Дальнейшие этапы являются общими для плат, изготовляемых фотохимическим и сеточно-химическим методами.
Травление представляет собой процесс удаления слоя металла для получения нужного рисунка схемы 5 (рис. 26.1, д). Процесс травления включает в себя предварительную очистку, собственно травление металла, очистку после травления и удаления фоторезиста или краски (рис. 26.1, е).
Механическая обработка платы заключается в штамповании или фрезеровании по контуру и получении отверстий. Для удаления пыли и грязи плату обдувают сжатым воздухом.
Химические методы при сравнительно простом технологическом процессе обеспечивают высокую прочность сцепления проводников с основанием (2 МПа), равномерную толщину проводников и их высокую электропроводность. Время химических воздействий на плату в процессе изготовления составляет »=>25 мин. Недостатком химических методов является низкая прочность в местах установки выводов, так как отверстия не металлизируются.
Комбинированный позитивный метод(табл. 26.1). Этот метод применяют для изготовления ДПП и ГПП с металлизированными Отверстиями на двустороннем фольгированном диэлектрике. Проводящий рисунок получают субтрактивным методом, а металлизацию отверстий осуществляют электрохимическим методом (рис. 22.1). Поверхность обеих сторон платы / и отверстия 2 подвергают химическому и предварительному гальваническому меднению для получения слоя меди толщиной 5...7 мкм (рис. 22.1, а). После подготовки металлизированных поверхностей на них создается негативное изображение схемы проводников 3 (рис. 22.1, б). Это изображение может быть получено с помощью сеткографической краски или сухого пленочного фоторезиста.
|
|
Таблица 26.1
Наименование этапа | Комбинированный позитивный метод (материал СФ-2-35) | Электрохимический (полуаддитивный) метод (материал СТЭФ.1-2ЛК) |
Механическая обработка до нанесения проводников | Входной контроль фольгированного диэлектрика | |
Нарезка заготовки Вскрытие базовых отверстий Сверление отверстий, подлежащих металлизации | ||
Гальванохимическая обработка | Химическая и предварительная гальваническая металлизация 5…7 мкм | |
Подготовка металлизированной поверхности заготовки | ||
Получение рисунка схемы проводников Гальваническое меднение Нанесение защитного покрытия Sn-Pb Удаление фоторезиста или краски | ||
Травление фольги 40…42 мкм | Травление меди 5…7 мкм | |
Оплавление защитного покрытия | ||
Заключительные операции | Обрезка плат по контуру Маркировка, консервация, упаковка |
На наружные поверхности, не защищенные резистивной маской, и в отверстия осаждается слой меди 4, толщина которого в отверстиях должна быть не менее 25 мкм. Гальваническое осаждение меди выполняется на заготовке платы, имеющей сплошной слой фольги, которая защищает поверхность диэлектрика и обеспечивает электрический контакт всех элементов схемы. Металлизированные поверхности покрываются защитным слоем сплава «олово— свинец», толщина которого не менее 10 мкм. Покрытие этим сплавом хорошо защищает медь от травления и после нанесения этого покрытия участки медной фольги, покрытые ранее фоторезистом, удаляются травлением. После травления на плате остается требуемый рисунок схемы 5, образованный облуженной медной фольгой (рис. 26.2, в).
|
|
Рис. 26.2. Основные этапы получения проводников комбинированным позитивным методом
Процесс экспонирования двусторонней печатной платы показан на рис. 26.3.
В пластину 6 из оргстекла запрессованы два штифта 1. На плату 5, имеющую фольгу 4 с двух сторон, нанесен фоторезист 3. На штифты устанавливают фотошаблон одной стороны платы, а сверху устанавливают другой шаблон 4.
Изображение проявляют под душем при t=40...50°С с легким протиранием поверхности губкой. Процесс проявления ускоряется при наложении ультразвуковых колебаний. Набухание пленки является диффузионным процессом внедрения низкомолекулярного раствора в высокомолекулярный слой светочувствительной эмульсии. Диффузия в ультразвуковом поле сильно ускоряется за счет акустических микропотоков. Кавитационные пузырьки проникают в образовавшиеся поры и отрывают копировальный слой от поверхности платы.
|
|
Удаление продуктов растворения осуществляется акустическими течениями, что ускоряет процесс проявления во много раз. При этом плата меньше находится в растворе.
Проверка после проявления осуществляется внешним осмотром. Рисунки должны быть четкими и ровными, без подтеков и наплывов эмульсии.
При получении проводников возникают эффекты их разрастания и подтравливания. Если толщина металлического покрытия превышает толщину слоя резиста, то начинается боковой рост покрытия с такой же скоростью, что и рост толщины основного покрытия, что приводит к образованию грибообразного сечения проводника (рис. 26.4). После покрытия вдоль всего проводника образуются нависаюш.ие хрупкие края из сплава SnPb. Обламываясь, они образуют тонкие заусенцы размером 25...50 мкм, которые трудно обнаружить невооруженным глазом. Такие заусенцы необходимо удалить, так" как Они могут вызвать замыкание соседних проводников.
|
|
Tttttttttt
Рис. 26.3. Экспонирование двусторонней печатной платы
Рис. 26.4 Сечение проводников
а — разрастание, б — подтравливание, 1 — сплав «олово — свинец»; 2 — металлизация, 3 — фоторезист; 4 — фольга, 5 — основание печатной платы
Электрохимический (полуаддитивный) метод.Данный метод применяют для изготовления ДПП с высокой плотностью токопроводящего рисунка. Основное отличие от комбинированного позитивного метода заключается в использовании нефольгированного диэлектрика СТЭФ.1-2ЛК с обязательной активацией его поверхности или диэлектрика слофодит с фольгой 5 мкм.
Разрешающая способность электрохимического полуаддитивного метода выше, чем комбинированного позитивного. Это объясняется малым боковым подтравливанием, которое равно толщине стравливаемого слоя и при полуаддитивном методе составляет всего 5 мкм. Метод обеспечивает высокую точность рисунка, хорошее сцепление проводников с основанием и устраняет неоправданный расход меди, который доходит до 80% при использовании фольгированных диэлектриков.
Метод металлизации сквозных отверстий.
Рис. 26.5. Схема типового технологического процесса изготовления МПП методом металлизации сквозных отверстий
Метод применяют для изготовления МПП. Основные операции технологического процесса получения печатных проводников показаны на рис. 26.6.
Заготовки из фольгированного диэлектрика отрезают с припуском 30 мм на сторону (рис 22.6, а). После снятия заусенцев по периметру заготовок и в отверстиях поверхность фольги защищают на крацевальном станке и обезжиривают механически (смесью венской извести и наждачного порошка) или химически (путем обработки в соляной кислоте и хромовом ангидриде).
Рисунок схемы внутренних слоев (рис. 26.6,6) выполняют химическим методом. При этом противоположная сторона платы не должна иметь механических повреждений и подтравливания фольги. Базовые отверстия получают пробивкой, ориентируясь на метки совмещения, расположенные на технологическом поле. Полученные заготовки собирают в пакет, перекладывая их склеивающими прокладками из стеклоткани, содержащими до 50% гермореактивной эпоксидной смолы. Совмещение отдельных слоев производят по базовым отверстиям.
Прессование пакета (рис. 26.6, в) осуществляется горячим способом. Приспособление с пакетом слоев устанавливают на плиты пресса, подогретые до 120...130°С. Первый цикл прессования осуществляют при давлении 0,5 МПа и выдержке 15...20 мин. Затем температуру повышают до 150.. 160°С, а давление — до 4... 6 МПа. При этом давлении плата выдерживается из расчета 10 мин на каждый миллиметр толщины платы. Охлаждение ведется без снижения давления.
Рис. 26.6. Основные этапы получения печатных проводников МПП
а – изготовление заготовок фольгированного материала и стеклоткани; б – получение рисунка схемы внутренних слоев; в – прессование МПП; г – сверление отверстий, предварительная металлизация, получение рисунка схемы наружных слоев МПП; д – окончательная металлизация отверстий, нанесение защитного покрытия; е – травление меди с пробельных мест
Важным моментом в процессе прессования является приложение максимального давления именно в тот момент, когда смола переходит в состояние геля. Если приложить давление, когда смола находится в жидком состоянии, значительное количество ее будет выдавлено и в готовой плате образуются пустоты. Если приложить давление после того, когда смола из состояния геля перейдет в твердое состояние, между слоями возникает плохая связь.
Для определения состояния геля ведут наблюдение за кромкой пакета. Через несколько минут на ней после предварительного сжатие появляется и начинает пузыриться смола. Момент, когда смола перестанет пузыриться (обычно через 1...2 мин), соответствует наступлению геля. В это время надо приложить полное давление. Воздух, находящийся между слоями, проходит через размягченную смолу и выходит наружу. Частично он задерживается у краев, образуя пустоты, которые удаляются при обрезке краев платы. Во избежание коробления после обрезки краев рекомендуется плату зажать между двумя пластинами и поместить на 40 мин в печь при t=125°С.
Сверление отверстий выполняют на станках с ЧПУ. Перед сверлением на обе стороны заготовки наносят защитный слой лака. В процессе механической обработки платы загрязняются. Для устранения загрязнения отверстия подвергаются гидроабразивному воздействию, что позволяет удалить заусенцы на фольге, образующиеся при сверлении, и очистить от эпоксидной смолы торцы контактных площадок внутренних слоев. При большом числе отверстий целесообразно применять ультразвуковую очистку, которая обеспечивает интенсивное перемешивание раствора за счет акустических течений и повышенную способность проникновения раствора в мельчайшие отверстия. После очистки и обезжиривания плату промывают в горячей и холодной проточной воде. Затем выполняются химическая и предварительная электролитическая металлизации отверстий и операции для получения рисунка наружных слоев (рис. 26.6, г). При окончательной электролитической металлизации необходимо получить равномерное по толщине покрытие в отверстиях с толщиной слоя меди не менее 25 мкм (рис. 26.6, д). Все наружные поверхности платы, не защищенные фоторезистом, и отверстия покрывают защитным сплавом «олово — свинец». После этого фоторезистивную маску удаляют.
Схему проводников на наружных слоях получают травлением (рис. 26.6, е). Для обеспечения равномерного травления поверхность фольги зачищают смесью венской извести и наждачного порошка.
Вследствие травления фольги в отверстиях многослойных плат остается большое количество шлака, который удаляют путем очистки при воздействии ультразвуковых колебаний.
Механическая обработка по контуру, получение конструктивных отверстий и пазов осуществляются на фрезерных, координатно-сверлильных и других станках. После окончательного контроля платы подвергают консервированию флюсом ФКСП (канифоль и спирт этиловый).
Метод металлизации сквозных отверстий с внутренними переходами(рис. 26.7). Этот метод отличается от рассмотренного выше наличием дополнительных операций, связанных со сверлением отверстий в отдельных слоях платы и их металлизацией.
Рис. 26.7Многослойная печатная плата с внутренними переходами:
1 — проводник; 2 — межслойный диэлектрик; 3 — внутренний металлизированный переход; 4 — металлизированный переход между наружными слоями
Технологический процесс изготовления печатных плат субтрактивными методами имеет ряд недостатков: значительный расход медной фольги; боковое подтравливание, ухудшающее механические и электрические характеристики печатных плат; высокая трудоемкость изготовления и ограниченные возможности повышения
плотности монтажа.
С внедрением МПП рост плотности монтажа происходит за счет увеличения числа слоев, а плотность печатного рисунка слоев практически оставалась на прежнем уровне. По технологическим особенностям увеличение числа слоев больше 10...12 является нецелесообразным. Многослойные печатные платы обладают высокими техническими и эксплуатационными характеристиками, однако их проектирование и производство сопряжены с большими трудностями.
Полуаддитивные методы изготовления позволяют повысит плотность печатного монтажа, значительно уменьшить подтравливание проводников и сократить количество операций технологического процесса. Стоимость таких плат на 20% ниже стоимости ДПП, изготовленных субтрактивными методами. Основной проблемой является повышение качества материалов и технологического оборудования.
Заключительный этап производства печатных плат — контроль механических и электрических свойств. Перед контролем платы подвергаются воздействию нагрузок, которые моделируют условия эксплуатации и транспортировки (удары, вибрации, тепловые воздействия и др.).
При контроле механических свойств проверяют наличие трещин и царапин на металлической фольге, форму отдельных элементов платы, качество соединений проводников с контактными площадками, неплоскостность платы, толщину и непрерывность слоя меди в отверстиях, степень подтравливания проводников, величину адгезии проводников и др. Контроль может быть разрушающий (например, изготовление и оценка шлифов) и неразрушающий (визуальный, радиационный и др.).
При контроле электрических свойств, проверяется наличие всех электрических соединений и изоляции между проводниками. Дефекты изоляции возникают вследствие образования перемычек (остатки меди после травления), уменьшения расстояния между проводниками из-за погрешностей оригинала рисунка.
Дата добавления: 2018-05-30; просмотров: 553; Мы поможем в написании вашей работы! |
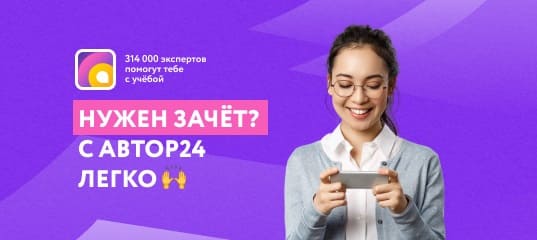
Мы поможем в написании ваших работ!