АНАЛИЗ СУЩЕСТВУЮЩЕГО ТЕХНОЛОГИЧЕСКОГО ПРОЦЕССА
При изучении существующих процессов ставятся задачи их глубокого анализа, так как без него невозможно оценить технологический процесс и, целесообразно, высказать предложения по его улучшению и модернизации.
Анализ существующего технологического процесса должен быть проведен с точки зрения обеспечения качества продукции.
При этом следует выяснить, правильно ли он составлен для выполнения требований чертежа и соблюдаются ли все требования
технологического процесса в цехе.
Для этого можно рекомендовать следующий примерный перечень вопросов:
а) рациональность метода получения заготовки для данного масштаба производства;
б) соответствие реальной заготовки чертежу в отношении фактических припусков на обработку и выполнения прочих технических требований;
в) правильность выбора черновых, чистовых и промежуточных баз на операциях технологического процесса, соблюдение принципа единства технологических баз;
г) правильность установки последовательности операций процесса для достижения заданной точности детали;
д) соответствие параметров установленного оборудования требованиям данной операции;
е) соответствие режимов резания прогрессивным;
ж) степень оснащенности операций;
з) применяемость высокопроизводительного режущего инструмента и новых марок материалов его режущей части;
и) соблюдение технологического процесса на операциях и качество обработки деталей;
|
|
к) степень концентрации операций технологического процесса и др.
Качество обработки деталей на каждой операции оценивается на основании данных о браке. Первоначальным источником о количестве брака по операциям могут служить данные, полученные из отдела технического контроля. Однако для большей объективности следует руководствоваться личными наблюдениями и результатами измерений важнейших параметров на операциях технологического процесса.
Следует также проанализировать причины появления брака и обратить внимание на реальное состояние оборудования в отношении возможности обеспечения заданной точности на операциях.
Правильность разработки технологического процесса и выбора оборудования целесообразно оценить с помощью таких количественных показателей, как коэффициент загрузки оборудования, коэффициенты использования оборудования по основному времени и по мощности. Способ определения этих коэффициентов приведен в параграфе 4.5.
Экономические показатели существующего технологического процесса по операциям на данном этапе проектирования сводятся к определению технологической себестоимости, так как сопоставление вариантов предлагаемого процесса с существующим достаточно произвести на основании этого показателя.
|
|
Результаты анализа существующего технологического процесса должны быть детально изложены в соответствующем разделе пояснительной записки, так как именно анализ может дать предпосылки для разработки варианта процесса.
Поэтому совершенно недопустимо заменять анализ технологического процесса простым его описанием или переписыванием сведений из технологических карт. Анализ целесообразно выполнять со ссылками на технологические карты.
При разработке курсового проекта перед студентом не ставится задача коренной переработки существующей технологии, это не диктуется соответствующими особыми условиями, например резким увеличением производственной программы, связанным с изменением типа производства. В большинстве случаев оказывается достаточным рассмотреть варианты по изменению нескольких, а иногда двух-трех технологических операций и сопоставить их по методике, предлагаемой ниже.
ВЫБОР ЗАГОТОВКИ
Общие рекомендации.Метод выполнения заготовок для деталей машин определяется назначением и конструкцией детали, материалом, техническими требованиями, масштабом и серийностью выпуска, а также экономичностью изготовления. Выбрать заготовку – значит установить способ ее получения, наметить припуски на обработку каждой поверхности, рассчитать размеры и указать допуски на неточность изготовления.
|
|
Для рационального выбора заготовки необходимо одновременно учитывать все вышеперечисленные исходные данные, так между ними существует тесная взаимосвязь. Окончательное решение можно принять только после экономического комплексного расчета себестоимости заготовки и механической обработки в целом.
При выполнении курсового проекта делается краткий анализ существующего способа получения заготовки на заводе. В анализе должны быть отражены: экономичность способа в условиях зовода; технологический процесс получения заготовки, который иллюстрируется эскизами; оснащенность технологического процесса, элементы его механизации и автоматизации, качество заготовки, неполадки в технологическом процессе, причины брака и методы его устранения. Следует также выявить основные технико-экономические показатели процесса получения заготовки на заводе: себестоимость, процент использования материала, трудоемкость и производительность на отдельных операциях.
|
|
Перечисленные факторы следует учитывать и при самостоятельной разработке заготовки на основании чертежа детали. Работа ведется в такой последовательности:
1) выбирается вид заготовки с учетом факторов, определяющих эксплуатационные характеристики детали, тип производства, экономию металла и др.
2) на все обрабатываемые поверхности назначаются, а на некоторые – рассчитываются аналитическим способом припуски обработку;
3) выполняется чертеж заготовки, и подсчитывается ее масса;
4) рассчитывается стоимость заготовки.
Иногда целесообразно сделать сопоставление двух возможных способов получения заготовки, как это делается при сравнении предлагаемого способа с существующим на заводе (с целью выбора оптимального).
Таблица 2.2. Сортовой покат и профили, область их применения
Вид проката или профиль | ГОСТ | Область применения |
Сортовой: Круглый горячекатаный повышенной и нормальной точности Круглый калиброванный квадратный, шестигранный, полосовой ( горячекатаный обычной точности) квадратный, шестигранный (калиброванный) | 2590-71 7415-75 2591-71 103-76 8559-75 8560-68 | Гладкие и ступенчатые валы с небольшим перепадом диаметров ступеней, стаканы диаметром до 50 мм, втулки с наружным диаметром до 25 мм. Крепеж, небольшие детали типа рычагов, тяг, планок и клиньев |
Листовой: толстолистовой горячекатаный тонколистовой горячекатаный и холоднокатаный Трубы: стальные бесшовные горячекатаные и холоднокатаные | 19903-74 19903-74 19903-74 8732-78 8734-75 | Фланцы, кольца, плоские детали различной формы; цилиндрические полые втулки Цилиндры, втулки, гильзы шпиндели, стаканы, барабаны, ролики, валы |
Периодический продольный | 6319-78 | Ступенчатые валы крупносерийного и массового производства |
Поперечно-винтовой | 8320-73 | Валы, полуоси, рычаги и другие детали крупносерийного и массового производства |
Примечание. Периодический и продольный прокат и поперечно-винтовой имеют переменное по длине сечение, остальные, приведенные в таблице, – постоянное.
Заготовки из проката. Виды проката, его характеристики и область применения приведены в таблице 2.2.
Прокат может применяться в качестве заготовки для непосредственного изготовления деталей либо в качестве исходной заготовки при пластическом формообразовании.
Таблица 2.3. Характеристика некоторых методов выполнения заготовок давлением углеродистые и легированные стали и специальные сплавы).
Метод выполнения заготовок | Размеры или масса | Точность выполнения заготовок | Шероховатость Rz, мкм |
Штамповка на молотах и прессах | Масса до 200 кг, наименьшая толщина стенок 2,5 мм | По ГОСТ 7505-74 | 320...160 |
Штамповка с последующей чеканкой | Масса до 100 кг, наименьшая толщина стеною 2,5 мм | 0,05...0,1 мм | 40…10 |
Штамповка (высадка) на ГКМ | Масса 0,1...100 кг диаметр до 315 мм | По ГОСТ 7505-74 | 320..160 |
Штамповка выдавливанием | Диаметр до 200 мм | 0,2...0,5 мм | 320...80 |
Специальный прокат применяется в условиях массового или крупносерийного производства, что в значительной степени снижает припуски и объем механической обработки.
Кованые и штампованные заготовки. Характеристика некоторых, наиболее часто применяемых в курсовых проектах методов получения заготовок путем обработки металлов давлением, приведены в таблице 2.3. Область применения этих методов – серийное и массовое производство. Штамповка на кривошипных прессах в 2...3 раза производительнее по сравнению со штамповкой на молотах, припуски и допуски уменьшаются на 20.. 35 %, расход металла снижается на 10...15 %. Заготовки для деталей типа стержня с утолщением, колец, втулок, деталей со сквозными и глухими отверстиями [33] целесообразно получать на горизонтально-ковочных машинах (ГКМ).
Отливки. Точность отливок в песчаные (земляные) формы и припуски на обработку регламентированы для чугунных деталей (в том числе и для деталей из ковкого чугуна) ГОСТ 1855-55 и для стальных деталей – ГОСТ 2009-55.
Установлены три класса точности отливок одинаковых для чугунных и стальных заготовок (табл. 2.4). При выборе литой заготовки в первую очередь следует определить класс точности в зависимости от масштаба производства и способа получения отливки, который обусловливается характером технологической оснастки литейного цеха и механизацией процессов изготовления и сборки форм и стержней. Данные для выбора класса точности отливок приведены в таблице 2.5. Следует учитывать, что основным фактором, определяющим выбор класса точности отливок, является себестоимость, которая при выборе отливки более высокого класса точности должна быть компенсирована снижением металлоемкости и стоимости механической обработки.
Наиболее универсальным методом является литье в песчаные формы, однако изготовление форм требует больших затрат времени. Так, набивка одного кубического метра формовочной смеси вручную занимает 1,5...2 ч, а с помощью пневматической трамбовки – 1ч. Применение пескомета для набивки форм сокращает время набивки до 6 мин. Встряхивающие машины ускоряют набивку по сравнению с ручной в 15, а прессование – в 20 раз.
Таблица 2.4.Допустимые отклонения по размерам, отливок, из серого чугуна и стали
Наибольшие габариты отливки, мм | Номинальный размер части отливок, на который дается допуск, мм | ||||||
До 50 | 50...120 | 120...260 | 260...600 | 500...800 | 800...1250 | 1250...2000 | |
1-й класс точности | |||||||
До 120 120…260 260…500 500…1250 1250…3150 3150…5000 | ±0,2 ±0,3 ±0,4 ±0,6 ±0,8 ±1,0 | ±0,3 ±0,4 ±0,6 ±0,8 ±1,0 ±1,2 | – ±0,6 ±0,8 ±1,0 ±1,2 ±1,5 | – – ±1,0 ±1,2 ±1,4 ±1,8 | – – – ±1,4 ±1,6 ±2,0 | – – – ±1,6 ±2,0 ±2,5 | – – – – ±2,5 ±3,0 |
2-й класс точности | |||||||
До 260 260…500 500…1250 1250…3150 3150…6300 | ±0,6 ±0,8 ±1,0 ±1,2 ±1,5 | ±0,8 ±1,0 ±1,2 ±1,5 ±1,8 | ±1,2 ±1,2 ±1,5 ±2,0 ±2,2 | – ±1,5 ±2,0 ±2,5 ±3,0 | – – ±2,5 ±3,0 ±4,0 | – – ±3,0 ±4,0 ±5,0 | – – – ±5,0 ±6,0 |
Примечание. 3-й класс точности предназначается для единичного производства.
Таблица 2.5. Зависимость класса точности отливок от характера производства
Класс точнос-ти | Характер производства | Количест-во изделий в год | Оснастка | Изготовление | |
форм | стержней | ||||
1 | От крупносерийного до массового | Свыше 10000 | Металлические модели и стерж-невые ящики, кон-дукторы для калибрования стержней | Машинная сбора стержней в кондук- торах | Машинное калиброва- ние в кондукторах перед сборкой |
2 | От серийного до крупносерийного | 1000… 10000 | Металлические модели в стержн-евые ящики | Машинное | Крупных- машинное мелких- ручное |
Литьем в землю по металлическим моделям при машинной формовке получают отливки массой до 10...15 т при наименьшей толщине стенок 3...8 мм.
Литье в оболочковые формы применяют главным образом получении ответственных фасонных отливок. При этом полуалюминиевые и стальные отливки массой до 150 кг; мини-толщина стенок для алюминиевых отливок – 1...1,5 мм, – 3...5 мм. Обеспечивается точность отливок в пределах 12...14-го квалитетов по СТ СЭВ 144-75, параметр шероховатости поверхности Rz 40...10. При автоматизации этого метода получать до 450 полуформ в 1 ч.
Литье в кокиль экономически целесообразно при величине не менее 300...500 шт. для мелких отливок и 30...50 шт. крупных отливок. Производительность способа – до 30 отливок 1 ч. Этим способом можно получать отливки массой 0,25…7 т, имеющие точность 13...15-го квалитетов по СТ СЭВ 144-75 и параметр шероховатости поверхности Rz 80…10.
Литье по выплавляемым моделям экономически целесообразно для литых деталей сложной конфигурации из любых сплавов при партии свыше 100 шт. Метод обеспечивает получение массой до 50 кг с минимальной толщиной стенок 0,5 мм; точность 11...12-го квалитетов по СТ СЭВ 144-75, параметр шероховатости поверхности Rz 40...10.
Литье под давлением применяется в основном для получения фасонных отливок из цинковых, алюминиевых, магниевых и латуневых сплавов. Способ считается целесообразным при партии 1000 и более деталей. Произво-дительность метода до 1000 деталей в час. Можно получать отливки массой до 100 кг с минимальной толщиной стенок 0,5 мм; точность 11.„12-го квалитетов СТ СЭВ 144-75, параметр шероховатости поверхности не больше Rz 20.
Центробежное литье может применяться при выполнении заготовок имеющих форму тел вращения. Производительность до 15 отливок в 1 ч. Масса отливок 0.01...3 т, минимальная толщина стенок 0,5 мм, точность 13...15-го квалитетов по СЭВ 144-75, параметр шероховатости поверхности 160...40.
Экономическое обоснование выбора заготовки. При выборе заготовки для вновь проектируемого технологического процесса возможны следующие варианты: 1) метод получения заготовки принимается аналогичным существующему в данном производстве; 2) метод получения заготовки изменяется, однако это обстоятельство не вызывает изменений в технологическом процессе механической обработки; 3) метод получения заготовки принимается, и в результате этого существенно изменяется ряд операций механической обработки детали.
Предпочтение следует отдавать той заготовке, которая обеспечивает меньшую технологическую себестоимость детали. Если же сопоставляемые варианты по технологической себестоимости оказываются равноценными, предпочтительным следует считать вариант заготовки с более высоким коэффициентом использования материала.
Себестоимость заготовок из проката:
где М – затраты на материал заготовки, руб.;
Со з – технологическая себестоимость операций правки, калибрования прутков, разрезки их на штучные заготовки:
где Сп з – приведенные затраты на рабочем месте, коп/ч;
Тшт(ш к) – штучное или штучно-калькуляционное время выполнения загото-вительной операции (правки, калибрования, резки и др.).
Затраты на материал определяются по массе проката, требующегося на изготовление детали, и массе сдаваемой стружки. При этом необходимо учитывать стандартную длину прутков к отходы в результате некратности длины заготовок этой стандартной длине:
где Q – масса заготовки, кг, S – цена 1 кг материала заготовки, руб.; q – масса готовой детали, кг; Sотх – цена 1 т отходов, руб.
Стоимость заготовок, получаемых такими методами, как в обычные земляные формы и кокили, литье по выплавляемым моделям, литье под давлением, горячая штамповка на молотах прессах, ГКМ, а также электровысадкой, можно с достаточной для курсового проектирования точностью определить по формуле:
где Ci– базовая стоимость 1 т заготовок, руб ;
– коэффициенты, зависящие от класса точности, группы сложности, массы, марки материала и объема производства заготовок.
Для отливок, полученных литьем в обычных земляных форм рекомендуется пользоваться нижеприведенными данными.
Таблица 2.8. Значение коэффициентов kС, kВ, kП, kC.
kС
Материал отливки | Группы сложности | ||||
1 | 2 | 3 | 4 | 5 | |
Чугун, сталь | 0,4 | 0,83 | 1 | 1,2 | 1,45 |
Алюминиевые сплавы | 0,82 | 0,89 | 1 | 1,1 | 1,22 |
Медные сплавы и бронзы | 0,97 | 0,98 | 1 | 1,02 | 1,04 |
kВ
Масса отливки, кг | Материал отливок | |||
Чугун | Сталь | Алюминиевые сплавы | Бронза | |
0,5…1 | 1,1 | 1,07 | 1,05 | 1,01 |
1…3 | 1 | 1 | 1 | 1 |
3..10 | 0,91 | 0,93 | 0,96 | 0,99 |
10 20 | 0,84 | 0,87 | 0,92 | 0,97 |
20 50 | 0,8 | 0,82 | 0,89 | 0,95 |
50 200 | 0,74 | 0,78 | 0,85 | 0,93 |
200 500 | 0,67 | 0,74 | 0,82 | 0,9 |
kП
Материал отливки | Группы сложности | ||||
1 | 2 | 3 | 4 | 5 | |
Чугун | 0,52 | 0,76 | 1 | 1,2 | 1,44 |
Сталь | 0,5 | 0,77 | 1 | 1,2 | 1,48 |
Алюминиевые сплавы | 0,77 | 0,9 | 1 | 1,11 | 1,22 |
Медные сплавы и бронзы | 0,91 | 0,96 | 1 | 1,05 | 1,08 |
Коэффициенты выбираются по следующим данным:
а) в зависимости от точности отливок значения коэффициента kт: для отливок из черных металлов – 1-ый класс точности – 1,1; 2-ой класс точности – 1,05; 3-ий класс точности – 1; для отливок из цветных металлов (по ОСТ 1.41154-72) – 4-ый класс точности – 1,1; 5-ый класс точности – 1,05; 6-ой класс точности – 1;
б) в зависимости от марки материала значения коэффициента kM, следующие: для чугуна – СЧ10, СЧ15, СЧ18 – 1; СЧ20, СЧ25, СЧЗО—1,04; СЧ35, СЧ40, СЧ45 – 1,08; ВЧ45-5, ВЧ50-2 – 1,19; КЧЗО-6, КЧЗЗ-8, КЧ35-10 –1.12; для стали – углеродистой – 1,22; низколегированной – 1,26; легированной – 1,93; для сплавов цветных металлов – алюминиевых – 5,94; медноцинковых – 5,53; бронзы оловянисто-свинцовой – 6,72.
Коэффициенты, зависящие от группы сложности отливок kС, массы отливок kВ и объема производства kп, определяются по табл. 2.8.
Таблица 2.9.Группы серийности отливок в зависимости вот способа получения и объема производства.
kC
Масса отливки кг | Объем ( тыс, шт.) при группах серийности | ||
1 | 2 | 3 | |
Литье в обычные земляные формы и кокили | |||
0,5..1 | Свыше 500 | 100…500 | Менее 100 |
1…3 | »350 | 75…350 | »75 |
3…10 | »200 | 30…200 | »30 |
10…20 | »100 | 15…1000 | »15 |
20…50 | »60 | 10…60 | »10 |
50…200 | »40 | 7,5…40 | »7,5 |
200…500 | »25 | 4,5…25 | »4,5 |
Литье по выплавляемым моделям | |||
0,1…0,2 | Свыше 400 | 300…400 | Менее 300 |
0,2…0,5 | »300 | 225…300 | »225 |
0,5…1 | »15 | 11…15 | »11 |
1…2 | »12 | 9…12 | »9 |
2…5 | »10 | 7…10 | »7 |
5…10 | »4 | 3…4 | »3 |
10 | »3 | 2…3 | »2 |
Литье под давлением. | |||
0,1..0,2 | Свыше 600 | 450…500 | Менее 450 |
0,2…0,5 | 500 | 375…500 | 375 |
0,5…1 | 400 | 300…400 | 300 |
1…2 | 300 | 225…300 | 225 |
2…5 | 200 | 150…200 | 150 |
5…10 | 100 | 75…100 | 75 |
10…20 | 50 | 35…50 | 35 |
Чтобы определить коэффициент kп, для курсового проектирования в качестве объема производства можно принимать годовую программу. Для этого необходимо сначала установить группу серийности по табл. 2.9, затем на основании группы серийности по табл. 2.8 найти значения kп.
Таблица 2.10 Значения коэффициентов kC и kВ
kC
Материал отливки | Группы сложности | ||||
1 | 2 | 3 | 4 | 5 | |
Сталь углеродистая | 0,86 | 0,92 | 1 | 1,12 | 1,2 |
Сталь низколегированная | 0,86 | 0,93 | 1 | 1,11 | 1,23 |
Сталь высоколегированная | 0,85 | 0,90 | 1 | 1,12 | 1,26 |
Медные сплавы | 0,865 | 0,925 | 1 | 1,15 | 1,26 |
Бронза безоловянистая | 0,9 | 0,95 | 1 | 1,08 | 1,19 |
Бронза оловянистая | 0,92 | 0,95 | 1 | 1,10 | 1,15 |
kB
Масса отливки кг | Материал отливок | ||||
Сталь углерод истая и низколегированная | Сталь высоколегированная | Медный сплав | Бронза безоловянистая | Бронза оловянистая | |
0,05..0,10 | 1,37 | 1,31 | 1,20 | 1,30 | 1,30 |
0,10…0,20 | 1 | 1 | 1 | 1 | 1 |
0,20…0,50 | 0,75 | 0,78 | 0,95 | 0,79 | 0,83 |
0,50…1 | 0,7 | 0,74 | 0,89 | 0,76 | 0,80 |
1,00…2 | 0,62 | 0,63 | 0,86 | 0,71 | 0,76 |
2…5 | 0,50 | 0,53 | 0,82 | 0,64 | 0,70 |
5,00…10 | 0,45 | 0,48 | 0,78 | 0,61 | 0,67 |
Свыше 10 | 0,38 | 0,40 | 0,72 | 0,57 | 0,64 |
Коэффициенты выбираются по следующим данным:
а) независимо от точности отливок значения коэффициента;
kт принимаются равными 1;
б) в зависимости от материала отливок значения коэффициента kм следующие: для стали углеродистой – 1; низколегированной – 1,08; высоколегированной – 1,1; медных сплавов – 2,44; бронзы безоловянистой – 2,11; оловянистой – 2,4.
Коэффициенты, зависящие от группы сложности отливок kC и массы kС, принимаются по табл. 2.10.
Коэффициент kП для отливок, получаемых по выплавляемым моделям, определяется независимо от марки материала отливки.
Группа серийности, на основании которой выбираются значения коэффициента kП, приведена в табл. 2.9.
Значения коэффициента kП в зависимости от группы серийности составляют: 1-я группа серийности – 0,83; 2-ая – 1; 3-ая – 1,23.
Таблица 2.11. Значения коэффициетов kC , kВ , kП
kC
Материал отливки | Группы сложности | |||
1 | 2 | 3 | 4 | |
Алюминиевые сплавы | 0,88 | 0,94 | 1 | 1,07 |
Медные сплавы | 0,90 | 0,95 | 1 | 1,07 |
Цинковые сплавы | 0,88 | 0,93 | 1 | 1,07 |
kП
Материал отливки | Группы серийности | ||
1 | 2 | 3 | |
Алюминиевые сплавы | 0,92 | 1 | 1,09 |
Медные сплавы | 0,93 | 1 | 1,07 |
Цинковые сплавы | 0,93 | 1 | 1,07 |
kВ
Масса отливки, кг | Материал отливки | ||
Алюминиевые сплавы | Медные сплавы | Цинковые вплавы | |
0,1..0,2 | 1 | 1 | 1 |
0,2…0,5 | 0,90 | 0,89 | 0,91 |
0,5…1 | 0,81 | 0,81 | 0,82 |
1…2 | 0,75 | 0,75 | 0,75 |
2…5 | 0,69 | 0,71 | 0,7 |
5…10 | 0,64 | 0,67 | 0,63 |
Свыше 10 | 0,62 | 0,65 | 0,61 |
Коэффициенты выбираются по следующим данным:
а) независимо от класса точности значения коэффициента kТ, принимают равными 1;
б) в зависимости от материала отливок коэффициент kМ принимается: для алюминиевых сплавов – 1; медных – Л,11;
цинковых – 1,29.
Значения коэффициентов kС, kПи kПприведены в табл. 2.11. Группа серийности принимается по табл. 29.
Отливки к той или иной группе сложности можно отнести по следующим признакам [33].
I группа – удлиненные детали типа тел вращения, которые можно отливать не только стационарным, но и центробежным способом. К ним относятся простые и биметаллические вкладыши, некоторые втулки и гильзы, трубы, цилиндры, некоторые типы шпинделей с фланцами, коленчатые и распределительные валы и др. Отношение длины к диаметру у таких деталей больше единицы.
II группа – детали типа дисков: маховики и основные диски муфт сцепления, шкивы, диски, корпусы подшипников.
III группа – простые по конфигурации коробчатые плоские детали, для формовки которых не требуется большого количества стержней. К этой группе относятся передние, боковые и нижние крышки двигателей; крышки коробок скоростей, передних бабок и других корпусных деталей, суппорты станков, кронштейны, планки, вилки, рычаги.
IV группа – закрытые корпусные детали коробчатого типа, внутри которых монтируются механизмы машин. Это – блоки и головки цилиндров автомобильных, тракторных и других двигателей, корпусы коробок передач, картеры двигателей, корпусы мостов автомобилей и тракторов, картеры рулевого управления, передние бабки, коробки подач и фартуки токарных станков, коробки скоростей и подач сверлильных станков и другие детали сложной формы, для изготовления которых требуется значительное количество стержней при формовке.
V группа – крупные и тяжелые коробчатые детали, на которых обычно монтируются узлы и механизмы машин. К ним можно отнести коробчатые литые рамы тракторов и сельскохозяйственных машин, станины металлорежущих станков и литейных машин, а также прессов, компрессоров и др. Внутри таких деталей обычно не монтируются какие-либо механизмы, т. е. они служат как несущие конструкции.
Коэффициенты выбираются по следующим данным:
а) в зависимости от точности штамповок по ГОСТ 7505-74 значения коэффициента kТ принимаются: повышенная точность – 1,05; нормальная – 1;
б) в зависимости от марки материала штамповки значения коэффициента kМ составляют: для углеродистой стали 08 – 85 – 1;
стали 15Х – 50Х – 1,13; стали 18ХГТ – ЗОХГТ – 1,21; стали ШХ15 – 1,77; стали 12ХНЗА – ЗОХНЗА – 1,79.
Значения коэффициентов kСи kВ приводятся в табл. 2.12.
Таблица 2.12. Значение Коэффициентов kС , kB.
kС
Материал штамповок | Группы сложности | |||
1 | 2 | 3 | 4 | |
Сталь углеродистая 08 – 85 | 0,75 | 0,84 | 1 | 1,15 |
Сталь 15Х – 50Х | 0,77 | 0,87 | 1 | 1,15 |
Сталь 18ХГТ – 30ХГТ | 0,78 | 0,88 | 1 | 1,14 |
Сталь ШХ15 | 0,77 | 0,89 | 1 | 1,13 |
Сталь 12ХНЗА – 30ХНЗА | 0,81 | 0,90 | 1 | 1,1 |
kВ
Масса штамповки кг | Материал штамповок | ||||
Сталь 08– 85 | Сталь 15Х–50Х | Сталь 18ХГТ–30ХГТ | Сталь ШХ15 | Сталь 12ХНЗА –30ХНЗА | |
Не более 0,25 | 2 | 2 | 1,94 | 1,82 | 1,62 |
0,25…0,63 | 1,85 | 1,64 | 1,61 | 1,52 | 1,42 |
0,63…1,6 | 1,33 | 1,29 | 1,29 | 1,3 | 1,25 |
1,60…2,5 | 1,14 | 1,14 | 1,15 | 1,14 | 1,11 |
2,50…4 | 1 | 1 | 1 | 1 | 1 |
4,0…10 | 0,87 | 0,89 | 0,89 | 0,88 | 0,9 |
10,0…25 | 0,8 | 0,8 | 0,79 | 0,76 | 0,8 |
25,0…63 | 0,73 | 0,73 | 0,74 | 0,71 | 0,75 |
63,0…160 | 0,7 | 0,7 | 0,72 | 0,65 | 0,7 |
Таблица 2.13 Объем производства штамповок, соответствующий 2-ой группе серийности.
Масса штамповки , кг | Объем производства, тыс. шт. |
Не более 0,25 | 15…5000 |
0,25…0,63 | 8…300 |
0,63…1,6 | 5…150 |
1,6…2,5 | 4,5…120 |
2,5…4 | 4…100 |
4…10 | 3,5…75 |
10…25 | 3…50 |
25…63 | 2…30 |
63…160 | 0,6…1 |
Коэффициент kП определяется из условия: если объем производства заготовок (годовая программа) больше значений, указанных в табл. 2.13, принимают kП = 0,8, в остальных случаях – kП. Группа (степень) сложности определяется по прил. 2 ГОСТ 7505-74.
Экономический эффект для сопоставления способов получения заготовок, при которых технологический процесс механической обработки не меняется, может быть рассчитан по формуле:
где Sзаг1, Sзаг2 – стоимость сопоставляемых заготовок, руб.
Определение стоимости заготовки в курсовом проекте следует оформить в виде расчетного формуляра, образец которого приведен в прил. 8.6.
2.4 ПРЕДВАРИТЕЛЬНАЯ РАЗРАБОТКА И ВЫБОР ВАРИАНТА ТЕХНОЛОГИЧЕСКОГО МАРШРУТА ПО МИНИМУМУ ПРИВЕДЕННЫХ ЗАТРАТ
Прежде чем принять решение о методах и последовательности обработки отдельных поверхностей детали и составить технологический маршрут изготовления всей детали, необходимо произвести расчеты экономической эффективности отдельных вариантов и выбрать из них наиболее рациональный для данных условий производства Критерием оптимальности является минимум приведенных затрат на единицу продукции
При выборе варианта технологического маршрута приведенные затраты могут быть определены в виде удельных величин на 1 ч работы оборудования В качестве себестоимости рассматривается технологическая себестоимость, которая включает изменяющиеся по вариантам статьи затрат Часовые приведенные затраты можно определить по формуле:
где СЗ – основная и дополнительная зарплата с начислениями, руб/ч; СЧЗ – часовые затраты по эксплуатации рабочего места, руб/ч; ЕН – нормативный коэффициент экономической эффективности капитальных вложений (в машиностроении ЕН = 0,15); КС, КЗ – удельные часовые капитальные вложения соответственно в станок и здание, руб /ч.
Основная и дополнительная зарплата с начислениями и учетом многостаночного обслуживания рассчитывается по формуле:
где ε – коэффициент, учитывающий дополнительную зарплату, начисления на социальное страхование и приработок к основной зарплате в результате перевыполнения норм; ε = 1,53, Стф – часовая тарифная ставка станочника-сдельщика соответствующего разряда, руб/ч; k – коэффициент, учитывающий зарплату наладчика (если наладка станка, как, например, часто в серийном производстве, выполняется самим рабочим, то k = l, в условиях массового производства k = 1,1 – 1,15); y– коэффициент, учитывающий оплату рабочего при многостаночном обслуживании.
Количество станков, обслуживаемых одним рабочим, можно принимать следующим, универсальные станки (токарные, протяжные горизонтальные, сверлильные, фрезерные, строгальные, шлифовальные и др.) – 1; токарные многорезцовые полуавтоматы – 1...2; многошпиндельные автоматы – 2...3; одношпиндельные автоматы – 3 ...4; зуборезные полуавтоматы – 4...5.
Коэффициент у, учитывающий оплату рабочего при многостаночном обслуживании, можно принимать в зависимости от числа обслуживаемых станков: при числе обслуживаемых станков 1; 2; 3; 4; 5; 6; 7; коэффициент у соответственно равен 1; 0,65; 0,48; 0,39; 0,35; 0,32; 0,3.
Часовые затраты по эксплуатации рабочего места:
где – практические часовые затраты на базовом рабочем месте, руб/ч; kм – коэффициент, показывающий, во сколько раз затраты, связанные с работой данного станка, больше, чем аналогичные расходы у базового станка.
Для универсальных и специализированных станков массой до 10 т, а также агрегатных и специальных станков, не вошедших в прил. 2, значения им можно определить расчетным способом [4]:
а) для автоматов и полуавтоматов:
б) для резьбофрезерных, зубофрезерных и протяжных станков:
в) для остальных станков, работающих неабразпвным инструментом:
г) дли станков, работающих абразивным инструментом:
д) для агрегатных и специальных станков:
где Ц – балансовая стоимость станка, определяемая как сумма оптовой цены станка и затрат на транспортирование и его монтаж, составляющих 10 – 15 % оптовой цены станка, руб.; Ny–установленная мощность двигателей, кВт; Рм и Рэ – категория ремонтной сложности соответственно механической и электрической частей станка, И – часовые затраты на возмещение износа металлорежущего инструмента, руб.;
Для определения kМ используются следующие данные оптовые цены, установленные мощности, категории ремонтной сложности станков (приведены в таблицах технических характеристик металлорежущих станков), часовые затраты на возмещение износа металлорежущего инструмента.
Часовые затраты по эксплуатации рабочего места в случае пониженной загрузки станка (ηз < 60%) должны быть скорректированы с помощью коэф-фициента φ, если станок не может быть дозагружен, как, например, в массовом производстве, В этом случае скорректированные затраты в час:
где φ – поправочный коэффициент.
α – доля постоянных затрат в себестоимости часовых на рабочем месте, принимаемых по прил. 2, а при отсутствии табличных данных а ≈ 0,3 – 0,5; ηЗ – коэффициент загрузки станка.
Капитальные вложения в станок (руб. /ч):
Капитальные вложения в здание (руб. /ч):
где Ц – балансовая стоимость станка, руб.; F – производственная площадь, занимаемая станком с учетом проходов, м2;
F – площадь станка в плане, м2; kf – коэффициент, учитывающий дополнительную производственную площадь проходов, проездов и др;
РД – действительный годовой фонд времени работы станка, ч;
ηЗ– коэффициент загрузки станка (в серийном производстве рекомендуется принимать равным 0,8, в массовом – по фактической загрузке станка);
Значения коэффициента kf в зависимости от площади станка в плане принимаются: более 20 м2 – 1,5; свыше 10 до 20 м2 – 2; свыше 6 до 10 м2 – 2,5; свыше 4 да 6 м2 – 3, свыше 2 до 4м2 – 3,5; менее 2 м2 – 4.
Минимальная производственная площадь на один станок равна 6 м2 (если меньше 6 м2, его принимают равным 6).
Технологическая себестоимость операции механической обработки (руб. /ч)
где Tшт(ш к) – штучное или штучно-калькуляционное время на операцию, мин; kВ – коэффициент выполнения норм, обычно принимаемый равным 1,3.
Приведенная годовая экономия (экономический эффект на программу) (руб.)
где и
– технологическая себестоимость сравниваемых операций, руб.
Если, кроме стоимости механической обработки, в вариантах изготовления деталей изменяются и другие статьи затрат, как, например, расходы на специальную оснастку, материалы, заготовки, то эти изменения также следует учитывать при расчете экономического эффекта В этом случае общий экономический эффект (руб.)
где – экономия или перерасход по другим статьям (знак плюс –дополнительная экономия, знак минус – перерасход).
Для экономической оценки вариантов технологических маршрутов механической обработки по предлагаемой методике необходимо использовать следующие исходные данные оптовую цену станка, площадь станка в плане, коэффициент загрузки станка, категорию ремонтной сложности и установленную мощность электродвигателей станка, трудоемкость операции Тшт или Тш к, определяемую по укрупненным нормативам, годовую программу и тип производства, количество станков, обслуживаемых одним рабочим.
Глава 3. ВЫБОР МЕТАЛЛОРЕЖУЩИХ СТАНКОВ
_________________________________________________________________
Дата добавления: 2018-05-12; просмотров: 7783; Мы поможем в написании вашей работы! |
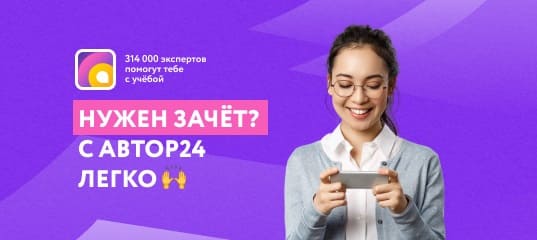
Мы поможем в написании ваших работ!