Обжиг цинковых концентратов в печах «КС» в гидрометаллургии.
На гидрометаллургическую переработку поступают сульфидные цинковые концентраты, содержащие, %: 45- 60 Zn; 29-35 S; 6-12 Fе; 1,5-5,0 А1203; 0,2-4,0 Рb; 0,1- 3,0 Сu; 0,4-3,05 SiO2; 0,5-1,5 СаО; 0,2-1,0 МgО; 0,25- 0,80 Сd; 0,01-0,4 Аs; 0,01-0,3 Sb, а также 20-160 г/т Аg и 0,5-10 г/т Аu.
Сульфид цинка ZnS практически нерастворим в разбавленных кислотах. Выщелачивание его в концентрированной серной кислоте (60-65 % Н2SО4) возможно при 150-170 °С, в автоклавах при высоких парциальных давления кислорода. Поэтому перед выщелачиванием цинковые сульфидные концентраты подвергают окислительному обжигу, продукты которого хорошо растворимы в разбавленных растворах серной кислоты при низких температурах.
При окислительном обжиге цинковых концентратов стремятся получить огарок, как можно полнее соответствующий требованиям последующих гидрометаллургических процессов. Очень важно, чтобы продукт обжига был порошкообразным. Чем мельче порошок, тем выше скорость его выщелачивания. Обжиг следует вести в основном с получением оксида цинка ZnО и некоторого количества сульфата цинка ZnSО4.
Несмотря на то что сульфатизирующий обжиг происходит при более низких температурах, чем окислительный, а следовательно, более экономичен и что сульфат цинка растворим в воде, тогда как для растворения оксида цинка требуется кислота, переводить весь цинк в форму водорастворимого сульфата нецелесообразно. Дело в том, что в процессе электролитического выделения цинка из сульфатного раствора образуется большое количество серной кислоты, которая может быть использована в случае выщелачивания оксидов металлов; отработанный электролит, содержащий 120-160 г/л Н2SО4, хороший растворитель оксидного огарка. В случае выщелачивания сульфатного огарка отработанный электролит использовать в качестве растворителя нельзя, из него предварительно нужно удалить избыток кислоты. А это более трудная задача, чем обжиг ZnS до ZnО.
|
|
Для компенсации потерь серной кислоты в последующих переделах в огарке оставляют до 2-3 % сульфатной серы. Остаточное содержание сульфидной серы в огарке не должно превышать 0,5 %. Обжиг следует вести таким образом, чтобы предотвратить образование труднорастворимых в слабокислых растворах ферритов цинка, силикатов цинка, способствующих загрязнению раствора кремнекислотой, а также кислоторастворимых оксидов железа и кремния. Обжиговые газы должны быть достаточно концентрированными по SО2 для получения серной кислоты контактным способом (>3,5 % SО2).
Наиболее полно удовлетворяет перечисленным требованиям обжиг в печах кипящего слоя (КС). Поэтому в настоящее время на всех цинковых заводах обжиг ведут в печах КС.
|
|
Рис. 12.4 Печь для обжига концентратов в кипящем слое;
1- шахта печи; 2- подина печи; 3- воздушная коробка; 4- питатель; 5- порог для выгрузки огарка; 6,7 - газоход; 8 - кессон трубчатый (амбразура); 9- загрузочная камера
Высота печи составляет 7-12 м, диаметр 5-7 м, площадь пода 20-40 м2, глубина кипящего слоя 0,8-1,2 м. Подина с соплами - наиболее важная часть печи КС. Конструкция подины и ее работа в значительной степени определяют процесс кипения слоя концентрата, аэродинамику кипящего слоя, качество огарка, производительность и длительность кампании печи, дутьевой режим. Подину делают из жаростойкого бетона толщиной 200-300 мм, выкладываемого на стальном листе (решетке) толщиной 14-30 мм. В подину вмонтированы воздухораспределительные сопла. Воздух в печь подают в воздушную камеру под подиной. Воздух, проходя через отверстия в соплах в рабочее пространство печи, пронизывает находящийся на подине слой обжигаемого материала, приводя его в псевдожидкое состояние. Этот слой движется по поду от загрузочной камеры до сливного порога, перетекает через него и выгружается из печи.
Затраты на создание кипящего слоя значительно ниже, чем для перевода всего материала во взвешенное состояние, а интенсивность перемешивания материала с газом в кипящем слое велика (примерно в 1000 раз больше, чем в фильтрующем слое). Поэтому обжиг в кипящем слое экономичен и обеспечивает высокую производительность печи.
|
|
Необходимо отметить, что цинковый концентрат представляет собой полидисперсный материал, поэтому некоторая часть его (наиболее мелкая) выносится потоком газа из слоя, переходит во взвешенное состояние и уносится с газовым потоком из печи.
Обжиг проводят при температуре кипящего слоя 920-980 °С. Температура отходящих газов под сводом печи равна 900-950 °С, перед циклонами 500-600 °С. В процессе обжига цинкового сульфидного концентрата в зоне кипящего слоя создается чрезмерно высокая температура.
Рис.12.5 Сопла печей КС:
а- сопло с двойной решеткой; б- канадское сопло; в- сопло конструкции Североникеля и Беловского завода; г- щелевое сопло Челябинского ЦЭЗ; д- сопло конструкции УКСЦК
Печные газы после охлаждения в котлах-утилизаторах или стояках поступают в циклоны, откуда эксгаустером передаются в электрофильтры. Газы электрофильтров, содержащие 0,08-0,15 г/м3 пыли и 10-12 % SО2, направляют в сернокислотное производство. Около 95 % выносимой пыли осаждается в стояках, газоходах, циклонах и 4-6 % в электрофильтрах. Система пылеулавливания обеспечивает очистку газов от пыли на 99,5 %.
|
|
В настоящее время обжиг в печах КС практически вытеснил все другие способы обжига. Достоинства обжига в кипящем слое:
· удельная производительность печи КС в 3-4 раза выше, чем в многоподовых печах, и в 1,5-2,0 раза выше, чем при обжиге во взвешенном состоянии;
· содержание в огарке сульфидной серы при обжиге в печах КС составляет 0,2-0,3 % вместо 0,2-0,5'% при обжиге во взвешенном состоянии и 0,3-1,0% во многоподовых печах;
· не требуется предварительная сушка концентрата, возможно питание печи КС не только влажным концентратом, но и пульпой концентрата;
· процесс обжига в печах КС легко поддается автоматизации;
Ниже приведены типовые технологические показатели работы обжиговых печей КС цинковых заводов.
Таблица 12.3 Показатели обжига цинковых концентратов в печи КС
Показатель | Величина |
Температура, °С: | |
· слоя | 900-980 |
· под сводом | 880-950 |
· перед циклоном | 550-600 |
· перед электрофильтром | 300-350 |
Расход воздуха на печь, тыс. м3/ч | 12-17 |
Давление воздуха, кПа | 15-25 |
Производительность печи, т/сут | 125-160 |
Удельная производительность, т/(м2-сут) | 4,5-5,0 |
Выход продуктов обжига в КС, %: | |
· огарка | 60-65 |
· пыли из циклонов | 35-40 |
· пыли из электрофильтров | 2-5 |
Содержание цинка в огарке, %: | 60-62 |
· кислоторастворимого | 56-59 |
Доля кислоторастворимого цинка от содержания в огарке, % | 93-95 |
Дата добавления: 2018-06-01; просмотров: 1617; Мы поможем в написании вашей работы! |
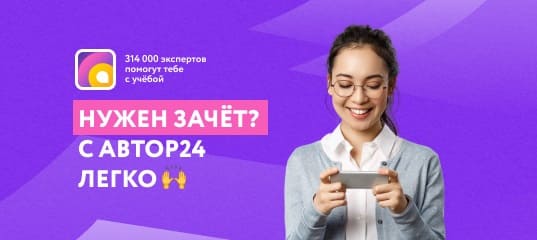
Мы поможем в написании ваших работ!