Линейный электрогидравлический привод подачи силового узла с автономным задатчиком перемещения
Выпускаемые в настоящее время агрегатные, шлифовальные, фрезерно-центровальные и другие гидрофицированные станки для массового автоматизированного производства имеют, как правило, гидравлический привод с путевым управлением. Это не позволяет встраивать их в ГПС и требует разработки принципиально иных схем построения приводов, которые обеспечивают, во-первых, автоматизацию переналадок циклов движения силовых узлов при смене объектов производства и, во-вторых, максимальную унификацию базовых деталей станков и силовой части приводов в обычном и новом исполнении, предназначенном для ГПС.
Указанная цель может быть реализована при использовании ЛЭГП с автономными задатчиками перемещений (АЗП) в качестве управляющих устройств. Принципиальная схема привода показана на рис. 1.
Рис. 1. Принципиальная схема ЛЭГП с АЗП
Силовой стол 1с установленным на нем рабочим органом (РО) 2 перемещается от гидроцилиндра 3. Скорость и ход устанавливаются автономным задатчиком, выполненным в виде отдельного устройства 5, состоящего из управляющего шагового двигателя (ШД) 6, дросселирующего распределителя 8, механизмов сравнения 7 и обратной связи 4. При работе ЛЭГП с АЗП сигнал от системы ЧПУ в виде угла поворота ШД поступает в механизм сравнения, который перемещает распределитель в сторону уменьшения рассогласования между заданным положением, определяемым ШД, и фактическим положением РО.
|
|
Выбор рассмотренной схемы объясняется следующими преимуществами, которые дает ЛЭГП с АЗП:
· гидроцилиндр обеспечивает отсутствие промежуточных передач между двигателем и РО станка, малую инерционность подвижных частей, и, как следствие, высокое быстродействие, хорошую плавность хода в широком диапазоне изменения скоростей;
· автономный задатчик позволяет охватить конечное звено (РО станка) отрицательной обратной связью по положению и тем самым повысить точность и жесткость (в частности, компенсировать упругие и тепловые деформации, возникающие в силовых элементах привода), а также предохранить его звенья от поломок при перегрузках благодаря возможности установки дополнительных предохранительных элементов;
· используемый в качестве задающего шагового электродвигателя задатчик обеспечивает простую и надежную конструкцию привода, так как в этом случае отпадает необходимость в установке датчиков обратной связи и применении соответствующих электронных схем управления.
Кроме того, выполнение задатчика в виде малогабаритного автономного устройства обеспечивает легкость встраивания в существующее оборудование, что позволяет унифицировать силовые узлы станков обычного исполнения предназначенных для ГПС.
|
|
Указания к расчёту режимов резания
Металлорежущие станки предназначены для обработки металла путем снятия стружки. Они обеспечивают изготовление деталей требуемой формы с заданными точностью размеров и шероховатостью поверхности. Обработка может производиться при помощи одного или нескольких инструментов.
В зависимости от способа обработки существуют станки следующих основных групп: токарные, сверлильные, шлифовальные, фрезерные, строгальные.
Металлорежущий станок, на котором производится процесс резания, является технологическим объектом управления. Основными технологическими процессами металлообработки являются точение, расточка, строгание, сверление, фрезерование и шлифование.
Точение (рис.2) осуществляется на токарных станках за счет вращения обрабатываемого изделия 1 (главное движение) и перемещения резца 2 (движение подачи).
Окружная скорость изделия в точке соприкосновения резца с обрабатываемой деталью называется скоростью резания. Скорость резания, м/мин, определяется по формуле
(1)
|
|
где dи — диаметр обработки, м; ωи — угловая скорость изделия, рад/с.
Величина подачи определяется перемещением резца, приходящимся на один оборот изделия. Глубина резания представляет собой разность радиусов обрабатываемой и обработанной поверхностей. Быстрое перемещение суппорта, зажим и отжатие обрабатываемого изделия, перемещение люнета, задней бабки и другие движения относятся к вспомогательным.
В процессе обработки происходит износ инструмента h, который можно разбить на три периода (рис. 1,6): I - приработка, II - нормальный и III- усиленный износ, заканчивающийся "посадкой" (затуплением) инструмента. Износ h0, при котором общий срок службы инструмента получается наибольшим, а расход наименьшим, называют оптимальным. Оптимальный износ обеспечивает минимальную стоимость инструмента, отнесенную на одну деталь. По достижении оптимального износа h0 инструмент перетачивают. Время работы инструмента между двумя переточками определяет его стойкость Т.
Рис. 2. Схема токарной обработки (а) и график износа иноса инструмента (б)
Параметры обработки связаны между собой эмпирической формулой
(2)
|
|
где Су — коэффициент, характеризующий вид и условия обработки, а также материал изделия и резца; s — подача, мм/об; tр — глубина резания, мм: Т - стойкость, мин; xv, yv, т - показатели степени, зависящие от свойств обрабатываемого металла, материала резца и вида обработки.
При снятии стружки резцом возникает усилие F, приложенное к режущей кромке инструмента, которое может быть разложено (рис. 1, а) на три составляющие:
(3)
где Fz - главная касательная сила, действующая в направлении траектории главного движения, преодолеваемая шпинделем станка и называемая усилием резания; Fy - радиальная сила, действующая нормально к обработанной поверхности и создающая давление на суппорт; Ру - осевая сила, действующая в направлении подачи.
Расчет усилия резания производится по эмпирической формуле
(4)
где СF коэффициент, характеризующий материал детали, резца и вид токарной обработки; хF, уF, n показатели степени.
Коэффициенты и показатели степени в (3) и (4) принимаются по справочникам режимов резания [11].
По аналогичным формулам рассчитываются усилия Fу и Fx, которые можно принять равными Fx ≈ 0,4Fz и Fу ≈ 0,3Fz.
Усилие FП действующее на механизм подачи, помимо собственного усилия подачи Fx содержит также составляющие, возникающие в направляющих за счет сил трения от действия усилий Fz и Fу :
FП=Fx+μ(Fz+Fу) (5)
где μ - коэффициент трения в направляющих.
Мощность резания, кВт,
(6)
Мощность подачи, кВт,
(7)
Поскольку скорость подачи во много раз меньше скорости резания, мощность подачи намного меньше мощности резания и составляет относительно последней 1 — 0,1 %.
Расточка применяется для черновой, чистовой и алмазной обработок отверстий на токарных и расточных станках. При расточке резцы, оснащенные пластинками из быстрорежущей стали, твердых сплавов или из ограненного технического алмаза, закрепляют в оправках. Скорость, силу и мощность резания при черновой и чистовой расточках определяют по тем же формулам (2) -- (6), что и для точения.
Строгание (рис. 3) можно рассматривать как точение участка детали с бесконечно большим диаметром. При этом деталь 1 перемещается возвратно - поступательно относительно резца 2, снятие стружки происходит в течение рабочего хода, а обратный ход совершается вхолостую. Скорость, с которой деталь перемещается относительно резца при рабочем ходе, называется скоростью резания v, м/мин. Продольное перемещение стола является главным движением.
Перемещение резца за один двойной ход стола перпендикулярно главному движению называется движением подачи х, мм/мин. Величина /р, на которую углубляется резец в изделие при одном проходе, называется глубиной резания. Перемещение траверсы и суппортов, подъем резца при обратном ходе, установочные медленные перемещения стола относятся к вспомогательным движениям.
Скорость, усилия и мощность резания при строгании определяют по тем же формулам (1) - (3), что и для точения.
Сверление (рис. 4) осуществляется за счет вращательного (главного) движения инструмента - сверла 1 (иногда детали) и его продольного перемещения в детали 2 - движения подачи. Продольное и поперечное перемещения стола, перемещение шпиндельной бабки, зажим колонны являются вспомогательными движениями.
Окружную скорость на периферии сверла v, м/мин, называют скоростью резания при сверлении. Перемещение сверла вдоль своей оси за один оборот определяет подачу. Скорость резания при сверлении находят по эмпирической формуле
(8)
где Сv -- коэффициент, зависящий от материала детали и сверла; dc -- диаметр сверла, мм; Т - стойкость сверла, мин; s -- подача, мм/об; уv,, zv, т -- показатели степени, зависящие от материала детали и диаметра сверла.
Вращающий момент, Нм, при сверлении определяют по эмпирической формуле
(9)
откуда, зная угловую скорость сверла, рассчитывают мощность резания, кВт:
(10)
Сила, Н, преодолеваемая механизмом подачи при сверлении, также определяется по эмпирической формуле:
(11)
Рис. 4. Схема сверления
Все коэффициенты и показатели степени, входящие в эмпирические формулы, приводятся в справочниках по режимам резания
Фрезерование (рис. 5) производится вращающейся фрезой 1, имеющей несколько режущих лезвий — зубьев, каждое из которых за счет поступательного перемещения фрезы относительно детали 2 снимает стружку в пределах определенного угла поворота фрезы, а затем вращается вхолостую. Главным движением при фрезеровании является вращение фрезы, перемещение детали относительно инструмента представляет движение подачи. Быстрое перемещение стола, на котором укреплена деталь, и ускоренное перемещение шпиндельной бабки при наладке относятся к вспомогательным движениям.
Под скоростью резания, v, м/мин, понимают окружную скорость на периферии фрезы, которую определяют по эмпирической формуле
(12)
где Сv,q, т, п., хv, уv, k — коэффициент и показатели степени, зависящие от материала детали и фрезы, вида обработки и охлаждения; dФ -- диаметр фрезы, мм; sz -- подача на зуб фрезы, мм; В — ширина фрезерования, мм; z -- число зубьев фрезы.
Рис. 5. Схема фрезерования
Усиление резания, Н, определяют по выражению
(13)
Мощность резания, кВт, рассчитывают по формуле
(14)
где nф — частота вращения фрезы, nф = 30wФ/p.
Все коэффициенты и показатели степени в (12) и (14) приводятся в справочниках по режимам резания.
Шлифование (рис. 6) производится, как правило, абразивными кругами, при этом каждое абразивное зерно в зоне обработки работает как резец, снимая стружку с детали в пределах определенного угла поворота. Главное движение при шлифовании — вращение шлифовального круга 1; поступательное перемещение круга относительно детали 2 представляет движение подачи.
Различают плоское шлифование (рис. 6, д, б), при котором обрабатывается плоская поверхность, и круглое шлифование (рис. 6, в, г), при котором обрабатывается поверхность тела вращения. Плоское шлифование может осуществляться периферией (рис. 6, д) или торцом (рис. 6, б) шлифовального круга 1.
Рис. 6. Схема шлифования на станках
а — плоскошлифовальном с прямоугольным столом; б — плоскошлифовальном с круглым столом; в — круглошлифовальном; г — внутришлифовальном; 1 - шлифовальный круг; 2 - деталь; 3 - стол (магнитная плита)
Стол 3, на котором устанавливается магнитная плита для крепления деталей 2, может иметь прямоугольную и круглую формы. На шлифовальных станках с прямоугольным столом (рис. 6, а) последний совершает возвратно-поступательное движение (продольная подача sп), периодическое дозированное перемещение (поперечная подача sп,п) и перемещение на врезание sвр. На шлифовальных станках с круглым столом (рис. 6, б) одним из движений подачи является вращение деталей с магнитной плитой и столом со скоростью wс. Другое движение подачи - перемещение sк шлифовального круга в радиальном направлении относительно стола, а также перемещение на врезание sвр.
Выбор режимов резания при шлифовании определяется по технологическим таблицам, составленным на основании эмпирических данных.
При круглом наружном (рис. 6, в) и внутреннем (рис. 6, г) шлифованиях изделие получает вращение со скоростью wи как правило, в сторону, противоположную вращению шлифовального круга. Относительное перемещение шлифовального круга вдоль оси вращения детали представляет продольную подачу sп.
Скорость резания при шлифовании v, м/с, определяется окружной скоростью шлифовального круга и равна примерно 20—80 м/с. При этом допускаются небольшие глубины шлифования tр, равные 0,05— 0,005 мм. Все большее применение стало находить силовое шлифование, обеспечивающее значительную глубину шлифования — до 10 мм.
В процессе шлифования абразивные зерна притупляются, что при постоянной подаче влечет за собой увеличение мощности шлифования и образование прижогов на поверхности детали. Для устранения этих явлений круг правят, срезая слой абразива и вводя в работу зерна с новыми режущими кромками. Время работы круга между двумя последовательными правками характеризует его стойкость Т, мин.
При плоском шлифовании периферией круга на станках с прямоугольным столом стойкость может быть рассчитана по формуле
(15)
где Сv — коэффициент, зависящий от скорости резания; sП — скорость движения стола (продольная подача), м/мин; sПП — поперечная подача в долях ширины шлифовального круга; sвр -- подача на врезание на ход стола, мм/ход; k1, k2 — коэффициенты, зависящие от обрабатываемого материала и диаметра шлифовального круга.
Дата добавления: 2018-05-12; просмотров: 363; Мы поможем в написании вашей работы! |
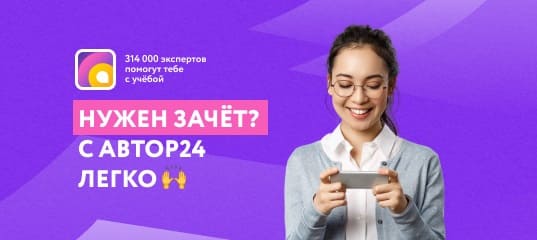
Мы поможем в написании ваших работ!