СИНТЕЗ КИСЛОРОДСОДЕРЖАЩИХ ОРГАНИЧЕСКИХ СОЕДИНЕНИЙ
При подборе соответствующих условий реакции и катализатора из СО и Н2 получают индивидуальные спирты—метиловый, первичный бутиловый и др.
Синтез метилового спирта проводят под давлением 200 - 300 ат и выше в присутствии катализаторов - окислов хрома, окиси цинка и др. В последние годы промышленное применение получили медь-цинк-хромовые катализаторы, нанесенные на оксид алюминия, которые восстанавливают при температуре 140—180 °С. Эти катализаторы обладают высокой активностью при температуре 260—280 °С и давлении 4—5 МПа.
В нашей стране в качестве катализатора синтеза метанола используют контакт СНМ-1 (состав до восстановления: 62—54% СuО, 26—28%ZnO, 5,6% Аl2О3), в присутствии которого процесс проводят при температуре 220—280 °С и давлении 4—6 МПа.
В развитии технологии процесса намечается тенденция замены ныне существующих малопроизводительных установок мощностью 35—50 тыс. т/год на одноагрегатные установки мощностью 750—1000 тыс. т/год метанола.
По технологической схеме и аппаратурному оформлению этот процесс напоминает синтез аммиака. Повышенное давление способствует смещению равновесия реакции в сторону образования метилового спирта, а при повышении температуры равновесие сдвигается влево.
СО + 2Н2 <==> СН3ОН
При низких температурах реакция проходит полнее, однако в промышленности процесс проводят при температуре 300—400 0С, так как при этой температуре возрастает активность катализатора (ускоряется процесс), что позволяет работать с большей объемной скоростью. Выход побочных продуктов незначителен. При однократном прохождении синтез-газа через слой катализатора в контактных газах содержится только 3—4% СН3ОН. После отделения сконденсировавшегося метилового спирта непрореагировавшие газы (циркуляционный газ) смешивают со свежим синтез-газом и вновь направляют в контактный аппарат.
|
|
Схема синтеза метилового спирта из СО и Н2
1—компрессор; 2- смеситель; 2—теплообменники; 4—колонна синтеза; 5—холодильники-конденсаторы; 6—сборник-сепаратор; 7—циркуляционный компрессор; 8—пусковой электроподогреватель.
Исходный синтез-газ, предварительно очищенный от пыли и примесей, отравляющих катализатор, нагнетают компрессором 1 под давлением 250 ат в смеситель 2. Отсюда смесь циркуляционного и синтез-газа направляют в теплообменники 3 и дале в реактор синтеза 4. Контактные газы выходят из колонны, охлаждаются в теплообменниках 3 и в холодильнике 5. Пары метилового спирта конденсируются и отделяются в сборнике-сепараторе от непрореагировавших газов. Циркуляционные газы компрессором 7 нагнетаются в смеситель 2. При накоплении в циркуляционном газе примесей его выводят из системы, которую затем заполняют свежей газовой смесью.
|
|
В связи с экзотермичностью реакции синтеза метанола (+110,8 кДж/моль) реакционный узел выполняют по-разному, что зависит от способа отвода тепла и проведения реакции.
1. В начале промышленного использования значительное рапространение получили трубчатые реакторы, в трубках которых находился катализатор, а движущаяся реакционная масса, охлаждалась кипящим в межтрубном пространстве водным конденсатом. Однако у таких аппаратов высока металлоемкость и стоимость аппарата, т.к. его надо выполнять из качественной стали и футеровать изнутри медью (для предотвращения взаимодействие окиси углерода с железом и образование пентакарбонила железа Fе(СО)5, являющегося вредной примесью).
2. В дальнейшем наибольшее распространение получили адиабатические реактора с несколькими (обычно с четырьмя) слоями катализатора. В этих аппаратах теплообменные устройства отсутствуют, а для съёма тепла и регулирования температуры подают холодный синтез-газ между слоями катализатора через специальные ромбические распределители, обеспечивающие эффективное смешение горячего и холодного газа. Такие технологические схемы внедрены фирмой ICI Великобритания.
|
|
В развитии технологии процесса намечается тенденция замены ныне существующих малопроизводительных установок мощностью 35—50 тыс. т/год на одноагрегатные установки мощностью 750—1000 тыс. т/год метанола. В технологической схеме процесса любой мощности обязательной стадией является очистка выходящего из газогенератора синтез-газа от соединений серы и других примесей, являющихся каталитическии ядами стадии синтеза.
В процессе можно использовать синтез-газ, полученный неполным окислением в присутствии пара угля или тяжелых нефтяных остатков, содержащий в основном Н2 и СО и небольшое количество СО2. После очистки от соединений серы состав газа регулируют таким образом, чтобы получить оптимальное соотношение Н2:(СО+СО2), и вводят в реактор синтеза без дополнительного компримирования.
Метанол синтезируют над медьсодержащим катализатором при 200—300 °С и давлении 5,0—10,0 .МПа. Срок службы катализатора 3—4 года. В реакторе катализатор расположен несколькими слоями на распределительных решетках. Охлаждение реакционной смеси производится холодным синтез-газом в нескольких точках по высоте реактора. Выходящие из реактора газы проходят серию теплообменников и поступают в сепаратор. Конденсат метанола-сырца подвергают быстрому испарению и направляют на ректификацию. Процесс характеризуется высокой эффективностью утилизации тепла газов конверсии и синтеза метанола.
|
|
3. В последнее время появился способ синтеза в техфазной системе. Процесс осуществляют в жидкой фазе инертного углеводорода с суспендированным в жидкости гетерогенным катализатором и барботированием синтез-газа через эту суспензию. Тепло реакции отводится за счёт циркуляции жидкости через парогенератор или при помощи внутренних теплообменников с кипящим водным конденсатом. Преимуществом этих систем (используемых фирмами “Лурги”, “Кемикл систем” и др.) является существенное уменьшение рецикла газа и повышение концентрации метанола в реакционных газах.
Синтез метанола проводят при температуре 250—260°С, при этом на 1 кг метанола получают 1,4 кг пара высокого давления. Выходящую из реактора газовую смесь охлаждают и конденсируют. Метанол-сырец отделяют в сепараторе, а не прореагировавший синтез-газ компримируют и возвращают в реактор. Часть газа используют для очистки исходного газа от соединений серы или в качестве топливного газа.
ПРИМЕНЕНИЕ МЕТИЛОВОГО СПИРТА
Важнейшей областью применения метанола является производство формальдегида путем неполного окисления СН3ОН - для дальнейшего производства изопрена из изобутилена и формальдегида через ДМД.
Кроме того, метанол традиционно используется как растворитель, полупродукт в синтезе диметилсульфата, диметиланилина и т. д. Выпуск его достигает сотен млн.т.
В последнее время в связи с энергетическим кризисом метанол (нашел применение) стал использоваться при создании новых технологических процессов по переработке метанола в высокооктановый бензин, этанол, уксусную кислоту и другие продукты вызывает повышенный спрос на него.
Другое направление использования метанола — применение его в качестве топлива. Решение проблемы топлива для двигателей внутреннего сгорания с помощью метанола рассматривается с нескольких точек зрения:
1) метанол—заменитель бензина; 2) метанол—добавка к бензинам; 3) метанол—сырье для производства высокоэффективных антидетонаторов — трет-бутилметилового и трет-пентилметилового эфиров.
Метанол — заменитель бензина. Метанол по ряду важных характеристик превосходит лучшие сорта углеводородных топлив, но обладает и недостатками: высокой гидрофильностью, токсичностью, агрессивностью по отношению к некоторым металлам и пластикам. Поэтому использование в качестве топлива для двигателей внутреннего сгорания чистого метанола потребует существенной реконструкции двигателя. Тем не менее в ряде стран проводят испытания автомобилей, работающих на чистом метаноле (топливо М-100). Исследования, проведенные в ФРГ и США, показали, что к. п. д. имеющихся метанольных двигателей на 20% выше к. п. д. традиционных.
Метанол — добавка к бензину. При добавлении метанола к бензину в небольших количествах (2—7%) реконструкции двигателя не потребуется, так как в этом случае даже пластмассовые детали, не стойкие по отношению к метанолу (бензопровод, прокладки и т. д.), не претерпевают каких-либо изменений. При увеличении же количества метанола до 15% (топливо М-15) эта смесь уже начинает воздействовать и на различные сплавы.
Добавление метанола приводит к уменьшению вредных выбросов в атмосферу, а октановое число смеси с увеличением содержания метанола повышается, что в конечном счете приводит к увеличению к.п.д. двигателя.
Кроме прямого использования метанола в качестве моторного топлива или его компонента все больший интерес метанол приобретает как исходное сырье для производства трет-бутилметилового и трет-пентилметилового эфиров—высокоэффективных антидетонаторов. Добавка 5—15% эфиров даст возможность практически отказаться от подмешивания к бензинам ТЭС (тетраэтилсвинца), ароматических углеводородов или алкилата.
Бензин из метанола. Открытие специальных высококремнеземных цеолитов дало возможность разработать метод превращения метанола в углеводороды. Преимущества этого процесса заключаются в высокой степени селективности и высоком октановом числе полученного бензина. Применяемые типы катализаторов ограничивают число атомов углерода в получаемых углеводородах до 11. В качестве сырья можно использовать обводненный метанол без его предварительной очистки.
Превращение метанола в бензин протекает с выделением большого количества тепла. Процесс осуществляется в две ступени. Сначала метанол дегидратирустся в смесь диметилового эфира и воды (при этом выделяется 20% суммарного тепла реакции), а затем полученная смесь вместе с не прореагировавшим метанолом на следующей ступени превращается в бензин. Степень превращения метанола составляет 44%. Образование СО, СО2 и кокса происходит в незначительной степени. Получающийся бензин является не только высокооктановым (ОЧ=93), но и высококачественным и содержит (в %): высокоразветвленных парафинов—51; разветвленных олефинов—13; нафтенов—8, ароматических углеводородов — 28%.
Процесс проводят при 380—440 °С и 2,1 МПа. Наряду с переработкой метанола в бензин в последние годы обсуждается возможность использования метанола в качестве топлива для крупных энергетических установок. Одним из факторов, определяющих перспективность использования метанола в качестве котельного топлива, является значительное уменьшение загрязнения атмосферы по сравнению с другими видами топлива.
Следует иметь в виду, что метиловый спирт—сильный, преимущественно нервный и сосудистый яд с резко выраженным кумулятивным действием. При попадании внутрь СН3ОН вызывает тяжелое поражение зрения и смерть. (Однако эта опасность сильно преувеличена)
Другие спирты также можно получать на основе СО и Н2. Так, при реакции г о м о л о г и з а ц и и метанола образуется этанол:
СН3ОН + СО + 2Н2 —> С2Н5ОН+Н2О.
Синтез протекает на соединениях кобальта с иодсодержащим промотором и триалкилфосфином при 200—210 °С и давлении 15—40 МПа с селективностью 85—95 %.
Разрабатывается синтез этиленгликоля непосредственно из СО и Н2; из спиртов, СО и О2 через эфиры щавелевой кислоты, а также из формальдегида, СО и Н2:
+Н2
Н2СО+СО+Н2 —> НОСН2—СНО ———> НОСН2—СН2ОН
Лучшие результаты достигнуты при последнем способе, если катализатором служат комплексы родия с фосфиновым лигандом или сильные минеральные кислоты с гидрирующим катализатором.
Пока эти методы не реализованы из-за недостаточной активности и селективности катализаторов, но они совершенствуются.
Больше известны методы получения из окиси углерода и водорода при их соотношении (СО : Н2— 1 : 2) - смеси кислородсодержащих органических соединений при 400—450 °С и 100— 150 ат. Процесс проводят в присутствии катализатора—железных стружек, обработанных поташом. Эта смесь, так называемый синтол, содержит 25% альдегидов. 29% спиртов, 10% органических кислот, 5% кетонов и 4% сложных эфиров. Содержание углеводородов в синтоле составляет только 2—2,5%. Продукт интересен для выделения индивидуальных соединений и для др. синтезов.
ПОЛУЧЕНИЕ АЦЕТИЛЕНА
Ацетилен (СН≡СН) используют для получения винилхлорида, винилацетата (сырье для получения пластмасс), нитрила акриловой кислоты (сырье для получения волокон), хлоропренового каучука, 30 % ацетилена расходуется на автогенную сварку.
Известно несколько способов получения ацетилена:
1) из карбида кальция,
2) из углеводородного сырья:
а) метод электрокрекинга метана,
б) термокрекинг метана в регенеративных печах,
в) окислительный пиролиз метана.
Дата добавления: 2018-06-27; просмотров: 456; Мы поможем в написании вашей работы! |
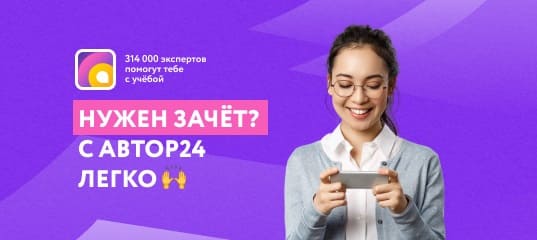
Мы поможем в написании ваших работ!