Отпуск проводится после закалки.
ЛЕКЦИЯ 10 ОСНОВНЫЕ ВИДЫ ТЕРМИЧЕСКОЙ ОБРАБОТКИ К основным видам термической обработки относятся: 1. Отжиг 2. Нормализация 3. Закалка 4. Отпуск Рассмотрим каждый вид термической обработки, классификацию, режимы и назначение.
ОТЖИГ
Отжигом называется термическая обработка, при которой производится нагрев до определенной температуры с последующей выдержкой и медленным охлаждением вместе с печью.
Назначение отжига получение однородной, равновесной структуры, свободной от остаточных напряжений.
На практике используют два принципиально различных вида отжига: отжиг I рода и отжиг II рода.
Отжиг I рода.
Особенностью всех разновидностей отжига I рода является то, что все они не связаны с фазовыми превращениями в твердом состоянии стали и протекают независимо от того, идут при этом фазовые превращения или нет.
Отжиг I рода включает:
1. Диффузионный отжиг применяют для устранения химической неоднородности, возникающей при кристаллизации металла. Этому отжигу подвергают слитки и отливки из легированной стали для устранения ликвации, которая повышает склонность стали при обработке давлением к трещинообразованию.
Нагрев при диффузионном отжиге проводят до максимально высоких температур, так как при этом наиболее интенсивно происходят диффузионные процессы, необходимые для выравнивания в отдельных объемах состава стали. Обычно для легированных сталей температуру диффузионного отжига выбирают в интервале 1050 ‑ 1250 °С.
|
|
2. Рекристаллизационный отжиг заключается в нагреве деформированной стали выше температуры начала рекристаллизации, выдержке при этой температуре и последующем медленном охлаждении.
Рекристаллизационный отжиг применяют для устранения наклепа после холодной пластической деформации. При проведении этого отжига главным процессом является рекристаллизация металла.
Рекристаллизационный отжиг используют в промышленности как промежуточный процесс между операциями холодного деформирования (для снятия наклепа).
3. Низкий отжиг для снятия внутренних напряжений проводят с целью уменьшения остаточных напряжений, образовавшихся в металле при ковке, литье, сварке и способных вызвать коробление и разрушение детали. Главным процессом, проходящим при отжиге для снятия внутренних напряжений, является полная или частичная релаксация остаточных напряжений.
На практике отжиг стальных изделий для снятия напряжений проводят в температурном интервале 200 – 700 °С с последующим медленным охлаждением.
Отжиг II рода
Отжиг II рода - термическая обработка, заключающаяся в нагреве стали до температур выше критических точек Ас1 или Ас3, выдержке и, как правило, в последующем медленном охлаждении. Отжиг II рода основан на прохождении фазовых превращений в твердом состоянии - превращении γ → α - и поэтому часто называется фазовой перекристаллизацией. При фазовой перекристаллизации измельчается зерно и устраняются неблагоприятные структуры стали.
|
|
В большинстве случаев отжиг II рода является подготовительной термической обработкой - в процессе отжига снижается твердость и прочность, что облегчает обработку резанием средне- и высокоуглеродистых сталей. Неполный отжиг инструментальных сталей предшествует окончательной термической обработке.
Существуют следующие виды отжига II рода:
1. Полный отжиг применяется для доэвтектоидных сталей и состоит в нагреве стали на 30 – 50 °С выше точки Ас3, выдержке при этой температуре до полной перекристаллизации металла и медленномохлаждении. При таком отжиге образуется мелкое аустенитное зерно, из которого при охлаждении формируется равномерная мелкозернистая феррито-перлитная структура.
2. Неполный отжиг широко применяется для заэвтектоидных углеродистых и легированных сталей. При неполном отжиге проводится нагрев до температур немного выше (на 10 – 30 °С) точки А1, что приводит к практически полной перекристаллизации стали и получению зернистой формы перлита вместо обычной пластинчатой.
|
|
Отжигу на зернистый перлит подвергают также тонкие листы и прутки из низко- и среднеуглеродистой стали перед холодной штамповкой или волочением для повышения пластичности.
После отжига на зернистый перлит эвтектоидные и заэвтектоидные стали обладают наилучшей обрабатываемостью резанием.
НОРМАЛИЗАЦИЯ
При нормализации сталь нагревают до температуры на 30 – 50 °Свыше линии GSE и охлаждают на воздухе.
Ускоренное по сравнению с обычным отжигом охлаждение обусловливает несколько большее переохлаждение аустенита. Поэтому при нормализации получается более тонкое строение перлита и более мелкое зерно. В результате прочность стали после нормализации становится больше прочности после отжига.
Нормализацию применяют чаще всего в следующих случаях: как промежуточную операцию для смягчения стали перед обработкой резанием и общего улучшения структуры стали перед закалкой.
Нормализацию используют и как окончательную термическую обработку средне- и высокоуглеродистых доэвтектоидных сталей, если требования к свойствам этих сталей умеренные и для них не обязательна закалка с высоким отпуском.
|
|
ЗАКАЛКА
Закалка стали состоит в нагреве ее выше температур фазовых превращений, выдержке для завершения всех превращений и охлаждении с высокой скоростью в закалочной среде с целью получения структуры мартенсита, обеспечивающего более высокую прочность и твердость стали.
В качестве закалочных сред используют жидкости разной плотности (вода, масло).
В зависимости от температуры нагрева различают:
1. Полная закалка - нагревна 30 – 50 °Свыше Ас3, выдержка, охлаждение в закалочной среде. Полная закалка используется для доэвтектоидных сталей.
После полной закалки получается мартенситная структура.
2. Неполная закалка - нагрев на 30 – 50 °С выше Ас1, выдержка,охлаждение в закалочной среде. Неполная закалка используется длязаэвтектоидных сталей.
После неполной закалки образуется структура мартенсит и цементит вторичный.
Заэвтектоидные стали обычно используют для изготовления инструмента. Важнейшим требованием, предъявляемым к инструментальным сталям, является твердость. Включения цементита после закалки не только не уменьшают, но даже увеличивают твердость, а следовательно, и износостойкость стали.
Таким образом, для доэвтектоидных сталей рационально применять полную закалку, для заэвтектоидных - неполную (рис.10.2).
Рис.10.2. Оптимальные температуры нагрева под закалку
углеродистых сталей
ЗАКАЛИВАЕМОСТЬ И ПРОКАЛИВАЕМОСТЬ СТАЛИ
Закаливаемость - способность стали подвергаться закалке, т.е. повышать твердость в результате закалки.
Прокаливаемость - способность стали закаливаться на определенную глубину.
Рассмотрим случаи полной (сквозной) прокаливаемости и неполной (несквозной) прокаливаемости. Несквозная прокаливаемость обусловлена тем, что при закалке деталь охлаждается быстрее с поверхности и медленнее в сердцевине. Распределение скорости охлаждения по сечению детали показывает (рис.10.3), что у поверхности скорость охлаждения максимальна, а в центре - минимальна.
Рис. 10.3
![]() | ![]() |
Случай полной прокаливаемости | Случай неполной прокаливаемости |
В качестве количественной оценки прокаливаемости вводятся следующие характеристики:
глубина прокаливаемости, l, мм - расстояние от поверхности до зоны с полумартенситной структурой (50% мартенсита + 50% тростита).
критический диаметр, Dкр, мм - максимальный диаметр сечения, в центре которой после закалки образуется полумартенситная структура.
Прокаливаемость является важной характеристикой стали. При сквозной прокаливаемости (рис.10.3) по сечению изделия механические свойства одинаковы, при несквозной прокаливаемости в сердцевине наблюдается снижение прочности, твердости металла.
На прокаливаемость оказывает влияние состав стали (содержание углерода и легирующих элементов) и характер закалочной среды. Так, легированные стали имеют значительно более высокую прокаливаемость по сравнению с углеродистыми сталями. С понижением содержания углерода прокаливаемость уменьшается.
ОТПУСК ЗАКАЛЕННОЙ СТАЛИ
Отпуск - заключительная стадия термической обработки, заключающаяся в нагреве до температур ниже нижней критической температуры Aс1, выдержке и охлаждении (чаще на воздухе, иногда в воде).
Отпуск проводится после закалки.
Назначение отпуска - снятие внутренних напряжений и получение заданных, требуемых свойств стали.
Свойства стали, получаемые после закалки и соответствующего отпуска зависят от структуры, образующейся после отпуска и, в свою очередь, от превращений, протекающих в процессе отпуска.
Непосредственно после закалки сталь имеет структуру, состоящую из тетрагонального мартенсита и остаточного аустенита. Такая структура является неравновесной. Переход к более устойчивому структурному состоянию закаленной стали сопровождается распадом тетрагонального мартенсита и превращением остаточного аустенита.
При нагревании закаленной стали до температур 80…100°С заметных изменений в структуре не наблюдается. Дальнейшее повышение температуры приводит к структурным превращениям, протекающим в определенных температурных интервалах.
В углеродистых сталях при отпуске наблюдается четыре превращения.
Первое ‑ превращение тетрагонального мартенсита протекает в интервале температур 80…200°С. Это превращение заключается в выделении углерода из мартенсита (за счет возрастания подвижности атомов при повышении температуры). Выделившийся углерод образует с железом ‑ карбид, химический состав которого близок к
. При этом кристаллы
‑ карбида и мартенсита имеют общие кристаллографические плоскости (когерентную связь). При образовании
‑ карбида происходит неравномерное обеднение пересыщенного альфа ‑ твердого раствора углеродом.
Вблизи карбидов мартенсит обеднен углеродом, в то время как отдельные его участки сохраняют исходный состав. Выделившийся карбид имеет пластинчатую форму, причем толщина этих пластинок составляет всего несколько атомных слоев.
По мере выделения углерода решетка мартенсита становится менее искаженной, отношение параметров решетки с/а приближается к единице. Такой мартенсит называют, мартенситом отпуска (отпущенным мартенситом). Он обладает высокой твердостью и износостойкостью, но в сравнении с мартенситом закалки представляет собой более стабильную структуру.
Второе ‑ превращение остаточного аустенита. Оно протекает в интервале температур 200…300°С. Сохранение в структуре закаленной стали аустенита было связано с большими напряжениями сжатия, возникающими в результате превращения аустенита в мартенсит. При последующем отпуске напряжения снижаются, уменьшается объем мартенсита (в результате первого превращения) и аустенит получает возможность превращения в мартенсит с увеличением объема. Одновременно продолжается процесс распада тетрагонального мартенсита.
Третье ‑ окончательный распад мартенсита и карбидное превращение. Это превращение протекает в интервале температур 300…400°С. В этом интервале температур из мартенсита выделяется весь избыточный углерод, что приводит к образованию феррита, ‑ карбид перестраивается в стабильный карбид железа (
) ‑ цементит. При этом происходит обособление карбида, т.е. отделение от решетки альфа ‑ твердого раствора. Изменяются размеры и форма карбидных частиц, они укрупняются и приобретают зернистую форму. Полученная тонкодисперсная смесь феррита и цементита называется троститом отпуска. Эта структура менее твердая и прочная, по более пластичная, чем мартенсит отпуска, и имеет повышенную упругость.
Четвертое ‑ коагуляция (укрупнение) частиц цементита. Структура стали, полученная в результате отпуска при 500…700°С представляет собой дисперсную смесь феррита с цементитом и называется сорбитом отпуска. Такая структура удачно сочетает хорошую прочность, пластичность и вязкость.
Различие тростита и сорбита отпуска от структур того же наименования, но полученных при распаде аустенита, заключается в форме цементитных включений. После отпуска цементит имеет зернистую форму.
Различие в форме частиц цементита в феррито ‑ цементитной смеси приводит к различию в свойствах стали. При равной твердости структура с цементитом зернистой формы обладает более высокой пластичностью и вязкостью.
Изменение свойств стали при увеличении температуры отпуска рассмотрено на рис.10.4.
Рис.10.4. Зависимость свойств стали от температуры отпуска.
Различают три вида отпуска:
Низкий отпуск - температура нагрева 150 - 250°С, структура: мартенсит отпуска, свойства: высокая твердость, снятие внутренних напряжений, уменьшение хрупкости; назначение: инструментальные стали
Средний отпуск - температура нагрева: 300 - 500°С; структура: тростит отпуска; свойства: высокая твердость, высокая упругость и выносливость; назначение; для упругих элементов (пружины, рессоры).
Высокий отпуск - температура нагрева: 500 - 680°С; структура: сорбит отпуска; свойства: высокая твердость, пластичность, вязкость. Наилучшее сочетание этих свойств; назначение: конструкционные стали.
Закалка + Высокий отпуск = Улучшение
ЛЕКЦИЯ 11.
СПОСОБЫ ПОВЕРХНОСТНОГО УПРОЧНЕНИЯ
Поверхностное упрочнение используется для деталей и изделий, работающих в условиях воздействия ударных нагрузок, в условиях трения. Также поверхностное упрочнение может использоваться для деталей тонких сечений.
Дата добавления: 2018-06-01; просмотров: 285; Мы поможем в написании вашей работы! |
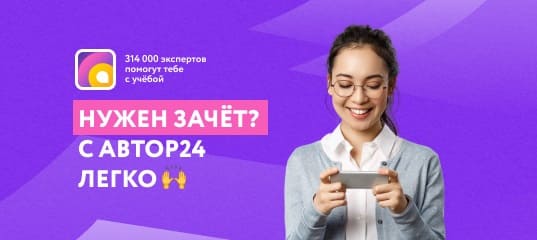
Мы поможем в написании ваших работ!