа; s0,2 = 286 МПа;sв = 460 МПа; НВ = 131,4 кгс/мм2, s-1= 197,8 МПа.
Справочные данные: 1 кгс/мм2 = 10 МПа.
Работа №2.
Железоуглеродистые сплавы.
Теоретические основы работы.
Железоуглеродистые сплавы – это сплавы железа с углеродом. Основными из них являются, стали и чугуны.
Чистое железо (Fe), в зависимости от температуры, может иметь различные кристаллические решётки: при температуре до 768°С – объёмно-центрированную решётку (ОЦК) – α-Fe (рисунок5 а), с магнитными свойствами (768° – точка Кюри); в интервале температур от 768°С до 910°С – ОЦК решётку, немагнитную; в интервале температур 910°С до 1392°С – гранецентрированную кубическую решётку (ГЦК) – g-Fe (рисунок5 б); в интервале температур 1392°С до 1539°С (температура плавления Fe) – ОЦК решётку – d-Fe .
Такое изменение кристаллической решётки в зависимости от температуры называется аллотропическим (полиморфным) превращением.
Графит (С) – разновидность углерода. Удельный вес – 2,2 г/см3. Твёрдость и прочность низкие. Кристаллическая решётка – гексагональная (рисунок 5 в).
Рисунок 5 – Кристаллические решетки:
а – объемно-центрированная кубическая; б – гранецентрированная кубическая; в – гексагональная плотноупакованная
Простые вещества (в данном случае Fe и С), образующие сплав, называют компонентами сплава. Ими могут быть чистые металлы или неметаллы, также промежуточные фазы постоянного состава, не разлагающиеся до полного расплавления (например – химические соединения).
Фаза – однородная часть сплава, отделённая от других частей (фаз) поверхностью раздела (границами), при переходе через которую химический состав и структура изменяются скачком. Это могут быть твердые растворы, химические соединения, чистые элементы. Совокупность фаз, находящихся в состоянии равновесия, определяет структуру сплава.
В железоуглеродистых сплавах образуются следующие фазы: феррит, аустенит, цементит, перлит, ледебурит.
Феррит – твёрдый раствор внедрения углерода в α-Fe и d-Fe. Кристаллическая решётка – ОЦК, в которую внедрены атомы углерода в междоузлия. Максимальная растворимость углерода в феррите (α-Fe) при 0°С – 0,006%, а при 727°С – 0,025%. Магнитен до 708°С, очень пластичен, НВ = 80 – 90 кгс/мм2; sв = 30 кгс/мм2.
Аустенит – твёрдый раствор внедрения углерода в g-Fe. Кристаллическая решётка – ГЦК, в которую внедрены атомы углерода в центр куба. Максимальная растворимость углерода в g-Fe (аустените) при 1147°С – 2,14%, а при 727°С – 0,83%. В нормальных условиях ниже 727°С аустенита не существует. Аустенит не магнитен, имеет меньший удельный объём, чем феррит. Обладает хорошей пластичностью и прочностью при невысокой твёрдости (170 НВ).
Цементит – карбид железа (Fe3С) – химическое соединение, содержит 6,67%С, остальное железо. Очень твёрд (НВ 100 – 800) и хрупок. Магнитен до 210°С.
Перлит – механическая смесь (эвтектоид) феррита и цементита.
Перлит содержит 0,83% С и образуется из аустенита при температуре 727°С. Перлит в зависимости от условий превращения может быть зернистый или пластинчатый. Свойства перлита зависят от формы цементита. Прочность перлита высокая, удельная вязкость невысока, НВ = 190 – 250 кгс/мм2.
Ледебурит – механическая смесь (эвтектика), образующаяся из жидкого расплава при 1147°С и содержит 4,3% С. При температуре выше 727°С состоит из аустенита и цементита, ниже 727°С – из перлита и цементита. Твёрдая (600 НВ), но хрупкая и не пластичная структура.
Чугун – сплав железа с углеродом, содержание углерода от 2,14% до 6,67%.
Чугун классифицируется в зависимости от химического состава, назначения, структуры и технологии получения.
Углерод, входящий в состав чугуна, может находиться в свободном состоянии в, виде отдельных частиц графита, вкрапленных между зернами железа, и в химически связанном состоянии – в виде карбида железа Fe3С (цементита). В зависимости от того, в какой форме присутствует углерод в чугуне, различают серый, высокопрочный и ковкий чугун.
Серый чугун– чугун, в котором весь углерод или большая его часть находится в виде графита пластинчатой формы. Его излом имеет серый цвет.
Отливки из серого чугуна маркируют буквами СЧ и двузначным числом, соединенными между собой дефисом; буквы обозначают серый чугун; число - предел прочности при растяжении в кгс/мм2. Так, например, марка СЧ28 расшифровывается: серый чугун с прочностью при растяжении не менее28 кгс/мм2 или 280 МПа. Применение необходимой марки определяется механическими свойствами.
Высокопрочный чугун – чугун с шаровидным графитом. Высокопрочный чугун обозначается аналогично серому: буквами и двузначным числом. Буквы ВЧ обозначают высокопрочный чугун, а число предел прочности при растяжении в кгс/мм2. Например, ВЧ 60 – высокопрочный чугун имеет sв = 60 кгс/мм2 = 600 МПа. Применяют для изготовления ответственных деталей.
Ковкий чугун имеет хлопьевидные графитовые включения. Обязательными характеристиками ковких чугунов является предел прочности и относительное удлинение, по которым маркируют ковкие чугуны. Так, например, марка КЧ37-12 расшифровывается следующим образом: ковкий чугун, предел прочности при растяжении sв=37 кгс/мм2 = 370 МПа, относительное удлинениеd = 12%. Применяют ковкий чугун для деталей небольшого сечения, работающих при ударных и вибрационных нагрузках.
Сталь – сплав железа с углеродом, содержание углерода до 2,14%.
Сталь, так же как и чугун содержит примеси: кремния (до 0,4%), марганца (до 1,1%), фосфора (до 0,045 %) и серы (до 0,055 %). Фосфор и сера являются нежелательными (вредными) примесями в составе стали.
Конструкционная сталь бывает углеродистой и легированной. Она служит для изготовления различных сооружений и инженерных конструкций, деталей машин, станков, крепежных и других изделий.
Конструкционную углеродистую сталь делят на стали обыкновенного качества (ГОСТ 380) и стали качественные (ГОСТ 1050).
Конструкционную углеродистую сталь обыкновенного качества маркируют буквами Ст с рядом стоящими цифрами от 0 до 6. Чем больше цифра, тем больший процент углерода в стали, тем она тверже и прочнее с соответствующим снижением пластичности. Например, сталь марки Ст6 содержит около 0,56% углерода с пределом прочности на растяжение 590 МПа и более. В зависимости от условий и степени раскисления стали подразделяют на спокойную – к марке стали добавляют индекс сп; полуспокойную – пс; кипящую – кп. В их составе разное массовое содержание кремния и кислорода.
Конструкционная углеродистая качественная сталь обозначается двузначным числом: 05кп, 08кп, 08, 10кп, 10 15кп, 15, 20кп, 20, 25, 30, 35 40, 45, 50 55 60 65, 70, 75, 80, 85, 60, 65, 70, 75, 80, 85. Двузначное число обозначает количество углерода в сотых долях процента, следовательно, сталь может содержать от 0,05 до 0,85 % С. В зависимости от содержания углерода стали подразделяют на: низкоуглеродистые (содержание углерода С£ 0,25 %); среднеуглеродистые (0,3 … 0,55 % С); высокоуглеродистые (0,6 … 0,85 % С).
Конструкционные легированные стали – стали, содержащие специально введенные с целью изменения строения и свойств легирующие элементы. Эти стали обладают особыми свойствами. Химический состав легированных сталей является основой для их маркировки буквенно-цифровой системой. Число, стоящее впереди марки конструкционной стали, обозначает среднее содержание углерода в сотых долях процента. За цифрами стоят буквы условных наименований легирующих элементов и числа, обозначающие процентное содержание их в стали. Отсутствие цифры после буквы указывает, что среднее содержание легирующего элемента не превышает 1 % (иногда 1,5%). ГОСТ 4543 приняты следующие буквенные обозначения: Х – хром, Н – никель, Г – марганец, С – кремний, Т – титан, В – вольфрам, М – молибден, Ф – ванадий, Ю – алюминий, Д – медь, К – кобальт, Б – ниобий, Р – бор. Если в конце названия марки стоит буква А, то это означает, что сталь высококачественная, содержащая наименьшее количество вредных примесей. Если буква А стоит в середине марки, например, 16Г2АФ, то это означает, что сталь легирована азотом. Буква Л, стоящая в конце марки стали, обозначает литейную сталь, например, 15Х25ТЛ.
Например, сталь 12ХН3А содержит С ~ 0,12 %, Cr~ до 1 %, Ni~ 3 %, высококачественная сталь.
Задание на работу № 2.
Задача 1(по вариантам).Определить количества феррита и цементита в железоуглеродистых сплавах по содержанию углерода. Построить совмещенную диаграмму изменения содержания феррита и цементита в сплавах.
Ф, Ц, %
С, %
(При решении задачи следует исходить из того, что в железоуглеродистых сплавах имеется только феррит (Ф) и цементит (Ц), а все другие структуры являются комбинациями из феррита и цементита, поэтому определяют только содержание цементита (смотри пример решения задачи), а феррит принимают по разности Ф = 100 % – Ц.)
Исходные данные:
№ варианта | Содержание углерода, % | № варианта | Содержание углерода, % | ||||||||
1 | 0,1 | 0,83 | 1,5 | 2,32 | 4,0 | 20 | 0,39 | 1,21 | 1,8 | 2,61 | 5,55 |
2 | 0,11 | 0,84 | 1,51 | 2,33 | 4,1 | 21 | 0,29 | 1,11 | 1,69 | 2,51 | 5,0 |
3 | 0,12 | 0,85 | 1,52 | 2,34 | 4,15 | 22 | 0,28 | 1,1 | 1,68 | 2,5 | 4,95 |
4 | 0,13 | 0,86 | 1,53 | 2,35 | 4,2 | 23 | 0,27 | 1,0 | 1,67 | 2,49 | 4,9 |
5 | 0,14 | 0,87 | 1,54 | 2,36 | 4,25 | 24 | 0,26 | 0,99 | 1,66 | 2,48 | 4,85 |
6 | 0,15 | 0,88 | 1,55 | 2,37 | 4,3 | 25 | 0,25 | 0,98 | 1,65 | 2,47 | 4,8 |
7 | 0,16 | 0,89 | 1,56 | 2,38 | 4,35 | 26 | 0,24 | 0,97 | 1,64 | 2,46 | 4,75 |
8 | 0,17 | 0,9 | 1,57 | 2,39 | 4,4 | 27 | 0,23 | 0,96 | 1,63 | 2,45 | 4,7 |
9 | 0,18 | 0,91 | 1,58 | 2,4 | 4,45 | 28 | 0,22 | 0,95 | 1,62 | 2,44 | 4,65 |
10 | 0,19 | 0,92 | 1,59 | 2,41 | 4,5 | 29 | 0,21 | 0,94 | 1,61 | 2,43 | 4,6 |
11 | 0,3 | 1,12 | 1,7 | 2,52 | 5,1 | 30 | 0,2 | 0,93 | 1,6 | 2,42 | 4,55 |
12 | 0,31 | 1,13 | 1,71 | 2,53 | 5,15 | 31 | 0,1 | 0,83 | 1,5 | 2,32 | 4,0 |
13 | 0,32 | 1,14 | 1,72 | 2,54 | 5,2 | 32 | 0,11 | 0,84 | 1,51 | 2,33 | 4,1 |
14 | 0,33 | 1,15 | 1,73 | 2,55 | 5,25 | 33 | 0,12 | 0,85 | 1,52 | 2,34 | 4,15 |
15 | 0,34 | 1,16 | 1,74 | 2,56 | 5,3 | 34 | 0,13 | 0,86 | 1,53 | 2,35 | 4,2 |
16 | 0,35 | 1,17 | 1,75 | 2,57 | 5,35 | 35 | 0,14 | 0,87 | 1,54 | 2,36 | 4,25 |
17 | 0,36 | 1,18 | 1,76 | 2,58 | 5,4 | 36 | 0,15 | 0,88 | 1,55 | 2,37 | 4,3 |
18 | 0,37 | 1,19 | 1,78 | 2,59 | 5,45 | 37 | 0,16 | 0,89 | 1,56 | 2,38 | 4,35 |
19 | 0,38 | 1,2 | 1,79 | 2,6 | 5,5 | 38 | 0,17 | 0,9 | 1,57 | 2,39 | 4,4 |
Задача 2. Какие вредные химические примеси могут быть в стали и каково их предельное содержание?
Задача 3. Расчет вала выполняется в двух вариантах, отличающихся принятым материалом: 1) сталь 40; 2) сталь 40ХН.
Можно ли с уверенностью утверждать, что при одинаковых диаметрах и конструкции валов в обоих вариантах вал из стали 40ХН окажется прочнее, чем из стали 40 и почему?
Задача 4.Сталь испытана на растяжение в образце диаметром d0 = 10мм, l0 = 90 мм. После испытания установлены следующие показатели: нагрузка при пределе текучести Р0,2 = 75000 Н; разрушающая нагрузка Рв = 82000 Н; длина образца после разрыва l1 = 97 мм, диаметр образца после испытания d1= 6,7 мм. Определить:s0,2, sв, d, y, марку стали.
Задача 5. Арматура из высокоуглеродистой стали была испытана на твердость на твердомере Роквелла. При этом по индикатору твердомера на шкале С получено значение твердости HRC = 21.Определить марку стали.
Задача 6(по вариантам).Расшифровать марку стали (определить примерный химический состав стали).
№ варианта | Марка стали | № варианта | Марка стали |
1 | 40Х24Н12СЛ | 20 | 31Х19Н9МВБТ |
2 | 15Х12ВНМФ | 21 | 37Х12Н8Г8МФБ |
3 | 10Х11Н20Т3Р | 22 | 06ХН28МДТ |
4 | 40ХСН2МА | 23 | 20Х12ВНМФ |
5 | 10Х17Н13М3Т | 24 | 08Х21Н6М2Т |
6 | 20Х1М1Ф1ТР | 25 | 36Х2Н2МФА |
7 | 55Х20Г9АН4 | 26 | 08Х15Н24В4ТР |
8 | 15Х2Г2СВА | 27 | 12Х29Н16Г7АР |
9 | 45Х14Н14В2М | 28 | 08Х16Н13М2Б |
10 | 12Х18Н9ТЛ | 29 | 15ХГСНДМ |
11 | 18Х12ВМБФР | 30 | 35ХНМ24В4ТР |
12 | 20ХГСНДМЛ | 31 | 40Х24Н12СЛ |
13 | 20Х20Н14С2 | 32 | 15Х12ВНМФ |
14 | 03Х19Г10Н7АР | 33 | 10Х11Н20Т3Р |
15 | 08Х17Н13М2Т | 34 | 40ХСН2МА |
16 | 10Х14Г12Н4Т | 35 | 10Х17Н13М3Т |
17 | 35ХН1М2ФА | 36 | 20Х1М1Ф1ТР |
18 | 13Х11Н2В2МФ | 37 | 55Х20Г9АН4 |
19 | 40Х15Н7Г7Ф2МС | 38 | 15Х2Г2СВА |
Пример решения задачи 1.
Железоуглеродистый сплав содержит углерода 0,27 %. Определить в нем содержание цементита (Ц) и феррита (Ф).
Решение.
При содержании углерода 6,67 % в железоуглеродистом сплаве содержится 100% цементита. Исходя из этого, составим пропорцию
6,67 % С – 100 % Ц
0,27 % С – х % Ц.
х = (0,27× 100) /6,67 =4% Ц.
Содержание феррита определяем по разности
Ф = 100 % – Ц = 100 – 4 = 96%.
При решении задачи 1 необходимо аналогично определить содержание цементита и феррита для каждого сплава (по содержанию углерода), а затем построить совмещенную диаграмму изменения содержания феррита и цементита в сплавах.
При решении задач 4, 5 следует воспользоваться теоретическими данными к работе № 1.
Справочные данные.
Марка стали | sв, МПа | sт, МПа | d, % | Марка стали | sв, МПа | sт, МПа | d, % |
Ст 1 | 310 | – | 35 | 55 | 660 | 390 | 13 |
Ст 2 | 330 | 225 | 32 | 60 | 700 | 410 | 12 |
Ст 3 | 370 | 245 | 26 | 65 | 710 | 420 | 10 |
Ст 4 | 410 | 265 | 24 | 70 | 730 | 430 | 9 |
Ст 5 | 490 | 285 | 20 | 75 | 1080 | 885 | 9 |
Ст 6 | 590 | 315 | 15 | 80 | 1100 | 950 | 8 |
1 кгс/мм2 = 10 МПа
Работа №3
Цветные металлы и их сплавы.
Теоретические основы работы.
Медь и ее сплавы
Чистая медь обладает высокой пластичностью, электро- и теплопроводностью, коррозионной стойкостью. Из чистой меди изготовляют электрические провода и кабели, детали приборов и электрических машин и т.д. Медь хорошо обрабатывается давлением и вытягивается в тонкие листы (фольгу) толщиной 0,05 – 0,06 мм и в проволоку диаметром 0,02 – 0,03 мм. Марки меди различаются в зависимости от чистоты. Примерно 75% меди расходуется на сплавы с другими металлами – цинком, оловом, свинцом, алюминием и т. д. Сплавы на медной основе объединяются в две основные группы – латуни и бронзы.
Латунью называется сплав меди с цинком. При содержании цинка менее 20% латунь называется томпаком. Латунь обозначают буковой Л с цифрами, соответствующими процентному содержанию меди в сплаве. Если в латуни кроме меди и цинка имеются еще добавки, то после буквы Л ставят обозначения добавок, после которых следуют цифры, указывающие среднее процентное содержание компонентов латуни, а латунь получает название по введенным в нее добавкам. Например, латунь марки ЛС59-1 обозначает: латунь свинцовистая с 59% меди, 1% свинца и 40% цинка.
По технологическому признаку латуни делятся на литейные и деформируемые (обрабатываемые давлением). Для улучшения механических свойств и обрабатываемости латуни в медноцинковый сплав добавляют 2 – 8 % железа, алюминия, никеля и других элементов. Такие латуни называются специальными.
Бронзой называется сплав меди с оловом и другими элементами, кроме цинка. Различают простые (оловянистые) и специальные (безоловянистые) бронзы. Бронзы, в состав которых входит олово, являются оловянистыми. В специальных бронзах олово заменено свинцом, алюминием, железом, марганцем, кадмием, бериллием и другими элементами. В зависимости от химического состава такие бронзы называются свинцовистыми, алюминиевыми, марганцовистыми, беррилиевыми и т. д. Как и латуни, бронзы делятся на литейные и деформируемые.
Принцип обозначения бронз такой же, как и латуней, лишь с той разницей, что цифры, следующие за буквами, указывают только среднее процентное содержание примесей в сплаве (остальное медь); например, БрОЦСН-3-7-5 обозначает: бронза оловянисто-цинко-свинцовисто-никелевая, содержащая 3% олова 7% цинка, 5% свинца и 1 % никеля.
Алюминий и его сплавы
Алюминий обладает хорошей пластичностью, электро- и теплопроводностью, высокой коррозионной стойкостью в пресной воде, в атмосферных и некоторых других условиях. На воздухе поверхность алюминия покрывается тонкой пленкой окислов Al2O3, которая защищает от окисления нижерасположенные слои металла.
Сплавы алюминия делятся на литейные и деформируемые. Наибольшее применение из литейных сплавов получил силумин. Деформируемые сплавы делят на неупрочняемые термообработкой, к ним относятся сплавы алюминия с марганцем и магнием, и упрочняемые, наиболее распространенным из них является дуралюмин.
Силумин представляет собой сплав алюминия с 8 – 14 % кремния. Он обладает хорошими литейными качествами и используется для отливки сложных деталей в песчаные формы, в кокиль и под давлением.
Сплавы алюминия с марганцем и магнием обладают высокой коррозионной стойкостью, умеренной прочностью, высокой пластичностью, хорошо свариваются. Их маркировка: АМц – сплавы алюминия с марганцем, АМг – с магнием. Например АМг7 – сплав алюминия с магнием, содержащий магния примерно 7%, остальное алюминий.
Дуралюминами называются сплавы алюминия с медью (2,25 – 5,2 %), магнием (0,2 – 1,8 %) и марганцем (0,1 – 1,0 %). Они обладают достаточно высокой прочностью, пластичностью и делятся на три группы: нормальный дуралюмин; дуралюмины с повышенной пластичностью; дуралюмины с повышенной прочностью. Дуралюмин маркируют буквой Д и порядковым номером, например, Д1, Д16 и т.д.
Задание на работу №3.
Задача 1 (по вариантам). По данной марке сплава определить:
- к какой группе материалов относится;
- химический состав (по марке сплава);
- механические и физические свойства (дать описание буквенным обозначениям свойств). Необходимо выбрать для соответствующей марки сплава по таблицам, приведенным в справочных данных для этой работы.
Исходные данные:
№ вар. | марка сплава | № вар. | марка сплава | № вар. | марка сплава |
1 | АМц | 14 | ЛКС80-3-3 (мягкая) | 27 | БрКН1-3 (твердая) |
2 | Л90 (твердая) | 15 | БрКМц3-1 (твердая) | 28 | ЛА67-2,5 (мягкая) |
3 | БрОФ8-0,3 (твердая) | 16 | АМц | 29 | БрОФ4-0,25 (мягкая) |
4 | АМг5 | 17 | ЛН65-5 (мягкая) | 30 | ЛМцЖ55-3-1 (мягкая) |
5 | ЛАЖ60-1-1 (мягкая) | 18 | БрОЦС4-4-2,5 (мягкая) | 31 | АМц |
6 | БрОЦ4-3 (мягкая) | 19 | АМг5 | 32 | Л90 (твердая) |
7 | АМг3 | 20 | Л70 (твердая) | 33 | БрОФ8-0,3 (твердая) |
8 | ЛС63-3 (твердая) | 21 | БрА7 (твердая) | 34 | АМг5 |
9 | БрАЖН10-4-4 (твердая) | 22 | АМг2 | 35 | ЛАЖ60-1-1 (мягкая) |
10 | АМг2 | 23 | ЛС59-1(мягкая) | 36 | БрОЦ4-3 (мягкая) |
11 | ЛЖС58-1-1 (мягкая) | 24 | БрБ2 (мягкая) | 37 | АМг3 |
12 | БрМц5 (мягкая) | 25 | АМг6 | 38 | ЛС63-3 (твердая) |
13 | АМг6 | 26 | ЛК80-3 (твердая) |
Задача 2.Определить механические характеристики (твердость и предел прочности) и марку алюминиевого сплава, если при испытании на твердость по Бринеллю (D = 10 мм, Р = 250 кгс) средний диаметр отпечатка составляет d = 2,3 мм.
Задача 3. Для деталей, работающих в условиях трения заменить КЧ60-3 (sв³ 588 МПа, НВ = 180 … 250) на бронзу.
Задача 4. Определить механические характеристики (твердость и предел прочности) и марки латуни и бронзы, если при испытании на твердость по Бринеллю (D = 10 мм, Р = 1000 кгс) средний диаметр отпечатка составляет d = 4,2 мм.
Задача 5. Щиты авиационных электродвигателей изготовляют из алюминиевого сплава. Какой материал и какой способ изготовления деталей в данном случае оптимален и почему: 1) Д1, литье в кокиль; 2) АЛ2, литье под давлением.
В этой задаче обратить внимание на сочетание материала и способа получения детали.
Справочные данные.
Механические и физические свойства деформируемых алюминиевых сплавов (ГОСТ 4784)
Марка | sв, МПа | d, % | y, % | НВ | g, г/см3 | l, Вт/(м×°С) | a×106, 1/°С |
АМц | 128 | 23 | 70 | 30 | 2,73 | 188 | 24,0 |
АМг2 | 186 | 23 | – | 45 | 2,67 | 143 | 23,8 |
АМг3 | 186 | 15 | – | 50 | 2,67 | 147 | 23,8 |
АМГ5 | 255 | 22 | – | 65 | 2,65 | 117 | 24,3 |
АМг6 | 295 | 18 | – | 80 | 2,63 | 293 | 24,0 |
АД31 | 235 | 10 | 50 | 80 | 2,71 | 188 | 23,4 |
АД33 | 315 | 10 | 25 | – | 2,71 | 143 | 23,2 |
Д1*1 | 372 | 15 | 30 | 100 | 2,8 | 117 | 22,0 |
Д16*1 | 441 | 17 | 30 | 105 | 2,78 | 117 | 22,7 |
АК4*2 | 382-421 | 10 | 20-25 | 120 | 2,8 | 180 | 22,0 |
АК6*2 | 411 | 13 | 40 | 100 | 2,75 | 176 | 21,4 |
АК8*2 | 470 | 10 | 25 | 135 | 2,8 | 160 | 25,5 |
В95*2 | 451 | 8 | 12 | 150 | 2,8 | 117 | 3,6 |
*1 Для закаленного и естественно состаренного сплава. *2 Для закаленного и искусственно состаренного сплава. |
Дата добавления: 2018-08-06; просмотров: 821; Мы поможем в написании вашей работы! |
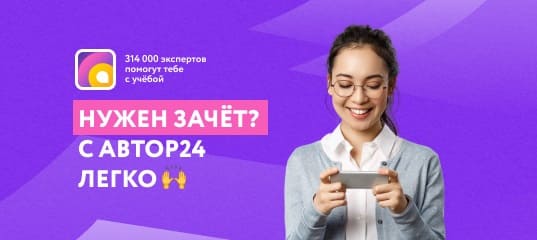
Мы поможем в написании ваших работ!