Формирование диэлектрических слоев на поверхности кремния
Формирование диэлектрических слоев на поверхности кремния в основном предназначено для решения трех задач. Во-первых, это пассивация поверхности пластины после создания в ней элементов микросхемы. Наличие такого слоя препятствует адсорбции атомов из окружающей среды на поверхность пластины, тем самым исключается образование электропроводящих дорожек, шунтирующих p-n-переходы. Обычно для решения этой задачи применяется SiO2 и Si3N4. Во-вторых, диэлектрические слои из SiO2 и Si3N4 используются при операции фотолитографии в качестве маскирующих покрытий. В-третьих, диэлектрические слои необходимы для создания МДП-транзисторов микросхем. Наиболее широко используются диэлектрические покрытия из SiO2, реже – из Si3N4 и еще реже – из Al2O3.
Формирование диэлектрических слоев SiO2 на поверхности кремния методом термического окисления
Получить пленку аморфного SiO2 на поверхности кремниевой пластины можно разными способами. Из них наиболее широко используется методы термического окисления и химического осаждения. При термическом окислении рост пленки SiO2 происходит за счет окисления кремния кислородом (сухое окисление) или парами воды (влажное окисление) согласно реакциям
Si + O2 ® SiO2,
Si + 2H2O ® SiO2 + 2H2.
Реакция окисления происходит на границе раздела Si - SiO2, то есть атомы и молекулы окислителя диффундируют через растущий слой оксида к поверхности кремния, где и происходит реакция. Температура процесса находится в диапазоне 800-1300°С. Чем выше температура, тем выше скорость роста пленки SiO2. Однако проводить процесс окисления пластин Si при высоких температурах, когда в них уже сформированы элементы микросхемы, нежелательно, поскольку дополнительный нагрев приводит к процессу диффузии примесей, уже внедренных в пластину.
|
|
Кинетика процесса окисления описывается моделью Дила-Гроува (рис.3.3). Авторы модели исходили из того, что весь процесс окисления можно разбить на несколько основных стадий: адсорбция и растворение молекул или атомов окислителя в приповерхностном слое, их диффузия через слой SiO2, реакция окисления. Каждая из этих стадий описывается плотностью потока окислителя j, под которой понимается количество молекул, проходящих через единичную поверхность за единицу времени. Плотность потока j1, описывающая адсорбцию и растворение молекул окислителя в приповерхностном слое, в первом приближении может считаться пропорциональной разности концентраций молекул в газовой фазе С0 и в слое оксида кремния С1
j1 = h(C0 - C1), (3.1)
|
|
где h – константа скорости растворения молекул окислителя в слое SiO2.
![]() |
Плотность потока молекул окислителя через растущий слой оксида кремния j2 определяется законом Фика:
где D – коэффициент диффузии молекул окислителя в SiO2; z0 – толщина слоя SiO; С2 – концентрация молекул на границе раздела SiO2 – Si.
Плотность потока j3, описывающая реакцию окисления, пропорциональна концентрации молекул окислителя C2
j3 = kC2, (3.3)
где k – константа скорости химической реакции.
![]() |
В установившемся режиме все эти три плотности потока должны быть равны. Объединяя (3.1) – (3.3), получим
![]() |
В данной системе уравнений реально измеряемой величиной является концентрация молекул окислителя в газовой фазе C0. Исключим концентрацию C1, а концентрацию C2 выразим через C0. В результате получим
![]() |
Пусть за время dt слой оксида кремния увеличивается на dz0, объем слоя SiO2 при этом увеличится на dV=Sdz0 , где S – площадь поверхности пластины. Для этого потребуется N молекул окислителя, причем N = Ci×dV= CiSdz0, где Ci - концентрация атомов кремния в слое SiO2 (для влажного окисления это количество в два раза больше). С другой стороны, из определения плотности потока следует, что это же количество молекул окислителя равно N = j3Sdt. Тогда с учетом (3.3) и (3.4) получим
|
|
![]() |
Произведем в уравнении (3.5) разделение переменных и проинтегрируем
![]() |
При определении нижнего предела интегрирования в уравнении (3.6) учтено, что при t=0 на поверхности кремния уже существовал слой SiO2 (так называемый самородный слой zi). В результате интегрирования получим
![]() |
Умножим левую и правую части выражения (3.7) на 2D и обозначим
![]() |
В результате выражение (3.7) после несложных преобразований примет вид
![]() |
где введено обозначение
Получилось квадратное уравнение относительно толщины оксидного слоя z0
![]() |
Учитывая, что z0 - величина положительная, решение уравнения будет
![]() |
![]() |
Проанализируем полученное выражение. При малых временах t, то есть при выполнении условия
![]() |
выражение (3.8) примет вид
![]() |
При больших временах, то есть при выполнении условия
выражение (3.8) примет вид
![]() |
Таким образом, на начальной стадии окисления толщина оксидной пленки увеличивается со временем по линейному закону, а при больших временах окисления зависимость толщины от времени становится корневой.
|
|
На рис. 3.4 представлены зависимости толщины слоя SiO2 от времени окисления при двух разных температурах. Видно, что температура значительно увеличивает скорость роста оксидного слоя. Повышение скорости роста с температурой объясняется увеличением коэффициента диффузии молекул окислителя в слое SiO2 и увеличением константы скорости химической реакции окисления на границе раздела SiO2 – Si.
Представленные на рис. 3.4 зависимости качественно верно описывают реальный процесс термического окисления кремния. Что касается конкретных значений скорости роста слоя SiO2, то, например, при сухом окислении и температуре порядка 1300 °С для получения слоя толщиной 1 мкм требуется примерно 15 часов. Если термическое окисление проводить в атмосфере водяного пара, то аналогичный слой при той же температуре можно получить примерно за 1час. Более высокая скорость объясняется меньшим эффективным диаметром молекул Н2О по сравнению с О2 и меньшей энергией активации диффузии молекул окислителя через растущий слой оксида. Качество слоев, полученных тем и другим способом, будет разным. При влажном окислении полученные слои SiO2 обладают худшим электрическими и защитными свойствами, чем слои, полученные сухим окислением. Поэтому обычно эти два способа комбинируют, тем самым удается получать слои SiO2 приемлемого качества с достаточно высокой скоростью.
Факторы, влияющие на скорость роста пленок SiO2
Кроме температуры и окислительной среды на скорость роста слоя SiO2 влияет давление газа-окислителя. Повышение давления увеличивает концентрацию молекул окислителя, растворенных в приповерхностном слое, тем самым увеличивается градиент концентрации молекул в слое SiO2, а значит, и скорость диффузии. Окисление при повышенном давлении водяного пара (ускоренное гидротермальное окисление) позволяет получать оксидные пленки толщиной 2-3 мкм, что особенно важно при формировании изопланарных структур, приборов с зарядовой связью и так далее. Недостатком метода является необходимость использования герметичных и высокопрочных реакторов вместо технологичных проточных систем.
На скорость роста слоя SiO2 оказывает влияние кристаллографическая ориентация кремниевой пластины. Окисление на пластине с ориентацией (111) происходит быстрее, чем с ориентацией (100). Влияние ориентации особенно заметно при относительно низких температурах. Так, например, при Т = 700 °С отличие в скорости окисления составляет 40 %, а при Т = 1200 °С всего 2 %. Зависимость скорости окисления от кристаллографической ориентации объясняется тем, что различным кристаллографическим направлениям пластины соответствует разное количество связей Si – Si.
Большое влияние на скорость роста слоя SiO2 оказывает концентрация легирующей примеси в исходной пластине кремния. Это влияние обусловлено явлением сегрегации примеси на границе раздела SiO2 – Si. Для одних примесных атомов растворимость в Si выше, чем в SiO2, поэтому при термическом окислении растущий оксид оттесняет примесные атомы в глубь пластины кремния. В результате оксидный слой обедняется данными примесными атомами. Так, в частности, ведут себя атомы фосфора, мышьяка, сурьмы. А такие атомы, как бор, напротив, лучше растворяются в SiO2, чем в Si, поэтому при окислении слой SiO2 получается обогащенным атомами бора. Наличие примесных атомов в слое SiO2 создает в нем механические напряжения и как бы «разрыхляет» его, что способствует увеличению скорости диффузии молекул окислителя через растущий слой оксида. Атомы фосфора, мышьяка и сурьмы оказывают влияние только на скорость химической реакции. Поэтому их влияние существенно только на ранней стадии процесса окисления, когда толщина слоя невелика и общая скорость окисления определяется скоростью химической реакции. Атомы бора, напротив, оказывают влияние и при относительно толстых слоях SiO2.
Существенный прогресс в технологии термического окисления был достигнут при добавлении в окислительную среду хлора и хлорсодержащих компонентов. Добавление хлора позволило увеличить скорость окисления, улучшить стабильность электрических характеристик и повысить пробивное напряжение оксидных слоев. Увеличение скорости окисления обусловлено образованием механических напряжений в растущем слое оксида, что способствует увеличению скорости диффузии молекул окислителя. Улучшение качества оксидных слоев обусловлено тем, что ионы хлора способны связать ионы натрия и калия, оказывающих очень негативное влияние на характеристики оксида. Данные ионы в слое SiO2 могут появиться на более ранней стадии технологического процесса, например, при удалении фоторезиста щелочными растворами на основе NaOH и KOH. Попав в слой SiO2, они способны перемещаться в нем под действием электрического поля, что резко снижает электрическую прочность оксидного слоя. Особенно важно это для подзатворного слоя диэлектрика в МДП-транзисторах.
Несмотря на то, что метод термического окисления позволяет получать качественные слои SiO2, он имеет один серьезный недостаток, а именно, с его помощью сложно получать «толстые» слои. При толщине порядка 1-2 мкм скорость роста слоя SiO2 становится практически равной нулю. Для многих задач (создание маскирующего покрытия при фотолитографии или подзатворного слоя диэлектрика в МДП-структурах) такая толщина и не требуется. Тем не менее, существуют задачи, для решения которых необходимо выращивать слои SiO2 толщиной несколько микрометров. Это требует применения других методов формирования оксидных слоев, в частности, метода химического осаждения.
Дата добавления: 2018-05-12; просмотров: 1492; Мы поможем в написании вашей работы! |
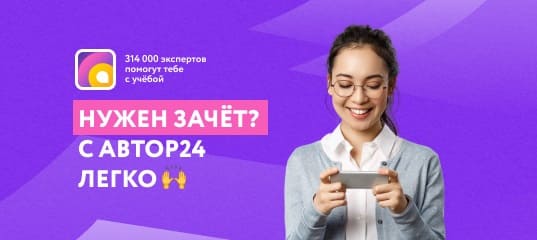
Мы поможем в написании ваших работ!