Дифференциальный (разностный) метод
Характеризуется разностью измеряемой и известной (воспроизводимой мерой) величинами. Например, измерение путем сравнения с рабочим эталоном на компаторе, выполняемые при поверке мер длины.
Преимущество - получение результатов с высокой точностью, даже при применении относительно грубых средств для измерения разности.
Нулевой метод
Метод сравнения с мерой, в которой результирующий эффект воздействия на прибор сравнения доводят до нуля.
Метод совпадения
Метод сравнения с мерой, в которой разность между значениями искомой и воспроизводимой мерой величин измеряют, используя совпадение отметок шкал или периодических сигналов.
Преимущество – метод позволяет существенно увеличить точность сравнения с мерой. Недостаток – затраты на приобретение более сложных СрИзм, необходимость наличия профессиональных навыков у оператора.
Метод замещения
Основан на сравнении с мерой, при котором измеряемую величину замещают известной величиной, воспроизводимой мерой, сохраняя все условия неизменными. Например, взвешивание с поочередным помещением измеряемой массы и гирь на одну и ту же чашку весов.
Преимущества – погрешность измерений мала, так как определяется в основном погрешностью меры и зоной нечувствительности прибора (ноль – индикатор). Недостаток – необходимость применения многозначных мер.
Косвенный метод измерения
|
|
Измерение физической величины одного наименования, связанной с другой искомой величиной, определенной функциональной зависимостью, с последующим расчетом путем решения управления. Косвенные методы широко применяются при химических методах испытания.
Преимущества – возможность измерения величин, для которых отсутствуют методы непосредственной оценки или они не дают достоверных результатов или связаны со значительными затратами. Недостатки – повышенные затраты времени и средств на измерение.
5.Погрешность – это отклонение результата измерения от истинного значения измеряемой величины.
Классификация погрешностей:
1) По способу выражения:
a) Абсолютная – погрешность, выраженная в единицах измеряемой величины ∆=Хд-Хизм
b) Относительная – погрешность, выраженная отношением абсолютной погрешности к результате измерений или действительному значению измеряемой величины γотн=(∆/Xд)* 100 .
c) Приведенная – это относительная погрешность, выраженная отношением абсолютной погрешности средства измерений к условию, принятому значению величины постоянному во всем диапазоне измерений (или части диапазона) γприв=(∆/Xнорм)*100, где Хнорм – нормирующее значение, установленное для приведенных значений. 2) По причинам и условиям возникновения:
|
|
a) Основная - это погрешность средств измерения, которое находятся в нормальных условиях эксплуатации, возникает из-за неидеальности функции преобразования и вообще неидеальности свойств средств измерений и отражает отличие действительной функции преобразования средств измерения в н.у. от номинальной нормированной документами на средства измерений (стандарты, тех. условия).
Рабочие условия измерений – это условия, при которых значения влияющих величин находятся в пределах рабочих областей, для которых нормируют дополнительную погрешность или изменение показаний СИ.
b) Дополнительная – это составляющая погрешности средств измерений, возникающая дополнительно к основной, вследствие отклонения какой-либо из влияющих величин от нормы её значения или вследствие её выхода за пределы нормированной области значений. Обычно нормируется наибольшее значение дополнительной погрешности.
Предел допускаемой основной погрешности – наиб. основная погрешность средств измерения, при которой СИ может быть годным и допущено к применению по тех. условиям.
Предел допускаемой дополнительной погрешности – наибольшая дополнительная погрешность, при которой СИ допущено к применению.
|
|
Например, для прибора с КТ 1.0 приведенная дополнительная погрешность по температуре не должна превышать ±1% при изменении температуры на каждые 10°.
Пределы, допустимой основной и дополнительной погрешности могут быть выражены в форме абсолютной, относительной или приведенной погрешности.
Для того чтобы иметь возможность выбирать СИ путем сравнения их характеристик вводят обобщенную характеристику данного типа СИ – класс точности (КТ). Обычно это предел допускаемых основной и дополнительной погрешностей. КТ позволяет судить в каких пределах находится погрешность СИ одного типа, но не является непосредственным показателем точности измерений, выполняемых с помощью каждого из этих СИ, т.к. погрешность зависит также от метода, условий измерений и т.д. Это нужно учитывать при выборе СИ в зависимости от заданной точности.
Значения КТ устанавливаются в стандартах или в технических условиях или других нормативных документах и выбираются в соответствии с ГОСТ 8.401-80 из стандартного ряда значений. Например, для электромеханических приборов: 0,05; 0,1; 0,2; 0,5; 1.0; 2,5; 4.0; 6.0.
Зная КТ СИ можно найти максимально допустимое значение абсолютной погрешности для всех точек диапазона измерений из формулы для приведенной погрешности: ∆maxдоп=(γприв*Xнорм)/100.
|
|
3) По характеру изменений:
a) систематические – составляющая погрешности, остающаяся постоянной или изменяющаяся по известной закономерности во все время проведения измерений. Может быть исключена из результатов измерения путем регулировки или введением поправок. К ним относят: методические П, инструментальные П, субъективные П и т д. Такое качество СИ, когда систематическая погрешность близка к нуля называют правильностью.
b) случайные – это составляющие погрешности, изменяющиеся случайным образом, причины нельзя точно указать, а значит, и устранить нельзя. Приводят к неоднозначности показаний. Уменьшение возможно при многократных измерениях и последующей статистической обработке результатов. Т.е. усредненный результат многократных измерений ближе к действительному значению, чем результат одного измерения. Качество, которое характеризуется близостью к нулю случайной составляющей погрешности называется сходимостьюпоказаний этого прибора.
c) промахи – грубые погрешности, связанные с ошибками оператора или неучтенными внешними воздействиями. Их обычно исключают из результатов измерений, не учитывают при обработке результатов.
4) По зависимости от измеряемой величины:
a) Аддитивные погрешности (не зависит от измеряемой величины)
b) Мультипликативные погрешности (пропорционально значению измеряемой величины).
Мультипликативная погрешность по-другому называется погрешностью чувствительности.
Аддитивная погрешность обычно возникает из-за шумов, наводок, вибраций, трения в опорах. Пример: погрешность нуля и погрешность дискретности (квантования).
Мультипликативная погрешность вызывается погрешностью регулировки отдельных элементов измерительных приборов. Например, из-за старения (погрешность чувствительности СИ).
5) В зависимости от влияния характера изменения измеряемой величины:
a) Статическая – погрешность СИ при измерении неизменной или медленно изменяющейся величины.
b) Динамическая – погрешность СИ, возникающая при измерении быстро меняющейся во времени ФВ. Динамическая погрешность является следствием инерционности прибора.
6.Государственная стандартизация — форма развития и проведения стандартизации, осуществляемая под руководством государственных органов по единым Государственным планам стандартизации.
Национальная стандартизация — проводится в масштабе государства без государственной формы руководства.
Международная стандартизация — проводится специальными международными организациями или группой государств с целью облегчения взаимной торговли, научных, технических и культурных связей.
Особое место в международной стандартизации занимают работы, проводимые странами-членами СНГ и в интересах их развития и экономической интеграции.
Устанавливаемые при стандартизации нормы оформляются в виде нормативно-технической документации по стандартизации — стандартов и технических условий.
Стандарт — нормативно-технический документ по стандартизации, устанавливающий комплекс норм, правил, требований к объекту стандартизации и утвержденный (принятый) компетентными органами. Стандарт разрабатывается на основе достижений науки, техники, передового опыта и должен предусматривать решения, оптимальные для общества. Стандарт может быть разработан как на материальные предметы (продукцию, сырье, образцы веществ), так и на нормы, правила, требования к объектам организационно-методического и общетехнического характера, порядок разработки документов, нормы безопасности, системы управления качеством, правила и порядок сертификации и др.Стандартизация — установление и применение правил с целью упорядочения деятельности в определенной области на пользу и при участии всех заинтересованных сторон в частности для достижения всеобщей оптимальной экономии при соблюдении условий эксплуатации (использования) и требований безопасности. Стандартизация основывается на объединенных достижениях науки, техники и передового опыта и определяет основу не только настоящего, но и будущего развития и должна осуществляться неразрывно с прогрессом.
Технические условия (ТУ) — нормативно-технический документ по стандартизации, устанавливающий комплекс требований к конкретным типам, маркам, артикулам продукции. Технические условия являются неотъемлемой частью комплекта технической документации на продукцию, на которую они распространяются,
7.Стандартизация направлена на достижение следующих основных целей: ускорение технического прогресса; повышение эффективности общественного производства и производительности труда (в том числе инженерного и управленческого); улучшение качества продукции и обеспечение его надлежащего уровня; совершенствование организации управления и установление рациональной номенклатуры выпускаемой продукции; развитие специализации в области проектирования и производства продукции; рациональное использование производственных фондов; экономию материальных и трудовых ресурсов; обеспечение охраны здоровья населения и безопасности труда; развитие международного экономического, технического и культурного сотрудничества; создание условий для развития экспорта товаров, отвечающих требованиям мирового рынка.
В соответствии с поставленными целями, задачами и направлениями стандартизации являются:
- установление требований к качеству готовой продукции на основе стандартизации ее качественных характеристик, а также характеристик сырья, материалов, полуфабрикатов и комплектующих изделий;
- разработка и установление единой системы показателей качества продукции, методов и средств контроля, испытаний и сертификации продукции, а также необходимого уровня надежности изделий с учетом их назначения и условий эксплуатации;
- установление норм, требований и методов в области проектирова-ния и производства с целью обеспечения оптимального качества и ис- ключения нерационального многообразия видов, марок и типоразмеров продукции;
- развитие унификации промышленной продукции как важнейшего условия специализации производства, комплексной механизации и автоматизации производственных процессов, повышения уровня взаимозаменяемости, эффективности эксплуатации и ремонта изделий; - обеспечение единства и достоверности измерений в стране, создание государственных эталонов единиц физических величин и совершенствование методов и средств измерений высшей точности;
- установление единых систем документации, в том числе унифицированных, используемых в автоматизированных системах управления, установление систем классификации и кодирования технико-экономической информации, разработка форм и систем организации производства;
- установление систем стандартов в области обеспечения безопасности труда, охраны природы и улучшения использования природных ресурсов.
8.Стандарты в РФ являются обязательными в пределах установленной сферы их действия и подразделяются на следующие категории: - государственные стандарты — ГОСТ; - отраслевые стандарты— ОСТ; - стандарты предприятий — СТП.
Государственные стандарты обязательны к применению всеми предприятиями, организациями и учреждениями во всех отраслях хозяйства. Они распространяются преимущественно на объекты межотраслевого применения, нормы, параметры, требования, показатели качества продукции, термины, обозначения и др., необходимые для обеспечения единства и взаимосвязи различных областей науки и техники, производства, а также на продукцию массового и крупносерийного производства широкого и межотраслевого применения. В частности, объектами государственной стандартизации должны быть:
общетехнические и организационно-методические правила и нормы (ряды номинальных частот и напряжений электрического тока, предпочтительные числа, требования охраны природной среды, рационального использования природных ресурсов и др. );
общие требования к продукции, имеющей межотраслевое применение (по устойчивости к воздействиям внешней среды, радиационной стойкости и др. );
основные эксплуатационные свойства и технические характеристики групп однородной продукции, имеющей межотраслевое применение (сырья, материалов, машин, приборов) и методы их контроля;
межотраслевые требования и нормы техники безопасности и производственной санитарии;
научно-технические термины, определения и обозначения;
единицы физических величин, государственные эталоны единиц физических величин, методы и средства поверки средств измерений, нормы точности и методики выполнения измерений, правила государственных испытаний средств измерений;
системы конструкторской, технологической, управленческой документации, формы и системы организации производства;
системы классификации и кодирования технико-экономической информации.
Государственные стандарты утверждает комитет Российской Федерации по стандартизации, метрологии и сертификации (Госстандарт РФ).
Отраслевые стандарты обязательны для всех предприятий и организаций данной отрасли, а также для предприятий и организаций других отраслей, применяющих (потребляющих) продукцию этой отрасли. Отраслевые стандарты организационно-методического характера, обяза-
тельны только для предприятий и организаций министерства (ведомства), их утвердившего.
Отраслевые стандарты устанавливают требования к продукции, не относящейся к объектам государственной стандартизации и необходимые для обеспечения взаимосвязи в производственно-технической и организационно-управленческой деятельности предприятий и организаций отрасли. В частности, объектами отраслевой стандартизации могут быть: изделия серийного и мелкосерийного производства; конкретные виды продукции, общие технические характеристики для которой установлены государственными стандартами; детали и сборочные единицы, технологическая оснастка и инструменты, сырье, материалы, полуфабрикаты, технологические нормы и типовые технологические процессы внутриотраслевого применения; нормы точности и методики выполнения измерений.
Отраслевые стандарты могут ограничивать применение государственных стандартов для используемой в отрасли номенклатуры изделий, типоразмеров и т. п. При этом, однако, технические характеристики продукции, включенные в отраслевой стандарт, не могут быть ниже, чем в государственном стандарте.
Отраслевые стандарты утверждает министерство, являющееся ведущим в производстве данного вида продукции.
Стандарты предприятия обязательны только для предприятия, утвердившего данный стандарт. Стандарты предприятия могут распространяться на составные части разрабатываемых или изготавливаемых на предприятии изделий; внутренние нормы и правила в области управления и организации производства, управления качеством продукции; оснастку и инструмент, типовые технологические процессы, методики измерений и контроля.
Стандарты предприятия могут также ограничивать, с учетом особенностей данного предприятия, применение номенклатуры деталей, узлов, материалов, установленной стандартами других категорий. На поставляемую предприятием продукцию стандарты предприятия не разрабатываются.
В зависимости от назначения и содержания Государственная система стандартизации устанавливает на продукцию стандарты всех категорий следующих видов:
общих технических условий;
общих технических требований (технических требований); параметров и (или) размеров;
типов, основных параметров и (или) размеров;
конструкции и размеров; марок; сортамента; правил приемки;
методов контроля (испытаний, анализа, измерений); правил маркировки, упаковки, транспортирования и хранения; правил эксплуатации и ремонта; типовых технологических процессов.
Общетехнические и организационно-методические стандарты (на общие нормы, показатели качества, методы расчета и проектирования, термины и определения, единицы физических величин, системы классификации и кодирования, требования к поставке, требования к изготовлению и др. ) на виды не подразделяются.
9.Разработка стандарта.Разработку государственных стандартов Российской Федерации осуществляют технические комитеты по стандартизации (ТК), а также предприятия, общественные объединения в соответствии с заданиями планов государственной стандартизации Российской Федерации, программ работ ТК и договоров на разработку стандартов или в инициативном порядке. При разработке стандартов следует руководствоваться законодательством Российской Федерации, государственными стандартами государственной системы стандартизации Российской Федерации и другими нормативными документами по стандартизации. При разработке стандартов используют научно-технические результаты научно-исследовательских, опытно-конструкторских, опытно-технологических, проектных работ, результаты патентных исследований, международные, региональные стандарты, правила, нормы и рекомендации по стандартизации, прогрессивные национальные стандарты других стран и иную информацию о современных достижениях отечественной и зарубежной науки, техники и технологии. Порядок разработки стандарта: 1 стадия — организация разработки стандарта; 2 стадия — разработка проекта стандарта (первая редакция); 3 стадия — разработка проекта стандарта (окончательная редакция) и представление его для принятия; 4 стадия — принятие и государственная регистрация стандарта; 5 стадия — издание стандарта.
Обновление стандарта.Обновление стандарта проводят для поддержания его соответствия потребностям населения, экономики и обороноспособности страны. ТК анализирует и обобщает предложения по обновлению стандарта, поступившие от предприятий — членов ТК, других предприятий, предпринимателей, научно-технических, инженерных обществ и других общественных объединений, государственных органов управления, в том числе от органов государственного контроля и надзора. В качестве предложения может быть представлен проект изменения или проект пересмотренного стандарта. С учетом поступивших предложений ТК разрабатывает и направляет в Госстандарт России (Госстрой России) проект изменения к стандарту (предложения по пересмотру стандарта) или предложение по отмене стандарта, решение по которым принимает Госстандарт России (Госстрой России).
Пересмотр стандарта.При пересмотре стандарта разрабатывают новый стандарт взамен действующего. При этом действующий стандарт отменяют, а в новом стандарте указывают, взамен какого стандарта он разработан. Новому стандарту присваивают обозначение старого стандарта с заменой двух последних цифр года принятия. Пересмотр стандарта на продукцию осуществляют при установлении новых, более прогрессивных требований, если они приводят к нарушению взаимозаменяемости новой продукции с продукцией, изготовляемой по действующему стандарту, и (или) изменению основных показателей качества продукции. При пересмотре стандарта на конкретную продукцию (невзаимозаменяемую по новому и действующему стандартам) в случае, если необходимо изготовлять запасные части и выполнять ремонт ранее выпущенных изделий, находящихся в эксплуатации, действующий стандарт не отменяют. В этом случае разработчик подготавливает проект изменения к действующему стандарту, в котором уточняет область его применения: "Настоящий стандарт применять только для изготовления запасных частей и ремонта изделий, находящихся в эксплуатации". При этом сохраняют регистрационный номер стандарта, к которому разработано такое изменение. При пересмотре стандарта одновременно осуществляют подготовку предложений по обновлению или отмене взаимосвязанных нормативных документов по стандартизации.
10.Взаимозаменяемость – свойство деталей, узлов, агрегатов и технических устройств, позволяющее установить их при сборке или заменить при ремонте без предварительной подгонки и сохранении эксплуатационных характеристик изделия.
Взаимозаменяемость обеспечивается системой принципов при проектировании, изготовлении, ремонте и утилизации изделий, собранных из независимых элементов.
Различают полную и неполную взаимозаменяемости как производства, так и изделия.
Полная взаимозаменяемость целесообразна при массовом и крупносерийном производстве, где все изготовленные сборочные единицы изделия или детали в целом являются взаимозаменяемыми, что позволяет сократить затраты на производство единицы продукции, легко автоматизировать производство, и не требует высокой квалификации рабочих, но, увеличиваются затраты на подготовку производства и трудно достичь высокой точности.
Неполная взаимозаменяемость применяется в производстве с высокими требованиями к точности и уникальности изделия, в этом случае лишь часть деталей является взаимозаменяемыми.
При сборке изделия используются следующие методы:
селекция;
регулирование;
пригонка.
Селекция применяется для достижения высокой точности при недостаточной точности оборудования, например при изготовлении подшипников, из серии выбирают детали с подходящими размерами.
При селекции разбивают подготовленные для сборки детали на несколько групп, уменьшая тем самым допуск на изготовление внутри группы в несколько раз по числу групп. На сборку поступают детали подходящих групп, обеспечивающие необходимые технические характеристики изделия, например радиальный зазор подшипника, что позволяет перенести затраты с производства на измерение (контроль).
Регулированиепредполагает сборку с регулированием положения или размеров одной или нескольких деталей, называемых компенсаторами.
Пригонка – сборка изделия с доработкой одной или нескольких сборочных единиц.
Различают также внешнюю и внутреннюю взаимозаменяемости.
Внешняя взаимозаменяемость относится к покупным деталям, например в электродвигателе внешнюю взаимозаменяемость обеспечивают по частоте вращения вала, в подшипниках качения – по внешнему и внутреннему диаметрам.
Внутренняя взаимозаменяемость распространяется на детали и агрегаты, входящие в изделие.
Различают геометрическую и функциональную взаимозаменяемости.
В геометрической взаимозаменяемостивзаимозаменяемыми считаются детали, геометрические размеры которых отличаются на величину, не превышающую допуск.
Функциональная взаимозаменяемость рассматривает отличие не только геометрических, но и других параметров (электропроводимость, теплопроводность, однородность механических свойств и т. д.). В этом случае необходимо установить соответствие между данными функциональными параметрами и эксплуатационными характеристиками изделия и, исходя из этого, назначить допуск на эти параметры, и, кроме того, обеспечить достаточную точность их измерения.
11.Номинальным размером называется основной размер, определенный исходя из функционального назначения детали и служащий началом отсчета отклонений.
Действительным размером называется размер, полученный в результате непосредственного измерения с допустимой погрешностью.
Предельными размерами называют два предельных значения размера, между которыми должен находится действительный размер.
Допуском размера, называется разность между наибольшим и наименьшим предельными размерами. Величина допуска обозначается в десятых, сотых долях миллиметра, микрометрах (0,001 мм). Допуск указывают в виде двух отклонений от номинального: верхнего и нижнего.
Верхним предельным отклонением называется разность между наибольшим предельным размером и номинальным, а нижним предельным отклонением – разность между наименьшим предельным размером и номинальным.
Чем меньше допуск, тем сложнее изготовить деталь.
При графическом изображении допусков пользуются нулевой линией.
Нулевой линией называется линия, соответствующая номинальному размеру, от которой откладываются отклонения.
Полем допуска называют интервал значений размеров, ограниченный предельными размерами. Зависит от класса точности.
На чертежах номинальный размер обозначается целыми числами, а отклонения в виде десятичной дроби проставляются от номинального размера одно над другим:
Верхнее – вверху, нижнее – внизу. Перед цифрой положительного отклонения ставится знак +, отрицательного -. Если отклонения одинаковы по значению, но различны по знаку ставится одна цифра перед знаками +.
Основные понятия и определения.
D - Отверстие - размер, который при обработке может только увеличиваться
(все параметры обозначаются прописными буквами).
d - Вал - размер, который при обработке может только уменьшаться
(все параметры обозначаются строчными буквами).
Номинальный размер – размер, проставленный на чертеже, служит началом отсчета предельных отклонений (нулевая линия) Dn – отверстия , dn – вала –определяется расчетом и округляется согласно ГОСТ «Нормальные линейные размеры».
Верхнее предельное отклонение отверстия – ES, вала – es
Нижнее предельное отклонение отверстия – EI, вала – ei
Наибольший предельный размер отверстия – Dmax, вала – dmax
Dmax = Dn + ES; dmax = dn + es
Наименьший предельный размер отверстия – Dmin, вала – dmin
Dmin = Dn + EI; dmin = dn + ei
Действительный размер – размер, полученный измерением с допускаемой
погрешностью измерений: Dd – отверстия, dd – вала
Допуск – разность между предельно допустимыми размерами или предельными
отклонениями : TD – допуск отверстия, Td –, допуск вала;
TD = Dmax – Dmin ,Td = dmax – dmin, или TD,(Td) = ES (es) – EI (ei)
Поле допуска определяется значением допуска и его положением относительно
номинального размера (нулевой линии).
12. Допуск размера – это разность между наибольшим и наименьшим предельными размерами или абсолютная величина алгебраической разности между верхним и нижним отклонениями.
Поле допуска – это поле, ограниченное верхним и нижним отклонениями. Все поля допуска для отверстий и валов обозначаются буквами латинского алфавита: для отверстий – прописными буквами (H, K, F, G и т. д.); для валов – строчными (h, k, f, g и т. д.).
Деталь, у которой положение поля допуска не зависит от вида посадки, называют основной деталью системы. Это может быть отверстие или вал, имеющие любое основное отклонение. В системе допусков и посадок СЭВ основными деталями служат отверстия или валы, имеющие основное отклонение, равное нулю.
Таким образом, основная деталь — это деталь, поле допуска которой является базовым для образования посадок, установленных в данной системе допусков и посадок.Поверхности, по которым соединяются детали, называют сопрягаемыми. В соединении двух деталей, входящих одна в другую, различают охватывающую поверхность и охватываемую. Наиболее распространены в машиностроении соединения с цилиндрическими и плоскими параллельными поверхностями. В цилиндрическом соединении поверхность отверстия охватывает поверхность вала. Охватывающую поверхность принято называть отверстие, охватывающую – вал. Эти же термины отверстие и вал условно применяют и для обозначения любых других нецилиндрическим охватывающим и охватываемым поверхностям.
Основное отверстие — отверстие, нижнее отклонение которого равно нулю EI = 0 . У основного отверстия верхнее отклонение всегда положительное и равно допуску ES — 0 = TD; поле допуска расположено выше нулевой линии и направлено в сторону увеличения номинального размера.
Основной вал — вал, верхнее отклонение которого равно нулю es = О. У основного вала Td = 0-(-еi) = \еi\, поле допуска расположено ниже нулевой линии и направлено в сторону уменьшения номинального размера.
13. Любая операция сборки деталей заключается в необходимости соединить или, как говорят, посадитьодну деталь на другую. Отсюда в технике принято выражение посадка для обозначения характера соединения деталей.
Под термином посадка понимают степень подвижности собранных деталей относительно друг друга.
Различают три группы посадок: с зазором, с натягом и переходные.
Зазором называют разность размеров отверстия D и вала d, если размер отверстия больше размера вала. Зазор обеспечивает свободное перемещение (вращение) вала в отверстии. Поэтому посадки с зазором называют подвижными посадками. Чем больше зазор, тем больше свобода в перемещении. Однако в действительности при конструировании машин с подвижными посадками выбирают такой зазор, при котором будет минимальным коэффициент трения вала и отверстия.
С натягом. Для этих посадок диаметр отверстия D меньше диаметра вала d. Реально осуществить это соединение можно под прессом, при нагреве охватывающей детали (отверстия) и (или) охлаждении охватываемой (вала).
Посадки с натягом называют неподвижными посадками, так как взаимное перемещение соединяемых деталей исключено.
Переходными эти посадки названы потому, что до сборки вала и отверстия нельзя сказать, что будет в соединении – зазор или натяг. Это означает, что в переходных посадках диаметр отверстия D может быть меньше, больше или равен диаметру вала d.
Допуск посадки — сумма допусков отверстия и вала, составляющих соединение.
14. Допуски и посадки нормированы государственными стандартами, входящими в две системы: ЕСДП - “Единая система допусков и посадок” и ОНВ - “Основные нормы взаимозаменяемости”. ЕСДП распространяется на допуски и посадки размеров гладких элементов деталей и на посадки, образуемые при соединении этих деталей. ОНВ регламентирует допуски и посадки шпоночных, шлицевых, резьбовых и конических соединений, а также зубчатых передач и колес.
Допуски и посадки указывают на чертежах, эскизах технологических картах и в другой технологической документации. На основе допусков и посадок разрабатываются технологические процессы изготовления деталей и контроля их размеров, а также сборки изделий.
На рабочим чертеже детали проставляют размеры, называемые номинальными, предельные отклонения размеров и условные обозначения полей допусков. Номинальный размер отверстия обозначают через D , а номинальный размер вала - d . В том случаи, когда вал и отверстие образует одно соединение за номинальный размер соединения, принимают общий размер вала и отверстия, обозначаемый d(D). Номинальный размер выбирают из ряда нормальных линейных размеров по ГОСТ 6636-69. ограничивающих число применяемых размеров. Для размеров в интервале 0,001-0,009 мм установлен ряд: 0,001; 0,002; 0,003;..0,009 мм . Предусмотрены четыре основных ряда нормальных размеров (Ra5; Ra10; Ra20; Ra40) и один ряд дополнительных размеров. Предпочтительны ряды с более крупной градацией размеров, т.е. ряд Ra5 сведут предпочесть ряду Ra10 и т.д.
Обработать деталь точно по номинальному размеру практически невозможно из-за многочисленных погрешностей, влияющих на прочес обработки. Размеры обрабатываемой детали отличаются от заданного номинального размера. Поэтому их ограничивают двумя придельными размерами, один из которых (больший) называется наибольшим предельным размером, а другой (меньший) - наименьшим предельным размером. Наибольший предельный размер отверстий обозначают D max , вала d max ; соответственно наименьший предельный размер отверстия D min , и вала d min .
Измерение отверстия или вала с допустимой погрешностью определяют их действительный размер. Деталь является годной, если ее действительный размер больше наименьшего предельного размера, но не превосходит наибольшего предельного размера.
На чертежах вместо предельных размеров рядом с номинальным размером указывают два предельных отклонения, например .
15. КВАЛИТЕТ (степень точности) – совокупность допусков, соответствующих одинаковой степени точности (одному квалитету) для всех номинальных размеров. Квалитет – ступень градации значений допусков системы.
В ЕСДП установлены 15 квалитетов для размеров менее 1 мм, и 20 квалитетов для размеров от 1 мм и выше.
Обозначаются квалитеты порядковыми номерами: 01; 0; 1; 2; 3; …15; 16; 17; 18.
Допуски в каждом квалитете возрастают с увеличением номинальных размеров, однако, степень точности этих размеров остаётся одной (равной порядковому номеру квалитета). Для одного номинального размера, с изменением квалитета, допуск изменяется в сторону увеличения (по закону геометрической прогрессии со знаменателем 1,6, начиная с 5 квалитета) при переходе с одного квалитета на другой с большим порядковым номером. При изменении степени точности на 5 квалитетов допуск, соответственно, изменяется в 10 раз.
При проектировании изделий (исходя из теоретических и экспериментальных исследований и опыта проектирования изделий с различными степенями точности), при назначении уровней точности на размеры этих изделий, руководствуются рекомендациями стандартов ЕСДП.
Квалитеты 01; 0 и 1 рекомендуются для ответственных размеров элементов плоскопараллельных концевых мер длины.
Квалитеты 2; 3 и 4 – для гладких калибров-пробок и калибров-скоб; размеры ответственных деталей суперточных станков (станки класса точности «С») и др.
Квалитеты 5 и 6 – для размеров деталей высокоточных соединений, например, подшипников качения, шеек коленчатых валов, ответственные детали станков повышенной точности (класс точности «А» и «В») и др.
Квалитеты 7 и 8 – наиболее используемые для размеров деталей точных ответственных соединений деталей в машиностроении, приборостроении и др. отраслях.
Квалитеты 9 и 10 – для размеров деталей неответственных соединений, входящих в соединения с другими деталями.
Квалитеты 11 и 12 – для размеров деталей, получаемых штамповкой, специальным литьём и др.
Квалитеты 13 и 14 – для размеров деталей, получаемых литьём в земляные формы, ковкой и др.
Квалитеты 15; 16 и 17 – предназначены для неответственных размеров деталей, не входящих в соединения с другими деталями, а также для межоперационных размеров.
В стандартах ЕСДП допуски установлены для всех номинальных размеров, начиная с размеров менее 1 мм до размера 10000 мм.
При заданных квалитете и интервале номинальных размеров (номинальном размере) значение допуска одинаково и для вала, и для отверстия.
В целях оптимизации количества допусков все номинальные размеры (предусмотренные стандартными рядами) разбиты на диапазоны [приложение 1]:
1. Охватывает размеры до 1 мм (включая 1 мм).
2. Охватывает размеры свыше 1 мм до 500 мм включительно.
3. Охватывает размеры свыше 500 мм до 3150 мм включительно.
4. Охватывает размеры свыше 3150 мм до 10000 мм включительно.
5. Дополнительный диапазон для размеров свыше 10000 мм до 40000 мм включительно.
Номинальные размеры в диапазоне, начиная со второго, разбиты на интервалы. Например, диапазон 2 разбит на 13 интервалов (свыше 1 мм до 3 мм включительно; свыше 3 мм до 6 мм; свыше 6 мм до 10 мм и т.д… свыше 400 мм до 500 мм включительно). Кроме того, отдельные интервалы данного диапазона разделены на два подинтервала. Например, интервал размеров свыше 80 мм до 120 мм разделён на подинтервалы: свыше 80 мм до 100 мм, и свыше 100 мм до 120 мм.
Все номинальные размеры, объединённые в одном интервале (подинтервале) при заданном квалитете имеют один (одинаковый) допуск.
Размеры в каждом интервале объединены, исходя из условия, чтобы допуски граничных размеров интервала (T(Dmin) и T(Dmax)) отличались бы от допусков средних размеров данных интервалов (T ( )) не более чем на (5÷8)%.
Ряды допусков
Для нормирования различных уровней точности деталей, имеющих один номинальный размер, установлено 20 рядов допусков, называемых квалитетами. Квалитеты обозначаются порядковым номером, возрастающим с увеличением допуска: IT01; IT0; IT1; IT2;.......IT17; IT18, где IT - международный допуск.
ПРИМЕР: IT8 - допуск ИСО по 8 квалитету.
Квалитеты 01, 0, 1 устанавливают величины допусков концевых мер длины, т.е. регламентируют точность их изготовления.
Квалитеты 2...7 регламентируют точность калибров и особо точных изделий.
Квалитеты 5...12 регламентируют точность сопрягаемых размеров и размеров, входящих в размерные цепи.
Квалитеты 12...17 регламентируют точность неответственных несопрягаемых размеров, размеров в грубых соединениях, а также размеры заготовок.
18 квалитет нормирует точность размеров деталей из пластмасс и древесины.
Чем выше номер квалитета, тем больше допуск.
По своей организации ЕСДП представляет собой набор полей допусков, которые служат исходным материалом для образования посадок. Каждое поле ЕСДП характеризуется двумя параметрами, не связанными между собой:
Величиной допуска IT;
Величиной основного отклонения D.
Величина допуска IT определяется номером квалитета и номинальным размером
Номинальные размеры элементов деталей после их определения расчётом выбираются из рядов предпочтительных чисел, представляющих собой геометрическую прогрессию с определёнными знаменателями.
Теоретически можно создать такую систему, в которой давались бы точностные требования на все предпочтительные номинальные размеры, охватываемые стандартом, но практически система такая стала бы очень громоздкой. Но для размеров близких по величине отклонения расчётные будут отличаться незначительно. Трудность изготовления деталей, в каком – либо небольшом диапазоне размеров тоже примерно одинаковая. Поэтому принято допуски давать одинаковыми для определённого интервала размеров.
Последняя цифра интервала относится к данному интервалу, а первая цифра к предыдущему.
Интервалы подразделяются на основные и промежуточные. Основные интервалы используются для определения всех допусков системы и тех предельных отклонений, которые более плавно изменяются в зависимости от номинального размера. Промежуточные интервалы введены для номинальных размеров свыше 10 мм и делят каждый основной интервал на два (в некоторых случаях на три ). Они используются для определения тех предельных отклонений, которые связаны с номинальным размером относительно крутой зависимостью (валы, обозначаемые буквами от «a» до «cd» и от «r» до «zc»; отверстия от «A» до «CD» и от «R» до «ZC»).
16.Калибры – средства измерительного контроля, предназначенные для проверки соответствия действительных размеров, формы и расположения поверхностей деталей заданным требованиям.
Калибры применяют для контроля деталей в массовом и серийном производствах. Калибры бывают нормальные и предельные.
Нормальный калибр – однозначная мера, которая воспроизводит среднее значение (значение середины поля допуска) контролируемого размера. При использовании нормального калибра о годности детали судят по зазорам между поверхностями детали и калибра. Оценка зазора, следовательно, результаты контроля в значительной мере зависят от квалификации контролера и имеют субъективный характер.
Предельные калибры обеспечивают контроль по наибольшему и наименьшему предельным значениям параметров. Изготавливают предельные калибры для проверки размеров гладких цилиндрических и конических поверхностей, глубины и высоты уступов, параметров резьбовых и шлицевых поверхностей деталей. Изготавливают также калибры для контроля расположения поверхностей деталей, нормированных позиционными допусками, допусками соосности и др.
При контроле предельными калибрами деталь считается годной, если проходной калибр под действием силы тяжести проходит, а непроходной калибр не проходит через контролируемый элемент детали. Результаты контроля практически не зависят от квалификации оператора.
По конструкции калибры делятся на пробки и скобы. Для контроля отверстий используют калибры-пробки, для контроля валов – калибры-скобы.
По назначению калибры делятся на рабочие и контрольные.
Рабочие калибры предназначены для контроля деталей в процессе их изготовления. Такими калибрами пользуются рабочие и контролеры отделов технического контроля (ОТК) на предприятиях.
Комплект рабочих предельных калибров для контроля гладких цилиндрических поверхностей деталей включает:
проходной калибр (ПР), номинальный размер которого равен наибольшему предельному размеру вала или наименьшему предельному размеру отверстия;
непроходной калибр (НЕ), номинальный размер которого равен наименьшему предельному размеру вала или наибольшему предельному размеру отверстия.
Проходной калибр контролирует предел максимума материала детали, значит, выявленный таким калибром брак будет исправимым (на детали остался избыток материала, который можно снять при дальнейшей обработке детали с помощью того же технологического процесса).
Непроходной калибр контролирует предел минимума материала детали, значит, выявленный таким калибром брак будет неисправимым (с детали снято слишком много материала, который нельзя вернуть с помощью того же технологического процесса).
Для всех калибров устанавливают допуски на изготовление рабочих поверхностей, а для проходного калибра, который при контроле детали изнашиваются более интенсивно, дополнительно устанавливают границу износа.
Контрольные калибры предназначены для контроля рабочих калибров-скоб. Для калибров-пробок контрольные калибры не изготавливают, поскольку наружные размеры достаточно просто проконтролировать универсальными средствами измерений – измерительными головками на стойках, гладкими или рычажными микрометрами и другими накладными приборами.
В комплект контрольных калибров входят три калибра, изготовленные в виде шайб:
контрольный проходной калибр (К-ПР);
контрольный непроходной калибр (К-НЕ);
Дата добавления: 2018-05-12; просмотров: 549; Мы поможем в написании вашей работы! |
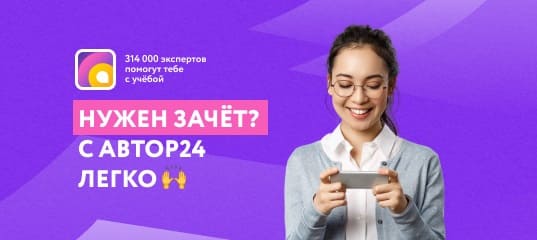
Мы поможем в написании ваших работ!