Этапы выполнения вакуумной металлизации
Существует более простой и менее вредный для окружающей среды способ металлизации пластмассовых поверхностей – металлизация в вакууме, за границей он носит название PVD-технология (PhysicalVapourDeposition). С помощью этого метода возможно: — нанесение покрытий от толщины в несколько атомных слоев и до 10 мкм; — нанесение покрытий как на ровные, так и на гнутые фасонные детали; — использование в качестве материала покрытий почти всех элементов периодической системы; — нанесение на одной и той же установке многослойных систем из различных материалов. Очень важно, что PVD-процессы не имеют ограничений с точки зрения охраны окружающей среды. Температура, скорость напыления и остаточное давление в вакуумных установках для катодного напыления легко поддаются регулированию. Сам процесс до достижения необходимого вакуума длится всего несколько секунд. Атомы пара конденсируются на сравнительно холодной поверхности детали, повышение температуры которой столь мало, что даже чувствительные к повышению температуры материалы обычно не деформируются. Толщина слоя регулируется с помощью времени нанесения слоя металла и температуры испарения источника нанесения. Толщина оптически толстого слоя на практике составляет обычно около 0,1 мкм. В целом толщина слоев на поверхности полимера ограничена. Слой отражает структуру поверхности металлизированной детали в мельчайших подробностях, причем шероховатые поверхности сглаживаются, а блестящие гладкие поверхности кажутся еще более гладкими, зеркальными, полированными. Для получения полированной металлизированной поверхности изначально шероховатых деталей необходимо их предварительное лакирование для сглаживания пор и небольших неровностей. В случае применения прозрачных ПМ практикуется металлизация оборотной стороны деталей. При этом предварительная лакировка не требуется, а формообразующие поверхности пресс-формы тщательно полируются для получения гладкой поверхности фасонной детали. При частичной металлизации детали поверхности, не подлежащие металлизации, защищаются с помощью масок или специальных лаков, которые удаляются после металлизации. Обычно в качестве материала покрытия применяется алюминий благодаря его серебряному блеску и хорошей адгезионной способности. Для защиты нанесенного на поверхность пластмассы слоя металла от коррозии, атмосферных воздействий и механических повреждений, как правило, применяют различные лаки. С помощью прозрачного лака желтого цвета можно достичь даже эффекта золочения. При необходимости возможно нанесение в условиях глубокого вакуума различных материалов в виде многослойного покрытия. Этот эффект достигается путем автономного испарения различных источников. Например, для экономии золота при нанесении его на платы сначала на грунтовую лакировку наносится слой серебра, затем на него наносится слой золота, значительно более тонкий, чем требовался бы при однослойном покрытии. При изготовлении отражателей (например, предупредительные дорожные знаки), когда требуется высокая отражающая способность, слой должен быть из серебра; использование алюминия здесь недостаточно. Для защиты серебра от атмосферного воздействия дополнительно на него наносится медь. Нанесение покрытий в глубоком вакууме позволяет создавать радужные эффекты, которые особенно ценятся в производстве украшений. Такие эффекты образуются при последовательном многослойном (от трех до девяти и более слоев) нанесении покрытий под большим (TiO2 и ZnS) и малым (SiO2 и MgF2 ) углами преломления. Первый и последний слои должны всегда иметь высокий показатель преломления. Для нанесения покрытий методом PVD-технологии пригодны многие полимерные материалы. Полистиролы, полиметиметакрилаты, сополимены стирола АБС, МСН, поликарбонаты сравнительно часто используются для металлизации в вакууме. Полиолефины (полиэтилен, полипропилен) также пригодны к применению в PVD-процессе в условиях высокого вакуума. Однако, учитывая, что структура их поверхности такова, что на них не могут наноситься никакие лаки, улучшающие связь полимера с металлом, необходима предварительная обработка поверхности деталей тлеющим разрядом и нанесения специального промежуточного слоя, улучшающего схватывание. Полиамиды в условиях вакуума выделяют газ, поэтому для нанесения покрытий используются очень редко. Часто возникают проблемы с теми пластмассами, которые содержат легко летучие пластификаторы, добавки. Смазки для пресс-форм также вызывают повреждение металлизированных деталей. Химически стойкие покрытия могут быть получены методом микроволновой полимеризации в плазме на установке для плазменной полимеризации и нанесении покрытий в периодическом режиме. При этом вакуумная камера заполняется газообразным мономерным веществом. Мономеры полимеризуются в тлеющем разряде и конденсируются на поверхности детали с образованием целостного защитного слоя. Гомогенность слоя может достигаться при скорости нанесения покрытия до 100 ?/с. Такие слои обладают стойкостью к воздействию чистящих и моющих средств. Металлизации могут подвергаться даже фторсодержащие полимерные материалы и композиции (политрифторхлорэтилен, фторопласты марок Ф-3, Ф-4), поверхность которых не обладает конструкционно необходимой адгезией к наносимым традиционными промышленными способами металлическим покрытиям. Для этой цели разработан способ детонационной металлизации. Ускоренные и нагретые продуктами детонации высокодисперсные частицы металлического порошка внедряются в поверхность полимера на глубину примерно на 10-25 мкм за счет разрушения полимера в каждой точке соударения. При этом образуется довольно прочное металл-полимерное соединение. Таким образом может быть решена проблема сложности сопряжения фторопластов между собой и другими материалами, которая является основной причиной недостаточной реализации ценных свойств этих полимеров. Составляющие узлы вакуумной установки: Устройства вакуумной транспортировки · Рабочая камера. В ней происходит сам процесс металлизации. · Источник испаряемых металлов вместе с управляющими и энергообеспечивающими устройствами. · Системы контроля и управления для регулировки температуры, скорости напыления, толщины плёнки, её физических свойств. · Откачивающая и газораспределительная система, обеспечивающая получение вакуума и регулировку газовых потоков. · Системы блокировки рабочих узлов, блоки электропитания. · Транспортирующее устройство, определяющее подачу-извлечение из вакуумной камеры, смену положений деталей при нанесении металлопокрытия. · Вспомогательные устройства – заслонки, внутрикамерные манипуляторы, газовые фильтры и др. Особенности оборудования Процесс магнетронного напыления Установки для вакуумного процесса нанесения металлического слоя бывают магнетронные и ионно-плазменные. В любых из них необходимо достигать испарения вещества с поверхности металлических болванок, минуя стадию расплава металла. При сублимационном способе процесс нагрева происходит быстро до температуры испарения, не допуская расплава. Для этого используются нагреватели, способные повышать кинетическую энергию вплоть до разрушения кристаллической решётки. Но некоторые металлы не сублимируют в вакууме, и поэтому с ними стадии расплава не избежать. Поэтому в таких случаях применяются дополнительные системы фильтров. Вакуумная металлизация, основанная на испарении и выпадении частиц металла на подложку, представляет собой ряд последовательно происходящих процессов. Они довольно сложные. Металл при нагревании перед тем, как стать покрытием, претерпевает целый ряд изменений. Вначале он испаряется, затем адсорбируется, после этого выпадает конденсатом и кристаллизуется на поверхности, с образованием металлической плёнки. Каждый процесс довольно сложный. На качество готового изделия влияют многие факторы. Главные из них – физико-технические характеристики материалов заготовок и выдерживаемые условия процесса металлизации. Образование слоя покрытия происходит в два основных этапа. Это перенос массы и энергии от источника и их равномерное распределение по поверхности обрабатываемого изделия.
|
|
|
|
|
|
|
|
Этапы выполнения вакуумной металлизации
Напыление металла на поверхности изделий методом вакуумной металлизации производится по технологии, состоящей из нескольких этапов:
Цели металлизации
· Деталь подготавливается к процессу нанесения покрытия. Для этой цели подходят только заготовки несложных форм, которые не имеют острых углов или участков, труднодоступных для прямолинейного попадания конденсата.
· Процесс нанесения защитного слоя. На полимеры с содержанием низкомолекулярных наполнителей предварительно наносятся слои антидиффузионных лаковых покрытий.
· Сушка и обезжиривание. Заготовки проходят этап сушки адсорбированной влаги в течение трех часов при температуре +80 .
· Процесс обезжиривания происходит уже на подготовительном этапе в вакуумной камере путём воздействия тлеющего разряда.
· Проведение отжига на этой стадии особенно благоприятно для полимерных материалов – положительно сказывается на их структуре, снижается при этом внутреннее напряжение.
· Проводится активационная обработка перед нанесением металлического слоя на поверхность для повышения её адгезии. Используемые методы зависят от материала заготовки.
· Нанесение металлического покрытия. При этом слой покрытия формируется путём конденсации пересыщенных паров металлов на холодную поверхность заготовки.
· Затем проводится контрольная проверка качества металлического слоя. Для декоративных изделий она заключается в осмотре поверхности с определением прочности и равномерности слоя. Для технических деталей используются дополнительные испытания. На практике применяются методы отслаивания липкой лентой, истирание, разрушение УЗ колебаниями и др.
Дата добавления: 2018-06-27; просмотров: 473; Мы поможем в написании вашей работы! |
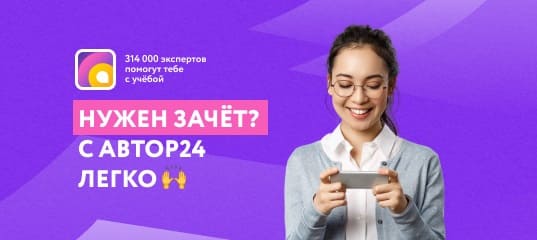
Мы поможем в написании ваших работ!