Максимальная крупность кусков руды для рудообогатительных фабрик( по данным Механобра)
Табл. 3
Производительность фабрики по руде, тыс. т/год | Максимальная крупность кусков, мм | |
Открытые работы | Подземные работы | |
Малая до 500 | 500 – 600 | 250 – 350 |
Средняя 500 – 3000 | 700 – 1000 | 400 – 500 |
Большая 3000 – 9000 | 900 – 1000 | 600 – 700 |
Очень большая > 9000 | 1200 | – |
Число стадий дробления определяется начальной и конечной крупностью дробимого материала.
Наиболее крупная руда получается при открытых работах и большой производительности, а наименее крупная — при подземных работах и малой производительности рудника.
Размер максимального куска руды устанавливается проектом горной части. Ориентировочная зависимость крупности куска от производительности рудника и способа добычи приведена в табл. 3. Крупность максимального куска руды, поступающей на измельчение, определяется возможностями применяемых в последней стадии дробления конусных дробилок мелкого дробления (КМД или «Гидрокон»).
В настоящее время принята оптимальная крупность максимального куска руды, поступающей в отделение измельчения:
для стержневых мельниц 15 – 20 мм
При рудах, легко разрушаемых в начальной стадии измельчения, а также при глинистых и влажных рудах, крупность материала, поступающего в стержневые мельницы, можно увеличить до 20—25 мм.
При заданных размерах максимальных кусков в руде и в дробленом продукте пределы общей степени дробления будут:
|
|
;
,
где S – общая степень дробления; D и d – размеры кусков соответственно в исходной руде и в дробленном продукте, мм.
Общая степень дробления равна произведению степеней дробления в отдельных стадиях. Дробилки крупного, среднего и мелкого дробления позволяют получить за один прием следующие степени дробления:
дробилки крупного дробления — до 5;
конусные дробилки для среднего приема дробления при работе без поверочного грохочения — до 6;
те же, дробилки при работе в замкнутом цикле с поверочным грохотом — до 8;
конусные дробилки мелкого дробления при работе без поверочного грохота — до 3—5;
те же дробилки при работе в замкнутом цикле — до 8.
Минимальная степень дробления Smax = 12,5 не может быть достигнута в одну стадию в дробилке первого приема, поэтому число стадий сухого дробления перед измельчением должно быть не менее двух.
Максимальная степень дробления Smax = 120 может быть получена при трех стадиях дробления, например,
Smax = 120 = 4∙5∙6
Smax = 120 ≈ 4,5∙4,5∙6
Отсюда следует первое правило выбора схемы дробления: число стадий дробления при подготовке руд к измельчению должно равняться двум или трем . ( Это правило относится к установке стандартных щековых и конусных дробилок. Опытные инерционные дробилки института Механобр, молотковые и роторные дробилки дают высокие степени дробления.)
|
|
Исключения из этого правила могут быть сделаны для обогатительных фабрик очень большой (свыше 40—60 тыс. т/сут) производительности, при поступлении на фабрику крепких руд, при дроблении которых получаются куски плитняковой формы (например, типа магнетитовых кварцитов Кривого Рога). В этом случае применяются четырехстадиальные схемы дробления.
Операции предварительного грохочения применяются для сокращения количества материала, поступающего в дробление, (за счет отсева мелочи) и увеличения подвижности материала в рабочей зоне дробилки. Последнее особенно необходимо при дроблении в конусных дробилках среднего и мелкого дробления, подверженных забиванию рудной мелочью.
Введение в схему дробления операций предварительного грохочения вызывает увеличение капитальных затрат и усложняет цех дробления. Поэтому предварительное грохочение следует применять при достаточно высоком содержании отсеваемого класса в исходном материале, а также при высокой влажности этого класса, когда значительно понижается производительность дробилки. В первой стадии при больших размерах выпускной щели (>100 мм) мелкая руда свободно проходит через дробилку и предварительное грохочение имеет значение только для повышения пропускной способности всего узла грохот — дробилка. Поэтому, если дробилка, выбранная по размеру поступающего куска, обеспечивает заданную производительность без установки грохота, то предварительное грохочение не предусматривается. Если же отказ от грохочения предопределяет установку двух дробилок, крупного дробления, то следует остановиться на варианте установки одной дробилки с предварительным грохочением, поскольку установка второй дробилки почти удваивает капитальные затраты на строительство отделения крупного дробления.
|
|
Во второй стадии дробления предварительное грохочение предусматривается в большинстве случаев. Но, если дробилки среднего дробления, связанные с дробилками мелкого дробления, имеют больший запас производительности по сравнению с последними и обеспечивают производительность без отсева мелочи, то предварительное грохочение не предусматривается. При решении этого вопроса следует учесть и свойства руды в отношении влажности и возможной подпрессовки дробилки мелкой рудой.
|
|
В третьей стадии дробления при малых выходных щелях (6—7 мм) предварительное грохочение должно применяться во всех случаях. Вышесказанное подтверждается анализом схем дробления фабрик, построенных после 1965 г. Из 17 фабрик для полиметаллических руд предварительное грохочение перед крупным дроблением применяется только на двух. На фабриках для железных руд большой производительности нет предварительного грохочения перед первой стадией дробления. То же можно сказать и относительно фабрик для медных руд.
Из тех же 17 фабрик для полиметаллических руд предварительное грохочение перед дробилками второй стадии применяется на 10 фабриках. На большинстве фабрик для железных руд предусмотрено предварительное грохочение перед дробилками второй стадии. При этом часто устанавливаются двухситные грохоты, и в подрешетный продукт выводится готовый по крупности продукт (минус 15—20 мм).
Дробилки третьей стадии на современных фабриках работают с предварительным и поверочным грохочением. Эти операции включаются в схемах или раздельно или в совмещенном варианте.
Второе правило выбора схемы:
а) предварительное грохочение перед первой стадией приме-
няется редко и в случае применения требует специального обосно-
вания;
б) предварительное грохочение перед второй стадией, как
правило, предусматривается; отказ от него должен обосновываться;
в) предварительное грохочение перед третьей стадией преду-
сматривается всегда.
Типовые характеристики крупности продуктов дробления необходимы для расчета схем дробления и выбора дробилок и грохотов. Графики типовых характеристик крупности дробленых продуктов щековых и конусных дробилок крупного дробления приведены на рис. 5 и 6.
Здесь по оси абсцисс отложена относительная, т. е. безразмерная крупность зерен z, равная отношению размера зерен к ширине выходной щели дробилки: z = d : i, а по оси ординат – содержание классов крупнее z – слева и мельче z – справа.
Графики составлены дляусловий, когда в дробление поступает материал, не содержащий зерен размером менее ширины выходной щели дробилки, т. е. когда размер отверстий сита предварительного грохота соответствует ширине выходной щели дробилки a = i,а эффективность грохочения Е = 100 %. Такой режим может быть осуществлен при испытаниях дробилок, при этом характеристика крупности дробленых продуктов будет определяться только свойствами руды и эффективностью работы самой дробилки.
При режимах, в которых работают дробилки на обогатительных фабриках (a ≈ i; E < 100 %), характеристика, крупности дробленого продукта зависит не только от эффективности работы самой дробилки, но и от эффективности работы грохота. Для обозначения содержания классов в продукте, разгружаемом из дробилки, работающей в режиме a = i и Е = 100%, принят символ b, а для всех прочих режимов та же величина обозначается символом β.
Условной максимальной крупностью dнкусков в дробленом продукте принято считать размер отверстий сита, через которое проходит 95 % материала. Соответственно условная относительная максимальная крупность кусков в дробленом продукте zн = dн:i.
Горизонтали на рис. 5 и 6 соответствуют содержанию отсеваемого класса 95 %. Точки пересечения горизонталей с кривыми определяют условную относительную максимальную крупность дробленого продукта zн.
Пунктирные прямые АВ лежат в большинстве случаев выше кривых. Это означает, что в дробленых продуктах содержание мелких классов будет больше, чем в материале, имеющем прямолинейную характеристику крупности и максимальную крупность, равную z. По сравнению с конусными и щековыми дробилками крупного дробления, конусные дробилки среднего и мелкого дробления имеют другое отношение размера выходной щели к эксцентриситету качаний конуса. В конусных дробилках среднего и мелкого дробления эксцентриситет превышает размер выходной щели и в большой степени влияет на крупность максимального куска, выходящего из дробилки. Поэтому характеристики крупности меняются не только в зависимости от ширины выходной щели, но также и от размера дробилки. Специальные исследования показали, что характеристики крупности, в которых на оси абсцисс отложены относительные размеры зерен (по отношению к максимальному куску), получаются одинаковыми для одной руды при разных размерах дробилок и разных щелях. Для построения конкретной типовой характеристики (т. е. полученной при дроблении материала, не содержащего зерен меньше размера щели, для дробилки данного размера, при заданном размере выходной щели) нужно по табл. 4 и 5 найти размер максимального куска для руды заданной прочности и, пользуясь рис. 7, по нескольким размерам зерен определить выход классов (пример построения см. ниже).
Операции поверочного грохочения имеют целью возвратить в дробилку избыточный продукт. (Избыточным продуктом называются крупные куски, содержащиеся в дробленом продукте, размер которых больше ширины выходной щели дробилки).
При дроблении без поверочного грохочения руд средней твердости в конусных дробилках мелкого дробления выход избыточного продукта достигает 65 %, а максимальная условная крупность дробленого продукта превышает в 4,5—5 раз ширину выходной щели. При твердых рудах выход избыточного продукта увеличивается до 85 %, а максимальная условная относительная крупность составляет 5,5 (см. рис. 7 и табл. 5 для щели 5 мм и дробилки КМД – 2200).
Таблица 4
Расчетный размер максимального куска руды dн в продукте конусных дробилок среднего дробления
Тип дробилки | Ширина разгрузочной щели i, мм | |||||||||||||||||
15 | 20 | 30 | 40 | 50 | 60 | |||||||||||||
Крепость руды | ||||||||||||||||||
| т | с | м | т | с | м | т | с | м | т | с | м | т | с | м | т | с | м |
Крупность максимальных кусков dH, мм | ||||||||||||||||||
КСД 1750 | 32 | 29 | 25 | 39 | 35 | 31 | 55 | 50 | 44 | 74 | 66 | 59 | 96 | 86 | 77 | 108 | 100 | 87 |
| Закрупнение, | |||||||||||||||||
2,1 | 1,9 | 1,7 | 1,9 | 1,7 | 1,6 | 1,8 | 1,7 | 1,5 | 1,8 | 1,6 | 1,5 | 1,9 | 1,7 | 1,5 | 1,8 | 1,7 | 1,5 | |
Крупность максимальных кусков dH, мм | ||||||||||||||||||
КСД 2200 | 45 | 40 | 36 | 53 | 48 | 42 | 71 | 64 | 57 | 93 | 84 | 74 | 117 | 106 | 94 | 130 | 117 | 105 |
| Закрупнение, | |||||||||||||||||
3,0 | 2,7 | 2,4 | 2,6 | 2,4 | 2,1 | 2,4 | 2,1 | 1,9 | 2,3 | 2,1 | 1,8 | 1,9 | 1,7 | 1,5 | 2,2 | 1,9 | 1,8 |
При поверочном грохочении в последней стадии дробления крупность конечного дробленого продукта может быть уменьшена в 3 раза для руд средней твердости и в 3,5 раза для твердых руд (при щели 10 мм по табл. 5).
Крупность дробленого продукта 10—20 мм, оптимальная для измельчения в шаровых и стержневых мельницах, может быть получена на конусных дробилках мелкого дробления только в замкнутом цикле с грохотами. Поэтому при подготовке руд к измельчению в стержневых и шаровых мельницах в последней стадии дробления необходимо включать операцию поверочного грохочения.
Таблица 5
Расчетный размер максимального куска руды dн в продукте конусных дробилок мелкого дробления
Тип дробилки | Ширина разгрузочной щели i, мм | ||||||||||||||
5 | 7 | 10 | 15 | 20 | |||||||||||
Крепость руды | |||||||||||||||
| т | с | м | т | с | м | т | с | м | т | с | м | т | с | м |
Крупность максимальных кусков dH, мм | |||||||||||||||
КМД 1750 | 18 | 16 | 14 | 20 | 18 | 16 | 24 | 22 | 19 | 30 | 27 | 24 | 36 | 32 | 29 |
| Закрупнение, | ||||||||||||||
3,6 | 3,2 | 2,8 | 2,8 | 2,6 | 2,3 | 2,4 | 2,2 | 1,9 | 2,0 | 1,8 | 1,6 | 1,8 | 1,6 | 1,5 | |
Крупность максимальных кусков dH, мм | |||||||||||||||
КМД 2200 | 28 | 25 | 23 | 30 | 27 | 24 | 34 | 31 | 27 | 41 | 37 | 33 | 49 | 44 | 40 |
| Закрупнение, | ||||||||||||||
5,6 | 5,0 | 4,6 | 4,3 | 3,8 | 3,4 | 3,4 | 3,1 | 2,7 | 2,7 | 2,5 | 2,2 | 2,5 | 2,2 | 2,0 |
Крупность дробленого продукта 10—20 мм, оптимальная для измельчения в шаровых и стержневых мельницах, может быть получена на конусных дробилках мелкого дробления только в замкнутом цикле с грохотами. Поэтому при подготовке руд к измельчению в стержневых и шаровых мельницах в последней стадии дробления необходимо включать операцию поверочного грохочения.
Замкнутый цикл дробления с грохочением, конечно, сложнее открытого с предварительным грохочением. Включение поверочного грохочения вызывает необходимость установки большего числа грохотов, конвейеров и питателей. В цехе появляются дополнительные перегрузки, в которых происходит пылеобразование. Все это приводит к увеличению затрат, вызывает усложнения в конструктивном решении цеха дробления и в его эксплуатации. Но отказаться от замкнутого цикла возможно лишь при условии увеличения крупности питания мельниц. А при этом общая себестоимость дробления и измельчения на фабрике возрастает.
Из изложенного следует третье правило выбора схем дробления: для получения дробленого продукта оптимальной крупности, обеспечивающего экономичную работу стержневых и шаровых мельниц и всего комплекса дробления и измельчения в последней стадии дробления, должна быть операция поверочного грохочения.
В соответствии со сформулированными правилами выбора схем рациональными следует признать две группы схем — одну для получения продукта крупностью не более 25 мм и другую— для продуктов мельче 10—20 мм. Схемы изображены на рис. 8.
Двухстадиальная схема ББ применима для кусков малой крупности исходной руды и трехстадиальная БББ – для крупных кусков. Обе схемы обеспечат продукт крупностью мельче 25 мм. Грохочение перед первой стадией показано пунктиром, как необязательное и применяемое по специальному обоснованию.
Схемы с замкнутым циклом в последней стадии с получением продукта крупностью 10 – 20 мм. Двухстадиальная БА – для мелкого исходного и ББА – для крупного (до 1200 мм) исходного материала.
При выборе оптимальной крупности дробленого продукта можно руководствоваться данными табл. 6.
Таблица 6
Дата добавления: 2018-06-01; просмотров: 1519; Мы поможем в написании вашей работы! |
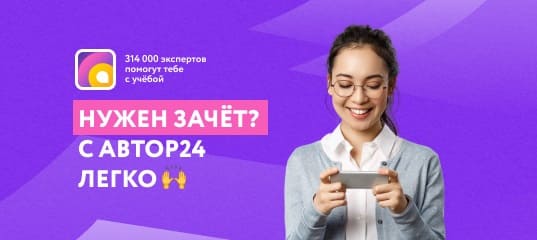
Мы поможем в написании ваших работ!