Лекция 5 Метод испытания на изгиб.
Изгиб – это вид деформации, характеризующийся искривлением оси или серединной поверхности деформируемого объекта под действием внешних сил или температуры.
При деформации изгиба нижние слои металла до нейтрального слоя испытывают растяжение, а верхние сжатие. Между зонами растяжения и сжатия располагается нейтральный недеформированный слой металла.
Испытание на изгиб проводят по двум схемам и различают :
- изгиб(сосредоточенный) с сосредоточенной нагрузкой, приложенной в середине пролёта (3точечный) Рис.1;
Рис.1
- изгиб чистый, с двумя равными симметрично приложенными (на равных расстояниях от опор) сосредоточенными нагрузками (4 точечный) Рис.2.
Рис.2
ГОСТ 14019-2003 «Металлы. Методы испытания на изгиб.»
Настоящий стандарт устанавливает методы испытаний металлов на изгиб при температуре (20 )°C (от 10 до 350С).
Испытание состоит в изгибе образца вокруг оправки под действием статического усилия и служит для определения способности металла выдерживать заданную пластическую деформацию, характеризуемую углом изгиба, или для оценки предельной пластичности металла, характеризуемой углом изгиба до появления первой трещины.
Испытания проводят на образцах круглого, квадратного, прямоугольного или многоугольного сечения.
Если в нормативных документах на металлопродукцию не оговорено иное, ширина образца должна быть следующей:
- при ширине изделия не более 20 мм ширина образца равна ширине изделия;
- при ширине изделия более 20 мм ширина образца составляет (20±5) мм для изделий толщиной менее 3 мм и от 20 до 50 мм - для изделий толщиной 3 мм и более.
|
|
Толщина образцов, отбираемых от листов, полос и фасонных профилей, должна быть равна толщине испытуемого изделия. Если толщина изделия более 25 мм, она может быть уменьшена путем механической обработки одной стороны для получения толщины не менее 25 мм.
При изгибе необработанная поверхность должна быть на растягиваемой стороне образца, лежать на опорах.
Металлопродукция круглого или многоугольного сечения подвергается испытанию на изгиб в состоянии поставки (в сечении, равном сечению металлопродукции), если номинальный диаметр (при круглом сечении) или диаметр вписанной окружности (при многоугольном сечении) не превышает 50 мм.
Длину образца устанавливают в зависимости от толщины металла и толщины (диаметра закругления) оправки. Ориентировочную длину образца (L, мм) вычисляют по формуле
L=2(a+D)+K,
где а - толщина или диаметр (диаметр вписанной окружности для многоугольного сечения образца, мм;
D -диаметр закругления (толщина) оправки, мм;
|
|
К = 100 ... 150.
Испытание на изгиб проводят на универсальных испытательных машинах или прессах. Для проведения испытания применяют приспособления:
- в виде двух опор с оправкой (Рис.1)
- в виде матрицы с V-образным углублением и оправкой (Рис.3).
Рис.3
При изготовлении плоского образца на его гранях после механической обработки не должно быть поперечных рисок от режущего инструмента. Шероховатость поверхности образца после механической обработки Rz по ГОСТ 2789-73 должна быть меньше или равна 40 мкм.
Острые кромки образца должны быть притуплены. Механическую обработку кромок производят вдоль образца. Допускается проводить испытания па образцах с непритупленными кромками, если при этом получаются удовлетворительные результаты.
На средней трети длины образца не допускаются пороки металлургического производства и механические повреждения. Маркировка должна быть на концах образца.
Расстояние между опорами (l) определяется с округлением до 1,0 мм и вычисляется (мм) по формуле
|
|
где D - диаметр закругления, мм
а - толщина или диаметр (диаметр вписанной окружности для многоугольного сечения образца), мм.
Ширина оправки и опор должна быть больше ширины образца.
Диаметр закругления (толщина) оправки и радиус закругления опор (R, мм) устанавливают в соответствии с требованиями нормативно-технической документации на металлопродукцию.
При отсутствии таких указаний диаметр закругления (толщину) оправки принимают равным двум толщинам (диаметрам) образца, а радиус закругления опор – не менее толщины (диаметра) образца.
При испытании не должно наблюдаться смятия рабочих поверхностей оправки и опор
Испытание на изгиб проводят:
- до заданного угла изгиба Рис.4;
- до появления первой трещины в растянутой зоне образца с определением угла изгиба Рис.4;
- до параллельности сторон Рис.5;
- до соприкосновения сторон Рис.6.
![]() | ![]() |
Рис.4 Рис.5 Рис.6
Вид изгиба должен быть оговорен в нормативно-технической документации на металлопродукцию
После проведения испытания осматривают кромки и наружную поверхность изогнутой части образца
|
|
Момент появления трещины фиксируют невооруженным глазом. Угол изгиба измеряют без снятия усилия угломером типа УМ-0-180º. Допускается измерять угол изгиба после снятия усилия.
Лекция 6. Метод определения величины обезуглероженного слоя.
При высокой температуре происходит взаимодействие поверхности металла с окружающей средой, причём особое значение имеют два процесса:
- обезуглероживание стали, связанное с выгоранием углерода в поверхностных слоях (С+О2→СО2);
- окисление стали, ведущее к образованию на поверхности окалины, окислов железа (2Fe+O2→FeO2).
Процессы окисления и обезуглероживания - диффузионные, с повышением температуры они ускоряются.
Диффу́зия— процесс взаимного проникновения молекул или атомов одного вещества между молекулами или атомами другого, приводящий к самопроизвольному выравниванию их концентраций по всему занимаемому объёму.
Глубину обезуглероженного слоя определяют в основном методами микроструктурного анализа.
|
|




|
|




Рис.2 шлиф из стали 60С2 100:1
|
|




Рис.3 шлиф из стали 50ХГФА 100:1
ГОСТ 1763-68 «Сталь. Методы определения величины обезуглероженного слоя»
Глубину обезуглероженного слоя определяют:
металлографическими методами - М, М1, М2,
методом замера термоэлектродвижущей силы - т.э.д.с.,
методом замера твердости - Т,
химическим методом - X,
методом замера микротвердости - МТ.
Глубину обезуглероженного слоя в ЛМ определяют металлографическим методом -
Метод М.
Настоящий стандарт распространяется на деформируемые стали: конструкционные - углеродистые и легированные с содержанием углерода не менее 0,3%; инструментальные - углеродистые, легированные и быстрорежущие; рессорно-пружинные; подшипниковые, поставляемые в виде горячекатаных и кованых прутков и заготовок диаметром или стороной квадрата до 150 мм, горячекатаных полос, труб, листов, лент и катанки, холоднокатаных листов и лент, а также холоднотянутых прутков, проволоки, труб и устанавливает методы определения глубины обезуглероженного слоя.
Сущность металлографического метода заключается в определении глубины обезуглероженного слоя по структуре под микроскопом. Образцы для изготовления шлифов отбирают от произвольных прутков, труб, листов, лент и полос.
Образцы следует отрезать холодным механическим способом, не вызывающим изменений в структуре металла (фрезой, резцом, пилой, камнем и т.д.), и вырезать поперек направления волокна.
Образцы для изготовления шлифов вырезают из полосы станочники холодным механическим способом:
шириной до 60 мм - из всего сечения полосы ;
шириной свыше 60 до 120 мм - из половины сечения полосы;
Черт 4.
по ГОСТ 1763-68 , по соглашению сторон допускается вырезка образцов по другим схемам, согласованным с заказчиком.
Образцы для металлографического исследования не должны иметь заусенцев, острых углов и кромок.
Дальнейшую подготовку шлифов к испытанию производит лаборант.
Образцы шлифов, неудобные в захвате (высотой менее 4см) для фиксации положения приготавливают в сплаве Вуда, либо в специальном приспособлении (струбцине).
Шлифование осуществлять на наждачной бумаге от крупной зернистости к мелкой.
Во время операции шлифования для удаления металлической и наждачной пыли образец периодически промывать проточной водой, а затем обдувать сжатым воздухом.
Полирование образцов осуществлять на тонкошерстном сукне с равномерно нанесенным слоем алмазной пасты или пасты ГОИ.
Шлифы должны отвечать следующим требованиям:
־ поверхность шлифов не должна иметь рисок, царапин. Микрошлиф должен быть чистым и сухим;
־ плоскость шлифа должна быть перпендикулярна исследуемой поверхности;
־ рекомендуемая площадь шлифа до 10 см 2.
На шлифах с заваленными краями глубину обезуглероженного слоя не определяют.
Травление шлифа, производится в 4%-ном растворе азотной или пикриновой кислоты в этиловом спирте и должно гарантировать четкое выявление структурных составляющих.
Для образцов, вырезанных из полосы по схемам, приведенным на черт. 4а, б, просмотр производится по широкой стороне на расстоянии не менее 2 мм от кромки.
Для пружинной рессорной полосы, определение обезуглероживания производят по всей широкой стороне образца.
Полосы трапецеидального и Т-образного профиля контролировать в месте наибольшей толщины, которое определяется визуально.
Определение производить визуально под микроскопом при увеличении (100±10)×, с точностью до
± 0,02мм , допускается увеличение от 200 до 500× или с использованием системы анализа изображений Thixomet Pro.
Глубину обезуглероженного слоя определять в миллиметрах. Результат выдавать в процентах, округляя до десятых, и вычислять по формуле:
А
Х = ------- х 100
В
а – глубина обезуглероживания при одностороннем измерении, мм;
в – толщина проката или полуфабриката, мм;
Различают две зоны обезуглероживания: зону полного обезуглероживания и зону частичного обезуглероживания.
Зона полного обезуглероживания характеризуется структурой чистого феррита.
Зона частичного обезуглероживания характеризуется структурой, отличной от структуры основного металла. Зона частичного обезуглероживания характеризуется: для доэвтектоидной стали феррито-перлитной структурой, содержание феррита в которой больше, чем в основной структуре
Общая глубина обезуглероживания включает зону полного обезуглероживания и зону частичного обезуглероживания и измеряется от края шлифа до основной структуры металла.
При отсутствии зоны полного обезуглероживания зону частичного обезуглероживания измеряют от края шлифа до основной структуры металла.
По распределению обезуглероживания различают равномерное - по всему периметру образца и местное обезуглероживание на отдельных участках периметра образца.
Глубину обезуглероженного слоя определяют как максимальную глубину для данного образца.
Обезуглероживание не измеряют в месте обнаружения поверхностного дефекта на шлифе. В протоколе испытаний указывают наличие поверхностного дефекта (ГОСТ 21014-88).
Лекция 7. Метод определения величины зерна.
Зерна металлов - это отдельные кристаллы поликристаллического конгломерата, разделенные между собой смежными поверхностями, называемыми границами зерен. Зерна могут быть равноосными и неравноосными.
Величина зерна - средняя величина случайных сечений зерен в плоскости металлографи-ческого шлифа - определяется методами:
1. визуального сравнения видимых под микроскопом зерен с эталонами шкал, приведенных в обязательном приложении 2, с определением номера зерна;
2. подсчета количества зерен, приходящихся на единицу поверхности шлифа, с определением среднего диаметра и средней площади зерна;
3. подсчета пересечений границ зерен отрезками прямых с определением среднего условного диаметра в случае равноосных зерен, количества зерен в 1 мм в случае неравноосных зерен;
4. измерения длин хорд под микроскопом или с использованием микрофотографий с определе-нием относительной доли зерен определенного размера;
5. ультразвуковым.
В ЛМ используют метод определения величины зерна сравнением с эталонными шкалами по ГОСТ 5639-82.
ГОСТ 5639-82 Стали и сплавы. Методы выявления и определеня величины зерна.
Настоящий стандарт устанавливает металлографические методы выявления и определения величины зерна сталей и сплавов.
Металлографическими методами определяют:
величину действительного зерна (после горячей деформации или любой термической обработки);
склонность зерна к росту - определением величины зерна аустенита после нагрева при температуре и времени выдержки, установленных нормативно-технической документацией на стали и сплавы;
кинетику роста зерен - определением величины зерна после нагрева в интервале температур и времени выдержки, установленных нормативно-технической документацией на стали и сплавы.
Площадь сечения шлифа на образце должна быть не менее 1 см .
Для металлопродукции толщиной менее 8 мм допускается изготовление шлифов площадью менее 1 см .
Границы зерен выявляются методами:
травления,
цементации,
окисления,
сетки феррита или цементита,
сетки перлита (троостита),
вакуумного термического травления.
Метод выбирают в зависимости от химического состава стали и цели испытания.
Метод травления
Метод травления применяют для выявления границ действительного зерна, а также границ зерен аустенита в углеродистых и легированных сталях, закаливающихся на мартенсит или бейнит, и сталях, в которых затруднено получение ферритной или цементитной сетки.
Выявление границ действительного зерна проводят на образцах без дополнительной термической обработки.
Для выявления границ зерен аустенита температуру нагрева, время выдержки и скорость охлаждения устанавливают нормативно-технической документацией на стали и сплавы.
На образцах, предназначенных для выявления зерна методом травления, готовят микрошлифы. Микрошлиф с шлифованной поверхностью помещают в электропечь.
Температура нагрева должна быть равна или на 20-300С выше температуры закалки:
- 8700С + (20-30) 0С для кремнистой стали время выдержки 3 часа;
- 8500С + (20-30) 0С для хромистой стали время выдержки 3 часа.
Образцы охлаждают в воде. После охлаждения образцы шлифуют, полируют, затем производят травление образцов раствором соляной кислоты в этиловом спирте в течение 4-5 мин согласно ГОСТ 5639-82.
Величину зерна определяют методом визуального сравнения видимых под микроскопом зерен с эталонами шкал, приведенными в обязательном приложении 2 ГОСТ 5639 с определением номера зерна при увеличении 100х.
После просмотра всей площади шлифа выбирают 3-5 полей зрения сравнивают с приведенными шкалами приложения 2 ГОСТ 5639. Шкалы 1 и 2 используют для оценки величины зерна всех сталей и сплавов. Шкалу 3 – для аустенитной стали.
Определение величины зерна с помощью системы анализа изображения Thixomet Pro ведется по заданной прикладной программе.
Дата добавления: 2018-06-27; просмотров: 2465; Мы поможем в написании вашей работы! |
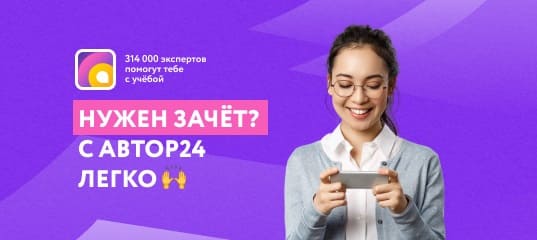
Мы поможем в написании ваших работ!