Общая характеристика производства
Содержание
1 Введение
2 Общая характеристика производства
3 Описание технологического процесса и его аппаратурного оформления (по ДП).
4 Контроль производства и управление технологическим процессом
5 Расчет первичных измерительных преобразователей (из ДП):
5.1 Сужающего устройства пр.
6 Обоснование выбора средств измерений по измерительным каналам
7 Монтаж средств контроля и автоматизации
7.1 Монтаж ………………………………….
8 Охрана труда.
9 Литература
Введение
Назначением и целью того или иного производственного процесса химической технологии является переработка сырья в соответствующую продукцию определенного количества и качества. Чтобы судить о качестве целевого продукта, необходимо характеризовать его теми или иными показателями, измеряя их. К таким показателям относятся плотность, вязкость, химический или фракционный состав, содержание нежелательных компонентов, концентрация целевого продукта в смеси, температура начала или конца кипения продукта и т.д. показатели качества следует оценивать с количественной стороны, т.е. отвечать на вопросы, «сколько?», « как они велики или малы?». На эти же вопросы мы получить ответ, измеряя количество продуктов независимо от их качества или измеряя количество сырья и других материалов, поступающих на производство.
|
|
В химической промышленности комплексной механизации и автоматизации уделяется большое внимание. Это объясняется сложностью протекания технологических процессов, а также чувствительностью их к нарушению режима, вредностью условий работы рабочих, взрыво- и пожароопасностью перерабатываемых веществ.
Наступает новый этап машинного производства – автоматизация, когда человек освобождается от непосредственного участия в производстве, а функции управления технологическими процессами, механизмами, машинами передаются автоматическим устройством.
Автоматизация приводит к улучшению основных показателей эффективности производства увеличению количества, улучшению качества и снижению себестоимости выпускаемой продукции, повышению производительности труда. Внедрение автоматических устройств обеспечивает сокращение брака и отходов, уменьшают затраты сырья и энергии, уменьшение численности основных рабочих, снижение капитальных затрат.
Проведение некоторых современных технологических процессов возможно только при условии их полной автоматизации (например, процессы осуществляемые на атомных установках и в паровых котлах высокого давления, процессы дегидрирования и др.) Комплексная автоматизация процессов химической технологии предполагает не только автоматическое обеспечение нормального хода этих процессов с использованием различных автоматических устройств, но и автоматическое управление пуском и остановки аппаратов для ремонтных работ и в критических случаях.
|
|
Основной целью управления технологическими процессами, протекающими в соответствующих аппаратах, является стабилизация технологических режимов. Решение этой задачи достигается с помощью автоматических регуляторов, являющихся частью системы автоматического регулирования. Кроме того, при управлении технологическими процессами нередко осуществляется их оптимизация т.е. реализация того или иного критерия эффективности, обеспечивающего протекание процесса в наилучшем направлении. При строительстве новых предприятий и реконструкции действующий большой объем работ приходится на монтаж систем автоматического контроля и управления автоматическими процессами. В настоящее время широкое распространение получил индустриальный метод полносборного монтажа систем автоматического контроля и управления, и поставляется на монтажную площадку в виде укрупненных узлов и блоков.
|
|
Решаемые в настоящее время задачи комплексной автоматизации производственных процессов с всеобщим переходом к цехам – автоматам и предприятиям автоматам и связаны с повышением сложности систем автоматического контроля и управления насыщенности процессов приборами. При этом ход технологического процесса, производительность установок, качество выпускаемой продукции и состояние технологического оборудования зависят от качества работы автоматических систем.
В автоматическом производстве человек переключается на творческую работу – анализ регуляторов управления, составление заданий и программ для автоматических приборов, наладку сложных автоматических устройств и т.д. От специалиста требуются знания не только устройства различных приборов, но и общих принципов составления систем автоматического управления. При подготовке кадров среднего звена по специальности: «Эксплуатация автоматических устройств химических производств» дисциплина «Автоматизация производственных процессов в химическом производстве» является профилирующей наряду с курсом «Автоматическое регулирование и регуляторы» и «Технологические измерения и КИП».
|
|
Автоматизация – одна из ведущих отраслей науки и техники, развивается в настоящее время особенно быстро, она проникает во все сферы деятельности человека.
Развитие автоматизации производства подразделяется на несколько этапов, значительно отличающихся один от другого в техническом, экономическом организационном отношениях.
Автоматизация технологических процессов и вспомогательных служб связана не только с совершенствованием производства и улучшением условий труда, но и с повышением его рентабельности за счёт технико-экономических показателей и снижение материальных и трудовых затрат на единицу продукции.
При создании схем автоматизации необходимо знать является ли процесс непрерывным или периодическим. Автоматизация непрерывных процессов приводит к большому эффекту, кроме того их легче автоматизировать, так как число параметров управления этих процессов невелико. Автоматизировать дискретные процессы значительно труднее, так как имеется большое число параметров управления.
Для управления применяют автоматизированные системы управления АСУ – человеко-машинные системы, обеспечивающие автоматизированный сбор и обработку информации, необходимой для оптимизации управления. Сбор и оперативная обработка информации, вычисление критериев, нахождение оптимальных значений управляющих воздействий в этих системах осуществляется с помощью различных технических средств и электронно-вычислительных машин. Обслуживать которые должен человек знающий технологический процесс и умеющий предотвратить сбой в режиме процесса.
Большую роль в повышении качества выпускаемой продукции играет автоматизация технологического процесса. В дипломном проекте в качестве системы управления выбрана «Автоматизированная система управления технологическими процессами» с централизованной структурой.
В качестве технических средств выбраны первичные измерительные преобразователи (датчики, нормирующие преобразователи, преобразователи сигналов, исполнительные механизмы, средства отображения информации, выпускаемые заводами-изготовителями на момент разработки проекта по высоким технологиям).
Для обработки информации и управления в проект заложены программно-технические средства автоматизации: программируемый микроконтроллер (КР-500) и микро ЭВМ.
Общая характеристика производства
Наименование производства: Промышленное производство перкарбоната натрия технического стабилизированного (пероксисольвата карбоната натрия).
Год ввода в эксплуатацию:
первая очередь – в 2001 г.
вторая очередь – в 2003 г.
Мощность производства:
проектная – 20 000 т/год
достигнутая на момент составления регламента 10 000 т/год (на первой очереди)
Метод производства:
Метод производства пероксисольвата карбоната натрия (ПКН) основан на взаимодействии раствора карбоната натрия с раствором пероксида водорода с последующей грануляцией и сушкой готового продукта. Поскольку ПКН способен разлагаться под влиянием влаги, ионов тяжелых металлов, органических и механических загрязнений в состав ПКН вводится комплекс стабилизаторов: сульфат магния, полифосфат натрия, жидкое стекло.
Количество технологических линий, стадий:
Приготовление рабочего раствора соды производится периодическим способом на одном технологическом потоке.
Синтез, гранулирование и сушка ПКН производится непрерывным способом: схема № 1 – 2 потока (первая очередь),
схема № 2 – 2 потока (вторая очередь).
Количество технологических стадий - 11.
Предприятие, выполнявшее проект:
Проект в полном объеме выполнен ПКУ ОАО «Химпром» в 1999, 2002 году.
Предприятие – разработчик технологического процесса:
Технологический процесс разработан ГНИИХТЭОС г. Москва.
Сведения о реконструкции:Данный регламент вводится с целью расширения производства. Проект № 22165-560 расширения производства ПКН выполнен ПКУ ОАО «Химпром» в 2002 году по разработке Инновационного центра ОАО «Химпром» («Исходные данные на проектирование промышленного производства пероксисольвата карбоната натрия мощностью 10000 т/год (2-я очередь), утв. 28.12.01 г.)
По условиям труда производство относится к вредным.
Дата добавления: 2018-06-01; просмотров: 198; Мы поможем в написании вашей работы! |
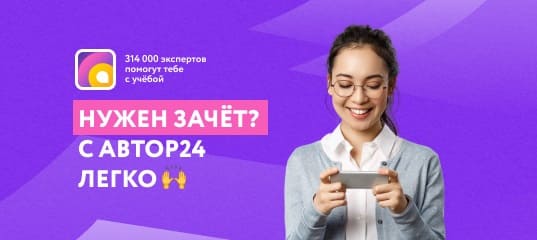
Мы поможем в написании ваших работ!