Методы контроля качества сварного шва
МИНИСТЕРСТВО ОБРАЗОВАНИЯ И НАУКИ
РОССИЙСКОЙ ФЕДЕРАЦИИ
Федеральное агентство по образованию Российской Федерации
Государственное образовательное учреждение высшего профессионального образования
«Ивановский государственный химико-технологический университет»
ИГХТУ
Курсовая работа
по дисциплине:
Технология конструкционных материалов
Студент:
Руководитель: Гоголев Ю.Г.
Иваново 2016
Содержание
Задание…………………………………………………………………………….3
Схема и сущность процесса ручной электродуговой сварки………………......4
Процесс сварки обечайки…………………………………………………….......8
Методы контроля качества сварного шва ……………………………..…........15
Список использованной литературы…………………………………………...17
Задание 1-5 Вариант №5
1.Привести схему и описать сущность процесса ручной электродуговой сварки толстопокрытыми электродами. Указать назначение покрытия.
2.Разработать процесс сварки обечайки (Рис.4). Привести, в соответствии с рекомендованным типом соединения, сечение шва с указанием его размеров, согласно ГОСТ 5264-80-С19-Р (исходные данные из таблицы 1).
3.Подобрать марку и диаметр электрода, определить режим сварки. По размерам шва подсчитать массу наплавленного металла. Определить расход электродов с учетом потерь, расход электроэнергии и время сварки изделия.
|
|
4.Указать методы контроля качества сварного шва.
Таблица 1.
Исходные данные для варианта №5 | |||||||
Dв мм | S мм | l1мм | l2мм | l3мм | Материал | Тип сварного соединения и номер шва | |
1400 | 14 | 1500 | 1500 | 1500 | 08Х21Н6М2Т | №1 ГОСТ 5264-80-С19-Р | №2 ГОСТ 5264-80-С19-Р |
Схема и сущность процесса ручной электродуговой сварки толстопокрытыми электродами
Ручной электродуговой сваркой изготовляется большая номенклатура деталей, особенно крупногабаритных (базисных), и строительных конструкций, а также устраняются у них эксплуатационные дефекты (трещины, обломы, износы).
На рисунке 1 представлена схема ручной электродуговой сварки.
Рис.1. Схема ручной электродуговой сварки
Сущность всех дуговых методов сварки заключается в использовании тепла электрической дуги – мощного стационарного самостоятельного газового разряда с низким катодным напряжением, существующего в промежутке между двумя электродами, роль которых при сварке выполняют плавящийся или неплавящийся электрод и металл свариваемого изделия. Это тепло идет на расплавление основного и присадочного металлов, сообщения их атомам энергии активации, образование физического контакта и другие процессы, имеющие место при сварке.
|
|
При ручной дуговой сварке в качестве анода и катода выступают металл свариваемого изделия и сварочный электрод – металлический стержень, покрытый слоем особого состава – обмазкой, или, согласно официальной терминологии, покрытием. Назначение покрытия – стабилизация дуги, защита и легирование расплавленного металла сварочной ванны. Различают четыре вида покрытия: основной, целлюлозный, рутиловый и кислый; для сварки магистральных трубопроводов разрешены только электроды первых двух видов. Различные виды покрытия электродов по-разному взаимодействуют с металлом в процессе сварки. Химический состав металла электрода и покрытия определяется химическим составом металла свариваемого изделия (труб) и выбранной технологией сварки.
Возбуждение электрической дуги при ручной дуговой сварке основано на использовании явления короткого замыкания. При этом происходит следующее: в месте контакта на катоде образуется катодное пятно, которое настолько сильно нагрето, что становится способным к электронной эмиссии (т.е. испусканию электронов) при приложении напряжения в 60-70В. Для возникновения сварочной дуги как газового разряда необходимо наличие заряженных частиц, направленное движение которых и будет электрическим током. Явлением, обеспечивающим появление этих частиц, является термическая, или ударная ионизация. Эмитированные катодом электроны в результате соударения с нейтральными ионами приводят к появлению ионов. В результате в газовом промежутке между двумя электродами возникают носители электричества – отрицательно заряженные электроны и положительно заряженные ионы, создаются условия для возникновения сварочной дуги, тепло которой используется при сварке.
|
|
Металл сварного шва – закристаллизовавшейся сварочной ванны – будет состоять из смеси металла труб и металла электродов. Его физико-химические характеристики будут зависеть как от качества и правильности принятия решений по выбору технологии сварки, так и от качества выполнения сварочных работ и последующей термообработки сварного шва.
Электроды подразделяются на тонкопокрытые (с тонким слоем обмазки), со средним по толщине слоем покрытия, с толстым покрытием (с толстым слоем обмазки), и с особо толстым покрытием. Толстопокрытыеэлектроды часто называют качественными электродами или электродами с качественной обмазкой. Марка электрода характеризуется составом электродного покрытия, материалом электродного стержня, технологическими свойствами электрода и механическими свойствами металла сварного шва, полученными при сварке данными электродами.
|
|
Электроды с толстым покрытием создают при сварке газовую и шлаковую защиту, стабилизируют дугу, раскисляют расплавленную ванну металла, легируют наплавленный металл, формируют сварной шов. Такие электроды подразделяют на электроды для сварки конструкционных, легированных сталей и для наплавки.
Органические соединения, а также мрамор, мел, известняк, входящие в обмазку электрода, разлагаются под действием высокой температуры вблизи торца электрода. Образующиеся при этом газы нагреваются, расширяются, оттесняя окружающий воздух.
В зависимости от электродных покрытий изменяются механические свойства металла шва. Наиболее высокие механические свойства (временное сопротивление, относительное удлинение, ударная вязкость) металла шва достигаются при применении электродов с толстыми покрытиями. Производительность сварки тем больше, чем больше коэффициент наплавки. Он колеблется в пределах 7-22 г/(А-ч). С увеличением сварочного тока и продолжительности горения дуги масса наплавленного металла увеличивается. Для определения производительности наплавки при сварке штучными электродами коэффициент наплавки данных электродов следует умножить на силу тока при сварке. Масса наплавленного металла и масса расплавленного металла электрода не одинаковы. Часть металла электрода теряется на угар, разбрызгивание и испарение. Потери при сварке обычно не менее 3 %. Если потери металла значительно превышают эту величину и достигают 15-20 %, следует тщательно разобраться в их причинах и принять меры для уменьшения потерь металла. При этом особое внимание должно быть уделено рассмотрению условий сварки.
При сварке электродами с толстыми покрытиями необходимо обеспечить полное и равномерное закрытие жидкого металла слоем расплавленного шлака. Шлак должен располагаться сзади дуги, не смешиваться с расплавленным металлом и не затекать перед дугой, т. е. не попадать на поверхность еще не расплавленного металла. Металл при этом должен поддерживаться более длительное время в жидком состоянии для того, чтобы частицы шлака всплыли на поверхность ванны, и шлак успел бы раскислить металл. Ширина поперечных колебаний конца электрода при сварке толстопокрытыми электродами должна быть меньше, чем при сварке тонкопокрытыми электродами. Сварку угловых швов в нижнем положении лучше производить в лодочку, а изделие наклонять так, чтобы шлак не затекал на металл перед дугой. Угол наклона утолстопокрытого электрода к вертикальной плоскости должен быть 15-20°. Валик, наплавленный толстопокрытым электродом, имеет более плоскую форму, так как наплавленный металл под слоем шлака застывает медленнее.
При сварке с глубоким проплавлением (Рис.2), может использоваться электрод ОЗС с повышенной толщиной покрытия, у которого расплавление обмазки несколько отстает от расплавления электрода, поэтому дуга плавится как бы внутри чехла. Действие дуги концентрируется и меньше потерь тепла, поэтому глубина проплавления увеличивается.
Рис.2. Сварка электродом с повышенной толщиной обмазки
Рис. 3. Схема сварки лежащим электродом
При сварке лежачим электродом (Рис.3), электрод с повышенной толщиной обмазки укладывается в разделку шва, возбуждают дугу, которая горит и по мере расплавления электрода перемещается по его длине.
Процесс сварки обечайки (Рис. 4). Сечение шва с указанием его размеров согласно ГОСТ 5264-80
Рис. 4. Сварка обечайки
Важным параметром технологического процесса дуговой сварки является подготовка кромок и сборка заготовок. Поэтому необходимо, прежде всего, указать тип соединения, форму разделки кромок, сборку под сварку (зазор). Подготовку кромок под сварку выполняют по ГОСТу, номер которого указывают на чертеже. Например, на рисунке заготовки задания указано С19-Р (ГОСТ 5264), что означает: Р- ручная дуговая сварка; С19 - условное обозначение шва сварного соединения. В этом же ГОСТе приведены поперечные сечения сварных швов с указанием геометрических размеров для заданных толщин металла.
Параметры сварных швов (Рис.5):
Для швов №1 и №2: тип соединения – стыковое;
Форма подготовленных кромок – со скосом кромок;
Характер сварного шва – односторонний на остающейся подкладке.
Рис. 5.Сварной шов
Подготовка кромок под сварку изображено на рисунке 6
Рис. 6. Подготовка кромок под сварку
Для нашего случая (S=S1=14мм) ширина сварного шва е=22мм; g=0,5мм.
Подбор марки и диаметра электрода, определение режимов сварки. Расчет массы наплавленного металла. Определение расхода электродов с учетом потерь, расхода электроэнергии и времени сварки изделия.
Режим сварки - один из основных элементов технологического процесса, который определяет качество и производительность сварки. При ручной дуговой сварке основными параметрами режима являются: диаметр электрода в мм (dэ), сварочный ток в амперах (Icв), напряжение на дуге в вольтах (Uд) и скорость сварки в м/ч (Vсв).
Определение режима сварки начинают с выбора диаметра электрода, его типа и марки. Диаметр электрода выбирается в зависимости от толщины свариваемого металла, а его марка - от химического состава. При выборе типа и марки электрода следует исходить из требований, предъявляемых к качеству сварного шва.
При изготовления обечайки используем сталь 08Х21Н6М2Т (хромоникельмолибденовая сталь аустенитно-ферритного класса). Она применяется для службы в окислительно-восстановительных средах, например, при органическом синтезе, сернокислотном производстве, и целлюлозно-бумажной промышленности. Типичное оборудование, изготавливаемое из стали 08X21Н6М2Т: ректификационные колонны, экстракционные, насадочные, продувные и другие емкости, хранилища, баки, сборники и т.д.
Для сварки листа 14 мм из стали 08Х21Н6М2Т выбирается электрод типа Э-08Х20Н9Г2Б.В нашем случае можно использовать несколько марок электродов. Остановим выбор на марке ЦЛ-11. Диаметр электрода выбирается – 5мм с основным покрытием. Сварочные электроды ЦЛ-11 предназначены для сварки изделий из коррозионно-стойких хромоникелевых сталей, когда к металлу шва предъявляют жесткие требования стойкости к межкристаллитной коррозии. Сварка во всех пространственных положениях шва постоянным током обратной полярности.Обеспечивает получение металла шва, стойкого к межкристаллитной коррозии при испытаниях по методу АМУ ГОСТ 6032-89 без провоцирующего отпуска. Содержание ферритной фазы в наплавленном металле 2,5-10% (типичное 6,1%).
Производительность процесса сварки определяется величиной коэффициента наплавки ан(г/А·ч). Для электродов ЦЛ-11 по ГОСТ 9466-75 ан = 11 г/А·ч;
Расход электродов на 1 кг наплавленного металла составляетΨ=1,7 кг;
Прокалка электродов ЦЛ-11 перед сваркой: 190-210°С, 1 ч.
Величину сварочного тока в зависимости от диаметра электрода определяют по формуле:
Icв= К · dэ(А),
где
К–эмпирический коэффициент, для высоколегированных сталей равный 35-40, выбираем К=40;
dэ- диаметр электрода(dэ=5мм)
Icв= 40 · 5=200А
Рекомендуемое число проходов для свариваемого металла толщиной 14 мм, электродом dэ=5 мм – четыре.
После того, как сила сварочного тока определена, следует рассчитать длину сварочной дуги (таблица 2). Расстояние между концом электрода и поверхностью свариваемого изделия и определяет длину сварочной дуги. Стабильное поддержание длины сварочной дуги очень важно при сварке, это сильно влияет на качество свариваемого шва. Лучше всего использовать короткую дугу, т.е. длина которой не превышает диаметр электрода, но это достаточно тяжело осуществить даже при наличии солидного опыта. Поэтому оптимальной длиной дуги принято считать размер, который находится между минимальным значением короткой дуги и максимальным значением (превышает диаметр электрода на 1-2 мм).
Таблица 2.
Примерное соотношение диаметра электрода и длины дуги | ||||||||
Диаметр электрода, мм | 1 | 1,5-2 | 3 | 3-4 | 4 | 4-5 | 5 | 6-8 |
Длина дуги, мм | 0,6 | 2,5 | 3,5 | 4 | 4,5 | 5 | 5,5 | 6,5 |
Напряжение на дуге для наиболее широко применяемых электродов в среднем составляет 25-30В.
Скорость сварки определяется из выражения:
Vсв = ( ан ·Icв) /(γ · Fн ·100) (м/ч),
где
ан — коэффициент наплавки ан = 11 г/А·ч;
Icв— сварочный ток Icв= 200 А;
γ — плотность металла γ=7,7 г/см3;
Fн — площадь поперечного сечения наплавленного металла шва, представляющая сумму площадей элементарных геометрических фигур, составляющих сечение шва и определяем его, используя сечение шва из ГОСТ, в масштабе 5:1. Сечение шва сформировано за счёт расплавленного основного металла и присадочного. Нам нужно выделить долю присадочного металла. Каждая клетка имеет площадь 1мм2. Подсчитав число клеток, принимаем суммарную площадь наплавленного металла в сечении Fн=160мм2=Fн=16см2
Для нашего многослойного сварного шва, под величиной Fн понимаемплощадь поперечного сечения наплавленного металла шва за один проход(Fпр):
Fпр=Fн/n(см2),
где
n – число наплавленных слоёв.
Fпр= 16/4 = 4(см2),
Vсв = ( 11·200) / (7,7 · 4 ·100)= 0,7(м/ч)
Объём наплавленного металла определяется по формуле:
Vн = Fн · L (см3),
где
L – суммарная длина сварных швов обечайки, находится по формуле:
L = l1+l2+l3+2·п·Dвн= 1500+1500+1500+2·3,14·1400 = 13292 (мм)
Vн = 160 · 13292 = 2126720 (мм3) = 2126,72(см3)
Зная площадь наплавленного металла, плотность и длину сварных швов, можно определить его массу на все изделие.
Масса наплавленного металла, для ручной дуговой сварки рассчитывается по формуле:
Gн= γ · Vн (г)
Gн= 7,7 · 2126,72 = 16376(г)
Общая масса наплавленного металла для изготовления обечайки Gн= 16376г.
Необходимая для сварки масса электродов, с учётом потерь, составит:
Gэ= Ψ · Gн (г)
Gэ= 1,7· 16376 = 27840 (г)
Полное время сварки, приближенно определяется по формуле:
tсв =Gн / Iсв · ан (ч)
tсв= 16376 / (200· 11)= 7,4 (ч)
Применим для проведения сварки однопостовый сварочный выпрямитель ВДГ – 301. Пределы регулирования по току данного аппарата 40-300 (Iсв=200) А, по напряжению 15-32 (U=20) В. КПД аппарата η=0,72.
Определим расход энергии, необходимой на сварку обечайки:
Е = U · Iсв · tсв (кВт·ч)
Е = 20 · 200 · 7,4 = 29600 (Вт·ч) = 29,6 (кВт·ч)
Расход электроэнергии, с учётом потерь в выбранном сварочном аппарате составит:
Еn = Е/ η (кВт·ч)
Еn = 29,6/ 0,72 = 41,1 (кВт·ч)
Параметры сварки обечайки из стали 08Х21Н6М2Т
Таблица 3.
Параметр | Обозначение | Значение |
Электроды | ЦЛ-11 | - |
Диаметр электрода | dэ | 5 |
Величина сварочного тока, А | Iсв | 200 |
Напряжение на дуге, В | U | 25 |
Скорость сварки, м/ч | Vсв | 0,7 |
Число наплавленных слоёв | n | 4 |
Суммарная длина сварных швов, мм | L | 13292 |
Объём наплавленного металла, см3 | Vн | 2126,72 |
Масса наплавленного металла, г | Gн | 16376 |
Масса электродов с учётом потерь, г | Gэ | 27840 |
Полное время сварки, ч | tсв | 7,4 |
Расход энергии на сварку, кВт·ч | Е | 29,6 |
Расход энергии, с учётом потерь в сварочном аппарате, кВт·ч | Еn | 41,1 |
Методы контроля качества сварного шва
Сварные швы и соединения ряда изделий и сооружений должны отвечать требованиям непроницаемости (герметичности) для различных жидкостей и газов. Учитывая это, во многих сварных конструкциях (емкости, трубопроводы, химическая аппаратура и т.д.) сварные швы подвергают контролю на непроницаемость. Этот вид контроля производится после окончания монтажа или изготовления конструкции.
Непроницаемость сварных швов контролируют следующимивидами неразрушающего контроля: технический (визуально-измерительный), капиллярный (проникающими веществами, люминесцентный или люминесцентно-цветной метод контроля),акустический (ультразвуковой), течеискание (воздушный или гидравлическим давлением), радиационный, магнитный.
Так как требований по давлению в обечайке не предусмотрено, то выбирается контроль: технический осмотр икапиллярный (люминесцентный, люминесцентно-цветной метод).
Визуально-измерительный метод. После изготовления изделия с применением сварки, первым делом необходимо провести технический осмотр (визуально-измерительный метод контроля). Контроль качества сварных соединений (наплавок) в процессе сварки (наплавки) и готового сварного соединения (наплавки) выполняют с целью подтверждения их соответствия требованиям конструкторской документации, ПТД и (или) НД и правил. Визуально-измерительный контроль сварных соединений (конструкций, узлов) проводят с целью выявления деформаций, поверхностных трещин, подрезов, прожогов, наплывов, кратеров, свищей, пор, раковин и других несплошностей и дефектов формы швов; проверки геометрических размеров сварных швов и допустимости выявленных деформаций, поверхностных несплошностей и дефектов формы сварных швов.
Дефекты, выявленные при визуальном и измерительном контроле, должны быть устранены до выполнения последующих технологических операций и проведения других видов (методов) неразрушающего контроля.
Люминесцентный илилюминесцентно-цветной метод контроля (метод красок),проводят с помощью специальных жидкостей, которые наносят на контролируемую поверхность изделия. Эти жидкости, обладающие большой смачивающей способностью, проникают в мельчайшие поверхностные дефекты - трещины, поры, непровары. Люминесцентный контроль основан на свойстве некоторых веществ светиться под действием ультрафиолетового облучения. Перед контролем поверхности шва и околошовной зоны очищают от шлака и загрязнений, на них наносят слой проникающей жидкости, которая затем удаляется, а изделие просушивается. Для обнаружения дефектов поверхность облучают ультрафиолетовым излучением - в местах дефектов следы жидкости обнаруживаются по свечению.
Контроль методом красок (цветная дефектоскопия) заключается в том, что на очищенную поверхность сварного соединения наносится смачивающая жидкость, которая под действием капиллярных сил проникает в полость дефектов. После ее удаления на поверхность шва наносится белая краска. Выступающие следы жидкости обозначают места расположения дефектов.
Литература
1.Технология конструкционных материалов: Учебник для студентов машиностроительных специальностей вузов / А.М. Дальский, Т.М. Барсукова, Л.Н. Бухаркин и др.; под ред. А. М. Дальского. - 5-е изд., исправленное. - М.: Машиностроение, 2004. - 512 с.
2.Китаев А.М. "Справочная книга сварщика" -М.,1985.(Серия справочников для рабочих).
3.Лащинский А.А. Конструирование сварных химических аппаратов: Справочник-Л.: Машиностроение. Ленингр. отд-ние 1981-382с.,ил.
4.Сварка и резка в промышленном строительстве. С 24 В2т.Т. 1/Б. Д.Малышев, А.И.Акулов, Е.К.Алексеев и др.; под редакциейБ.Д.Малышева. – 3-е изд., переработал и дополнил – М. Стройиздат, 1989-509с.: ил.- (справочник строителя).
5.Гоголев Ю.Г. Выполнение индивидуальных заданий и курсовой работы по технологии конструкционных материалов: учеб. пособие / Ю.Г. Гоголев; Иван. гос. хим.-технол. ун-т. – Иваново, 2014. – 111 с.
6.Контроль неразрушающий, межгосударственный стандарт. Москва ИПК Издательство стандартов, 2005.
Дата добавления: 2018-06-01; просмотров: 422; Мы поможем в написании вашей работы! |
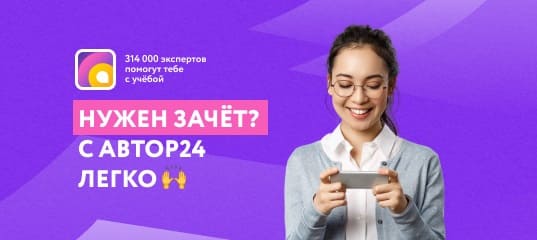
Мы поможем в написании ваших работ!