Сборка прессовых соединений(шлицевых)
Сборка прессовых соединений или соединений с гарантированным натягом осуществляется на прессах (продольно прессовые соединения) путем теплового воздействия или гидропрессовым способом (поперечно-прессовые соединения).
Процесс сборки продольно-прессовых соединений состоит в том, что к одной из сопрягающихся деталей прикладывается осевая сила. Усилие запрессовки растет от 0 до мах. В связи с наличием натяга в процессе сборки происходит деформирование металла, в результате чего на поверхности контакта возникают значительные нормальные давления и силы трения, препятствующие относительному сдвигу этих деталей. Натяг является основным показателем, определяющим способность передавать нагрузки. Необходимую величину натяга определяет шероховатость поверхности, которую необходимо учитывать при определении его величины. Шероховатость собираемых поверхностей должна быть Rа = 1,25...0,63 мкн.
Использование смазки (машинное масло) способствует повышению прочности соединения. Трудоемкость сборки таких соединений составляет 10-12 % от трудоемкости общей сборки.
Усилие распрессовки должно превышать усилие запрессовки на 10-15%.
Усилие запрессовки при сборке продольно-прессового соединения с гарантированным натягом находится по формуле:
Р=fзап*p*D*L
где ƒ– коэффициент трения
ρ– удельное давление на поверхности контакта Н/м2
d –Ø охватываемой детали
|
|
L – длина запрессовки
Удельное давление на поверхности контакта определяется по формуле:
где
– расчетный натяг
Е1 и Е2 – модули упругости охватываемой и охватывающей деталей
С1 и С2 – коэффициенты
μ и μ1 – коэффициенты Пуассона
d0 – внутренний диаметр охватываемой детали
Д – наружный диаметр охватывающей детали
d– наружный Ø охват детали.
Значения С1 и С2 определяют по таблице 30 стр. 225 [II] (Новиков), через отношения
и
: при этом если охватываемая деталь выполнена в виде сплошного вала, то
Расчетный натяг определяют по формуле:
d=Dd-1.2*(RZ1+RZ2)
где ∆d – номинальный натяг (разность диаметров)
Rz1 и Rz2 – шероховатости сопрягаемых деталей.
Распространенной погрешностью запрессовки является перекос детали и ее деформация, поэтому вначале запрессовки проводят медленно, чтобы не вызвать перекоса. Входящая кромка должна иметь галтель или фаску. Для устранения задиров деталь смазывают машинным маслом или сульфидом молибдена .
Требуемое усилие пресса принимают с коэффициентом запаса 1,5...2,0.
Для уменьшения усилий запрессовку производят с количеством колебаний (100 кол. в секунду).
Сборка с тепловым воздействием повышает прочность соединения в 1,5...2,5 раза по сравнению со сборкой на прессе. Это объясняется тем, что неровности сопрягаемых деталей не сглаживаются, а как бы сцепляются друг с другом. В результате создаются натяги, равнопрочные по передаче крутящего момента шлицевым, но выгодно отличающиеся простотой изготовления и высокой надежностью и долговечностью.
|
|
Температура нагрева при запрессовке – 75...400 С в зависимости от необходимого натяга.
Одним из существенных преимуществ теплового метода является перевод сборки с натягом в область сборки с зазором. Это открывает перспективы для механизации и автоматизации процесса, позволяет перейти к полной взаимозаменяемости.
Дата добавления: 2018-06-01; просмотров: 575; Мы поможем в написании вашей работы! |
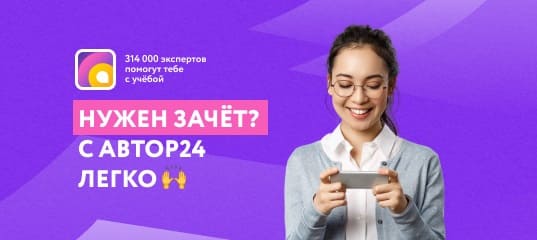
Мы поможем в написании ваших работ!