Весовой метод определения жаростойкости по уменьшению массы образца.
МОСКОВСКИЙ ГОСУДАРСТВЕННЫЙ ТЕХНИЧЕСКИЙ УНИВЕРСИТЕТ им. Н. Э. БАУМАНА Факультет «Машиностроительные технологии» Кафедра «Материаловедение» Реферат по курсу «Инженерия поверхности» на тему «Определение жаростойкости покрытий» Студент: Власова О.В. Группа: МТ8-82 Преподаватель: Пахомова С.А. Москва 2018 Оглавление Жаростойкие покрытия. 3 Методы определения жаростойкости: 4 1. Метод основан на ГОСТ 6130—71 «Металлы. Методы определения жаростойкости». 4 2. Весовой метод определения жаростойкости по уменьшению массы образца. 7 3. Метод непосредственного измерения глубины коррозии. 7 4. Комбинированный метод определения глубины коррозии. 8 Список литературы. 9
Жаростойкие покрытия
Жаростойкость (окалиностойкость)- способность материала противостоять химическому разрушению на воздухе или в газовых средах в процессе эксплуатации при температурах выше 550 °С без нагрузки или в слабонагруженном состоянии. Наиболее интенсивное разрушение материалов в первую очередь происходит на поверхности нагретых изделий, находящихся в непосредственном контакте с коррозионной средой.
С целью экономии дорогих и дефицитных жаростойких сплавов в ряде случаев оказывается целесообразным использование обычных металлов с последующей защитой их специальными жароустойчивыми покрытиями. Такие покрытия, естественно, относятся к классу неорганических и могут иметь как металлическую, так и неметаллическую природу.
|
|
К металлическим покрытиям, значительно повышающим жаростойкость сталей, относятся хромовые и алюминиевые, которые чаще всего наносятся на детали термодиффузионным способом. Для защиты от газовой коррозии при относительно невысоких температурах порядка 600-700 °С иногда применяют сравнительно тонкие покрытия хрома и никеля, наносимые путем электролиза из водных растворов.
Неметаллические покрытия могут быть получены на основе некоторых стеклоэмалей с повышенным содержанием тугоплавких окислов таких металлов, как хром, титан, алюминий и др. эти покрытия наносятся напылением с последующим оплавлением стеклоэмали и способны выдерживать температуры порядка 1100-1200 °С.
Наиболее высокую жаростойкость обеспечивают покрытия на основе тугоплавких карбидов, нитридов, боридов и силицидов металлов, выдерживающие температуру до 2000 °С. Они получаются при высоких температурах как из твердой, так и из газообразной фаз, содержащих реакционноспособные соединения углерода, бора и других элементов, в условиях непосредственного контакта этих соединений с покрываемыми поверхностями.
|
|
В последнее время весьма перспективными для повышения жароустойчивости поверхности металлов стали так называемые металлокерамические покрытия-керметы. Они образуются при введении в окислы или другие тугоплавкие соединения мелкодисперсных металлических порошков. Керметы дают возможность в широких пределах варьировать свойства покрытий, в частности, улучшать их теплопроводность, пластичность и ряд других свойств. Получение металлокерамических покрытий осуществляется методом газопламенного напыления.
Методы определения жаростойкости:
Метод основан на ГОСТ 6130—71 «Металлы. Методы определения жаростойкости».
Распространяется на определение жаростойкости газотермических покрытий, нанесенных на образцы из жаропрочных сплавов. Жаростойкость определяют путем выдержки образцов с покрытием (и контрольных без покрытия) в воздушной печи в течение заданного времени при постоянной температуре с последующим взвешиванием, осмотром, металлографическим исследованием. Ускоренные циклические испытания проводят с выключением печи через 10—50 часов.
Для испытания следует применять маркированные образцы, вырезанные из металла одной плавки. Образцы могут быть:
|
|
плоские размером 30 x 20 x 1,5 мм, кромки скруглены (r = 0,5—0,7 мм);
цилиндрические диаметром 10 и длиной 25 мм, кромки скруглены (r = 2 мм).
При невозможности изготовления стандартных образцов допускается применение образцов другой формы и размеров, но одинаковых для данной партии. Количество образцов должно быть не менее 3 на одну точку кривой привеса. Образцы очищаются от минерального масла обезжириванием и подвергаются пескоструйной обработке по рабочей поверхности. Не допускается касаться опескоструенной поверхности незащищенными руками и загрязнять ее. Проводят измерение и взвешивание образцов на аналитических весах. Данные заносят в журнал.
Нанесение покрытий проводят газотермическим методом, например, наплазменной установке или на высокоскоростной типа JP-5000. Следят за тем, чтобы перерыв между пескоструйной обработкой и нанесением покрытия был минимальным и не превышал 2 ч. После нанесения покрытий образцы измеряются и взвешиваются. Данные заносят в журнал. Образцы с покрытиями до начала испытаний хранят в закрытой чистой таре (эксикаторе). Перед испытанием образцы с покрытиями и контрольный образец без покрытия помещают в прокаленные до постоянного веса тигли и взвешивают на аналитических весах. Испытания на жаростойкость проводят в электрических печах сопротивления типа Г-30 в атмосфере воздуха.
|
|
Печь должна иметь автоматическую регулировку температуры с точностью до ±10° С и обеспечивать отклонение температуры в печи в зоне расположения образцов не более ±10° С от заданной температуры.
При определении жаростойкости следует применять керамические тигли, обеспечивающие сохранение осыпающихся оксидов. Тигель с образцами размещают в печи на подставках (керамических или металлических).
Взвешивание образцов производят на аналитических весах типа ВЛР-200 (АДВ-200М, ВАР-200) с точностью до ±1 мг.
Приборы и оборудование, имеющие метрологические характеристики, должны иметь свидетельство о поверке или метрологической аттестации.
Тигли загружают в печь, имеющую заданную температуру. Допускается загрузка образцов в холодную печь. Началом испытания считают момент достижения в рабочей зоне печи заданной температуры. Окончанием испытания считают момент выключения печи или выгрузки образцов. Температуру и продолжительность испытаний устанавливают в зависимости от срока службы изделия.
Для определения закономерности окисления тигли с образцами и образцы без тиглей взвешивают с интервалом времени: 50 ч при 1150° С и 20 ч при 1200° С.
Продолжительность испытаний, определяемая в зависимости от срока службы материала с защитным покрытием, должна соответствовать указанной в табл.1.
Таблица 1
Срок службы материала | Время испытаний, не менее |
Свыше 100000 | 10000 |
От 50000 до 100000 включ. | 5000 |
От 25000 до 50000 включ. | 3000 |
От 10000 до 25000 включ. | 2000 |
Менее 10000 | 20% от срока службы |
Рассчитывают толщину и массу покрытия каждого образца, данные заносят в журнал. Оценку жаростойкости проводят по привесу, по внешнему виду, металлографически.
Для оценки по привесу разность результатов взвешивания образцов в тиглях и без тиглей до (Р0) и после испытания (Рi) при каждом интервале времени относят к исходному весу образца или к площади его поверхности S.
Привес определяется в %:
где i = 50, 100, 150 ч и т. д. (при 1150° С); Р0 — исходный вес образца.
Металлографическое исследование структуры окисленного металла и покрытия, глубины зоны внутреннего окисления проводится в том случае, когда не удается сделать выбор наиболее жаростойкого покрытия по привесу и оценке внешнего вида.
По окончании испытаний строят график зависимости привеса (в размерных и безразмерных единицах) от продолжительности испытания, дают качественную оценку внешнего вида образца.
Для определения закономерности окисления периодический отбор образцов должен производиться через: 5, 10, 20, 50, 100, 200, 500, 1000, 2000, 5000, 10000 ч. Максимальная длительность испытания может не соответствовать времени, указанному в табл.1. Количество экспериментальных точек должно быть не менее пяти.
Каждая точка определяется как среднее арифметическое результатов испытания не менее трех образцов.
Испытания на жаростойкость проводятся с периодическим охлаждением образцов вместе с печью или на спокойном воздухе.
Циклы охлаждения выбираются в зависимости от назначения исследуемого металла.
Для промышленных установок, работающих непрерывно (в течение недели и более), образцы следует охлаждать через 100, 200, 500 ч и далее через каждые 200 ч.
Для установок, работающих периодически, а также при натурных и стендовых испытаниях образцы следует охлаждать в соответствии с запланированным режимом работы установок.
Температуру испытаний устанавливают в зависимости от условий эксплуатации исследуемого материала.
Весовой метод определения жаростойкости по уменьшению массы образца.
При определении жаростойкости по уменьшению массы образца с его поверхности полностью удаляют образовавшиеся продукты окисления, чтобы при осмотре образца через лупу с 10-кратным увеличением не было обнаружено следов окисления.
Очищенные от окалины образцы должны быть взвешены с точностью ±0,1 мг.
Далее расчет убыли массы образца и самого покрытия проводят аналогично расчету с привесом массы.
Дата добавления: 2018-05-09; просмотров: 926; Мы поможем в написании вашей работы! |
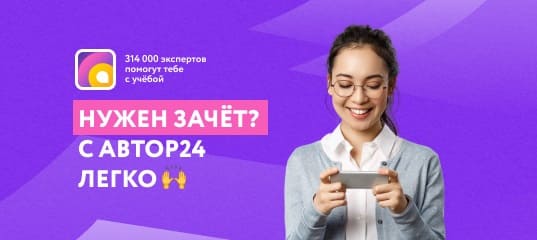
Мы поможем в написании ваших работ!