Программа испытаний электронной аппаратуры.
Испытанием электронной аппаратуры называется экспериментальное определение значений параметров и показателей качества изделия в процессе функционирования. Испытания являются одним из важнейших и завершающих этапов производства, так как по их результатам судят об эксплуатационной надежности изделия.
Испытания могут осуществляться с целью контроля качества продукции (контрольные испытания) и изучения ее параметров и показателей качества (исследовательские испытания).
По методу проведения различают испытания: разрушающие и неразрушающие. В результате проведения разрушающих испытаний проверенные изделия становятся непригодными к использованию. Основным требованием, предъявляемым к изделиям, подвергаемым климатическим, механическим и электрическим испытаниям является сохранение выходных (проверяемых) параметров после проведения испытания в пределах, установленных технически условиями.
Основными видами электрических испытаний являются определение сопротивления изоляции в холодном и горячем состояниях, испытание электрической прочности изоляции. Механические испытания включают в себя вибрационные и ударные испытания, испытания на воздействие линейных ускорений и на транспортирование. Основными видами климатических испытаний являются проверка на хладоустойчивость, теплоустойчивость, высотность (пониженное давление) и влажность.
|
|
Механическая обработка печатных плат.
Основные этапы: входной контроль материала (проверка размера листа, состояния поверхности, прочности сцепления фольги и диэлектрика и т.д.), получение заготовки (резка заготовки с припуском по контур), сверление монтажных отверстий (заготовки собирают в пакет толщиной не более 4,5мм, сверление выполняют в кондукторе спиральным сверлом из твердого сплава), обработка по контуру (вырубкой или фрезерованием получают окончательный контур платы после изготовления печатных проводников).
Получение рисунка печатной платы.
Основные методы, используемые в промышленности:
1.офсетная печать состоит в изготовлении печатной формы, на поверхности кт формируется рисунок слоя. Форму закатывают валиком трафаретной краской, а затем трафаретный цилиндр переносит краску с формы на подготовленную поверхность ПП (метод ограниченного применения);
2.сеткография основана на нанесении спец краски на плату путем продавливания ее резиновой лопаткой (рекелем) через сетчатый трафарет, на кт необходимый рисунок образован ячейками сетки, открытыми для продавливания (метод для массового производства);
3.фотопечать обладает самой высокой точностью и плотностью монтажа. Состоит в контактном копировании рисунка монтажа с фотошаблона на основание, покрытое светочувствительным слоем (фоторезистом).
|
|
Типовые технологические процессы изготовления печатных плат.
Субтрактивный процесс – получение рисунка путем травления, аддитивный – путем избирательного осаждения проводящего материала на нефольгированный материал основания, полуаддитивный – предусматривает предварительное нанесение тонкого (вспомогательного) проводящего покрытия, впоследствии удаляемого с пробельных мест.
Химический метод – на медную фольгу, приклеенную на диэлектрик, наносят позитивный рисунок схемы проводников. Травлением удаляется металл с незащищенных участков.
Комбинированный позитивный – для МПП и ГПП, проводящий рисунок суб. методом, а металлизацию отверстий электрохимическим способом.
Электрохимический – для ДПП высокой плотности, основное отличие – использование нефольгированного диэлектрика с обязательной его активацией поверхности.
Пайка. Групповые методы пайки. Проводной монтаж на печатных платах.
Пайка заключается в прогреве соединяемых элементов после нанесения припоя и сохранении их в сжатом состоянии до полного затвердения припоя. Состоит из двух фаз: смачивание припоем металлических поверхностей и заполнение припоем зазора между смоченными поверхностями.
|
|
Групповые методы:
- пайка погружением – плату помещают в кассету и погружают в расплавленный припой на половину толщины платы, затем включают вибрацию, что создает условия для проникновения флюса и припоя. Недостаток: коробление («сминается») плат.
- пайка в кассете – плата помещается в кассету, при опускании кассету в ванну с припоем она раздвигает оксидную пленку, кт находится по граням кассеты, когда кассета раскрывается припой, свободный от оксидной пленки, поступает в кассету.
- пайка с опрокидыванием – в ванну погружают сначала один конец платы, затем постепенно второй конец, подъем платы производится под углом, чтобы припой стекал и не образовывал наплывов.
- пайка волной припоя – нагрев паяемых материалов, перемещаемых над ванной, и подача припоя к месту соединения осуществляются стоячей волной припоя, возбуждаемой в ванне (электромагнитом).
- пайка струей припоя – разновидность пайки волной припоя, при ней происходит более интенсивное перемешивание припоя, что обеспечивает большую равномерность температуры и состава припоя.
|
|
Стежковый монтаж – изолированный провод укладывается на одной стороне ДПП и выводят его в виде петель через монтажные отверстия на другую сторону с присоединениям к контактным площадкам платы.
Многопроводной монтаж, фиксируемый проводами – прокладывание изолированных проводов с полиамидной изоляцией на поверхности ДПП, в плате с закрепленными монтажными проводами сверлят монтажные отверстия, торец провода должен соответствовать краю отверстия по форме, далее отверстие и торец подвергаются химико-гальванической металлизации.
Сварка. Монтажная сварка.
Контактная – осуществляется методом сопротивления, при котором ток, используемый для нагревания, пропускается последовательно от одного свариваемого изделия к другому через поверхность их соприкосновения.
Электродуговая – основана на плавлении металла под воздействием электрической дуги, образуемой при прохождении тока через воздушный промежуток между двумя проводниками. Один из проводников явл свариваемый металл, а другим – угольный или металлический электрод.
Диффузная – применяется для материалов, сварка кт обычными методами затруднена. Ее осуществляют при повышенных температурах с приложением сдавливающего усилия к месту сварки.
Термокомпрессионная сварка – осуществляется при одновременном воздействии повышенной температуры и давления.
Сварка с косвенным импульсным нагревом – наиболее прогрессивный, отличается от термоком. тем, что рабочий инструмент нагревается только в момент сварки, а выделение теплоты сосредоточено в нижней части инструмента.
Электроконтактная сварка расщепленным электродом – осуществляется за счет нагрева при пропускании электрического тока через свариваемые проводники между изолированными друг от друга электродами.
Ультразвуковая сварка – позволяет получить неразъемное соединение при совместном воздействии механических колебаний высокой частоты и относительно небольших сдавливающих усилий.
Склеивание.
Склеивание применяют для неразъемного соединения деталей из различных материалов. В основе процесса лежит явление адгезии, т.е. способность некоторых веществ прилипать к поверхности других материалов. Преимущество: отсутствует контактная коррозия, благодаря наличию клеевой пленки затрудняется передача колебаний. Недостатки: сравнительно низкая прочность, незначительная тепловая стойкость, длительность технологического процесса (ждать, пока затвердеет клей).
Дата добавления: 2018-05-31; просмотров: 263; Мы поможем в написании вашей работы! |
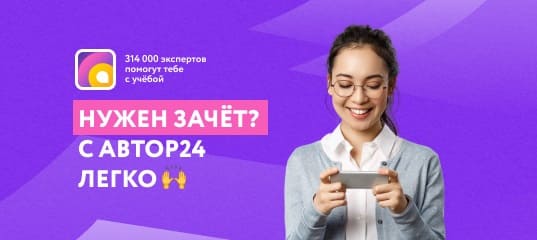
Мы поможем в написании ваших работ!