Все это способствует правильному, четкому и быстрому выполнению заказов потребителей, а значит и повышению репутации самого предприятия.
Введение
Сегодня без складской деятельности ни одно предприятие не может существовать.
Складская деятельность важный элемент общественного производства, свойственна всем отраслям и имеет очень сложную структуру.
Выбранная тема дипломной работы актуальна тем, что операции на складе имеют большое значение для деятельности всего предприятия.
Важным показателем является правильно организованная складская деятельность. Качество товара, сохранность и комплектность товарно-материальных ценностей зависит от того как настроена складская деятельность, как оборудован склад, как специализированные помещения склада, а также от устройств, предназначенных для приемки, размещения, хранения товара. Главным показателем является механизация и автоматизация технологического процесса на складе, потому что применение средств механизации и автоматизации при приемке, хранении и отпуске товаров повышает рост производительности труда складских работников и повышает эффективность использования площади на складе.
На всех этапах технологического процесса на складе безошибочное заполнение документов, также имеет большое значение.
Складское хозяйство – это материально-техническая база системы, которая занимается снабжением и сбытом.
От работы складской системы зависит качество снабжения эффективности потребителей материальными ресурсами.
|
|
Правильная организация складской деятельности обеспечивать сохранность материальных ценностей, а также направлена на исключение потерь, недостачи и пересортицы. От работы персонала склада зависит себестоимость продукции, прибыль, рентабельность, рост производительности труда, выполнение договорных обязательств по поставкам продукции.
Темой исследования дипломной работы является – ООО «Метро Кэш энд Кэрри» г. Липецк.
В качестве предмета исследования выступает процесс совершенствования складской деятельности предприятия.
Цель дипломной работы является организация складской деятельности на предприятии и разработка рекомендации по совершенствованию деятельности склада.
Для достижения цели дипломной работы нужно решить следующие задачи:
- изучить теорию организации деятельности складского хозяйства;
- провести анализ экономического состояния предприятия и анализ деятельности складского хозяйства в ООО «Метро Кэш энд Кэрри»
- разработать мероприятия по совершенствованию деятельности складского хозяйства в ООО «Метро Кэш энд Кэрри».
Метод исследования сбор, обобщение и систематизация информации, анализ.
Для выполнения дипломной работы были использованы источники информации: периодическая литература, посвященная теме работы и анализу складского хозяйства; работы отечественных и зарубежных авторов о работе управления складом; электронные ресурсы.
|
|
1 Теоретические основы грузопереработки на складе, виды складов и оборудования
1.1 Понятие и основы переработки грузов на складе
Грузопереработка(MaterialsHandling) – это совокупность операций, выполняемых на различных стадиях складского технологического процесса [2с].
Операции грузопереработки реализуются в рамках складского технологического процесса. Этот процесс разделен на четыре основных этапа:
- поступление товаров (состав логистических операций, выполняемых при получении товаров, может сильно варьироваться в зависимости от рода поступающего груза);
- приемка товаров по количеству и качеству;
- складирование и хранение товаров (осуществляется в виде штабельного или стеллажного хранения);
- отпуск товаров со склада (отборка товаров из мест хранения, комплектование партиями, экспедирование грузов, погрузка транспортного средства).
Одна из важнейших задач современной логистики – обеспечить,чтобы капиталовложения в оборудование грузопереработки приносили максимальную отдачу, воплощенную в росте производительности труда.
|
|
Грузопереработка в логистике неизбежна, но следует стремиться к сокращению ее объемов до возможного минимума.
Главными задачами грузопереработки являются разукрупнение поступающих грузов и подборка отправок в соответствии с требованиями заказчиков. Рассмотрим три основные операции грузопереработки: приём и разгрузку поступающих партий грузов, перемещение грузов внутри склада и их отправку.
Ввиду ряда причин грузопереработка является ключевым фактором производительности складских операций.
Во-первых, расходуется столько человеко-часов труда, что любое снижение производительности ведёт к значительным потерям. Из-за высокой трудоёмкости грузопереработки складские операции более чувствительны к уровню производительности, чем производственные процессы.
Во-вторых, в силу своей специфики, грузопереработка мало что выиграла от совершенствования информационных технологий. Компьютеризация внесла некоторые изменения, но всё же преобладание физического труда осталось неизменным.
В-третьих, до недавнего времени на грузопереработку не распространялись принципы комплексного управления логистическими операциями, вследствие чего руководители не занимались соответствующими вопросами.
|
|
Склад необходим для хранения сырья, материалов, а также различных комплектующих и готовой продукции.
Суть в том, чтобы обеспечить достаточно эффективную загрузку склада большим объёмом продукции и отправку этой продукции со склада в соответствии с заказами.
Основные задачи грузопереработки.
Главными задачами грузопереработки являются разукрупнение поступающих грузов и подборка отправок в соответствии с требованиями заказчиков. Рассмотрим три основные операции грузопереработки: приём и разгрузку поступающих партий грузов, перемещение грузов внутри склада и их отправку.
Приёмка и отгрузка.
В большинстве случаев, товары поступают на склад более крупными партиями, нежели требуется для отправки со склада заказчикам. В любом случае, сначала нужно разгрузить прибывший груз. На большинстве складов эту операцию выполняют вручную. Существует немного методов автоматизации разгрузки, применимых к широкому набору товаров, обладающих различными техническими характеристиками.
Перемещение грузов на складе.
Выгруженные товары нужно ввезти на склад, а именно в зону хранения или в зону комплектования отправок. Также при поступлении заказа необходимо подобрать товары в соответствии со спецификацией и поместить их в зону отгрузки. Внутрискладскаягрузопереработка включает в себя перемещение и подборку товаров. В процессе перемещения товаров, они сначала ввозятся на склад и размещаются в зоне хранения. В случае если товары уложены на поддонах, используются вилочные погрузчики, а для более крупных грузов – другие механические средства перемещения. Что касается подборки, необходимо отметить, что она является одной из основных функций склада. В процессе подборки из затребованных заказчиком материалов, комплектующих и готовой продукции формируется отправка.
Отправка.
Процесс отправки заключается в проверке подготовленных к отправке товаров в соответствии с требованиями заказчика, а также в их погрузке на транспортное средство. Чаще всего загрузка, как и разгрузка осуществляется вручную. Самым удобным способом для отправки является использование укрупнённых грузовых единиц, так как это позволяет экономить время на загрузку. Такая грузовая единица представляет собой несколько упаковок продукта в одной таре, и благодаря этому при загрузке не нужно разбирать штабеля отдельных ящиков или коробок и по одному загружать их в кузов.
Принципы грузопереработки
Большая часть операций грузопереработки в логистике приходится на складское хозяйство. Существует значительное различие между обработкой упакованной продукции и обработкой жидких, насыпных и навалочных грузов. В последнем случае отсутствует необходимость использования защитной упаковки. Для разгрузки жидких, сыпучих и навалочных грузов применяют специализированное оборудование.
Если говорить о системах грузопереработки, то их чаще всего делят на четыре типа:
1 механизированные;
2 автоматизированные;
3 полуавтоматизированные;
4 компьютеризированные.
В механизированных системах используется подъёмно-транспортное оборудование для приёмки, перемещения и отправки грузов.
В данном случае значительную часть издержек составляют расходы на оплату труда. В случае автоматизированных систем, инвестиции в оборудование позволяют сократить долю ручного труда до приемлемого уровня. Автоматизации поддаются практически все операции грузопереработки. Благодаря компьютеризации обеспечивается максимальный контроль над использованием подъёмно-транспортного оборудования. Достаточно часто встречаются механизированные системы грузопереработки, но со временем всё большее развитие и распространение имеют автоматизированные и полуавтоматизированные системы.
Дополнительные задачи грузопереработки
Иногда возникают ситуации, когда системе грузопереработки приходится иметь дело с обратными товарно-материальными потоками в логистической сети, а именно с возвратом товаров из магазинов. По ряду причин товары иногда подлежат возврату производителю или же он отзывает их сам. Как правило, возвратные потоки включают в себя паллеты, картон и другие виды упаковки, а также повреждённые, просроченные или излишние продукты. При организации систем грузопереработки необходимо принимать в расчёт возможное влияние таких обратных потоков на уровень логистических издержек и сервиса.
1.1 Факторы влияющие на грузопереработку на складе
Выделяют следующие основные цели грузопереработки:
- эффективное использование складской мощности;
- улучшение операционной эффективности (минимизация видов перерабатываемых грузовых единиц);
- улучшение условий труда персонала (повышение безопасности операций грузопереработки. эргономических и экологических характеристик рабочих мест, механизация и автоматизация складских работ и т. д.);
- обеспечение должного уровня логистического сервиса (повышение качества обслуживания потребителей за счет более быстрой реакции на их запросы);
- минимизация логистических издержек.
Реализация этих целей в значительной степени зависит от соблюдения следующих основных принципов рациональной организации процесса грузопереработки:
- механизации и автоматизации технологических операций;
- оптимального использования площади и емкости помещений;
- организации сквозного товарного потока;
- планомерности и ритмичности складских работ;
- полной сохранности товаров.
К основным операциям грузопереработки относятся:
- подготовка склада к приемке продукции;
- разгрузка транспорта;
- приемка продукции по количеству и качеству;
- размещение на хранение (укладка товаров в стеллажи, штабели);
- отборка товаров из мест хранения;
- комплектование заказов и упаковка;
- отпуск товаров;
- погрузка в транспортное средство.
Последовательность выполнения операций грузопереработки с указанием их продолжительности отражается в технологической карте. Технологические карты разрабатываются с учетом конкретных условий и могут иметь вид таблиц, графических схем или текстовых документов.
На продолжительность и характер складских операций оказывают влияние следующие факторы:
- объем поступления и отпуска;
- размеры товарных запасов;
- условия транспортировки (вагон, контейнер, автомобиль);
- ассортиментная структура товарооборота и способ упаковки товаров;
- габариты, вес товаров, тарных мест;
- условия и порядок хранения;
- площадь склада, состав помещений, их планировка, размеры конструктивных элементов, ширина проходов;
- габариты складских помещений;
- наличие технологического оборудования, его виды.
Грузопереработкаявляется составной частью логистического процесса на складе.
Выделяют следующие основные цели грузопереработки:
- эффективное использование складской мощности;
- улучшение операционной эффективности (минимизация видов перерабатываемых грузовых единиц);
- улучшение условий труда персонала (повышение безопасности операций грузопереработки, эргономических и экологических характеристик рабочих мест, механизация и автоматизация складских работ и т. д.);
- обеспечение должного уровня логистического сервиса (повышение качества обслуживания потребителей за счет более быстрой реакции на их запросы);
- минимизация логистических издержек.
Реализация этих целей в значительной степени зависит от соблюдения следующих основных принципов рациональной организации процесса грузопереработки:
- механизации и автоматизации технологических операций;
- оптимального использования площади и емкости помещений;
- организации сквозного товарного потока;
- планомерности и ритмичности складских работ;
- полной сохранности товаров.
К основным операциям грузопереработки относятся (приложение А):
- подготовка склада к приемке продукции;
- разгрузка транспорта;
- приемка продукции по количеству и качеству;
- размещение на хранение (укладка товаров в стеллажи, штабели);
- отборка товаров из мест хранения;
- комплектование заказов и упаковка;
- отпуск товаров;
- погрузка в транспортное средство.
Последовательность выполнения операции грузопереработки с указанием их продолжительности отражается в технологической карте. Технологические карты разрабатываются с учетом конкретных условий и могутиметь вид таблиц, графических схем или текстовых документов.
На продолжительность и характер складских операций оказывают влияние следующие факторы:
- объем поступления и отпуска;
- размеры товарных запасов;
- условия траспортировки (вагон, контейнер, автомобиль);
- ассортиментная структура товарооборота и способ упаковки товаров;
- габариты, вес товаров, тарных мест;
- условия и порядок хранения;
- площадь склада, состав помещений, их планировки, размеры конструктивных элементов, ширина проходов;
- габариты складских помещений;
-наличие технологического оборудования, его виды.
1.3 Складское оборудование, склады и их классификация
Большие потоки продукции делают необходимой концентрацию изделий. Для этого сооружаются специализированные элементы инфраструктуры, с которых происходит снабжение производственных предприятий сырьем и комплектующими, а конечного потребителя – готовыми товарами. Такие места для хранения называются складами в широком смысле слова, и, в зависимости от специфики – базами, терминалами или хранилищами.
Потребность в складских помещениях возникает у всех предприятий, занимающихся выпуском какой-либо продукции, торговых структур и компаний, которым для оказания услуг требуются расходные материалы. Чем более развитой является структура фирмы, тем большую важность имеет склад в общем хозяйственном комплексе.
Современный склад является достаточно сложным объектом, и с технической стороны, и с управленческой. Необходимость в складировании имеется на всех этапах производства, от места добычи сырья и до реализации товара. Поэтому существует большое количество различных складов, которые нуждаются в классификации. Чтобы понимать принципы классификации, необходимо знать основные принципы работы складских помещений.
Структура склада и используемое оборудование
Склад является не просто помещением, где находятся различные грузы. У него есть определенная внутренняя структура, которая бывает довольно развитой. Склад состоит из нескольких зон, различающихся по назначению и используемому оборудованию.
Выделяют такие основные зоны:
1 зона погрузки и выгрузки. Может быть цельной или разделенной на две отдельные. В этой зоне располагаются площадки, непосредственно контактирующие с транспортом. Требования к площадкам различаются в зависимости от обслуживаемого транспорта.
2 зона приемки. Данная зона обычно отделена от остальных помещений. В ней выполняется прием грузов и их дальнейшее направление на место хранения. Как правило, эта зона имеет высокую автоматизацию.
3 зона хранения. Её занимает оборудование, предназначенное для хранения грузов.
4 зона сортировки. Обеспечивает прием заявок на транспортировку грузов и их перемещение с мест хранения в зону погрузки.
5 зона экспедирования. Выполняется учет отправляемых грузов, составляется сопроводительная документация.
Административные и хозяйственно-бытовые помещения.
Для хранения и транспортировки грузов используется разнообразное оборудование. На складах с грузами небольшой массы широко применяются ручные устройства, тяжелые и габаритные предметы перемещаются кранами и погрузчиками.
Выбор склада
Современные рынки бывают достаточно изменчивыми, и компаниям для достижения наибольшей эффективности работы часто требуется искать новые помещения под склады. В этой ситуации выбор склада ставится задачей конкретных сотрудников. Чтобы найти нужный объект, необходимо сформировать обоснованные и четкие требования.
Для этого следует определить потребности фирмы, иначе будет неэффективная затрата средств. Лишняя площадь склада будет требовать большей оплаты, а производительность останется на том же уровне. Если, к тому же, технология обработки грузов будет нерациональной, то картина станет еще хуже.
Во время выбора склада следует руководствоваться четкими требованиям к его следующим характеристикам:
- общая площадь и объем здания;
- площадь и высоты зон;
- количество ворот или доков, их месторасположение и оснащение;
- размеры площадки для маневров транспорта.
Основной задачей является выбор размеров складов, чтобы с учетом прогнозируемого изменения потоков груза объект, его площади и объемы, использовались с наибольшей эффективностью. Чтобы оценить каждое технологическое решение в складском хозяйстве, введены специализированные нормативные коэффициенты.
Соответствие реальных показателей рекомендуемым коэффициентам показывает, что склад будет функционировать правильно. Отклонение от установленных норм приводит к снижению емкости и потере общей эффективности работы склада.
Перед тем, как выбрать склад, следует убедиться в наличии требований к помещению, их четкой формулировке, корректности и обоснованности. Наилучший случай – когда компания располагает специалистами, которые имеют соответствующее образование и опыт, что позволяет им произвести расчеты и обосновать их. Такая работа узкоспециализирована и требует определенной квалификации, поэтому такие специалисты имеются только в наиболее крупных компаниях.
Большинство фирм не имеют в штате подобных сотрудников, поэтому оптимальным выходом для них является привлечение компаний, специализирующихся на выполнении данных проектрировночно-расчетных работ.
Стоимость привлечения грамотных специалистов будет намного меньше, чем потери, которые могут произойти от ошибок с выбором склада, его планирования и оснащения.
Классификация складов
Для более простого выбора склада следует разделить здания на разные виды в зависимости от определенных признаков. Можно выделить такие критерии выбора склада:
- отношение к логистическим областям;
- отношение к другим участникам системы логистики;
- форма собственности;
- принадлежность;
- функциональное назначение;
- ассортиментная специализация;
- режим хранения;
- технологическая оснащенность;
- вид складских зданий;
- вид складирование;
- наличие транспортных связей и их тип;
- масштаб деятельности.
Склады с большой площадью–от 5 тыс. м2 часто называют терминалами.
Существуют специализированные таможенные склады, на которых хранятся товары, ввозимые на территорию РФ или вывозимые из страны. Хранение на этих складах производится согласно с Таможенным кодексом РФ. Из таможенных складов выделяют склады временного хранения, где находятся предметы, подлежащие как экспорту, так и импорту, с предоставления их органу таможни до выпуска в свободный оборот.
Во время хранения товаров на таможенном складе с них не взимается пошлины и налоги, а также не применяются меры экономической политики.
Способы классификации складских помещений в РФ
Многие компании, имеющие опыт в логистике и оценке коммерческой недвижимости, имеют свои системы, по которым выполняется классификация складов.
Представляет интерес системы Санкт-петербургской группы компаний «РМС» и лондонской фирмы KnightFrank, ведущей мировой компании в оценке всевозможной недвижимости. Во многом эти системы классификации похожи.
Рисунок1– Склады класса А
Первая классификация разработана в РФ, поэтому она учитывает особенности центральных регионов России и основные требования, на которые обращают внимание арендаторы и покупатели в первую очередь. Согласно этой классификации, складские помещения разделяются на 4 категории, которые обозначаются заглавными латинскими буквами.
Склады класса «А»
Склад класса А представляет собой современное одноэтажное здание, строительство которого велось с соблюдением предписанных технологий и с использованием материалов высокого качества. К нему предъявляются такие требования:
- высота не менее 8 м, чтобы можно было разместить многоуровневые стеллажи;
- пол с ровной поверхностью, без дефектов и с антифрикционным покрытием;
- пожарная сигнализация и автоматизированная система тушения пожаров спринклерного или порошкового типа;
- возможность четкой регуляции температурного режима;
- наличие тепловых завес на воротах;
- ворота докового типа автоматического действия, оборудованные гидравлическим пандусом с регулированием по высоте;
- центральное кондиционирование;
- охранная сигнализация и видеонаблюдение всей площади и окружающего пространство (пример проекта системы видеонаблюдения на складе);
- офисные помещения, совмещенные со складом;
- наличие телекоммуникационных линий оптико-волоконного типа;
- достаточная площадка, чтобы большегрузные автопоезда могли свободно маневрировать и стоять в отстое;
- удобный подъезд, предпочтительно размещение рядом с центральными магистралями.
Класс B:
- капитальное многоэтажное здание;
- высота потолков от 4,5 до 8 м;
- асфальтные или бетонные полы без покрытия;
- температурный режим в пределах от +10 до +18 °С;
- противопожарная система;
- пандус для разгрузки;
- наличие офисных помещений;
- телекоммуникации;
- охраняемая территория.
Рисунок 2 – Складские помещения класса B
Класс C:
- капитальное производственное помещение или утепленный ангар;
- высота от 3,5 до 18 м;
- отапливаемое помещение (температура зимой +8:+14 °С).
- асфальтные, плиточные или бетонные полы без покрытия;
- ворота на нулевой отметке (транспорт заходит внутрь помещения).
Рисунок 3 – Складские помещения класса C
Класс D:
Таким образом, требования к этому классу складов весьма жесткие. Далеко не все здания удовлетворяют им. Наиболее мягкие требования к складам класса D.
К ним относят такие площади, используемые под склады:
- подвальные помещения;
- объекты гражданской обороны;
- неотапливаемые производственные здания;
- ангары.
Рисунок 4 – Складские помещения класса D
Остальные складские помещения, в зависимости от своих конструктивных особенностей, попадают в классы B и C. Класс склада оказывает основное влияние на его стоимость приобретения или аренды.
Западная классификация складов
Британская компания разработала KnightFrank собственную систему, по которой определяются виды складов и их классификация. Эта система создана на основе мирового опыта и в некоторой степени адаптирована для работы в РФ. Классификация данной компании принята большинством крупных фирм, работающих в области оценки коммерческой недвижимости. Сейчас происходит её внедрение на российском рынке.
Рисунок 5 –Автоматизированные складские системы
Динамично развивающийся рынок складской недвижимости требует от участников классификацию уже существующих и еще строящихся объектов по единым критериям. На российском рынке коммерческой и жилой недвижимости большинством крупных компаний приняты объективные способы классифицировать эти здания. На очереди стоит классификация промышленных объектов, и разработки таких значимых фирм, как KnightFrank, могут стать его основой.
Введение единой классификации для некоторого сегмента коммерческой недвижимости ставит своей целью облегчить проведение операций с объектами недвижимости.
В западных странах используется базовая система, на основании которой определяется классификация и назначение складов в логистике. Это упорядочивает значительный спектр продукции, под который используются склады. Основным критерием в данной классификации является наличие у складского помещения условия, необходимых для хранения конкретного класса продукции.
Поэтому в обозначении категории склада сначала указывается его главная особенность, например холодильный терминал или склад с контролем уровня влажности.
Складским помещениям присваиваются один из шести классов, начиная от наиболее высокого А+ до самого низкого D. В этой шкале классов C+ и D+ не предусмотрено. Разделение на 6 классов позволяет более точно определить уровень оснащенности и эффективности здания. В целом, к складам класса А+ и А предъявляются более жесткие требования, чем к аналогичному классу по классификации компании «РМС».
Рисунок 6 –Склад класса А +
Наибольшая разница в высоте: класса А+ присваивается зданиям с высотой потолка 13 м, а класс А – 10 м. Также наблюдаются отличия в таких параметрах:
- шаг колонн и расстояние между пролетами;
- нагрузка на пол и его высота от земли;
- площадь застройки;
- наличие электрической подстанции и теплового узла;
- количество ворот и их оборудование;
- наличие автоматизированной системы учета товаров, контролирующей уровень доступа сотрудников;
- наличие парковки для легковушек;
- наличие ограждений и круглосуточной охраны;
- благоустройство территории;
- собственная железнодорожная ветка;
- опытный девелопер.
По этим требованиям видно, что большинство складов, которые в классификации компании «РМС» имеют класс А, по системе KnightFrank получат классы В+ или В. Тем не менее, оценка склада с помощью класса достаточно грубая, и для подсчета реальной стоимости аренды или приобретения складского помещения учитывается большое количество значимых параметров.
2 Анализ основной деятельности предприятия и грузопереработки на складе, разработка путей совершенствования переработки грузов на складе
2.1 Организационно-экономическая характеристика ООО «Метро Кэш энд Кэрри»
ООО «Метро Кеш энд Керри»– крупнейшая управляющая компания международного бизнес-формата, стоящая на четвертом месте в списке десяти мировых торговых компаний на 2010 год.
Миссия ООО «Метро Кеш энд Керри» – продажа высококачественных продуктов питания и товаров первой необходимости по невысоким ценам и в широком ассортименте
Принципы построения организационной структуры ООО «Метро Кэш энд Керри»:
- иерархичность уровней управления, при которой каждый нижестоящий уровень контролируется вышестоящим и подчиняется ему;
- соответствие полномочий и ответственности работников управления месту в иерархии;
- разделение процесса труда на отдельные функции и специализация работников по выполняемым функциям;
- формализация и стандартизация деятельности, обеспечивающие однородность выполнения работниками своих обязанностей и скоординированность решения различных задач;
- обезличенность выполнения работниками своих функций;
- квалификационный отбор, в соответствии с которым наем и увольнение с работы производятся в строгом соответствии с квалификационными требованиями;
Ассортимент ООО «Метро Кэш энд Керри». Соотношение продовольственной и непродовольственной групп товаров составляет 70% на 30% от общего числа позиций. Для более наглядного представления всей широты и глубины ассортимента, рассмотрим перечень товаров:
Продовольственные товары (Food).
Ассортимент продовольственных формируется таким образом, чтобы максимально подходить для профессиональных закупщиков. В ООО «Метро Кэш энд Кэрри» представлен широкий выбор известных брендов и собственных марок («Aro», «HORECA», «FineFood» и другие), предлагающих отличное соотношение цены и качества. Продукты категории «Fresh» доставляются в торговые центры ежедневно. Структура ассортимента представлена в приложении В.
Анализируя структуру непродовольственных товаров, можно сделать вывод, что большая ее часть приходится на товары для офиса (14 %), спортивные и сезонные товары (12 %), одежду (11 %) и на различное оборудование и технику (9-10%). Если учесть, что непродовольственные товары составляют приблизительно около 27000 наименований, то на офисные товары приходится около 3780 наименований товаров, на видеотехнику и оборудование приходится приблизительно 2700 видов товаров, на хозяйственные товары –1890 наименований товаров.
Аналогично проанализируется структуру продовольственной группы товаров в компании ООО «Метро Кеш энд Керри».
Анализируя данные структуры продовольственных товаров, видно, что большую часть этой структуры занимает категория «напитки», которая включает в себя «вино» (9 %), «безалкогольные напитки» (9 %) и «крепкий алкоголь» (6 %), затем приблизительно одинаковые ниши занимают категории «консервы», «молочные товары», «кондитерские изделия», «бакалея», «косметика», на которые приходится по 12% и 10% от общего количества наименований продовольственных товаров, которые составляют приблизительно 18000 наименований.
Делая вывод, можно сказать, что компания «Метро Кеш энд Керри» располагает сбалансированным и устойчивым ассортиментом, который представлен достаточной широтой и глубиной.
Правило Парето в ассортименте.
В ООО «Метро Кэш энд Кэрри» существует несколько стратегических направлений, которые являются главным преимуществом профессиональных покупателей копании. Направления: напитки, консервы, молочные товары, товары для дома и офиса. Именно эти 20% ассортимента обеспечивают 80% дохода компании. В приложении Г рассматриваются основные экономические показатели ООО «Метро Кэш энд Кэрри» в России.
Снижение среднего оборота одного магазина обусловлено массовым открытием торговых центров по всему миру за этот период. Стоит отметить, что строительство одного магазина обходится руководству в среднем в 12 млн $
В настоящее время ООО «Метро Кеш энд Керри» представлено более 700 торговыми центрами в 30 странах мира. Международная компания, занимающая ведущее положение на рынке в сфере оптовой торговли, по итогам 2017 года, вновь показала существенный рост, увеличив объем продаж на 4,6 %, что составило 31,1 млрд. евро. Размер прибыли до уплаты процентов и налогов (EBIT) вырос на 6,8 % и составил € 1,3 млрд.
Существует три основных категории клиентов ООО «Метро Кэш энд Кэрри»:
- предприниматели (Traders) - юридические лица, перепродающие продовольственные и непродовольственные товары (киоски, магазины, павильоны);
- HoReCa (Hotels (Отели), Restaraunts (Рестораны), Canteen (кафе, столовая)»
- предприятия и офисы: различные учреждения, администрации, институты, некоммерческие организации, предприятия сферы услуг.
Финансовые результаты хозяйственной деятельности ООО «Метро Кэш энд Керри» характеризуются показателями прибыли от продаж, прибыли до и после налогообложения и выражаются в тысячах рублей или в процентах к обороту (рентабельности). Анализ основных показателей финансово-хозяйственной деятельности ООО «Метро Кеш энд Керри» можно увидеть в приложении Б
Выручка в отчетном году составил 201448 млн. руб., что на 21,3% в относительной форме или на 35377 млн. руб. в абсолютном выражении больше оборота прошлого года. Рост продаж вызван расширением ассортимента, ценовым фактором. Валовая прибыль в отчетном году выросла на 32,21% в относительной форме по сравнению с прошлым годом или на 16577 тыс. руб. в денежной форме и составила 68037 тыс. руб. в 2017 году. Уровень валовой прибыли увеличился на 2,79% и составил 33,77% в 2017 году. Данная динамика связана с ростом уровня оптовой торговой надбавки на товары, реализуемые ООО «Метро Кеш энд Керри».
Негативно оценивается развитие издержек обращения предприятия. За отчетный период их величина растет быстрее, чем оборот реализации, а именно на 39,77%. В денежном выражении прирост издержек обращения составил 15380 тыс. руб., в результате чего они составили 54051 тыс. руб. в 2016 году. Данная ситуация обусловила увеличение уровня издержек обращения в 2017 году на 3,55% до 26,83% в общем обороте предприятия. Рост уровня затрат является негативным моментом и свидетельствует о перерасходе денежных средств, имеющихся у организации.
В результате отмеченных изменений прибыль от продаж ООО «Метро Кеш энд Керри» выросла на 9,36% в относительной форме или на 1197 тыс. руб. в абсолютном выражении и составила 13986 тыс. руб. в 2016 году. Одновременно наблюдается снижение рентабельности продаж с 7,7% в 2009 году до 6,94% в 2016 году. Данная динамика свидетельствует о снижении эффективности основного вида деятельности предприятия.
После уплаты налога на прибыль в размере 2082 тыс. руб. в прошлом году и 3692 тыс. руб. в отчетном году, предприятие получило чистую прибыль. Она составила в отчетном году лишь 198 тыс. руб., что ниже чистой прибыли, полученной в прошлом году на 9089 тыс. руб. в денежной форме. Такая ситуация не позволяет фирме формировать фонды для дальнейшего развития, пополнять собственные оборотные средства и так далее. Рентабельность конечной деятельности предприятия в динамике снизилась на 5,49% до 0,1% в 2016 году. Уменьшение рентабельности конечной деятельности предприятия свидетельствует о снижении эффективности работы ООО «Метро Кеш энд Керри».
Как таковых прямых конкурентов у ООО «Метро Кэш энд Керри» в России пока нет, поскольку оптовые базы не располагают таким широким ассортимент товаров, а другие магазины формата «Кеш энд Керри» (ECO, Junior, Classic) не представлены на российском рынке. Однако в качестве непрямых конкурентов ООО «Метро Кэш энд Керри Россия» можно назвать розничные торговые сети («Ашан», «Перекресток», «Магнит», имеющие столь же широкий ассортимент товаров), но работающие, главным образом, с физическими лицами.
Значительный процент товаров из ассортимента компании закупается у региональных производителей. Это позволяет представить клиентам «Метро Кэш энд Керри» товары высочайшего качества при минимальных затратах на логистику. Компания имеет базу постоянных поставщиков, лучших партнеров, где успешно работают ее торговые центры.
Для обеспечения богатого ассортимента для своих покупателей, компания сотрудничает с поставщиками, представленными ниже:
1 бакалея–ООО «Art-Food», ООО «Любавич», ООО «ИМАКО» и др.
2 дизайн– ООО «Визант», ООО «ART Peoplegroup», ООО «НИКОЛ+» и др.
3 молочные продукты – ООО «Димарко Трейд», ООО Торговый Дом «Биомикс», ООО «Юниджел» и др.
4 напитки– ООО «Алеф Трейд», ООО «Дайкон Континенталь», ООО «Лорд Прауд», ООО «Nespresso», ООО «ArtCoffee», ООО «RoyalCellar», ООО «Бородино», ООО «GourmetStyle» и др.
5 оборудование– ООО «Тарплан», ООО «ФС Консалтинг», ООО «ИМЛАЙТ», ООО «Bayland Музыкальные технологии», ООО «Masterglass»,ООО «BravilorBonamat» и др.
6 посуда и аксессуары– ООО «Алеф Трейд», ООО «Полная чаша», ООО «Dieta-HeresGroup», ООО «Dick» и др.
7 продукты питания– ООО «Valencia экспресс, фруктовая компания», ООО «Атардо-тропик», ООО «Дайкон Континенталь», ООО «Италика-Трейдинг», ООО «Фрегат», ООО «Аквариус» и др.
8 текстиль– ООО «Еланна», ООО «Ковакс», ООО «Авик-Тайм», ООО «Блайндс», ООО «SMILE», «АБ-Отельсервис», «Веста Альфа торговая компания» и др.[20].
ООО «Метро Кэш энд Керри» – социально-ответственный и активный партнер в развитии локальных поставщиков.Развивая местный рынок, тем самым развиваются клиенты. В ассортименте всегда присутствуют локальные производители, но, тем не менее, предоставляются определенные требования поставщикам по качеству товара, объему поставок, бесперебойности в поставках, ведении и предоставлении документов, наличие специального оборудования и многое другое. Компания ООО «Метро Кэш энд Керри» принципиальна в данных вопросах, так как она поддерживает международные стандарты ведения бизнеса. Компания представляет только тех поставщиков, чья работа и качество продукции устраивает на все 100%.
Привлекая и удерживая клиентов ООО «Метро Кэш энд Керри»
- оповещает клиентов с помощью METРO ПОЧТЫ. Журналы почты делятся на категории: продовольственные, непродовольственные и специализированные товары;
- оформляет карты безналичной оплаты (карты предоплаты);
- создает предварительные заказы для крупных клиентов.
Кроме того, ООО «Метро Кэш энд Кэрри» применяет промо-акций. К примеру, в июне 2012 года стартовала федеральная акция «минус 35%», приуроченая к открытию ТЦ в Брянске. В эту честь во всех торговых центрах была скидка на 35% на 2-3 товара из каждого отдела.
Летом 2012 года проводился «фестиваль собственных брендов». На входе стояли две тележки с товарами первой необходимости. В одной из них – собственные бренды ООО «Метро Кэш энд Кэрри», а во второй – бренды ведущих производителей. Суммарная разница в цене составляет примерно 2000 рублей в пользу собственных брендов.
2.2 Направления и методы совершенствования грузопереработки в ООО «Метро Кэш энд Кэрри»
Грузопереработка (MaterialsHandling) – это совокупность операций, выполняемых на различных стадиях складского технологического процесса [2].
Операции грузопереработки реализуются в рамках складского технологического процесса.
Этот процесс разделен на четыре основных этапа:
1 поступление товаров (состав логистических операций, выполняемых при получении товаров, может сильно варьироваться в зависимости от рода поступающего груза);
2 приемка товаров по количеству и качеству;
3 складирование и хранение товаров (осуществляется в виде штабельного или стеллажного хранения);
4 отпуск товаров со склада (отборка товаров из мест хранения, комплектование партиями, экспедирование грузов, погрузка транспортного средства).
Операции, осуществляемые на приведенных этапах, составляют основу складской деятельности, и эффективное осуществление этих операций является ключевым фактором производительности складов.
Следовательно, актуальным становится вопрос о совершенствовании как отдельных операций грузопереработки, так и функционирования всего склада в целом. Нами были проанализированы различные источники на предмет поиска существующих направлений оптимизации грузопереработки.
Следует отметить тот факт, что в литературе отсутствует какая-либо систематизация таких направлений, что говорит о непроработанности данного вопроса на сегодняшний день. Проведенный анализ позволил систематизировать все найденные способы оптимизации складской деятельности и выделить два направления оптимизации:
1 первое направление – логистические технологии, которые направлены на оптимизацию конкретных операций в складской деятельности (например, идентификация продукции, размещение поступающих продуктов, отгрузка продуктов);
2 второе – логистические технологии, которые оптимизируют деятельность склада в целом (таблица 1).
Таблица 1 Логистические технологии оптимизации грузопереработки
Оптимизация отдельных операций грузопереработки | Оптимизация деятельности склада в целом |
Штриховое кодирование, Радиочастотная идентификация | «Система управления складом» – WMS |
Кросс-докинг | Имитационное моделирование |
АВС-XYZ -анализ |
Источник: собственная разработка на основе [1].
Используя такую группировку, мы попытались выделить те логистические технологии, которые актуальны, если предприятие планирует незначительные изменения в своей складской деятельности, и те, которые потребуют от предприятия кардинальных изменений, аследовательно и финансовых затрат. Рассмотрим предложенные логистические технологии более детально и обозначим положительные эффекты от их применения:
1 внедрение штрихового кодирования на складе упрощает и ускоряет процесс идентификации продукции. Данная технология позволяет существенно ускорить процесс приемки продукции (в случае если на поступающих грузовых единицах уже имеется штрих-код), значительно снизить риск «человеческих ошибок» в процессе выполнения технологических операций и при проведении инвентаризации, а также упростить поиск нужного товара на стеллаже.
Внедрение штрихового кодирования также обоснованно тем, что все чаще крупные клиенты производственных предприятий ставят обязательным условием при закупках продукции наличие штрих-кода [3];
2 одним из перспективных направлений в складской логистике является радиочастотная идентификация (RFID). Данная система сравнительно недавно появилась за рубежом и пока в российской и белорусской практике еще не используется.
Основными элементами системы являются метки, антенна и компьютер. На метку с помощью компьютера наносится информация. Метка помещается внутри полеты. После этого все данные метки с помощью антенны переносятся в компьютер.
Применение радиочастотной идентификации позволяет контролировать перемещение груза, сокращать время на обработку информации и тем самым сокращать издержки [4];
3 следующее направление оптимизации складских операций – кросс-докинг. Кросс-докинг – это технология и сам процесс приемки и отгрузки товаров и грузов через склад напрямую, без размещения в зоне долговременного хранения.
При классической модели кросс-докинга имеет место прямая перегрузка из одного транспортного средства в другое (иногда сопровождаемая одновременной перетаркой, перекомплектованием и некоторыми другими возможными операциями с грузами и товарами).
Таким образом, кросс-докинг позволяет получить значительное сокращение издержек на складское хранение товаров и грузов, простои и порожний прогон транспорта и др.).
Причины и потребности, вызывающие необходимость применения кросс-докинга, могут быть самыми различными, но всегда продиктованы ситуацией, когда требуется оперативно ускорить процесс получения товара заказанного объема и комплектации конечными потребителями:
- перетарка контейнера с последующей его транспортировкой уже с измененным товарным наполнением;
- комплектация товара в наборе из различных отгрузочных источников (мест);
- прямая перегрузка товара из одного транспорта, пункт назначения которого кросс-докинговая площадка, в другой транспортировщик, пунктом разгрузки которого станет конечный потребитель, или другой склад, или средняя точка кросс-докинга [4];
4 размещение товаров на хранение необходимо производить таким образом, чтобы при последующих технологических операциях количество перемещений складских служащих было минимальным.
С этой целью производится деление всех товарных позиций на 3 группы, после чего для их хранения выделяются «горячие» и «холодные» складские зоны.
Для того чтобы произвести оптимальное деление всей номенклатуры, рациональным решением будет воспользоваться методикой ABC-XYZ-анализа.
В данном случае применительно к технологическому процессу основным критерием деления товарных позиций на группы будет выступать количество подходов/перемещений складского персонала при выполнении технологический операций, в частности при процедуре комплектации заказов в производство или клиентам.
После проведения ABC-XYZ-анализа вычисляется норма запаса по каждой товарной позиции, находящейся на складе единовременно, далее определяется количество мест хранения для каждой товарной позиции и производится размещение на основе проведенного анализа. «Горячая» зона, как правило, располагается ближе к зоне отгрузки, на стеллажах, находящихся в центральном проезде, в нижних ярусах стеллажей. Данное размещение позволяет существенно сократить время на выполнение технологических операций (размещение на хранение, комплектацию и т.д.) [5];
5 автоматизация склада с помощью системы управления складом WMS (WarehouseManagementSystem) позволяет существенно сократить время выполнения операций, уменьшить их стоимость, сократить количество ошибок, улучшить качество обслуживания клиентов, повысить производительность работы персонала, уменьшить издержки хранения товаров, т.е. осуществлять максимально эффективное управление складом.
Принцип работы WMS следующий. Территория склада разбивается на зоны по видам технологических операций в целях автоматизации процедур: приема, размещения, хранения, обработки и отгрузки товаров, что позволяет упорядочивать работу персонала на различных участках и эффективно распределять сферы ответственности.
На стадии внедрения в систему заносится описание физических характеристик склада, погрузочной техники, параметров всего используемого оборудования и правила работы с ними. Все поступающие грузы помечены штрих-кодами. Проведение технологических складских операций под контролем системы производится на основании данных штрих-кодов, мест хранения и погрузочной техники.
Погрузочная техника и работники склада оснащаются радиотерминалами ввода-вывода данных, которые представляют собой переносной компьютер, общающийся с главным сервером системы по радиоканалу.
Система может использовать любой из существующих типов кодов или печатать этикетки с внутренним штрих-кодом.
Система учитывает все требования к условиям хранения при распределении мест хранения для поступающих на склад товаров.
Например, могут учитываться влажность, температурный режим, сроки годности, производители, сроки реализации, поставщики, правила совместимости и любые другие параметры.
Система WMS автоматически подбирает места хранения для принятых грузов и формирует задания для работников склада. Задания поступают на экран радиотерминалов в виде элементарных поэтапных команд индивидуально для каждого работника [4, с. 66];
6 моделирование движения потоков позволяет определить их количественные характеристики.
Применительно к складской логистике имитационное моделирование как эффективный инструмент, обеспечивающий высокую точность расчета за счет возможности детального «проигрывания» поведения моделируемой системы, обеспечивает решение следующих задач:
- определение оптимального расположения складского комплекса на основе данных о возможных поставщиках, потребителях и посредниках;
- выбор объемно-планировочного решения при определении оптимальной пропускной способности и совместимости склада, выбор оборудования;
- определение количества выбранных типов подъемно-транспортного оборудования на основе анализа эффективности его работы;
- моделирование пропускной способноститехно-логических зон и логистической системы в целом;
- расчет количества портов прибытия и отправления транспортных средств;
- оптимальное расположение грузовых единиц в стеллажных складах и другие задачи.
Заметим, что каждая из перечисленных задач требует создания специальных имитационных моделей.
Разновидностью имитационного моделирования является дискретно-событийное моделирование, которое наилучшим образом подходит для имитации складских процессов, поскольку предполагает представление склада в виде системы массового обслуживания.
В модели заявки представляют собой прибывающие и убывающие транспортные средства и грузовые единицы, а ресурсы (объекты, осуществляющие обработку заявок) – единицы подъемно-транспортного оборудования выбранных типов в различных техно- логических зонах склада.
Описанный вид моделирования был реализован с помощью универсальной программы имитационного моделирования AnyLogic, разработанной организацией XJ Technologies. Входными параметрами имитационной модели являлись:
- интенсивность прибытия транспортных средств и их вместимость;
- технические характеристики подъемно-транспортного оборудования в соответствии с выбранными вариантами (габариты, скорость и т. п.);
- количество ярусов склада;
- количество и производительность персонала (время обработки одной грузовой единицы) в зонах контроля и комплектации.
Основной выходной параметр – оптимальное количество подъемно-транспортного оборудования, определяемое для каждой технологической зоны склада.
К дополнительным выходным параметрам в данной модели могут быть отнесены статистические параметры (грузооборот, количество операций грузопереработки в единицу времени и др.), измеряемые в процессе прогона модели [6].
Проанализируем рассмотренные логистические технологии с точки зрения предоставляемых ими выгод, а также операций, которые они оптимизируют (таблица 2).
На основании результатов анализа можно сделать вывод о том, что разработки в направлении совершенствования процессов грузопереработки производятся. Однако следует отметить что внедрение предлагаемых логистических технологий требует значительных затрат (в особенности это касается таких направлений, как внедрение штрихового кодирования, радиочастотной идентификации, внедрение Системы управления складом WMS), которые отечественные предприятия не могут себе позволить.
Следовательно, актуальным ставится вопрос о разработке и внедрении экономичных логистических технологий совершенствования складских операций, которые найдут отклик у отечественных производителей.
Таблица 2 Анализ логистических технологий совершенствования складской деятельности
Логистические технологии совершенствования грузопереработки.Оптимизация отдельных операций складской деятельности | Операции грузопереработки | Предоставляемые выгоды | |
1 | 2 | 3 | |
Штриховое кодирование, Радиочастотная идентификация | Идентификация товаров | Контроль перемещения груза, сокращение времени на обработку информации, что влечет за собой сокращение издержек | |
Внедрение кросс-докинга | Перемещение из зоны приемки в зону отгрузки | Значительное сокращение издержек на складское хранение товаров и грузов, простои и порожний прогон транспорта; ускорение процесса отправки грузов (однако, его применение возможно только при определенных условиях) | |
Применение АВС-XYZ-анализа | Складирование и хранение товаров | Минимизация перемещения складских служащих (сокращение времени на перемещение товара из зоны хранения в зону комплектования и отгрузки, что в свою очередь сокращает логистические издержки) | |
Оптимизация деятельности склада в целом |
| ||
Внедрение WMS (система управления складом) | Все операции | Высокая оборачиваемость склада, быстрая комплектация партий товара, отгрузка их потребителям |
Продолжение таблицы на следующей странице
Имитационное моделирование складских логистических процессов (дискретно-событийное моделирование) | Все операции | Оптимальное количество подъемно-транспортного оборудования, определяемое для каждой технологической зоны склада, что позволяет сократить как очередь заказчиков, так и очередь грузов (теория массового обслуживания), что значительно сократит логистические издержки склада |
2.3 Расчет ожидаемого экономического эффекта от предложных мероприятий
Расчет величины суммарного потока и стоимости грузопереработки на складе
Исходные данные для расчёта.
Таблица 3 Исходные данные.
Т, т/год | А1, % | А2, % | А3, % | А4, % | А5, % | А6, % |
5000 | 15 | 20 | 70 | 40 | 60 | 30 |
А7 , % | S1, уе/ ту | S2, уе/ ту | S3, уе/ ту | S4, уе/ ту | S5, уе/ ту | S6, уе/ ту |
200 | 0,6 | 2,0 | 5,0 | 1,0 | 4,0 | 0,8 |
Методика расчёта
1 Группа материальных потоков – грузы, рассматриваемые в процессе внутрискладского перемещения.
Перемещение грузов (механизированное, в контейнерах или на поддонах) осуществляется с участка на участок, а суммарный материальный поток по данной группе равен сумме грузовых потоков всех участков, без последнего.
Р п.г. = Т + Т*А1/100 + Т*А2/100 + Т*А3/100 + Т*А4/100, (1)
А1 - доля товаров, поставляемых на склад в нерабочее время и проходящих через приёмочную экспедицию, %;
А2 - доля товаров, проходящая через участок приёмки склада, %;
А3 - доля товаров, подлежащих комплектованию на складе, %;
А4 - доля товаров, попадающих на участок погрузки из отправочной экспедиции (уровень централизованной поставки), %.
2 Группа материальных потоков –грузы, рассматриваемые в процессе выполнения операций на участках разгрузки и погрузки. Грузопоток при ручной разгрузке груза составит:
Рр.р. = Т*А5/100 (т/год), (2)
Где А5 - доля доставленных на склад товаров, не подлежащих механизированной выгрузке из транспортного средства и требующих ручной выгрузки с укладкой на поддоны, %.
Остальная разгрузка является механизированной. Грузопоток при механизированной разгрузке груза составит:
Рм.р. = Т*(1-А5/100) (3)
Грузопоток при ручной погрузке груза составит:
Рр.п. = Т*А6/100 (4)
Где А6 - доля товаров, загружаемых в транспортное средство при отпуске со склада вручную (из-за неприспособленности транспортного средства покупателя к механизированной загрузке), %.
Грузопоток при механизированной погрузке груза составит:
Рм.п. = Т*(1-А6/100) (5)
3Группа материальных потоков –грузы, рассматриваемые в процессе ручной переборки при приёмке товаров:
Рпр. = Т*А2/100 (6)
4 Группа материальных потоков – грузы, рассматриваемые в процессе ручной переборки при комплектации заказов покупателей:
Ркм. = Т*А3/100 (7)
5 Группа материальных потоков – грузы, рассматриваемые в процессе выполнения операций в экспедициях. Если груз прибыл в нерабочее время, то он разгружается в экспедиционное помещение и лишь в ближайший рабочий день подается на участок приемки или в зону хранения. Следовательно, в приемочной экспедиции появляется новая операция, которая увеличивает совокупный материальный поток на величину:
Рп.э = Т*А1/100 (8)
Аналогично для отправочной экспедиции:
Ро.э.=Т*А4/100 (9)
Итого операции в экспедициях увеличивают совокупный материальный поток на величину:
Рэк. = Рп.э. + Ро.э = Т*(А1 + A4)/100 (10)
6Группа материальных потоков – операции в зоне хранения. Весь поступивший на склад товар сосредотачивается в местах хранения, где с ним выполняются обязательные операции по укладке на хранение и выемке из мест хранения. Таким образом минимальный материальный поток в зоне хранения составляет
2*Т или, по аналогии с приведенными выше формулами:
Рхр = Т*А7/100 (11)
где А7 - доля товаров, обрабатываемых на участках хранения (кратность обработки), 200%.
Величина суммарного материального потока на складе определяется по формуле:
Р = Рп.г + Рр.р + Рм.р. + Рр.п. + Рм.п. + Рпр. + Ркм. + Рэк. + Рхр. (12)
Суммарная стоимость работ с материальными потоками (стоимость грузопереработки) определяется по формуле:
Сгруз. = S1*Рп.г. + S2*Рэк. + S3*(Рпр. + Ркм) + S4 *Рхр + S5*(Рр.р.+ Рп.р.) + S6*(Рм.р. + Рм.п.) (13)
где S1 - удельная стоимость работ в процессе внутрискладского перемещения грузов, у.е./т;
S2 - удельная стоимость работ в процессе выполнения операций в экспедициях, у.е./т;
S3 - удельная стоимость работ в процессе выполнения операций на участкахприемки и комплектования, у.е./т;
S4 - удельная стоимость работ в процессе выполнения операций в зоне
хранения, у.е./т;
S5 - удельная стоимость работ в процессе выполнения операций ручной
погрузки и разгрузки, у.е./т;
S6 - удельная стоимость работ в процессе выполнения операций механизированной погрузки и разгрузки, у.е./т.
Расчёт результатов.
Р п.г. = 5000 + 5000*15/100 + 5000*20/100 + 5000*70/100 + 5000*40/100 = 12250
Рр.р. = 5000*60/100 = 3000
Рм.р. = 5000*(1-60/100) = 2000
Рр.п. = 5000*30/100 = 1500
Рм.п. = 5000*(1-30/100) = 3500
Рпр. = 5000*20/100 = 1000
Ркм. = 5000*70/100 = 3500
Рп.э. = 5000*15/100 = 750
Ро.э.= 5000*40/100 = 2000
Рэк. = 750 + 2000 = 2750
Рхр = 5000*200/100 = 10000
Р. = 12250+3000+2000+1500+3500+1000+3500+2750+10000 = 39500
Сгруз. = 0,6*12250+2*2750+5*(1000+3500)+1*10000+4*(3000+1500) + 0,8*(2000+3500) = 67750
Результаты расчёта приведены в таблице 4.
Таблица 4– Результаты расчёта
Группы материальных потоков. | Значение фактора Аi, % | Величина материального потока по данной группе, т/год. | Удельная стоимость работ на потоке данной группы, Si, у.е./т | Стоимость работ на потоке данной группы, у.е./год |
1 | 2 | 3 | 4 | 5 |
Грузы, рассматриваемые в процессе внутрискладского перемещения, Рп.г. | А1=15, А2=20, А3=70, А4=40. | 12250 | 0,6 | 7350 |
Грузы, рассматриваемые в процессе выполнения операций на участках разгрузки и погрузки, Рр.р. | 60 | 3000 | 4 | 12000 |
Грузы, рассматриваемые в процессе выполнения механизированной разгрузки груза, Рм.р | 60 | 2000 | 0,8 | 1600 |
Грузы, рассматриваемые в процессе выполнения ручной погрузки груза, Рр.п. | 30 | 1500 | 4 | 6000 |
Продолжение таблицы на следующей странице.
1 | 2 | 3 | 4 | 5 |
Грузы, рассматриваемые в процессе выполнения механизированной погрузки, Рм.п | 30 | 3500 | 0,8 | 2800 |
Грузы, рассматриваемые в процессе ручной переборки при приёмке товаров, Рпр. | 20 | 1000 | 5 | 5000 |
Грузы, рассматриваемые в процессе ручной переборки при комплектации заказов покупателей, Ркм. | 70 | 3500 | 5 | 17500 |
Грузы, рассматриваемые в процессе операции, которые в экспедициях увеличивают совокупный материальный поток на величину, Рэк. | А1=15, А4=40. | 2750 | 2 | 5500 |
Грузы, рассматриваемые в процессе операции в зоне хранения, Рхр | 200 | 10000 | 1 | 10000 |
Суммарный внутренний материальный поток, Р | 39500 | 67750 |
Расчёт точки безубыточности деятельности склада
Исходные данные для расчёта
Таблица5–Исходные данные для расчёта.
Показатель | |
1 | 2 |
R, у.е./год | 5500 |
K | 0,050 |
N, % | 8,0 |
Спост, у.е./год | 330000 |
Расчёт
Доход предприятия оптовой торговли зависит от торговой надбавки и рассчитывается по формуле (для одного вида товара):
Д = Т*R*N /100, (14)
где Д - доход, у.е./год;
Т - входной (выходной) материальный поток, т/год;
N - торговая надбавка, %;
R - цена закупки, у.е./т.
Прибыль склада составит:
П = Д - Собщ (у.е./год) (15)
где Со6щ - общие издержки, у.е./год.
Собщ = Сперс + Спост (16)
где Сперс ,Спост - соответственно переменные и постоянные издержки, у.е./год.
Постоянные издержки не зависят от грузооборота склада и включают в себя расходы на аренду складского помещения, амортизацию, оплату электроэнергии и тепла, заработную плату управленческого персонала и специалистов и др. Переменные издержки зависят от грузооборота и складываются из процентов за кредит (Скр) и стоимости грузопереработки (Сгр). Размер процентов за кредит определяется по формуле:
Скр = k*T*R (17)
где k - коэффициент пропорциональности, зависящий от величины запаса ибанковского процента.
Подставляя в формулу 15 выражения для определения дохода и общихиздержек, получим:
П = Т*R*N/100 - k*Т*R - Сгр–Cпост (18)
В точке безубыточности
Сгр = Сгр.уо.*Тбу(19)
где Сгр.уо - удельная стоимость грузопереработки, приходящаяся на 1т грузооборота склада, рассчитываемая по формуле:
Сгр,уо. = Сгр/Т (20)
Подставив в формулу 18 формулы 19 и 20 и приравняв правую часть к нулю, получим формулу для расчета точки безубыточности:
Тбу*R*N/100 - k* Tбy*R - Сгр,/Т*Тбу - Cпост = 0
Отсюда:
Тбу = (100*Спост)/(R*N - 100*k*R - 100*Cгр/T) (21)
Расчёт результатов
Тбу = (100*330000)/(5500*8 - 100*0,05*5500 - 100*67750/39500) = 2021,009
Т >Тбу, значит предприятие прибыльное.
склад безубыточность запас
Заключение
На сегодняшний день ни одно предприятие не может существовать без складской деятельности а особенно без грузопереработки на складе. Потребность в складах объясняется тем, что они предназначены не только для накопления и хранения запасов товара, но и для прохождения временной и пространственной разницы между производством и применением продукции.
Работа склада состоит из комплекса задач, которые связанны с подготовкой к приемке и приемкой товаров, размещением их на хранение, организацией хранения, подготовкой к отпуску и отпуск покупателям этого товара. Все эти операции в совместности и образуют технологический процесс[24].
Управление товарными запасами предполагает их нормирование, контроль и регулирование. Нормирование товарных запасов разрешает разработать и установить их наилучшие нормативы. Для оптовых баз устанавливаются определенные нормы товарных запасов, которые должны гарантировать сопровождение их в экономических обоснованных размерах, для обеспечения бесперебойного и правильного снабжения розничных торговых предприятии товаром.
Важно правильно и грамотно организовать процесс грузопереработкина складе. Тщательный прием товар по количеству и качеству разрешает вовремя находить и предупреждать поступление недостающего количества товаров, а также товаров, качество которых не отвечает стандартам. Применение при хранении рациональных способов укладки, соблюдение всех принципов хранения товара, организация постоянного контроля за хранением товара, всё это обеспечивает отсутствие их потерь, а также создает удобства для их правильной и быстрой отборки, способствует более эффективному использованию складской площади.
Необходимо соблюдать технологию выдачи товара, а это и получение заказов от покупателей, и отбор товаров с мест хранения, и перемещение их в зону комплектования заказов, и само комплектование заказов и упаковка, и передвижение укомплектованного товара в зону погрузки, и погрузка транспорта и внимательность складских работников.
Все это способствует правильному, четкому и быстрому выполнению заказов потребителей, а значит и повышению репутации самого предприятия.
В настоящее время для складов наиболее важной направленностью является полная автоматизация и механизация работ на складе, компьютеризация учетных и других операций. Это ведет к повышению требований к высокой квалификации и уровню подготовки всех работников склада.
Дата добавления: 2018-08-06; просмотров: 848; Мы поможем в написании вашей работы! |
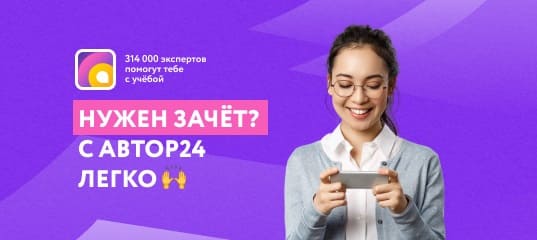
Мы поможем в написании ваших работ!