Характеристика готового продукта.
Государственное бюджетное образовательное учреждение среднего профессионального образования «Пермский химико-технологический техникум»
ЗАДАНИЕ
Для курсового проектирования по дисциплине: «Основы технологии переработки полимерных материалов и эластомеров»
специальности 18.02.07 Технология производства и переработки пластических масс и эластомеров.
студентукурса: 4 группы: Т-12-9
Стрелкову Максиму Александровичу
(фамилия, имя, отчество)
Тема задания: Разработать технологический процесс изготовления фасонных деталей к канализационным трубам методом литья под давлением.
Курсовой проект на указанную тему выполняется в следующем объеме Пояснительная записка:
Введение. 1 Выбор и обоснование. 2. Характеристика готовой продукции, сырья и материалов. 3.Технологический процесс производства.3.1 Разработка проектируемой фазы. 3.2.Характеристика основного и вспомогательного оборудования. 4 Мероприятия по выпуску качественной продукции. 5 Механизация и автоматизация производства.6.Точки технологического контроля 7 Отходы производства и охрана окружающей среды. 8. Характеристика производственного здания. 9 Охрана труда. 10. Материальные расчеты. 11. Заключение. Литература.
|
|
2.Расчетная часть проекта:
1. Материальные расчеты
3.Графическая часть проекта:
Лист 1. Технологическая схема технологического процесса
Лист 2. Чертеж общего вида термопластавтомата
Дата выдачи:
Срок окончания: _________________
Преподаватель: ________________
Содержание.
Введение...............................................................................................................4
Выбор и обоснование способа производства................................................5
2. Характеристика готовой продукции, сырья и материалов
2.1 Характеристика готовой продукции............................................................6
2.2 Характеристика сырья и материалов...........................................................8
3. Технологический процесс производства
3.1 Проектируемая фаза производства
3.2 Характеристика основного и вспомогательного оборудования
3.2.1 Характеристика основного оборудования
3.2.2 Характеристика вспомогательного оборудования
4. Мероприятия по выпуску качественной продукции
5. Механизация и автоматизация на фазе
6. Точки технологического контроля
7. Охрана окружающей среды и отходы производства
8. Материальные расчеты
· Заключение
· Список используемой литературы
|
|
Введение
Фасонные детали - это детали трубопроводов, которые служат для соединения отдельных труб и используются в местах переходов, поворотов, разветвлений и т.д. Другими словами, фасонные изделия – это то, что собирает трубопровод воедино, делая его герметичным и удобным в эксплуатации. Даже если предположить, что трубопровод является абсолютно прямым или таким длинным и гибким, что промежуточные фитинги для его монтажа не понадобятся, все равно в местах входа и выхода потребуются соединительные элементы.
Деревянные трубопроводы в свое время соединялись с помощью металлических хомутов либо, как терракотовые трубопроводы времен Древней Греции, на основе безрезьбового соединения «муфта – штуцер» с возможным уплотнением известняковым раствором либо свинцовой зачеканкой. С тех времен человек в значительной степени отошел от использования природных материалов. Появились трубопроводы на основе полимерных материалов (полипропилен, полиэтилен, ПВХ и др.).
А раз появились трубопроводы из полимеров, то и тратить на них металлы не целесообразно. Поэтому фасонные детали тоже стали делать из полимеров.
Очень часто встречаются фитинги из полиэтилена, так как он довольно распространен и не дорог, его легко перерабатывать (особенно литьем под давлением), а так же всегда гранулируется, что обеспечивает наименьшие потери материала и высокую сыпучесть, по сравнению, например с ПВХ, который находится в виде порошка. Так же полиэтилену не страшна коррозия и не требуются стабилизаторы, пластификаторы и другие наполнители, кроме красителя (если есть нужда) или инертного наполнителя (для удешевления производства).
|
|
Полиэтиленовые канализационные трубы и фасонные части к ним могут прослужить без замены до 30, а иногда и более лет.
1. Выбор и обоснование способа производства.
Для производства фасонных деталей можно использовать разные способы производства. Но в основном применяются прессование и литье под давлением.
Минус прессования состоит в том, что у него высокий шанс появления брака, большие потери сырья и материалов, да и прессованием невозможно получить большие и сложные фасонные детали. К тому же изделие требует дополнительной механической обработки. Однако прессование не подходит для изготовления изделий из термопластов.
Литье под давлением, кроме своего основного преимущества, заключающегося в возможности получения сложнейших отливок с рельефными контурами с толщиной стенок от 0,8 мм и выше, имеет еще ряд ценных преимуществ, такие как:
|
|
-высокая технологичность метода;
-высокая степень автоматизации процесса;
-низкая себестоимость готовых изделий;
-возможность получения деталей любых оттенков;
-высокие механические и прочностные качества готовых изделий;
Из недостатков можно отметить высокую стоимость формующего инструмента, сравнительно низкую производительность при изготовлении армированных изделий и изделий сложной конфигурации.
При литье под давлением размер и форма фасонных деталей ограничены лишь возможностями машины. Детали получаются высококачественные. Поэтому фасонные детали большей частью изготавливают литьем под давлением.
2. Характеристика готового продукта, сырья и материалов .
Характеристика готового продукта.
Фасонные части к полиэтиленовым канализационным трубам предназначены для систем внутренней канализации зданий с максимальной температурой сточной жидкости 60оС и кратковременной (до 1 мин) 95оС.
Полиэтиленовые фасонные части к канализационным трубам должны удовлетворять требованиям ГОСТ 22689.0 – ГОСТ 22889.2 – 89 и утвержденным образцам – эталонам.
Поверхность фасонных частей должна быть ровной и гладкой. Высота выступов после удаления литников не должна превышать 2,0 мм. Цвет изделий - белый. Соединения труб и фасонных частей должны быть герметичны при испытании внутренним гидростатическим давлением 0,1 МПа (1 кгс/см2 при температуре окружающей среды 15 ± 10 °С). Трубы и фасонные части не должны растрескиваться при прогреве в течение 24 ч в 20 %-ном растворе вещества ОП-10 по ГОСТ 8433 при температуре 80 ± 3 °С. Длины и диаметры тройников типа КСК указаны в таблице №1.
Таблица №1. Характеристика тройника типа КСК
Диаметр, мм | Длина, мм | ||||
d | d1 | l1 | l2 | l3 | |
|
| α=87°30' | |||
Не менее | |||||
50,0 | 40,0 | 33 | 31 | 39 | |
50,0 | 50,0 | 31 | 39 | 39 | |
90,0 | 50,0 | 39 | 36 | 58 | |
90,0 | 90,0 | 63 | 59 | 63 | |
Зависимость массы тройниковот диаметра указана в таблице №2.
Таблица №2. Теоретическая масса полиэтиленовых тройников типа КСК
Диаметр, мм | Угол | Масса, кг | |
d | d1 | α | ПЭВД |
50,0 | 50,0 | 87°30' | 0,094 |
90,0 | 50,0 | 0,24 | |
90,0 | 90,0 | 0,38 |
КСК – с двумя раструбами для соединения уплотнительными кольцами и раструбом для соединения сваркой.
Условное обозначение тройника типа КСК с углом α=87°30' для соединения с трубами диаметром 110 мм и 50 мм из ПЭВД:
Тройник Т 110К×110С×50К - ПВД ГОСТ 22689.2
Фасонные части транспортируют любым видом транспорта в соответствии с правилами перевозки грузов и техническими условиями погрузки и крепления грузов, действующими на данном виде транспорта. Транспортирование должно производиться с максимальным использованием вместимости транспортного средства.
Фасонные части должны храниться в не отапливаемых складских помещениях в условиях, исключающих вероятность механических повреждений, или в отапливаемых складах не ближе 1 м от отопительных приборов, защищенными от воздействия прямых солнечных лучей и атмосферных осадков.
2.2 Характеристика сырья и материалов.
1) Полиэтилен высокого давления (ПЭВД) - представляет собой массу белого цвета (тонкие листы прозрачны и бесцветны). Химически- и морозостоек, диэлектрик, не чувствителен к удару (амортизатор), при нагревании размягчается (80—120°С), адгезия (прилипание) — чрезвычайно низкая. Химическая формула: (-CH2-CH2-)n
Физико-химические свойства ПЭВД указаны в таблице №3.
Таблица №3. Физико-химические свойства ПЭВД при 20°C
Параметр | Значение |
Плотность, кг/м3 | 940 - 960 |
Насыпная плотность, г/см3 | 0,5-0,6 |
Разрушающее напряжение при статическом изгибе, кгс/см² | 120—170 |
Температура плавления, °С | 103-110 |
Усадка при литье, % | 1,0-3,5 |
Температура хрупкости, °С | От минус 45 до минус 100 |
Относительное удлинение при разрыве, %, не менее | 250 |
Модуль упругости при изгибе, кгс/см² | 1200—2600 |
Предел текучести при растяжении, кгс/см², не менее | 95 |
Относительное удлинение в начале течения, % | 15-20 |
твёрдость по Бринеллю, кгс/мм² | 1,4-2,5 |
Полиэтилен упаковывают в специальные бумажные мешки, имеющие клапан, или в полиэтиленовые мешки по ГОСТ 17811 или в полиэтиленовые мешки, размеры и форма которых определяются возможностями специальной упаковочной установки, обеспечивающие сохранность и качество продукции. Обязателен вкладыш.
Горловину вкладыша и полиэтиленовых мешков заваривают или прошивают машинным способом, горловину бумажных мешков прошивают машинным способом. Масса полиэтилена в мешке должна быть (20,0±0,3)
или (25±0,3) кг.
Полиэтилен транспортируют всеми видами транспорта в крытых транспортных средствах в соответствии с правилами перевозки грузов, действующими на данном виде транспорта.
Полиэтилен хранят в закрытом помещении, исключающем попадание прямых солнечных лучей, на расстоянии не менее 1 м от нагревательных приборов. Перед вскрытием мешки с полиэтиленом должны быть выдержаны не менее 12 ч в производственном помещении.
2) Титановые белила (марка Р – 02) – в полимере является красящим веществом. Химическая формула: TiO2. Должен соответствовать ГОСТ 9808 – 84. Показатели норм приведены в таблице №4.
Таблица№4. Показатели норм для TiO2 марки Р - 02
Показатель | Норма |
Массовая доля двуокиси титана, %, не менее | 93 |
Массовая доля рутильной формы, %, не менее | 95 |
Массовая доля летучих веществ , %, не менее | 0,5 |
Массовая доля водорастворимых веществ, %, не менее | 0,3 |
pH водной суспензии | 6,5 – 8,0 |
Разбеливающая способность, условные единицы, не менее | 1600(1700) |
Для упаковывания лакокрасочных материалов применяют потребительскую и транспортную тару, контейнеры, мешки бумажные шестислойные (масса не превышает 50 кг).
Транспортируют всеми видами транспорта в крытых транспортных средствах в соответствии с правилами перевозки грузов, действующими на данном виде транспорта. Срок хранения 12 месяцев со дня изготовления.
3. Технологический процесс производства
![]() |
3.1 Краткое описание технологического процесса
На предприятие ПЭВП поступает упакованным в полиэтиленовых мешках массой 25 кг на грузовых машинах, а титановые белила в бумажных шестислойных мешках массой 50 кг. Затем ПЭВП разгружается на складе и остается в мешках в течение 12 часов. Потом мешки распарывают и ПЭВП засыпают в емкость для хранения сырья. Так же поступают и TiO2.
Из емкости для хранения сырья, с помощью пневмотранспорта, ПЭВП поступает в смеситель, в который поступает и краситель, перемешивается, а так же подсушивается. Затем смесь поступает в бункер термопластавтомата.
Захватываясь витками червяка, смесь попадает в материальный цилиндр, нагревается и плавится, после чего впрыскивается под давлением в литьевую форму, где происходит формование изделия. Форма охлаждается водой, холодноканальная.
Отформованные изделия попадают на разбраковку и механическую обработку. Литники и забракованные изделия собирают в чистую тару и направляют на измельчение в дробилки, затем гранулируют в грануляторах. Вторичное сырье добавляют к свежему, но не более 30%.
Готовые изделия отправляются на упаковку в полиэтиленовые мешки по ГОСТ 10354 – 82 толщиной не менее 0,1 мм и отвозятся покупателю.
3.2 Фаза литья
Физико-химические процессы
Влияние различных факторов
Переработка литьем под давлением заключается в нагреве материала до размягчения и последующего перехода в вязко – текучее состояние, в инжекции (впрыске) расплава в форму, где материал приобретает необходимую конфигурацию и затвердевает, так как в каналах формы циркулирует вода.
Основными параметрами процесса литья под давлением являются:
1. температура литья (Т литья); 4. Время цикла (t цикла);
2. давление литья (Р литья);
3. температура формы (Т формы);
Кроме этих параметров на процесс литья так же оказывают влияние форма и размеры изделия, конструкция литниковой системы, свойства материала (вязкость, термостабильность, релаксационные свойства).
1) Температура литья – определяет текучесть расплава, плотность, степень ориентации макромолекул полимера при течении в форме. Текучесть должна быть достаточной для заполнения гнезд формы и точного воспроизведения их конфигураций.
Слишком высокая температура литья может привести к интенсивной термодеструкции, а следовательно к низкой прочности, эластичности, изменению цвета. Полимерные материалы плохо проводят тепло, поэтому для обеспечения оптимальной производительности материального цилиндра разность температур между стенками и расплавом должна быть значительной.
Чем выше температура, тем меньше вязкость расплава и тем легче передается давление и заполняется форма. Снижение температуры расплава может привести к необходимости увеличения времени пребывания сырья в цилиндре. Это может снизить производительность машины.
2) Давление литья – создается червяком узла пластикации. Под давлением материал, расплавляясь, проходит через материальный цилиндр и заполняет полость формы. Повышение давления, действующего на расплав в материальном цилиндре приводит в повышению скорости впрыска и заполнению формы.
3) Температура формы – зависит от температуры литья. Чем выше температура литья, тем выше температура формы.
4) Время цикла – определяется технологическими требованиями: временем заполнения формы, временем охлаждения изделия и машинным временем: время смыкания формы, время подвода и отвода сопла, время смыкания и размыкания формы. Машинное время является паспортной характеристикой машины, технологическое время устанавливается опытным путем.
Продолжительность цикла может быть подсчитана, как сумма промежутков времени, затраченных на все операции.
3.3 Ведение технологического процесса на фазе
1) Работа термопластавтомата (далее ТПА).
Перед изготовлением изделий на термопластавтомате КУАСИ – 1800/400 слесарь-наладчик устанавливает необходимую пресс-форму в режиме "Наладка". Проверяет наличие масла в баке маслостанками через смотровое стекло уровнемера, а также наличие смазки в узлах подвижной плиты и направляющих колонн. В режиме "Ручное управление" кнопками управления проверяют действие функций аппарата, наличие материала в бункере. Проверяют срабатывание блокировок и аварийного выключения.
Пускает ТПА в работу в режиме "Автомат" или "Полуавтомат".
Аппаратчик подбирает требуемую порцию материала установкой конечного выключателя в нужное для этого положение. Изготовление изделий ведут при температурах обогрева зон цилиндра, указанных в таблице №5.
Таблица №5. Технологические параметры литья
Параметры | ПЭВП |
Т литья, °С | 150 - 270 |
Т формы, °С | 20 - 60 |
Р литья, МПа | 100 |
Усадка, % | 1 - 2 |
Температура обогрева материального цилиндра указана в таблице №6.
Таблица №6. Температура обогрева по зонам материального цилиндра
Номер зоны | Температура, °С |
1 | 60 – 150 |
2 | 60 - 180 |
3 | 60 - 160 |
4 | 70 - 180 |
Материал загружается в бункер ТПА и при вращении червяка материал из бункера захватывается и перемещается вперед. В цилиндре материал нагревается, пластицируется и нагнетается в переднюю часть цилиндра перед соплом.
Под давлением расплавленного материала червяк отходится назад из установленного положения, зависящего от объема набираемой порции. После накопления определенной порции вращение червяка прекращается.
Форма смыкается, материальный цилиндр с соплом подводится вплотную к неподвижной полуформе, сопло соединяется с литниковым каналом формы, червяку сообщается движение вперед и он впрыскивает расплав в литьевую форму. Расплав в форме выдерживается под давлением.
Это необходимо для материала, для компенсации усадки и предупреждения обратного движения расплава из формы. По окончании выдержки под давлением червяк, вращаясь, отходит назад, при этом набирая новую порцию материала для следующего цикла литья.
Так как форма охлаждается, то изделие затвердевает, форма раскрывается, изделие извлекается.
В случае, если изделия автоматически не удаляются, термопласт автомат отключают, изделия удаляют в ручную, термопластавтомат вновь включают в работу.
Характеристика оборудования
Дата добавления: 2018-06-27; просмотров: 209; Мы поможем в написании вашей работы! |
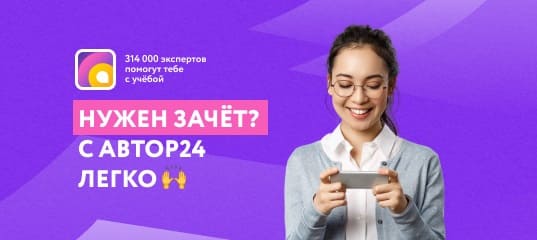
Мы поможем в написании ваших работ!