Тема 5. Точность при механической обработке
МИНИСТЕРСТВО ОБРАЗОВАНИЯ И НАУКИ
РОССИЙСКОЙ ФЕДЕРАЦИИ
Федеральное государственное автономное образовательное
Учреждение высшего образования
Севастопольский государственный университет
Кафедра технологии машиностроения
Основы технологии мащиностроения
Конспект лекций для студентов заочной формы обучения
Севастополь 2016
Технология мащиностроения
Тема 1. Производство изделий в машиностроении
- Виды изделий в машиностроении, основные этапы освоения производства изделий.
- Роль отечественных ученых в развитии технологии как науки.
- Понятия "производственный" и "технологический" процессы в машиностроении.
- Структура технологического процесса.
- Виды изделий в маниностроении, основные этапы освоения производства
изделий
Под изделием в машиностроении понимают любой конечный продукт данного конкретного предприятия.
Рис. 1.1. Виды изделий.
Это может быть полуфабрикат, заготовка, деталь, узел, агрегат, машина. Так например, Мелитопольский завод "Цветлит" выпускает заготовки для деталей силового агрегата, Мичуринский завод поршневых колец – поршневые кольца, подшипниковые заводы – подшипники заданной номенклатуры, Мелитопольский моторный завод – силовые агрегаты, Запорожский автомобильный завод – автомобили. К каждому изделию предьявляется целый комплекс технических требований. Часть из них отображается в соответствующих ГОСТах. Основная задача изделия – выполнять свое служебное назначение. Основные требования, предьявляемые к изделию: Высокое качество, удобство эксплуатации и ремонта, доступность материалов, возможность применения при изготовлении высокопроизводительных и эффективных методов и технологий. Качество изделий характеризуется целой гаммой параметров. Это совокупность свойств продукции, которые характеризуют ее пригодность удовлетворять определенные потребности общества. Основные группы показателей качества:
|
|
- Показатели качества, которые характеризуют полезность и эффективность использования продукции.
- Показатели надежности (безотказность, сохраняемость, ремонтнопригодность, долговечность).
- Показатели стандартизации и унификации, которые характеризуют степень использования стандартных и унифицированных элементов.
- Показатели технологичности.
- Экологические показатели, отражающие совокупность свойств изделие – среда – человек.
- Патентно–правовые показатели.
- Эстетические показатели.
- Экономические показатели.
Рассмотренные показатели качества обеспечиваются на всех этапах освоения производства изделия.
|
|
Основные этапы освоения производства изделия.
Освоение производства любого изделия является многоэтапным, многоуровневым процессом, основеые этапы которого рассмотрены на рис. 1.2.
Рис.1.2. Этапы освоения производства изделий.
На первом этапе изучают потребности общества и делают заключение о возможности производства изделия. При этом устанавливают: основные потребительские свойства изделия и их развитие во времени, объем выпуска и перспективы изменения потребностей общества в изделии, техническую возможность выпуска изделия с заданными потребительскими свойствами, выполняют предварительную экономическую оценку целесообразности производства изделия.
На втором этапе на основе анализа служебного назначения разрабатывают основные технические требования к изделию, составляют проект технического задания на производство изделия.
Этап проектирования изделия (третий этап, см. рис.1.1) включает в себя следующие подэтапы: научный, конструкторский, технологический и организационный. При выполнении научного этапа формируют цели и техническую стратегию с учетом перспективного развития, анализируют возможность использования новых научных открытий и изобретений, выдвигают гипотезы и проводят их опробацию, принимают принципиальные решения. При выполнении конструкторского подэтапа последовательно разрабатывают техническое задание, технические предложения, эскизный проект, технический проект, рабочую документацию. При выполнении технологической части проекта изделие отрабатывают на технологичность, вся конструкторская документация обязательно проверяется и подписывается технологом.
|
|
Четвертый этап, этап проектирования технологических процессов, является одним из наиболее отвественных. Он в значительной мере определяет качество изготавливаемого изделия, себестоимость и трудоемкость его производства, конкурентноспособность. Если вклад первых трех этапов в себестоимость изделия для массового производства, как правило, не превышает 1-2%, то за счет совершенствования технологии можно добиться снижения себестоимости на 10-20%. Так, например, применяя более совершенную технологию, нам удалось снизить себестоимость изготовления клапана автомобиля на 10 копеек. При программе производства автомобилей 800 тысяч в год для четырехцилиндрового двигателя экономия составит 640 тысяч гривен. Технологические процессы определяют структуру машиностроительного предприятия, состав оборудования, конструкцию технологической оснастки. Проектирование, строительство предприятия, изготовление оборудования, как правило, выполняются специализированными предприятиями. Этап эксплуатации изделия сопровождается конструкторами и технологами завода изготовителя. Предприятие разрабатывает технические требования к эксплуатации изделия, технологические процессы технического обслуживания и ремонта изделия, технологию его утилизации.
|
|
1.2. Роль отечественных ученых в развитии технологии как науки
Основоположником технологии машиностроения как науки принято считать Тиме. В 1885 году он издал первый капитальный труд по технологии машиностроения - «Основы машиностроения, организация машиностроительных фабрик в техническом и экономическом отношениях и производство в них работ». Наиболее крупный вклад в развитие технологии вложили Соколовский А.П., Балакшин Б.С., Кован В.В. и другие.
Профессор Соколовский А.П. предложил идею типизации технологических процессов. Он показал, что 80% деталй машин заданного класса имеют сходную конфигурацию и одинаковые служебные назначения, а следовательно технологические процессы их обработки должны быть подобными. Для каждого класса изделий может быть разработан образцовый технологический процесс, который принято называть типовым.
Профессор Балакшин Б.С.разработал теорию размеры цепей и обосновал методы обеспечения точности при сборке и механической обработке.
Профессор Кован В.В. предложил методику аналитического расчёта припусков при механической обработке. Из отечественных ученых, работающих в области машмностроения, можно отметить работы Якимова А.В., Линчевского П.А., Грабченко А.И.
Якимов А.В. обосновал методы обеспечения качества поверхностей деталей при механической обработки.
Линчевский П.А. предложил методику оптимизации технологических процессов. В последние годы Якимовым А.В. и Линчевским П.А. опубликовано два учебника по технологии машинолстроения.
1.3. Понятия "производственный" и "технологический" процессы в машиностроении
Производственный процесс – совокупность всех процессов данного конкретного предприятия (получение сырья, его хранение, переработка, храниение готовой продукции, её реализация, содержание зданий-сооружений, энергетическое и кадровое обеспечение, финансовая деятельность).
Технологический процесс – это часть производственного процесса, содержащая действия по изменению и последующему определению состояния предмета производства. При механической обработке изменяются форма, размеры поверхностей, при термической обработке – физико-механическое состояние материала. Контрольные операции (измерение размера поверхностей, измерение твердости, испытание изделия на стенде и т. д.) включаются в состав технологического процесса, хотя и не изменяют состояние предмета производства. Они необходимы для оценки изменения состояния предмета производства.
Технологические процессы могут быть непрерывными и дискретными. Примеры неперывных процессов: производство чугунва, стали, химическое производство (например переработка нефти).
Непрерывное производство, по сравнению с дискретным, имеет ряд преимуществ:
· более высокая производительность;
· более простое оборудование;
· облегчаются процессы организации производства.
1.4. Структура технологического процесса
Для машиностроения характерно дискретное производство, когда весь технологический процесс разбивается на ряд этапов, называемых операциями. Операция - это часть технологического процесса, выполняемая на одном рабочем месте. На операцию назначаются норма времени, норма выработки и другие материальные и трудовые затраты. Для проектирования и выполнения операции она делится на ряд составных элементов (установка – позиция – переход – проход).
Установка – часть технологической операции, выполняемая при одном закреплении заготовки.
Позиция – часть операции, характеризующаяся неизменностью положения заготовки вместе с приспособлением относительно неподвижной части станка или инструмента.
Переход – часть операции, характеризующаяся неизменностью обрабатываемой поверхности, инструмента и режима резания.
Рассмотрим два варианта обработки заготовки на токарных станках, рис. 1.3.
Рис. 1.3. Схема установки заготовки на токарном станке:
1 - передняя бабка; 2 - центр; 3 - поводковое устройство; 4 - задняя бабка;
А, В, С – обрабатываемые поверхности.
Вариант 1.
На станке обрабатываются поверхности С и В, затем деталь снимается со станка, переворачивается, закрепляется на этом же станке и обрабатывается поверхность А.
Вариант 2.
Поверхность А обрабатывается на 2-м станке.
Для варианта 1 имеем одну операцию, две установки, при первой установке выполняется два перехода. Во втором варианте - две операции, в каждой из них по одной установке. При выполнении первой операции – два перехода, при выполнении второй операции – один переход.
Проход – одно относительное перемещение инструмента по обрабатываемой поверхности.
Тема 2. Типы, виды производств
- Характеристика типов производств.
- Такт выпуска и его определение.
- Формы организации работ на машиностроительных предприятиях.
2.1. Характеристика типов производств
Все многообразие машиностроительных производств можно классифицировать не только по виду выпускаемых изделий, но и по обьёму выпуска этих изделий
В машиностроении различаются следующие виды производств:
-единичное;
-серийное;
-массовое.
Тип производства рекомендуется определять по коэффициенту закрепления операций, который вычисляется по зависимости
K30= , (2.1)
где K30 - коэффициент закрепления операции;
Qi - число операций, закрепленных за i-м рабочим местом;
Pj - число рабочих мест j-вида.
Например, имеется два токарных станка и один фрезерный станок. На токарных станках выполняется шесь операций, на фрезеном – четыре. Коэффициент закрепления операций вычислится
K30= (6+4)/2=5.
Если K30 меньше или равен 1, то производство считается массовым, если больше 1 до 10 – крупносерийным, от 10 до 20 – среднесерийным, от 20 до 40 – мелкосерийным, более 40 – единичным. Предварительно тип производства может быть определен по таблице 2.1.
Таблица 2.1. Выбор типа производства
Тип производства | Количество деталей, выпускаемых в год | ||
крупных | средних | мелких | |
единичное | До 5 | До 10 | До 100 |
серийное | 5…1000 | 10…5000 | 100…50000 |
массовое | > 1000 | >5000 | >50000 |
Дадим краткую характеристику каждому из типов производств.
К единичному относятся такие производства, в которых изделия изготавливаются единицами и, как правило, не повторяются в течение длительного промежутка времени (например, предприятия по изготовлению тяжелых машин, опытные производства, мастерские, заводы по производству нестандартного оборудования).
Технологический процесс в единичном производстве подробно не разрабатывается, трудоёмкость изготавления деталей определяется по укрупненным нормативам. Оборудование применяется универсальное, состав оборудования подбирается таким образом, чтобы обеспечить определенную пропускную способность данного предприятия.
Квалификация рабочих – высокая, 5-6 разряд. Себестоимость продукции очень высокая. Например, легковой автомобиль массового производства стоит сегодня 20-30 тыс. евро, автомобиль по индивидуальному заказу – 1 млн. евро.
Серийное производство – такое производство, в котором изделие выпускается сериями, а детали партиями. Партия равна серии, если на одно изделие устанавливается одна деталь. Число деталей в партии рекомендуется определять по зависимости
n= , (2.2)
где n – число деталей в партии;
N – программа выпуска деталей;
a – число дней, на которое необходимо необходимо иметь запас деталей для сборки изделия;
Fg – годовой фонд работы оборудования в днях.
Считается что до 80% современных предприятий могут быть отнесены к предприятиям серийного производства. Технологический процесс в серийном производстве подробно разрабатывается только для наиболее сложных деталей, на простые детали ограничиваются составлением маршрутной технологии.
Состав оборудования, устанавливаемого на предприятиях серийного производства, зависит от программы выпуска изделий. В мелкосерийном производстве применяют универсальные станки и станки с ЧПУ; в среднесерийном – станки с ЧПУ, автоматы и полуавтоматы, гибкие производственные системы, в крупносерийном – автоматические системы с микропроцессорным управлением. Оснастка, мерительные, режущие инструменты применяют как специальные, так и универсальные. Разряд рабочих ниже, чем в единичном производстве.
Массовое производство.
К массовым производствам относятся такие, в которых изделия изготавливаются в массовых количествах по неизменным чертежам в течение длительного промежутка времени. Технологический процесс разработаывается подробно на все детали. Оборудование устанавливается по ходу технологического процесса. Как правило, применяется специализированное оборудование (станки автоматы, автоматические линии). Разряд рабочих – низкий (2,3 разряд). Себестоимость продукции – низкая.
2.2. Такт выпуска и его определение
Такт выпуска – промежуток времени между выпуском 2-х последовательных изделий (конвейер по сборке автомобилей). Он определяется по зависимости
tв = , (2.3)
где F – действительный годовой фонд времени работы оборудования при работе в одну смену в часах;
m – количество смен;
N – программа выпуска изделия в год.
2.3. Формы организации работ на машиностроительных предприятиях
Различают 5 форм организации работ на машиностроительном предприятии:
- Поточно-массовая;
- Прямоточная;
- Поточно-серийная;
- Предметная;
- По видам оборудования.
При поточно-массовом производстве оборудование устанавливается по ходу технического процесса, детали передаются со станка на станок, образуя непрерывный поток. Время выполнения каждой операции согласовывается с тактом выпуска изделия.
Так, например, при такте выпуска изделий tв = 2 минут время выполнения операций T может быть примерно равно 2-м, 4-м, 6-ти минутам.
В прямоточном производстве, в отличие от поточного, время согласовывается с тактом выпуска не на всех операциях. На отдельных операциях оно может быть больше или меньше такта. Производство менее ритмично Оборудование операций, на которых
T<tв работает с перегрузкой, а у которых T>tв частично простаивает.
Поточно-серийная форма отличается от поточно-массовой тем, что оборудование (станки, автоматические линии) перестраивается время от времени на выпуск новых изделий. При предметной форме организации детали передаются от станка к станку партиями. При пятой форме организации производства создаются участки токарных, фрезерных, шлифовальных станков. Деталь после обработки на одном из участков передаётся либо на другой участок, либо на промежуточный склад.
Тема 3. Основы технического нормирования
1. Задачи технического нормирования, его роль в производстве.
2. Техническая норма времени, штучное-калькуляционное время.
3. Штучное время и его структура.
4. Методы нормирования технологических операций.
Задачи технического нормирования, его роль в производстве.
Целью технического нормирования является установление нормы времени на обработку детали (сборку изделия) или нормы выработки. Для современного производства техническое нормирование имеет большое значение:
- Благодоря техническому нормированию можно более рационально распределить ресурсы и более рационально использовать производственные мощности.
- Осуществить оптимальную загрузку оборудования.
- Обнаружить узкие места в производстве и во время их ликвидировать.
Разработка технологического процесса также непосредственно связана с техническим нормированием. С помощью технтческого нормирования оценивается производительность каждого из возможных вриантов технологических процессов. Ьлагодаря этому становится возможным выбрать вариант, который будет оптимальным для данного, конкретного производства.
Техническая норма времени непосредственно определяет расценки, необходимое для выполнения данной операции количество оборудования, себестоимость обработки деталей и сборки изделия. Расценка на выполнение операции определяется по зависимости
, (3.1)
где К – тарифный коэффициент;
З – заработная плата рабочего первого разряда гривен в час;
t – время на выполнение операции.
Пример: t=2 минуты; заработная плата рабочего первого разряда з=1,4 гривен в час (1,4/60 гривен в минуту); тарифный коэффициент для рабочего 4-го разряда к=1,5
Р=1,5*1,4/60*2=0,07 гривен при обработке одной детали.
Число сианков q, необходимых для выполнения операции, вычисляется
, (3.2)
где Fд – действительный фонд времени работы оборудования в часах при работе в одну смену.
Время на обработку детали непосредственно влияет на себестоимость ее изготовления. Себестоимость вычисляется
, (3.3)
где М – расходы на материалы;
З – заработная плата основных рабочих;
Н – накладные расходы.
Накладные расходы берутся в % от заработной платы, а заработная плата на обработку детали вычисляется как сумма расценок на выполнение каждой операции.
Техническая норма времени, штучно-калькуляционное время.
Технической нормой времени в машиностроениипринято называть время, необходимое для выполнения данного объема работы. Техническая норма времени назначается на операцию. Следовательно, операция является основным объектом нормирования.
Нормой выработки называется объем работы, который должен выполнить рабочий за определенный промежуток времени (смену, час).
Норма времени на операцию называется штучнокалькуляционным временем. Оно определяется по зависимости
, (3.4)
где Тп.з – подготовительно-заключительное время;
n – число деталей в партии;
tшт – штучное время.
Подготовительно-заключительное время тратится один раз наобработкувсей партии деталей, В него входит время, необходимое для получения задания, ознакомления с чертежом, технологическим процессом, получения оснастки, режущего инструмента, настройку станка, уборку станка после обработки партии, сдачу оснастки и технологической документации. Подготовительно-заключительное время свойственно серийному производству. В массовом производстве нет партий, а следовательно Тп.з равно нулю и штучнокалькуляционное время равно штучному.
Штучное время определяется по зависимости
,
(3.5)
где tо – основное время;
tв – вспомогательное время;
tорг.тех.об – время на организационное и техническое обслуживание рабочего места;
te – естественное время (время на отдых).
Основное время непосредственно связано с изменением формы и размеров обрабатываемой детали или взаимного расположения деталей при сборке. Оно может быть машинным, когда работа выполняется без непосредственного участия рабочего; ашино- ручным, когта работа выполняется станком при непосредственном участии рабочего; ручным (слесарные работы, сборка).
Вспомогательное время – это время, затраченное на различные рабочие приемы, необходимые для выполнения основной работы. Эти приемы повторяются либо с каждой новой деталью, либо с их группой. Вспомогательное время необходимо:
а) на установку детали на станок и ее снятие;
б) на управление станком;
в) на выполнение промеров заготовок и деталей.
Вспомогательное время зависит от размеров, конфигурации и веса обрабатываемой детали, от конструкции приспособления исамого станка, принятых методов управления станком, от требований к точности и шероховатости обрабатываемых поверхностей, конструкции мерительного тнструмента и ряда других факторов. Вспомогательное время, как правило, определяется по нормативным данным.
Сумму основного и вспомогательно времен принято называть временем оперативным
. (3.6)
Время на организационное и техническое обслуживание разделяется на время технического обслуживания рабочего места, которое необходимо на смену режущего инструмента и настройку станка и время на организационное обслуживание, которое необходимо на раскладку инструмента, приведение станка в порядок после смены. Время на техническое обслуживание берется в процентах от основного, время на организационное обслуживания – в процентах от оперативного, время на естественные надобности – в процентах от оперативного:
; (3.7)
; (3.8)
. (3.9)
3.3. Методы нормирования технологических операций
Одним из свойств нормы времени является ее конкретность, т.е. она задается для данных конкретных производственных условий. В других условиях детель может быть обработана по другому технологическому процессу, нормы времени на однотипные операции будут иными. Точность нормы должна быть тем выше, чем больше программа выпуска изделий. Для определения нормы времени применяется два метода:
а) расчетно-аналитический;
б) опытно-статистический (исследовательский).
Более эффективным является расчетно-аналитический метод. При его использовании на основе выбранных режимов резания и размерам обрабатываемой поверхности вычисляется основное время. Так для токарной обработки, рис. 3, основное время вычисляется
![]() |
Рис. 3.1. Схема токарной операции для расчета основного времени.
L – длина обрабатываемой поверхности; L2= Lвр. – путь врезания; L1=Lпер. – путь перебега.
to=(L+ Lвр. + Lпер.)/ns,
где n – частота вращения заготовки, об/мин;
s – продольная подача, мм/об.
При сверлении, рис.3.2, основное время определяется
Рис.3.2. Схема операции сверления для расчета основного времени.
Вспомогательное время определяется для каждого приема или группы приемов по нормативам. Применение расчетно-аналитического метода позволяет проводить техническое нормирование на стадии проектирования технологического процесса.
При применении опытно-статистического метода норма времени устанавливается непосредственно в цехе на основе хронометража. При этом часто выявляются и наиболее рациональные режимы выполнения операций.
Тема 4. Базирование деталей при механической обработке
1. Основы базирования.
2. Определимость базирования. Необходимость силового замыкания.
3. Конструкторские и технологические базы.
4. Выбор баз при проектировании технологических процессов.
5. Структура технологических баз.
6. Расчёт погрешности базирования.
4.1.Основы базирования.
Для обеспечения заданной точности при обработке необходимо придать заготовке вполне определенное расположение относительно исполнителтных механизмов станка и режущего инструмента. Эта процедура называтется БАЗИРОВАНИЕМ. Каждое твердое тело, как известно из механики, 6 степеней свободы, три поступательных и три вращательных. Для того чтобы соорентировать тело в пространстве достаточно определнным образом задать 6 координат. Для этого у детали должно быть не менее трех поверхностей. Рассмотрим пример базирования параллепипеда, рис.4.1.
Рис. 4.1. Схема базирования параллепипеда.
На нижней плоскости (установочная плоскость) выделяем 3 точки – точки 1,2,3 и для каждой точки зададим координаты Z1, Z2, Z3. При этом тело лишается одного поступательного (по оси Z) и двух вращательных ( ось X и осьY) степеней свободы. ( по x – вращается, и постоянно по Z).
Выделим еще две точки на боковой поверхности (направляющая плоскость) - точки 4 и 5 и зададим координаты X4, X5. Тело лишается еще двух степеней свободы – врашательной по оси Z и поступательной – по оси X.
Шестую точку выберем на самой маленькой торцовой поверхпости (упорная плоскость) и зададим для нее координату Y6, тем самым мы лишим тело последней шестой степени свободы. Оно не может поступательно перемещаться и по координате Y.
На рис. 4.2 рассмотрена схема задания шести координат для детали типа цилиндра.
Рис. 4.2. Схема базирования цилиндрической заготовки.
4.2. Определимость базирования. Необходимость силового замыкания.
Определимость базированного заключается в том, что для каждой заготовки в зависимости от её формы может быть предложена наиболее рациональная схема базирования, при которой заготовка лишается всех 6 степеней свободы и обеспечивается при обработке выполнение всех технологических требований предусмотренных чертежом детали. При этом дополнительных баз назначать не следует. С целью повышения жесткости системы можно применять дополнительные, подводимые опоры. Так при обработке длинных валов с целью снижения прогиба вала применяют люнеты.
Для того, чтобы заготовка сохранению своё положение во время обработки при установке детали на станок необходимо приложить силы, прижимающее заготовку к опорам, или иначе говоря создать силовое замыкание. При создании силового замыкания
необходимо руководствовать 2 положениями:
Силы, создающие силовое замыкание, прикладываются раньше сил резания.
Силы и момент этих сил должны быть больше сил и моментов, возникающих при резании.
При создании силового замыкания могут использоваться: силы собственного веса, силы трения, упругие силы элементов зажимного приспособления, электромагнитные, гидравлические, пневматические силы, различная комбинация перечисленных сил.
4.3. Конструкторские и технологические базы
Совокупность поверхностей, линий и точек, от кеоторых конструктор проставляет размеры, называется КОНСТРУКТОРСКИМИ БАЗАМИ.
Рис. 4.3. Конструкторские базы.
Для примера, рассмотренного на рис. 4.3, конструктор проставил размеры L1 и L2 от поверхности 1, следовательно, поверхность 1 и будет являться конструкторской базой. Для поверхностей 4 и 5 такой конструкторской базой является ось детали. При проектировании технологических процессов технолог не всегда может использовать конструторские базы. Например, при обработке заготовки детали, представленной на рис. 6, при первой установке нет поверхности 1, она закрыта слоем припуска. Совокупность поверхностей, линий, точек, которая используется в качестве баз при проектировании технологического процесса и обработке называется ТЕХНОЛОГИЧЕСКИМИ БАЗАМИ.
Конструкционные и технические базы могут совпадать, а могут и не совпадать.
Структура технологических баз
Рис. 4.4. Структура технологических баз.
К измерительным базам относятся такие поверхности, от которых отсчитывается размер при механической обработке. С помощью проверочных баз производится выверка расположений детали относительно стола станка или приспособления.
Опорные базы бывают основными и оперативными. Основные - такие поверхности, которые связаны с обрабатываемыми основными размерами.
Оперативные базы бывают естественными и искусственными. Естественные базы – это неоконченно обработанные поверхности. Искусственные базы – это поверхности, которые создаются специально для обработки детали. Классическим примером искусственных баз являются центровые отверстия, которые применяются при обработке деталей типа валов, рис. 4.5.
,
|
3 – центр.
Рис.4.5. Базирование детали с примением центрового отверстия
4.5. Выбор баз при проектировании технологических процессов.
При проектировании технологического процесса выбору технологических баз уделяется большое внимание, поскольку от этого в значительной степени зависит точность обработки.
Для приведеной на рис. 9 а) схемы поверхность 1 является двойной направляющей ( ось вращения детали в пределах погрешности закрепления совпадает с осью поверхности). Согласно принятым обозначениям, зажимным самоцентрирующим трехкулачковым патроном заготовка лишается по этой поверхности четырех степеней свободы. Своей торцевой поверхностью заготовка опирается только на один кулачек, тело лишается пятой степени свободы. Шестая база условно называется скрытой и реализуется за счет трения заготовки о кулачки. Для схемы б) заготовка опирается торцем 1 трех кулачнов и лищается трех степеней свободы, по поверхности 2 заготовка лишается двух степеней свободы.
а) б)
Рис.4.6. Схема базирования деталей при токарной обработке.
Для варианта базирования а) можно готовить об обеспечении высокой точности взаимного расположения повенрхностей 2 и 3 по отношению к поверхности 1 и возможности обеспечения перпендикулярности поверхностей 3 и 4 к оси поверхности 1. Для данной установки невозможно обеспечить высокую точность взаимного расположения поверхностей 3 и 4 к поверхности 5. При варианте б) наоборот обеспечивается высокая точность взаимного расположения поверхностей 2, 3, 5 относительно поверхности 1 и не обеспечивается соосность поверхности 5 относительно поверхности 4.
При проектировании технологического процесса в первую очередь выбирают черновые базы.
Рекомендации по выбору черновых баз.
- за черновую базу необходимо использовать поверхности, имеющие достаточные размеры без значительных отклонений формы.
- Если у детали имеются необработанные поверхности, то они часто принимаются за
черновые базы. За счёт этого обеспечивается их правильное расположение относительно обработанных поверхностей.
Например, при обработке поршня внутренняя поверхность не обрабатывается, она и принимается за черновую базу, при этом обеспечивается равномерностью толщины стенки поршня.
- Если у детали имеется ответственная поверхность, с которой желательно снять равномерный и минимальный припуск, то она и принимается за черновую базу, например направляющие станины станка.
Рис. 4.7. Выбор черновой базы.
Если для детали, рис. 4.7, более ответственной является поверхность 1 то она и будет принята за черновую базу.
Черновую базу используют один раз. После выбора черновой базы назначают базы для выполнения других технологических операций.
При выборе основных и оперативных баз возможны следующие варианты:
1) Одработка нескольких поверхностей выполняется за одну установку. В этом случае погрешность базирования и закрепления заготовки не будут оказывать влияния на точность взаимного расположения поверхностей. Она будет определяться в основном точностью станка, приспособления и инструмента.
2) Обработка ведется с использованием ранее обработанной поверхности в качестве базы. Например, при обработке втулки, когда обрабатывают наружную поверхность, за базу принимают внутренную поверхность, затем обрабатывают внутренную - за базу принимают наружную. В этом случае погрешности базирования не учитывается. На точность взаимного расположения поверхностей будет оказывать влияние погрешность закрепления заготовки.
3) Несколько поверхностей обрабатывают последовательно на разных установках, но от одной базы. Погрешности базирования не учитываются, погрешности закрпления будут суммироваться столько раз, сколько у нас установок.
4) Различные поверхности обрабатываются на различных установках с изменением баз. На точность взаимного расположения поверхностей будут оказывать влияние, как погрешность базирования, так и погрешность закрепления. Точность будет наименьшей.
Из анализа рассмотренных вариантов следует принцип постоянмтва баз. Без серьезных оснований базы в ходе технологического процесса менять не следует. Целесообразно на первых операциях обрабатать поверхности, которые будут использоваться в качестве базирующих, аостальные поверхности обрабатывать от этих поверхностей.
На рис. 4.8 приводится пример базирования корпусной призматической детали.
|

При обработке производят черновое и чистовое фрезерование поверхности 1 и сверление и развертывание двух отверстий небольшого диаметра 2. Затем поверхность 1 и отверстия 2 используются в качестве баз при обрабоке всех других поверхностей, например поверхностей 3 и 4.
4.6. Расчет погрешности базирования
Для того чтобы обосновать точность при механической обработке и выбрать более рациональный вариант базирования выполняется расчет погрешности базирования. Погрешность базирования определяется величиной колебания расстояний измерительной базы от режущей кромки установленного на размер инструмента. Так при установке втулки на оправку с зазором, рис. 4.9 , погрешность базирования вычисляется
|
Рис. 4.9. Погрешность базирования при установке втулки на оправку с зазором: 1 – оправка; 2 – обрабатываемая втулка.
|
где Dmax – максимальный диаметр отверстия втулки;
dmin – минимальный диаметр оправки.
Тема 5. Точность при механической обработке
- Понятие о точности.
- Виды погрешностей, возникающих при механической обработке.
- Погрешность установки заготовки. Влияние на точность точности станка, приспособления и инструмента.
- Погрешность настройки станка и инструмента.
5. Динамические погрешности, возникающие при механической обработке.
- Понятие о точности
Точность является одной из основных характеристик современного машиностроения. В общем случае о точности можно говорить как о соответствии некоторой реальной детали идеальной, заданной конструкции. Деталь считается годной, если все отклонения находятся в пределах допуска. Допуск это тот предел, или интервал, в котором отклонения реальной детали от идеальной являются допустимыми.
Точность включает в себя, рис 5.1:
- Точность размеров отдельных участков и поверхностей.
- Точность взаимного расположения поверхностей.
- Точность формы.
Точность размеров Точность формы Точность взаимного расположения
а) б) в)
Рис. 5.1. Точность размеров а), точность формы б) и точность взаимного расположения поверхностей в).
Допуски и посадки размеров определяются по стандартам ДСТУ ISO. В таблице 5.1 приводятся данные по влиянию на допуск квалитета и размера детали.
Таблица 5.1. Влияние на допуски квалитета и размера поверхности.
Квалитет | Размер, мм | Допуск, мкм | Степень точности формы | Размер, мм | Допуск формы, мкм |
14 | 50 100 | 620 870 | 12 | 30 50 | 100 120 |
10 | 50 100 | 100 140 | 10 | 30 50 | 40 50 |
8 | 50 100 | 39 57 | 8 | 30 50 | 16 20 |
5.2. Виды погрешностей, возникающих при механической обработке.
При анализе технлогических операций говорят о погрешностиях, возникающих при механической обработке. Такие погрешности могут зависеть от каждого из факторов, участвующих в процессе изготовления детали. При выполнении технологической операции допуск T должен быть меньше суммы погрешностей Q.
T> (5.1)
Вес погрешности, возникающие при механической обработке можно разбить на две группы:
- статические погрешности;
- динамические погрешности.
Кроме того погрешности могут быть закономерными и случайными.
К статическим погрешностям, которые наиболее значительно виляют на точность при механической обработке относятся:
- Точность станка.
- Точность приспособления.
- Точность инструмента.
- Точность настройки станка и инструмента.
- Погрешности базирования и закрепления заготовки.
- Погрешности измерений.
1. Погрешность установки заготовки. Влияние на точность
точности станка, приспособления и инструмента
Погрешность установки заготовки
Погрешность установки заготовки на станке, в приспособлении определяется векторной суммой погрешностей базирования и закрепления εз.
. (5.2)
Если направление погрешностей неизвестно, то вычисления ведут по зависимости
. (5.3)
Погрешность базирования опеределяется по геометрическим соотношениям, которые приводятся в справочной литературе. Погрешность закрепления возникает вследствии смещения заготовки под действием сил, создающих силовое замыкание. Смещения связаны с упругими деформациями заготовки и элементов приспособления. Погрешность закрепления, как правило, определяется экспериментально.
Точность станков
Станки бывают нормальной, повышенной, высокой, особо-высокой точности и мастер-станки. Точность станков обычно определяется в ненагруженном состоянии, либо при медленном перемещении узлов станка. Нормы точности станков определяются соответствующими стандартами. Наиболее важные параметры: прямолинейность направляющих, плоскостность направляющих, биение шпинделя и т. д. Так, например, для токарных станков нормальной точности биение шпинделя не должно превышать 0,01…0,15 мм, для шлифовальных станков – 0,005 мм.
Точность приспособления
Точность приспособления оказывает непосредственное влияние на точность изготовления детали. Например, при сверлении отверстий с направлением сверл кондукторными втулками точность межцентрового расстояния напрямую зависит от точности изготовления кондукторной плиты и втулок. Допуск на изготовление приспособления выбирается в два - четыре раза меньше допуска на обрабатываемую деталь.
Точность режущего инструмента
Точность обработки непосредственно связана с точностью изготовления режущего инструмента в двух случаях:
- При обработке инструментом, размер которого непосредственно определяет размер обрабатываемой повершности (сверло, зинкер, развертка, протяжка).
- При обработке детали фасонным инструментом.
5.4. Погрешности настройки станка и инструмента на заданный
размер
В зависимости от типа протзводства существуют два метода насмтройки:
1) В единичном производстве настройка станка на требуемый размер производится непосредственно рабочим методом пробных проходов.
2) В серийном и массовом производствах используется метод автоматического получения размеров. Станки и инструменты настраиваются наладчиком. Настройка производится либо при пробной обработке нескольких деталей, либо по эталонной детали. Чтобы не повредить режущую кромку инструмента и повысить точность, между инструментом и эталонной деталью устанавливается щуп. При этом эталон детали делается меньше на величину щупа.
При обработке заготовок на автоматических станках, автоматических линиях и станках с ЧПУ настройку инструмента на требуемый размер выполняют вне станка на специальном приспособлении, рис. 5.2.
Рис. 5.2. Схема настройки инструмента на размер вне станка.
Динамические погрешности при механической обработке
Динамические погрешности появляются под действием сил и температур, возникающих при резании. Основными факторами, определяющими появление таких погрешностей, являются: упругие и температурные деформации технологической системы, износ инструмента, деформации под воздействием остаточных напряжений, вибрации.
Влияние износа инструмента
При механической обработке снимается не только слой материала заготовки, но и изнашивается сам режущий инструмент. При износе меняется размер инструмента, увеличиваются силы резания. Износ резца в момент времени t принято определять по формуле
U= , мкм, (5.4)
Где Uo – удельный или относительный износ резца, мкм/м;
L – длина пути резания, м. L=V*t.
Величина относительного износа Uo определяется на основе экспериментальных данных. Так при точении стали резцом Т15К6 Uo= 8*10-3 мкм/м, при точении чугуна резцами ВК6 – 17*10-3 мкм/м. При скорости резания 100 м/мин и стойкости резца 60 минут износ резца соответственно составит 48 и 102 мкм, следовательно отклонение размера обрабатываемой поверхности за счет износа резца может превысить 0,1 мм, а при обработке поверхности вращения – 0,2 мм.
Тепловые деформации
При обработке материалов резанием выделяется большое количество тепла, под действием которого нагреваются станок, заготовка, инструмент, приспособление. Появляются температурные деформации, которые могут существенно влиять на точность. Если температура, например заготовки, изменяется на Δt градусов, то ее размер L определяется по зависимости
L=Lo (1+ Δt), (5.5)
Где Lo – исходный размер;
α – коэффициент линейного расширения, для стали α=0,12*10-4.
Если заготовка длиной 100 мм в процессе обработки нагреется всего на 10 градусов, то приращение ее размера составит12 мкм.
Основные пути снижения влияние температуры на точность при механической обработке:
- охлаждение детали в зоне резания;
- охлаждение самзки станка;
- разработка конструкций станков с учётом их тепловых деформаций;
- поддержание постоянной температуры в помещении.
Внутренне напряжение заготовок
Внутренние (остаточные) напряжения – это напряжения, которые существуют в заготовке (детале) без приложения внешних нагрузок. Так при литье остаточные напряжения вызываются неодновременным застыванием наружных и внутренних слоев и неодинаковой их усадкой. При механической обработке снимается самый напряженный наружный слой, вследствие этого детали деформируются, появляется их коробление.
С целью снижения погрешностей от внутренних напряжений производят искуственное или естественное старение заготовок до механической обработки, а также деталей в процессе изготовления, между черновой и чистовой обработкой.
При естественном старении детали выдерживается на складе или улице в течение нескольких дней. Искусственное старение производится в печах. Детали нагреваются до температуры 400-500о С и выдерживаются при такой температуре 8-12 часов, а затем охлаждаются вместе с печью, рекомендуемый темп охлаждения - 20 градусов в час. Мелкие детали обкатывают в специальных барабанах. Напряжения снимаются при соударении деталей.
Упругие деформации
Процесс обработки материалов резанием связан с появлением значительных сил. Так, например, осевая сила при сверлении отверстия диаметром 50 мм в стальной заготовке равна - 50 000 Н. При обработке на токарных станках сила резания может составлять нескольколько тысяч ньютонов. Под действием сил резания упруго деформируются станок, заготовка, приспособление, инструмент. Величина упругих деформаций зависит как от величины сил, так и от жесткости технологической системы и её составных элементов.
Жесткость – это способность системы оказывать сопротивление силам, стермящимся ее сдеформировать. Она вычисляется по соотношению
J= , (5.6)
Где Py – радиальная составляющая силы резания;
y – смещение в направлении дествия силы Py.
Жёсткость современных токарных станков составляет 20*103.... 40*103 Н/мм.
Величина обратная жесткости называется податливостью системы
ω=1/J = y/Py. (5.7)
Податливость технологической системы определяется как сумма податливости отдельных составляющих
, (5.8)
где ωп.б. – податливость передней бабки станка;
ωз.б. – податливость задней бабки станка;
ωс – податливость суппорта;
ωз – податливость заготовки;
ωи – податливость инструмента.
Погрешности возникающие вследствие нежесткости технологической системы могут быть учтены по зависимостям сопротивления материалов. Так при обработке в центрах, рис. 5.3, эквивалентная расчетная схема представляется в виде балки на двух опорах, рис. 16
Рис. 5.3. Схема к расчету упругих деформаций при обработке деталей в центрах.
Рис. 5.4. Эквивалентная схема к расчету упругих деформаций при обработке деталей в центрах.
Максимальный прогиб при обработке детали в центрах определится по зависимости
, (5.8)
где E – модуль упругости;
J – момент инерции.
Аналогично жёсткость может быть определена для детали, закрепленной в трехкулачковом патроне, рис. 5.5.
. (5.9)
![]() |



Дата добавления: 2018-05-12; просмотров: 532; Мы поможем в написании вашей работы! |
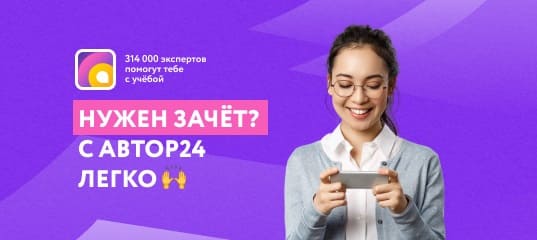
Мы поможем в написании ваших работ!