Испытания холодильной системы на прочность.
Необходимость испытаний холодильной системы на прочность определяется организацией-разработчиком холодильного оборудования, при этом возможны испытания как отдельных элементов, так и всей холодильной установки.
Ниже приведена последовательность действий при испытании на прочность установки в целом. Отличие испытания всей установки от испытаний отдельных элементов приведены ниже.
Давление для проведения испытаний на прочность указывается в технической документации конкретной холодильной установки и зависит от области её применения и типа хладагента.
При испытаниях холодильной установки на прочность используется следующее оборудование:
Манометры (2 шт.) класса точности не ниже 1,5 с диаметром корпуса не менее 160 мм и шкалой с максимальным значением, равным 4/3 измеряемого давления;
баллоны с азотом;
редуктор с предохранительным клапаном, предназначенный для работы с азотом.
Испытания холодильного контура на прочность проводятся путем заполнения магистралей сухим (точка росы не выше -40 °С) азотом под давлением.
Испытания необходимо проводить в следующей последовательности:
Установить один манометр после запорного вентиля у источника давления, а второй—в самой удаленной точке системы.
В холодильном контуре открыть запорные вентили и при необходимости—электромагнитные клапаны—так, чтобы каждый участок контура имел возможность подачи и сброса азота.
|
|
Отключить от контура все приборы КИПиА, а также другие элементы, не рассчитанные на давление испытания.
Поднять давление в контуре до величины давления испытания. Подъем давления следует осуществлять со скоростью не выше 1 бар в минуту. При достижении давления, равного 0,3 и 0,6 давления испытания, а также при давлении испытания, необходимо прекратить повышение давления и провести промежуточный осмотр и проверку наружной поверхности контура.
Под давлением испытания система должна находиться не менее 10 мин, после чего давление следует постепенно снизить до расчетного, также указанного в документации. Затем следует осмотреть наружную поверхность сосудов, аппаратов, трубопроводов, арматуры с проверкой герметичности швов и разъемных соединений мыльным раствором.
Результаты признаются удовлетворительными, если во время испытаний не произошло разрывов, видимых деформаций, падения давления по показаниям манометра.
При обнаружении утечек, деформаций, разрывов необходимо сбросить давление из контура, выполнить работы по устранению неисправностей и повторить предыдущие операции.
Испытания отдельных элементов холодильного контура проводятся в последовательности, указанной выше, но с учетом следующих мероприятий:
|
|
испытываемый элемент холодильного контура (сосуд, аппарат, трубопровод) должен быть отсоединен от других элементов с использованием металлических заглушек с прокладками, имеющими хвостовики, выступающие за пределы фланцев не менее, чем на 20 мм. Толщина заглушки указывается в документации.
места расположения заглушек на время проведения испытания должны быть отмечены предупредительными знаками, и пребывание около них людей не допускается.
использование запорной арматуры для отключения испытуемого сосуда (аппарата), трубопровода не допускается.
Испытания системы на плотность.
Проверка холодильного контура на плотность (опрессовка) проводится в обязательном порядке для обнаружения мест возможных утечек хладагента, а также после завершения ремонтных работ, связанных с разгерметизацией холодильного контура.
Испытания на плотность проводятся раздельно по сторонам высокого и низкого давления. При равенстве давлений испытания для стороны высокого и низкого давления, например, для установок с воздухоохладителями, допускается проводить испытание на плотность всей системы.
Давление для проведения испытаний на плотность назначается организацией-разработчиком и указывается в технической документации. Оно зависит от области применения установки и типа хладагента.
|
|
При испытаниях холодильной установки на плотность используется следующее оборудование:
Манометры (2 шт.) класса точности не ниже 1,5 с диаметром корпуса не менее 160 мм и шкалой с максимальным давлением, равным 4/3 измеряемого давления;
баллоны с азотом;
редуктор с предохранительным клапаном, предназначенный для работы с азотом.
Испытания холодильного контура на плотность проводятся путем заполнения магистралей сухим (точка росы не выше минус 40 °С) азотом под давлением.
При равенстве давлений испытания для стороны высокого и низкого давлений, последовательность испытаний такова:
Установить один манометр был установлен после запорного вентиля у источника давления, а второй—в самой удаленной точке системы.
В холодильном контуре открыть запорные вентили и, при необходимости, электромагнитные клапаны так, чтобы каждый участок контура имел возможность подачи и сброса азота.
Поднять давление в контуре до величины давления испытания. Подъем следует осуществлять со скоростью не выше 1 бар в минуту. При достижении давления, равного 0,3 и 0,6 давления испытания, необходимо прекратить повышение давления и провести промежуточный осмотр и проверку наружной поверхности контура.
|
|
Не производить никаких манипуляций с установкой в течение не менее 3 часов для выравнивания температур внутренней и наружной среды. Зафиксировать давление в контуре и температуру окружающей среды.
Выдержать установку под давлением не менее 12 часов. По прошествии данного времени проверить давление в контуре. Изменений давления, кроме вызванных колебаниями температуры окружающей среды, быть не должно. Эти изменения определяются следующей зависимостью:
P1/P2=T1/T2,
где P1, P2 – абсолютные значения давления газа в контуре, бар, T1, T2 – термодинамическая температура газа в контуре, К.
Если во время испытаний не произошло разрывов, видимых деформаций, падения давления по показаниям манометра, их результаты признаются удовлетворительными,.
При обнаружении утечек, деформаций, разрывов необходимо сбросить давление из контура, выполнить работы по устранению неисправностей и повторить предыдущие операции.
Испытание на вакуум (вакуумирование холодильного контура)
Вакуумирование холодильного контура проводится для удаления воздуха из агрегатов и трубопроводов и осушения холодильного контура после завершения ремонтных работ, а также после проведения испытаний на прочность и/или плотность.
Вакуумирование проводится до восстановления теплоизоляции, нарушенной при проведении ремонтных работ.
Использовать для вакуумирования компрессор холодильной установки категорически запрещено. Подавать напряжение на компрессор и проверять целостность его цепей в процессе выполнения работ по вакуумированию запрещено.
Исходное состояние холодильной установки перед вакуумированием зависит от вида выполненного ремонта и характеризуется изолированностью участка холодильного контура, на котором выполнялись ремонтные работы, от остальной схемы холодильной установки. В этой связи выбор сервисных штуцеров для подключения вакуумного оборудования, используемого в процессе вакуумирования, производится оператором в зависимости от участка, который требуется вакуумировать.
Для проведения вакуумирования применяют следующее оборудование:
манометрический коллектор*;
комплект гибких шлангов*;
вакуумный насос;
вакуумметр.
Оборудование, помеченное *, должно быть предназначено для работы с применяемыми в установке хладагентом и маслом и иметь соответствующую маркировку.
Порядок действий при ваккумировании:
Произвести сборку схемы вакуумирования с таким расчетом, чтобы расстояние между вакуумным насосом и холодильной установкой было как можно меньшим, а диаметр соединительных шлангов как можно большим.
Подключить манометрический коллектор к контуру и убедиться в отсутствии избыточного давления. При наличии избыточного давления, понизить его до атмосферного и проконтролировать его рост.
Подключить вакуумный насос к сервисным штуцерам вакуумируемого участка холодильного контура.
Подключить вакуумметр в наиболее отдаленной от места установки вакуумного насоса точке.
Открыть вентиль перед вакуумным насосом и, при необходимости, электромагнитные клапаны так, чтобы каждый участок подлежащего вакуумированию контура имел возможность подключения вакуумного насоса.
Включить насос и отвакуумировать холодильный контур до остаточного давления
Остаточное давление следует принять 1 кПа (8 мм рт.ст.).
Вакуумирование рекомендуется проводить при нормальных температурных условиях в помещениях (20°С), в крайнем случае, при температуре в помещениях с холодильным оборудованием не ниже 5°С.
При низких температурах (ниже 2°С) рекомендуется проводить обогрев помещения, в которых размещен вакуумируемый участок контура.
При протяженных трассах трубопроводов рекомендуется разбить подлежащий вакуумированию участок на несколько подучастков (с помощью запорных вентилей) и проводить вакуумирование по подучасткам.
Запрещается подогревать участки холодильного контура открытым пламенем.
После достижения величины остаточного давления, следует продолжить вакуумирование в течении 18 часов. После этого следует закрыть вентиль и выключить вакуумный насос.
Если при низких температурах не удается достичь необходимой величины остаточного давления, то процесс вакуумирования следует чередовать с процессом наддува сухим азотом (отсоединяя насос) до абсолютного давления 2…3 бар.
При проведении испытаний холодильная установка должна находиться под вакуумом в течении 18 часов, при этом изменение давление в контуре должно фиксироваться не реже, чем через 1 час. Допускается повышение давления до 50% за первые 6 ч. В остальное время давление должно оставаться постоянным.
Если по окончании вакуумирования заправка установки хладагентом не планируется, то установку необходимо заполнить сухим азотом до абсолютного давления 2…3 бар.
Если в первые 3 часа выдержки под вакуумом давление резко повышается до уровня давления насыщенных паров воды, соответствующего температуре окружающей среды в помещении, а затем стабилизируется, то, значит, система герметична, но не достаточно осушена. Необходимо продолжить вакуумирование.
Если за 18 часов рост давления превысил 500 Па (5 мбар), давление не стабилизируется на уровне давления насыщенных паров воды при температуре окружающей среды и продолжает расти, то установка негерметична. Следует произвести поиск и устранить причину негерметичности контура. После этого повторить работы по вакуумированию.
Ниже приведена таблица зависимости давления насыщенных паров воды от температуры окружающей среды.
T,°C | 0 | 4 | 8 | 12 | 16 | 20 | 24 | 28 | 32 |
Р, Па | 610 | 812 | 1072 | 1401 | 1817 | 2337 | 2982 | 3778 | 4753 |
3. В центральных системах кондиционирования оборудование для обработки воздуха расположено компактно в отдельном техническом помещении. Обычно это один или несколько центральных кондиционеров 3 (приточных установок), вытяжные установки, холодообеспечение. Подача обработанного воздуха в рабочую зону производится по воздуховодам. Преимуществом таких систем является удобство централизованного технического обслуживания в ходе их эксплуатации. Подвод теплоносителя и хладоносителя к аппаратам кондиционера осуществляется централизованно и не требует разводки теплоизолированных трубопроводов по зданию. Недостатком центральных систем кондиционирования можно считать наличие разветвленной сети воздуховодов, которую не всегда удобно совмещать с уже существующими архитектурными решениями здания. Центральную систему кондиционирования воздуха обычно используют для обслуживания больших помещений – производственных цехов, зрительных и спортивных залов, ресторанов, а также для групп помещений, имеющих схожие тепловлажностные характеристики, например в офисных зданиях и гостиницах. Иногда для одного объекта крупного объема используется несколько центральных приточных установок, обслуживающих отдельные зоны помещения. Как правило, центральные кондиционеры имеют широкий диапазон производительности по воздуху - от 1.5 до 150 тыс.м3 /ч. Требуемая производительность кондиционера определяется исходя из теплопритоков и влагопритоков в обслуживаемое помещение, количества вредных выделений, санитарной нормы подачи наружного воздуха. По расчетной производительности подбирается стандартный типоразмер кондиционера. Каждый типоразмер характеризуется своим размером живого сечения для прохода воздуха. Он выбирается из условия оптимальной для успешной обработки скорости прохождения воздуха через тепло- массообменные аппараты. Центральный кондиционер представляет из себя группу аппаратов для обработки воздуха, собранных в едином корпусе. Какие именно аппараты будут включены в центральный кондиционер и порядок их расположения, обычно определяется выбранной схемой обработки воздуха. Схема обработки воздуха разрабатывается исходя из условий микроклимата обслуживаемого помещения и климатических данных для места расположения здания (параметры группы Б). В центральный кондиционер могут быть включены воздухоохладитель, воздухонагреватель, сотовый увлажнитель, камера орошения, устройство для увлажнения воздуха паром, устройство для утилизации тепла, воздушный фильтр, камера смешения, приемный клапан, вентиляторный агрегат, шумоглушитель. При необходимости дополнительной, особой, обработки воздуха могут быть добавлены адсорбер, абсорбер, ионизатор воздуха, фильтры тонкой очистки и другие устройства. Центральный кондиционер может монтироваться из отдельных функциональных блоков или как моноблок с типовой схемой компоновки в едином корпусе.
Дата добавления: 2018-06-27; просмотров: 1780; Мы поможем в написании вашей работы! |
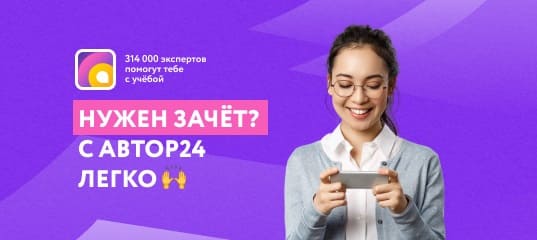
Мы поможем в написании ваших работ!