Марки и химический состав отечественных быстрорежущих сталей (ГОСТ 19265-73) и аналоги других стран, соответствующие этим маркам
Износ и стойкость режущих инструментов
Современные инструментальные материалы.
Требования, предъявляемые к инструментальным материалам.
Области применения инструментальных материалов
(для самостоятельного изучения)
Способность режущего инструмента обеспечивать требуемую производительность обработки во многом определяется свойствами инструментального материала, которым оснащена его режущая часть. Инструментальные материалы условно группируются в соответствии с их составом и свойствами. Условная схема их классификации представлена на рис. 41.
Требования, предъявляемые к инструментальным
Материалам
Инструментальные материалы должны удовлетворять следующим требованиям:
1) обладать высокими механическими характеристиками (твердостью, прочностью, ударной вязкостью);
2) быть химически инертными к обрабатываемому материалу. То есть режущий инструмент нужно подбирать таким образом, чтобы исключить совпадение химических элементов, входящих в состав инструмента и заготовки. В том случае, если в инструменте и в заготовке количество одних и тех же элементов превышает 3...5%, то возможно «химическое сродство», приводящее к интенсивному износу режущего инструмента;
Рис. 41. Условная схема классификации инструментальных материалов
3) обладать высокой теплостойкостью, теплопроводностью и быть малочувствительными к циклическим колебаниям температуры. Теплостойкость - это свойство инструментального материала сохранять твердость, а, следовательно, и режущие свойства при высоких температурах;
|
|
4) иметь высокую износостойкость - способность инструментального материала сопротивляться изнашиванию при трении с обрабатываемым материалом;
5) обладать хорошей обрабатываемостью, так как многие режущие инструменты имеют сложную фасонную форму, т.е. быть достаточно технологичными;
6) быть относительно дешевыми.
В настоящее время не существует универсального инструментального материала, который в полной мере удовлетворял бы перечисленным требованиям.
Физико-механические характеристики
Основных групп инструментальных материалов
Инструментальные стали
Углеродистые и легированные инструментальные стали
Химическим элементом, определяющим физико-механические свойства этих групп материалов, является углерод. Он образует карбиды железа, которые участвуют в процессе термообработки, активно участвуют в фазовых превращениях и образовании твердой мартенситной структуры.
Для изготовления режущих инструментов используют углеродистые стали марок от У7А до У13А. Цифрами в обозначении данных сталей указано содержание углерода в десятых долях процента.
|
|
Углеродистые стали при термообработке не дают равномерной по объему твердости, она уменьшается от поверхности к сердцевине инструмента. Так на поверхности твердость может быть равна 61...64 , а в сердцевине уменьшиться до 41
.
В процессе термообработки заготовки из этих сталей склонны к поводке и трещинообразованию. Изготовленные режущие инструменты имеют низкую теплостойкость (200…250 ). Поэтому из углеродистых сталей изготавливают малогабаритные инструменты, обрабатывающие материалы с низкими механическими свойствами на малых скоростях резания. Используют такой инструмент в условиях единичного и мелкосерийного производства, а также для изготовления слесарного, кузнечного и деревообрабатывающего инструмента.
Легированные инструментальные стали отличаются от углеродистых наличием в них повышенного содержания кремния и марганца, а также одного или нескольких легирующих элементов: хрома, вольфрама, ванадия и др., которые повышают твердость, прочность и износостойкость инструмента.
Для режущих инструментов используются стали марок 9ХС, 9ХФ, ХВГ, ХВСГ, Х6ВФ, 9Х5ВФ и др. Теплостойкость сталей этой группы на 100…200 превышает теплостойкость инструментальных углеродистых сталей и составляет 350…400
. Легированные стали более технологичны: лучше прокаливаются и закаливаются, меньше склонны к короблению. Эти стали за некоторым исключением применяются для изготовления того же инструмента, что и углеродистые стали. В частности, из этих материалов изготавливают метчики, круглые плашки, резьбонакатной инструмент, матрицы и пуансоны вырубных и просечных штампов т.д.
|
|
Быстрорежущие стали
Быстрорежущие стали от ранее рассмотренных материалов отличаются высоким содержанием легирующих элементов – вольфрама, хрома, молибдена, ванадия, кобальта.
Вольфрам и молибден повышают износостойкость и теплостойкость сталей до 600…635 . Стойкость инструментов из быстрорежущих сталей в 4…8 раз выше, чем из углеродистых сталей, а при равной стойкости инструменты из быстрорежущих сталей обеспечивают повышение скорости резание в 2…3 раза по сравнению с инструментами из углеродистых сталей.
Быстрорежущие стали условно можно разделить на две группы: общего назначения (нормальной производительности) и повышенной производительности.
|
|
К быстрорежущим сталям нормальной производительности относятся вольфрамовые стали марок Р9, Р12, Р18 и вольфрамомолибденовые стали марок Р6МЗ, Р6М5, Р9М4, Р12МЗ. Содержание легирующих элементов в них определяется в процентах числом, стоящим после буквенного обозначения.
Рассмотренные стали содержат от 6 до 18% вольфрама (число после буквы Р). Их твердость после термообработки составляет 63…66 , теплостойкость не превышает 620
, предел прочности на изгиб
3000...4000 МПа.
Из этих сталей изготавливают все типы металлорежущих инструментов, в том числе сложного профиля. Введение в состав сталей 3…5% молибдена позволило повысить ударную вязкость и пластичность.
К быстрорежущим сталям повышенной производительности относятся стали, имеющие в своем составе увеличенное содержание по сравнению с обычными быстрорежущими сталями углерода (это стали 10Р8М5 и 10Р8МЗ), ванадия (Р12ФЗ, Р14Ф4, Р18Ф2) и кобальта (Р9К5, Р9К10, Р9Ф2К10, Р18Ф2К5).
Повышенное содержание углерода (на 0,1...0,2%) увеличивает вторичную твердость сталей до 67…67,5 и теплостойкость до 635
, улучшает износостойкость за счет увеличения количества карбидов. Стойкость инструмента при этом увеличивается до 75% при той же скорости резания.
Наличие в быстрорежущих сталях ванадия в количестве от 1 до 1,4% также обеспечивает повышение их твердости до 67...68 при теплостойкости порядка 635°С. Вместе с тем следует отметить, что главным недостатком быстрорежущих сталей, содержащих ванадий, является их плохая обрабатываемость шлифованием.
Введение в состав быстрорежущих сталей кобальта повышает их теплопроводность и теплостойкость (~650°С) и одновременно твердость до 66...70 .
Некоторые марки быстрорежущих сталей приведены в табл. 1. В маркировке этих сталей цифра перед буквой Р обозначает содержание углерода в десятых долях процента, цифры за буквами Р, М, Ф, К и А обозначают, соответственно, процентное содержание вольфрама, молибдена, ванадия, кобальта и азота.
Таблица 1
Марки и химический состав отечественных быстрорежущих сталей (ГОСТ 19265-73) и аналоги других стран, соответствующие этим маркам
Марка стали | Аналоги стандартов других стран | |||||
BS Англия | DIN Германия | DN-86/ H-85022 Польша | AISI США | NFA Франция | JIS Япония | |
Р18 | ВТ2 | 1,3355 S18-0-1 1,3558 X7SWCrV1841 | SW18 | Т1 | 18-0-1 | KH-2 |
Р6М5 | ВМ1 | – | SW7M | М2С.1 | 6-5-2 | KH-9 |
11Р3АМ3Ф2 | – | – | – | – | – | – |
Р6М5Ф3 | – | S6-5-3 | – | M3 | – | KH-52 |
Р12Ф3 | – | – | SW12 | – | ||
Р18К5Ф2 | ВТ4 | 1,3558 S18-1-2-5 | – | Т4 | – | – |
Р9К5 | – | – | SK5 | – | ||
Р6М5К5 | – | S6-5-2-5 | SK5M | – | 6-5-2-5 | KH-55 |
Р9М4К8 | 0 | 0 | SK10V | 0 | – | – |
Р2АМ9К5 | – | – | SK8M | – | – | – |
Улучшение технологических свойств быстрорежущих сталей достигается путем изготовления их методами порошковой металлургии.
Порошковые быстрорежущие стали, имеют равномерную однородную мелкозернистую структуру и обозначаются буквами МП. Современная промышленность выпускает порошковые быстрорежущие стали следующих марок: Р12МЗФ2К8-МП, С12МФ5-МП, С9М4К8-МП, Р6М5К5-МП, Р0М2ФЗ-МП. Их твердость и ударная вязкость выше твердости и ударной вязкости традиционных быстрорежущих сталей, соответственно, на две единицы и 2…6 раз. Кроме того, порошковые быстрорежущие стали достаточно хорошо обрабатываются резанием, а при их упрочнении имеют место незначительные искривления формы инструмента. Период стойкости режущих инструментов из таких сталей возрастает до 1,5 раз.
Порошковые быстрорежущие стали рекомендуется применять для изготовления инструментов, обрабатывающих титановые сплавы, высоколегированные стали и другие труднообрабатываемые материалы в тяжелых условиях резания, а именно: при прерывистой обработке, ударных нагрузках, повышенных скоростях резания.
К сравнительно новым инструментальным материалам относятся дисперсионно-твердеющие быстрорежущие стали.
Дисперсионно-твердеющие быстрорежущие стали (с интерметаллидным упрочнением) имеют пониженное содержание углерода (0,1...0,3%), повышенную твердость после отпуска (70 ) и теплостойкость до 725
. Основными легирующими элементами в этих сталях являются кобальт (16-25%), вольфрам (11-20%) и молибден (4-7%).
К «безуглеродистым» дисперсионно-твердеющим сталям (С < 0,06%) относятся стали марок В3М12К23, В14М7К25, В18М7К25, В18М4К25, В7К25, а к «углеродистым» (С = 0,1…0,3%) – 25В20К25ХФ и 30В20К16.
Инструменты из дисперсионно-твердеющих быстрорежущих сталей применяются для точения, сверления, фрезерования и строгания труднообрабатываемых материалов и титановых сплавов, обеспечивая повышение стойкости в 30-80 раз по сравнению со сталью Р18, а при резании жаропрочных сплавов и нержавеющих сталей с аустенитной структурой – в 10…20 раз по сравнению с Р12Ф4К5.
Твердые сплавы
Главными компонентами твердых сплавов являются карбиды вольфрама (WC), титана (TiC), тантала (ТаС) и ниобия (NbC), частицы которых соединены связкой из сравнительно мягкого и тугоплавкого кобальта ( 1493
).
Твердые сплавы получают методом порошковой металлургии в виде пластин различной формы. Одним из основных свойств металлокерамических твердых сплавов является высокая теплостойкость (до 900-1000 ), что позволяет осуществлять обработку материалов в зависимости от их марки при скоростях до 600 м/мин.
Применяемые для механической обработки твердые сплавы подразделяются на следующие группы.
Вольфрамовые (одно карбидные) твердые сплавы (ВК), состоящие из зерен карбида, связанных кобальтом. Материалы этой группы содержат от 3 до 22% кобальта. В зависимости от состава и зернистости, предел прочности при изгибе у твердых сплавов данной группы ВК изменяется в диапазоне от 1170 до 2100 МПа, а твердость от 82 до 91 HRA. Марки сплавов вольфрамовой группы обозначаются буквами ВК, после которых цифрами указывается процентное содержание в сплаве кобальта. Например, сплав ВК8 содержит 8% кобальта (Co), остальное (92%) - карбид вольфрама (WC).
В настоящее время в России выпускаются следующие марки твердых сплавов вольфрамовой группы: ВКЗ, ВКЗ-М, ВК4-В, ВК6, ВК6-М, ВК6-0М, ВК6-В, ВК8, ВК8-В, ВК8-ВК, ВК10, ВК10-Х0М, В10-КС, ВК11-B, BK11-BK, BK15, BK20, BK20-KC (ГОСТ 3882-74).
Буквы, стоящие в конце маркировки, указывают на размер карбидных зерен (мкм): М - (1,0-1.5) мелкозернистый, ОМ - (0,1-1,0) особомелкозернистый, крупнозернистый В - (3-5), у обычных сплавов (без букв в маркировке) размер карбидов составляет около 2 мкм. Мелкозернистые сплавы по сравнению с обычными твердыми сплавами имеют плотную структуру, более износостойкие, но менее прочные. Крупнозернистые сплавы являются более прочными, лучше сопротивляются ударным нагрузкам, но менее износостойкие.
Вольфрамовые твердые сплавы рекомендуется использовать при обработке заготовок из конструкционных сталей в условиях низкой жесткости технологической системы, при прерывистом резании и работе с ударами, а также для обработки хрупких материалов - чугуна, стеклопластиков, а также цветных сплавов, в частности, титановых.
Титановолъфрамовые (двух карбидные) твердые сплавы (ТК) кроме карбидов вольфрама и кобальта содержат карбиды титана. По ГОСТ 3882-74 выпускаются следующие марки твердых сплавов группы ТК: Т30К4 (30% TiC + 4% Co + 66% WC), Т15К6, Т14К8, Т5К10, Т5К12.
Сплавы этой группы предназначены в основном для обработки сталей. По сравнению с однокарбидными сплавами (ВК) они обладают большей стойкостью к окислению, твердостью (87-92 HRA) и теплостойкостью, но меньшей теплопроводностью и прочностью.
Титанотанталоволъфрамовые (трехкарбидные) твердые сплавы (ТТК) содержат WC, TiC, ТаС и в качестве связки Со. Промышленностью выпускаются трехкарбидные сплавы следующих марок: ТТ7К12, ТТ8К6, ТТ10К8Б, ТТ20К9. Цифра, стоящая после букв ТТ, указывает суммарное содержание карбидов Ti и Та, а после буквы К - процентное содержание Со. Основной составляющей в этих сплавах также являются карбиды вольфрама. Например, сплав ТТ20К9 содержит: 20% (TiC + TaC) + 9% Co + 71% WC. В этих сплавах карбид тантала повышает предел усталости при циклическом нагружении, теплостойкость, прочность и твердость. Твердость и предел прочности на изгиб в сплавах группы ТК в зависимости от марки сплава колеблются, соответственно, в пределах 87-92 HRA и = 1320-1670 МПа. Поэтому их используют при черновой обработке с большими сечениями срезаемого слоя, при работе с ударами.
Безвольфрамовые твердые сплавы разработаны с целью экономии таких дефицитных материалов, как вольфрам и кобальт. Определяющим компонентов этих сплавов является карбид титана. Отечественная промышленность выпускает сплавы на никель-молибденовой связке следующих марок: ТНМ20, ТНМ25, ТНМ30, КТНМ30А, МНТ-А2, МНТ-Б2 и др.
Безвольфрамовые твердые сплавы обладают низкой окисляемостью, имеют большую теплостойкость, меньшие коэффициенты трения и теплопроводности, менее склонны к наростообразованию, чем вольфрамосодержащие твердые сплавы. Повышенная износостойкость способствует высокой размерной стойкости инструмента, меньшей шероховатости и большей точности обработки. Твердость безвольфрамовых сплавов лежит в пределах 87.5-91 HRA, а предел прочности на изгиб = 980-1710 МПа.
В ГОСТ 26530-85 внесены только две марки безвольфрамовых твердых сплавов, а именно: ТН20 и КНТ-16. Сплав ТН20 рекомендуется применять для непрерывного и чистового точения углеродистых, низколегированных конструкционных сталей цветных металлов на основе меди, низколегированных сплавов никеля, серых чугунов, а также пористого и чистового торцевого фрезерования заготовок из чугуна. Сплав КНТ-16 за небольшим исключением целесообразно использовать в тех же условиях, что и сплав ТН20.
В настоящее время для изготовления безвольфрамовых твердых сплавов инновационная технология, основанная на самораспространяющемся высокотемпературном синтезе (СВС). Указанным методом получены новые марки сплавов, названные СТИМ - синтетические твердые инструментальные материалы.
Физико-механические свойства синтетических твердых сплавов приведены в табл. 2.
Таблица 2
Дата добавления: 2018-06-01; просмотров: 498; Мы поможем в написании вашей работы! |
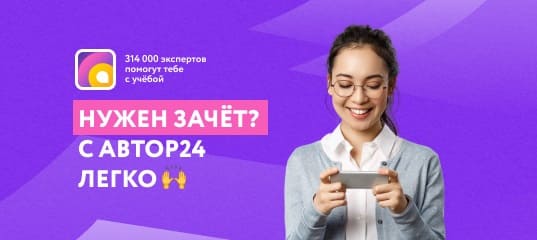
Мы поможем в написании ваших работ!