Титан и сплавы на его основе.
ЦВЕТНЫЕ МЕТАЛЛЫ И СПЛАВЫ
К цветным металлам относятся все металлы за исключением железа, марганца, хрома и сплавов на их основе. Наиболее широко применяют сплавы на основе Cu, Al, Mg, Ti, Zn, Ni, Pb, Sn.
Условное обозначение основных элементов, входящих в состав металлов и сплавов приведено в таблице 2.1.
Таблица 2.1 – Условное обозначение основных элементов, входящих в состав металлов и сплавов.
Элемент | Обозначение | Обозначение в марках металлов и сплавов | Элемент | Обозначение | Обозначение в марках металлов и сплавов | ||
черных | цветных | черных | цветных | ||||
Алюминий | Al | Ю | А | Ниобий | Nb | Б | - |
Азот | N | А | - | Олово | Sn | - | О |
Барий | Ba | - | - | Свинец | Pb | - | С |
Бериллий | Be | - | Б | Селен | Se | Е | - |
Бор | B | Р | - | Сера | S | - | - |
Ванадий | V | Ф | - | Серебро | Ar | - | Ср |
Вольфрам | W | В | - | Сурьма | Sc | - | С |
Железо | Fe | - | Ж | Теллур | Te | - | - |
Кадмий | Cd | - | - | Титан | Ti | Т | Т |
Кремний | Si | С | К | Углерод | C | У | - |
Магний | Mg | - | Мг | Фосфор | P | П | Ф |
Марганец | Mn | Г | Мц | Хром | Cr | Х | - |
Медь | Cu | Д | М | Церий | Ce | - | - |
Молибден | Mo | М | - | Цинк | Zn | - | Ц |
Мышьяк | As | - | Мш | Цирконий | Zr | Ц | - |
Никель | Ni | Н | Н |
|
|
Алюминий и сплавы на его основе
Алюминиевые сплавы в соответствии с основными компонентами получили следующие названия: силумины (алюминий – кремний), дюралюмины (алюминий – медь – марганец), магналий (алюминий – марганец). В зависимости от назначения они подразделяются на литейные и деформируемые (до 80% от всех сплавов).
Сплавы алюминиевые литейные применяют для фасонных отливок. Выпускается 37 марок литейных сплавов, подразделенных на пять групп в зависимости от основы.
Сплавы алюминиевые деформируемые предназначены для изготовления листов, лент, полос, профилей, панелей, прутков, труб, проволоки, штамповок и поковок методом горячей или холодной деформации. Они выпускаются следующих марок: АД0, АД1, АД, ММ, АМц, АМцС, Д12, АМг1, АМг2, АМг3, АМг4, АМг5, АМг6, АД31, АД33, АД35, АВ, Д1, Д16, Д18, В65, АК4, АК4-1, АК6, АК8, В95, 1915, 1925.
Применение алюминия и его сплавов всегда рационально там, где они могут заменить нержавеющие стали, латунь и другие, более дорогие цветные металлы.
Для изготовления нефтехимической аппаратуры чаще всего применяют технически чистый алюминий марок АД0 и АД1 (ГОСТ4784-74), с содержанием не менее 99,3% алюминия. Химический состав и механические свойства технически чистого алюминия приведены в таблице 2.2.
|
|
Таблица 2.2 – Механические свойства технически чистого алюминия
Страна | Материал | Характеристика проката | ||||||
марка | стандарт | Содержание Al, %, не менее | стандарт | вид и состояние | толщина, мм | σв, МПа | σ0,2, МПа | |
Россия | АД0 | ГОСТ 4784-74 | 99,50 | ГОСТ 18475-82 | Трубы холоднокатные и холоднотянутые отожженные | по ГОСТ | 60 | – |
АД0 | ГОСТ 4784-74 | 99,50 | – | Листы отожженные | 3–10 | 60 | – | |
АД1 | ГОСТ 4784-74 | 99,30 | – | Листы горячекатные | 5–10,5 | 70 | – | |
ФРГ | Al99,7F6 | DIN 1712 | 99,7 | DIN 1745 | Листы мягкие | 20 | 60 | 20 |
Al99,5F7 | DIN 1712 | 99,5 | DIN 1746 | Трубы мягкие | ||||
Япония | AIPO, AITO, AIBO | – | 99,7 | – | – | – | 60 | – |
Наряду с технически чистым алюминием для изготовления сварных сосудов применяют сплавы алюминия, хорошо деформируемые и не упрочняемые термической обработкой. Обладая более высокими механическими свойствами, чем технически чистый алюминий, сплавы сохраняют высокую коррозионную стойкость в различных средах. Наибольшее применение нашли сплав алюминия с марганцем (АМг) и с магнием (АМг3, АМг5 и АМг6). Из сплава АМц изготовляют листы, трубы, прутки и плиты.
|
|
Широкое применение нашли алюминий и его сплавы в нефтеперерабатывающей и нефтехимической промышленности.
Алюминий широко применяется при изготовлении оборудования установок для получения жирных кислот. Из алюминия высокой чистоты (99,9%) изготовляют колонны, предназначенные для окисления парафина, корпусы и трубки (длиной до 7,5 м), конденсаторы для охлаждения, резервуары емкостью до 50 м3, предназначенные для отделения шлама. Из алюминия марки АВ2 монтируют резервуары для оксилата, баки емкостью до 270 м3 для хранения высокомолекулярных жирных кислот (от С7 и выше).
Алюминиевые сплавы применяют для изготовления теплообменных аппаратов нефтеперерабатывающих заводов. Трубчатые пучки этих аппаратов обычно изготовляют из алюминиево-магниевого сплава марки АМг или АМг2. Трубки развальцовываются в трубной решетке, изготовленной из алюминиево-магниевого сплава марки АМг6Т.
Такие теплообменники с поверхностью теплообмена около 50 м2, успешно работают при давлении в корпусе 2 кГ/см2, в трубках 1,5 кГ/см2. Среда в корпусе аппарата – пары бензина, нагретые до 130 оС. В трубки поступает охлаждающая вода с температурой 25 – 30 оС.
|
|
Теплообменники такого же типа работают на установках ЭЛОУ при следующих условиях эксплуатации: в корпус поступает обессоленная нефть, нагретая до 90 оС, в трубки – сырая нефть с температурой 25 – 30 оС. Давление в корпусе 6, а в трубках – 12 кГ/см2.
Теплообменник предназначен для подогрева высоковязких нефтепродуктов. Аппарат изготовляют полностью из алюминиево-магниевых сплавов, что позволяет: увеличить коррозионную стойкость в серосодержащих средах в 4 – 6 раз и увеличить теплопередачу в аппарате по сравнению с аналогичным стальным аппаратом до 40%.
Из алюминиево-магниевых сплавов изготовляются также теплообменники, предназначенные для нагрева, конденсации и охлаждения нефти, нефтепродуктов и других жидких газо-парообразных сред.
Из сплавов АМг изготовляются трубы, работающие в пресной воде оборотной системы водоснабжения нефтеперерабатывающих заводов при температуре 45 оС. В этих условиях трубы из сплава АМг в 3 – 4 раза долговечнее, чем из углеродистой стали и в 2 раза долговечнее труб из нестабилизированной латуни.
В морской воде трубы из сплава АМг в 6 – 7 раз долговечнее, чем стальные, но в 3 раза менее долговечны, чем трубы из латуни ЛА 77-2.
Коррозийная стойкость алюминиево-магниевых сплавов в охлаждающей воде может быть повышена методами оксидирования поверхности труб. Оксидные пленки увеличивают срок службы оборудования из алюминиево-магниевых сплавов, потому что период до начала коррозионного разрушения из- меняется, а скорость коррозионного процесса уменьшается.
Одной из перспективных областей применения алюминиевых сплавов являются конденсаторы воздушного охлаждения, в которых охлаждающей средой служит атмосферный воздух, прогоняемый вентилятором по межтрубному пространству, в то время, как по трубкам транспортируются конденсируемые пары :или охлаждаемые жидкие продукты. Для придания конденсаторам большой эффективности в них ставятся трубы с развитой за счет оребрения теплопередающей поверхностью.
Вследствие своей высокой коррозионной стойкости в атмосфере промышленных предприятий, содержащей обычно примеси углекислого и сернистого газа, сероводорода, влаги и других агрессивных агентов, алюминиевые сплавы являются весьма подходящим материалом для изготовления оребренных трубных пучков. В тех случаях, когда продукт не обладает заметной агрессивностью по отношению к алюминиевым сплавам, применяются монометаллические отрубы. В противном случае применяются трубы, во внутреннюю поверхность которых впрессовывается вкладыш из латуни монель-металла или нержавеющих сталей, стойких к данному продукту .
Из алюминиево-магниевых сплавов изготовляются крыши и верхние пояса резервуаров для хранения сырых агрессивных сернистых нефтей. Так, резервуар с алюминиевой крышей и верхним поясом емкостью 1000 м3 состоит из шести нижних поясов, выполненных из стали марки Ст3 методом рулонирования, и седьмого – верхнего пояса, выполненного из алюминиевого сплава марки АМг, в виде десяти отдельных монтажных элементов.
Алюминиевая крыша резервуара монтируется из одного центрального и двенадцати плоских щитов. Щиты состоят из каркаса, выполненного из сварного двутавра, прессованных швеллеров и уголков. Листы кровли привариваются к каркасу щита. Заводские и монтажные сварные соединения конструкции резервуара из алюминиевых сплавов выполняются аргонодуговой сваркой. Стальной и алюминиевый пояса соединяются на бензостойкой полихлорвиниловой прокладке оцинкованными болтами.
Для хранения ряда химических продуктов применяются резервуары, целиком изготовленные из алюминиевых сплавов. Так, для хранения жирных кислот изготовляются резервуары емкостью 700 м3 из алюминиево-магниевых сплавов марки АМг5В.
Нефтепроводы из алюминиевых сплавов, ввиду их коррозионной устойчивости в атмосфере можно прокладывать без защитных покрытий и окраски.
Легкость алюминиевых труб снижает стоимость их укладки, по сравнению со стальными трубами. Кроме того, трубы из алюминиевых сплавов имеют высокую чистоту обработки внутренней поверхности, в результате чего уменьшаются потери напора на трение жидкости, которые могут быть на 10% ниже, чем в стальных трубах. Вес труб из алюминиевого сплава приблизительно в 3 раза меньше веса соответствующих стальных труб. Поэтому, несмотря на относительную высокую стоимость, в ряде случаев целесообразнее применять алюминиево-магниевые трубы.
Химический состав и механические свойства листов из алюминиевомарганцевых сплавов приведены в таблице 2.3.
Таблица 2.3 – Содержание элементов и механические свойства алюминиево-марганцевых сплавов
Страна | Сплав | Проката | ||||||||||
марка | стандарт | Содержание, %, не более | стандарт | вид и состояние | толщина, мм | σв, МПа | σ0,2, МПа | |||||
Mn | Fe | Si | Cu | Zn | ||||||||
Россия | АМц | ГОСТ 4784-74 | 1-1,6 | 0,7 | 0,6 | 0,15 | 0,1 | ГОСТ 347-61 | Плиты горячекатные | 11-25 | 120 | – |
26-80 | 110 | – | ||||||||||
ГОСТ 12592-67 | Листы горячекатные | 5-10,5 | 100 | – | ||||||||
ГОСТ 18475-73 | Трубы мягкие | ГОСТ | 90 | – | ||||||||
США | 3003 | – | 1-1,5 | 0,7 | 0,6 | 0,2 | 0,1 | – | – | – | – | – |
Германия | AlMnF10 | DIN 1725 | – | 0,5 | – | 0,1 | – | DIN 1745 | Листы мягкие | До 6 | 100 | 40 |
DIN 1746 | Трубы мягкие | До 10 | 100 |
Лучшими (по сравнению с алюминиево-марганцевыми сплавами) механическими свойствами обладают алюминиево-магниевые сплавы.
Медь и сплавы на её основе
Медь – пластичный металл розоватого – красного цвета; плотность при 200С – 8,94 г/см3, температура плавления 10830С, отжиг 500 – 700 0С. Механические свойства сильно меняются в зависимости от обработки: sв = 220-450 МПа; d=4 – 60%; НВ = 350 – 1300 МПа.
На нефтеперерабатывающих и нефтехимических заводах медь и ее сплавы широко применяются для изготовления трубок теплообменной и конденсационно-холодильной аппаратуры, а также для изготовления некоторой аппаратуры при производстве смазочных масел и спиртов из нефтяных газов. Трубчатые змеевики, применяемые для обогрева емкостей жирных кислот, а также некоторые аппараты для производства спиртов из нефтяных газов изготовляются обычно из красной меди. Так, для изготовления щелочного скруббер-аппарата бутылочного типа диаметром 2200 мм в верхней и 1100 мм в нижней части, высотой 10750 мм применяется медь марки МЗ.
Латуни – сплавы меди с цинком. При введении третьего, четвертого и более компонентов латуни называют сложными, или специальными; к ним относятся алюминиевая латунь, железомарганцевая латунь, марганцево-оловянно-свинцовая латунь и т.д. По сравнению с медью латуни обладают большой прочностью, коррозионной стойкостью, упругостью и лучшей обрабатываемостью (литьем, давлением и резанием).
По химическому составу нормировано 8 марок простых латуней: Л96, Л90 (томпак); Л85, Л80 (полутомпак); Л70, Л68, Л63 и Л60. Они обозначаются русской буквой Л, следующая за ней цифра указывает средний процент меди в этом сплаве. Cложные латуни (23 марки) в обозначении имеют после буквы Л другую букву, а цифры, размещенные после цифры, показывающей процент меди, указывают процент добавок в марке латуни. Например, ЛС59-1 обозначает латунь свинцовая, содержащая 57 – 60% меди и 0,8 – 1,5% свинца; ЛМцА57-3-1 латунь марганцово-алюминиевая, содержащая 55,0 – 58,5% меди, 2,5 – 3,5% марганца и 0,5 – 1,5% алюминия. Все добавляемые к латуни элементы обозначаются русскими буквами: О – олово, Ц – цинк, С – свинец, Ж – железо, Мц – марганец, Н – никель, К – кремний, А – алюминий и т.д.
По технологическому признаку латуни подразделяются на литейные и обрабатываемые давлением.
Литейные латуни поставляются в виде чушек. Предназначаются для изготовления фасонных отливок, характеристики и назначения которых приведены в таблице 2.4.
Таблица 2.4 — Марки, химический состав и назначение латунных отливок
Название и марка латуни | Химический состав*, % | Примерное назначение | ||
Сu | прочие компоненты | примеси, не более | ||
Кремнистая ЛК80-3Л | 78-81 | Si 3,0-4,5 | 2,8 | Детали, работающие в морской воде, при протекторной защите арматуры до 250 0С |
Кремнисто-свинцовая ЛКС80-3-3 | 77-81 | Si 2,5-4,5 Pb 2,0-4,0 | 2,3 | Подшипники и втулки неответственного назначения |
Алюминиево-железо-марганцевая ЛАЖМц 66-6-3-2 | 64-68 | А1 4,0—7,0 Fe 2,0—4,0 Мn 1,5—3,0 | 2,1 | Гайки нажимных работающих червячных винтов |
Алюминиевая ЛА67-2,5 | 66-68 | А1 2,0—3,0 | 3,4 | Коррозионностойкие детали, работающие в морской воде |
Алюминиево-железная ЛАЖ 60-1-2Л | 58-61 | Аl 0,8—1,5 Fe 0,8—1,5 Мn 0,1—0,6 Sn 0,2—0,7 | 0,7 | Арматура, втулки, подшипники |
Марганцево-никеле-железоалюминиевая ЛМцНЖА 60-2-1-1-1 | 58-62 | Al 0,5—1,0 Fe 0,5—1,1 Мn 1,5—2,5 Pb 0,5—1,5 | 2,3 | Арматура, не имеющая притираемых поверхностей, работающая на воздухе, в воде, масле, жидком топливе до 250 °С |
Свинцовая ЛС59-1ЛД | 58-61 | Pb 0,8—2,0 | 1,5 | Литье под давлением |
Свинцовая ЛС59-1ЛД | 57-61 | Pb 0,8—2,0 | 2,0 | Арматура, втулки, сепараторы для подшипников качения |
Марганцево-оловяно-свинцовая ЛМцОС58-2-2-2 | 57-60 | Мn 1,5—2,5 Sn 1,5—2,5 Pb 0,5—2,5 | 1,2 | Зубчатые колеса |
Марганцево-свинцовая ЛМцС58-2-2 | 57-60 | Mn 1,5—2,5 Pb 1,5—2,5 | 2,5 | Антифрикционные детали |
Марганцевая ЛМц58-2Л | 57-60 | Mn 1,0—2,0 | 2,0 | Детали, подвергающиеся лужению, заливке баббитом. Детали упорных и опорных подшипников, дейдвудных труб |
Марганцево-железная ЛМцЖ55-3-1 | 53-58 | Fe 0,5—1,5 Mn 3,0—4,0 | 2,0 | Несложные детали ответственного назначения, арматура, работающая при температурах до 300 °С |
Оловянно-свинцовая ЛВОС | 68-75 | Sn 0,5—2,0 Pb 1,0-1,3 | 1,5 | Штуцера гидросистем автомобилей |
Добавки этих металлов к латуням необходимы для улучшения их механических свойств или обрабатываемости, а также повышения коррозионной стойкости.
Бронзы – сплав меди (кроме латуней и медно-никелевых сплавов) с оловом (оловянные бронзы) и сплавы меди с алюминием, бериллием, кремнием, марганцем и другими компонентами, которые являются главными и в соответствии, с которыми бронзы получают названия. Как латуни, бронзы подразделяются на литейные и деформируемые. Обозначение бронз начинается с букв Бр. Справа ставят элементы, входящие в бронзу: О – олово, А – алюминий, Ф фосфор, Т – титан и другие, обозначаемые так же, как и в латунях, но цифры, стоящие за буквами, обозначают среднее содержание добавок этих дополнительных элементов в бронзе (цифры, обозначающие процентное содержание меди в бронзах, не ставят). Например, БрОЦ4-4 означает, что в бронзе содержится в среднем 4% олова, 3% цинка, остальное медь.
Большинство современных бронз редко содержат больше 7% олова и обычно имеют однофазную структуру, состоящую из твердого раствора олова в меди. Олово дороже и дефицитнее меди. Поэтому широкое применение нашли заменители – в первую очередь алюминиевые бронзы как простые БрА5, так и более сложные БрАЖМц10-3-1,5.
Бронзы оловянные, обрабатываемые давлением(деформируемые), подразделяются на следующие группы.:
Оловянно-фосфористые бронзы: БрОФ8,0-0,3 – для проволочных сеток целлюлозно-бумажной промышленности; БрОФ6,5-0,4 – то же, а также для пружин, лент, полос и деталей; БрОФ6,5-0,15 – для лент, полос, прутков, подшипниковых деталей, биметаллических изделий; БрОФ7-02 – для прутков; БрОФ4-0,25 – для трубок контрольно-измерительных и других приборов.
Оловянно-цинковые бронзы БрОЦ4-3 – для лент, полос, прутков, применяемых в электротехнике, машиностроении, для пружинной проволоки в химической промышленности.
Оловянно-цинково-свинцовые бронзы: БрОЦС4-42,5 и БрОЦС4-4-4 – для лент и полос, применяемых для прокладок во втулках и подшипниках.
Трубчатые пучки и решетки теплообменной и конденсационно-холодильной аппаратуры часто изготовляют из латуней различных марок. В частности, для изготовления трубчатых пучков конденсаторов широко используется латунь марки ЛО-70-1.
Ознакомление с опытом эксплуатации латунных труб на нефтеперерабатывающих и нефтехимических заводах показывает, что коррозия труб происходит из-за контакта поверхности трубы с технологическим продуктом, а также водой, охлаждающей трубчатую конденсационно-холодильную аппаратуру.
В ряде случаев, как, например, в конденсаторах установки термического крекинга разрушение латунных трубок происходит преимущественно за счет контакта внутренней поверхности трубок с охлаждающей (оборотной) водой.
При воздействии воды, охлаждающей трубчатые установки, чаще всего на поверхности трубок наблюдается появление язвин и сквозных разъеданий. Разрушение металла в этих случаях идет за счет обесцинкования латуни;
Для предотвращения обесцинкования латуни типа ЛО-70-1 и повышения ее служебных свойств в качестве материала труб конденсационно-холодильного и теплообменного оборудования нефтеперерабатывающих и нефтехимических заводов необходимо применять стабилизированную латунь.
Сроки службы трубок из стабилизированной латуни при коррозии с внутренней стороны (поверхности контакта с охлаждающей водой) значительно выше, чем у трубок из нестабилизированной латуни.
Высокой коррозионной стойкостью отличается стабилизированная алюминиевая латунь следующего состава: 76% меди, 2% алюминия, 0,05% мышьяка. Трубки, изготовленные из этого материала, развальцованные в трубных решетках из фосфористой бронзы (96,5% меди, 4,3% олова, 0,2% фосфора), показали в 2 раза более высокую коррозионную стойкость по сравнению с стабилизированной оловянистой латунью.
В ряде случаев на различных нефтеперерабатывающих установках трубчатые пучки конденсаторов, изготовленные из нестабилизированной латуни, служат без заметных коррозионных разрушений в течение ряда лет. Так трубки, изготовленные из латуни марки ЛО-70-1, установленные в конденсаторе деизобутанизатора установки алкилации Куйбышевского нефтеперерабатывающего завода служат в течение 6 – 7 лет. Такой же срок службы имеют трубчатые аппараты, изготовленные из латуни марки ЛО-70-1 на установке ГФУ в аппарате предконтактного холодильника крекинга и в других местах. Технологические среды, охлаждающие воды и режим работы аппаратов в этих случаях не вызывают быстрого разрушения нестабилизированной латуни.
Титан и сплавы на его основе.
Титан характеризуется небольшой плотностью, высокой прочностью и коррозионной устойчивостью ко многим агрессивным средам в частности, к морской воде, поэтому титан и сплавы на его основе широко используются в качестве конструкционного материала.
Чистый титан выпускают двух марок: ВТ1-00 и ВТ1-0, здесь титана более 99,5%. Титановые сплавы выпускают 14 марок.
Химический состав титана приведен в таблице 2.5.
Таблица 2.5 – Химический состав титана.
Страна | Марка титана | Ti, % | Примеси, %, не более | |||||
Fe | Si | C | O2 | N2 | H2 | |||
Россия | ВТ1-0 | Основа | 0,20 | 0,10 | 0,07 | 0,12 | 0,04 | 0,010 |
ВТ1-00 | » | 0,20 | 0,08 | 0,05 | 0,10 | 0,04 | 0,008 | |
Германия | RT-12 | » | 0,20 | – | 0,08 | 0,10 | 0,05 | 0,013 |
RT-15 | » | 0,25 | – | 0,08 | 0,20 | 0,06 | 0,013 | |
RT-18 | » | 0,30 | – | 0,10 | 0,25 | 0,06 | 0,013 | |
Япония | KS-50 | ≥99,5 | 0,15 | 0,10 | 0,08 | 0,10 | 0,01 | 0,01 |
KS-70 | ≥99,4 | 0,30 | 0,10 | 0,08 | 0,10 | 0,02 | 0,01 | |
США | MST | Основа | 0,25 | – | 0,03 | – | 0,04 | – |
Листы изготавливают из титана ВТ1-00 и ВТ1-0 и титановых сплавов ОТ4-0, ОТ4-1, ОТ4, ВТ5, ВТ6С, ВТ14 и ВТ20. Листы выпускают толщиной 0,3 – 0,8 мм (через 0,1 мм); 1,0; 1,2; 1,5; 1,8; 2,0; 2,2; 2,5 – 10,5 мм (через 0,5 мм), шириной 400 – 1200 мм, длиной 1500 – 5000 мм.
Существует мнение, что титан и его сплавы целесообразно применять для изготовления оборудования, подверженного действию сернистой коррозии и соленых вод. Применение титана для изготовления труб при бурении на газ и нефть позволит значительно реже производить их замену.
Представляет интерес изготовление стальных емкостей для нефти и нефтепродуктов с обкладками из тонкого листового титана, соединенного с основным металлом сваркой. Стоимость таких емкостей такая же, как емкостей, целиком выполненных из нержавеющей стали.
Высокая коррозионная стойкость титана в кислотах позволяет применять его в нефтяном и химическом машиностроении. Из титана изготовляют трубчатые теплообменники с трубками диаметром 25 мм и длиной 3 м, работающие в среде 15%-нога раствора гипохлорита натрия.
Титан пригоден для форсунок, работающих на морской воде, сеток фильтров, теплообменников, работающих в азотной кислоте. Так, в 60-ной азотной кислоте при 250 оС теплообменники из титана работают без повреждений в течение двух лет, а теплообменники из нержавеющей стали – всего 6 месяцев.
Крыльчатки из титана для центробежных насосов показали наиболее высокую коррозионную и эрозионную стойкость.
Паровые реактивные диффузоры, регулирующие высокое давление пара, изготовленные из титана, работают без заметных признаков разрушения 5 лет.
Технический титан марки ВТ1 и сплав ОТ4 применяются при изготовлении теплообменно-конденсационной аппаратуры нефтеперерабатывающих заводов.
Однако, поскольку трубы из ВТ1 и ОТ4 выпускаются длиной 3 – 4 м, а теплообменники и конденсаторы могут быть длиной до 12 м, возникла необходимость сваривать трубы из этих сплавов и приваривать их к трубным решеткам так же изготовленным из титана.
Наилучшие результаты сварки технического титана марки ВТ1 обеспечиваются автоматической сваркой под слоем флюса. В этом случае предел прочности и угол загиба сварных соединений равны прочности и углу загиба основного металла, а ударная вязкость несколько понижается (7,4 кГм/см2 против 14 кГм/см2 для основного металла). Высокие показатели получены также при сварке сплава ОТ4.
Коррозионная стойкость сварных соединений ВТ1 и ОТ4 в средах процесса прямой перегонки нефти (совместное воздействие хлористого водорода и сероводорода), а также и в жирных кислотах не уступает коррозионной стойкости основного металла. Глубинный показатель скорости коррозии составляет 0,001 – 0,064 мм/год.
Полевые испытания коррозионной стойкости технического титана марки ВТ1 сплава ОТ4 в среде оборотной охлаждающей воды показали, помимо полного отсутствия коррозии, также и отсутствие накипеобразования.
Все сказанное выше свидетельствует о том, что титан и его сплавы являются перспективным материалом для изготовления труб конденсационно-холодильного оборудования. За рубежом уже сейчас в химической промышленности успешно применяют конденсаторы и холодильники с трубными пучками из титана.
Биметалл
Для изготовления нефтезаводской аппаратуры широко применяется биметалл – двухслойный лист, состоящий из двух различных металлов. Основной (толстый) лист воспринимает нагрузку. Тонкий слой, называемый защитным или плакирующим, предохраняет основной слой от коррозионного действия среды: обычно в расчетах на прочность толщину тонкого слоя не учитывают. Толщина двухслойных листов по ГОСТ может быть в пределах от 4 до 160 мм.
Основной слой биметалла выполняется обычно из углеродистых сталей ВСт3сп5; 20К; марганцовистых сталей 16ГС, 09Г2С, теплоустойчивой хромомолибденовой стали 12ХМ и др. Защитный слой биметалла толщиной 1 – 6 мм выполняют из сталей 08Х13, 12Х18Н10Т, 10Х17Н13М2Т (для особо агрессивных сред), монеля, никеля и др. марок высоколегированных сталей и сплавов.
Для изготовления труб конденсационно-холодильного оборудования находит применение и биметалл: внутренняя часть труб изготовляется из стабилизированной алюминиевой латуни, а наружная часть – из малоуглеродистой стали.
Применение таких труб дает возможность значительно сократить потребление дефицитных медных сплавов.
Для устранения коррозии холодильников и теплообменников легких дистиллятов под действием H2S, NH3, и СО2 с успехом применяются биметаллические трубы (алюминий – латунь). Алюминиевое покрытие трубы играет роль протектора.
Дата добавления: 2018-08-06; просмотров: 306; Мы поможем в написании вашей работы! |
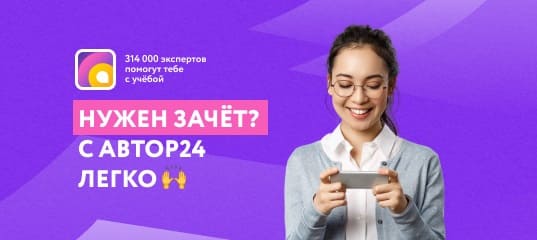
Мы поможем в написании ваших работ!