Окончательное (качественное) рафинирование
В задачу этой стадии входит очистка свинца от кальция, магния и сурьмы, оставшихся после обезвисмучивания, и от цинка, если не проводилась операция обесцинкования. Исходный свинец содержит: 0,1% Mg; 0,05% Са; 0,003% Sb; 0,4-0,5% Zn.
Очистка свинца от указанных примесей проводится окислительным методом в присутствии NaOH и иногда с добавкой NaNO3. Все примеси обладают высоким сродством к кислороду и легко удаляются из свинца. Температуру свинца в котле поднимают до 450 °С, на поверхности ванны расплавляют едкий натр и перемешивают ванну. Расход NaOH равен 2-3 кг/т, NaNO3 0,5 кг/т.
Операция длится 2-4 ч, к концу ее температура свинца поднимается до 600 °С. Выход оксидов, содержащих 40-70% Pb, составляет 3-4% от массы свинцовой ванны. Оксиды направляют в агломерационный цех и перерабатывают совместно с основным сырьем; иногда плавят отдельно, что менее целесообразно.
Разливка свинца
Свинец разливают, либо на прямолинейной, либо карусельной машинах в чушки массой 30-40 кг. Иногда отливают блоки массой ~1 т. Транспортировка чушек от разливочной машины на склад производится автопогрузчиками или электрокарами. Температура свинца при разливке 450-470 °С. Скорость разливки 30-35 т/ч.
Таблица 11.3 Баланс свинца при огневом рафинировании
Завод 1 | Завод 2 | |
Рафинированный свинец | 92,4 | 76,5 |
Висмутистый свинец | 0,9 | 1,2 |
Серебристая пена | 0,9 | 1,0 |
Шликеры | - | 9,1 |
Окислы | - | 11,9 |
Жидкие плавы | 0,1 | - |
Окислы качественного рафинирования | 1,7 | - |
Штейн товарный | 0,4 | - |
Оборотные продукты | 3,5 | - |
Потери | 0,1 | 0,3 |
Итого | 100,0 | 100,0 |
Завод 1 проводит непрерывное обезмеживание свинца и смягчение с получением жидких плавов. Завод 2 получает свинец с содержанием 1,4% Cu; при увеличении содержания меди до 2-3% эта цифра возрастает до 15-20%. Завод 2 обезмеживает свинец в котле с получением шликеров и смягчает с получением твердых окислов (плавы).
|
|
Непрерывное обезмеживание и смягчение свинца с получением жидких плавов позволяет значительно повысить (на 16%) выход свинца в рафинированный металл и снизить потери его при последующей переработке полупродуктов.
Рис 11.5 Карусельная машина для разливки свинца (продольный разрез и план):
1-электродвигатель; 2-червячный редуктор; 3-стойка (тумба); 4-ведущая шестерня; 5-кронштейн; 6-вытяжной кожух; 7-изложница; 8-водяное охлаждение; 9-каток; 10-опорное кольцо; 11-упорный ролик; 12-заливочный ковш; 13-соединительный угольник; 14-корпус карусели; 15-зубчатый венец; 16-площадка [4, стр667-669]
Достоинство пирометаллургического рафинирования свинца - высокая производительность процессов, низкие капитальные и эксплуатационные затраты, простота операций рафинирования и переработки промпродуктов. Затраты труда составляют 1-2 чел-ч на 1 т рафинированного свинца.
|
|
Электролитическое рафинирование свинца.
Некоторые заводы применяют электролитическое рафинирование свинца. Преимущество его заключается в возможности очистки свинца в одну-две стадии с получением металла высокой чистоты, недостаток - экстенсивность и очень сложная схема переработки шлама.
В качестве электролита используют раствор кремнефтористоводородной кислоты H2SiF6 и PbSiF6 хорошо растворяющий свинец и отличающийся хорошей электропроводностью. При растворении анода цинк, железо, никель, олово как более отрицательные переходят в электролит, а серебро, золото, медь, висмут, мышьяк, сурьма как более положительные образуют шлам. При электролизе свинца наиболее нежелательными примесями являются медь и олово. Медь способствует поляризации анода и переходу в раствор, а затем на катод сурьмы, мышьяка и других примесей, загрязняющих свинец. Олово обладает близким к свинцу потенциалом и при небольшой поляризации осаждается совместно со свинцом на катоде. В связи с этим перед электролизом свинец рафинируют от меди и олова, после чего отливают аноды.
|
|
Электролиз проводят в железобетонных ваннах, футерованных винипластом или кислотоупорной керамикой на гидроизоляции. Объем ванн до 6 м3. В ванну завешивают 24 анода и 25 катодов. Аноды отливают на карусельной машине. Их масса 150 - 200 кг, толщина 30 - 40 мм. В качестве катодов применяют - свинцовые листы толщиной 1 мм.
Электролит содержит 70 - 90 г/л свинца в виде PbSiF6 и 80 - 100 г/л кислоты H2SiF6 . Добавками, способствующими получению плотного осадка свинца, служат столярный клей или желатин, которые расходуют в количестве 0,1 г/л. Электролитическое рафинирование свинца проводят при низкой плотности тока: 160 - 220 А/м2. Расстояние между электродами 30 - 50 мм. Напряжение на ванне: 0,3 - 0,4 В (начальное) и 0,6 - 0,8 В (конечное). Температура электролита 30 – 50 °С, при необходимости его подогревают в сборном баке. Выход по току 95 - 97%. Расход электроэнергии 150 - 200 кВт.ч/т свинца. Аноды находятся в ванне 5 - 10 суток, при этом растворяются до 70% металла. Продолжительность наращивания катодов чаще всего 2 - 3 суток. Режим и показатели электролиза свинца на некоторых заводах приведены в табл.11.4
Таблица 11.4. Режим и показатели электролитического рафинирования свинца
|
|
Режим и показатели электролиза | «Трейл» | «Ист-Чикаго» | «Ля Оройя» | «Шеньян» | «Сан-Гавино» |
(Канада) | (США) | (Перу) | (КНР) | (Италия) | |
Состав электролита, г/л: PbSiF6 | 85 | - | 80 | 80 - 90 | 70 - 75 |
Состав электролита, г/л: H2SiF6 | 95 | - | 74 | 95 - 105 | 70 - 80 |
Анодная .плотность тока, А/м2 | 240 | 130 - 160 | 190 | 160 - 220 | 150 |
Температура электролита, °С | 40 - 48 | 48 | 37 | 32 - 38 | - |
Выход по току, % | 97 | - | - | 97 | 96 - 97 |
Напряжение на ванне, В | - | 0,5 | 0,4 - 0,6 | 0,42 | 0,3 - 0,5 |
Скорость циркуляции рас- | 18 - 21 | 11 - 15 | 15 | 20 | - |
Срок службы анодов, сут: | 6 | 10 | 4 | 3 | - |
Срок службы катодов, сут: | 3 | 5 | 2 | 3 | - |
Выход анодного скрапа , %: | 30 - 32 | 23 | - | 40 | 30 |
Выход анодного скрапа , %: | 2 | - | - | 1,2 | 3 |
Полученные листы катодного свинца после промывки переплавляют. Одновременно проводят доочистку свинца от мышьяка и сурьмы, для чего свинец перемешивают под слоем NaOH. Шлам, снятый с анодов, промывают, фильтруют, сушат и направляют на специальную переработку. В шламе концентрируется большинстве примесей чернового свинца. В нем находятся: 12 - 20% Pb; 1
- 15% Cu; 5 - 15% As; 25 - 45% Sb; 2 -10% Bi; 4 - 6% Ag; 40-100 г/т Au другие примеси. Технология переработки шлама очень сложная. В основу ее положены различия в энергии Гиббса окисления примесей и в упругостях паров их оксидов. При плавке шлама и последующем окислении сплава удается селективно перевести примеси либо в шлак, либо в возгоны.
Этот процесс проводят в отражательных печах, или в конвертерах. Вначале окисляют и переводят в шлак и возгоны мышьяк и сурьму, затем окисляют и переводят в шлак медь и висмут; конечный сплав состоит в основном из серебра и золота (сплав Доре). Температура операций 1000 - 1200° С. Пыль и шлаки восстанавливают для получения металлов, затем их рафинируют.
Дата добавления: 2018-06-01; просмотров: 767; Мы поможем в написании вашей работы! |
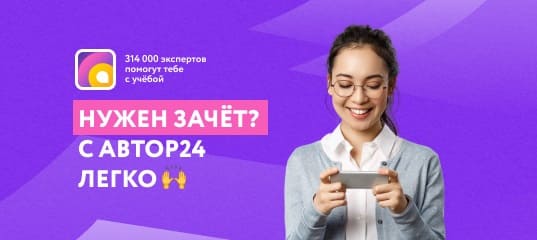
Мы поможем в написании ваших работ!