Подготовка деталей к контролю
На участок контроля детали должны поступать после тщательной очистки и мойки. При наличии на деталях остатков загрязнений (в пазах, канавках резьбе и т.п.), их необходимо очистить вручную, с помощью жестких волосяных щеток, деревянных или пластмассовых скребков и моющих препаратов. При очистке деталей нельзя применять металлические предметы, а также ветошь, оставляющую ворс и нитки. Моющие вещества, рекомендуемые для очистки деталей, приведены в таблице 1.2 приложения.
При проведении контроля с применением водной суспензии детали необходимо предварительно обезжирить моющим раствором, т.к. на поверхности, покрытой пленкой жира, резко снижается чувствительность порошка к мелким дефектам.
При проведении контроля с использованием водной суспензии на основе концентрата ДИАГМА для очистки поверхности деталей от масляных загрязнений необходимо протереть ее ветошью, смоченной в приготовленной для контроля суспензии.
Намагничивание деталей
В технологических картах на магнитопорошковый контроль вагонных деталей в графе "ОПЕРАЦИИ КОНТРОЛЯ" должны быть указаны технологические операции процесса намагничивания с учетом применяемого дефектоскопа, вида и способа намагничивания.
При контроле вагонных деталей применяются следующие виды намагничивания: полюсное (продольное или поперечное), циркулярное и комбинированное. Способы и схемы намагничивания приведены в таблице 3.2. Способ намагничивания деталей определяется формой и габаритами контролируемых деталей, а также от местоположения и направления ожидаемых дефектов.
|
|
Применяются следующие виды намагничивающего тока: переменный, постоянный и импульсный (последовательность импульсов) - при контроле СОН. Намагничивание импульсным током при контроле СОН осуществляется путем пропускания по детали или намагничивающему устройству не менее трех импульсов тока.
Таблица 3.2 Основные виды и способы намагничивания, применяемые при контроле деталей вагонов
Вид намагничивания | Способ намагничивания (дефектоскопы или НУ) | Схема намагничивания | ||
Полюсное (продольное и поперечное) При намагничивании протяженных деталей вектор напряженности магнитного поля направлен вдоль детали, что позволяет выявлять поперечные трещины | При помощи электромагнита (МД-14П. УНМД-300/2000. ЭМПД-12/36В) | |||
При помощи соленоида (МД-12ПШ, МД-12ПЭ. МД-12ПС, МД-13ПР, МД-14П - соленоиды) | ||||
При помощи кабеля, свитого в соленоид или навитого на деталь (МД-14П, УНМД-300/2000) | ||||
При намагничивании силовые линии магнитного поля замыкаются вокруг проводника с током, при этом выявляются продольные трещины. направление которых совпадает с током.
| Пропусканием тока по контролируемой детали (Электроконтакты дефектоскопов и установок: МДУ-КПВ. УНМД-300/2000, МДС-5) | |||
Пропусканием тока по проводнику, пропущенному в сквозное отверстие в детали (МД-14П, УНМД-300/2000, УМДП-01) | ||||
Пропусканием тока по тороидальной обмотке (УМД-300/2000,МД-14П) |
Условные обозначения: НУ-намагничивающее устройство. Д- контролируемая деталь.I-электрический ток.
Рис 3.1
Распределение магнитного поля соленоида при намагничивании различных участков протяженных деталей: а) концов деталей; б) участков, имеющих переменное сечение.
Н - вектор напряженности магнитного поля на поверхности детали:
Ht и Нn - тангенциальная и нормальные составляющие Н;
Нд - Напряженность поля дефекта;
ДН - зона достаточной намагниченности.
При намагничивании контролируемых деталей необходимо учитывать ряд факторов, влияющих на выявляемость дефектов, то есть на чувствительность контроля.
Вектор напряженности магнитного поля в любой точке намагниченной детали можно разложить на две составляющие: тангенциальную (направленную вдоль контролируемой поверхности) Ht и нормальную (направленную перпендикулярно контролируемой поверхности) Нn. Поле дефекта формируется за счет тангенциальной составляющей поля (Рис- 3.1а). Если нормальная составляющая поля превышает тангенциальную составляющую поля более, чем в_3раза ( Hn/Ht > 3), выявляемость резко ухудшается.
|
|
Это явление наблюдается при полюсном намагничивании соленоидами протяженных деталей на расстоянии 20 - 50 мм от конца детали и в местах резкого изменения сечения детали, т.е. вблизи полюсов, образовавшихся при намагничивании детали. Чем короче деталь, тем больше влияние полюсов. Чтобы устранить это явление, необходимо детали длиной менее 300 мм, при отношении длины к диаметру L/D < 5, удлинить с помощью специальных наконечников или составить их в цепочки.
В качестве удлинительных наконечников может быть использована любая деталь такого же или большего сечения, чем контролируемая или специально изготовленная технологическая деталь, представляющая брусок, размеры которого не менее (100 х 140 х 80) мм, набранный из трансформаторного железа любой марки. Размер и форма бруска могут быть изменены в зависимости от размеров и формы контролируемой детали (Рис. 3.2). Пластины в наборе во время контроля должны располагаться вдоль детали, являясь ее продолжением.
|
|
![]() |
При установке детали в положение контроля для достижения наилучшей выявляемости необходимо намагничивающее устройство и контролируемую деталь располагать таким образом, чтобы угол между направлением вектора напряженности магнитного поля и трещиной был близок к 90 градусам. Выявляемость дефектов значительно ухудшается в случаях, когда угол между направлением ожидаемых дефектов и направлением намагничивающего поля меньше 30 градусов (Рис. 3.3). Если направление распространения трещин заранее неизвестно, а также, если деталь имеет сложную форму, то намагничивание нужно проводить последовательно в. нескольких направлениях.
Рис. 3.2 Способы намагничивания коротких деталей: с помощью
удлинителей (а и б); составлением коротких деталей в цепочки (в).
1 - намагничиваемая деталь; 2 - удлинители
Рис. 3.3
Влияние положения трещины по отношению к силовым линиям магнитного поля (или положению соленоида) на выявляемость дефекта.
Н - вектор напряженности Магнитного поля; 1 - соленоид;
2 - деталь; 3 - трещины.
Проведение контроля
3.4.1 Общие положения
При проведении контроля в течение смены после каждого часа работы необходимо проверять показания приборов, контролирующих напряжение и ток намагничивания на соответствие паспортным данным. При этом вблизи намагничивающего устройства (внутри рабочего отверстия или межполюсного промежутка и снаружи не ближе 100 мм от корпуса) не должно быть никаких металлических предметов, в том числе контролируемых деталей.
При изменении показания какого-либо прибора, превышающем допустимые значения, а также при обнаружении в процессе эксплуатации каких-либо других неисправностей дефектоскопа или вспомогательных приборов, дефектоскопист должен заявить об этом мастеру участка (цеха) для решения вопроса об устранении неисправности или замене указанного средства контроля.
При проведении подготовительных или вспомогательных работ дефектоскоп или намагничивающее устройство должны быть отключеныот сети.
По окончании контроля необходимо отключить дефектоскоп или установку от сети, очистить - соленоиды и другие устройства, соприкасающиеся с магнитной суспензией, от загрязнений и остатков суспензии и провести профилактические работы в соответствии с требованиями технической документации на дефектоскоп или установку.
3.4.2 Контроль длинных деталей с помощью соленоидов
При намагничивании длинных (L > 300 мм) деталей соленоидом необходимо учитывать, что с увеличением расстояния от торца соленоида вдоль детали напряженность магнитного поля уменьшается и, начиная с некоторого значения, становится недостаточной для выявления трещин с требуемым уровнем чувствительности (Рис. 3.4). Следовательно, нанесение индикатора и осмотр нужно проводить в зоне достаточной намагниченности (далее зона ДН). Зона ДН зависит от типа дефектоскопа, взаимного расположения детали и соленоида, а также от размеров и формы детали.
Рис. 3.4
Характер изменения напряженности магнитного поля на поверхности детали по мере удаления от торца соленоида, Ht - тангенциальная составляющая поля; ЗДН - зона достаточной намагниченности
|
|
Рис.3.5 Факторы, влияющие на длину зоны ДН:
а) смещение детали в отверстии соленоида к внутренней стенке корпуса соленоида уменьшает зону ДН;
б) увеличение сечения на конце длинной детали увеличивает зону ДН на части детали меньшего сечения.
Зоны ДН могут уменьшаться в следующих случаях:
- при приближении соленоида к концу детали на расстояние менее 300 мм из-за возрастания нормальной составляющей поля, поэтому рекомендуется перемещать соленоид всегда от конца детали кее центру.
- при приближении контролируемой поверхности к корпусу соленоида
на расстояние меньшее 1/5 диаметра отверстия соленоида (40-50 мм от контролируемой поверхности до внутренней поверхности корпуса соленоида с диаметром рабочего отверстия более 200 мм). (Рис.3.5а).
- при увеличении сечения детали. В этом случае каждый участок детали большего сечения необходимо рассматривать как самостоятельную деталь и контролировать его дважды, перемещая соленоид от концов участка к центру (Рис. 3.5б).
Если деталь имеет с одной стороны массивную часть,токонтролировать необходимо всегда со стороны меньшего сечения. В этом случае зоны ДН могут увеличиваться в пределах от 1.2 до 1.5 раз за счет уменьшения нормальной составляющей поля (Рис- 3.5б).
С целью повышения производительности контроля намагничивание можно проводить двумя соленоидами одного типа (например, два дефектоскопа МД-12ПШ), расположенными соосно. Соленоиды (или один из них) должны иметь возможность перемещения вдоль их общей оси. При включении соленоиды должны притягиваться друг к другу. В противном случае один из соленоидов необходимо развернуть (МД-12ПШ, МД-14П) или изменить полярность включения (МД-12ПЭ, МД-12ПС). Намагничивающие устройства дефектоскопа МД-12ПЭ должны располагаться так, чтобы магнитопроводы были снаружи.
Контролируемая деталь должна располагаться между соленоидами таким образом, чтобы концы ее входили в отверстия соленоидов или контролируемую деталь нужно удлинить технологическими деталями, входящими в отверстия соленоидов.
Длинные детали (L/d > 5) из магнитотвердых материалов, в которых необходимо выявлять поперечные трещины, возникающие в любом месте по всей длине детали, целесообразно контролировать при помощи соленоидов переменного тока (продольное намагничивание) способом приложенного поля (СПП).
3.4.3 Контроль деталей седлообразным намагничивающим устройством дефектоскопа МД-12ПС
Седлообразное намагничивающее устройство допускается применять для намагничивания деталей, имеющих диаметр (или максимальный поперечный размер) не менее 100 мм, для контроля которых достаточна напряженность магнитного поля не менее 30 А/см (средняя часть оси колесной пары, хвостовик автосцепки, гребень цельнокатаного колеса). Седлообразное намагничивающее устройство необходимо располагать над контролируемой деталью (осью колесной пары) таким образом, чтобы расстояние между поверхностью детали и дугой корпуса соленоида было (40 - 60) мм.
Магнитный порошок или суспензия должны наносится с двух сторон от корпуса намагничивающего устройства. Часть поверхности контролируемой детали, заключенная в промежутке между его дугами, находится вне зоны контроля. Чтобы ее проверить, необходимо сместить седлообразное намагничивающее устройство так, чтобы непроверенная часть оказалась в зоне Ж
Для увеличения зоны контроля рекомендуется намагничивать длинные детали 1(например, ось колесной пары) или цепочки из коротких деталей, общей длиной более 600 мм двумя седлообразными устройствами, расположенными на расстоянии 220 - 240 мм друг от друга. В этом случае в зоне контроля оказывается вся поверхность детали, находящаяся между седлообразными устройствами и с внешних сторон от них в пределах зон ДН. При намагничивании деталей типа валов или осей диаметром более 100 мм в зоне контроля оказывается 1/3 окружности детали, расположенная под седлообразным намагничивающим устройством. Поэтому такие детали необходимо контролировать не менее, чем за три прохода, поворачивая ее каждый раз на 120 или 90 градусов, или контролировать за один проход, перемещая намагничивающее устройство со скоростью не более 2 м в минуту при вращении детали со скоростью не более 5 оборотов в минуту. В последнем случае суспензия наносится перед движущимся седлообразным намагничивающим устройством и одновременно осматривается поверхность детали непосредственно за ним.
3.4.4 Намагничивание деталей приставным электромагнитом
Приставной электромагнит применяется в тех случаях, когда известно место зарождения трещины и ее ориентация на крупногабаритных деталях и при вторичном контроле по показаниям вихретокового дефектоскопа или визуального контроля.
Электромагнит устанавливается на деталь таким образом, чтобы его полюса опирались в поверхность детали по разные стороны от предполагаемой трещины. В зоне контроля оказывается часть поверхности детали, заключенная между полюсами, за исключением участков, примыкающих к ним (зона невыявления) в пределах от 5 до 15мм в зависимости от размеров электромагнита.
3.4.5 Намагничивание деталей гибким кабелем
Для контроля колец, полых цилиндров, хомутов rf других деталей с отверстиями применяется циркулярное намагничивание путем пропускания тока по кабелю или стержню, вставленному в отверстие детали, или по кабелю (проводу), намотанному на деталь тороидально.
Кабель или стержень вставляется в отверстие детали строго по центру, так как при его смещении могут возникнуть на контролируемой поверхности местные полюса, на которых собирается магнитный порошок.
Способ контроля (СПП или СОН) выбирается в зависимости от магнитных характеристик материала и от величины тока, который может обеспечить имеющийся дефектоскоп.
При контроле СПП колец, хомутов и т, п. на деталь необходимо намотать 3-6 витков кабеля, расположенных рядом друг с другом нанести индикатор на свободную поверхность детали, после отекания суспензии поверхность осмотреть, затем витки переместить на проверенный участок и проверить оставшуюся часть детали.
Для составления технологической карты и определения числа витков, которые нужно наматывать на деталь, необходимо измерить амплитудное значение продольной составляющей напряженности поля на поверхности детали с противоположной от витков стороны. Если напряженность поля окажется ниже допустимой для данной стали, то необходимо определить зоны ДН и контролировать в несколько этапов, перемещая каждый раз витки на одну-две зоны ДН.
При контроле СОН кабель необходимо намотать на деталь равномерно по ее окружности, если дефектоскоп обеспечивает требуемый ток, или намагничивать по частям, смещая каждый раз витки не более, чем на одну зону ДН.
Дата добавления: 2018-06-01; просмотров: 975; Мы поможем в написании вашей работы! |
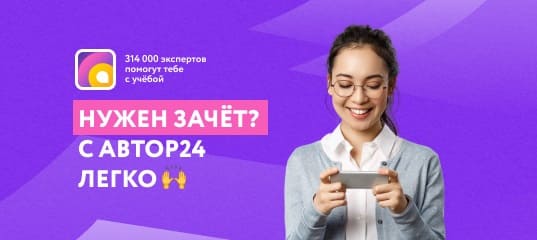
Мы поможем в написании ваших работ!