Основные технологические требования к деталям, изготовленных гибкой
[1, c.407-408]]
1 .Минимально допустимые радиусы гибки следует применять лишь в случае конструктивной необходимости. В большинстве случаев возможно применять увеличенные радиусы гибки r >S, а для толстых заготовок еще больше r >2S.
2.В случае гибки пластичных металлов с малым радиусом закругления (r <0,5S) линию изгиба желательно располагать поперек волокон проката. В случае гибки тех же металлов с радиусом r >S расположение линии изгиба безразлично; решающее значение при этом имеет достижение наиболее выгодного раскроя металла.
3.При изгибе заготовки в разных направлениях, а также при изготовлении правых и левых деталей из одной заготовки радиус закругления одного из перегибов должен быть увеличен. Гибка должна быть произведена таким образом, чтобы сторона с заусенцами пришлась на наружную сторону перегиба с увеличенным радиусом.
4.Наименьшая высота отгибаемой полки должна быть h>3S.
5.При гибке деталей, имеющих широкую и узкую часть, радиус изгиба не должен захватывать широкую часть, иначе образуются наплывы. Если по конструктивным соображениям линия изгиба проходит вместе сопряжения этих частей, следует применять вырезы шириной b>S.
6.В случае многооперационной гибки необходимо предусматривать технологические базы для фиксирования заготовок на операциях.
Параметры технологичности проектного варианта удовлетворяют базовым параметрам, то есть размеры детали и ее конструкция соответствуют требованиям штамповочных операций, поэтому рассматриваемую деталь можно считать технологичной.
|
|
2 Выбор и обоснование оптимального варианта технологического процесса штамповки детали
Технология листовой штамповки и конструкция штампового инструмента устанавливается в зависимости от размеров и формы штампуемой детали, точности штамповки, а также от серийности производства. В массовом и крупносерийном производствах оправдывают себя сложные совмещенные штампы. Уменьшаются затраты на рабочую силу, повышается производительность труда, что прямо влияет на себестоимость детали.
Для получения детали можно предложить несколько вариантов технологического процесса, имеющего следующую последовательность операций:
1. Штамповка из листа
1.1 Разделение листа на полосы;
1.2 Вырубка наружного контура и пробивка отверстия;
1.3 Гибка;
2. Штамповка из листа
2.1 Разделение листа на полосы;
2.2 Вырубка наружного контура;
2.3 Пробивка отверстия.
2.4 Гибка;
При изготовлении мелких деталей целесообразно применять комбинированные штампы, так как пооперационная штамповка с установкой заготовок вручную пинцетом недостаточно производительна и небезопасна. Поэтому наиболее рациональным будет принять раздельную совмещенную вырубку и пробивку отверстия (по варианту 1).
|
|
Определение формы и размеров заготовки
Чтобы определить размеры сложной пространственной детали, необходимо развернуть ее на плоскость.
Определение размеров плоских заготовок, подлежащих гибке, основано на равенстве длины заготовки длине нейтрального слоя изогнутой детали. В случае определения размеров заготовок при гибке с закруглением по радиусу длина заготовки равна сумме длин прямых участков и длины нейтрального слоя в изогнутом участке в зависимости от относительного радиуса изгиба .
,
где L – длина нейтрального слоя изогнутого участка
x – коэффициент, определяющий положение нейтрального слоя, определяется в зависимости от отношения
, следовательно x = 0,42 [1, c. 68, табл. 2.1]
Рисунок 3.1
Принимаем межцентровое расстояние 29,5 мм.
Аналогичным образом определим другие размеры развертки детали.
Рисунок 3.2. Развертка детали
Раскрой листового материала
Для холодной штамповки наиболее широко применяют листы, полосы, ленты, фасонный материал. Наибольшую часть себестоимости штампованных деталей (до 80%) составляет стоимость основного материала. Поэтому необходимо выбрать рациональный раскрой материала при разработке технологического процесса штамповки.
|
|
При заданных параметрах, вытекающих из конструкции и размеров штампуемой детали и частично определяющих сортамент основного материала, окончательный его выбор осуществляют на основании экономического анализа возможных вариантов и определение оптимального.
Поскольку контур вырубаемой заготовки криволинейный, то контуры вырубаемых заготовок должны быть удалены друг от друга на величину технологической перемычки. Основное назначение перемычки - компенсировать погрешности подачи материала и фиксация его в штампе с тем, чтобы обеспечить полную вырубку детали по всему контуру и предотвратить получение бракованных деталей. Ширину перемычки выполняют меньшей для снижения расхода материала, а также для уменьшения усилий, необходимых для снятия материала с пуансона.
Определение перемычек
Перемычка между контурами заготовок называется межконтурной и принимается а1=2,5мм [ 1, с 424 ,табл. 166]
Перемычка между контуром заготовки и краем полосы называется боковой, принимается b1 = 2,5 мм [1, с 424,табл.166]
|
|
Определение ширины полосы
Расчет номинальной ширины полосы проводят исходя из условия сохранения минимально необходимой ширины боковых перемычек при различных способах подачи и допусков по ширине ленты.
Расчетная ширина полосы: В = А + 2(b1 + Δш) + z [1, с.428, табл.169]
А - размер вырезаемой детали (поперек полосы);
b1 - наименьшая величина боковой перемычки;
z - гарантийный зазор между направляющими и наибольшей возможной шириной ленты;
Δш- односторонний допуск на ширину полосы.
А = 67,34мм (из построения), b1 = 2,5мм, z = 0,5-l,0, Δш =0,6 мм [1, с.429, табл.170-171]
В = 67,34 + 2(2,5 + 0,6) + 0,5 = 74,04мм.
Принимаем номинальную ширину полосы B = 74 мм.
Шаг подачи: t = D + а = 16,26 + 2,5 = 18,76 мм,
где D – размер вырезаемой детали вдоль ленты;
a- межконтурная перемычка.
1. Продольный раскрой листа
Число полос, получаемых из листа 700х1400:
Число деталей, получаемых из полосы:
Число деталей, получаемых из листа:
Коэффициент использования металла при продольном раскрое:
,
где - площадь вырубаемой детали.
2. Поперечный раскрой листа
Число полос, получаемых из листа 700х1400:
Число деталей, получаемых из полосы:
Число деталей, получаемых из листа:
Коэффициент использования металла при продольном раскрое:
,
где - площадь вырубаемой детали.
3. Продольный раскрой листа
Число полос, получаемых из листа 600х1200:
Число деталей, получаемых из полосы:
Число деталей, получаемых из листа:
Коэффициент использования металла при продольном раскрое:
,
где - площадь вырубаемой детали.
4. Поперечный раскрой листа
Число полос, получаемых из листа 600х1200:
Число деталей, получаемых из полосы:
Число деталей, получаемых из листа:
Коэффициент использования металла при продольном раскрое:
,
где - площадь вырубаемой детали.
Рис. 4.1 Раскрой полосы
![]() |
Из рассмотренных вариантов принимаем продольный раскрой листа 600х1200, так как при нем обеспечивается наибольшее использование металла.
Расчет технологических сил
Разрезка листа на полосы
- сопротивление сдвигу для стали 08пс
S – толщина полосы
- угол створа, для гильотинных ножниц
C учетом притупления режущих кромок
5.2 Вырубка и пробивка
Расчетное усилие процесса среза штампами с параллельно режущими кромками определим по формуле:
, [1, с.23]
где L – периметр вырубаемого контура;
S – толщина полосы;
- сопротивление сдвигу при вырубке на кривошипных прессах;
[1, с.22]
По операционному эскизу вырубаемой заготовки ее периметр равен L = 153,9 мм
Полное усилие вырубки обычно учитывает поправку на неоднородность металла и затупление режущих кромок введением поправочного коэффициента 1,2.
Усилие для сжатия прижима: ,
где - площадь детали;
МПа – давление;
Н
Усилие для проталкивания детали через матрицу: , [1, с.26]
где - при вырубке с обратным выталкиванием;
Н.
Усилие для снятия ленты с пуансона , [1, с.26]
где ;
Н.
Требуемое усилие пресса составит:
Н
Гибка
Усилие гибки:
, где [3, c.211]
B = 42мм – сумма длин линий сгиба;
= 0,43 (для r/S = 1,0)
10836 Н
Усилие прижима:
Требуемое усилие пресса с учетом затупления кромок составит:
.
Дата добавления: 2018-06-27; просмотров: 809; Мы поможем в написании вашей работы! |
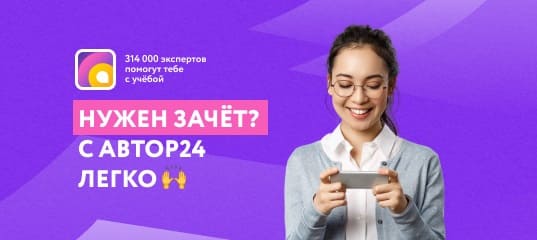
Мы поможем в написании ваших работ!