Расчет экономической эффективности
Технико-экономическое обоснование ремонта гидроцилиндра
Большинство хозяйств в современных условиях испытывают недостаток средств при выполнении заданного комплекса технологических операций на должном уровне. Это негативно отражается на конечных, результирующих показателях. Одним из факторов уменьшения финансовых средств в хозяйствах является «дорогой» ремонт, выполняемый в большинстве случаев с использованием новых деталей.
Предлагаемый к внедрению способ восстановления гильз гидроцилиндров методом заливки в полость износа полимерных материалов является приемлемым для мастерских хозяйств с программой ремонта 210 дм2
Внедрение проектируемой технологии восстановления изношенной поверхности гидроцилиндров позволяет уменьшить потребность в новых гидроцилиндрах. При этом ресурс сопряжения полимерное покрытие – резиновое уплотнение поршня по данным [ ] в 7 – 10 раз больше, чем металл – резиновое уплотнение поршня. В итоге ресурс гидроцилиндра с полимерным покрытием на 20% больше ресурса нового гидроцилиндра.
Исходные данные сведены в таблице 1.
Таблица 1. – Исходные данные для технико-экономического обоснования*
№ | Наименование показателя | ед. |
| |||
0 | Коэффициент варианта Кв |
| 1 |
| ||
Данные для расчета заработной платы: |
| |||||
1 | Минимальная оплата труда (МО) | руб | 1100 |
| ||
2 | Коэффициент сложности выполняемых работ (Ксл); | 1,5 |
| |||
3 | Кдм – количество рабочих дней в месяце, | дн. | 25,2 |
| ||
4 | Крд – количество рабочих часов в день, | час. | 7 |
| ||
5 | Др – доплаты к тарифному фонду, (в процентах от тарифного фонда) | % | 10 |
| ||
6 | Кр – районный коэффициент | 1,15 |
| |||
7 | Котп – отпускной коэффициент | 1,067 |
| |||
8 | Ксоц – социальный коэффициент | 1,263 |
| |||
Данные для расчета единовременных затрат: |
| |||||
9 | - стоимость монтажных, пусконаладочных работ и обучение персонала (в процентах от стоимости оборудования) | % | 10 |
| ||
10 | Накладные расходы (в процентах от затрат на заработную плату) | % | 120 |
| ||
11 | Стоимость доставки оборудования | % Спок.об | 5 |
| ||
12 | Стоимость монтажа оборудования и пуско-наладки | % Соб | 10 |
| ||
13 | Затраты на разработку проекта. | %( Ск + Сз) | 4 |
| ||
14 | Затраты на обучение (переподготовку) кадров | % Ск | 0,1 |
| ||
| Данные для расчета производственных затрат: |
|
|
| ||
15 | W – годовая программа , | дм2 | 210 |
| ||
16 | Площадь условного гидроцилиндра | дм2 | 11,62 |
| ||
17 | Цена нового условного гидроцилиндра | руб./шт | 10550 | у=Ц*Кв | ||
18 | Стоимость 1 кВт-ч. | руб/кВт | 1,67 |
| ||
19 | Общепроизводственные расходы | % Ззп | 120 |
| ||
20 | Общехозяйственные расходы, %(Ззп + За + Зр + Зм + Зэн + Зп) |
| 1 |
| ||
21 | Прочие расходы %(Ззп + За + Зр + Зм + Зэн + Зп+ Зоб.х) |
| 0,5 |
| ||
22 | Коэффициент ресурса нового гидроцилиндра |
| 1 |
| ||
23 | Коэффициент ресурса восстановленного гидроцилиндра |
| 1,2 |
|
* - исходные данные предназначены только для учебных целей.
Проведем расчет единовременных затрат необходимых для реализации проекта.
5.1. Расчет единовременных затрат (Зе)
Единовременные затраты равны:
Зе = Ск +Сз + Ср + Со + Соб.п., (5.1)
где Ск – капитальные затраты на приобретение (изготовление) оборудования, приспособлений, монтаж и пуско-наладку, руб.;
Сз – затраты на строительство (реконструкцию) здания, необходимого для реализации проекта, руб.;
|
|
Ср – затраты на разработку проекта, Ср = 4%( Ск + Сз), руб.;
Со – величина оборотных средств необходимая для запуска технологии производства, руб.;
Соб.п. – затраты на обучение (переподготовку) кадров (Соб.п. = 0,1%Ск), руб.
5.1.1. Капитальные затраты определяются по формуле:
Ск = Соб + Сдост + Смонт + Спн, (5.2)
где Соб – стоимость оборудования необходимого для запуска проектируемой технологии, руб.;
Сдост – стоимость доставки оборудования (Сдост = 5% Спок.об), руб.;
Смонт – стоимость монтажа оборудования, руб.;
Спн – стоимость пуско-наладки оборудования, руб.
Стоимость оборудования необходимого для запуска проектируемой технологии определяются по формуле:
Соб = Спок.об + Сизг.об, (5.3)
где Спок.об – стоимость покупного оборудования и приспособлений, руб.;
Сизг.об – стоимость изготавливаемого оборудования, руб.
Стоимость покупного оборудования определяются по формуле:
Спок.об = Σ Коб * Цоб, (5.4)
где Коб – количество покупного оборудования, ед.;
Цоб – цена покупного оборудования, руб./ед.
Данные расчетов по стоимости покупного оборудования и приспособлений заносим в таблицу 5.1.
|
|
Таблица 5.1
Определение стоимости покупного оборудования и приспособлений
Наименование | Ед. изм. | Количество ед. | Цена с НДС, тыс. руб. | Стоимость, руб. |
1 | 2 | 3 | 4 | 5 |
у=Ц*Кв | ||||
Моечная ванна | шт. | 1 | 6,64 | 6,64 |
Дефектовочный слол | шт. | 1 | 6 | 6 |
Стенд для испытания гидроцилиндров КИ-4815М | шт. | 1 | 110,64 | 110,64 |
Контейнер для гидроцилиндров ожидающий ремонта | шт. | 1 | 4,64 | 4,64 |
Бункер для утилизируемых деталей Р-938 | шт. | 1 | 7,68 | 7,68 |
Верстак слесарный ОРГ-1468-01-060А | шт. | 2 | 6,88 | 13,76 |
Приспособление для заливки полимерных материалов | шт. | 1 | 49,6 | 49,6 |
Термошкаф | шт. | 1 | 9,6 | 9,6 |
Шкаф для хранения материала и измерительного инструмента ОРГ-1468-07-040 | шт. | 1 | 6 | 6 |
Стеллаж для хранения деталей и запасных частей ОРГ-1468-05-230А | шт. | 1 | 6,48 | 6,48 |
Ларь для песка ОРГ-1468-03-320 | шт. | 1 | 1,2 | 1,2 |
Бункер для мусора | шт. | 1 | 1,28 | 1,28 |
Ларь для обдирочного материала ОРГ-1468-07-090А | шт. | 1 | 1,2 | 1,2 |
Электролитическая ванна ОРГ-2967-03-320 | шт. | 2 | 71,2 | 142,4 |
Итого | 367,12 |
* - данные взяты
В проекте предлагается изготовить стенд для разборки и сборки гидроцилиндров силами мастерской хозяйства.
Стоимость изготавливаемого оборудования определяются по формуле:
Сизг.об = Ззп + Зм +Зн, (5.5)
где Ззп – стоимость оплаты труда работников изготавливающих оборудование, руб.;
Зм – стоимость материалов и приспособлений, руб.;
Зн – накладные расходы, руб.
Стоимость оплаты труда работников изготавливающих оборудование рассчитываем по формуле:
Ззп = (Тф + Др) * Кр * Котп * Ксоц, (5.6)
где Тф – тарифный фонд, руб.;
Др – доплаты к тарифному фонду, (Др = 10% * Тф) руб.;
Кр – районный коэффициент, (Кр = 1,15);
Котп – коэффициент, учитывающий отчисления на отпуск, (Кр = 1,067);
Ксоц – коэффициент, учитывающий отчисления на социальны нужды, (Кр = 1,263, согласно статьи НК РФ № 241 от 1 января 2006 г.).
Тарифный фонд рассчитывается по формуле:
Тф = Тч * tр, (5.7)
где Тч – часовая тарифная ставка, руб./час;
tр – количество часов затраченных на выполнение данных видов работ, час.
Часовая тарифная ставка определяется по формуле:
Тч = (МО * Краз * Ксл) / Крм, (5.8)
где МО – минимальная оплата труда, принимаем МО = 1100 руб.;
Краз – коэффициент разряда;
Ксл – коэффициент сложности выполняемых работ, (Ксл = 1,5);
Крм – количество рабочих часов в месяц, Крм = 176,4 час.
Используя формулы (5.7), (5,8) определим часовые тарифные ставки и затраты на тарифный фонд. Результаты расчетов заносим в таблицу 5.2.
Таблица 5.2
Определение величины тарифного фонда
Наименование работ | Разряд работ | Коэффициент разряда | Часовая тарифная ставка, руб./час. | Количество часов работы, час. | Тарифный фонд, руб. |
Сварочные | 10 | 3,27 | 30,59 | 5 | 152,93 |
Токарные | 10 | 3,27 | 30,59 | 15 | 458,80 |
Сверлильные | 8 | 2,54 | 23,76 | 5 | 118,79 |
Слесарные | 8 | 2,54 | 23,76 | 20 | 475,17 |
Электромонтажные | 8 | 2,54 | 23,76 | 1,5 | 35,64 |
Итого: | - | - | - | - | 1241,34 |
Стоимость оплаты труда работников изготавливающих оборудование рассчитываем по формуле(5.6):
Ззп = (1241,34+ 124,13) * 1,15 * 1,067 * 1,263 = 2116,16 руб.
Стоимость материалов и приспособлений определяем по формуле:
Зм = Σ Км * Цм, (5.9)
где Км – количество материалов и приспособлений, ед.;
Цм – цена единицы материала и приспособлений, руб./ед.
Результаты расчетов заносим в таблицу 5.3.
Таблица 5.3
Определение стоимости материалов и приспособлений
Наименование | Ед. изм. | Количество ед.* | Цена с НДС, руб./ед.** | Стоимость, руб. |
1 | 2 | 3 | 4 | 5 |
у=Ц*Кв | ||||
Насосная станция | шт. | 1 | 575 | 575 |
Приводная станция | шт. | 1 | 940 | 940 |
Гидроцилиндр | шт. | 1 | 9060 | 9060 |
Зажимное устройство | шт. | 2 | 540 | 1080 |
Опорно-центрирующие ролики | шт. | 3 | 180 | 540 |
Пульт управления отвинчиванием-завинчиванием | шт. | 2 | 840 | 1680 |
Пульт управления вытягиванием-установкой | шт. | 1 | 760 | 760 |
Захват | шт. | 1 | 186 | 186 |
Каретка | шт. | 1 | 340 | 340 |
Вытягивающий захват | шт. | 1 | 140 | 140 |
Захват-стопор | шт. | 1 | 80 | 80 |
Рама | шт. | 1 | 4650 | 4650 |
Электро-пусковое оборудование | шт. | 1 | 2800 | 2800 |
Карданный вал | шт. | 2 | 2230 | 4460 |
Гидрораспределитель | шт. | 1 | 8620 | 8620 |
Рычаг управлением гидрораспределителем | шт. | 1 | 140 | 140 |
Опорный винт | шт. | 1 | 24 | 24 |
Гидравлические труб.опроводы | шт. | 6 | 256 | 1536 |
Направляющая каретки | шт. | 2 | 224 | 448 |
Поддон | шт. | 1 | 620 | 620 |
Стягивающая шпилька | шт. | 2 | 64 | 128 |
Анкерные болты | шт. | 6 | 94 | 564 |
Итого | 39376 |
* - смотри приложение №
** - смотри приложение №
Накладные расходы принимаем 120% от Ззп.
Зн = 1,2 * 2116,16 = 2539,40 руб.
По формуле (5.9) находим стоимость изготавливаемого оборудования:
Сизг.об = 2116,16 + 39376 +2539,40 = 44032 руб.
Используя формулу (5.3) находим стоимость оборудования необходимого для запуска проектируемой технологии:
Соб =367120+44032=411151,56 руб.
Стоимость доставки оборудования принимаем равным 5% Спок.об
Сдост = 0,05 * 367120 = 18356 руб.
Стоимость монтажа оборудования и пуско-наладки принимаем равным 10% Соб
Смонт +Спн = 0,1 * 411151,5 =41115,16 руб.
По формуле (5.2) находим капитальные затраты на приобретение, изготовление оборудования, приспособлений, монтаж и пуско-наладку:
Ск = 411151,5 + 18356 + 41115,16 = 470622,72 руб.
5.1.2. Определение затрат на строительство (реконструкцию) здания, необходимого для реализации проекта.
В связи с тем что, проектируемая технология не привязывается к конкретному производству и может быть внедрена в типовых мастерских хозяйств, то вопрос, касающийся производственных площадей в каждом конкретном случае решается индивидуально и в данном расчете принимаем Сз=0.
5.1.3. Затраты на разработку проекта.
Средства на разработку проекта состоят из стоимости подготовки проектно-сметной документации и ее утверждения во всех необходимых в этих случаях инстанциях. Принимаем Ср = 4%( Ск + Сз).
Ср = 0,04*(470622,72 + 0) = 18824,91 руб.
5.1.4. Определение величины оборотных средств необходимых для запуска технологии производства.
Согласно исходных данных, в хозяйстве выделены оборотные средства для покупки новых гидроцилиндров. Проектируемая технология позволяет уменьшить их величину, следовательно оборотные средства необходимые для запуска проектируемой технологии производства будут браться из имеющихся средств и в расчете единовременных затрат Со=0.
5.1.5. Определение затрат на обучение (переподготовку) кадров.
Затраты связанные с обучением (переподготовкой) кадров состоят из повышения квалификации имеющихся специалистов и составят 0,1% Ск.
Соб.п = 0,001 * 470622,72 = 470,62 руб.
По формуле (5.1) находим единовременные затраты:
Зе = 470622,72 + 0 + 18824,91 +0 + 470,62 = 489918,25 руб.
Финансирование проекта осуществляется за счет средств инвесторов.
Расчет экономической эффективности
Для обоснования целесообразности внедрения предлагаемого проектного решения определим годовую экономию (Эг). Она получается путем сравнения стоимости базовой технологии ремонта гидроцилиндров (использование новых деталей) и проектируемой (восстановление изношенной поверхности полимерным покрытием) с условием, что коэффициент ресурса нового гидроцилиндра равен kрн = 1, восстановленного kрв = 1,2:
Эг = (Сб / kрн –Спр / kрв )* kрв, (5.10)
где Сб – стоимость ремонта гидроцилиндров по базовой технологии, руб.;
Спр – стоимость ремонта гидроцилиндров по проектируемой технологии, руб.;
5.2.1. Стоимость ремонта гидроцилиндров по базовой технологии находим по формуле:
Сб = Цн * Кн, (5.11)
где Цн – цена нового условного гидроцилиндра (Цн=10550 руб./шт, по данным фирмы Алтайагротех см. приложение № );
Кн – количество новых условных гидроцилиндров, руб.
Количество новых условных гидроцилиндров определяется из условия годовой программы ремонтируемых гидроцилиндров W = 210 дм2. За условных гидроцилиндр принимаем ЦГ-110.56.1120.11 с рабочей площадью равной 11,62 дм2. Следовательно, Кн = 18 шт.
Сб = 10550 * 18 = 189900 руб.
5.2.2. Стоимость ремонта гидроцилиндров по проектируемой технологии находим по формуле:
Спр = Св * W, (5.12)
где Св – себестоимость восстановления 1дм2 полимерным покрытием на рабочую поверхность гидроцилиндра, руб./ дм2;
W – годовая программа восстанавливаемых гидроцилиндров, дм2.
Для удобства расчетов себестоимость восстановления 1дм2 полимерным покрытием на рабочую поверхность гидроцилиндра определим на примере восстановления рабочей поверхности гидроцилиндра ЦГ-110.56.1120.11. Как было ранее сказано его площадь равна 11,62 дм2.
Св = (Ззп + За + Зр + Зм + Зэн + Зп + Зоб.х+ Зпр) / W1, (5.13)
где Ззп
– затраты на заработную плату, руб.;
За – затраты на амортизацию технологического оборудования, руб.;
Зр – затраты на ремонт и техническое обслуживание технологического оборудования, руб.;
Зм – затраты на материалы, руб.;
Зэн – затраты на электроэнергию, руб.;
Зп – общепроизводственные расходы, руб.;
Зоб.х – общехозяйственные расходы, руб.;
Зпр – прочие расходы, руб.;
W1 – рабочая площадь гидроцилиндра ЦГ-110.56.1120.11, дм2.
Затраты на заработную плату рассчитываем по формуле (5.6, 5.7, 5.8):
Данные расчета заносим в таблицу 5.4.
Таблица 5.4
Определение величины тарифного фонда
Наименование работ | Разряд работ | Коэффициент разряда | Часовая тарифная ставка, руб./час. | Количество часов работы, час. | Тарифный фонд, руб. |
Дефектация | 9 | 2,91 | 27,22 | 0,30 | 8,17 |
Токарная | 9 | 2,91 | 27,22 | 0,20 | 5,44 |
Расточная | 9 | 2,91 | 27,22 | 0,35 | 9,53 |
Заливка полимера | 9 | 2,91 | 27,22 | 1,88 | 51,17 |
Токарная | 9 | 2,91 | 27,22 | 0,15 | 4,08 |
Итого: | - | - | - | - | 78,39 |
Затраты на заработную плату рабочих восстанавливающих изношенную поверхности гидроцилиндра равны:
Ззп = (78,39+ 7,84) * 1,15 * 1,067 * 1,263 = 133,64 руб.
Затраты на амортизацию определяем по формуле:
За = Б * На * Кт * W1 / (100 * W), (5.14)
где Б – балансовая стоимость оборудования, руб.;
На – норма амортизационных отчислений, %.
Кт – коэффициент использования оборудования на проектируемой технологии.
Затраты на ремонт и техническое обслуживание рассчитывают по формуле:
Зр = Б * Нр * Кт * W1 / (100 * W), (5.15)
где Нр – норма отчислений на ремонт и техническое обслуживание, %.
Данные расчета заносим в таблицу 5.5.
Таблица 5.5
Затраты на амортизацию и ремонт
Наименование | Балансовая стоимость, руб. | Коэффициент использования оборудования | Норма отчислений на амортизацию, % | Норма отчислений на ремонт и ТО, % | Затраты на амортизацию, руб. | Затраты на ремонт и ТО, руб. |
Стоимость покупного и изготавливаемого оборудования | 470622 | 0,8 | 4,5 | 5,2 | 937,48 | 1083,31 |
Токарный станок 1К62 | 320000*Кв | 0,012 | 5,4 | 5,8 | 11,47 | 12,32 |
Расточной станок | 260000*Кв | 0,017 | 5 | 6,2 | 12,23 | 15,16 |
Итого | 961,18 | 1110,80 |
Затраты на материалы определяются по формуле (5.9):
Данные по расчету затрат на материалы заносим в таблицу 5.6
Таблица 5.6
Определение стоимости материалов
Наименование | Ед. изм. | Количество ед.* | Цена с НДС, руб./ед.** | Стоимость, руб./шт. |
1 | 2 | 3 | 4 | 5 |
у=Ц*Кв | ||||
ЭД-2 | кг | 0,915 | 256 | 234,24 |
Пластификатор МГФ-9 | кг | 0,138 | 382 | 52,716 |
Графит | кг | 0,138 | 23 | 3,174 |
Отвердитель политилен-полиамид | кг | 0,109 | 860 | 93,74 |
Итого | 383,87 |
Затраты на электроэнергию определяются по формуле:
Зэн = Σ Цэл * Ni *Тi, (5.16)
где Цэл – цена за 1 кВт*час, Цэл = 1,67 руб./(кВт-ч), см. приложение № ;
Ni – номинальная мощность энергопотребителя, кВт;
Тi – время работы энергопотребителя, ч.
Результаты расчетов заносим в таблицу 5.7.
Таблица 5.7
Затраты на электроэнергию
Наименование | Номинальная мощность, кВт. | Время работы, ч/шт. | Затраты на электроэнергию, руб./шт. |
Токарный станок | 8,5 | 0,35 | 4,97 |
Горизонтально расточной станок | 10 | 0,35 | 5,85 |
Термошкаф | 8,9 | 1,5 | 22,29 |
Итого | 33,11 |
В состав общепроизводственных затрат входит содержание аппарата управления производством, содержание прочего персонала, затраты на содержание здания мастерской, инвентаря другие затраты. Принимаем общепроизводственные расходы равные 120% от затрат на заработную плату (Ззп).
Зп = 1,2 * 133,64 = 160,37 руб.
Общехозяйственные расходы, связанные с управлением предприятием, подготовка кадров, сборы, отчисления и другие. Принимаем равными 1% от (Ззп + За + Зр + Зм + Зэн + Зп)
Зоб.х = 0,01 * (133,64 +961,18+1110,80+383,87+33,11+160,37) = 27,83 руб.
Потери от брака и прочие неучтенные расходы равны 0,5% от (Ззп + За + Зр + Зм + Зэн + Зп+ Зоб.х)
Зпр =0,005*(133,64 +961,18+1110,80+383,87+33,11+160,37+27,83) = 14,05 руб.
По формуле (5.14) найдем себестоимость восстановления 1дм2 полимерным покрытием на рабочую поверхность гидроцилиндра
Св =(133,64 +961,18+1110,80+383,87+33,11+160,37+27,83+14,05) / 11,62 =
= 243,10 руб./дм2.
Стоимость ремонта гидроцилиндров по проектируемой технологии находим по формуле (5.12)
Спр = 243,10 * 210 = 51051,49 руб.
Годовую экономию от внедрения проектируемой технологии определим по формуле (5.10)
Эг =(189900/1 - 51051,49 / 1,2 )* 1,2 = 176829 руб.
Находим фактический коэффициент эффективности капиталовложения (Эф):
Эф = Эг / Ск, (5.17)
Эф = 176829 / 470622,72 = 0,38
Находим срок окупаемости проектного решения:
То = 1/ Эф, (5.18)
где То – срок окупаемости проектного решения, лет.
То = 1 / 0,38 = 2,63 года.
Находим технологическую стоимость оборудования
Стех = Σ Бi * Кi, (5.19)
где Стех – технологическая стоимость оборудования, руб.;
Бi – балансовая стоимость оборудования, руб.;
Кi – коэффициент использования времени работы оборудования на проектируемой технологии.
Результаты расчетов заносим в таблицу 5.8.
Таблица 5.8
Определение технологической стоимости оборудования
Наименование | Балансовая стоимость, руб. | Коэффициент использования времени оборудования | Технологическая стоимость, руб. |
Стоимость покупного и изготавливаемого оборудования | 470622 | 0,8 | 376498 |
Токарный станок 1К62 | 320000*Кв | 0,012 | 3840 |
Расточной станок | 260000*Кв | 0,017 | 4420 |
Итого | 384758 |
Определяем объем производства равный нулевой эффективности с учетом коэффициента ресурса восстановленного гидроцилиндра 1,2:
Qэф.нул = kрв *Зпос / (kрн *Цн – kрв *Зпер), (5.20)
где Qэф.нул – объем производства с нулевой эффективностью, дм2;
Зпос – затраты постоянные, руб.;
Зпер – затраты переменные, руб./ дм2.
Постоянные затраты определяются:
Зпос = (За + Зр + Зп + Зоб.х+ Зпр) * W / W1, (5.21)
Зпос = (961,18+1110,80+160,37+27,83+14,05) * 210 / 11,62 = 41100,5 руб.
Переменные затраты определяются:
Зпер = (Ззп + Зм + Зэн) / W1, (5.22)
Зпер = (133,64 + 383,87+33,11) / 11,62 = 47,38 руб./ дм2.
По формуле (5.20) находим объем производства с нулевой эффективностью:
Qэф.нул = 1,2*41100,5 / (1*10550 - 1,2*47,38) = 4,70 дм2.
Результаты расчетов заносим в итоговую таблицу.
Таблица 5.9
Технико-экономические показатели проекта
Наименование показателей | Значение |
1. Затраты единовременные, руб. | 489918,2 |
2. Технологическая стоимость оборудования, руб. | 384758,0 |
3. Годовая программа, дм2. | 210 |
4. Трудоемкость 1 дм2, чел.-ч. | 0,25 |
5. Энергоемкость 1, кВт-ч./ дм2. | 1,71 |
6. Стоимость ремонта, руб. 6.1 по базовой технологии 6.2 по проектируемой технологии в том числе на 1 дм2, руб./ дм2. - на заработную плату - на содержание основных средств - на материалы - на электроэнергию | 189900,0 51051,5 11,5 178,3 33,3 2,8 |
7. Годовая экономия, руб. | 176829 |
8. Фактический коэффициент эффективности капиталовложения | 0,38 |
9. Объем производства с нулевой эффективностью, дм2. | 4,70 |
10. Срок окупаемости, лет. | 2,63 |
Выводы
Проведенные расчеты показывают, что фактический коэффициент эффективности (Эф = 0,38) больше нормативного (Ен = 0,25) следовательно, проектируемая технология в сравнении с базовой экономически выгодна. Ее внедрение в мастерских хозяйств позволит получить годовую экономию равную 176829 руб. Срок окупаемости технологии составит 2,63 года.
Дата добавления: 2018-05-30; просмотров: 204; Мы поможем в написании вашей работы! |
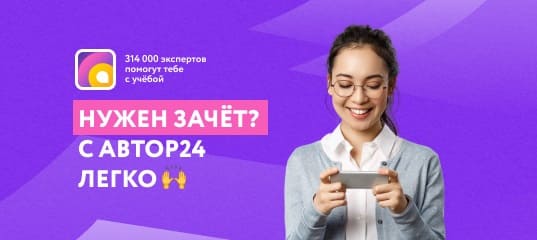
Мы поможем в написании ваших работ!