Монтаж керамических трубопроводов
ведут как отдельными трубами, так и укрупнительными звеньями (секциями) в две, три, пять труб при общей длине секции не более 8 м. Укладку трубопроводов производят снизу вверх по уклону, начиная от смотрового колодца раструбами против течения сточной жидкости. Трубы укладывают на подготовленное и тщательно спланированное основание с выдерживанием заданного уклона по ходовой визирке. Первую трубу укладывают на подушку (основание) смотрового колодца раструбом вверх, т. е. «от колодца». Закрепив надежно первую трубу, укладывают последующие, соединяя их с помощью раструбов. Правильность уклонов проверяют нивелиром, а прямолинейность оси в горизонтальной плоскости - шнуром. Лотки уложенных труб должны совпадать и не образовывать уступов. Опускаемую трубу заводят гладким концом в раструб уложенной трубы, оставляя зазор. Стыковые соединения трубопроводов из керамических труб уплотняют пеньковой смоляной или битуминизированной прядью с последующим устройством замка из асфальтовой мастики, цементного раствора или асбестоцементной смеси. Прядь обвивают вокруг трубы не менее двух раз, а затем уплотняют конопаткой (без ударов молотком). Для ускорения процесса укладки труб в траншею и заделки их стыков производят их предварительную укрупнительную сборку в звенья (секции) по две, три и пять труб. Иногда к керамическим трубам приделывают заранее кольца конической формы из асфальтовой мастики на внутренней поверхности раструба и на внешней поверхности другого конца трубы. Перед стыкованием таких труб асфальтовые кольца в раструбе и на концах труб покрывают расплавленным горячим битумом или обильно смазывают каким-либо растворителем (бензином, бензолом), размягчающим поверхность мастиковых колец. Благодаря конической форме прилитых асфальтовых колец и размягченности их поверхности имеется возможность свободного соединения труб так называемым холодным способом. После испарения растворителя и отвердения размягченной мастики получается прочный и герметичный стык труб.
|
|
83. Организация работ по прокладке стальных трубопроводов. Сварочно-монтажные работы при прокладке стальных трубопроводов.
Сварные стыки бывают поворотные, выполняемые при одновременном поворачивании труб и неповоротные (потолочные), свариваемые без поворота труб. Сварку поворотных стыков выполняют в основном при укрупнителыюй сборке и сварке труб в звенья (секции) на трубозаготовительных базах или на берме траншеи, а неповоротных - в траншеях (каналах) и при сваривании в полевых условиях длинных плетей или непрерывных ниток, которые поворачивать невозможно. Автоматическую сварку под слоем флюса поворотных стыков секций труб в базовых условиях осуществляют сварочными головками, сварочными тракторами, полуавтоматами. Трубы с толщиной стенки 8... 12 мм сваривают в три слоя, 12... 15 мм - в четыре слоя и 16...20 мм - в пять слоев. Первый слои называют корневым, или разделительным, следующие за ним - заполняющими и последний - облицовочным. Для сварки труб в секции наиболее целесообразно применять автоматическую сварку под слоем флюса, позволяющую в 5... 10 раз повысить скорость сварки и в 6... 8 раз производительность труда сварщика. После проверки соединений секции подают для нанесения на них слоя противокоррозионной изоляции или отгружают на трассу (при изоляции их на трассе в процессе укладки трубопровода в траншею). Доставленные на трассу изолированные трубы или их секции размещают вдоль траншеи на расстоянии 1 ... 1,5 м. Изолированный трубопровод можно укладывать в траншею следующими тремя способами: опуская секции или отдельные трубы со сваркой их в траншее; опуская сваренные из труб или секций плети с последовательным наращиванием их в приподнятом положении или на лежках (деревянных подкладках); опуская плети непрерывной ниткой с бермы траншеи. При укладке трубопровода опусканием сваренной плети с последовательным наращиванием ее на берме траншеи или опусканием непрерывной ниткой технологическая последовательность процессов обычно следующая: из изолированных на базе труб (секции) сваривают длинную плеть, которую по мере укладки в траншею постоянно наращивают, или непрерывную нитку; изолируют стыки между секциями; отрывают траншею (она может быть отрыта раньше, чем секции соединены в нитку, если прочность грунта обеспечивает удержание откосов без обвалов); трубопровод в виде плети или нитки, лежащей на берме траншеи, перекладывают в траншею. Плеть или непрерывную нитку трубопровода с бермы траншеи на ее дно укладывают четырьмя или тремя кранами-трубоукладчиками.
|
|
|
|
86. Гидравлическое испытание напорных трубявляется наиболее экономичным и простым; оно применимо для любых трубопроводов. Однако недостатком является необходимость вытеснения воды и опасность ее замерзания зимой. Для испытания применяют насосы или наполнительные агрегаты, производящие закачку воды, и гидравлические прессы или опрессовочные агрегаты, обеспечивающие подъем внутреннего давления. При небольших объемах испытаний применяют компактные перевозные установки и гидравлические прессы.
|
|
Предварительное гидравлическое испытание напорных трубопроводов на прочность, а также окончательное на герметичность производят внутренним испытательным давлением, принимаемым по проекту. По достижении испытательного давления опрессовочные агрегаты останавливают и трубопровод выдерживают на прочность, причем металлические, асбестоцементные и железобетонные трубопроводы должны выдерживаться под испытательным давлением не менее 10 мин, а пластмассовые (полиэтиленовые)- не менее 30 мин. Трубопровод считают выдержавшим предварительное испытание, если в нем под испытательным давлением не произошло разрыва труб и фасонных частей и нарушение заделки стыков, а под рабочим - не обнаружено утечек воды. Окончательное гидравлическое испытание трубопроводов начинают, если с момента засыпки их грунтом и заполнения водой прошло для труб металлических, асбсстоцементных и полиэтиленовых не менее 24 ч, а для железобетонных -- не менее 72 ч. По истечении этого времен давление в трубопроводе поднимают до испытательного и поддерживают его в течение всего периода испытания. При этом утечка воды (в л/мин) на 1 км трубопровода не должны превышать величин, указанных в СНиПе. Участок трубопровода признается выдержавшим окончательное испытание, если не обнаружено нарушений целостности трубопровода и если фактические утечки воды не превышают допустимые.
75. Промывка и дезинфекция трубопроводов.Трубопроводы диаметром более 300 мм помимо испытаний на прочность и плотность, как правило, подвергают дополнительным испытаниям для определения их фактической пропускной способности. Перед приемкой построенного трубопровода в эксплуатацию его предварительно промывают, а затем дезинфицируют хлорной водой при концентрации активного хлора 20... 40 мг/л и суточном контакте. В заключение трубопровод окончательно промывают до получения двух удовлетворительных бактериологических и физико-химических анализов воды. Акт о санитарной обработке трубопровода предъявляют приемочной комиссии, и он является документом, разрешающим присоединение (врезку) трубопровода к действующей сети.
88. Способы испытания напорных трубопроводов.После окончания монтажа и заделки стыков напорные и безнапорные трубопроводы подвергают испытанию в целях выявления и устранения дефектов и определения надежности построенных водоводов. К началу испытаний трубопроводы необходимо подготовить и в первую очередь очистить их внутреннюю полость.
Напорные трубопроводы испытывают на прочность и плотность (водонепроницаемость) гидравлическим или пневматическим способом. Выбор способа зависит от конкретныхусловий проведения испытаний - климатических условий, наличия воды для испытаний и возможностей ее сброса. В водопроводном строительстве, чаще применяют гидравлический способ испытания трубопроводов. Напорные трубопроводы, проложенные в траншеях или непроходных тоннелях и каналах, испытывают дважды. Вначале производят предварительное испытание (на прочность) - до засыпки траншеи и установки арматуры, а затем окончательное их испытание (на плотность) - после засыпки траншеи и завершения всех работ на испытываемом участке. Предварительное испытание трубопроводов выполняют строительно-монтажные организации, а окончательное - они же, но с участием представителей заказчика и эксплуатирующей организации.
Дата добавления: 2018-05-09; просмотров: 370; Мы поможем в написании вашей работы! |
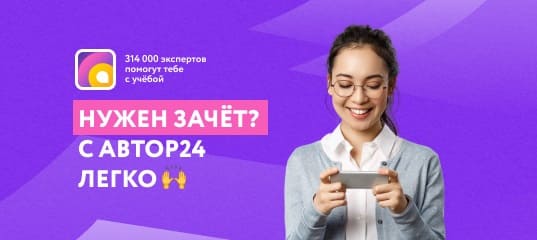
Мы поможем в написании ваших работ!