Технология разборочных работ.
Разборка - это часть технологического процесса ремонта, содержащая работы по разъединению объекта ремонта на детали и сборочные единицы.
Цель разборочных работ - подготовка материальной основы производства предметов дальнейшего труда (деталей, узлов и агрегатов) для восстановления или использования без ремонтного воздействия.
Разборочные работы занимают важное место в общем комплексе деятельности ремонтного предприятия. Производственный процесс ремонта автомобилей отличается от автомобилестроения наличием в первую очередь, разборочных, моечных и дефектовочных работ.
Если на автомобилестроительных заводах основой производства является изготовление деталей из заготовок, то ремонтное производство немыслимо без восстановления изношенных деталей.
Качество выполнения разборочных работ существенно влияет на технико-экономические показатели работы ремонтного предприятия.
Разборочные работы включают очистку, собственно разборку, подъемно-транспортные (по перемещению объекта) работы и дефектацию.
Как правило, все эти работы выполняются на участке разборочно-моечных работ авторемонтных предприятий.
Разборка наиболее трудно поддается комплексной механизации, является одной из самых трудоемких операций технологического процесса ремонта автомобилей и выполняется в наиболее неблагоприятных для ремонтников условиях (если плохо выполнены предыдущие операции по очистке).
|
|
Например, от общей трудоемкости этих работ на долю собственно разборочных приходится 60-65%.
На разборочные работы приходится до 11% трудоемкости капитального ремонта машин.
Опыт ремонтных предприятий показывает, что соблюдение технологии разборочных работ и применение при этом эффективных средств механизации позволяет увеличить объем повторного использования подшипников на 15-20%, нормалей до 25%, кронштейнов до 10% и снизить себестоимость ремонта автомобилей на 5-6%.
Количество годных деталей, трудоемкость восстановления деталей, требующих ремонта, зависит от организации и технологии выполнения разборочных работ.
Такие дефекты в деталях, как трещины, пробоины, погнутость, обломы, срыв резьбы и другие, часто появляются в результате нарушений технологических приемов разборки (применение кувалд, ломов, сварки).
Последовательность разборки, ее трудоемкость, необходимые средства технологического оснащения предусматриваются технологическим процессом на разборку.
Общие предупредительные мероприятия при текущем ремонте:
1.Разборку машины (агрегата, узла) выполнять только в необходимых для устранения неисправности (отказа) пределах; разборка - сборка приработанных сопряжений сокращает их ресурс.
|
|
2. Снятые агрегаты (турбокомпрессор, электрооборудование, радиатор и некоторые другие) перед разборкой должны пройти приремонтную диагностику.
3.Сохранять по месту крепежные детали, если они не мешают последующему проведению ремонтных операций (шпильки блока и др.)
4.Перед разборкой рекомендуется проверять величину запаса на регулировку в конических парах шестерен, конических подшипниках, в рулевом управлении и др.
5.Не раскомплектовывать крышки шатунов, крышки коренных подшипников, наружные обоймы конических и цилиндрических подшипников и др.
6. В парах шестерен с кратным числом зубьев (i =1,2,3…) перед разборкой разметить зубья с тем, чтобы при последующей сборке сохранить взаиморасположение шестерен..
Технологическим процессом капитального ремонта предусматривается полная разборка машин на детали.
В отдельных, оговоренных техническими условиями на капитальный ремонт, случаях полная разборка некоторых узлов и сборочных единиц, детали которых имеют неразъемные соединения (заклепочные, сварные, паяные, клеевые) не выполняется, если в процессе эксплуатации не произошло их ослабление или повреждение.
|
|
Разборка автомобилей при капитальном ремонте производится по следующей схеме: общая разборка автомобиля на агрегаты, узлы и детали; разборка агрегатов на узлы и детали; разборка узлов и сборочных единиц на детали
Порядок выполнения разборочных работ зависит от конструктивных особенностей автомобилей и метода организации производства на разборочных участках.
Разборка в зависимости от объема производства может быть организована на стационарных постах или поточных линиях. Основными организационными формами разборки являются непоточная и поточная организация.
В свою очередь при непоточной организации разборка может быть организована на универсальных, специализированных или смешанных постах.
Непоточная форма организации разборки, как правило, применяется при производстве текущего и среднего ремонта машин в войсковых ремонтных средствах.
Разборку агрегатов на узлы и детали проводят на стендах, эстакадах или конвейерах.
Поточная форма организации разборочного процесса является наиболее прогрессивной, позволяющей улучшить качество разборки, увеличить производительность труда и снизить себестоимость разборочных работ. Применение поточного метода позволяет сосредоточить одноименные технологические операции на специализированных постах, сократить количество одноименных инструментов на 30% увеличить интенсивность использования технологической оснастки на 50% и повысить производительность труда на 20%.
|
|
Машины, агрегаты со склада ремонтного фонда подают для разборки козловым краном и устанавливают на рельсовую тележку перед выездом на участок разборки.
В тех случаях, когда парк ремонтного фонда находится на значительном расстоянии от участка разборки, и нет возможности непосредственной подачи машины на тележке, применяют буксировку ремонтного фонда на жесткой сцепке.
Участок разборки, как правило, содержит рабочие места предварительной наружной мойки и слива остатков масел, предварительной подразборки, наружной очистки, разборки на агрегаты и узлы, наружной очистки деталей.
Рабочие места располагают вдоль конвейера - транспортера или линии перемещения машин.
На посту предварительной разборки обычно снимают сиденья, обшивку кабин, приборы электрооборудования, аккумуляторные батареи, рулевое колесо, открывают пробки баков, лючки коробок передач, раздаточных коробок, крышки ведущих мостов, проводят другие работы, обеспечивающие в дальнейшем качественную очистку внутренних экранированных полостей.
Обычно таких постов не менее трех:
На первом посту с машины снимают кабину, оперение, радиатор, топливные баки, кузов.
Двигатель вместе с коробкой передач, раздаточную коробку снимают с шасси на втором посту. На этом же посту частично снимают приборы, трубопроводы систем питания тормозов.
Перед подачей на третий пост или непосредственно на нем шасси разбираемой машины, как правило, переворачивают с помощью кантователей вверх мостами (для удобства дальнейшей разборки), отсоединяют мосты, рессоры, реактивные штанги, карданные валы, амортизаторы, балансирные тележки и другие агрегаты и узлы.
Снятые на постах разборки агрегаты и узлы после их наружной очистки передают на посты разборки агрегатов и узлов.
Эти посты могут быть расположены или в непосредственной близости от мест разборки машины на агрегаты, или территориально обособлены от них.
Снятые при разборке детали укладывают в контейнеры и подают в установки для мойки и далее на участок контроля и дефектации.
Для предотвращения повреждения деталей в процессе разборки необходимо соблюдать определенные правила выполнения работ.
При разборке агрегатов и узлов необходимо сохранять комплектность пар с ограниченной взаимозаменяемостью: шатун-крышка нижней головки шатуна, блок цилиндров двигателей - крышки коренных подшипников, шестерни механизма газораспределения, ведущая и ведомые шестерни главных передач и другие (перечень таких пар приводится в технических условиях на капитальный ремонт).
В процессе разборки детали пар с ограниченной взаимозаменяемостью должны быть скреплены между собой (болтами, вязальной проволокой).
Применение зубил, газовых резаков для срубания резки болтов, гаек крайне ограничено, и оно особо оговаривается инструкциями на выполнение работ. Запрещается при разборке наносить удары непосредственно по концам валов, имеющих резьбу, по обоймам подшипников, шестерням.
Для предотвращения повреждения этих деталей при разборке должны использоваться выколотки, проставки, снабженные наконечниками из цветных металлов.
Основными средствами технологического оснащения процессов разборки являются: подъемно-транспортное, прессовое оборудование, стенды, оснастка и инструмент (с механизированным или ручным приводом), технологическая тара, стеллажи, подставки (стандартные и нестандартные, специализированные и универсальные.
Для подачи ремонтного фонда на участок разборки снятия кузовов, кабин, двигателя, мостов и других сборочных единиц, имеющих значительные габариты или массу более 20кг, используют мостовые, козловые краны, кран-балки.
Для перемещения машин, агрегатов из парка хранения в производственное здание используют лебедки, а для перемещения по постам в процессе разборки - тяговые, грузонесущие, толкающие конвейеры (транспортеры)..
Для поворота шасси, корпусов гусеничных машин, агрегатов и других сборочных единиц, имеющих значительные габариты и массу, применяют кантователи.
Основным оборудованием для разборки посадок с натягом (снятие шкивов, шестерен, извлечение из картеров подшипников, осей, гильз блоков цилиндров…) являются прессы и съемники.
Широкое распространение для разборки соединений с переходными посадками и посадок с натягом получили универсальные гидравлические установки.
Для разборки резьбовых соединений применяют ручной инструмент (ключи рожковые, накидные, коловоротные и трещоточные) и механизированный (пневматические, электрические, гидравлические гайковерты, сверлильные машины).
В целях создания удобств и повышения производительности труда для разборки агрегатов, узлов применяют различного рода стенды.
Разборка многих сопряжений невозможна без специальной оснастки или инструмента.
Повышение эффективности работ по разборке может быть обеспечено за счет комплекса организационно-технологических и экономических мероприятий, широкого внедрения средств механизации разборки резьбовых, заклепочных и неподвижных соединений.
Основными направлениями повышения эффективности разборочных работ являются:
-Совершенствование организации разборочных работ за счет рационального разделения труда между исполнителями;
-Механизация процессов разборки, внедрение высокопроизводительного оборудования;
-Всемерное сокращение затрат ручного труда на транспортные операции;
-Обеспечение заинтересованности рабочих в улучшении качества своего труда и в увеличении числа годных деталей;
-Постоянное повышение квалификации рабочих, занятых на разборке;
-Улучшение санитарно-гигиенических условий труда и культуры производства..
Дата добавления: 2018-08-06; просмотров: 2653; Мы поможем в написании вашей работы! |
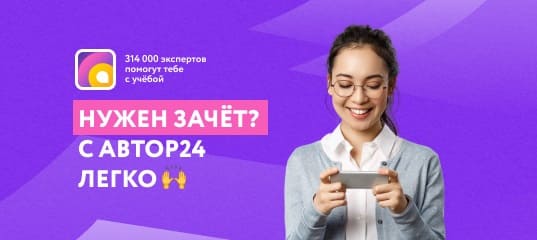
Мы поможем в написании ваших работ!