И рН начала коагуляции кремневой кислоты
Лекция №14. Гидрометаллургическое производство цинка.
Выщелачивание цинкового огарка.
Взаимодействие компонентов огарка с серной кислотой. Назначение операции выщелачивания огарка - растворить как можно полнее соединения цинка, содержащиеся в огарке, и получить чистые растворы для электролиза. Растворение происходит в сернокислых растворах. Выбор серной кислоты как растворителя обусловлен хорошей растворимостью в ней ZnО, условиями последующей операции электролитического восстановления цинка, а также наличием на любом цинковом заводе в достаточном количестве серной кислоты, получаемой при электролизе и производимой на месте из обжиговых газов. Оксид цинка хорошо растворим в слабых растворах серной кислоты, с образованием сульфата цинка:
ZnО + Н2SО4 = ZnSО4 + Н2О
Сульфид цинка ZnS можно растворить только в концентрированной серной кислоте при нагревании. При этом выделяется токсичный сероводород:
ZnS+ Н2SО4 = ZnSO4 + Н2S
В ходе обжига образуется некоторое количество силикатов (nZnО·mSiO2), ферритов (xZnО·yFе2O3) и алюмината (ZnО·А12О3) цинка, малорастворимых в растворах серной кислоты. Их растворимость возрастает по мере повышения концентрации Н2SO4 и температуры раствора. Так, для перевода в раствор цинка из ферритных соединений необходима концентрация Н2SО4 200- 300 г/л и температура 80-90 °С. Кроме цинка, в огарке находятся соединения железа, меди, кадмия, свинца, серебра, золота, никеля, кобальта, марганца, бария, кальция, алюминия и других металлов. Кадмий близок по свойствам к цинку, его оксид СdO хорошо растворим в сернокислых растворах. Из огарка в раствор переходит 85-90 % Сd. Железо в огарке находится в основном в виде ферритов цинка и меди, в некоторой степени в виде оксидов Fе2О3 и Fе3О4 и весьма незначительно в виде FеО. Оксиды железа растворимы в слабых растворах серной кислоты: FеО-хорошо, Fе2О3 -частично. В раствор переходит 3-4 % железа, содержащегося в огарке, в результате чего концентрация его в растворе достигает 1-2 г/л, что оказывается полезным при последующей гидролитической очистке раствора от мышьяка, сурьмы, германия и других примесей. Медь находится в огарке в виде оксидов (СuО, Сu2О), ферритов (nСuО·mFе2O3), силикатов (xСu2О·ySiО2). Наиболее легко растворяется СuО с образованием СuSО4. Ферриты меди также труднорастворимы, как и ферриты цинка. Окисленные соединения сурьмы (III) и мышьяка (III) при выщелачивании огарка переходят в раствор в виде Аs2(SО4)3 и Sb2(SО4)3. Оксиды сурьмы (V) и мышьяка (V) труднорастворимы.
|
|
Свинец при сернокислотном выщелачивании практически весь переходит в кек в виде труднорастворимого сульфата:
РbSiО3+ Н2SО4 = РbSО4 + Н2SiО3
|
|
Растворение силикатов свинца, меди, цинка приводит к загрязнению раствора кремнекислотой, которая затрудняет отстаивание и фильтрацию пульпы после выщелачивания. Серебро в огарке находится в виде Аg2S и Аg2SО4. Сульфат серебра растворяется, но затем осаждается ионами хлора, присутствующими в растворе, в виде труднорастворимого АgС1. Сульфид серебра не растворяется и остается в кеке. Золото полностью остается в твердом остатке. Оксиды кальция и бария в сернокислых растворах переходят в труднорастворимые сульфаты по реакции
МеО + Н2SО4 = МеSO4 + Н2О
где Ме - Са, Ва.
Соединения хлора, фтора, натрия, магния легко выщелачиваются и накапливаются в оборотных растворах. Рассеянные элементы - таллий, галлий, индий, германий - частично переходят в раствор.
Схемы выщелачивания обожженных концентратов.
В мировой практике применяют разнообразные схемы выщелачивания: одностадийную, двустадийную и трехстадийную. Выщелачивание осуществляют периодически и непрерывно. Наиболее распространена схема непрерывного противоточного двустадийного выщелачивания (рис.14.1). Cпособы выщелачивания могут отличаться приемами подачи огарка в растворитель (прямое или обратное) и концентрацией кислоты на первой и второй стадиях. Сравнение схем приводит к выводам:
|
|
· Эксплуатационные и капитальные затраты при обеих схемах работы одинаковы.
· Периодическое выщелачивание надежнее при переменном составе сырья или наличии в нем примесей мышьяка и кремнезема.
· Обучение рабочих занимает меньше времени при периодическом процессе.
· Одностадийное выщелачивание может применяться при высококремнистом сырье.
· Достоинство непрерывной схемы, это удобный гидротранспорт огарка и использование его тепла, что важно для повышения скорости выщелачивания и отстаивания.
· Недостаток непрерывной схемы - большое количество растворов (пульп) в незавершенном производстве (в постоянном обороте).
Непрерывный процесс характеризуется непрерывной подачей огарка и кислого раствора в примерно постоянном соотношении; периодический отличается точной дозировкой огарка и раствора при проведении выщелачивания отдельными операциями.
При одностадийном выщелачивании огарок обрабатывают отработанным электролитом с добавкой небольшого количества промывных растворов. Вначале производят кислое выщелачивание, снижая кислотность до 3 - 10 г/л. Далее, после нейтрализации остаточной кислотности вводимым огарком осаждают примеси. Очищенный нейтральный раствор идет на электролиз. Извлечение цинка в раствор при одностадийном выщелачивании снижается до 76 - 80%, т.е. на 6 - 4%. При высоком качестве сырья одностадийное выщелачивание в комплексе с противоточной промывкой обеспечивает высокие показатели по переводу цинка в раствор (до 90%).
|
|
При двустадийном выщелачивании первая стадия проводится до нейтрализации кислоты (нейтральное выщелачивание) раствором, полученным на второй стадии. Во второй стадии сгущенную нейтральную пульпу обрабатывают отработанным кислым электролитом (кислое выщелачивание).
Стандартная схема выщелачивания предусматривает применение для выщелачивания отработанного электролита кислотностью 120 - 160 г/л. На заводе «Сулливан» (США) применяют для выщелачивания электролит с кислотностью до 300 г/л (метод Тейнтона) с целью растворения ферритного цинка. Завод «Носса» (Италия) из-за высокого содержания в огарке растворимого кремнезема ведет выщелачивание в одну стадию, подавая отработанный электролит в пульпу огарка и строго регулируя рН в пределах 4 - 5.
На многих заводах («Корпус-Кристи» и др.) при выщелачивании не стремятся к максимальному извлечению цинка из концентратов и тщательной промывке кеков, так как эти кеки в дальнейшем поступают на переработку на свинцовые и медеплавильные заводы, где цинк доизвлекается в виде возгонов, возвращаемых на цинковые заводы. Однако это связано с потерями цинка и определяется конъюнктурой. По заводам мира Н.В.Гудима приводит данные представленные в таблице 11.7.
Таблица 14.1 Способы выщелачивания огарка на цинковых заводах.
Предприятие (страна) | Метод выщелачивания |
«Укрцинк» (Украина) | Периодическое в две стадии * |
«Электроцинк» (Россия) | Непрерывное в две стадии |
Челябинский цинковый завод (Россия) | То же |
Лениногорский комбинат (Казахстан) | Непрерывная в одну стадию |
УКСЦК (Казахстан) | Одностадийное |
«Грейт-Фолс» (США) | Непрерывное в две стадии (иногда в три) |
«Анаконда» (США) | Непрерывное в две стадии |
«Корпус-Кристи» (США) | Периодическое в одну стадию |
«Сильвер-Кинг» (США) | То же |
«Трейл» (Канада) | Непрерывное в две стадии с довыщелачиванием кека |
«Флин-Флон» (Канада) | Непрерывное в две стадии |
«Серро де Паско» (Перу) | Периодическое в одну стадию |
«Винье» (Франция) | Непрерывное в две стадии |
«Бален» (Бельгия) | То же |
«Порто-Маргера» (Италия) | Периодическое в две стадии |
. «Носса» (Италия) | Одностадийное «обратное» |
«Эйтрхейм» (Норвегия) | Непрерывное в две стадии |
«Брокен-Хилл» (Северная Родезия) | Периодическое в одну стадию |
«Акита» (Япония) | Непрерывное в две стадий- |
«Рисдон» (Тасмания) | Непрерывное в одну стадию с флотацией песков и шламов |
«Коккола» (Финляндия) | Периодическое в одну стадию . |
«Баллифилд» (Канада) | То же - |
«Аннака» (Япония) | Непрерывная в две стадии |
* Вторая стадия — довыщелачивание в аппаратах кипящего слоя. |
При выборе схемы выщелачивания решающее влияние, имеет содержание мышьяка и кремнезема. Вредное влияние мышьяка после перехода на обжиг в печах КС практически отпало. Имеются заводы, успешно работающие на шихте, содержащей около 0,5% As, по двухстадийной непрерывной схеме, в то время как раньше считали работу по такой схеме трудной уже при 0,07 - 0,1% As. Однако трудности, связанные с растворимым кремнеземом, несколько возросли. Поэтому во избежание расстройства процесса сгущения были приняты следующие меры:
· нейтральное выщелачивание ведут при избытке огарка, достаточном для
доведения рН до 5,1 - 5,3, что обусловливает коагуляцию кремнезема, контроль рН
автоматический; .
· часть отработанного электролита подают в нейтральный цикл (непрерывная схема);
· содержание кремнезема в растворах поддерживают в пределах 1,5-2 г-/л,
регулируя съем цинка с 1 м3 раствора и кислотность отработанного электролита;
· нагревают пульпу в кислых сгустителях до 70 - 80 оС;
· применяют для лучшего осветления полиакриламид (сепаран) - до 70 г/м3;
· снижают кислотность в кислом сливе до 1 - 2 г/л, работу сгустителей автоматизируют.
В принятых для осаждения кремнезема условиях распределение других металлов между раствором и осадком гидратов происходит в соответствии с общей закономерностью:
где - концентрация металла;
- коэффициент активности катиона; n - валентность; Пр - произведение растворимости;
- константа диссоциации воды при 60 – 70 °С, равная 10-13; рН - водородный показатель.
Степень растворения цинка из огарка возрастает с увеличением концентрации Н2SО4 и температуры, но при этом повышается и содержание в растворе примесей, которые могут ухудшить условия электролиза раствора. Концентрация многих примесей в растворе зависит от рН. Чем выше рН раствора, тем ниже содержание в нем таких примесей, как железо, алюминий, медь, мышьяк, сурьма и др. Повышение рН возможно до 5,2-5,4. При более высоких рН может гидролизоваться цинк и выпасть в осадок в виде гидроксида. Принцип противотока позволяет вести выщелачивание цинка во второй стадии крепкими растворами серной кислоты (130-150 г/л Н2SO4), а в первой стадии вести выщелачивание слабым раствором (50-60 г/л Н2SО4), в результате чего раствор, получаемый с первой стадии, не содержит кислоты (рН = 5,2:5,4). При таком выщелачивании нейтральный раствор содержит минимальное количество примесей, что упрощает и удешевляет его очистку перед электролизом.
Рис.14.1 Технологическая схема переработки цинковых концентратов на заводе Трейл (Канада)
[Шиврин Г.Н. Металлургия свинца и цинка.-М: Металлургия, 1982.]
В первой стадии выщелачивания (так называемый нейтральный цикл) решаются следующие технологические задачи:
· растворение из огарка сульфата цинка и некоторой части оксида цинка;
· нейтрализация серной кислоты в растворе, поступающем с кислого выщелачивания;
· гидролитическая очистка раствора от примесей;
· осветление раствора, отделение его от твердой фазы;
· утилизация тепла огарка.
Конечная цель нейтрального выщелачивания - получить цинксодержащий раствор, очищенный от гидролизующихся примесей.
Задачи второй стадии выщелачивания (кислый цикл):
· полное растворение цинка из огарка;
· по возможности избежание растворения примесей;
· окисление мышьяка и германия;
· очистка раствора от примесей;
· разделение фаз и отмывка растворенного цинка от твердой фазы.
Конечная цель кислого выщелачивания - получить кек, не содержащий растворимых соединений цинка.
Практика выщелачивания цинкового огарка. В зависимости от способа выщелачивания огарка доставку его из обжигового цеха в цех выщелачивания и классификацию осуществляют сухим или мокрым путем. Непременное условие периодического выщелачивания - транспортировка холодного огарка и его сухая классификация. Смесь огарка из обжиговой печи, и пыли из циклона, имеющую температуру 700-750°С, охлаждают в аэрохолодильниках, трубных или скребковых конвейерах. Охлажденную смесь классифицируют по крупности в аэросепараторах. Крупную фракцию (>0,3 мм) измельчают в шаровых мельницах, после чего снова классифицируют. Сухую транспортировку и классификацию применяют и при непрерывном выщелачивании. Обычно классификацию проводят в две стадии: нейтральную и кислую.
Рис.14.2 Влияние крупности огарка на продолжительность его растворения
[3, стр309]
Предварительная (нейтральная) классификация делит всю пульпу, поступающую на выщелачивание, на пески ( + 0,30 мм) и илы (-0,3 мм). Каждая фракция требует особого режима выщелачивания. Слив нейтральной классификации направляют на нейтральное выщелачивание. Песковой продукт нейтрального конуса выщелачивают отработанным электролитом (при остаточной кислотности пульпы 20- 60г/л Н2SO4).Выщелачивание песков ведут либо в механическом, либо в пневматическом агитаторе с добавкой марганцевой руды или пиролюзита МnО2 для окисления двухвалентного железа в трехвалентное. После выщелачивания пески снова классифицируют. Песковой продукт кислой классификации по составу мало отличается от цинковых кеков, получаемых после кислого выщелачивания. Поэтому его направляют на вельцевание. Слив нейтрального классификатора, содержащий иловую часть огарка, а также пыль циклонов и электрофильтров подают на нейтральное выщелачивание, которое обычно осуществляют в серии агитаторов пневматического типа, установленных последовательно.
Рис.14.3 Пневматическая мешалка (пачук)
[3, стр309]
Концентрация серной кислоты в первом агитаторе составляет 50-60 г/л. В процессе выщелачивания кислота нейтрализуется, а примеси, подвергающиеся гидролизу, переходят в осадок. Процесс гидролиза регулируют с помощью рН раствора дозировкой марганцевой руды в первый агитатор. В последнем агитаторе рН жидкой фазы пульпы повышается до 5,2-5,4.
Рис.14.4 Механическая мешалка:
1- чан; 2 - мешалка; 3 - труба для подачи пульпы; 4 - подогреватель; 5 - патрубок для выпуска пульпы
Пульпу из последнего агитатора нейтрального цикла направляют в сгустители. Слив нейтрального сгустителя обычно хорошо осветлен, содержание твердого в нем не превышает 1 г/л. Слив представляет собой конечный продукт выщелачивания. Его направляют на очистку от примесей, которые в условиях нейтрального выщелачивания не гидролизуются. Очищенный от примесей нейтральный раствор поступает на электроосаждение цинка.
Сгущенный продукт нейтральных сгустителей с отношением ж:т = 3:4 перекачивают в серию пневматических агитаторов кислого цикла, В первый агитатор кислого выщелачивания подают отработанный электролит, содержащий обычно 40 г/л цинка и 120-160 г/л серной кислоты, а также слив кислой классификации. В последнем агитаторе концентрация Н2SО4 снижается до 0,5- 1 г/л, а отношение ж : т достигает 10-12.
Пульпа из последнего агитатора кислого цикла поступает на сгущение. Сгущенный продукт направляют на рамные фильтры, где его фильтруют и промывают. Кек рамных фильтров репульпируют в горячей воде. Пульпу повторно фильтруют на дисковых фильтрах. Кек дисковых фильтров сушат и подвергают вельцеванию с целью отгонки цинка, свинца, кадмия и редких элементов.
Фильтраты рамных и дисковых фильтров объединяют со сливом кислых сгустителей и направляют на смыв и репульпацию огарка печей КС.
14.3. Очистка раствора сульфата цинка от примесей
Примеси в растворе сульфата цинка в соответствии со способами выведения их из раствора можно разделить на группы:
· Первая группа объединяет примеси, которые можно удалить из раствора гидролизом, осаждением, адсорбцией и коагуляцией: Fe, Cu, Al, As, Sb, In, Ge, Ga, SiO2. Гидролитическая очистка происходит при нейтральном выщелачивании огарка и сгущении нейтральной пульпы.
· Во вторую группу входят металлы, более электроположительные, чем цинк (Cu, Cd, Ni, Co, Tl), которые можно вывести из раствора цементацией металлическим цинком.
· Для удаления из раствора примесей третьей группы необходимо применять специальные реагенты, образующие с этими примесями труднорастворимые соединения. К этой группе относятся кобальт, хлорид-ион и фторид-ион.
· Примеси четвертой группы (калий, натрий, магний, марганец) не извлекаются применяемыми методами очистки растворов и накапливаются. Для поддержания их концентрации на определенном уровне приходится часть рабочего раствора выводить из процесса и заменять свежеприготовленным, не содержащим примесей этой группы.
Гидролитическая очистка. Гидролитическая очистка основана на способности катионов металлов в растворе взаимодействовать с водой с образованием труднорастворимых гидроксидов. При этом концентрация металла в растворе снижается - происходит очистка раствора.
В общем виде реакцию гидролиза катиона какого-либо металла выражают уравнением
Меn+ + n Н2О = Ме(ОН)n + nН+
где Меn+ - катион металла; n - заряд катиона.
Направление протекания реакции зависит от рН раствора: в кислой среде гидроксид металла будет растворяться, в щелочной - осаждаться.
Равновесие реакции гидролиза для каждого металла наступает при определенном рН раствора, называемом рН гидратообразования (рН°).
Таблица 14.2 Значения рНг для стандартных условий (аMen+ = 1 моль/л, t = 25 °С)
Катион металла | Со3+ | Sb3+ | Sn2+ | Fe3+ | Al3+ | Cu2+ | Zn2+ | Co2+ | Fe2+ | Cd2+ |
pHг | 1,0 | 1,2 | 1,4 | 1,6 | 3,1 | 4,5 | 5,9 | 6,4 | 6,7 | 7,0 |
При нейтральном выщелачивании рН пульпы поддерживают в пределах 5,2 - 5,4. При этом цинк еще не гидролизуется, но катионы Со3+, Sb3+, Sn2+, Fe3+, А13+ образуют нерастворимые в этих условиях гидроксиды. Катионы Со2+, Fе2+ и Сd2+ не гидролизуются и остаются в растворе. Катион Сu2+ гидролизуется частично.
Рис.14.5 Влияние концентрации катиона в растворе на рН осаждения гидроксидов металлов (по Б. В. Громову) [17 – стр.12]
При более высокой концентрации металла в растворе образование гидроксида начинается при меньшем значении рН. При повышении рН раствора концентрация гидролизуемого металла снижается. Из данных рисунка 11.14 следует, что для накопления в растворе нейтрального выщелачивания цинка до 100 - 120 г/л необходимо рН раствора поддерживать не выше 5,5. В противном случае произойдет гидролиз цинка и растворение его прекратится. Таким образом, при рН нейтрального выщелачивания возможно осаждение нерастворимых гидроксидов железа (III), мышьяка (III), сурьмы (III), алюминия, меди (II) и некоторых редких элементов.
Для полноты осаждения железа (поскольку часть его находится в закисной форме FeO и осаждается при рН = 8,5) его предварительно окисляют, используя для этого марганцевую руду или концентрат, анодный марганцевый шлам.
В условиях выщелачивания огарка железо осаждается в виде основных сульфатов или гидрата. Главный способ окисления закисного железа - окисление марганцевым (пиролюзитовым) концентратом:
2 FeSO4 + MnO2 + 2 H2SO4 = Fe2(SO4)3 + MnSO4 + 2 H2O
Реакция протекает в кислой среде при 5 - 8 г/л H2SO4 в отдельном окислительном чане. По данным В.Г.Агеенкова, окисление железа при кислотности, превышающей 5 г/л, заканчивается не более чем за 30 мин. При меньшей кислотности окисление затягивается, и образуются вязкие золи гидрата окиси железа.
Алюминий ведет себя аналогично трехвалентному железу. Гидролиз меди протекает не полностью по суммарной реакции:
CuSO4 + 2 H2O = Cu(OH)2 + H2SO4
Повышение рН раствора в процессе нейтрального выщелачивания сопровождается коагуляцией кремневой кислоты (золь переходит в гель).
Практически при рН = 5,2 - 5,3 содержание SiO2 снижается до 0,2 г/л.
Таблица 14.3 Соотношение между содержанием SiO2 в растворе
и рН начала коагуляции кремневой кислоты
Содержание SiO2, г/л | 12,0 | 8,0 | 2,0—2,5 | 1,0—2,0 |
рН начала коагуляции | 3,5—3,6 | 4,1—4,2 | 4,7—4 | 5,0—5,1 |
Очистка раствора цементацией.Цементацией называют окислительно-восстановительный процесс, сопровождающийся ионизацией и растворением более электроотрицательного металла и осаждением из раствора в эквивалентном количестве более электроположительного металла. Для осаждения из раствора какого-либо металла необходимо ввести в раствор металлический лист или металлический порошок металла - цементатора, который должен быть более электроотрицательным, чем цементируемый.
Чтобы использовать явление цементации для очистки раствора сульфата цинка, необходимо соблюсти обязательное условие: металлом - цементатором может быть только цинк. В противном случае металл - цементатор, растворяясь, загрязнит раствор.
В основе явления цементации лежит ионизация металла - цементатора:
Zn → Zn2+ + 2е
При этом произойдет реакция восстановления иона металла - примесей, который выделится из раствора на поверхности цинка в виде металла:
Меn+ + пе → Ме
Принять электроны от металлического цинка могут только более электроположительные металлы или элементы. Следовательно, цементацией цинком можно выделить из раствора примеси, более электроположительные, чем цинк.
Взаимное влияние примесей на эффективность цементационной очистки раствора нейтрального выщелачивания, как правило, положительно. Так, основная примесь – медь, ускоряет цементацию кадмия, никеля. Мышьяк, сурьма, теллур, ртуть также ускоряют цементацию никеля, кобальта. На заводах в качестве активирующей добавки для цементации кобальта применяют ортосульфоантимонат натрия Na3SbS4 · 9 Н2О (соль Шлиппе).
Повышение температуры ускоряет осаждение меди, никеля, кобальта, но ухудшает цементацию кадмия, который при повышенной температуре интенсивнее окисляется и растворяется.
Эффективность цементации зависит от интенсивности перемешивания раствора с порошком цинка. Перемешивание должно быть механическим. При пневматическом перемешивании цинк и кадмий окисляются кислородом воздуха до ZnО и СdО.
Очистка от меди. Метод цементации используется для очистки цинкового раствора от меди, кадмия и ряда других металлов (таллия и др.). Обычно с этой целью применяется цинковая пыль крупностью 0,054 - 0,074 мм. Очистка ведется в механических мешалках при автоматическом контроле чистоты раствора и автоматической дозировке цинковой пыли в одну или две стадии. Установки оборудованы указывающими приборами. Расход цинковой пыли составляет 30 - 45 кг на 1 т чушкового цинка.
После реакций:
CuSO4 + Zn = ZnSO4 + Cu
CdSO4 + Zn = ZnSO4 + Cd
Tl2SO4 + Zn = ZnSO4 + 2 Tl
остаточное содержание меди составляет 0,1 - 0,2 мг/л, кадмия 1 - 2 мг/л и менее. Осадки меди и кадмия фильтруют на фильтрпрессах и кек поступает в кадмиевый цех.
Во время операции, цементации следует принимать меры предосторожности против отравления арсином:
2 AsCl3 + 6 Zn + 6 H2O = 2 AsH3 + 3 ZnCl2 + 3 Zn(OH)2
Попутно выделяющийся при ведении этой операции водород взрывоопасен.
Таблица 14.4 Состав медно-кадмиевых кеков
Cd | 3,5 | 16-22 | 11,6 | 8-12 | 4,7 | 7,9 | 6,0 | 4,24 | 6,0 | 5,0 |
Zn | 37,5-40,0 | 25-35 | 33,4 | 36-40 | 34,3 | 31,0 | 27,0 | 43,8 | 39 | 40,5 |
Си | 12,5 | 8-10 | 7,4 | 1,8 | 19,1 | 17,4 | 22,0 | 8,6 | 12,6 | 12,2 |
Pb | 1,2 | 2,5 | 0,3 | 0,9 | 1,98 | 0,7 | ||||
As | 0,18 | 0,05 | 0,1 | 0,3 | ||||||
Fe | 0,85 . | 3,4 | ||||||||
Ni | 0,04 | 1,38 | ||||||||
Co | 0,02 | 0,03 | 0,0 |
Качество медно-кадмиевых кеков можно значительно улучшить, применяя фильтрацию слива сгустителей и предварительное осаждение меди, кроме того, фильтрация заметно снижает расход цинковой пыли. Часто применяют цинковую, пыль для очистки раствора от кобальта и никеля, подогревая его до 85 – 95 оС и вводя активирующие добавки - сульфат меди и триоксид мышьяка. Среда при этом слабо кислая (рН = 4). Цинковая пыль вводится порциями. Кобальт и никель удаляются этим способом до остаточного содержания 0,02 - 0,1 мг/л вместе с кадмием. После фильтрации производят две дополнительные очистки от кадмия. Всего, учитывая предварительную очистку от меди, используют 4 стадии очистки раствора. Очистку растворов можно вести непрерывно и периодически. Непрерывный вариант имеет значительные преимущества.
Очистка от кобальта. На заводах в качестве активирующей добавки для осаждения кобальта применяют ортосульфоантимонат натрия (соль Шлиппе), проводя очистку одновременно с цементацией меди и кадмия при температуре 50 – 60 оС. Такая операция продолжается примерно 1 час, в результате остаточная концентрация кобальта в растворе доводится до 1,0 - 2,0 мг/л. Далее кобальт выделяют в кадмиевом цикле. Второй раз кобальт осаждают после растворения медно-кадмиевой губки ксантогенатом в присутствии ионов меди (концентрация которых поддерживается около 20 - 40 мг/л) для окисления двухвалентного кобальта в трехвалентный:
CoSO4 + CuSO4 + 4 R-CS2Na = Со (R - CS2)3 + 2 Na2SO4
где R- этиловый радикал.
Очистку ведут в чанах с механическим перемешиванием при 40 – 50 oС в течение 2 ч. Остаточное содержание кобальта в очищенном растворе находится в пределах 1 - 2 мг/л. Расход ксантогената составляет 15 - 20 кг на 1 кг на сумму Со + Ni. Совместно с кобальтом частично осаждается кадмий. Состав первичных кобальтовых кеков примерно следующий: 12,4 - 23,3% Zn; 2,8 - 7,4% Со; 7 - 4,9% Cd; 2 - 8% Сu; ~1% Fe.
Химическая очистка от кобальта ведется а-нитрозо-Р-нафтолом (заводы «Рисдон», «Трейл», «Флин-Флон»).
Очистка от хлора. Хлор в виде ионов С1- накапливается в растворе до 500 - 800 мг/л при допустимом содержании 80 - 150 мг/л.
На заводах хлор из раствора выделяют в виде трудно растворимой полухлористой меди. В раствор вводят медный купорос и цинковую пыль, перемешивают пульпу в течение 1 часа и фильтруют. Происходит реакция
2 СuSО4 + Zn + 2 Сl- = Cu2С12 + ZnSО4 + SО42-
Остаточное содержание хлора составляет 100 – 150 мг/л. Весь цикл занимает около 5 ч. Иногда удается поддержать допустимое содержание хлора в цикле производства путем промывки водой вельц-окислов и сброса этой воды после выделения металлов.
Химически наиболее эффективной считается очистка от хлора с помощью сернокислого серебра, что позволяет практически полностью удалять хлор из раствора.
Удовлетворительных методов очистки растворов от ионов фтора нет. Иногда последний осаждают окисью кальция в виде CaF2, но при этом не менее 20 мг/л фтора остается в растворе. В последнее время появилась возможность выводить фтор с осадком ярозита.
Вывод части раствора из технологического цикла. Катионы калия, натрия, магния, марганца накапливаются в растворе цинкэлектролитного производства. Суммарная концентрация их достигает 15 - 30 г/л. При этом увеличиваются плотность и вязкость раствора, повышается его омическое сопротивление, что неблагоприятно сказывается на осаждении цинка и затрудняет процессы отстаивания и фильтрации пульп.
Для поддержания концентрации этих металлов на определенном уровне часть раствора систематически выводят из производственного цикла и перерабатывают с получением различных товарных солей. Обычно - это цинковый купорос для обогатительных фабрик.
На заводах в нейтральном растворе допускается следующее содержание примесей: 0,1 - 0,2 мг/л Сu; 30 - 50 мг/л Fe; 1 - 3 мг/л Со; 1 – 2 мг/л Na; 150 - 250 мг/л С1; 1 - 3 мг/л Cd; 0,1 мг/л As; 0,1 мг/л Sb; 0,2 - 0,4 г/л SiO2; 5 - 6 г/л Мn. Содержание уже 0,05 мг/л Ge приводит к резкому ухудшению показателей электролиза цинка. Плотность раствора близка к 1340 - 1370 кг/м3. Сильно влияют на выход по току органические примеси
Электролиз цинка.
Выделение цинка из очищенного раствора сульфата цинка с получением готового продукта осуществляют путем электролиза раствора. Для осуществления процесса подводят электрический ток к электродам электролизной ячейки: катоду и аноду. На катоде идет восстановление ионов Zn2+ из раствора до металлического состояния. На аноде электрическая энергия расходуется на анодные реакции.
При электролитическом рафинировании металлов на аноде происходит полезный процесс - растворение чернового металла. В случае же электролиза цинка анод растворять нельзя, так как металл анода или примеси, растворяясь, загрязнит раствор, а затем и цинковый катодный осадок. Полезных анодных реакций при электроосаждении цинка из раствора практически нет. Следовательно, при реализации электролитического восстановления цинка из раствора необходимо, чтобы продукты анодного процесса не загрязняли электролит, а сам процесс шел с минимальным расходом энергии; кроме того, выделяющиеся на аноде вещества не должны быть токсичными.
Теоретические основы электроэкстракции цинка из раствора. Цинк – один из наиболее электроотрицательных тяжелых металлов. Стандартные потенциалы цинка и водорода равны:
и
; В
Выделение на катоде более отрицательного цинка возможно благодаря высокому перенапряжению водорода на цинке (не менее 0,7 В), в то время как перенапряжение разряда ионов цинка составляет всего десятки милливольт. Поэтому в процессе электролиза необходимо соблюдать условия для высокого перенапряжения водорода. Все факторы, снижающие перенапряжение водорода, способствуют его разряду, коррозии цинка и приводят к снижению выхода по току.
Потенциал разряда ионов на катоде выражается уравнением Нернста:
где φ – потенциал восстановления иона на катоде, В; φ0 – стандартный потенциал восстановления иона на катоде, В; Т – температура электролита; R – универсальная газовая постоянная, R = 8,31 Дж/(моль·К); n –заряд иона; F – число Фарадея (F = 96 487 Кл/моль); а – активность иона в электролите, моль/л; Δφ – перенапряжение (поляризация) восстановления иона, В.
На катоде сначала восстанавливаются элементы с более электроположительным потенциалом. Для ионов цинка и водорода потенциалы разряда на катоде могут быть представлены следующими выражениями:
и
где – активность ионов цинка в растворе;
– активность ионов водорода в растворе, моль/л;
,
– перенапряжение цинка и водорода, В.
На перенапряжение водорода влияют материал катода, плотность тока, состав и температура электролита, состояние поверхности осажденного цинка.
Катоды для электролиза цинка изготавливают из алюминия, т.к. на нем водород выделяется с большим перенапряжением ( = 1,1 В). Зависимость перенапряжения водорода на цинке от катодной плотности тока при 25 °С выражается уравнением
= 0,77 + 0,118·lg iк
где iк – катодная плотность тока, А/м2.
Зависимость перенапряжения водорода от температуры приближенно можно выразить уравнением
(t)=
(25) – 0,16· lg (t/25)
где t – температура электролита, 0С; (t) ,
(25) – перенапряжение водорода на цинке, соответственно, при температуре электролита t и при 25 °С.
Как видно из уравнения, с повышением температуры электролита перенапряжение водорода снижается и это приводит к понижению выхода по току цинка. В кислых растворах перенапряжение водорода снижается с повышением концентрации кислоты.
При электролизе цинка большие затруднения вызывают катионы металлов-примесей, которые способны восстанавливаться на катоде. Совместное осаждение на катоде цинка и металла-примеси становится термодинамически возможным, когда электродный потенциал металла-примеси более положительный или равен потенциалу цинка.
Ионы металлов, более электроотрицательных, чем цинк (алюминий, натрий, калий, магний, марганец), не восстанавливаются на катоде, т.к. практически невозможно создать условия для их совместного разряда с цинком. Так, для ионов Mn2+, Na+, Mg2+ совместный разряд c цинком возможен при их концентрации в растворе 1016, 1034, 1055 г/л.
Но накопление катионов этих металлов в электролите ведет к повышению вязкости и удельного сопротивления электролита, вследствие чего увеличивается напряжение на ванне и возрастает расход электроэнергии при электролитическом выделении цинка.
Ионы металлов, более электроположительных, чем цинк, восстанавливаются на катоде при любых условиях. При этом одни металлы (кадмий, свинец, железо) только загрязняют катодный цинк и существенно не влияют на выход по току. Другие металлы-примеси (медь, кобальт, сурьма, никель) сильно влияют на выход по току цинка. Эти металлы, восстанавливаясь на цинковом катоде, образуют микрокатод, на котором при данной плотности тока перенапряжение водорода становится ниже, чем на цинке, и начинается интенсивное выделение водорода при электролизе.
Кроме того, металлы примеси, имеющие более высокий потенциал, чем у цинка, образуют на поверхности цинкового катода многочисленные гальванические микроэлементы типа: Zn/H2SO4/Me, где Me – Cu, Ni, Co, Sb. Работа этих короткозамкнутых микроэлементов приводит к растворению катодного осадка цинка, так как цинк в этих элементах выполняет роль анода.
Влияние примесей на электроосаждение цинка. В процессе очистки раствора не удается полностью удалить все примеси. Наиболее серьезные затруднения при электроосаждении цинка доставляет группа металлов, катионы которых способны восстанавливаться на катоде и загрязнять цинк.
Анодный процесс: Zn → Zn2+ + 2е
Катодный процесс: 2 Н+аq + 2е → Н2 (на металле-примеси)
Подавить работу этих элементов и уменьшить коррозию цинка можно, если создать условия, при которых на катоде протекал бы процесс:
Zn2+ + 2е → Zn (на металле-примеси)
Этого добиваются путем увеличения катодной плотности тока. При этом возрастает перенапряжение водорода на всех металлах, что затрудняет процесс и благоприятствует протеканию реакции восстановления цинка.
Плотность тока, при которой процесс восстановления цинка протекает преимущественно, а процесс разряда ионов водорода практически подавляется, называют критической. Другими словами, под критической плотностью тока понимают минимальную плотность тока, при достижении которой на данном металле идет восстановление цинка из раствора.
Таблица 14.5 Критическая плотность тока на гладких катодах
Металл | Al | Co | Ni | Fe | Cu |
Плотность тока iкр, А/м2 | 70-80 | 80 | 230 | 250 | 250 |
Однако если на полированной поверхности катода критическая плотность тока достигается легко, то на электролитически осажденной поверхности она возрастает в несколько раз. Поэтому в реальных условиях электролиза не всегда удается достичь критической плотности тока. Вследствие этого полностью локализовать вредное действие таких примесей, как никель, кобальт, сурьма, в производственных условиях практически невозможно. Тем не менее, увеличение плотности тока всегда повышает выход по току.
Накопление электроположительных (относительно цинка) примесей в катодном цинке происходит пропорционально концентрации примеси в электролите. Изменение концентрации серной кислоты в электролите от 48 до 200 г/л, а также температуры электролита от 20 до 35 °С мало изменяет степень осаждения всех примесей. Вредное действие примесей отражается в первую очередь, на снижении выхода по току цинка за счет увеличения выхода по току водорода. При этом такие примеси, как медь, мышьяк, рений, при Сме <0,5 мг/л в малой степени снижают выход по току в отличие от кобальта и никеля, которые сильно снижают выход по току, особенно при СМе >2 мг/л.
Повышение концентрации меди приводит к снижению выхода по току, коррозии цинка и алюминиевых катодов. Кадмий не снижает выхода по току. Сурьма при концентрации 0,1 мг/л заметно снижает выход по току, а при 1 мг/л коррозия идет так интенсивно, что от катода отслаиваются тонкие слои цинка. В присутствии селена и теллура на катодном осадке возникают вертикальные борозды и мелкие сквозные отверстия с небольшим растворением цинка вокруг отверстий со стороны алюминиевой матрицы.
Особенно опасная примесь - германий. При концентрации его в электролите свыше 1 мг/л осаждение цинка на катоде может совсем прекратиться. Германий, как и селен, но в значительно большей степени способствует образованию в осадке мелких сквозных отверстий, увеличенных со стороны матрицы. Вредное действие германия возрастает в присутствии кобальта и сурьмы.
Возникновение отверстий в осадке объясняют образованием летучих гидридов примесей, которые, удаляясь, сильно разрыхляют поверхность осадка. Поскольку вредное действие примесей связано с ухудшением структуры катодного осадка, с увеличением его шишковатости и пористости, то одной из мер противодействию этому является введение в электролит поверхностно-активных веществ (ПАВ), которые, адсорбируясь на активных точках роста кристаллов, затормаживают разряд ионов цинка или ионов водорода в этом месте. Осадки становятся более плотными и гладкими, фактическая плотность тока возрастает, приближаясь к расчетной. При электроосаждении цинка в качестве ПАВ применяют столярный клей и желатину.
Таблица 14.6 Показатели процесса электроосаждения цинка на прерывистом и постоянном токе:
Плотность тока, А/м2 | 600 | 700 | 800 | 1000 |
Выход цинка по току, %: | ||||
· прерывистый ток | 94,6 | 92,3 | 90,2 | 86,2 |
· постоянный ток | 91,2 | 90,6 | 89,4 | 85,2 |
Удельный расход электроэнергии, кВт-ч/т: | ||||
· прерывистый ток | 2820 | 2860 | 2910 | 3180 |
· постоянный ток | 3010 | 3040 | 3170 | 3420 |
Напряжение на ванне, В: | ||||
· прерывистый ток | 3,19 | 3,32 | 3,39 | 3,49 |
· постоянный ток | 3,29 | 3,41 | 3,50 | 3,60 |
Результаты испытаний свидетельствуют о перспективности интенсификации электролиза цинка с применением прерывистого тока.
Практика электролиза цинка.Электролиз очищенных цинковых растворов осуществляется в ваннах, аналогичных по конструкции ваннам, используемым для электролиза меди. Цех в плане имеет форму прямоугольника.
Применяют ванны из сборного железобетона (иногда стальные) с защитой из кислотоупорных материалов типа асфальта или убракса с обклейкой рубероидом на битуме в два слоя и вкладышем из 8 мм винипласта. Из винипласта делается и обортовка ванн, и сливные коробки. Снаружи ванны окрашивают кислотоупорной краской или битумом или обклеивают резиной (по стали). В дне ванн имеется отверстие для выпуска шлама. Известны случаи сооружения ванн из армированных пластмасс.
На старых заводах ванны длинными бортами устанавливают рядом и, таким образом, объединяют в блоки (каскады) по 20 - 30 ванн. В случае выхода из строя ванна может быть заменена новой. Каскады располагают перпендикулярно продольной оси цеха с проходами между ними.
На новых заводах принята более удобная расстановка: ванны устанавливают длинными сторонами поперек пролета попарно. Однако в этом случае значительно увеличивается расход меди на ошиновки. В проходы между рядами ванн в обоих случаях может заезжать электрокар.
Циркуляция электролита индивидуальная. Ток от ванны к ванне передается путем контакта разноименных электродов. Для лучшего распределения тока электроды соединяют на уравнительной трехгранной промежуточной медной шинке.
Рис. 14.3 Схема железобетонной электролизной ванны для электроосаждения цинка:
1 – рама; 2 – винипластовая прокладка; 3 – изолятор; 4 – корпус; 5 – сливной носик;
6 – отверстие для стока электролита [7, стр.157]
Размеры ванн находятся в следующих пределах: длина 1 - 4 м, ширина 0,85 м, глубина 1,3 -1,4 м. Для заводов Казахстана и России типичны ванны длиной 2,0 - 2,3 м с 28 -33 парами электродов. Кроме винипластовой, широко применялась футеровка (обкладка) из рольного свинца. В настоящее время ванны изготовляют из полимербетона, не требующего дополнительной футеровки.
Нерастворимые аноды изготавливают из свинца с добавкой 1% Ag, что снижает их коррозию. Этому же способствует обработка анодов горячим раствором (80 °С, р-р КМnO4 + H2SO4). Толщина анода 5 - 8 мм, катоды применяют из листового алюминия толщиной 3 - 4 мм. Практически оправдали себя аноды толщиной 6 - 8 и катоды 4 мм. Лучше служат 8 мм катаные аноды с почти гладкой поверхностью. Срок службы анодов до 4 лет. В СССР были разработаны аноды из сплава Pb – Ag - Т1 - Са примененные на Челябинском цинковом заводе. Края катодов защищают резиновыми рейками, предупреждающими срастание цинка и образование дендритов. От края катода до борта ванны оставляют 70 - 75 мм. Типичные размеры катода следующие: полная высота -1100 мм, рабочая высота ~900 мм, ширина ~660 мм, рабочая поверхность 1,2 - 1,25 м2. Полная высота анода соответственно 1100 мм, ширина 640 мм. Катоды подвергают систематической чистке 1 раз в 10 дней на катодоочистительной машине. Аноды очищают 1 раз в 20 - 25 дней. Износ катодов равен ~1,5 кг, а анодов 0,8 - 1,5 кг на 1 т цинка.
Во время электролиза на катоде осаждается металлический цинк, на аноде выделяется газообразный кислород, в растворе образуется H2SO4:
· На катоде Zn2+ + 2 e = Zn
· На аноде H2O – 2 e = 2H+ + ½ O2
· В ванне ZnSO4 + H2O = Zn + H2SO4 + ½ O2
Вследствие выделения кислорода электролит в ванне хорошо перемешивается, но несколько разбрызгивается. Чтобы оздоровить атмосферу в цехе, в электролит вводят экстракт мыльного корня или лакрицы (около 150 г/т цинка).
Электролиз ведут в кислой среде (120 - 200 г/л H2SO4). Поэтому при сравнительно высокой кислотности маловероятен разряд ионов гидроксила, концентрация которых очень мала (10-12 - 10-14 моль/л). Ввиду высокого потенциала процесса исключается разряд ионов SO42- . Следовательно, на аноде могут разряжаться молекулы воды при потенциале 1,24 В.
где - изменение энергии Гиббса реакции, протекающей в ванне (
= 100 ккал);
F - число Фарадея.
По расчету получим Нр = 2,10 В.
Напряжение разложения ZnSO4 при активностях Н2O и Zn2+, равных 1, равно
1,24+ 0,76= 2 В. С другой стороны, перенапряжение кислорода на анодном сплаве Рb - Ag близко к 0,35 В и напряжение разложения составляет величину 2,35 - 2,45 В или 2,40 ± 0,05 В.
В общем виде зависимость перенапряжения водорода, В, от плотности тока, А/см2, на цинке выражается уравнением
Вид кривых потенциал разряда - плотность тока для цинка и водорода доказывает, что их совместный разряд маловероятен. На практике разряд водорода в пределах 5 - 6% все же имеет место вследствие образования участков со сплавами цинк - примесь, на которых перенапряжение водорода снижается.
Для расчетов полного напряжения на ванне необходимо еще знать сопротивление электролита и расстояние анод - катод. Сопротивление электролита понижается с увеличением температуры и повышается с ростом концентрации цинка. В рабочих пределах кислотности 120 - 200 г/л, при содержании цинка 40 г/л и температуре 35 °С сопротивление растет почти линейно от 2 Ом.см при 200 г/л до 3,2 Ом.см при кислотности 120 г/л. Для расчетов электропроводности А.Ф.Никифоровым предложено уравнение:
; ом-1.см-1
где К - кислотность, г/л; Ц - содержание цинка, г/л; t - температура, С°.
Межэлектродное расстояние обычно измеряют от центра до центра между одноименными электродами. В настоящее время расстояние анод - анод на заводах СНГ можно считать равным 58 ± 2 мм. На зарубежных заводах оно составляет 67 - 90 мм, типично 75 мм. При сближении электродов до 60 мм на анод устанавливают винипластовые ограничители, предупреждающие короткие замыкания анода с катодом. При катаных анодах для этого достаточно установить на нижнем крае анодов два кольца или ролика. Иногда можно ограничиться катодными рейками.
Потеря напряжения в электролите равна
где l - расстояние анод - катод, см; а - толщина анода, см; k - толщина катода, см; D - плотность тока, А/см2; р - удельное сопротивление электролита, Ом.см.
При наличии в электролите примесей натрия, магния и алюминия сопротивление электролита возрастает ориентировочно на 2% на каждый 1 г примеси в литре. Эти примеси, кроме того, несколько снижают выход по току.
Потери в контактах в сумме составляют 0,03 - 0,04 В.
Общее напряжение на ванне Uв определяется уравнением:
где I - сила тока, А; RЭл - сопротивление электролита, Ом; RKон - сопротивление контактов, Ом; RШл -сопротивление слоя шлама, Ом.
В практике UВ = 3,3 + 3,6 В, что указывает на необходимость своевременной чистки анодов от шлама, так как сумма всех прочих величин, кроме IRШл, равна ~3,2 В. Из них около 2,4 В приходится на анодный процесс (около 67%).
Отмечен, поскольку это существенно для интенсификации процесса, небольшой рост потенциалов анода и катода с повышением плотности тока от 400 до 1000 А/м2. Прочие потери напряжения растут быстро, почти прямо пропорционально D. Удовлетворительные результаты при электроосаждении цинка можно получить начиная с D = 250 А/м2 при содержании цинка в электролите не менее 40 г/л, температуре не выше 35 – 45 °С и кислотности около, 100 г/л. Обычно заводы работают на плотностях тока 400 - 700 А/м2.
Исследования Г.Н.Пахомовой в заводских условиях показали возможность хорошей работы при D = 700 А/м2, содержании цинка 50 г/л, кислотности 135 г/л и расходе клея 450 г/т цинка. Обычный расход клея 200 - 300 г/т. Некоторые зарубежные заводы работают при плотностях тока около 800 А/м2 и, как исключение, при 1100 А/м2. Высокой плотности тока соответствует более высокая кислотность.
Эффективность использования электроэнергии в процессе электролитического осаждения цинка оценивают по удельному расходу электроэнергии на 1 кг катодного цинка, который вычисляют по уравнению
Wуд = Uв·1000/(qZn· ηт) = 819,7 (U/ηт)
где Wуд – удельный расход электроэнергии, кВт·ч/кг; Uв – напряжение на ванне, В; ηт – выход по току, %; qZn – электрохимический эквивалент цинка (1,22 г/(А·ч)).
Выход по току в производстве цинка обычно равен 90 ± 2%. Расход электроэнергии постоянного тока
; кВт.ч/т цинка
Путем статистической обработки производственных данных и математической модели процесса электролиза проф. А. Бенуни нашел, что расход электроэнергии W равен:
где - выход по току, %; Q - производительность ванны, т/сут; U - напряжение на ванне, В.
В этой же работе найдено, что основными факторами, влияющими на процесс электролиза цинка, являются температура, плотность тока, кислотность и расход клея. Для получения высокого выхода по току температуру электролита необходимо поддерживать в пределах 35 – 40 °С. Охлаждение электролита может быть индивидуальным в каждой ванне с помощью алюминиевых или углеродистых змеевиков или централизованное вакуум - испарительное при 6 - 12-кратной циркуляции раствора.
Для расчета скорости подачи нейтрального раствора в ванну следует пользоваться следующей формулой:
где v - подача нейтрального раствора, л/ч; I - сила тока в цепи, А; выход по току, доли ед.; Цн - содержание Zn в нейтральном растворе, г/л; Ц0 - содержание Zn в отработанном электролите, г/л.
Сдирка цинка с алюминиевых катодов производится раз в сутки, иногда раз в двое суток. Для облегчения сдирки по предложению Г.М.Штейнгарта в период установки катодов в ванну подают раствор «рвотного» камня из расчета 0,2 мг/л Sb. Эту добавку частично вводят непрерывно с клеем и частично единовременно во время сдирки. По данным В.В.Стендера, облегчает сдирку и применение катодов из листов сплава Al (~99) + Ti (~l). Ha ряде заводов осуществлена машинная сдирка.
Таблица 14.7 Состав отработанного электролита заводов, г/л:
Завод | Zn | h2so4 |
«Корпус-Кристи» (США) | 50 - 60 | 200 |
«Силвер-Кинг» (США) | 50 | 270 |
«Монсанто» (США) | 95 | 200 |
«Грейт-Фоле» (США) | 45 | 100 – 1 50 |
«Валлифилд» (Канада) | 65 | 190 |
«Трейл» (Канада) | 70 | 100 |
«Флин-Флон (Канада) | 55 | 110 -120 |
«Порто-Маргера» (Италия) | 70 | 130 |
«Рисдон» (Австралия) | 50 | 90 |
Япония | 40 | 190 |
Челябинский ЦЗ (Россия) | 46 | 140 |
«Электроцинк» (Россия) | 38 | 117 |
УКСЦК (Казахстан) | 45 | 190 |
ЛЦЗ (Казахстан) | 40 | 150 |
Чистота катодного осадка зависит от чистоты нейтрального раствора и состояния анодов, которые не только окисляются, но и несколько растворяются. Содержание свинца в электролите может достигать 4 - 7 мг/л, оно повышается с увеличением концентрации в электролите хлора. Примеси более электроположительные, чем цинк, разряжаются на предельном токе и, следовательно, выделяются из раствора не полностью. В катодный осадок переходит 5 - 20% примесей (Сu, Sb, Co, Fe, Ni) от их содержания в подаваемом растворе.
Образующийся при электролизе на анодах шлам состоит из двуокиси марганца и из соединений свинца. Примерный состав шлама: 70% МnO2; 10 - 14% Pb; до 2% Zn. Он используется для окисления железа при выщелачивании огарка.
Съем цинка с 1 м3 раствора за один цикл электролиза составляет 80 - 120 кг. На некоторых заводах он выше: на «Корпус-Кристи» 135 кг и на «Силвер-Кинг» 180 кг. При высоких съемах уменьшается объем необходимого оборудования в цехах выщелачивания и электролиза.
Таблица 14.8 Основные показатели электролиза цинка на заводах СНГ следующие:
Плотность тока, А/м2 | 550—650 |
Кислотность отработанного электролита, г/л | 115—200 |
Съем цинка с 1 л раствора, г | 90—120 |
Выход цинка по току, % | 89—92 |
Расход электроэнергии (постоянный ток), кВт. ч/т | 2900—3150 |
Переплавка катодного цинка.
Катодный осадок цинка в отличие от других металлов (например, меди и никеля) не является конечным товарным продуктом цинкового завода. Катодные листы имеют развитую поверхность и при хранении на воздухе легко окисляются. Кроме того, их неудобно хранить, они малопригодны для потребителей, так как при их переплавке возникает угар. Поэтому ГОСТ предусматривает выпуск цинка в виде чушек определенной формы и массы.
Катодный цинк переплавляют в печах с добавкой флюса - хлористого аммония (0,5-0,6 % от массы цинка). Хлористый аммоний разрушает оксидную пленку на поверхности катодных листов и способствует слиянию корольков расплавленного металла. При последующей переработке дроссов, полученных при разливке цинка, в цикл выщелачивание - электролиз вводят хлорид-ион, поэтому желательно заменять хлористый аммоний другими флюсами.
Раньше на старых заводах переплавку катодного цинка вели в отражательных печах. В настоящее время отражательные печи заменены индукционными, в которых вторичной обмоткой является расплавленный цинк. В индукционных печах потери металла в виде дросса и угара уменьшаются в 2-3 раза по сравнению с отражательными печами, производительность труда возрастает в 6-8 раз. Производительность индукционных печей составляет от 100-120 (стандартная печь емкостью 20 т) до 350- 500 т/сут.
Выход чушкового цинка от массы катодного осадка - около 98%. Потери цинка на угар могут достигать 0,3-0,4 %, в дроссы и пыль переходит до 2 % катодного цинка. Разливку на большинстве отечественных заводов производят карусельными разливочными машинами. Более удобными для обслуживания индукционных печей большой производительности являются прямолинейные разливочные машины, позволяющие разместить параллельно два ряда изложниц. Такие машины установлены на ряде отечественных и зарубежных заводов.
В итоге при гидрометаллургическом процессе производства получают: цинк, кадмий, свинцовый кек, клинкер (Ag, Au, Сu и редкие металлы), товарные индий, германий, таллий, галлий, серную кислоту, ртуть, шламы, содержащие селен и теллур.
Общий расход электроэнергии на 1 т цинка в чушках составляет 3450 - 3800 кВт.ч/т.
Примерное извлечение в готовую продукцию из сырья по зарубежной и отечественной практике следующее: 94-97% Zn; 85-90% Cd; 85-88% Pb; 80-90% Сu; 90% Ag; 75% Аu; до 90% S. Извлечение редких металлов учитывается менее точно. В ряде случаев оно составляет 35-40% от содержания в исходном сырье.
Дата добавления: 2018-06-01; просмотров: 355; Мы поможем в написании вашей работы! |
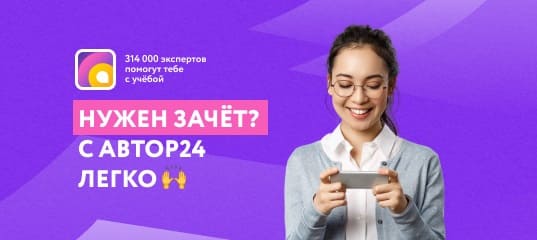
Мы поможем в написании ваших работ!