Области применения мартенситно – стареющих сталей
Лекция 12. Мартенситно – стареющие стали.
Мартенситно – стареющие стали обладают хорошим сочетанием высоких прочностных и пластических свойств, хорошей тепло- и хладостойкостью, достаточным сопротивлением хрупкому разрушению, размерной стабильностью при термической обработке.
Основными системами мартенситно – стареющих сталей являются: Fe – Ni, Fe – Ni – Co, Fe – Ni – Cr, Fe – Cr – Co, также дополнительно применяется легирование Mo, Co, Ti, Al и др. общей особенностью сплавов этого класса является то, сто они практически бузуглеродистые (С £ 0,03 %) и их матрица после закалки представляет собой a - твердый раствор, пересыщенный элементами замещения. При распаде a - твердого раствора при старении сплавов происходит выделение упрочняющих интерметаллидных фаз.
Структура мартенситно – стареющих сталей после закалки – массивный или реечный мартенсит, имеющий высокую плотность дефектов кристаллической решетки.
Классификация и принципы легирования
Мартенситно – стареющие стали делят на стали:
- общего назначения;
- стали специального назначения (нержавеющие стали).
Стали общего и специального назначения также имеют свои подгруппы классификации.
1. Стали общего назначения:
- умеренной прочности, экономнолегированные: sв = 1000 – 2000 МПа; 0,04 – 0,10 % С, 4 – 12 % Ni, 1 – 3 % Mo, £ 1,5 % Al + Ti, 2 – 5% Cu.
- высокопрочные:
sв = 2000 – 2500 МПа, 16 – 18% Ni, 8 – 10 % Co, 4 – 5 % Mo, 1 – 1,5 % Ti;
|
|
sв = 2500 – 3500 МПа, 18% Ni, 13 – 15 % Co, 4 – 6 % Mo, 1 – 1,5 % Ti.
- сверхвысокопрочные: sв ³ 3500, 10 – 13 % Ni, 15 – 18 % Co, 10 – 14 % Mo,
0,8 – 1,5 % Ti.
2. Коррозионностойкие.
- умеренной прочности экономнолегированные:
c высокой коррозионной стойкостью: 14 – 16 % Cr, 4 – 6 % Ni, 1,5 – 3,0 % Cu, £ 0,5 % Al + Ti.
c повышенной прочностью для слабоагрессивных сред: 11 – 13 % Cr, 7 – 9 % Ni, 1,5 – 3 % Mo, 1 - 2 % Al + Ti.
- высокопрочные: 11 – 14 % Cr, 5 – 9 % Ni, 5 – 8 % Co, 2 – 5 % Mo, £ 1,5 % Al + Ti.
- теплостойкие: 10 – 14 % Cr, 10 – 15 % Co, 5 – 7 % Mo.
Мартенситно – стареющие стали, являются высокопрочными и характеризуются высоким значением вязкости разрушения при одновременно высоком значении предела текучести. Вязкость разрушения мартенситно – стареющих сталей при одинаковом пределе текучести значительно превышает значения этого параметра для высокопрочных дисперсионнотвердеющих сталей.
Составы мартенситно – стареющих сталей регламентируются соответствующими техническими условиями ТУ.
В таблице 1 приведены химические составы и свойства некоторых мартенситно – стареющих сталей.
Таблица 1
Марка стали | Содержание основных элементов, % | t старения | sв | s0,2 | y | d | HRC | KCU МДж/м2 | ||||||
С | Ni | Co | Mo | Ti | Al | Cr | МПа
| % | ||||||
Н18К9М5Т (ЭП637) | £0,03 | 17,7-19,0 | 8,5-9,5 | 4,6-5,5 | 0,5-0,8 | 0,15 | - | 500 | 2200 | 1950 | - | 8 | 55 | 0,35 |
Н18К12М5Т2 (ЭП809) | £0,03 | 17,0-18,0 | 11,8-13,2 | 3,3-4,2 | 3,3-4,2 | 1,5-1,9 | 0,20 | 500 | 2450 | 2350 | 35 | 7 | 60 | - |
Н17К12М5Т (ЭП845) | £0,01 | 17,0-18,0 | 11,5-12,5 | 4,5-5,0 | 1,3-1,9 | - | - | 500 | 2050 | 2000 | 45 | 8 | 54 | 0,30 |
Х11Н10М2Т (ЭП678) | £0,03 | 10,5-11,5 | - | 2,0-3,0 | 0,8-1,2 | 0,15-0,35 | 9,5-10,5 | 500 | 1550 | 1480 | 50 | 8 | 46 | 0,50 |
Основными легирующими элементами в мартенситно – стареющих сталях являются: никель, кобальт, кобальт молибден.
При легировании железоникелевого мартенсита существенно изменяются температуры прямого – Мн (g a) и обратного – Ан (a g) превращения.
Мартенситно - стареющие стали общего назначения содержат 8 – 20 % Ni. При добавлении к железу 4 – 8 % Ni происходит снижение температуры g a - превращения, и после закалки образуется мартенсит замещения. Введение 8 – 12 % Ni с одновременным легированием титаном, алюминием, молибденом и др. элементами приводит к развитию старения благодаря уменьшению растворимости легирующих элементов в мартенсите; с повышением содержания никеля до 12 – 20 % увеличивается сопротивление хрупкому разрушению.
|
|
Легирующие элементы по эффекту упрочняющего влияния располагаются в следующем порядке: титан, бериллий, алюминий, вольфрам, молибден, медь. При этом изменение прочностных свойств при увеличении содержания легирующего элемента, как правило, не монотонно. При комплексном легировании аддитивного упрочнения не наблюдается: общая величина прироста прочности после старения, как правило, меньше, чем при раздельном легировании.
Положительно влияет комплексное легирование при совместных добавках молибдена и кобальта – в этом случае интенсивность упрочнения при старении существенно возрастает. Такое влияние кобальта связывают с уменьшением растворимости молибдена в a - железе, а также с протеканием процесса упорядочения в системе Fe – Co с образованием областей ближнего порядка. Кроме того, кобальт увеличивает теплостойкость матрицы.
Также существует отдельная группа экономнолегированных сталей, не содержащих кобальт и имеющих в составе пониженное количество никеля и молибдена при повышенном содержании углерода.
Титан и алюминий относятся к наиболее эффективным упрочнителям мартенситно – стареющих сталей. Растворимость их в a - фазе мала, и в присутствии никеля при нагреве происходит выделение дисперсных фаз Ni3Ti, NiAl и т.п. однако титан и алюминий резко понижают пластичность, вязкость и сопротивление хрупкому разрушению, поэтому суммарное количество титана и алюминия обычно не превышает 1 %. Понижение пластичности мартенситно – стареющих сталей при увеличении содержания титана связано с образованием при охлаждении в интервале температур 1000 – 800 оС карбонитрида Ti(C, N) по границам аустенитных зерен.
|
|
В отличие от титана и алюминия молибден не оказывает столь сильного охрупчивающего воздействия и поэтому он присутствует в составе практически всех мартенситно – стареющих сталей. При содержании свыше 3 % Mo старение приводит к образованию частиц фаз Ni3Mo, (Fe, Ni)2Mo, (Fe, Co)2Mо за счет которых обеспечивается благоприятный комплекс механических свойств.
В экономнолегированных мартенитно – стареющих сталях с повышением содержания углерода до 0,1 % в качестве упрочняющей фазы могут присутствовать карбиды легирующих элементов.
К Цупакава и Н Уэхара предложили обобщенные эмпирические зависимости для определения влияния легирующих элементов на механические свойства высокопрочных мартенситно – стареющих сталей типа Н18К8М5Т:
sв = 11+42,4 % Ni + 158,5 % Mo + 37,7 % Co + 322,4 % Ti.
d = 44,12 – 0,46 % Ni – 2,42 % Mo – 0,60 % Co – 5,20 % Ti.
Подобные зависимости позволяют качественно оценить влияние легирующих элементов на формирование комплекса свойств стали.
Суммарное упрочнение мартенситно – стареющих сталей складывается из упрочнения твердого раствора путем легирования, упрочнения при пластической деформации (если таковая реализуется) и старения.
Одним из главных преимуществ мартенситно – стареющих сталей перед другими высокопрочными материалами является высокие сопротивление хрупкому разрушению и сопротивление развитию трещины.
Термическая обработка
Важным достоинством мартенситно – стареющих сталей является их высокая технологичность. По ряду технологических свойств мартенситно – стареющие стали превосходят стали других классов соответствующего уровня прочности. Для них характерны: высокая технологическая пластичность, отсутствие трещинообразования при охлаждении, возможность сведения упрочняющей обработки к операциям закалки и старения, малая изменяемость геометрических размеров в процессе окончательной термической обработки – старения, хорошая свариваемость и возможность получения равнопрочности сварного шва и основного изделия при проведении последующего старения.
Вместе с тем мартенситно – стареющие стали имеют и ряд недостатков: склонность к ликвационной неоднородности, особенно по титану, «тепловая хрупкость» (выделение по границам зерна карбонитридных или интерметаллидных фаз), сравнительно высокие значения пределов текучести в закаленном состоянии.
Устранение этих недостатков может быть достигнуто рациональным легированием, пластической и термической обработкой.
Предварительная обработка мартенситно – стареющих сталей должна уменьшить ликвацию и выделение частиц второй фазы. Это достигается гомогенизацией при 1200 – 1260 оС (для сплавов, не содержащих меди).
Операцией термической обработки, обеспечивающей реализацию IIэтапа упрочнения, является закалка. Качество закалки определяется наличием или отсутствием заметных количеств остаточного аустенита; степенью пересыщения твердого раствора легирующими элементами, отчего зависит эффективность последующего старения; дисперсностью структуры, т.е. полнотой процессов фазовой и структурной перекристаллизации; наличием или отсутствием в закаленном мартенсите охрупчивающих фаз и d - феррита.
Первое условие реализуется легированием с учетом влияния элементов на положение точки Мк. Кроме того, уменьшить количество остаточного аустенита можно дестабилизацией g - фазы путем переохлаждения стали от 1100 – 1200 оС и выдержке в интервале 650 – 800 оС с последующим быстрым охлаждением. При выдержке в области 650 – 800 оС в аустените выделяются интерметаллидные фазы, что приводит к обеднению аустенита легирующими элементами, и соответственно, к повышению точки Мк.
Для реализации второго условия используется повышение температуры и увеличение времени выдержки при закалке, что способствует равномерному распределению легирующих элементов и, за счет этого, увеличивает эффект упрочнения при старении. Для достижения максимального прироста прочности обычно рекомендуемая температура закалки на 100 – 200 оС выше температуры А3.
С понижением температуры аустенитизации повышаются прочностные свойства мартенситно – стареющей стали после старения, особенно если после закалки следует холодная пластическая деформация.
Вышеперечисленные условия выдвигаются, если после закалки следует упрочняющая обработка – старение. Если закалку проводят в качестве смягчающей обработки перед последующей пластической деформацией, то эффективным оказывается применение закалки из двухфазной a + g - области с целью получения в структуре стабилизированного аустенита, повышающего пластичность и ударную вязкость.
Большое внимание уделяется методам борьбы с «тепловым» охрупчиванием, причина которого заключается в появлении по границам аустенитного зерна при выдержке в аустенитной области или замедленном охлаждении выделений карбонитридов Ti(C,N), Mo(C,N), интерметаллидов Fe2Mo, сульфидов типа TiS2, нитридов, c - фазы или других фаз в зависимости от состава стали и температурно – временных параметров обработки. Основные пути устранения зернограничного теплового охрупчивания: применение многократных закалок, с нагревом до высоких температур, ускоренного охлаждения.
Области применения мартенситно – стареющих сталей
Мартеситно – стареющие стали обладают высокой хладостойкостью, что позволяет применять мартенситно – стареющие стали для изготовления криогенных систем, деталей авиационной техники, гидрокрыльев и т.д. Хорошее сопротивление хрупкому разрушению и весьма высокая прочность сварных конструкций в сочетании с коррозионной стойкостью позволяет использовать мартенситно - стареющие стали, особенно коррозионностойкие для производства корпусов батискафов, химических сосудов, аппаратов и т.д.
Также мартенситно – стареющие стали могут использоваться в качестве пружинного материала.
Мартенситно – стареющие стали обладают высокой размерной стабильностью при термической обработке, т.е. практически не испытывают коробления. Поэтому из них можно изготавливать особо сложные и точные детали (например, элементы пресс – форм для литья).
Совершенствование мартенситно – стареющих сталей ведется в трех направлениях:
1 Оптимизация легирования.
2 Применение перспективных систем термической и термомеханической обработки.
3 Использование мартенситно – стареющих сталей совместно с другими материалами.
Отдельную группу составляют сверхвысокопрочные мартенситно - стареющие стали, отличительной особенностью которых является легирование 15 – 20 % Co, 6 – 15 % Mo, 8 – 25 % Ni. Это позволяет получать изделия со значением временного сопротивления около 3500 МПа.
Холодная пластическая деформация таких сталей в сочетании с последующим старением увеличивает значение предела прочности до 4000 МПа. Следует отметить, что такая высокая прочность сочетается с пониженными пластическими свойствами y = 3 - 20 %.
Повысить пластичность и вязкость мартенситно – стареющих сталей разных систем легирования возможно:
1 Путем качественной выплавки: использование двойных вакуумно – дуговых и вакуумно – индукционных переплавов и т.п.
2 Микролегированием редкоземельными металлами и кальцием, поскольку при этом снижается эффект зернограничного охрупчивания.
Совершенствование термической обработки ведется в направлении использования ступенчатой и многократной закалок, а также двойного старения (например, по режиму 560 оС, 1 час + 400 оС, 2 часа), цель которого добиться наиболее полного проявления упрочняющего эффекта.
Также может быть проведена термомеханическая обработка, сочетающая в себе деформацию стали в аустенитной области при температуре несколько выше точки Мн с целью получения мартенсита деформации и последующего старения.
Также мартенситно – стареющие стали нашли широкое применение в области композиционных материалов. В частности распространен композит алюминиевый сплав (матрица) – мартенситно – стареющая сталь (арматура).
Помимо этого мартенситно – стареющие стали используются в порошковой металлургии.
Дата добавления: 2018-06-27; просмотров: 1686; Мы поможем в написании вашей работы! |
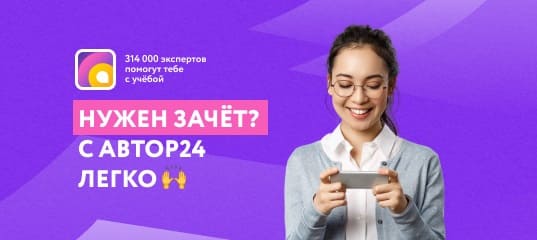
Мы поможем в написании ваших работ!