Литейные жаропрочные никелевые сплавы
Литейные жаропрочные никелевые сплавы по химическому и фазовому составам в значительной степени напоминают некоторые деформируемые никелевые сплавы. Например, зарубежные никелевые жаропрочные сплавы нимокаст 80 и 90 мало отличаются от нимоников 80 и 90 и т. д.
Наиболее высокие характеристики жаропрочности имеют жаропрочные литейные никелевые сплавы ЖС6-К (12% Cr, 2,75% Ti, 5,5% Al, 4% Mo, 4,5% Co, 5% W, 0,02% B), МАR-М-211 (9% Cr, 2% Ti, 5% Al, 10% Co, 5,5% W, 2,7% Nb, 0,05% Zr, 0,02% B), у которых предел длительной прочности при 900° С s100 = 320 МПа, апри 1000° С s100 =150-180 МПа. Объясняется это умеренным содержанием легирующих элементов, снижающих температуру солидуса (титан, ниобий, молибден, хром), и повышенным содержанием элементов, не снижающих температуру солидуса сплавов (кобальт, вольфрам), при высоком содержании алюминия.
Литейные жаропрочные никелевые сплавы применяют для изготовления лопаток, газотурбинных авиационных двигателей и других деталей. В последнее время сплав ЖС6-К (рис. 4.21) стали применять в деформируемом варианте (ЖС6-КП) за счет улучшения технологии его изготовления.
Для повышения жаропрочности особое значение приобретает использование высокочистых (по легкоплавким примесям) шихтовых материалов и защитных сред при плавке, разливке и термической обработке жаропрочных никелевых сплавов, исключающих окисление и обеднение поверхностных слоев изделий легирующими элементами.
Температура закалки жаропрочных никелевых сплавов определенным образом связана с их химическим (и фазовым) составом и количеством избыточных фаз-упрочнителей. Чем больше в сплаве основной упрочняющей фазы Ni3(Аl,Ti) или Ni3Al, тем, при прочих равных условиях, выше его температура закалки. Сплавы ЭИ437А, ЭИ437Б, а также нимоники 80 и 80А, содержащие в среднем около 10% фазы Ni3(Al,Ti), закаливают с 1080° С, а сплавы ЭИ867, ЭИ929 и нимоники 105 и 115, содержащие в 3-4 раза больше упрочнителя Ni3(Al,Ti), - с 1220°С. Применяют двойную закалку (1160° С, 2 ч, воздух и 1080° С, 4 ч, воздух), старение сначала проводят при 840° С в течение 2 ч, а затем — при 760° С в течение 16 ч. Такой режим старения обеспечивает наиболее оптимальное сочетание характеристик жаропрочности и пластичности.
|
|
Жаропрочные кобальтовые сплавы
Кобальт является аналогом никеля, но претерпевает полиморфное превращение. Ниже 477° С кобальт имеет ГПУ, а выше — ГЦК решетку. По характеристикам кратковременной и длительной жаропрочности кобальт и никель близки, хотя предел ползучести при сжатии кобальта при 1000° С в три раза выше, чем у никеля. Что касается сплавов, то наилучшие из жаропрочных кобальтовых сплавов не способны конкурировать с лучшими жаропрочными никелевыми сплавами. Если к этому добавить, что кобальт является дефицитным и дорогостоящим металлом, то станет ясно, почему жаропрочные кобальтовые сплавы стараются, где это возможно, заменить никелевыми. Существуют американские сплавы HS-23 (25% Ni, 19% Cr, 10%W, 1,5% Nb, 1% Fe) и YS-27 (10% Ni, 20% Cr, 15%W, 1,5% Mn, 0,5% Si), HS-21 (называемый виталлиумом, 32% Ni, 27% Cr, 5% Mo, 1% Fe, 0,25% C, 0,6% Mn, 0,6% Si)
|
|
Тугоплавкие металлы и сплавы на их основе
Металловедение тугоплавких металлов – это относительно новый раздел науки о металлах. Тугоплавкими называют металлы, температура плавления которых равна или выше температуры плавления хрома (1863 0С). Таких металлов в периодической системе Менделеева тринадцать. Они относятся к переходным металлам трех больших периодов периодической системы и находятся в IV-VIIIA группах (таблица 4.4).
Таблица 4.4.
Расположение тугоплавких металлов в периодической системе элементов
Номер периода | Номер группы | ||||
IVА | VА | VIA | VIIA | VIIIA | |
Первый | V | Cr | |||
Второй | Nb | Mo | Tc | Ru, Rh | |
Третий | Hf | Ta | W | Re | Os, Jr |
Хотя большинство из этих металлов известно науке давно (только гафний, рений и технеций открыты в 20 веке), широкое использование тугоплавких металлов в качестве основы конструкционных материалов началось относительно недавно, в послевоенные годы, особенно в 50-60-е годы. Развитие новых отраслей техники таких, как сверхзвуковая авиация, ракетная техника, ядерная энергетика, электронная промышленность, потребовало создание материалов, которые обладают высокой прочностью при температурах выше 1100 0С и даже выше 20000С. Жаропрочные стали и сплавы могут работать до 600-750 0С, жаропрочные сплавы на основе никеля и кобальта используются до 950-1050 0С. Современная технология создания супер-сплавов: получение быстрозакаленных сплавов методом гранульной металлургии, монокристаллическое литье, направленная кристаллизация и другие технологии позволяют поднять потолок до 1100-1150 0С.
|
|
К недостаткам следует отнести их высокую склонность к хладноломкости. Особенно ярко она выражена у металлов VIA группы – у хрома, молибдена и вольфрама. У этих металлов технической чистоты температура перехода из хрупкого состояния в пластичное лежит в выше комнатной (хром, вольфрам) или близка к комнатной (молибден). Это создает трудности при их производстве и применении. Другой существенный недостаток тугоплавких металлов заключается в их высокой склонности к окислению и к взаимодействию с другими газами воздуха (кроме кислорода) при нагреве, т.е. низкая жаростойкость. Это делает их нетехнологичными, требует применения защитных сред в виде инертных газов или вакуума при производстве полуфабрикатов и изделий. Кроме того, низкая жаростойкость тугоплавких металлов вызывает необходимость нанесения защитных покрытий на изделия при работе в условиях высоких температур.
|
|
При повышенных температурах химическая активность тугоплавких металлов резко возрастает. Это создает одну из главных проблем при работе с тугоплавкими металлами – их низкую жаростойкость. Заметное окисление тугоплавких металлов начинается при низких температурах – 400-6000С. Выше температуры 6000С все рассматриваемые металлы, за исключением хрома, активно взаимодействуют с кислородом. При рабочих температурах скорости окисления становятся катастрофически высокими, так, что не может быть и речи об использовании их в окислительной среде без защитных покрытий. Например, молибденовый лист без защиты при 12000С окисляется насквозь за несколько минут. Для повышения жаростойкости тугоплавких металлов в сплавы вводят небольшие количества активных металлов IIIA и IVА группы (V, La, Zr, Ti, Hf), которые образуют стабильные окислы. Наиболее часто используют плакирование более жаростойкими металлами (хромирование, цинкование); наносят термодиффузионным способом многослойные покрытия, в состав которых входит хром, кремний, или оксиды (Al2O3, ThO2, ZrO2), силициды MoSi2 и др.; наносят металлы электролитическим способом, напылением.
Сплавы тугоплавких металлов.
Ниобиевые сплавы.
Ниобиевые сплавы среди сплавов тугоплавких металлов являются самыми многочисленными. Так как ниобий имеет самую низкую плотность среди тугоплавких металлов. Поэтому по удельной прочности и жаропрочности в интервале температур 900-13000С. Эти сплавы имеют хорошую технологичность по сравнению с молибденовыми и вольфрамовыми. Кроме того, ниобиевые сплавы хорошо свариваются и имеют хорошую коррозионную стойкость. Основные легирующие элементы – молибден, вольфрам, цирконий (15%W, 10% Mo, 7% V, 5% Zr). Для гетерогенизации структуры в отдельные сплавы вводят углерод (ВН3, ВН4), а для улучшения технологических свойств некоторые сплавы легируют (раскисляют) редкоземельными металлами (La, Ce), например, сплавы ВН4,ВН5. Например для сплава ВН3, при комнатной температуре sВ= 770 МПа, при 1100 0С – 450 МПа, а при 1500 0С – 125 МПа.
Танталовые сплавы.
Основное преимущество танталовых сплавов – это их высокая технологичность при обработке давлением и хорошая свариваемость, позволяющая получать пластичные сварные соединения при комнатной и более низких температурах. Существующие жаропрочные танталовые сплавы содержат 1-2 легирующих элемента (вольфрам, цирконий, гафний, ниобий, ванадий). Эти элементы даже в больших количествах (до 10%) не охрупчивают тантал. По уровню прочности танатловые сплавы до 1200 0С находятся на уровне ниобиевых, а при более высоких температурах уступают молибденовым и вольфрамовым. Танталовые сплавы требуют защиты от окисления. Основой коррозионно-стойких сплавов являются сплавы системы Ta-Nb.
Молибденовые сплавы.
При создании жаропрочных сплавов молибден легируют элементами, упрочняющими матрицу за счет образования твердых растворов и частиц избыточных фаз. Но при таком легировании снижается пластичность и повышается температура хрупкого перехода. Поэтому молибденовые сплавы малолегированные, суммарное содержание элементов 1-1,5% (сплавы ЦМ2А (0,1%Zr, 0,2%Ti), ЦМ5 (0,5%Zr, 0,06%C), с рабочими температурами 13000С, sВ=250МПа и 16000С, sВ=500 МПа, соответственно), исключение составляют сплавы – повышенной жаропрочности - ЦМВ30 (30% W) и МР47ВП (47%Re), имеющий порог хладноломкости ниже комнатной. Все молибденовые сплавы требуют применения защитных покрытий.
Вольфрамовые сплавы.
Создание вольфрамовых сплавов имеет свои специфические особенности. Для этих сплавов необходимо повышение высокотемпературной кратковременной и длительной прочности, а также улучшение низкотемпературной пластичности. Повышение прочностных характеристик может быть эффективно реализовано за счет деформационного упрочнения, но такое упрочнение эффективно до 0,4 от температуры плавления. При более высоких температурах из-за развивающихся процессов рекристаллизации сплавы быстро разупрочняются. Чтобы снижение температуры плавления (солидуса) было минимально в вольфрамовые сплавы вводят Ta, Mo, Nb, Re. Для предотвращения охрупчивания создана группа сплавов типа МВ, ВР и МВР с 15-50% Mo и 5-25% Re (такие сплавы имеют при 13700С, sВ=324МПа, sВ=560 МПа, при 16500С, sВ=206МПа, sВ=210 МПа, соответственно). Максимально достигнутые характеристики жаропрочности связаны с гететрофазным упрочнением, т.е. сплавы с карбидным и оксидным упрочнением (сплав с 0,92%Zr-0,72%C при 16500С имеют sВ=546 МПа и при 19270С sВ=436 МПа, сплав с 4% Re-0,28%Hf – 0,39%C при 19270С, sВ=414 МПа). Повышение характеристик жаропрочности вольфрамовых сплавов может быть достигнуто за счет увеличения объемной доли упрочняющих фаз, однако при этом резко ухудшается технологичность сплавов. Поэтому возможно создание других сплавов при использовании металлургии гранул, механического легирования и т.д.
Подшипниковые сплавы
Подшипниковыми сплавами называются сплавы, из которых изготавливают вкладыши подшипников. Для этой цели применяют чугун, бронзу и легкоплавкие сплавы на основе свинца, олова, цинка или алюминия, так называемые баббиты.
Несмотря на все большее применение в машинах подшипников качения (шариковых или роликовых подшипников), подшипники скольжения применяются достаточно широко.
Металл вкладыша должен обладать следующими свойствами:
1) коэффициент трения со стальной поверхностью должен быть небольшим; 2) обе трущиеся поверхности должны мало изнашиваться; 3) этот материал должен выдерживать достаточные удельные давления.
Первое и второе требования удовлетворяются тогда, когда поверхность вала и вкладыша разделена пленкой смазки. Если структура вкладыша неоднородна и состоит из твердых включений и мягкой основы, то после непродолжительной работы («приработки») на поверхности вкладыша образуется микрорельеф — выступают твердые включения и между валом и вкладышем образуется пространство, в котором удерживается смазка (так называемый «принцип Шарпи»).
Подобной структурой обладают сплавы олова и сплавы свинца. Однако эти сплавы из-за своей низкой прочности не могут выдерживать больших давлений, а вследствие низкой температуры плавления — сравнительно небольшого нагрева. В современном машиностроении, как уже указывалось, для вкладышей подшипников применяют чугуны, бронзы и баббиты, а также пористые спеченные материалы.
Чугунные вкладыши изготавливают из серого перлитного чугуна (марки АЧЦ-1 и АЧЦ-2); это самый дешевый материал для вкладышей; он может выдерживать значительные удельные давления, но из-за более высокого коэффициента трения (у пары сталь — чугун по сравнению с парой бронза—сталь или баббит—сталь) чугунные вкладыши не следует применять в быстроходных двигателях.
Бронзовые вкладыши изготавливают из оловянистой и свинцовистой бронз. Благодаря неоднородной структуре бронзы (у оловянистой бронзы a-твердый раствор является мягкой основой, а эвтектоид a+b — твердыми включением) смазка хорошо удерживается на поверхности вкладыша. Бронзы обладают высокой прочностью. Сказанное позволяет применять бронзовые вкладыши для ответственных подшипников, работающих в тяжелых условиях (большие удельные давления, большие числа оборотов).
При применении очень мягких легкоплавких подшипниковых сплавов обеспечивается меньший износ шейки вала. Баббиты, кроме того, имеют и минимальный коэффициент трения со сталью и хорошо удерживают смазку. Поэтому наряду с чугунными и бронзовыми вкладышами в машиностроении для вкладышей подшипников широко применяют легкоплавкие сплавы на основе олова, свинца, а также цинка и алюминия.
Подшипниковые сплавы, созданные на основе олова или свинца, заливают в стальную или чугунную обойму подшипника (литейные сплавы). Ликвационная неоднородность существенно ухудшает их эксплуатационные свойства. Вращающийся вал и вкладыш (залитый сплав) истирают друг друга при любой, даже очень хорошей, смазке. В производственных условиях стремятся к тому, чтобы истирался главным образом вкладыш, заменить который сравнительно просто. Вал должен быть значительно тверже и изнашиваться гораздо меньше, чем вкладыш, но все таки вкладыш не должен быстро изнашиваться. Материал трущейся пары (в данном случае вал — вкладыш) подбирают таким, чтобы получить минимальный коэффициент трения при хорошей теплопроводности вкладыша. Среди чистых металлов в паре со сталью этим условиям удовлетворяет лишь серебро, которое из-за дороговизны применяют лишь для особо ответственных авиационных подшипников малого размера.
В оловянных и свинцовых сплавах такое сочетание противоположных свойств, материал вкладыша должен быть и твердым и мягким одновременно, осуществляется, если они двухфазны или даже многофазны. Одна из составляющих должна быть твердой, а другая мягкой и пластичной. Твердой составляющей должно быть меньше и ее кристаллы в виде включений должны быть равномерно распределены в мягкой составляющей (основе). В процессе прирабатываемсти сначала истирается мягкая основа и включения твердой составляющей оказываются выступающими (в рельефе), далее трение в основном переносится на них. Их обтекает смазка, находящаяся в зазоре между валом и вкладышем, и задерживается ими. Давление, возникающее в отдельных точках, амортизируется благодаря тому, что твердые включения сплава вдавливаются в мягкую основу.
Сплавы на основе олова, так называемые баббиты, применяются в качестве подшипников подвижного состава железнодорожного транспорта. Они легированы сурьмой (до 12 %) и медью (до 6,5%). Структура их в основном определяется диаграммой равновесия Sn—Sb (диаграмма перитектического типа). На микроструктуре сплава Б83 видна мягкая a-фаза (темная) и твердые кристаллы b-фазы (светлые квадраты). Фаза b при затвердевании выпадает в двойном сплаве в первую очередь. В b-фазе сурьмы значительно больше, чем в жидкой фазе, из которой она выпадает. Олово отличается гораздо большей плотностью, чем сурьма, и поэтому b-фаза всплывает — образуется ликвация по плотности. Чтобы предотвратить ее, вводят медь. Медь вместе с оловом образует e-фазу (~Сu3Sn), причем она тугоплавка и выпадает при затвердевании раньше b-фазы. По плотности она близка к жидкой фазе и поэтому при выпадении распределяется равномерно по всему ее объему. После нее из жидкости выпадают кристаллики b-фазы, но их всплыванию в тройном сплаве препятствуют мелкие кристаллики e-фазы. Подшипниковые сплавы на основе олова — это лучшие сплавы.
Сплавы на основе свинца являются их заменителями. Тройные сплавы легируют сурьмой (16—18%) и медью (до 3%). В тройных сплавах, содержащих 3 % Сu, сурьма выделяется в виде правильно ограненных первичных кристаллов и является твердой составляющей подшипникового сплава. Мягкой основой служит эвтектика Pb—Sb. Хотя она содержит 87 % Рb, все же она тверже и хрупче, чем a-фаза в баббитах на основе олова. Ликвация по удельному весу в сплавах Pb—Sb еще больше, чем в сплавах Sn—Sb, так как свинец имеет большую плотность, чем олово, а сурьма (твердая фаза) легче b-фазы. Введением меди в свинцовые сплавы преследуют ту же цель, что и введением ее в сплав Б83. Образуется соединение Сu3Sb, которое равномерно взвешено в жидкой фазе, обогащенной свинцом, и препятствует всплыванию кристаллов сурьмы.
Для повышения пластичности и прирабатываемости в подшипниковые сплавы на основе свинца, кроме сурьмы, вводят олово (до 16 %). Рассматриваемый тройной сплав 68/16/16 (Б 16) не слишком легкоплавок — температура начала его плавления составляет 245°С. В него также вводят 1,5—2 % Си для предотвращения ликвации по плотности. Содержание в нем ограничивают величиной около 0,1 ,% каждого элемента. В сплавы типа Б16 для улучшения их антифрикционных свойств вводят Ni, Cd, As (до 1%), Те (до 0,1 %).
Таблица 4.18.
Состав и структура баббитов
Марка баббита | Содержание элементов, % | Примеси | Структура | |||||
Sn | Sb | Cu | Pb | Прочие | Осн. | Твердое | ||
Б83 | Основа | 10-12 | 5,5-6,5 | - | - | 0,55 | Sn | SnSb, Cu3Sn |
Б89 | Основа | 7,2-8,2 | 2,5-3,5 | - | - | 0,55 | Sn | Cu3Sn |
Б6 | 5-6 | 14-16 | 2,5-3,0 | Основа | 2,0 Сd | 0,4 | Pb | SnSb, Cu3Sn |
БТ | 9-11 | 14-16 | 0,7-1,1 | Основа | 0,1 Te | 0,6 | Pb | SnSb |
БН | 9-11 | 13-15 | 1,5-2,0 | Основа | 0,8 As 1,0Ni 1,5Cd | 0,35 | Pb | SnSb, SnAs2 |
Б16 | 15-17 | 15-17 | 1,5-2,0 | Основа | - | 0,6 | Pb | SnSb, Cu3Sn |
БС | - | 16-18 | 1,0-1,5 | Основа | 1,0Ca 0,7Na | 0,5 | Эвтектика | Sb |
БК | - | - | - | Основа | - | 0,7 | Pb | Pb2Ca, Pb3Na |
Приведенные в таблице 4.18. составы баббитов можно разделить на три группы. К первой относятся оловянносурьмяные (Б83 и Б89), ко второй — свинцовооловян-носурьмяные (Б6, БН, Б16), к третьей — свинцовые баббиты, не содержащие олова. Баббиты второй группы Б6, БН, БТ, кроме олова, сурьмы и меди, содержат еще добавки других компонентов. Назначение этих присадок различное — мышьяк увеличивает жидкотекучесть (облегчается заливка вкладыша), никель повышает твердость, что уменьшает износ, аналогично влияет и кадмий. Роль теллура и мышьяка — образовывать мелкие твердые включения, повышающие износоустойчивость баббита.
Оловянносурьмяные баббиты (Б83 и Б89) являются наилучшими. Оловянная основа вязкая и пластичная и менее склонна к усталостному разрушению. На втором месте стоит оловянносвинцовосурьмяный баббит (Б16), в котором мягкая основа — свинец. Оловянносвинцовосурьмяные баббиты значительно дешевле оловянно-свинцовых, а по качеству уступают им ненамного. Хуже свинцовосурьмяный баббит (БС), основой которого является недостаточно пластичная эвтектика. Баббит БК (кальциевый), применяемый в железнодорожном транспорте, как и баббит БС, является относительно дешевым сплавом, его структура: основа — свинец, твердые включения — химические соединения свинца с кальцием и натрием. Свойства этих баббитов приведены в таблице 4.19.
Таблица 4.19
Свойства баббитов
Марка баббита | Плотность г/см3 | tпл, 0С | sВ, МПа | d,% | Коэфф. трения | a×106 |
Б83 | 7,5 | 380 | 90 | 6 | 0,005 | 21 |
Б89 | 7,3 | 342 | 90 | 9 | - | - |
Б6 | 9,6 | 460 | 70 | 0,5 | 0,005 | 21 |
БТ | - | - | 80 | 2 | 0,009 | 23 |
БН | 9,5 | 400 | 70 | 1 | 0,006 | - |
Б16 | 9,3 | 410 | 80 | 0,5 | 0,006 | 24 |
БС | 10,1 | 410 | 40 | 0,5 | 0,007 | 26 |
БК | 10,5 | 470 | 100 | 2,5 | 0,004 | 26 |
Дефицитность олова, а также свинца заставляет изыскивать и применять сплавы на другой, менее дефицитной основе (цинка, алюминия).
В качестве цинковых подшипниковых применяют сплавы марки ЦАМ10-5 и ЦАМ5-10. Их состав приведен в таблице 4.20 (там же указаны структура и некоторые свойства). Цинковые сплавы ЦАМ10-5 и ЦАМ5-10 уступают баббитам на оловянной основе по пластичности, коэффициенту трения и коэффициенту линейного расширения и примерно равноценны свинцовистым баббитам.
Имеется также серия алюминиевых сплавов, применяемых как подшипниковые. Это двухфазные высоколегированные сплавы, в которых твердый раствор на базе алюминия является мягкой основой, а химические соединения — твердыми включениями. Состав и некоторые свойства алюминиевых подшипниковых сплавов приведены в таблице 4.21. Алюминиевые подшипниковые сплавы обладают высокими свойствами (низким коэффициентом трения и высокой износостойкостью). Но по технологичности они уступают обычным баббитам. Их более высокая твердость является скорее недостатком, чем преимуществом сплава, так как требует обработки цапф и вкладыша повышенной чистоты, а шейка вала должна быть твердой. Наблюдение этих условий вызовет ускоренный износ. Высокий коэффициент линейного расширения алюминиевых баббитов требует более тщательной сборки с большими зазорами.
Таблица 4.20.
Состав и некоторые свойства цинковых баббитов
Марка баббита | Содержание элементов, % | Свойства | |||||
Al | Cu | Плотность г/см3 | tпл, 0С | d,% | Коэфф. трения | a×106 | |
ЦАМ10-5 | 10 | 5 | 6,3 | 395 | 0,5 | 0,009 | 27 |
ЦАМ5-10 | 5 | 10 | 7,1 | 500 | 1 | - | 28 |
Примечания: 1. Мягкая основа баббитов — эвтектика Zn+Al+CuZn3; твердые включения — CuZn3. 2. Предел прочности указанных баббитов 300 МПа.
Алюминиевые баббиты применяют вместо оловянных и свинцовых баббитов, а также свинцовистой бронзы.
Таблица 4.21.
Состав и некоторые свойства алюминиевых баббитов
Марка баббита | Содержание элементов, % | Твер- дые включ | Свойства | |||||||
Sb | Pb | Mg | Др. | Плотность г/см3 | tпл, 0С | sВ, МПа | d,% | a×106 | ||
АСС6-5 | 5,5 | 4,5 | AlSb | 3,1 | 750 | 80 | 14 | 24 | ||
АСМ | 4 | - | 0,6 | AlSb | 2,8 | 750 | 90 | 29 | 24 | |
АН2,5 | 3,0Ni | Al3Ni | 2,9 | 650 | 140 | 23 | 25 | |||
Алькусин D | 8,5Cu 2,0Si | CuAl2 | 2,9 | 632 | 160 | 1 | 26 |
Дата добавления: 2018-08-06; просмотров: 1206; Мы поможем в написании вашей работы! |
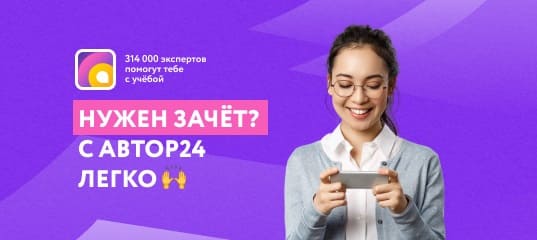
Мы поможем в написании ваших работ!