Требования по надежности, точности и технологичности, предъявляемые к деталям и механизмам электронных приборов.
Понятие о надежности приборов и ее обеспечение
В литературе и в стандартах, посвященных надежности, под надежностью технического изделия понимают его свойство выполнять заданные функции, сохраняя эксплуатационные показатели в установленных пределах (т.е. работоспособность), соответствующих заданным режимам и условиям использования, технического обслуживания, хранения и транспортирования в течение требуемого промежутка времени или требуемой наработки.
Под наработкой понимают объем или продолжительность работы изделия, которые измеряются в единицах времени, длины, массы, количестве повторных циклов функционирования и т.д. Например, наработка выключателей, реле измеряется в числе циклов включения-выключения; наработка двигателей и покрышек автомобиля - в километрах; наработка источников и приемников излучения, аккумуляторов - в часах работы.
Надежность изделия обусловливается его безотказностью, ремонтопригодностью, долговечностью и сохраняемостью.
Безотказность- свойство изделия сохранять работоспособное состояние в течение заданного времени или наработка без вынужденных перерывов.
Ремонтопригодность - свойство изделия, заключающееся в его приспособленности к предупреждению, обнаружению и устранению отказов, а также поддержанию работоспособности путем технического обслуживания и ремонтов. Ремонтопригодность характеризуется затратами времени и средств на восстановление изделия после отказа и поддержание его в работоспособном состоянии.
|
|
Ремонтопригодность прибора закладывается на этапе разработки его конструкции (особенно при компоновке), обеспечивающей доступность к малонадежным элементам, контролепригодность, легкозаменяемость, удобство и простоту (рациональность) обслуживания и ремонта.
Долговечность - свойство изделия сохранять работоспособность до наступления предельного состояния, т.е. способность к длительной эксплуатации при проведении необходимого технического обслуживания и ремонтов.
Предельное состояние изделия - состояние, при котором его дальнейшее использование по назначению невозможно, недопустимо или нецелесообразно. Данное состояние наступает в случаях: когда после отказа прибора его невозможно восстановить, либо невозможно достичь требуемых показателей качества (например, точности); когда безопасность эксплуатации прибора ухудшается до недопустимых пределов; когда восстановление прибора после отказа экономически нецелесообразно либо его эксплуатация экономически не эффективна, так как он морально устарел и не обеспечивает необходимых производительности работы, сервиса, энергоемкости, габаритов и т.п.
|
|
Сохраняемость -свойство изделия сохранять значения показателей безотказности, ремонтопригодности и долговечности (т.е. эксплуатационные показатели) в течение и после хранения и транспортирования.
Наиболее эффективные методы повышения сохраняемости связаны с правильной конструкцией упаковки, консервацией, применением специальных защитных покрытий, профилактическим обслуживанием при хранении, а также повышением культуры работы транспортных и складских служб.
Одним из важнейших понятий надежности является понятие отказа.
Отказом называют неисправность, без устранения которой невозможно дальнейшее выполнение изделием всех или хотя бы одной из его основных функций, т.е. это событие, заключающееся в нарушении работоспособного состояния изделия.
Проектно-конструкторскими причинами появления отказов являются ошибки, заложенные в концепцию, структуру или конструкцию элементов прибора. Например, физический принцип работы и структура прибора не согласованы с условиями его эксплуатации (наличие электромагнитных полей, динамических нагрузок, климатических воздействий); неправильно выполнена компоновка (источник излучения нагревает эталонные элементы); неудачно выбран материал деталей и неправильно рассчитаны допуски на погрешности их размеров (деформации или децентрировки оптических деталей в оправах при колебаниях температуры).
|
|
Технологическимиили производственными причинами появления отказов являются нарушения технологических процессов изготовления и сборки деталей, дефекты материалов и комплектующих, а также отступления от инструкций и методик юстировки, калибровки, аттестации и испытаний приборов. Например, расклейка деталей из-за того, что они не были обезжирены перед склейкой, или вследствие применения клея с истекшим сроком использования.
Эксплуатационными причинами появления отказов являются ошибки операторов, эксплуатация приборов при недопустимых условиях и режимах, износ и старение элементов.
Отказы, возникающие в начальный период эксплуатации изделия, называют отказами этапа приработки. Они обусловлены, как правило, проектно- производственными ошибками и погрешностями, поэтому их называют часто конструкторско-технологическими отказами.
Отказы, появляющиеся после периода приработки (см. рис.109,б) называют отказами этапа нормальной работы.
|
|
Отказы, обусловленные старением, износом и коррозией элементов называютотказами этапа старения.
Внезапные отказы - отказы, появляющиеся внезапно в результате резкого, скачкообразного изменения основных параметров прибора под воздействием факторов, связанных с внутренними дефектами его элементов или с ошибками оператора. Наиболее характерным признаком внезапного отказа является то, что он может наступить в любой момент, предвидеть и предупредить его очень трудно. Чаще всего внезапные отказы происходят в начальный период эксплуатации прибора. Закон распределения случайного времени работы прибора до наступления внезапного отказа на этом этапе обычно носит экспоненциальный характер (см. рис. 107,а).
Постепенные отказы - отказы, при которых наблюдается постепенное изменение параметров прибора в результате естественного старения, износа, коррозии его элементов. Такими отказами является, например, отказ по точности вследствие износа направляющих подвижных функциональных систем прибора; заклинивание (или увеличение моментов вращения) окуляров бинокля из-за загустевания смазки; ухудшение контраста изображения из-за старения трубки видикона телекамеры или трубки монитора. Так как параметры элементов прибора ухудшаются постепенно, то данный отказ можно предвидеть и предупредить. Например, профилактической заменой элементов, срок эксплуатации которых приближается к предельному.
Естественно, что постепенный отказ не может произойти при испытаниях прибора или на этапе приработки. Закон распределения случайного времени работы прибора до появления постепенного отказа обычно близок к нормальному (рис. 107,б).
Полным отказом называют такой отказ, при возникновении которого невозможно использовать прибор по прямому назначению до устранения причины отказа. Например, перегорела лампочка подсветки марки автоколлиматора; не взводится затвор фотоаппарата.
Частичный отказ - отказ, связанный с ухудшением какой-либо одной из характеристик прибора, при котором возможно частичное использование изделия по прямому назначению. Например, невозможность включения светофильтра для повышения контраста изображения; появление осыпки в поле зрения, возникновение "ВАD" секторов на дисках компьютера.
Катастрофический отказ (тяжелый) - отказ прибора, приводящий к полному нарушению его работоспособности, устранение которого связано с большими экономическими и временными затратами. К нему относятся: разрушение оптических элементов; полная разъюстировка систем; поломки; деформации, заклинивания подвижных частей прибора (винчестера в компьютере); короткое замыкание в электросхемах (системной плате) и т.п.
Параметрические отказы - такие отказы, при которых прибор выполняет все свои основные функции, но один из эксплуатационных параметров (показателей) вышел за границу допустимых значений. Например, увеличился шум работы прибора, появился разворот (расфокусировка) изображения, ухудшилась точность функционирования. Часто параметрические отказы (особенно по точности) удается обнаружить не сразу, что может привести к нежелательным последствиям (например, к выпуску бракованной продукции).
Легкими отказами называют такие отказы, устранение которых не связано со значительными экономическими и временными затратами и не требует привлечения ремонтных служб. Например, замена предохранителей, источников излучения, элементов питания, тестирование программ после сбоя и т.п.
Опасными отказами называют такие, которые связаны с опасностью для жизни или здоровья людей, а также экологическими катастрофами. Если отказы не связаны с этими факторами, они называются безопасными.
Независимыми отказами называются такие, которые не являются причиной других отказов. Если же отказ возникает или изменяется вероятность его появления из-за других отказов, то он называется зависимым.
Примерами зависимых отказов являются: уменьшение срока службы лампы подсветки при подаче на нее напряжения выше номинального из-за сбоя регулировки блока питания; заклинивание гайки винтового механизма при поломке ограничителя вращения винта (двигателя).
Устойчивым отказомназывается такой, который устраняется только в результате ремонта, регулировки (тестирования) или замены отказавших элементов и блоков прибора.
Временный (самоустраняющийся) отказ - это самопроизвольно устраняющийся, без вмешательства обслуживающего персонала, вследствие исчезновения вызвавшей его причины. Такие отказы возникают часто из-за нарушения режимов или условий работы. Например, отказ из-за запотевания оптических деталей; из-за расфокусировки, обусловленной перепадом температуры; потеря точности из-за недопустимых внешних вибраций прибора.
Перемежающиеся отказы (сбои) - это внезапно повторяющиеся непродолжительные самоустраняющиеся отказы. Они свидетельствуют о наличие ненормальности в элементах прибора, программах или режимах и условиях его работы. Например, отказ из-за нарушения контакта лампочки подсветки, обусловленной ослаблением крепления и вибрациями прибора; погрешность некоторых результатов измерений из-за вируса в памяти приборного компьютера.
Устранимым отказомназывают такой, который подлежит устранению и может быть устранен.
Неустранимыйотказ-отказ, не подлежащий устранению (невосстанавливаемые объекты) или не поддающийся устранению.
По способу устранения отказы подразделяются на такие, которые осуществляются заменой элементов и блоков (из входящих в комплект прибора, или приобретаемых); юстировкой, регулировкой или настройкойотказавшего элемента или всего прибора; организационно-техническими мероприятиями: очисткой, смазкой, тестированием ("лечением").
Требования к точности
Точность функционирования, как было упомянуто выше, является одной из основных характеристик качества любого точного прибора. Обеспечение требуемой точности проектируемого прибора требует от конструктора знания источников погрешностей работы прибора, умения находить их влияние на точность, навыков расчета точности прибора и его функциональных устройств.
От того, насколько правильно будут решены вопросы выявления и учета погрешностей, назначения допусков, зависят показатели качества прибора, его технологичность и надежность.
Разновидности погрешностей, основные понятия и определения
В общем случае погрешность результата функционирования прибора обусловлена потерей информации, возникающей до преобразования входного сигнала в приборе, непосредственно в процессе преобразования и при регистрации (обработке) результатов.
Погрешности из-за потери информации до преобразования ее в приборе, а также при регистрации и обработке, называют обычно методическими погрешностями.
Погрешности, обусловленные потерей информации в оптических, механических, электронных и других ФУ, осуществляющих преобразование информативного параметра входного сигнала в информативный параметр выходного сигнала, называют инструментальными (аппаратурными, приборными).
Методические погрешности
Методические погрешности обусловлены ошибочностью или недостаточностью разработки принятой теории метода функционирования прибора в целом, допущениями в отношении объекта, сигнала или канала прохождения сигнала, неправильной ориентировкой прибора относительно объекта, дискретностью представления информации и т.п.
Методические погрешности, связанные с допущениями, особенно характерны для измерительных приборов, принцип действия которых основан на косвенных методах измерения.
Простым, но весьма наглядным примером возникновения методических погрешностей может служить погрешность, возникающая в измерительной схеме контроля диаметров d цилиндров в призматической опоре с помощью индикатора часового типа.
Отклонение диаметров (Δ d) от номинального значения контролируется относительным способом по отклонению стрелки индикатора от нулевого значения, настроенного по эталонному цилиндру. Однако из-за базирования контролируемых цилиндров в призме возникает методическая погрешность измерения отклонения диаметров:
,
Измерительная схема контроля цилиндров
где β - угол призмы.
Если, кроме того, и температура контролируемого цилиндра отличается от номинального значения (Т0=20 ° С) на некоторую величину D T, то дополнительно возникает методическая погрешность измерения из-за изменения температуры:
, (2)
где α - коэффициент линейного расширения материала цилиндра.
Ниже изображен график погрешности от мертвого хода червячной передачи, измеренной с помощью оптического кинематомера через один градус поворота (Y ) ведомого звена (примерно две точки контроля на зуб ведомого колеса). Если такую передачу контролировать в ограниченном числе точек (дискретно), например, в четырех-пяти, как это иногда делается на практике, то может возникнуть большая методическая погрешность, представляющая собой разность между истинным * и полученным при такой дискретности измерений
значениями максимальной погрешности:
(3)
Схема червячной передачи (а) и график ее мертвого хода (б)
Инструментальные погрешности
Инструментальные погрешности подразделяются на теоретические, технологические и эксплуатационные.
Теоретические погрешности обусловлены тремя видами допущений: структурными (допущения в законе функционирования прибора, в функции fi, связывающей информативные параметры входного (Xi) и выходного (Yi) сигналов),параметрическими (допущения в значениях конструктивных параметров (qi)); конструктивными (допущения в конструкциях высших кинематических пар).
Теоретические погрешности первого вида (структурные, схемные) возникают при замене точной функции преобразования сигнала приближенной зависимостью. Чаще всего это происходит, когда вместо нелинейной функции пользуются ее линейным приближением (замена некруглых зубчатых колес круглыми).
Теоретические погрешности второго вида (параметрические) обусловлены округлениями конструктивных параметров до значений, нормируемых стандартами, и округлениями иррациональных параметров.
Классическим примером возникновения подобной теоретической погрешности является конструкция индикатора часового типа, схема которого изображена на рисунке. Здесь при перемещении Y измерительного штока 1 с рейкой поворачивается триб Z 1, зубчатое колесо Z2, закрепленное на оси триба, и триб Z3, на оси которого насажена стрелка 2; поворот последней на угол Х позволяет сформировать отсчет по шкале 3.
Функция, связывающая перемещение штока (Y) и поворот стрелки (Х) индикатора (закон функционирования), имеет вид:
,
где m - модуль зацепления зубчатой рейки и триба (Z1); Z1, Z2, Z3 - числа зубьев соответствующих колес.
При расчете конструктивных параметров исходят из того, что Ymax = 10 мм, шкала имеет 100 делений, цена деления шкалы 0,01 мм. Следовательно, при Y = 1 мм стрелка должна совершить целый оборот (т.е. Х = 2π ). Для выполнения этого условия рассчитывают один из конструктивных параметров (модуль зацепления m), задавая значения других конструктивных параметров (числа зубьев колес).
Исходя из конструктивных, точностных и технологических условий, числа зубьев колес серийного индикатора, выпускаемого промышленностью, выбраны следующими: Z1 = 16, Z2 = 100, Z3 = 10.
Выразив значение модуля из и подставив соответствующие значения входящих параметров, получим расчетное (иррациональное) значение модуля:
= 0,19894... мм.
Если округлить это значение до ближайшего стандартного (по ГОСТ 9563-60), то значение модуля будет mс = 0,2 мм.
Разность между расчетным значением модуля и его стандартным значением определяется:
Δ m = mc - mp = 0,2 -0,19894... = 0,00106.
Погрешность измерения Y из-за округления модуля, на полном диапазоне измерений будет равна:
мкм.
Схема стрелочного индикатора
Это в несколько раз больше, чем допуск на всю суммарную погрешность работы индикатора. Поэтому разработчик вынужден пойти на нарушение требований стандарта и использовать специальный модуль m = 0,199 мм. Теоретическая погрешность измерения при этом остается, но будет существенно уменьшена, (так как Δ m = m - mр = 0,199-0,19894 » 0,00006 мм):
мкм.
Теоретические погрешности третьего вида (конструктивные) обычно возникают при конструировании высших кинематических пар кулачковых и рычажных механизмов.
На рисунке (а) изображена исходная схема кулачкового механизма, в котором толкатель 1 контактирует с поверхностью кулачка 2 в точке А0. При переходе от схемы к реальной конструкции конец толкателя будет представлять собой сферу или ролик (б) и контактировать с расчетным профилем кулачка в точке А.
Рис.86. Схемы кулачкового механизма
В результате возникает теоретическая погрешность положения толкателя:
где r - радиус сферы или ролика; β - угол давления.
Погрешность функционирования, возникающая из-за замены идеализированной кинематической пары "кулачок-толкатель" реальной парой, равна:
где β т, β н - текущее и начальное значения угла давления.
Погрешность функционирования будет отсутствовать в случае, когда угол давления постоянен, либо когда профиль кулачка скорректирован с учетом конкретного значения радиуса сферы толкателя. Расчет координат теоретического 1 и эквидистантного 2 профилей (в), использование инструмента при изготовлении профиля кулачка (фрезы, шлифовального круга) с радиусом, равным радиусу сферы или ролика толкателя, позволяет избежать возникновения конструктивной теоретической погрешности.
Технологические погрешности возникают в процессе изготовления и сборки элементов ОП и могут быть следующими: отклонения от расчетных значений характеристик материалов деталей (например, показателя преломления и средней дисперсии стекла, модуля упругости, коэффициента линейного расширения); погрешности размеров и форм деталей, возникающие при их изготовлении (например, погрешности радиусов кривизны и формы рабочих поверхностей линз, клиновидности призм, погрешности деления шкал, погрешности форм поверхностей направляющих); погрешности расположения и деформации деталей, возникающие при их сборке (например, децентрировки и деформации линз, перекосы шкал, погрешности значений воздушных промежутков).
К технологическим погрешностям часто относят погрешности параметров и характеристик покупных (стандартизованных) элементов и блоков (подшипников, приемников, шаговых двигателей, датчиков, АЦП и т.п.), т.к. их погрешности обусловлены дефектами изготовления. Однако если значения этих погрешностей известны (паспортизованы) и могут быть приписаны конкретным значениям информативного параметра выходного сигнала (Yi), то их относят к теоретическим погрешностям.
Технологические погрешности - это один из самых многочисленных и наиболее сильно влияющих на точность функционирования и качество изображения ОП источников погрешностей.
Эксплуатационные погрешности возникают из-за воздействия на ОП внешних и внутренних влияющих факторов: нагрузок, вибраций, сил трения, температуры, радиационного излучения, нестабильности источников питания и т.д. Влияние этих факторов приводит к изменению характеристик материалов; изменению размеров, формы и положения деталей (например, радиусов и формы кривизны поверхностей, длин плеч рычагов, значений воздушных промежутков между оптическими деталями, положения осей в подшипниках); изменению характеристик и параметров покупных изделий (например, чувствительности приемников).
Отличительной особенностью инструментальных погрешностей является то, что они могут быть измерены (исследованы) и занесены в паспорт прибора (устройства).
ТЕХНОЛОГИЧНОСТЬ и некоторые ее аспекты
Обеспечение технологичности конструкции изделия - это взаимосвязанные решения конструкторских и технологических задач, направленных на повышение производительности труда, достижение оптимальных трудовых и материальных затрат и сокращение времени на производство, техническое обслуживание и ремонт изделия.
Оценка технологичности конструкции может быть качественной и количественной. Обеспечение качественной оценки технологичности конструкции достигается опытом конструктора и технолога. Количественная оценка ведется с помощью системы показателей и применяется главным образом для сборочных единиц и специфицированных изделий. В помощь студентам для ведения анализа качественной оценки технологичности конструкций и внесения корректив в чертежи деталей приведена табл. 1.1.
В зависимости от типа производства одна и та же конструкция может выполняться в разных вариантах с выбором наиболее экономичной заготовки в конкретных условиях (рис. 1.2). На рис. 1.2, а показана наиболее рациональная конструкция кронштейна – литая. При такой конструкции достигается наименьший расход металла (масса наименьшая), наименьший объем механической обработки. Однако в условиях мелкосерийного производства может оказаться, что литая конструкция детали будет менее экономичной, чем, например, сварная (рис. 1.2, б). При единичном типе производства, когда нужно изготовить всего несколько деталей, наиболее рациональной может стать конструкция, показанная на рис. 1.2, в, вырезанная непосредственно из полосовой или толстолистовой стали.
Некоторые рекомендации
А. Технологичность механообрабатываемых конструкций
1. Обрабатываемые плоскости следует располагать по возможности на одном уровне.
Конструкция детали (вариант 2) дает возможность:
1) вести обработку за один проход или нескольких деталей одновременно;
упростить контроль размеров
2. Размеры поверхностей, обрабатываемых сборным или фасонным инструментом, должны быть связаны между собой, а также с установочной базой
Простановка размеров по варианту 2 облегчает определение размеров режущего инструмента, а также выдерживание размера С от установочной базы
3. Размеры, проставленные на чертеже, должны способствовать наиболее простому точному измерению обрабатываемых элементов
Размер А (вариант 2) упрощает точное измерение глубины и паза
4. При нарезании зубьев, шлицов, резьбы и т. п. поверхностей конструкция детали должна обеспечивать свободный выход режущего инструмента
В конструкции, выполненной по варианту 2, обеспечено требование технологичности за счет увеличения канавки А
5. При сверлении отверстий поверхности деталей у входа и выхода сверла должны располагаться перпендикулярно к оси инструмента
![]() | ![]() |
В конструкциях, выполненных по варианту 2, заданные технологические требования обеспечены, что ведет к предохранению инструмента от поломок и повышению точности расположения отверстия
Б. Использование принципа совместной обработки рабочих и базовых элементов детали
Этот принцип заключается в предпочтительности конструкции детали, позволяющей осуществлять совместную технологическую обработку (за одну установку) ее рабочих и базовых элементов, так как в этом случае точность их взаимного расположения будет выше.
Рис.8.
На рисунке изображены варианты упрощенной конструкции оправы линз объектива, в одном из которых оба рабочих элемента (РЭ1, РЭ2) не могут быть обработаны совместно с базовым элементом (а), а в другом такая возможность существует (б). В первом случае погрешность расположения РЭ2 относительно РЭ1 и БЭ будет больше, а, следовательно, хуже центрировка линз и точность выдерживания воздушного промежутка, чем во втором варианте. Обусловлено это тем, что при перестановке (технологическом перебазировании) оправы в патроне станка возникают погрешности взаимного расположения ее РЭ и БЭ, обусловленные изменением технологической и измерительных баз.
В. Использование принципа точностной технологичности деталей
Этот принцип заключается в учете экономических факторов при назначении допусков на характеристики материала детали и на погрешности ее изготовления.
Конструктор должен помнить, что от допусков на деталь в существенной степени зависит ее стоимость.
Рис.10.
На рисунке изображен график зависимости между допуском (δq)на точность изготовления детали и затратами по его выполнению (Zdq). На графике показана кривая, образованная участками равнобочных гипербол 1-4, характеризующих затраты на получение допуска при обработке детали на различном оборудовании, используя различный инструмент, оснастку и т.д. Узловые точки Э, П, Т, образованные пересечением соответствующих кривых, являются границами зон, характеризующими низкие, средние и высокие затраты и соответствующие им уровни точности технологических процессов, называемые экономическими, производственными и техническими* [30]*, [55]*.
Экономическому уровню точности (ЭУТ) технологических процессов (допуск обозначается dqэ) соответствует точность, получаемая в серийном производстве при изготовлении деталей на автоматическом и универсальном оборудовании с помощью типового инструмента, оснастки и приспособлений. Контроль производится средствами, находящимися на рабочем месте (микрометры, индикаторы, калибры, эталонные стекла). Для заводов оптической промышленности экономический уровень, в среднем, начинается с 9-10 квалитетов точности.
Производственному уровню точности (ПУТ) соответствует точность dqп, получаемая в серийном производстве при изготовлении деталей также на автоматическом и универсальном оборудовании, но с применением специального инструмента, оснастки и технологических процессов (например, при изготовлении деталей на шлифовальных станках; с использованием алмазных резцов; разверток; кондукторов; приспособлений для центрирования заготовки; с увеличением числа повторных циклов ("выхаживанием") обработки поверхностей детали и т.п.). Контроль производится средствами, находящимися как на рабочем месте, так и в отделе технического контроля (ОТК) цеха. Производственному уровню соответствуют в среднем допуски по 6-8 квалитетам точности.
Техническому уровню точности (ТУТ) соответствует предельно высокая точность dqт, которая может быть достигнута с помощью специального (прецизионного) оборудования, инструмента, технологических процессов и условий производства. Например, для достижения точности нанесения делений на штриховых лимбах (диаметром около 100 мм) с погрешностью в 1-2" используют прецизионные делительные машины, производят стабилизацию температуры (до сотых долей градуса), давления и влажности в рабочем помещении, осуществляют защиту от вибраций и другие мероприятия. Контроль деталей выполняют с привлечением лабораторных средств (автоколлиматоров, микроскопов, интерферометров). Техническому уровню соответствуют допуски по 4-5 квалитетам.
Более высокую точность изготовления детали (зона Д) можно получить ее доводкой, выполняемой на станках, или слесарным способом вручную (шабрением, притиркой, развертыванием, прикаткой и т.п.), как правило, в процессе сборки детали в узел (обычно этот процесс называют технологической компенсацией погрешностей деталей). Левая граница этой зоны весьма неопределенна, так как в существенной степени зависит от квалификации рабочего, наличия необходимого оборудования, инструмента и контрольных средств.
Дата добавления: 2018-08-06; просмотров: 333; Мы поможем в написании вашей работы! |
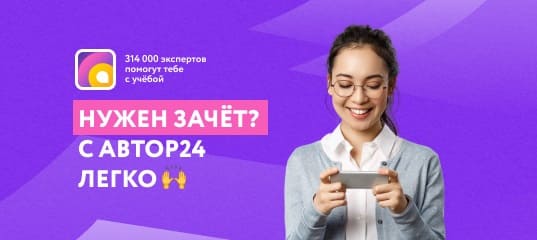
Мы поможем в написании ваших работ!