Содержание графической части проекта
1-й лист – Годовой график ППР или планировка РМЦ, РММ.
2-й лист – Конструктивный узел станка.
3-й лист – Рабочие чертежи деталей конструктивного узла.
4-й лист – Карта и схема смазки станка или геометрические выверки станка.
5-й лист – Кинематическая, пневматическая, гидравлическая и другие принципиальные схемы станка.
Если разрабатывается проект реконструкции РМЦ или РММ, то выполняется план цеха до реконструкции и план цеха после реконструкции. Количество и содержание листов графической части определяется руководителем проекта.
Введение
Этот вступительный раздел дипломного проекта должен отразить основные задачи, стоящие перед деревообрабатывающей промышленностью, по дальнейшему совершенствованию техники и технологии основного производства, повышению производительности и качества выпускаемой продукции. Отмечается роль в решении задач эффективной организации системы планово-предупредительного ремонта в организации.
Общая часть
1.1 Характеристика организации, на базе которой выполняется дипломный проект
Описать расположение организации, состав основных производственных цехов (можно дать краткую характеристику главных цехов), ассортимент выпускаемой продукции, технико-экономические показатели работ за предыдущий год, перспективы развития организации (можно дать диаграммы роста выпуска продукции, производительности труда, фотографии цехов, схемы предприятия – по согласованию с руководителем проекта).
|
|
1.2 Обоснование выбора темы проекта
В этом разделе учащийся должен провести анализ состояния существующей ремонтной базы организации и раскрыть её недостатки (наличие ремонтно-механических мастерских, цехов, состояние основных участков для выполнения станочных, слесарных, кузнечных, сварочных работ и т. д., оснащённость всех участков оборудованием, механизация трудоёмких работ, организация рабочих мест). На основании анализа необходимо сделать вывод о целесообразности выполнения дипломного проекта на соответствующую тему.
Учащийся должен рассмотреть различные варианты решения вопроса по выявленным недостаткам и принять наиболее эффективный.
Технологическая часть
2.1 Выбор системы технического обслуживания и ремонта оборудования
Существует три основных вида организации выполнения ремонтных работ на промышленных предприятиях: централизованная, децентрализованная и смешанная.
Централизованная организация выполнения ремонтных работ, предусматривающая выполнение всех ремонтных работ на заводе силами и средствами отдела главного механика и его ремонтно-механического цеха, типична для предприятий с небольшим количеством оборудования. Ее недостатком является полное освобождение цехов от выполнения ремонта эксплуатируемого оборудования, что снижает ответственность производственного персонала за его техническое состояние.
|
|
Децентрализованная организация выполнения ремонтных работ состоит в том, что все виды ремонтных работ (межремонтное обслуживание, периодический ремонт, в том числе и капитальный) производятся под руководством механиков цехов, так называемыми цеховыми ремонтными базами, в состав которых входят ремонтные бригады. В ремонтно-механическом цехе, подчиняющемся главному механику, осуществляется только капитальный ремонт сложных агрегатов. Кроме того, в нем изготавливают и восстанавливают для цеховых ремонтных баз те детали и сборочные единицы, изготовление и восстановление которых требует применения оборудования, отсутствующего на ремонтной базе.
Для смешанной организации выполнения ремонтных работ характерно то, что все виды ремонта, кроме капитального, выполняют цеховые ремонтные базы, а капитальный ремонт — ремонтно-механический цех, имеющий соответствующие отделения (слесарное, станочное, сварочное).
|
|
Кроме перечисленных методов технического обслуживания ГОСТ 18322 — 78 предусматривает:
- поточное техническое обслуживание, выполняемое на специализированных рабочих местах в определенной технологической последовательности (применяется в массовом или крупносерийном производстве);
- техническое обслуживание эксплуатационным персоналом, т.е. персоналом, работающим на данном оборудовании в период его эксплуатации;
- техническое обслуживание специализированным персоналом — рабочими, подготовленными специально по объектам, маркам объектов, видам операций и видам технического обслуживания;
- техническое обслуживание специализированной организацией, с которой заключается соответствующий договор;
- техническое обслуживание предприятием-изготовителем (в гарантийный период или по договору оно производит замену деталей и агрегатов, отказавших во время работы или настройки оборудования).
Учащийся должен выбрать наиболее целесообразную для своего предприятия систему организации ремонтной службы с учетом существующей.
2.2 Выбор системы планово-предупредительного ремонта оборудования
|
|
Правильный выбор системы ППР, как и выбор системы организации ремонтного хозяйства, имеет решающее значение в разработке темы: «Проект организации технического обслуживания и системы ППР для технологического оборудования», так как расчет трудоемкости ремонта и технического обслуживания, расчет и составление графика ППР зависят от видов системы ОГМ и ППР.
Система планово-предупредительного ремонта (ППР) представляет собой комплекс организационных и технических мероприятий предупредительного характера по техническому обслуживанию (ТО) и ремонту (Р) изношенных деталей и узлов, проводимых по составленному плану для обеспечения работоспособности станков в течение всего срока службы.
Планово-предупредительный ремонт оборудования производится, когда его износ не перешел в прогрессирующее состояние, а не тогда, когда оборудование износилось настолько, что уже вышло из строя (ремонт по потребности). Такой ремонт в отличие от ремонта по потребности планируется заранее (отсюда и его название — планово-предупредительный).
Система ППР предусматривает проведение профилактических осмотров и видов планового ремонта (текущего, среднего и капитального) каждого агрегата после того, как он отработал определенное количество часов.
Чередование и периодичность осмотров и видов планового ремонта оборудования определяются его назначением и условиями эксплуатации.
В систему ППР входит периодический, послеосмотровой и стандартный ремонт. Наибольшее распространение в д/о промышленности получила система периодического ремонта; она положена в основу типового положения «Единая система ППР» (ГОСТ 18322—78). Наибольший экономический эффект ее применение дает при ремонте оборудования, работающего в условиях массового и крупносерийного производства при достаточно высокой загрузке и учете отработанного им времени (наработки). Но поскольку даже на предприятиях крупносерийного и массового производства наряду с таким оборудованием имеется значительное количество станков и машин, загруженных не полностью и используемых лишь эпизодически, в настоящее время признано экономически целесообразным применять на большинстве заводов все три системы ППР:
- для оборудования, работающего в условиях массового и важного для предприятия крупносерийного производства, — систему периодического ремонта;
оборудования, применяющегося в менее ответственном производстве — систему послеосмотрового ремонта;
специального оборудования, работающего на постоянном режиме — систему стандартного ремонта.
Учащийся должен обосновать выбор системы ППР, указать ее сущность, достоинства и недостатки.
2.3 Определение объема ремонтных работ
2.3.1 Составление сводной ведомости технологического оборудования
Здесь учащийся должен дать ведомость на оборудование своего цеха или участка, в которой указываются необходимые для проектирования сведения об оборудовании. Категория ремонтной сложности и все остальные данные для ведомости принимаются по графикам ППР оборудования из отчета по преддипломной практике.
Различное по назначению оборудование имеет разную загрузку в процессе производства и разную степень долговечности и износа. Поэтому для расчета трудоемкости ремонта оборудование разбивается на группы.
В условиях дипломного проекта это разделение может быть следующим:
- I группа (Rм ≥ 10 ЕРС)
К этой группе оборудования обычно относятся пресса, лесопильные рамы, мощные четырехсторонние продольно-фрезерные станки, лущильные, шпонострогальные, для измельчения древесины, сушилки и т.п.
- II группа (Rм= 7 ÷9ЕРС)
К этой группе относятся маломощные продольно-фрезерные станки, круглопильные станки для распиловки бревен и брусьев, ленточнопильные бревнопильные и делительные, рейсмусовые и др.
- III группа (Rм= 4 ÷6ЕРС)
К этой группе относятся ленточнопильные столярные станки, круглопильные станки для распиловки пиломатериалов, фрезерные, заточные и др.
- IV группа (Rм = 3 ≤ ЕРС)
К этой группе следует отнести маломощное оборудование с ручной подачей
- V (Оборудование по производству ДСП, ДВП, ДСтП)
- VI (Подъемно-транспортное оборудование)
- VII (Металлорежущее оборудование)
- VIII (Вентиляционное оборудование д/о цехов)
В основе расчета трудоемкости ремонта и технического обслуживания лежит понятие о категории ремонтной сложности оборудования, которая зависит от сложности конструкции и габаритных размеров станка.
Категорию ремонтной сложности можно определить по справочным таблицам или расчетным методом.
Категорию ремонтной сложности оборудования для механическойRм, ЕРС и электрической Rэ, ЕРС частейвычисляют по формулам 1, 2
(1)
+ 1,15*п) (2)
где Р – масса станка, т;
V – габаритный объем станка без учета выступающих частей, м3;
N – суммарная мощность электродвигателей, кВт;
Км – коэффициент металлоемкости станка, т/м3;
Кт – коэффициент точности изготовления станка;
К – коэффициент приведения к асинхронному электродвигателю;
п – количество электродвигателей, установленных на станке.
Значения Р, N, п принимают по технической характеристике оборудования.
Габаритный объем оборудования V, м3, вычисляют по формуле
(3)
где L – длина оборудования, м;
B – ширина оборудования, м;
H – высота оборудования, м.
Коэффициент металлоемкости оборудования Км, вычисляют по формуле
(4)
Значения коэффициентов Кт и К находят по таблицам 1, 2 приложения А.
Учащийся должен иметь навыки расчета категории ремонтной сложности оборудования, поэтому он должен дать примеры расчета Rм и Rэ на оборудование, которое прорабатывается в специальной части проекта.
При составлении сводной ведомости необходимо учесть перспективы развития предприятия, неучтенное вспомогательное оборудование, приспособления и механизированные инструменты, поэтому суммарная ремонтная сложность увеличивается на определенный процент, величина которого определяется индивидуально в соответствии с данными предприятия.
Cводную ведомость оборудования технологического цеха выполняем в виде таблицы 1
Таблица 1 - Сводная ведомость оборудования технологического цеха
Наименование оборудования | Марка | Количество | Категория ремонтной сложности | Суммарная ремонтная сложность | Группа оборудования | ||
Rм | Rэ | åRм | åRэ | ||||
1 | 2 | 3 | 4 | 5 | 6 | 7 | 8 |
Пресс гидравлический | Mixota | 1 | 89,0 | 96,3 | 89,0 | 96,3 | I |
Лесопильная рама | Р65-4А | 1 | 10,0 | 5,0 | 10,0 | 5,0 | I |
Станок четырехсторонний | С25-4 | 1 | 9,3 | 13,5 | 9,3 | 13,5 | II |
Станок круглопильный | ЦМР-3 | 1 | 6,6 | 9,1 | 6,6 | 9,1 | II |
Станок фуговальный | DOUH | 1 | 4,8 | 4,0 | 4,8 | 4,0 | III |
Станок фрезерный | ФСА | 1 | 6,3 | 5,0 | 6,3 | 5,0 | III |
Станок шлифовальный | с/и | 2 | 3,0 | 4,0 | 6,0 | 8,0 | IV |
Станок стружечный | ДС- 5 | 2 | 9,0 | 8,0 | 18,0 | 16,0 | V |
Таль электрическая | 5т | 1 | 6,0 | 10,5 | 6,0 | 10,5 | VI |
Транспортер | ПРД36 | 2 | 2,0 | 1,0 | 4,0 | 2,0 | VI |
Станок токарный | 16К20 | 1 | 15,0 | 14,0 | 15,0 | 14,0 | VII |
Компрессор | В-20/8 | 1 | 15,0 | 9,0 | 15,0 | 9,0 | VIII |
Итого | 15 | 190 | 192,4 | ||||
Итого с увеличением на % | 190*% | 192,4*% |
Примечание -Сведенияоб оборудовании собственного изготовления и процентное увеличение суммарной сложности оборудования согласуется с руководителем проекта.
2.3.2 Определение объема ремонтных работ по группам оборудования
Для определения объема ремонтных работ по группам оборудования, необходимо разбить все оборудование на укрупненные группы.
Данные и результаты расчетов приведены в виде таблице 2
Таблица 2 - Объём ремонтных работ по группам оборудования
№ группы | Марка оборудования | Категории ремонтной сложности, Rм | Количество станков, шт | Количество ремонтных единиц по группам оборудования |
1 | 2 | 3 | 4 | 5 |
I | Mixota | 89,0 | 1 | 89,0 |
Р65-4А | 10,0 | 1 | 10,0 | |
Итого | 2 | 99,0 | ||
Итого с увеличением на % | 99,0 * % | |||
II | С25-4 | 9,3 | 1 | 9,3 |
ЦМР-3 | 6,6 | 1 | 6,6 | |
Итого | 2 | 15,9 | ||
Итого с увеличением на% | 15,9 * % | |||
III | DOUH | 4,8 | 1 | 4,8 |
ФСА | 6,3 | 1 | 6,3 | |
Итого | 2 | 11,1 | ||
Итого с увеличением на% | 11,1 * % | |||
IV | с/и | 3,0 | 2 | 6,0 |
Итого | 2 | 6,0 | ||
Итого с увеличением на % | 6,0 * % | |||
V | ДС-5 | 9,0 | 2 | 18,0 |
Итого | 2 | 18,0 | ||
Итого с увеличением на % | 18,0 * % | |||
VI | 5т | 6,0 | 1 | 6,0 |
ПРД36 | 2,0 | 2 | 4,0 | |
Итого | 3 | 10,0 | ||
Итого с увеличением на % | 10,0 * % | |||
VII | 16К20 | 15,0 | 1 | 15,0 |
Итого | 1 | 15,0 | ||
Итого с увеличением на % | 15,0 * % | |||
VIII | В-20/8 | 15,0 | 1 | 15,0 |
Итого | 1 | 15,0 | ||
Итого с увеличением на % | 15,0 * % | |||
Всего | 15 | 107,0 | ||
Всего с увеличением на % | 190,0 * % |
2.4 Определение продолжительности и структуры ремонтного цикла
Ремонтный цикл Т по ГОСТ 18322 – это наименьший повторяющийся интервал времени, в течении которого выполняются в определенной последовательности в соответствии с требованиями нормативно-технической документации все установленные виды ремонта, т. е. это период работы станка от ввода в эксплуатацию до первого капитального ремонта ( или между очередными капитальными ремонтами).
Структура ремонтного цикла – это перечень и последовательность осмотров и ремонтов за ремонтный цикл.
Условные обозначения плановых ремонтных мероприятий следующие:
О – осмотр;
Т – текущий ремонт;
С – средний ремонт;
К – капитальный ремонт.
По согласованию с руководителем дипломного проекта учащийся выбирает структуру и продолжительность ремонтного цикла.
Структура и продолжительность ремонтного цикла по группам оборудования представлены в виде таблицы 3
Таблица 3 – Продолжительность и структуры ремонтных циклов по группам
оборудования
Группы оборудования | Продолжительность ремонтного цикла, Тц | Количество мероприятий за ремонтный цикл | |||||||
В отрабо-танных часах | В отработанных годах при работе | Осмотр | Текущий ремонт | Средний ремонт | Капитальный ремонт | ||||
в 1-у смену | в 2-е смены | ||||||||
1 | 2 | 3 | 4 | 5 | 6 | 7 | 8 | ||
I | 11100 | 5,5 | 3 | 12 | 9 | 2 | 1 | ||
К-О-Т1-О-Т2-О-Т3-О-С1-О-Т4-О-Т5-О-Т6-О-С2-О-Т7-О-Т8-О-Т9-О-К Всего ∑М =24 мероприятия | |||||||||
II | 15200 | 7,0 | 3,5 | 18 | 6 | 2 | 1 | ||
К- О-О-Т1-О-О-Т2-О-О-С1-О-О-Т3-О-О-Т4-О-О-С2-О-О-Т5-О-О-Т6-О-О-К Всего ∑М = 27 мероприятий | |||||||||
III | 20000 | 8,5 | 4,0 | 20 | 7 | 2 | 1 | ||
К-О-О-Т1-О-О-Т2-О-О-Т3-О-О-С1-О-О-Т4-О-О-Т5-О-О-С2-О-О-Т6-О-О-Т7-О-О-К Всего ∑М = 30 мероприятий | |||||||||
IV | 18600 | 9,5 | 4.5 | 18 | 6 | 2 | 1 | ||
К-О-O-Т1-ОO-Т2-О-O-C1-OO-Т3-О-O-Т4-О-O-C2-O-O-Т5-О-O-Т6-О-O-К Всего ∑М = 27 мероприятия | |||||||||
V | 25900 | 9,0 | 6,0 | 12 | 9 | 2 | 1 | ||
|
| ||||||||
Продолжение таблицы 3 | |||||||||
1 | 2 | 3 | 4 | 5 | 6 | 7 | 8 | ||
К-О-Т1-О-Т2-О-Т3-О-С1-О-Т4-О-Т5-О-Т6-О-С2-О-Т7-О-Т8-О-Т9-О-К Всего ∑М = 24 мероприятия | |||||||||
VI | 14000 | 7,0 | 3,5 | 36 | 8 | - | 1 | ||
К-О-О-О-O-Т1-О-О-О-O-Т2-О-О-О-O-Т3-О-О-О-О-Т4-О-О-О-O-Т5-О-O-О-O-Т6-О-О-О-О-Т7-О-О-О-O-Т8-О-O-О-О-К Всего ∑М = 45 мероприятия | |||||||||
VII | 39600 | 20,0 | 10,0 | 6 | 4 | 1 | 1 | ||
К-О-Т1- О-Т2 –О-С-О-Т3-О-Т4-О-К Всего ∑М = 12 мероприятий | |||||||||
VIII | 17600 | 8,8 | 4,4 | 12 | 4 | 1 | 1 | ||
К-О-О-Т1-О-О-Т2-О-О-C-О-О-Т3-О-O-Т4- -О-О-К Всего ∑М = 18 мероприятия | |||||||||
Примечание –таблицаоформляется по группам своего оборудования.
2.5 Расчет коэффициента цикличности ремонтных операций
Для определения трудоёмкости ремонта оборудования необходимо рассчитать цикличность ремонтных операций, т.е. сколько ремонтных операций из структуры ремонтного цикла придётся на один год.
а) Коэффициент цикличности Кц, вычисляют по формуле
(5)
где п - число осмотров или ремонтов в структуре ремонтного цикла, кол;
Тц - продолжительность ремонтного цикла, год.
Расчеты выполняются в виде таблицы 4.
Таблица 4 - Коэффициенты цикличности ремонта оборудования
Группа оборудова-ния | Продол-житель-ностьре-монтного циклаТц, год | Коэффициент цикличности | |||||||
Осмотр
| Текущий ремонт | Средний ремонт | Капитальный ремонт | ||||||
по | Кцо | пт | Кцт | пс | Кцс | пк | Кцк | ||
1 | 2 | 3 | 4 | 5 | 6 | 7 | 8 | 9 | 10 |
I | 12 | 9 | 2 | 1 | |||||
II | 18 | 6 | 2 | 1 | |||||
III | 20 | 7 | 2 | 1 | |||||
Продолжение таблицы 4 | |||||||||
1 | 2 | 3 | 4 | 5 | 6 | 7 | 8 | 9 | 10 |
IV | 18 | 6 | 2 | 1 | |||||
V | 12 | 9 | 2 | 1 | |||||
VI | 36 | 8 | - | 1 | |||||
VII | 6 | 4 | 1 | 1 | |||||
VIII | 12 | 4 | 1 | 1 |
2.6 Определение годового объема трудозатрат на ремонт и техническое обслуживание оборудования
2.6.1 Расчет годового объёма ремонтных работ
а) Годовой объем ремонтных работ для каждой группы оборудованияNм, ЕРС, вычисляют по формуле
(6)
где – количество ремонтных единиц по каждой группе оборудования c увеличением на %, ЕРС (таблица 2) .
Расчеты выполняются в виде таблицы 5.
Таблица 5 - Годовой объём ремонтных работ по видам и группам оборудования
Группа обору-дования | Количество ремонтных единиц∑Rм, ЕРС | Осмотр | Текущий ремонт | Средний ремонт | Капитальный ремонт | ||||
Кцо | Nм.о | Кцт | Nм.т | Кцс | Nм.с | Кцк | Nм.к | ||
1 | 2 | 3 | 4 | 5 | 6 | 7 | 8 | 9 | 10 |
I | |||||||||
II | |||||||||
III | |||||||||
IV | |||||||||
V | |||||||||
VI | |||||||||
VII | |||||||||
VIII | |||||||||
Итого | ∑Nм.о | ∑Nм.т | ∑Nм.с | ∑Nм.к |
2.6.2 Расчет годовой трудоемкости ремонта оборудования
а) Годовую трудоемкость ремонта механической части оборудования Ам, чел-час, вычисляют по формуле
где ∑Nм - суммарный годовой объем ремонтных работ по каждому виду мероприятий, ЕРС;
С - норматив трудоемкости на 1 ЕРС, чел-час (таблица 3, приложение А).
Расчеты выполняются в виде таблицы 6
Таблица 6 - Годовая трудоёмкость ремонта механической части оборудования
Виды мероприятий
| Суммарный годовой объем ремонтных работ ∑N, чел-час | Трудозатраты | |||||
Слесарные | Станочные | Прочие | |||||
Ссл | Асл | Сст | Аст | Спр | Апр | ||
1 | 2 | 3 | 4 | 5 | 6 | 7 | 8 |
Осмотр | ∑Nм.о | 1,9 | 0,2 | - | - | ||
Текущий | ∑Nм.т | 5,2 | 1,5 | 0,2 | |||
Средний | ∑Nм.с | 9,8 | 4,8 | 0,4 | |||
Капитальный | ∑Nм.к | 23,1 | 9,7 | 2,1 | |||
Итого | ![]() | ![]() | ![]() |
2.6.3 Расчет полного объем трудозатрат на ремонт оборудования
а) Полный объем трудозатрат ∑ Аобщ, чел-час, вычисляют по формуле
(8)
где - суммарная трудоёмкость ремонта, соответственно слесарная, станочная и прочая, чел-час
2.7 Определение штата рабочих по ремонту и техническому обслуживанию оборудования
2.7.1 Расчет численного состава ремонтной бригады
а) Численность слесарей-ремонтниковчсл, кол., вычисляют по формуле
(9)
где Тр- количество часов работы 1 рабочего в год, час ( принимается по данным отчета по преддипломной практике).
Принимается определенное количество человек
б) Годовой объём кузнечных работ Акуз, чел-час и численность кузнецов чкуз, кол., вычисляют по формулам 10, 11
, (10)
(11)
Принимается определенное количество человек
в) Годовой объём жестяницких работ Ажес., чел-час и численность жестянщиков чжес, кол., вычисляют по формулам 12, 13
, (12)
(13)
Принимается определенное количество человек
г) Годовой объём сварочных работ Асв, чел-час и численность сварщиков чсв, кол., вычисляют по формулам 14, 15
, (14)
(15)
Принимается определенное количество человек
2.7.2 Расчет численного состава бригады по техническому обслуживанию
Для межремонтного технического обслуживания определяется численность дежурного персонала по нормативам технического обслуживания.
2.7.2.1 Численность дежурного персонала чдеж., кол.,и объем трудозатрат Адеж., чел-час, для различных профессий вычисляют по формулам 16, 17
(16)
(17)
где åR - суммарный коэффициент ремонтной сложности по механической и электрической частям с увеличением на соответствующий процент, ЕРС;
m- сменность работы оборудования, кол;
Н – норматив межремонтного технического обслуживания, ЕРС (таблица 4 приложения А).
а) Число дежурных слесарей и их объем трудозатрат
Принимается определенное количество человек
б) Число дежурных станочников и их объем трудозатрат
Принимается определенное количество человек
в) Число дежурных электрослесарей и их объем трудозатрат
Принимается определенное количество человек
2.8 Определение объёма ремонтных работ по электрической части
оборудования и штата ремонтного персонала(выполняется по теме «Проект (реконструкция) ремонтно-механического цеха или мастерской деревообрабатывающего предприятия».
Расчет объёма ремонтных работ по электрической части оборудования производится исходя из ремонтной сложности оборудования, структуры и продолжительности ремонтного цикла, а так же нормативов на ремонтные работы.
2.8.1 Определение продолжительности ремонтного цикла и расчет количества ремонтов
а) Продолжительность ремонтного цикла определяют по данным таблицы 7
Таблица 7 -Продолжительность ремонтных периодов и циклов для
электрооборудования
Электродвигатели закрытого исполнения | Продолжительность ремонтныхпериодов и циклов | ||
Период между Т- С, Пт.с | Период между С- К, Пс.к | Ремонтный цикл, Тц | |
1 | 2 | 3 | 4 |
При работе в 1 смену | 24 (2 года) | 72 (6 лет) | 96 (8 лет) |
При работе в 2 смены | 12 (1 год) | 36 (3 года) | 48 (4 года) |
При работе в 3 смены | 6 (0,5 года) | 18 (1,5 года) | 24 (2 года) |
Примечание – таблица оформляется по данным своего предприятия
б) Число текущих Ти средних С ремонтов за цикл Чс.т, кол., вычисляют по формуле
(18)
где Тц – продолжительность ремонтного цикла для электрооборудования, год;
пт.с – продолжительность ремонтного периода между текущим и средним ремонтами, год.
в) Число средних ремонтовСза циклЧс, кол., вычисляют по формуле
(19)
где пс.к – продолжительность ремонтного периода между средним и капитальным ремонтами, год.
г) Число текущих ремонтов Т за цикл ЧT, кол.,вычисляют по формуле 20
(20)
д) Число капитальных ремонтовК в циклеЧк, кол., вычисляют по формуле 21
(21)
На основании выше указанных расчетов определяются коэффициенты цикличности.
2.8.2 Расчет коэффициентов цикличности
а) Коэффициент цикличности Кц, вычисляют по формуле
(22)
где п - число ремонтов за ремонтный цикл, кол;
Тр - продолжительность ремонтного цикла электрооборудования, год.
Расчеты выполняем в виде таблицы 8
Таблица 8 – Коэффициенты цикличности ремонта электрооборудования
Продол-жительность ремонтного цикла Тц, год | Коэффициент цикличности | |||||
Текущий ремонт | Средний ремонт | Капитальный ремонт | ||||
пт | Кц.т | пс | Кц.с | пк | Кц.к | |
1 | 2 | 3 | 4 | 5 | 6 | 7 |
8,0 | 3 | 0,375 | 1 | 0,125 | 1 | 0,125 |
4,0 | 3 | 0,75 | 1 | 0,25 | 1 | 0,25 |
2,0 | 3 | 1,5 | 1 | 0,5 | 1 | 0,5 |
Примечание – таблица оформляется по данным своего предприятия.
2.8.3 Определение годового объема трудозатрат по ремонту электрической
части оборудования
а) Годовой объём работ по электрической части Nэл, чел-час, вычисляют по формуле
(23)
где åRэ- суммарная ремонтная сложность по электрической части с увеличением на % ;
Кц- коэффициент цикличности по электрической части.
Расчеты выполняются в виде таблицы 9
Таблица 9 - Объём ремонтных работ по электрической части
Количество ремонтных | Текущий ремонт | Средний ремонт | Капитальный ремонт | |||
единиц, åRэ | Кцт | Nэл.т | Кцс | Nэл.с | Кцк | Nэл.к |
1 | 2 | 3 | 4 | 5 | 6 | 7 |
б) Годовой объём трудозатрат по электрической части оборудования Аэл,
чел-час, вычисляют по формуле
(24)
где С – нормы времени на одну ремонтную единицу, час (таблица 5, приложение А)
Расчеты выполняются в виде таблицы 10.
Таблица 10 - Годовой объём трудозатрат по ремонту электрической части оборудования
Виды ремонтов | Объем ремонтных работ по электрической части,Nэл | Трудозатраты, чел-час | |||||
слесарные | станочные | прочие | |||||
С | Аэлсл | С | Аэлст | С | Аэл.пр | ||
1 | 2 | 3 | 4 | 5 | 6 | 7 | 8 |
Текущий | 1,0 | 0,2 | - | - | |||
Средний | 5,0 | 1,0 | 1,0 | ||||
Капитальный | 11 | 2,0 | 2,0 | ||||
Итого | ∑Аэл. сл | ∑Аэл. ст | ∑Аэл.пр |
2.8.4 Определение численности электрослесарей
а) Число электрослесарей ремонтной бригады nэл сл, кол, вычисляют по
формуле
(25)
где ∑Аэл.сл – суммарные трудозатраты электрослесарные, чел-час.
Принимается определенное количество человек.
2.9 Расчет и выбор оборудования ремонтно-механического цеха (РМЦ) или
ремонтно-механической мастерской (РММ)
Расчеты выполняются по данным преддипломной практики по ремонтно-механическому цеху или мастерской.
2.9.1 Определение полного объёма станочных работ
а) Полный объем станочных ∑Аст.пол, чел-час, вычисляют по формуле
(26)
где ∑Аст - трудозатраты суммарные станочные ремонтной бригады, чел-час (таблица 7);
∑Адеж.ст–трудозатраты суммарные станочные бригады технадзора, чел-час(пункт 2.7.2.1, б);
∑Аэл.ст- трудозатраты суммарные станочные электрослесарей ремонтной бригады, чел-час (таблица 10)
б) Число металлорежущих станков Сст.см, станко-смен., вычисляют по формуле
(27)
где Д – число рабочих дней в году, кол (принимается по данным преддипломной практики);
К - коэффициент загрузки оборудования, К = 0,86 – 0,95;
Ф–номинальная продолжительность смены, час.
Далее следует полученное количество станков распределить по типам в рекомендуемом процентном отношении (по рекомендации Единой системы ППР) к общему количеству:
- токарные 45 - 50%
- строгальные 20 - 25%
-фрезерные 20 - 25%
-сверлильные 5 - 10%
2.9.2 Числометаллорежущих станков по каждому типу Пст, кол., и коэффициент их загрузки Кз, вычисляем по формулам 28, 29
(28)
(29)
где п – число принятых станков, кол;
m – число смен работы РМЦ или РММ, принимается по данным предприятия.
На основании расчетов составляется ведомость оборудования РМЦ или РММ по примеру таблицы 11
Таблица 11 - Ведомость оборудования РММ
Наименование оборудования | Коли-чест во | Марка | Технологическая характеристика | Габариты, мм | Установленная мощность кВт | |
Длина | Ширина | |||||
1 | 2 | 3 | 4 | 5 | 6 | 9 |
Станок токарно-винторезный | 1 | 16К20 | ВЦ 200 РМЦ710 | 2085 | 1328 | 7,5 |
Станок фрезерный универсальный | 1 | 6Б82 | Стол 300х1250 | 2500 | 2000 | 4,3 |
Станок поперечно-строгальный | 1 | 736 | Ход ползуна 650 | 2830 | 1500 | 4,5 |
Станок вертикально-сверлильный | 1 | 2А125 | Dmax =25 | 980 | 825 | 2,8 |
Вспомогательное оборудование | ||||||
Станок настольно-сверлильный | 1 | НС-12 | Dmax=12мм | 730 | 355 | 0,6 |
Приводная ножовка | 1 | Р2 | Dmax=200 мм | 2110 | 1000 | 5,8 |
Станок заточной | 1 | 3633 | Круг D=300 мм | 595 | 540 | 2,5 |
Ручной пресс | 1 | - | - | 600 | 600 | - |
Кран балка | 1 | Тип 05/2185 | Грузоподъемн До 1 т | 12000 | - | 2,4 |
Итого | 8 | 30,4 |
Примечание –по теме «Проект организации технического обслуживания и системы ППР для технологического оборудования» наименование, количество, марка оборудования принимается по данным предприятия
С учётом оборудования вспомогательных участков РМЦ (РММ), установленную мощность увеличивается на 30%.
Nу = 30,4 * 1,3 = 39,53 кВт
2.9 Расчёт и подбор штата РМЦ ( РММ)
На основании расчётов численности ремонтного персонала и бригады технадзора, с учётом выбранного металлорежущего оборудования и его загрузки, составляется предварительная сводная ведомость штата рабочих РММ или РМЦ.
2.9.1 Разработка сводной ведомости штата рабочих выполняется в виде таблицы 12
Таблица 12 – Штат рабочих РМЦ (РММ)
Наименование профессий | Расчетный годовой объем трудозатрат, чел-час | Количество человек | Тарифный разряд | Принятый объем трудозатрат ∑Апр, чел-час | Примечание |
1 | 2 | 3 | 4 | 5 | 6 |
Токарь |
∑Аст.пол | 1 | V | 4 * Тр | Приняты с выполнением сверлильных работ |
Фрезеровщик | 1 | IV | |||
Строгальщик | 1 | IV | |||
Слесарь-ремонтник | ∑Асл | 1 | VI | 6 * Тр | |
Слесарь-ремонтник | 2 | V | |||
Слесарь-ремонтник | 2 | IV | |||
Слесарь-ремонтник | 1 | III | |||
Сварщик | Асв | 1 | VI | 2 * Тр | Приняты с выполнением кузнечных работ |
Сварщик | 1 | V | |||
Жестянщик | Ажес | 1 | VI | 1 * Тр | |
Кузнец | Акуз | - | VI | Акуз | |
Электрослесарь | ∑Аэл.сл | 1 | VI | 2 * Тр | |
Электрослесарь | 2 | V | |||
Бригада технадзора | |||||
Деж. слесарь | Адеж.сл | 1 | VI | 1 *Тр | |
Деж. электрослесарь | Адеж.эл | 1 | V | 1 *Тр | |
Итого | 17 |
2.9.2 Расчёт штата рабочих с разбивкой на текущий и капитальный ремонты и технадзор.
а) Определение процентного соотношения годового объёма слесарных работ на текущий и капитальный ремонты
Процент затрат на капитальный ремонт Х, %, вычисляют по формуле
(30)
Процент затрат на текущий ремонт Z, %, вычисляют по формуле 31
(31)
б) Определение соотношения процента принятого от расчетного объема станочных работ
Процент станочных работ У, %, вычисляют по формуле
(32)
где ∑Аст. пр – принятый объем станочных работ, чел-час.
в) Определение объема станочных работ по технадзору
Годовой объем станочных работ по технадзору ∑Адеж.ст, чел-час, вычисляют по формуле
(33)
где Адеж.ст – объем трудозатрат дежурного станочника, чел-час,
(пункт 2.7.2.1, б)
г) Определение объём станочных работ на текущий и капитальный ремонты
Годовой объем станочных работ на текущий и капитальный ремонты
∑Аст.тек. и кап., чел-час, вычисляют по формуле 34
(34)
д) Определение объёма станочных работ по капитальному ремонту
Годовой объем станочных работ на капитальный ремонт ∑Ас.кап, чел-час, вычисляют по формуле 35
(35)
е) Определение объёма станочных работ на текущий ремонт
Годовой объем станочных работ на текущий ремонт ∑Аст. тек., чел-час, вычисляют по формуле 36
(36)
2.9.3 Разработка уточнённой штатной ведомости рабочих
Уточненная штатная ведомость рабочих выполняется в виде таблицы 13
Таблица 13 – Уточненная ведомость штата рабочих по ремонту и технадзору
Наименование работ | Принятые трудозатраты, чел-час | Годовой фонд, час | Количество человек | Средний тарифный разряд |
1 | 2 | 3 | 4 | 5 |
Продолжение таблицы 13 | ||||
1 | 2 | 3 | 4 | 5 |
Текущий ремонт | ||||
Станочные | ∑Аст. тек |
Тр | ||
Слесарные | ∑Апр * Z | |||
Сварочные | ∑Апр * Z | |||
Жестяницкие | ∑Апр * Z | |||
Кузнечные | ∑Апр * Z | |||
Электрослесарные | ∑Апр * Z | |||
Итого по текущему ремонту | ||||
Капитальный ремонт | ||||
Станочные | ∑Аст.кап |
Тр | ||
Слесарные | ∑Апр * Х | |||
Сварочные | ∑Апр * Х | |||
Жестяницкие | ∑Апр * Х | |||
Кузнечные | ∑Апр * Х | |||
Электрослесарные | ∑Апр * Х | |||
Итого по капитальному ремонту | ||||
Бригада технадзора | ||||
Деж. станочные | ∑Адеж.ст |
Тр | ||
Деж. слесарные | Адеж.сл | |||
Деж.электрослесарные | Адеж.эл | |||
Итого по технадзору | ||||
Всего |
2.9.4 Расчет численности руководителей, служащих и специалистов
Численный состав руководителей, служащих и специалистов принимается в зависимости от количества ремонтного персонала, данных предприятия и согласовываются с руководителем. Данные заносятся в таблицу 14
Таблица 14 - Штат ИТР, служащих, МОП
Наименование должность | Количество человек |
1 | 2 |
Механик | |
Мастер | |
Кладовщик | |
Уборщик | |
Итого |
2.10 Расчёт расхода материалов и комплектующих для ремонта и
технического обслуживания оборудования
В этом подразделе необходимо рассчитать расход основных материалов и комплектующих изделий на ремонт и техническое обслуживание.
Наибольшее распространение в ремонте оборудования находят: чугун, сталь, цветные металлы.
а) Годовой расход материаловQ, кг, вычисляют по формуле
(37)
где Х – коэффициент, учитывающий расход материалов на осмотры и межремонтное обслуживание, Х = 1,15;
Нi – норма расхода материалов на 1 ЕРС при капитальном ремонте, кг( таблица 17);
J - коэффициент, характеризующий соотношение между количеством материала, расходуемым при среднем и капитальном ремонтах;
R - коэффициент, характеризующий соотношение между количеством материала, расходуемым при текущем и капитальном ремонтах ;
сумма ремонтных единиц оборудования, подвергаемого в течении года капитальному, среднему и текущему ремонтам, ЕРС, (таблица 5)
Значения Нi, J, R принимаются по таблице 15
Таблица 15 –Значение коэффициентов и норм расхода основных материалов
Материалы | Hi | J | R |
1 | 2 | 3 | 4 |
Чугунное литье | 4,0 | 0,5 | 0.15 |
Сталь углеродистая | 10,2 | 0,6 | 0.2 |
Сталь легированная | 5,5 | 0,6 | 0,2 |
Стальное литье | 0,28 | 0,6 | 0.15 |
Бронзовое литье | 0,38 | 0,7 | 0.3 |
Сталь конструкционная | 8,7 | 0.6 | 0.2 |
Расчет выполняется по всем видам материалов, указанных в таблице 15
б) Годовой расход вспомогательных материалов и комплектующих выполняется с учетом установленного технологического оборудования по форме таблицы 16
Таблица 16 – Годовая потребность в материалах и комплектующих изделий
Материалы | Норма расхода на объем ремонтных работ | ||||||||
КР | Nкр | СР | Nср | ТР | Nтр | ТО | Nто | Итого | |
1 | 2 | 3 | 4 | 5 | 6 | 7 | 8 | 9 | 10 |
Сетка латунная, м2 | 0,019 | 0,008 | 0,005 | 0,002 | |||||
Фрикционный материал м2 | 0,019 | 0,003 | 0,002 | 0,001 | |||||
Трубы стальные, кг | 0,874 | 0,331 | 0,184 | 0,101 | |||||
Трубы цветные, кг | 0,027 | 0,012 | 0,006 | 0,003 | |||||
Электроды, кг | 0,532 | 0,202 | 0,112 | 0,061 | |||||
Припой, кг | 0,005 | 0,002 | 0,001 | --- | |||||
Продолжение таблицы 16 | |||||||||
1 | 2 | 3 | 4 | 5 | 6 | 7 | 8 | 9 | 10 |
Ремни клиновые, усл.ед | 0,15 | ---- | --- | 1,1 | |||||
Ремни плоские,м2 | 0,1 | 3 | --- | --- | 1,1 | ||||
Цепи втулочно-роликовые, м | 0,9 | ---- | --- | --- | |||||
Крепежные детали, кг | 0,76 | 0,288 | 0,16 | 0,088 | |||||
Резина листовая, кг | 0,043 | 0,012 | 0,006 | 0,005 | |||||
Фетр, кг | 0,024 | 0,003 | 0,002 | 0,001 | |||||
Набивка пеньковая, кг | 0,047 | 0,013 | 0,006 | 0,005 | |||||
Шнур асбестовый, кг | 0,01 | 0,003 | 0,002 | 0,001 | |||||
Бура, кг | 0,006 | 0,003 | 0,002 | 0,001 | |||||
Паста ГОИ, кг | 0,003 | 0,002 | 0,001 | 0,001 | |||||
Канифоль, кг | 0,005 | 0,002 | 0,001 | 0,001 | |||||
Карбид кальция, кг | 0,038 | 0,011 | 0,005 | 0,004 | |||||
Кислород, м3 | 0,019 | 0,005 | 0,003 | 0,002 | |||||
Сода каустическая, кг | 0,199 | 0,057 | 0,027 | 0,023 | |||||
Клей | 0,004 | 0,002 | 0,001 | 0,001 | |||||
Шланги резиновые, м | 0,1 | --- | --- | --- | |||||
Эмаль, кг | 1,56 | --- | --- | 0,058 | |||||
Шпатлевка,кг | 0,42 | --- | --- | 0,046 | |||||
Грунтовка,кг | 0,53 | --- | --- | 0,058 | |||||
Уайт-спирит, кг | 0,03 | --- | --- | 0,003 | |||||
Нитрорас-творитель, кг | 0,03 | --- | --- | 0,003 | |||||
Текстолит | 0,275 | 0,78 | 0,038 | 0,032 | |||||
Подшипники | 2,0 | - | - | - |
в) Годовой расход смазочных и обтирочных материалов выполняется по форме таблицы 17
Таблица 17 – Годовая потребность в смазочных и обтирочных материалов
Наименование материала | Количество оборудования | Норма расхода на один станок | Годовая потребность |
1 | 2 | 3 | 4 |
Масло индустриальное, кг | 6,7 | ||
Консистентная смазка, кг | 7,5 | ||
Продолжение таблицы 17 | |||
1 | 2 | 3 | 4 |
Моющая паста, кг | 0.3 | ||
Обтирочный материал, кг | 2,0 |
2.11 Расчёт площадей РМЦ (РММ)
2.11.1 Расчет производственных площадей
Расчет площадей ведется в упрощенной форме и включает определение размеров площадей производственных участков, бытовых помещений и размеров здания.
Расчет необходимых площадей производственных участков ведется в зависимости от оборудования, которое учащийся намерен установить с учетом рекомендуемых норм площадей.
Расчет производственных площадей выполняется в виде таблицы 18 с учетом рекомендуемых норм площади на единицу оборудования или рабочее место в квадратных метрах.
Таблица 18 – Расчет производственных площадей РМЦ (РММ)
Наименование оборудования по участкам | Норма площади, метр квадратный | Количество единиц или рабочих мест | Площадь отделения, участка |
1 | 2 | 3 | 4 |
Слесарное отделение | |||
Верстак с тисками | 5,0 | ||
Настольно-сверлильный станок | 5,0 | ||
Поверочная плита | 4,5 | ||
Разметочная плита | 1,5 | ||
Ванна для мойки деталей | 1,0 | ||
Балансировочный станок | 12,0 | ||
Стеллаж для крепежных деталей | 1,0 | ||
Сборочно-разборочный стапель | 10-15 | ||
Заточной станок | 5,0 | ||
Стол дефектовщика | 5,0 | ||
Ручной пресс | 5,0 | ||
Механическая ножовка | 5,0 | ||
Шкаф для инструментов | 2,0 | ||
Итого по отделению | |||
Станочное отделение | |||
Металлорежущие станки | 12-15 | ||
Гидравлический пресс | 5,0 | ||
Стеллаж для деталей | 2,0 | ||
Итого по отделению | |||
Электро-газосварочное отделение | |||
Электросварочный трансформатор | 5,0 | ||
Продолжение таблицы 18 | |||
1 | 2 | 3 | 4 |
Генератор ацетиленовый | до 2,0 | ||
Стол сварщика | до10 | ||
Верстак с тисками | 5,0 | ||
Ящик с песком | 0,24 | ||
Ящик для электродов | 0,12 | ||
Стеллаж для инструментов | 1,2 | ||
Итого по отделению | |||
Кузнечное отделение | |||
Горн кузнечный на два огня | 10,0 | ||
Молот пневматический | 10,0 | ||
Бак закалочный | 1,0 | ||
Ящик для угля | 0,5 | ||
Наковальня | 10,0 | ||
Ящик для песка | 0,3 | ||
Верстак слесарный | 5 | ||
Стеллаж для деталей и инструментов | 1,5 | ||
Печь нагревательная | 5,0 | ||
Итого по отделению | |||
Жестяницкое отделение | |||
Ножницы гильотинные | 5,0 | ||
Трубоотрезной станок | 5,0 | ||
Станок для гибки труб | 5,0 | ||
Верстак для жестяницких работ | 1,2 | ||
Верстак с тисками | 1,2 | ||
Итого по отделению | |||
Электрослесарное отделение | |||
Принимается с учетом 5м2 на одного человека | |||
Инструментальная кладовая | |||
Принимается с учетом 0,8м2 на один металлорежущий станок, но не менее 18м2 | |||
Итого по производственным помещениям | |||
Всего с увеличением на 20 % (главные проходы) |
Примечание- Суммарная площадь по отделениям и участкам округляется до целого числа и принимается кратной 6.
2.11.2 Расчёт площадей бытовых помещений
Состав и оборудование бытовых помещений ремонтных предприятий устанавливается в соответствии со строительными нормами и правилами ССБТ 2.09.02-85 «Производственные задания».
В состав бытовых помещений входят: гардеробные, помещения для приема пищи, умывальные, душевые, уборные, курительные.
Гардеробные для хранения уличной, домашней и рабочей одежды должны приниматься из условий самообслуживания и, предусматривая закрытый способ их хранения, проектироваться в индивидуальных шкафчиках. Для хранения двух различных видов (уличной и рабочей) одежды должны использоваться закрытые двойные шкафы глубиной 50, шириной 40 и высотой 165 см. Количество шкафчиков равно списочному количеству работающих. В верхней и нижней части закрытых шкафов предусматриваются отверстия (решети, сетки) для проветривания. Гардеробные должны быть оборудованы скамьями шириной 0,3 м, располагаемыми у шкафов по всей длине рядов шкафов. Расстояние между рядами шкафов в гардеробных, оборудованных скамьями, должны быть 2м, между крайним рядом и стеной 1,3 м.
Расчёт площади под гардероб производится исходя из расчета на 1 шкафчик принимается 1,0 м2, с учётом проходов.
а) Площадь гардероба Sг, м2, вычисляют по формуле
(38)
где ∑чел – численность рабочих РМЦ, кол.
Душевые размещаются смежено с гардеробными. При душевых должны быть размещены преддушевые для переодевания. Душевые должны быть оборудованы
открытыми кабинами с перегородками из влагостойких материалов высотой 1,6 м не доходящими до плана на 0,2 м.
Количество душевых сеток определяется из расчета 7 человек на сетку. Размер кабины душевой - 0,9 х 0,9 м2 и проход 0,7 м . Таким образом площадь одной сетки составит
Sсет = (0,9 * 0,9) + 0,7 = 1,51 м2
б) Общую площадь душевой Sд, м2, вычисляют по формуле
(39)
где Sсет – площадь одной душевой сетки, м2.
Уборные должны быть на каждом этаже здания. Размеры в плане кабины на 1 унитаз составляет 1,2 *0,9м2. Ширина прохода между двумя рядами кабин 2 метра, а между рядом кабин и стеной 1,3 м.
Количество кабин для:
- 25 человек - 1 кабина;
- 40 человек - 2 кабины;
- 55 человек - 3 кабины;
- 70 человек - 4 кабины.
Так как уборная оснащается умывальниками, то площадь уборной вместе
с умывальниками составляет 5,6 м2 на 1 умывальник и кабину.
в) Общую площадь уборной Sу.об, м2, вычисляют по формуле
(40)
где У – количество уборных, шт.
Курительные следует размещать смежно с уборными или с помещениями для обогревания работающих. Расстояние от рабочих мест до курительных не должно превышать 100 м. Площадь курительной определяется из расчета 0,03 м2на одного работающего, но не менее 9 м2.
г) Общую площадь курительной Sк, м2, вычисляют по формуле 4
(41)
Пункты питания размещаются в бытовых помещениях и должны иметь умывальники из расчета один кран на 50 посадочных мест.
Площадь пункта питания определяем исходя из нормы 1 м2 на 1 человека.
д) Общую площадь пункта питания Sп, м2, вычисляют по формуле 5
(42)
Цеховые конторы располагают в бытовых помещениях и должны быть изолированы от воздушных шумов. Площади помещений принимаются из расчета не менее 3,25 м2 на одного работающего в конторе.
е) Общую площадь конторских помещений Sк. п.., м2, вычисляют по формуле
(43)
где – численность ИТР и МОП, кол.
ж) Полную площадь бытовых помещений ∑Sбыт,. м2, вычисляют по формуле 7
(44)
з) Общую площадь здания Sобщ., м2, вычисляют по формуле
(45)
где ∑Sпр - суммарная площадь производственных помещений, м2 (таблица 18);
∑Sбыт – суммарная площадь бытовых помещений, м2.
Полученная расчетная площадь служит для определения строительных размеров здания. Для этого задаемся шириной здания (пролетом) кратно 6 м. Рекомендуемая ширина пролета принимается 12, 18, 24, 30, 36 м.
и) Длину цеха L, м2, вычисляют по формуле
(46)
где В – принятая ширина здания, м
Полученная расчетная длина здания округляется кратной 6 м и обычно составляет18, 24, 30, 36, 42, 54 и 60 м. С учетом установки в цехе или мастерской мостового крана или кран-балки принимается высота:
- при установке мостового крана Н = 12,6 м;
- при установке кран-балки Н = 6 м.
Далее даются окончательные размеры здания:
- длина – L = м.
- ширина – В = м.
- высота – Н = м.
- площадь - S = м2
2.12 Расчет годового графика планово-предупредительного ремонта на год
Расчет и разработка годового графика ППР производится для оборудования технологического цеха своего предприятия.
Годовой график ППР должен обеспечивать выполнение структуры ремонтных циклов с соблюдением межосмотровых и межремонтных периодов при ритмичной загрузке ремонтной бригады от месяца к месяцу в разрезе года. Неритмичность загрузки ремонтной бригады не должна превышать 5%.
а) Вилку слесарных трудозатрат в месяц Асл.мес., чел-час, вычисляют по формуле
(47)
где 12 – число месяцев в году, кол.;
% - процент увеличения ЕРС.
б) Минимальное Асл.мин, чел-час, и максимальное Асл.мах, чел-час, значения вилки слесарных трудозатрат вычисляют по формулам 48, 49
, (48)
(49)
Принимается вилка месячного объёма слесарных трудозатрат в пределах
от Асл.мин. до Асл.мах
в) Число мероприятий из структуры ремонтного цикла для каждой группы оборудованияп, кол., вычисляют по формуле
(50)
где ∑М - суммарное число мероприятий за ремонтный цикл по каждой группе оборудования, кол., (таблица 3).
г) Число капитальных mкап, кол., и средних mср, кол., ремонтов для каждой группы оборудования вычисляют по формулам 51, 52
, (51)
(52)
где ∑iст – суммарное число станков по каждой группе оборудования, кол., (таблица 2)
Простои планируем только для капитальных и средних ремонтов. Нормативы простоев представлены в таблице 19
Таблица 19 – Нормативы продолжительности простоев оборудования в ремонте
Ремонтные операции | Нормативы простоя на 1 ремонтную единицу в сутках при работе ремонтной бригады | ||
в 1 смену | в 2 смены | в 3 смены | |
1 | 2 | 3 | 4 |
Средний ремонт | 0,6 | 0,38 | 0,25 |
Капитальный ремонт | 1,0 | 0,54 | 0,41 |
3 Энергетическая часть
В этой части учащийся должен произвести расчет основных тепло-и
энергозатрат в РММ или РМЦ
3.1 Расчет расхода электроэнергии
3.1.1 Расчет расхода электроэнергии на оборудование
Потребность в силовой электроэнергииNс, кВт*час, вычисляют по формуле
(53)
где Nу–общая установленная мощность оборудования, кВт*час. (таблица 11);
Т - время работы оборудования в год, час;
Кз - коэффициент загрузки оборудования, (Кз = 0,3 – 0,5);
h - 1,05 – коэффициент, учитывающий потери в сети (h = 1,06 – 1,07).
Время работы оборудования в году Т, час, вычисляют по формуле 54
(54)
где Ф – номинальная продолжительность смены, час.
m- сменность работы оборудования, кол;
Д – число рабочих дней в году, кол.
3.1.2 Расчет расхода электроэнергии на освещение
Потребность в осветительной энергииNо, кВт*час, вычисляют по формуле
(55)
где S- общая площадь РМЦ или РММ, м2;
Тл- время работ ламп в году, при односменной работе – 1000 часов, при двухсменной – 3200 часов, при трехсменной – 4100 часа;
Но - норма освещённости, кВт/м2 (Но = 0,018);
К - коэффициент использования осветительной нагрузки ( К =0,8);
h- коэффициент, учитывающий потери в сети (h = 1,03)
3.2 Расчет потребности в воде на бытовые нужды
Потребность в водеQв, литр, вычисляют по формуле
(56)
где Z – наибольшее число рабочих, кол;
Д - число рабочих дней в году ;
В1 – годовой расход воды для пользования умывальниками и туалетами на одного человека, л (25);
В2 – годовой расход воды на душевые на одного человека, л (40)
3.3 Расчет расхода сжатого воздуха
Сжатый воздух используется в ремонтном производстве на слесарном участке для обдувки деталей, на пневматических подъемниках, пневматических зажимах, ручном пневмаинструменте, в металлизационных участках и т. д.
Годовой расход сжатого воздуха Qсж, м3, вычисляют по формуле
(57)
где q – расход сжатого воздуха потребителями при их непрерывной работе, м3/час, (таблица 1, приложение Б);
К1 – коэффициент использования, учитывающий фактическую загрузку пневмаоборудования, (таблица 1, приложение Б);
К2 – коэффициент одновременности, при количестве потребителей сжатого воздуха п ≤ 4 К2 = 0,9, при п = 5 – 9 К2 = 0,8, при п = 10 – 14 К2 = 0,7;
3.3 Расчет расхода пара на отопление
Годовой расход пара на отопление D, т, вычисляют по формуле
(58)
где Q – расход тепла , ккал/час;
in- теплосодержание пара , ккал/кг, ( in = 630 -640);
t – время работы отопления за год, час.
В нерабочее время температура помещения понижается, вентиляция не работает и расход пара уменьшается. Ориентировочно расход тепла в нерабочее время принимается в количестве 50 % от расхода в рабочее время.
Расход тепла на отопление в рабочее Qр, и нерабочее Qнр, ккал/час, вычисляют по формулам 59, 60
(59)
(60)
где tд – продолжительность рабочего дня, час, ( при работе в 2 смены tд = 20);
V – объем здания РМЦ или РММ, м3.
Время работы отопления за год в рабочее tр, и нерабочее tнр, час., время вычисляют по формулам 61, 62
(61)
(62)
где tсм – продолжительность смены, час, (при работе в 2 смены tсм = 16);
210 – продолжительность отопительного сезона, дней;
60 – среднее число выходных дней, кол.;
24 – число часов работы отопительной системы, час.
Общий расход пара за год Dо, Гкал, вычисляют по формуле
(63)
где Dр – расход пара на отопление за год в рабочее время, т;
Dнр – расход пара на отопление за год в нерабочее время, т.
4 Энерго- и ресурсосбережение в РМЦ или РММ
Раздел разрабатывается в соответствии с Директивой Президента Республики Беларусь от 14 июня 2007 года №3 “Экономия и бережливость – главные факторы безопасности государства”, постановлением Совета Министров Республики Беларусь от 30.05.2007 №701 “Об утверждении программы мер по экономии энергоресурсов и денежных средств” и постановлением совета Министров Республики Беларусь от 30 июля 2007г. №972 “О некоторых мерах по реализации Директивы президента Республики Беларусь” от 14 июня 2007г. №3.
В современных условиях всё возрастающий эффект экономии топливно-энергетических ресурсов достигается путём проведения различных экономико-организационных мероприятий на ремонтных предприятиях.
Рассмотрим основные направления экономии электроэнергии в ремонтно-механических цехах и мастерских:
- совершенствование и рационализация технологических процессов потери электроэнергии, вызванные нерациональной технологией и организацией производства, в ряде случаев могут превышать потери энергетических процессов и даже полезный расход энергии. Так, в ремонтных предприятиях индукционного способа термообработки деталей и закалки их токами высокой частоты вместо термообработки в печах сопротивления позволяет в 2-3 раза сократить расход электроэнергии;
- внедрение прогрессивных технологических режимов и методов работы оборудования. Сюда следует отнести повышение скорости резания на станочном оборудовании, сокращение числа припусков при прокате, введение оптимальных температурных режимов при электронагреве, термообработке металлов. Исследования показывают, что увеличение скорости резания на станках с 50 до 200 м/мин снижает расход электроэнергии на 17 %, а применение скоростных плавок при оптимальном режиме в сочетании с организационными мероприятиями на 20-30 % сокращает удельный расход электроэнергии;
- улучшение качественных характеристик используемого оборудования. Анализ энергобалансов электротермических печей, которые являются самыми энергоёмкими электроустановками показывает, что потери теплоты через поверхность составляют около 48 % от всей потребляемой электроэнергии. Соответственно резервы экономии здесь чрезвычайно велики;
- совершенствование конструкций промышленных зданий и сооружений. Опыт зарубежной энергетики показывает, что только за счёт применения таких очевидных мероприятий, как усиление теплоизоляции зданий, устройство уплотняющих окон и дверей, рациональное сокращение площади окон и т.д., можно значительно снизить (до 50%) потребление энергии на отопление и кондинцирования промышленных зданий и сооружений;
- внедрение прямого технологического использования электроэнергии. Наибольший эффект от применения электроэнергии достигается в том случае, когда электроэнергия используется непосредственно на выполнение технологической операции;
- уменьшение объёма металла, спиленного при обработке. В результате замены механической обработки ковкой и штамповкой, а также точным литьём за счёт уменьшения обработки резанием удельный расход электроэнергии сокращается на 15-20%. Согласования мощности двигателей станков только по их номинальным нагрузкам недостаточно. При согласовании необходимо учитывать режим работы и характеристики двигателя и привода. Приуменьшения нагрузки снижается КПД электродвигателя и рабочей машины и увеличивается расход электроэнергии;
- замена асинхронных двигателей синхронными. Это мероприятие может осуществляться без предварительных технико-экономических расчётов. Основными достоинствами синхронных двигателей, кроме выдачи в сеть реактивной мощности, являются более высокий КПД (по сравнению с асинхронными) на 1-3% выше и меньшая чувствительность к изменению напряжения в сети;
- установка ограничителей холостого хода на станках всегда оправдана экономией электроэнергии, если по технологической операции время составляет 10 с и более;
Для экономии ресурсов на деревообрабатывающих предприятиях следует применять более рациональные формы организации ремонтного производства и прогрессивные методы ремонта технологического оборудования. Большое значение при этом уделяется технической базе ремонтного производства. Для получения экономической эффективности капитального ремонта необходима сравнительная характеристика двух вариантов: покупка нового оборудования, или же восстановление имеющегося оборудования.
Снижение энергопотребления возможно также и при эксплуатации ремонтно-механических цехов и мастерских. Построенные за последние 30-40 лет здания из-за существующих до недавнего времени низких цен на топливо и электроэнергию, не стимулирующих их экономию, имеют низкую энергоэффективность. Потеря тепла через ограждающие конструкции зданий достигает 80% от общих потерь.
Основными мероприятиями по снижению энергопотребления существующими промышленными зданиями являются:
- перепланировка помещений для их рационального использования с учетом номенклатуры и объемов выпускаемой продукции, исключение из пользования излишних площадей зданий;
- установка приборов учета и контроля потребления тепловой энергии
- усовершенствование систем вентиляции (обогрев, душирование непосредственно рабочих мест);
- изменение режимов отопления зданий;
- децентрализация отопления с установкой котлов малой мощности непосредственно в цехе;
- максимальная утилизация вторичных энергоресурсов;
- использование в качестве топлива отходов производства и местных видов топлива (дрова, торф и др.);
- уменьшение теплопроводности ограждающих конструкций (стен, кровли, окон);
- уменьшение площади остекления и доведение ее величины до оптимальной, увеличение количества слоев остекления и др. (теплопотери через прозрачные конструкции составляют 30-35%, поэтому их совершенствование с целью уменьшения потерь тепла имеет большое значение);
- замена П-образных светоаэрационных фонарей на зенитные
- применение эффективного оборудования для освещения зданий;
- утепление (закладка) ворот, использование которых не требуется по действующей технологии;
- отказ или сокращение использования мостовых кранов большой грузоподъемности, переход на напольные виды транспорта;
- совершенствование технологии производства;
- увеличение единичной мощности агрегатов;
- использование проектной мощности тепловых агрегатов;
- рациональное использование холодной и горячей воды;
- замена устаревшего оборудования в котельных на автоматизированные котлы малой мощности;
- совершенствование тепловых сетей путем улучшения теплоизоляционного покрытия теплопроводов;
- снижение потерь тепла за счет сокращения длины наружных теплотрасс;
- применение систем отопления с газовыми инфракрасными излучателями.
Применение рациональных форм организации ремонтного производства и прогрессивных методов ремонта технологического оборудования даёт значительный экономический эффект.
Общие затраты на техническое и ремонтное обслуживание включает в себя заработную плату, стоимость основных материалов, комплектующих изделий и накладные расходы. Экономия средств при ремонте возможна за счёт экономии и жёсткого учёта расхода комплектующих сменяемых деталей для ремонта и технического обслуживания, а также применения более современных методов ремонта.
5 Охрана труда и окружающей среды
Учащиеся выполняют дипломные проекты на основе общих указаний руководителя проекта при обязательном использовании во всех разделах проектов требований ОТ, системы стандартов безопасности труда, стандартов системы управления ОТ, системы стандартов пожарной безопасности, строительных, санитарных норм и правил, других нормативно-правовых документов. Ответственность за принятые решения в дипломных проектах несет автор этих работ - дипломник. Непосредственное руководство дипломным проектированием осуществляет руководитель проекта, а консультации по вопросам ОТ проводит консультант – преподаватель ОТ.
С учетом темы дипломного проекта дипломника консультант может выделить для углубления проработки наиболее важные вопросы безопасности труда за счет сокращения или исключения других вопросов из раздела «Охрана труда и окружающей среды».
Рекомендуется следующий примерный перечень вопросов по охране труда и окружающей среды, которые должны быть разработаны в дипломном проекте:
1 Правовые, нормативные и организационные вопросы охраны труда.
2 Требования охраны труда к устройству и содержанию предприятий.(для темы ДП «Проект РММ).
3 Требования безопасности при ремонте
4 Требования безопасности при монтаже
5 Обеспечение электробезопасности.
6 Соблюдение производственной санитарии.
6.1 Нормализация параметров микроклимота, чистоты воздушной среды в производственном помещении.
6.2 Освещение производственных помещений.
6.3 Защита от шума, инфразвука, ультразвука и вибрации.
6.4 Защита от воздействия производственных излучений.
6.5 Средства коллективной и индивидуальной защиты.
7 Обеспечения пожарной безопасности
8 Обеспечение охраны окружающей среды
При раскрытии составных частей раздела «Охрана труда и окружающей среды» дипломник должен руководствоваться новейшими строительными нормами и правилами (СНиП), обеспечить здоровые и безопасные условия труда для рабочих-ремонтников всех специальностей.
6 Экономическая часть
6.1 Производственная программа
Производственная программа определяется количеством ремонтных единиц оборудования подлежащего обслуживанию и ремонту.
Баланс времени одного рабочего составляется на основании данных предприятия и представлен в виде таблицы 20
Таблица 20 – Баланс рабочего времени одного рабочего на год.
Показатели | По плану на год |
1 | 2 |
Календарный фонд времени, дней | |
Количество нерабочих дней, всего | |
в том числе: праздничных | |
выходных | |
Номинальный фонд времени в днях | |
Неиспользованныедни,всего | |
в том числе: очередные и дополнительные отпуска | |
прочие неявки, разрешенные законом | |
учебные | |
по болезни | |
сразрешенияадминистрации | |
простои, прогулы | |
Число рабочих дней в году | |
Неиспользованноевремязасмену | |
Номинальная продолжительность смены в часах | |
Фактическая продолжительность рабочей смены в часах | |
Эффективный фонд времени одного рабочего в год, в часах |
Часовые тарифные ставки рабочих представлены в таблице 20
Таблица 20 - Часовые тарифные ставки
Разряд | Тарифный коэффициент | Часовая тарифная ставка, руб | Часовая тарифная ставка при вредности %, руб. |
1 | 2 | 3 | 4 |
I | |||
II | |||
III | |||
IV | |||
V | |||
VI |
6.2 Расчет годового фонда заработной платы
6.2.1 Расчет годового тарифного фонда зарплаты рабочих
Расчет тарифного фонда зарплаты выполняется в виде таблицы 21
Таблица 21 - Тарифный фонд зарплаты ремонтных рабочих и рабочих по
технадзору
Наименование работ | Трудо-емкость, чел-час | Списоч-ное число рабо-чих | Средний разряд | Часовая тарифная ставка, руб | Тарифный фонд зарплаты, тыс.руб. |
1 | 2 | 4 | 5 | 6 | 7 |
Текущий ремонт | |||||
Станочные | |||||
Слесарные | |||||
Сварочные | |||||
Жестяницкие | |||||
Кузнечные | |||||
Электрослесарные | |||||
Итого по текущему ремонту | |||||
Капитальный ремонт | |||||
Станочные | |||||
Слесарные | |||||
Сварочные | |||||
Жестяницкие | |||||
Кузнечные | |||||
Электрослесар ные | |||||
Итого по капитальному ремонту | |||||
Деж. станочные | |||||
Деж. слесарные | |||||
Деж.электрослесарные | |||||
Итого по технадзору | |||||
Всего |
6.2.2 Расчет годового фонда заработной платы
а) Расчет годовой фонд заработной платы рабочих выполняется в виде таблицы 22
б) Расчет годовой фонд заработной платы руководителей, специалистов, служащих выполняется в виде таблицы 23
Таблица 23 - Расчёт годового фонда зарплаты руководителей,служащих, МОП
Наименование должностей | Количество человек | Должностной оклад в месяц, тыс.руб. | Годовой фонд зарплаты, тыс.руб |
1 | 2 | 3 | 4 |
Руководители и специалисты | |||
Механик | |||
Мастер | |||
Итого | |||
Служащие | |||
Кладовщик | |||
Итого | |||
МОП | |||
Уборщик | |||
Итого | |||
Всего |
6.3 Расчет годового фонда премий и других выплат выполняем
Расчет годового фонда премий и других выплат выполняется в виде таблицы 24
Таблица 24 - Расчёт премий и других выплат из единого фонда оплаты труда
Категория | Тарифный фонд | Выплаты из единого фонда | |
работающих | зарплаты, тыс.руб. | % | тыс.руб. |
1 | 2 | 3 | 4 |
Рабочие по ремонту | |||
Рабочие по технадзору | |||
Итого | |||
Руководители и специалисты | |||
Служащие | |||
МОП | |||
Итого | |||
Всего |
Примечание - Премии к тарифному фонду зарплаты в процентном отношении принимаются по данным предприятия.
6.3 Расчёт стоимости материалов и комплектующих
а) Расчет стоимости металлов
Расчет стоимости металлов выполняется в виде таблицы 25
Таблица 25–Расчет стоимости металлов
Наименование | Един.изм. | Годовая потребность | Цена, тыс. руб. | Сумма, тыс.руб. |
Продолжение таблицы 25 | ||||
1 | 2 | 3 | 4 | 5 |
Чугунное литье | ||||
Сталь углеродистая | ||||
Сталь легированная | ||||
Стальное литье | ||||
Бронзовое литье | ||||
Сталь конструкционная | ||||
Итого |
б) Расчет стоимости вспомогательных материалов и комплектующих
Расчет стоимости комплектующих выполняется в виде таблицы 26
Таблица 26 - Стоимость вспомогательных материалов и комплектующих
Наименование | Един.изм. | Цена, руб. | Количество | Сумма, тыс.руб. |
1 | 2 | 3 | 4 | 5 |
Итого |
в) Расчет стоимости запасных частей
Стоимость запасных частей на год Сзап, тыс. руб., выполняют по формуле
(64)
где Ц – стоимость запчастей на 1 ЕРС, тыс. руб.
г) Расчет стоимости смазочных и обтирочных материалов
Расчет стоимости смазочных и обтирочных материалов выполняется в виде таблицы 27
Таблица 27 - Стоимость смазочных и обтирочных материалов
Наименование | Един.изм. | Цена, тыс.руб. | Количество | Сумма, тыс.руб. |
1 | 2 | 3 | 4 | 5 |
Масло индустриальное | ||||
Консистентная смазка | ||||
Обтирочный материал | ||||
Моющая паста | ||||
Итого |
д) Расчет общих затрат на материалы и комплектующие
Общие затраты на материалы и комплектующие выполняются в виде таблицы 28
Таблица 28 - Стоимость запчастей, метизов, металлов, смазочных материалов
Наименование | Сумма, тыс.руб. |
1 | 2 |
Металлы | |
Вспомогательные материалы и комплектующие | |
Запасные части | |
Смазочные и обтирочные материалы | |
Итого | |
Дополнительные расходы 7% (доставка, хранение) | |
Всего |
6.4 Расчёт стоимости оборудования, здания, амортизационных отчислений
а) Расчет стоимости оборудования РМЦ (РММ)
Расчет стоимости оборудования выполняется в виде таблицы 29
Таблица 29 - Стоимость оборудования РМЦ (РММ)
Наименование | Марка | Кол-во | Цена, тыс.руб. | Сумма, тыс.руб. | |
1 | 2 | 3 | 4 | 5 | |
Станок токарно-винторезный | 16К20 | 1 | |||
Станок фрезерный универсальный | 6Б82 | 1 | |||
Станок поперечно-строгальный | 736 | 1 | |||
Станок вертикально-сверлильный | 2А125 | 1 | |||
Итого | |||||
Вспомогательное оборудование | |||||
Станок настольно-сверлильный | НС-12 | 1 | |||
Приводная ножовка | Р2 | 1 | |||
Станок заточной | 3633 | 1 | |||
Ручной пресс | - | 1 | |||
Кран балка | Тип 05/2185 | 1 | |||
Итого | |||||
Всего | |||||
Неучтенное оборудование (30%) | |||||
Транспортные расходы (7%) | |||||
Расходы на монтаж (20%) | |||||
Всего по РМЦ (РММ) | |||||
Примечание- Стоимость оборудования РМЦ(РММ) определяется по данным предприятия и с учетом данных таблицы 11.
б) Определение стоимости здания РМЦ (РММ)
При выполнении дипломного проекта на тему: « Проект (реконструкция) ремонтно-механического цеха или мастерской деревообрабатывающего предприятия» необходимо рассчитывать ориентировочную стоимость затрат на постройку здания.
При выполнении дипломного проекта на тему: «Проект организации технического обслуживания и системы ППР для технологического оборудования» в расчетах принимается балансовая стоимость здания.
Стоимость здания РМЦ (РММ) Сзд, тыс. руб., вычисляется по формуле
(65)
где V - объём здания, м3
Ц - стоимость строительства 1 м3 здания, тыс. руб.
в) Расчет амортизационных отчислений
Амортизационные отчисления определяем в виде таблицы 30
Таблица 30 - Амортизационные отчисления по РММ (РМЦ)
Типы основных фондов | Стоимость, тыс.руб. | Амортизационные отчисления | |
% | тыс.руб | ||
Здание Оборудование | 2 5 | ||
Итого |
6.5 Расчет стоимости электроэнергии, воды, сжатого воздуха и пара
а) Расчет стоимости силовой электроэнергии
Стоимость силовой электроэнергии Ссил, тыс. руб., вычисляют по формуле
(66)
где Nс – годовая потребность в силовой электроэнергии, кВт*час;
Ц – стоимость 1 кВт*час силовой электроэнергии, руб.
б) Расчет стоимости осветительной электроэнергии
Стоимость осветительной электроэнергии Сосв, тыс. руб., вычисляют по формуле
(67)
где Nо – годовая потребность в осветительной электроэнергии, кВт*час;
Ц – стоимость 1 кВт*час осветительной электроэнергии, руб.
в) Расчет общей стоимости электроэнергии
Общая стоимость электроэнергии Собщ, тыс. руб., вычисляют по формуле
(68)
г) Расчет стоимости воды
Стоимость воды Св, тыс. руб., вычисляют по формуле
(69)
где Qв – годовая потребность в воде на бытовые нужды, м3
Ц – стоимость 1 м3 воды, руб.
д) Расчет стоимости сжатого воздуха
Стоимость сжатого воздуха Ссж, тыс. руб., вычисляют по формуле
(70)
где Qсж – годовой расход сжатого воздуха, м3;
Ц – стоимость 1 м3 сжатого воздуха, руб
е) Расчет стоимости отопления
Стоимость отопления Со, тыс. руб., вычисляют по формуле
(71)
где Dо - общий расход пара на отопление, Гкал;
Ц – стоимость 1 Гкал пара, тыс. руб.
6.6 Составление сметы затрат и технико-экономических показателей
а) Расход по охране труда принимается в размере 4% от заработной платы рабочих
Рох. =Зр * 4 %
Таблица 31 - Смета затрат РММ.
Наименование расходов | Сумма, тыс.руб. |
1 | 2 |
Материалы и запчасти | |
Основная и дополнительная зарплата | |
Охрана труда | |
Отчисления на социальное страхование | |
Отчисления в фонд занятости | |
Чрезвычайный налог | |
Продолжение таблицы 31 | |
1 | 2 |
Амортизация | |
Текущий ремонт (30% от амортизации) | |
Капитальный ремонт (20% от амортизации) | |
Электроэнергия | |
Вода | |
Сжатый воздух | |
Отопление | |
Итого | |
Прочие (5% от итого) | |
Всего |
б) Распределение затрат между видами ремонтных работ
Это распределение производится пропорционально зарплате рабочих по ремонту.
Тарифный фонд зарплаты, всего - 100%
Тарифный фонд зарплаты по текущему ремонту – Х%
Тарифный фонд по текущему ремонту * 100
Хт = -----------------------------------------------------------------
Тарифный фонд зарплаты, итого
Всего затрат РММ - 100%
Затраты на текущий ремонт – Х%
Всего затрат РММ * 100
Хт = ----------------------------------
Хт
Затраты на капиталь = Всего затрат РММ - Затраты на текущий
ный ремонт ремонт
Технико-экономические показатели представлены в виде таблицы 32
Таблица 32 - Технико - экономические показатели
Наименование | Един.изм. | Показатели |
1 | 2 | 3 |
Количество установленных станков | ||
Продолжение таблицы 32 | ||
1 | 2 | 3 |
Количество ремонтных единиц, всего | ЕРС | |
- по механической части | ||
- по электрической части | ||
Средняя ремонтная сложность | ЕРС | |
Списочное число рабочих | кол | |
Численность руководителей, служащих и специалистов | ||
Годовой фонд зарплаты, всего | тыс. руб | |
- рабочих | ||
- руководителей, служащих, специалистов | ||
Премии и другие выплаты, всего | тыс. руб | |
- рабочим | ||
- руководителям, служащим, специалистам | ||
Среднегодовая зарплата с учетом премий | руб | |
- одного рабочего | ||
- одного работающего | ||
Себестоимость ремонтных работ, всего | тыс. руб | |
- по текущему ремонту | ||
- по капитальному ремонту | ||
Расходы на 1 ЕРС, всего | тыс. руб | |
- при текущем ремонте | ||
- при капитальном ремонте |
7 Специальная часть (капитальный ремонт)
7.1 Разработка технологии капитального ремонта
Даётся формулировка капитального ремонта. Приводится перечень выполняемых работ при капитальном ремонте с учетом конкретного станка
7.2 Назначение н техническая характеристика станка.
Указываете технологическое назначение станка и его основные технические данные.
7.3 Устройство и принцип действия станка.
Отражаются основные конструктивные элементы их назначение, а также дается описание работы станка при выполнении своей технологической операции.
7.4 Расчёт трудозатрат на капитальный ремонт.
Для расчета трудоемкости необходимо знать категорию ремонтной сложности станка и норматив трудозатрат.
7.4.1 Трудоемкость слесарных работ при капитальном ремонте Тсл, чел-час, вычисляют по формуле
(72)
где С – норматив трудоемкости при слесарных работах, час, (таблица 3, Приложение А);
R- ремонтная сложность станка по механической части, ЕРС, (пункт 2.3.1).
7.4.2 Трудоемкость станочных работ при капитальном ремонте Тст, чел-час, вычисляют по формуле
(73)
где С – норматив трудоемкости при станочных работах, час, (таблица 3, Приложение А) ;
7.5 Расчет количества суток простоя станка в ремонте и составление графика ремонта
Простой станка в капитальном ремонте рассчитывается в часах и сутках.
а) Простои станка в ремонте Акч, час, вычисляют по формуле
(74)
гдеСо - сменность работы станка, кол.;
Сс - сменность работы слесарей, кол.;
К - число слесарей в ремонтной бригаде, кол.
б) Простой станка в Акс, сут., вычисляют по формуле
где Тсм – количество часов работы слесарей в сутки, час.
в) Составление графика капитального ремонта
График капитального ремонта составляется на конкретный месяц с учетом полученных расчетов и данных предприятия.
График капитального ремонта выполняют по форме таблицы 33
Таблица 33 - Календарный график капитального ремонта станка
Ремонтные операции | Дни | |||||||||||||||||||||||||
1 | 2 | 3 | ||||||||||||||||||||||||
Смены | ||||||||||||||||||||||||||
1 | 2 | 1 | 2 | 1 | 2 | |||||||||||||||||||||
Часы | ||||||||||||||||||||||||||
2 | 4 | 6 | 8 | 2 | 4 | 6 | 8 | 2 | 4 | 6 | 8 | 2 | 4 | 6 | 8 | 2 | 4 | 6 | 8 | 2 | 4 | 6 | 8 | |||
Демонтаж и доставка |
. | |||||||||||||||||||||||||
Разборка | ||||||||||||||||||||||||||
Помывка и очистка | ||||||||||||||||||||||||||
Дефектация | ||||||||||||||||||||||||||
Ремонт столов и корпусов | ||||||||||||||||||||||||||
Ремонт деталей | ||||||||||||||||||||||||||
Ремонт эл. оборудования | ||||||||||||||||||||||||||
Сборка узлов | ||||||||||||||||||||||||||
Сборка станка | ||||||||||||||||||||||||||
Наладка и испытание | ||||||||||||||||||||||||||
Окраска и сдача в эксплуатацию | ||||||||||||||||||||||||||
Примечание - пример заполнения графика капитального ремонта представлен в приложении В
7.6 Составление дефектной ведомости на капитальный ремонт.
Дефектация деталей - важная технологическая операция при ремонте станков. Она определяет степень износа деталей, определяет детали, годные к эксплуатации без ремонта; детали, подлежащие восстановлению, и детали, отправляемые в металлолом. Важным моментом повышения эффективности капитального ремонта является широкое использование изношенных деталей, восстановленных различными методами. Наибольшее распространение получили следующие методы дефектации: визуальный, капиллярный (для обнаружения трещин) и с помощью контрольно-измерительных приборов: штангенциркулей, индикатора, дула, зубомера и т.п.
Далее даются наиболее типичные износы и дефекты деталей деревообрабатывающего станка, технологию ремонта которого разрабатывает дипломник.
На детали следует указать предельно допустимые износы и способы установления фактических износов, например износ зубьев шестерен, посадочных шеек валов, шпонок и т.д.
Дефектная ведомость составляется после окончательной разборки станка поформетаблицы34 (количество дефектов согласовывается с руководителем проекта).
Таблица 34 - Дефектная ведомость на капитальный ремонт станка
Предприятие | Цех | Машина (агрегат) | Вид ремонта | Завод изготовитель | Инвентарный номер | |
| ||||||
Наименование узла и детали | Наименование дефекта | Меры устранения | Потребные запасные части и материалы | Исполнители, разряд | ||
1 | 2 | 3 | 4 | 5 | ||
|
| |||||
Примечание – пример дефектной ведомости представлен в приложении Г
7.7 Составление технологической карты на капитальный ремонт
Технологическая карта на капитальный ремонт составляется на основании дефектной ведомости по форме таблицы 35
Таблица 35 – Технологическая карта капитального ремонта
Наименование работ | Исполнители | Потребные материально-технические ресурсы |
1 | 2 | 3 |
Подготовительные операции | ||
Проверка состояния станка и составления предварительной дефектной ведомости | ||
Подготовка станка к ремонту и подготовка для ремонта материалов, комплектование бригады ремонтников | ||
Демонтаж станка и подготовка к транспортировке на ремонт | ||
Транспортировка станка в цех на разборочную площадку | ||
Ремонтные операции | ||
Разборка станка | ||
Ремонт и регулирование | ||
Сборка станка | ||
Доставка станка к месту установки | ||
Испытание станка и сдача в эксплуатацию |
Примечание – пример технологической карты на капитальный ремонт представлен в приложении Д
7.8 Испытание станка и сдача в эксплуатацию
7.8.1 Испытание станка на холостом ходу
7.8.2 Испытание станка под нагрузкой
7.8.3 Испытание станка на геометрическую точность, жёсткость и уровень шума
7.8.4 Сдача станка в эксплуатацию
При выполнении пункта «Испытание станка и сдача его в эксплуатацию» разрабатываются конкретные операции для своего станка с учётом его назначения и конструкции.
7 Специальная часть (монтаж станка)
7.1 Разработка технологии монтажа станка
Даётся описание основных этапов монтажных работ.
7.2 Назначение и техническая характеристика станка
Указывается технологическое назначение станка и его основные технические данные.
7.3 Устройство и принцип действия станка
Отражаются конструктивные элементы их назначение, а также дается описание работы станка при выполнении своей технологической операции.
7.4 Расчёт фундамента
В зависимости от типа станка необходимо произвести расчёт фундамента по общепринятой методике с определением расчётной схемы, размеров фундамента, статических и динамических нагрузок, а также произвести выбор фундаментных болтов.
7.4.1 Составление расчетной схемы
Этот этап заключается в определении величин и координат точек приложения сил, действующих на фундамент. В общем случае на него действуют статические и динамические силы.
Статические силы возникают от действия масс станка (mст), фундамента (mф) и обрабатываемой детали (mд). К статическим силам также относятся сила натяжения ремней привода Рпр и усилие подачи Рп( если электродвигатель привода и механизма подачи установлены вне станка).
Динамические силы возникают от дисбаланса вращающихся частей станка, а также при возвратно-поступательном движении элементов. Динамические силы для упрощения расчетов приводятся к эквивалентным статическим.
7.4.2 Определение размеров фундамента
К размерам основания добавляем 150-200 мм на каждую сторону.
а) Длину фундамента Lф и ширину Вф, м, вычисляют по формулам 72, 73
(72)
(73)
где Lс – длина станка, мм;
Вс – ширина станка, мм/
б) Массу фундамента mф, кг., вычисляют по формуле
(74)
гдеКн – коэффициент нагрузки: для оборудования, работающего со статическими нагрузками, Кн = 0,6 – 1,5, с динамическими нагрузками Кн = 2 – 3;
mст– масса станка, кг
в) Высоту фундамента Нф, м, вычисляют по формуле
(75)
Высоту фундамента принимают с учетом следующих рекомендаций
7.4.3 Проверочный расчет по статическим нагрузкам
Расчет сводится к определению давления на грунт и сравнения его с допускаемым давлением
а) Давление на грунт системы «Станок-фундамент-деталь» Р, мПа, вычисляют по формуле
(76)
где Gст. – сила тяжести станка, Н;
Gфун. – сила тяжести фундамента, Н;
Gдет.- сила тяжести детали, Н;
S - площадь фундамента,мм2;
[р] – допускаемое давление , МПа , ( 0,15 – 0,3).
б) Силу тяжести G, Н, вычисляют по формуле
(77)
где m – соответственно масса станка, фундамента, детали, кг;
g – ускорение свободного падения, м2/с.
7.5 Разработка технологической карты монтажа
Технологическая карта монтажа выполняется по следующей форме:
Технологическая карта
Таблица 1 – Сведения по предприятию, объекту и работам
Наименование предприятия | Наименование объекта | Наименование работы |
1 | 2 | 3 |
Таблица 2 – График выполнения монтажных работ
Наименование работы | Исполнители | Потребные материально-технические ресурсы | Календарный график (дни) |
1 | 2 | 3 | 4 |
Таблица 3 – Лимит материалов и полуфабрикатов
Наименование и характеристика | Единица измерения | Количество | |
по проекту | по факту | ||
1 | 2 | 3 | 4 |
Таблица 4 – Перечень оборудования, инвентаря и приспособлений
Наименование и характеристика | Единица измерения | Количество | |
по проекту | по факту | ||
1 | 2 | 3 | 4 |
Примечание
– пример оформления технологической карты монтажа представлен в приложении Ж
7.5 Испытание станка и сдача в эксплуатацию
7.5.1 Испытание станка на холостом ходу
7.5.2 Испытание станка под нагрузкой
7.5.3 Испытание станка на геометрическую точность, жёсткость и уровень шума
7.5.4 Сдача станка в эксплуатацию
При выполнении пункта «Испытание станка и сдача его в эксплуатацию» разрабатываются конкретные операции для своего станка с учётом его назначения и конструкции.
Приложение А
Значения коэффициентов Кт и К
Таблица 1 – Коэффициенты точности изготовления оборудования
Группа оборудования | Предельные значения Кт |
1 | 2 |
1 Рамы лесопильные двухэтажные | 1,0 |
2 Рамы лесопильные одноэтажные | 2,0 – 0,66 |
3 Станки ленточнопильные | 1,35 – 0,5 |
4 Станки круглопильные с конвейерной подачей | 1,35 – 1,0 |
5 Станки круглопильные с ручной подачей | 0,66 – 0,24 |
6 Станки торцовочные с механической подачей | 1,0 |
7 Станки маятниковые | 0,5 – 0,24 |
8 Станки строгальные калевочные | 2,0 – 0,66 |
9 Станки фуговальные и рейсмусовые | 1,35 – 0,66 |
10 Станки фрезерные | 2,0 – 1,0 |
11 Станки фрезерные для шипов и проушин | 1,35 – 0,66 |
12 Станки шипорезные | 2,0 – 1,0 |
13 Станки сверлильные | 2,0 – 0,66 |
14 Станки цепнодолбежные | 1,35 – 0,66 |
15 Оборудование прессовое | 1,0 |
16 Станки шлифовальные и полировальные | 1,0 – 0,66 |
17 Оборудование клеильно-сборочное | 2,0 – 1,0 |
18 Станки строгальные | 2,0 – 1,0 |
19 Станки автоматические и полуавтоматические | 2,0 – 1,35 |
20 Станки для подготовки дереворежущего инструмента | 2,0 – 0,5 |
21 Подъемно-транспортное оборудование: | |
подъемники | 0,66 – 0,24 |
рольганги и транспортеры | 0,66 – 0,24 |
прочие приспособления | 0,24 |
Таблица 2 – Значения коэффициента приведения к асинхронному электродвигателю
Диапазон величин суммарной электрической мощности установленных электродвигателей, кВт | К |
1 | 2 |
До 0,60 | |
0,61 – 3,0 | |
3,1 – 5,0 | |
5,1 – 100,0 | |
100,1 – 155,0 | |
155,1 – 215,0 | |
215,1- 240,0 | |
240,1 – 280,0 | |
280,1 – 320,0 |
Таблица 3 – Нормы времени на одну ремонтную единицу
Наименование ремонтных операций | Виды работ | ||
Слесарные | Станочные | Прочие | |
1 | 2 | 3 | 4 |
Осмотр | 1,9 | 0,2 | - |
Текущий ремонт | 5,2 | 1,5 | 0,2 |
Средний ремонт | 9,8 | 4,8 | 0,4 |
Капитальный ремонт | 23,1 | 9,7 | 2,1 |
Таблица 4 - Нормативы межремонтного технического обслуживания на одного
рабочего в ремонтных единицах
Оборудование | Профессии рабочих | |||
Станочники | Слесари | Электрослесаря | ||
1 | 2 | 3 | 4 | |
Д\о оборудование | 1350 | 250 | 350 |
Таблица 5 - Нормы времени на одну ремонтную единицу
Наименование | Наименование ремонтных работ | ||
Текущий ремонт | Среднийремонт | Капитальный ремонт | |
1 | 2 | 3 | 4 |
Электрослесарные | 1,0 | 5,0 | 11,0 |
Станочные | 0,2 | 1,0 | 2,0 |
Прочие | - | 1,0 | 2,0 |
Приложение Б
Таблица 1 Данные расчета потребности в сжатом воздухе
Наименование потребителей | Расход сжатого воздуха одним потребителем, м3/ч | Коэффициент использования, К1 |
1 | 2 | 3 |
Ручной инструмент | 36 - 60 | 0,2 |
Пневмозажимы | 3 - 5 | 0,1 – 0,3 |
Пневмоподъемники | 0,4 на 1 подъем | 0,1 |
Металлизационные участки | 36 -72 | 0,6 – 0,8 |
Сопла для обдувки деталей | 0,15 – 0,85 | 0,1 |
Распылители краски | 12 - 18 | 0,4 – 0,5 |
Пескоструй | 60 - 90 | 0,4 – 0,6 |
Приложение В
Таблица 2 - Календарный график капитального ремонта фуговального станка СФ4-1
Ремонтные операции | Дни | |||||||||||||||||||||||||
1 | 2 | 3 | ||||||||||||||||||||||||
Смены | ||||||||||||||||||||||||||
1 | 2 | 1 | 2 | 1 | 2 | |||||||||||||||||||||
Часы | ||||||||||||||||||||||||||
2 | 4 | 6 | 8 | 2 | 4 | 6 | 8 | 2 | 4 | 6 | 8 | 2 | 4 | 6 | 8 | 2 | 4 | 6 | 8 | 2 | 4 | 6 | 8 | |||
Демонтаж и доставка |
бр. сл. ___бр. сл.___
___бр. сл.____ ____механик ____
__ бр. сл., станочник_
_____ бр. сл., станочник____
_____ бр. эл. сл_____ ______бригада слесарей___
__бр. слесарей _
_бр. сл._
_бр. сл_ механ. | |||||||||||||||||||||||||
Разборка | ||||||||||||||||||||||||||
Помывка и очистка | ||||||||||||||||||||||||||
Дефектация | ||||||||||||||||||||||||||
Ремонт столов и корпусов | ||||||||||||||||||||||||||
Ремонт деталей | ||||||||||||||||||||||||||
Ремонт эл. оборудования | ||||||||||||||||||||||||||
Сборка узлов | ||||||||||||||||||||||||||
Сборка станка | ||||||||||||||||||||||||||
Наладка и испытание | ||||||||||||||||||||||||||
Окраска и сдача в эксплуатацию | ||||||||||||||||||||||||||
Примечание - на разборку станка идет 10-15 % от часов простоя, а на сборку, регулировку и сдачу в эксплуатацию 15-20%
Приложение Г
Таблица 1 - Дефектная ведомость на капитальный ремонт лесопильной рамы
2Р75-2
Предприятие | Цех | Машина (агрегат) | Вид ремонта | Завод изготовитель | Инвентарный номер | |||
ОАО «ФанДОК» | Лесопильный | Рама лесопильная двухэтажная 2Р75-2 | Капитальный | Дзержинский станкостроительный завод | 0526 | |||
Наименование узла и детали | Наименование дефекта | Меры устранения | Потребные запасные части и материалы | Исполнители, разряд | ||||
1 | 2 | 3 | 4 | 5 | ||||
1 Разобрать раму на узлы и детали, промыть и просушить, произвести дефекацию |
|
| ||||||
2 Станина | Трещина в соединительной поперечине | Произвести реставрацию поперечины, заварить и зачистить, произвести выверку | Электроды, сварочная проволока | Слесарь – IIIр. Сварщик – IVр. | ||||
Механизм резания | ||||||||
3 Коленчатый вал | Износ сферических роликовых подшипников | Заменить роликовые подшипники
| Сферические роликовые подшипники №13630 – 2 шт., солидол | Слесарь- IV и V р. | ||||
4 Шатун | Выработка в гнездах подшипника и шатуна | Заменить шатун
| Шатун, солидол | Слесарь- III и IV р. | ||||
5 Пильная рамка | Износ ползунов, выработка в нижней поперечине | Заменить ползуны и нижнюю поперечину | Текстолит на 4 ползуна и нижняя поперечина | Слесарь- III и IV р. | ||||
6.Направляющие пильной рамки | Выработка в виде полос на длине хода пильной рамки | Прострогать, прошлифовать и 2 шт. конусных направляющих заменить | Чугунное литье – 4 шт. конусных и 4 шт. плоских | Слесарь- III р. Строгальщик-Vр | ||||
Механизм подачи | ||||||||
7 Фрикционный диск | Выработка поверхностей | Проточить и проверить диск | Чугунное литье | Слесарь- III р. Токарь -Vр | ||||
8Текстолитовый фрикционный диск | Равномерная выработка диска | Заменить текстолит на диске | Текстолит | Слесарь- III и IV р. | ||||
9 Горизонталь- ный валик | Износ подшипника качения | Заменить подшипник | Шарикоподшипники №13009 | Слесарь- IV и V р. | ||||
Продолжение таблицы 1 | ||||||||
1 | 2 | 3 | 4 | 5 | ||||
10Вертикальный валик посылочного механизма | Износ упорного шарикоподшипника
| Заменить подшипник
| Шарикоподшипник №8211 – 2 шт. | Слесарь- IV и V р. | ||||
11Поддерживающие кронштейны | Поломка кронштейна
| Заменить новыми
| Кронштейн чугунный -2 шт. | Слесарь- III и IV р. | ||||
12 Конические шестерни посылочного механизма | Поломка зубьев
| Выточить новые шестерни
| Шестерни чугунные – 2 шт. | Слесарь- III р. Токарь –Vр Фрезеровщик-Vр | ||||
13 Шестерни подающих вальцов | Срез зубьев шестерен | Нарезать зубья, изготовить новые шестерни | Чугунное литье – 2 шт. | Слесарь- III р. Токарь –Vр Фрезеровщик-Vр | ||||
14 Привод верхних подающих вальцов | Звездочки цепи предельно выработаны | Заменить 4 звездочки и цепь, шаг 35 мм | Сталь, цепь роликовая втулочная | Слесарь- III и IV р. | ||||
15 Направляющие планки цепи, вал кронштейнов передних ворот | Выработка на планке, выработка на шейках вала
| Заварить выработанные места и прострогать, наварить шейки вала и проточить | Электроды | Слесарь –IIIр. Сварщик -IVр. Фрезеровщик-Vр | ||||
16 Валы, кронштейны подающих вальцов | Имеют выработку и обрывы резьбы
| Изготовить новые валы, нарезать резьбу на валах и в кронштейнах | Сталь 5 | Слесарь- III р. Токарь –Vр | ||||
17 Нижние подающие вальцы | Затуплены шипы и рифли | Углубить продольное рифление. Заменить кольца рябух | Чугунное литье – 2 шт. | Слесарь- III р. Строгальщик-Vр | ||||
18 Верхние подающие вальцы | Затупление шипов | Углубить продольное рифление | Чугунное литье – 2 шт. | Слесарь- III р. Строгальщик-Vр | ||||
19 Вал-шестерня | Поломка зубьев | Выточить новый вал-шестерню и профрезеровать зубья | Сталь 45 | Слесарь- III р. Токарь –Vр Фрезеровщик-Vр | ||||
20 Вал замка ворот | Выработка вала
| Наварить и проточить | Электроды | Слесарь –IIIр. Сварщик – IVр. Токарь –Vр | ||||
21Направляющий аппарат | По плоскости ножа выработка | Прострогать ножи
| Резцы токарные | Слесарь- III Строгальщик-Vр | ||||
Продолжение таблицы 1 | ||||||||
1 | 2 | 3 | 4 | 5 | ||||
22 Рычаг с ручкой | Поломка стойки рычагов посылки | Заменить стойку
| Чугун | Слесарь- III и IV р. | ||||
23 Левая и правая тормозные ленты на маховиках | Разрыв ленты тормоза
| Заменить ленту тормоза
| Ленточная сталь | Слесарь- III и IV р. | ||||
24 Вилка переводки | Разработана втулка | Заменить втулки
| Чугун | Слесарь- III и IV р. | ||||
25 Лесорама РД75-2 |
| Собрать и выверить, испытать вхолостую и под нагрузкой | Бр. слесар., мастер, механик | |||||
Приложение Д
Таблица 1 - Технологическая карта капитального ремонта фуговального станка СФ4-1
Наименование работ | Исполнители | Потребные материально-технические ресурсы | |
1 | 2 | 3 | |
Подготовительные операции | |||
1 Проверка состояния станка и составление предварительной дефектной ведомости | Механик, мастер и бригадир по ремонту
| Контрольная линейка, щуп, угольник и индикатор, виброметр, тахометр | |
2 Подготовка станка к ремонту и подготовка для ремонта материалов и инструментов, комплектование бригады ремонтников | Механик, мастер и бригадир по ремонту
| На основании дефектной ведомости и технологических карт ремонта | |
3 Демонтаж станка и подготовка к транспортировке на ремонт | Бригадир и слесарь V разряда, слесарь III разряда, электромонтер IV разряда | Домкрат на 1 т. Таль на 1 т. Слесарный инструмент | |
4 Транспортировка станка в цех на разборочную площадку | Слесарь IV и III разряда | Электрокара или автомашина | |
Ремонтные операции | |||
5 Разборка станка: |
| ||
а) снять электродвигатель | Слесарь IV разряда Слесарь III разряда | Подъемник
| |
б) снять и разобрать ограждения, направляющую линейку | Слесарь III разряда | Съемники, выколотки, гаечные ключи Стеллаж для деталей | |
в) разобрать механизмы столов и снять столы | Слесарь III разряда Слесарь IV разряда | Съемники, выколотки, гаечные ключи Стеллаж для деталей | |
г) снять и разобрать ножевой вал с подшипниками | -//- | -//-
| |
6 Очистка, промывка и дефектация деталей | Механик, мастер, бригадир, слесарь III разряда, | Баки для промывки, дефектоскоп, микрометры, штангенциркуль, контрольные линейки, щуп и др., контрольно-измерительныеинструменты | |
7 Ремонт и регулирование: |
| ||
а) подтяжка ослабленных деталей, произвести регулировку соединения | Слесарь IV разряда Слесарь III разряда | Слесарный инструмент, ключи, молотки, зубила, ножовки и др. инструменты | |
б) ремонт деталей зачисткой, осадкой, раздачей | Слесарь V разряда, слесарь IV разряда | Слесарное отделение, слесарный инструмент, верстак, пресс ручной | |
в) ремонт деталей обработкой на новый ремонтный размер или наращиванием | Токарь IV разряда, строгальщик IV разряда, фрезеровщик V разряда, шлифовщик V разряда, сварщик | Станки: токарный, строгальный, фрезерный, сверлильный, шлифовальный. Сварочное отделение: газосварочный аппарат, электросварочный аппарат. | |
Продолжение таблицы 1 | |||
1 | 2 | 3 | |
г) ремонт электрооборудования | Электромонтеры IV и III разрядов | Электромонтажное отделение
| |
д) замена износившихся деталей: подшипников, вкладышей, пальцев | Слесарь IV и III разрядов | Съемники, выколотки, слесарный инструмент, пресс в слесарном отделении
| |
8 Сборка станка: |
| ||
а) собрать и установить ножевой вал | Слесарь V и III разрядов | Слесарный инструмент Бак для нагрева подшипников | |
б) собрать и установить столы с механизмами крепления | Слесарь IV и III разрядов | Слесарный инструмент
| |
в) собрать и установить привод и электрическую часть | Электрослесарь V и III разрядов | Слесарный инструмент
| |
г) собрать и установить ограждения и направляющую линейку | Слесарь III разряда Слесарь IV разряда | Слесарный инструмент
| |
9 Доставка станка к месту установки | Слесарь IV и III разряда | Электрокара или автомашина | |
10 Испытание станка и сдача в эксплуатацию | Слесарь V разряда, бригадир, мастер, механик, нач. цеха | Контрольно-измерительный инструмент | |
Приложение Ж
Технологическая карта монтажа станка
Таблица 1 – Сведения по предприятию, объекту и работам
Наименование предприятия | Наименование объекта | Наименование работы |
1 | 2 | 3 |
ГУО «БГЛК» | Станок ленточнопильный МП-9 | Сооружение фундамента и монтаж станка |
Таблица 2 – График выполнения монтажных работ
Наименование работы | Исполнители | Потребные материально-технические ресурсы | Календарный график (дни) |
1 | 2 | 3 | 4 |
Доставка оборудования | Такелажник V Подсобник IV | Электрокар Автомобиль | 11.02.2013 |
Разметка фундамента | Бригадир, подсобник IV | Отвесы, угольник, струны. | 11.02.213. |
Земляные работы | Землекопы IV Землекоп V | Лопаты, носилки | 12.02.2013 |
Плотничные работы | Плотник V Подсобник IV | Плотничный инструмент | 12.02.2013 |
Бетонные работы | Бетонщик V Подсобник IV | Бетономешалка носилки, лопаты, | 12.02.2013 |
Схватывание фундамента | Бетонщик V Подсобник IV | Шланги, ведра | 12.02-17.02.2013 |
Монтаж станка | Слесарь V Подсобник IV | Слесарный инструмент | 18.02 – 19.02.2013 |
Подливка фундамента | Бетонщик V Подсобник IV | Бетономешалка носилки, лопаты, мастерок | 20.02.2013 |
Схватывание подливки | Бетонщик V Подсобник IV | Шланги, ведра | 20.02-22.02.2013 |
Испытание и сдача станка в эксплуатацию | Механик, электрослесарь, мастер, слесарь | Индикатор, секундомер | 23.02.2013 |
Таблица 3 – Лимит материалов и полуфабрикатов
Наименование и характеристика | Единица измерения | Количество | |
по проекту | по факту | ||
1 | 2 | 3 | 4 |
Гвозди | кг. | 3,0 | |
Доски 3000x300x30 | шт | 20 | |
Бруски 600х30х30 | шт | 30 | |
Бетон | м3 | 3,0 |
Таблица 4 – Перечень оборудования, инвентаря и приспособлений
Наименование и характеристика | Единица измерения | Количество | |
по проекту | по факту | ||
1 | 2 | 3 | 4 |
Электрокар | шт | 1 | |
Автомобиль | шт | 1 | |
Бетономешалка | шт | 1 | |
Слесарный инструмент | комплект | 1 | |
Плотничный инструмент | комплект | 1 | |
Лопата | шт | 2 | |
Уровень | шт | 1 | |
Индикатор | шт | 2 | |
Носилки | шт | 1 | |
Вибратор | шт | 1 | |
Отвесы | шт | 2 |
Дата добавления: 2018-06-01; просмотров: 442; Мы поможем в написании вашей работы! |
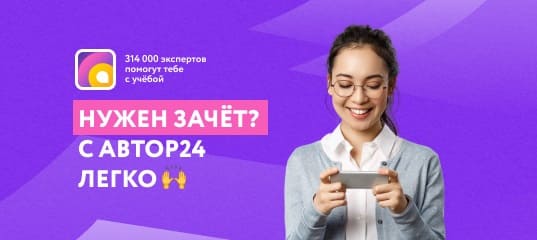
Мы поможем в написании ваших работ!