Термический крекинг нефти и её отдельных фракций
Процесс термического крекинга разработан в 1932 г. Ф.О. Райсом.
Исходное сырье: мазут, полугудрон, соляровое масло.
Условия процесса: температура – 470-550 оС, давление – 30-80 атм., время пиролиза – 2 сек.
Механизм – радикально-цепной.
В настоящее время термический крекинг используют для получения ограниченного числа продуктов: котельного топлива из гудрона, сырья для технического углерода, α-олефинов для производства моющих веществ.
Технологическая схема установки термического крекинга представлена на рис. 1.3.
Исходное сырье поступает в камерную печь 1, где нагревается до 430-470 оС. Образовавшаяся пароэмульсионная смесь идет в реактор крекинга 3, где пары в течении 2 сек выдерживаются при температуре 500 оС и давлении 80 атм. За это время протекают все реакции крекинга.
Образовавшиеся продукты проходят через редукционный вентиль 4, при помощи которого давление понижается до атмосферного. В результате понижения давления протекает конденсация продуктов с образованием жидкой и газовой фазы, которая разделяется в аппарате 5.
Газообразные продукты С1-С4, обогащенные этиленом, пропиленом, водородом, бутиленом, разделяются на индивидуальные соединения, которые используются в органическом синтезе для получения спиртов, растворителей, пластмасс, дивинила, ацетона, уксусной кислоты и других продуктов.
Жидкие продукты, пройдя через отделитель, из колонны 5 поступают на ректификацию в колонну 6, которая орошается мазутом. Низкомолекулярные продукты из колонны 6 идут на четкую ректификацию в колонну 7, орошаемую бензином; а тяжелые - в печь 1 для повторного крекинга.
|
|
В колонне 7 отбирается бензиновая фракция, которая конденсируется в холодильнике 8 и сливается в приемник 9. Часть фракции возвращают в процесс. В кубе колонны после крекинга
Рис. 1.1.4.1.1. Технологическая схема установки термического крекинга
остается фракция – соляровое масло, которая подается в печь 2, нагревается до 490-530 оС, смешивается с продуктами из печи 1 и направляется на термический крекинг.
Выход бензиновой фракции в расчете на исходное сырье составляет 35-40 %. Октановое число бензина равно 72-76. Для использования крекинг-бензина в качестве компонента автомобильного бензина необходима дополнительная стабилизация, для чего к бензину прибавляют 0.5 % березового или букового дегтя, обогащенного фенолами или синтетическими ингибиторами (неозон-Д).
Керосино-газойлевая фракция (200-350 оС) является ценным компонентом флотского мазута. После гидроочистки он может применяться также как компонент дизельных топлив.
Термогазойль – сырье для производства технического углерода.
|
|
Крекинг-остаток (фракция выше 350 оС) используется как котельное топливо. Он характеризуется более высокой теплотой сгорания и более низкой температурой застывания и вязкостью, чем прямогонный мазут.
Каталитический крекинг нефти и её отдельных фракций
Выход бензина термического крекинга высокий, но качество его низкое. Учитывая потребности современной техники, необходимо производство высокооктановых бензинов (95-98), не нуждающихся в стабилизации.
С этой целью проводят каталитический крекинг. Процесс разработан Н.Д. Зелинским, Локтевым, Лапидусом.
Исходное сырье: соляровое мало, керосин, тяжелые фракции бензина.
Условия процесса: температура 430-450 оС, давление 1.5-2.5 атм, алюмосиликатный катализатор.
Механизм – карбкатионный, цепной.
Первые катализаторы каталитического крекинга представляли собой природные глины – аморфные алюмосиликаты типа монтморрилонита (Al2O3∙ 4 SiO2∙H2O + nH2O). Эти катализаторы термически мало устойчивы. Выход бензина на них не превышает 20–30 масс. %.
В настоящее время природные алюмосиликаты практически полностью вытеснены синтетическими, также аморфными веществами. Средний состав катализатора: 10-30 % Al2O3, 90-70 % SiO2 и небольшое количество других окислов (Fe2O3, CaO и др.). Выход бензина с использованием синтетических катализаторов достигает 34-36 масс. %.
|
|
В последние годы в качестве катализатора широко используются природные и синтетические цеолиты, кристаллические алюмосиликаты аналогичного состава. Для повышения активности катализатора добавляют промоторы на основе редкоземельных металлов (лантан, ниобий, церий).
Использование цеолитсодержащих катализаторов позволяет увеличить выход бензина до 45-47 % без ухудшения других показателей процесса. Эти катализаторы более устойчивы к действию ядов и высокой температуры.
Технологическая схема установки термического крекинга представлена на рис. 1.4.
Керосин насосом 1 подается в камерную печь 2, где поддерживается температура 430-450 оС. Образовавшиеся в печи 2 пары керосина поступают в контактный аппарат 3, куда также подается катализатор, нагретый до 600 оС.
Все реакции крекинга протекают на поверхности катализатора, поэтому с течением времени поверхность катализатора покрывается тонкой пленкой сажистого углерода. Это уменьшает активность катализатора, поэтому продукты крекинга и катализатор направляют на разделение в циклон-аппарат 4. После отделения катализатор поступает в печь обжига 5, продуваемую снизу атмосферным воздухом, где при температуре 700-800 оС углеродная пленка выгорает. Продукты горения и катализатор разделяются в циклон аппарате 6. Регенерированный катализатор возвращается в процесс.
|
|
Газообразные продукты крекинга после циклон аппарата 4 проходят водяной холодильник 7, редуктор 8 и поступают в колонну конденсации 9. За счет резкого понижения давления и температуры образуется жидкая и газовая фазы. В газовой фазе преобладает этилен, пропилен, бутилен, водород, метан. Эти продукты разделяются и идут на производство спиртов, растворителей, дивинила, изопропена. Жидкие продукты поступают на глубокую ректификацию в колонну 10, орошаемую бензином, для лучшего отделения высококипящих фракций. Тяжелые фракции в колонне 10 отделяются и возвращаются в процесс, легкие - поступают на четкую ректификацию в колонну 11, которая орошается бензином. Пары бензина охлаждают в водяном
Рис. 1.1.4.2. Технологическая схема установки термического крекинга
холодильнике 12, где они конденсируются, и сливают в приемник 13. Часть бензина возвращается на орошение колонны 11.
Выход бензина каталитического крекинга может составлять 55 % от исходного сырья, его октановое число 80-98.
Основными преимуществами каталитического крекинга перед термическим является более высокая скорость реакции в присутствии катализатора и большая ценность получаемых продуктов.
Бензиновая фракция применяется как компонент автомобильного и авиационного бензина.
Легкий газойль используется как компонент дизельного топлива, как сырье для производства сажи, а также в качестве разбавителя при получении мазутов.
Тяжелый газойль – остаточный продукт каталитического крекинга. Используется при приготовлении мазутов и в качестве сырья для производства сажи, термического крекинга и коксования.
Каталитический риформинг
Каталитический риформинг бензинов – высокотемпературный каталитический процесс, позволяющий получать высокооктановые компоненты автомобильных топлив, а также ароматические углеводороды – бензол, толуол, ксилол, этилбензол.
Температура риформинга зависит от применяемого катализатора. Так, при использовании оксидных катализаторов (оксиды хрома и молибдена) температура процесса примерно 540 оС, при использовании платино-рениевого катализатора при давлении 1.4-2.0 Мпа – 470-520 и платинового – 480-530 оС.
При каталитическом риформинге происходит ароматизация бензинов за счет дегидрогенизации шестичленных нафтенов и дегидроциклизации парафинов. Для насыщения непредельных побочных продуктов крекинга риформинг проводят в присутствии водорода.
КОНТРОЛЬНЫЕ ВОПРОСЫ К ТЕМЕ 1.1
1-1.На какие классы подразделяются нефти по составу?
1-2.Из чего состоят углеводородная, неуглеводородная и минеральная части нефти?
1-3.Какие вещества называются нефтепродуктами? Перечислите основные из них.
1-4.Приведите общую схему переработки нефти. Для чего проводятся операции обессоливания и обезвоживания нефти?
1-5.В чем преимущество каталитического крекинга перед термическим?
ЗАДАЧИ К ТЕМЕ 1.1
1-1. В соединениях, входящих в состав нефтей, на 1 массовую долю элементов приходится 10 таких долей углерода и водорода (в среднем). Определите, какова массовая доля моноатомных сернистых соединений по отношению к другим соединениям во фракции, средняя относительная молекулярная масса которой 300. Элементный анализ показал массовую долю серы равную 1 %.
1-2. Массовая доля азота в нефтях в среднем 0.2 %. Из всех азотсодержащих соединений 30 % составляют азотистые основания, которые могут быть выделены обработкой 40 %-ным спиртовым раствором серной кислоты. При перегонке нефти все эти основания переходят в дистиллаты. Рассчитайте сколько железнодорожных цистерн вместимостью 32 м3 92 %-ной серной кислоты потребуется нефтеперерабатывающему заводу производительностью (по сырью) 500 тыс. т/г. Массовая доля дистиллатов прямой гонки равна 45 % от сырья, азотистые основания пиридин и хинолин (1: 1).
1-3. Рассчитайте поверхность теплопередачи (м3) конвективной камеры трубчатой печи для нагрева нефти с 443 до 523 К. Производительность печи 20 м3/ч, плотность нефти 0.85 т/м3; теплоемкость 2.05 кДж/(кг·град). Коэффициент теплопередачи 150 кДж/(м2· град·ч). Температура газов на входе в камеру 1123 К, а на выходе 693 К.
1-4. Определите массу этаноламина, необходимую для приготовления раствора, который может поглотить в виде кислой соли весь сероводород из попутного газа Марковского месторождения Иркутской области объемом 10000 м3.
1-5. Какая масса низкооктанового бензина в год потребуется для установки, производящей этилен массой 450 тыс. т, если потери в производстве составляют 0.5 %?
1-6. Масса бензина для пиролиза составила 11.1 млн. т. Рассчитайте объем пиролизных газов, который получен из этой массы бензина, и массу синтез-газа, если на нее расходовалось 18 % ресурсов метана пиролизного газа.
1-7. Мощности технологических линий по производству полиэтилена низкого давления составляют 150 тыс. т в год. Какую минимальную массу керосина следует подвергнуть пиролизу для обеспечения бесперебойной работы такой линии?
1-8. Какая масса канальной сажи может быть получена из газов прямой гонки нефти, если на нефтеперегонном заводе разгоняется 6 млн. т нефти и при этом образуется газ, массовая доля которого составляет 8.5 %? Выход сажи от углерода газа 22 %. Массовые доли компонентов газа (%): С2H6 – 12; СН4 – 28; С3H8 – 10; С2H10 – 26; С5H12 – 24.
1-9. Масса светлых нефтепродуктов как сырья для пиролиза составляет 16.5 млн. т. Валовой выход этих нефтепродуктов увеличивается за счет каталитического крекинга, коксования и гидрокрекинга мазута. Выход в этих процессах составляет соответственно 34.15 и 42 % светлых нефтепродуктов. Определите потребность в мазуте для получения светлых нефтепродуктов массой 7.6 млн. т. Доля каждого из процессов одинакова.
1-10. При получении бутадиена одностадийным окислительным дегидрированием бутана КПД процесса составляет 40 %. Масса бензина для пиролиза 15 млн. т. Рассчитайте массу бутадиена, которую можно получить при этом, если объемные доли компонентов газа окислительного пиролиза (%): Н2 – 24.8; СН4 – 17.1; С2Н4 – 19.4; C2H6 – 3.1; С3Н8 – 3.3; C4H10 – 15.4; СО и CO2 – 16.9 %. Выход газа 72 % от массы сырья.
1-11. Для увеличения ресурсов бензина керосиногазойлевую фракцию подвергают жидкофазному крекингу, одним из продуктов которого является газ, состав которого следующий (об. %): Н2 – 5; СН4 – 39; C2H6 – 19; С3Н8 – 16; C2H4 – 6; C4H6 –6; C3H9 –9. Определите выход газа (в % от сырья), если на 1 т фракции получается 100 м3 газа.
1-12. Какой объем природного газа необходим на неделю непрерывной работы котельной, обеспечивающей нагрев 1.5 м3/мин воды от 315 до 365 К? КПД котельной 15 % .
1-13. Рассчитайте теплоту сгорания смеси природного и доменного газов, в которой объемные доли компонентов: оксид углерода(II) – 30; водород – 3; оксид углерода(IV) – 9; азот – 58 %. Газы взяты в объемных долях 1 : 2.
1-14. Ежесуточно на Кубани добывается 50 млн. м3 природного газа. Рассчитайте, какую массу антрацита в год можно заменить этим газом, если использовать его как энергетическое топливо.
1-15. Какую массу изопрена и дивинила можно получить из попутного нефтяного газа объемом 4.5 млрд. мЗ, сжигаемого в факелах, если первый из них получается преимущественно из пентана, а второй из бутана?
1-16. Определите массу 96 %-ного этанола, которая может быть получена из этана, содержащегося в попутном нефтяном газе объемом 45 млрд. м3 (объемная доля 11 %), если потери в производстве составляют 15 %?
1-17. Полагая, что объемная доля метана в природном газе равна 94 %, рассчитайте, какую массу кокса как восстановителя позволит заменить такой газ объемом 1 м3. Массовая доля углерода в коксе 85 %.
1-18. За год сожжен в факелах и выпущен в атмосферу попутный газ объемом 10.5 млрд. м3. Какую массовую долю от угля, добытого в этом году (578 млн. т.), можно было бы заменить этим газом, если бы использовать его как топливо? Для расчета принять газ Серафимовского месторождения Коми АССР, уголь каменный и бурый (1 : 2) длиннопламенный и челябинский.
1-19. Минеральные удобрения могут быть получены из попутного газа по схеме водород – аммиак – мочевина. Определите, какая масса мочевины может быть получена из попутного газа объемом 15 млрд. м3. Какую массовую долю от выпуска минеральных удобрений (143 млн. т) составляет эта мочевина? При расчете принять, что в попутном газе объемная доля метана в среднем 80 %, пиролизом которого и получают водород. Суммарный выход всех процессов метан – мочевина составляет 60 %.
1-20. Если перевести в жидкое состояние попутный газ месторождения Русский хутор Ставропольского края, то какую массу бензина как топлива может заменить такой сжиженный газ массой 1 кг?
Переработка твердого топлива
Дата добавления: 2018-05-12; просмотров: 1134; Мы поможем в написании вашей работы! |
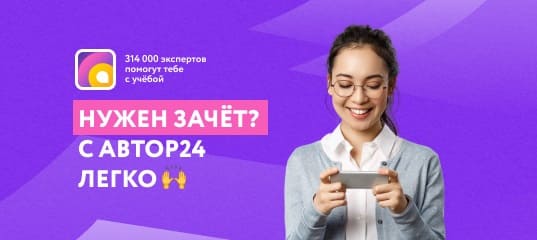
Мы поможем в написании ваших работ!