Особенности формирование и технологические
Требования к конструкции литых заготовок
Дня получения отливок при любом способе литья необходима литейная форма, которая определяет наружные и внутренние контуры отливок. Литейные формы изготавливают из различных материалов и в зависимости от свойств последних подразделяют на две группы: разовые и постоянные. Разовые формы используют для получения одной отливки, при извлечении которой форму разрушают. Дня изготовления разовых форм применяют песчано-глинистые, термореактивные и другие формовочные смеси. Разовые формы могут быть сухими и сырыми. По толщине стенок их подразделяют на толстостенные (толщина стенок25— 250 мм и более), тонкостенные и оболочковые (толщина стенок 5 —10 мм). К разовым формам относятся также неразъемные формы, используемые, в частности, при литье по выплавляемым моделям. Постоянные металлические формы широко используют в серийном и массовом производстве отливок, в основном из цветных металлов и сплавов. Материалом для этих форм могут быть чугун, сталь или алюминиевые сплавы. Постоянные формы применяют при специальных способах литья — кокильном, центробежном, под давлением и др.
При всех способах литья (за исключением литья по выплавляемым моделям) форма имеет один или несколько разъемов. При выборе литейной формы исходят из назначения, характера отливок и серийности их выпуска.
Конструкция литейной формы и материал, из которого она изготовлена, оказывают большое влияние на характер формирования отливок и на их качество. Материал формы должен обладать достаточной податливостью, хорошо противостоять статическому и динамическому воздействиям жидкого металла. Формирование основных свойств отливки (плотности, структуры, механических свойств, стабильности размеров и параметров шероховатости поверхности) обусловлено протеканием процессов взаимодействия металла отливки и формы в процессе заливки формы, затвердевания и охлаждения отливки.
|
|
Процесс затвердевания в значительной степени зависит от условий теплообмена между металлом и формой. Отличительная особенность разовых форм — их низкая по сравнению с металлом отливки теплоаккумулирующая способность. Процессы кристаллизации и охлаждения протекают в естественных условиях медленно, в результате чего структура отливок становится неравномерной; поэтому наиболее плотный и качественный металл с наилучшими механическими свойствами, расположен вблизи от поверхности отливки; в центральных слоях структура крупнозернистая, механические свойства пониженные. Повышенная скорость охлаждения способствует улучшению качества отливки, структура получается более мелкозернистой, что существенно повышает механические свойства отливки.
|
|
Охлаждение жидкого металла, его затвердевание, а также последующее охлаждение в твердом состоянии связаны с сокращением объема отливки. При кристаллизации по внешнему контуру в первую очередь образуется твердая корка. Затвердевший контур отливки можно рассматривать как сосуд, в котором заключена имеющая более высокую температуру жидкость. В процессе затвердевания и охлаждения объем жидкости и твердая корка сокращаются, но в разной степени. Результатом этой разницы является образование в отливке свободных от металла усадочных полостей. В процессе охлаждения из-за усадки происходит сокращение линейных размеров отливки, т. е. происходит линейная усадка, которая может вызвать появление в металле внутренних литейных напряжений, деформацию отливки и трещины.
После заливки металла в форму на границе их соприкосновения создается повышенное газовое давление, иногда достаточное для проталкивания газов в металл. Если форма газопроницаема, то часть газов через поры формы вытесняется в окружающую среду. Если же формаобладает низкой газопроницаемостью, то внутри отливки образуются газовые раковины и поры. Песчаные разовые формы - тела пористые, хорошо пропускают газ и воздух, металлическая форма практически не обладает газопроницаемостью, поэтому при ее использовании возможность получения отливок с повышенной газовой пористостью более вероятна.
|
|
Если материал детали, изготавливаемой литьем, обладает пониженными литейными свойствами, то для получения качественной заготовки более целесообразно использовать литье в разовые формы.
Технологичность отливки.
Под технологичностью отливки понимают выбор такой конструктивной формы и материала литой детали, которые способствуют получению качественной отливки с заданными физико-механическими свойствами, требуемой геометрией и минимальной трудоемкостью.
При определении себестоимости заготовки основной базой для расчета является ее масса. Снижение массы деталей, изготовленных из литых заготовок – одна из важнейших задач конструкторов. (проверка на технологичность). В себестоимость отливки входит размер брака. Конструкция литой детали должна обеспечивать направленное затвердевание отливки. Внешние контуры детали должны быть плавными, что снижает концентрацию остаточных напряжений в местах сопряжения прямоугольных участков, уменьшает торможение усадке при охлаждении формы. Надо стремиться к уменьшению габаритных размеров литой детали, особенно ее высоты, к устранению чрезмерно выступающих частей, тонкостенных ребер большой протяженности, глубоких впадин.
|
|
В целях уменьшения трудоемкости изготовления и сборки форм, снижения брака по перекосу и искажению конструкция литой детали должна обеспечивать минимальное количество разъемов модели, отсутствие отъемных частей, минимальное количество стержней.
Правило теней: освещают деталь параллельными лучами в направлении перпендикулярном к плоскости разъема формы, появление теневых участков свидетельствует о несовершенстве конструкции.
Рисунок 2.10 – Правило теней
Выбор толщины стенок.
Внешние контуры литой детали должны быть плавными, что снижает концентрацию остаточных напряжений в местах сопряжения прямоугольных участков, уменьшает торможение усадки при охлаждении формы.
Толщину стенок литых деталей определяют в зависимости от механических и технологических свойств сплава, конфигурации и габаритных размеров детали, способа ее получения. Правильно выбранная толщина стенок обеспечивает необходимые жесткость, герметичность и является одним из важнейших условий получения годных отливок с высоким коэффициентом использования металла. Чрезмерно толстые стенки увеличивают массу детали, вызывают появление усадочной рыхлости и пористости, снижают прочность изделий. Очень тонкие стенки при литье получить практически невозможно из-за большого брака по незаполнению формы, трещинам и прочим дефектам.
При конструировании литых деталей необходимо стремиться по возможности к одинаковой толщине стенок по всему сечению, избегать локального скопления металла, так называемых горячих мест или термических узлов. Термический узел - место локального скопления металла, которое дольше остается горячим, дольше затвердевает и где больше вероятность образования усадочных рыхлости и раковин.
Рис. 3.3. Исключение термического узла изменением
конструкции детали
Правильность конструкции в этом случае проверяют методом вписанных окружностей: окружность, вписанная в любое сечение отливки должна беспрепятственно выкатываться в сторону прибыли. Соотношение диаметров двух рядом лежащих окружностей 1,0 – 1,5.
Наименьшую толщину стенки литых деталей можно определить в зависимости от сплава по графикам.
Для деталей прямоугольной формы приведенный габаритный размер определяется по формуле:
N = (2L + B + H)/ 4,
Для стальных и чугунных литых деталей при N> 8, толщину стенок принимают 30-40 мм, для медных и алюминиевых сплавов с N< 0,1 – Smin = 4 мм(для безоловянных), 2,5 (для оловянных) 2мм (алюминиевых). Толщина стенок чугунных литых деталей, габаритные размеры которых меньше 0,5м может быть принята 0,5 – 2 мм; стальных – 4-5 мм. Учитывая более низкую жидкотекучесть высокопрочного и модифицированного чугунов, толщину стенок из них увеличивают на 15-20% по сравнению с серыми чугунами.Толщину внутренних стенок принимают: для чугунных и алюминиевых отливок на 10-20% меньше толщины наружних, для стальных – на 20-30%, для медных – на 15-20%. Толщину стенок из легированных сталей принимают на 20-30% меньше, чем из углеродистых. Толщину краев стенок крупногабаритных деталей рекомендуется увеличивать для выравнивания температуры по сечению при охлаждении и уменьшения остаточных напряжений.
Таблица Наименьшие толщины стенок отливок, получаемых литьем в песчано-глинистые формы
Материал | Размеры отливки | Наименьшая толщина стенки, мм |
Мелкие | 8 | |
Сталь | Средние | 12 |
Крупные | 20 | |
Чугун серый обычный и с шаровидным графитом | Мелкие (масса до 2 кг) | 3-4 |
Средние (масса до 50 кг) | 6-8 | |
Крупные (масса св. 50 кг) | 10-20 | |
Наибольшие размеры стенки, мм: | ||
50×50 | 2,5-3,5 | |
Чугун ковкий | 100×100 | 3,0-4,0 |
200×200 | 3,5-5,5 | |
350×350 | 4,0-5,5 | |
500×500 | 5,0-7,0 | |
Наибольшая длина стенки, мм: | ||
до 50 | 3 | |
Бронза оловянная | св. 50 до 100 | 5 |
» 100 » 250 | 6 | |
» 250 » 600 | 8 | |
Бронзы специальные | Мелкие | 6 |
и латуни | Средние | 8 |
Бронза кремнистая | — | 4 |
Алюминиевые сплавы | Мелкие при наибольшей длине стенки, мм, не более: 200 | 3-5 |
800 | 5-8 | |
Мелкие | 4 | |
Магниевые сплавы | Средние при длине стенки не более 400 мм | 6 |
Цинковые сплавы | — | 3 |
Прочность повышают не за счет увеличения толщины стенок, а придания стенкам коробчатого, V- образного или ребристого профиля, что упрощает литейную технологию и снижает себестоимость отливки.
Практикой литейного производства установлены следующие типы сопряжения стенок: угловое, тавровое, вилко-, V-, К-, Х-образное, крестообразное.
Дата добавления: 2018-05-12; просмотров: 343; Мы поможем в написании вашей работы! |
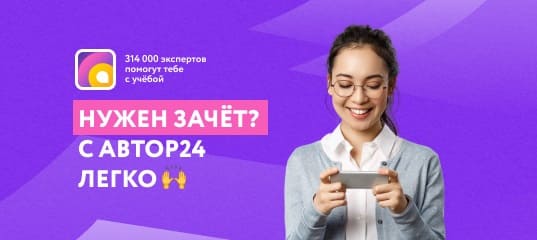
Мы поможем в написании ваших работ!