Ионное легирование полупроводников
Ионное легирование применяется при изготовлении полупроводниковых приборов с большой площадью; для изготовления резисторов с большими номиналами.
Суть метода: ускоренные электрическим и магнитным полями ионы примесей фокусируются и бомбардируют поверхность полупроводника. При этом они взаимодействуют с его атомами. Сталкиваясь с электронами (электронное торможение) и с ядрами атомов полупроводника (ядерное торможение) ионы теряют свою энергию. Если энергия иона больше энергии межатомной связи полупроводника, то атом полупроводника покидает узел кристаллической решетки. Энергия первично смещенного атома велика, поэтому этот атом образует каскад последовательных смещений. Таким образом, внедрение (имплантации) ионов сопровождается накоплением радиационных дефектов.
Для обеспечения активного легирования, нужно чтобы кристаллическая решетка была искажена минимально, а примеси занимали бы узлы кристаллической решетки. С этой целью, после внедрения ионов, полупроводник подвергают отжигу. В результате происходит распад радиационных дефектов. Отжиг проводится при t°= 600-700ºС в течение 10-20 мин. Иногда отжиг совмещают с внедрением, т.е. осуществляют внедрение в горячую пластину (применяется для примесей с малым коэффициентом диффузии). Ионное внедрение идет при высоком вакууме (≈10-6 мм.рт.ст.).
Профиль распределения примеси при ионном внедрении
|
|
В результате ядерного торможения атом примеси может резко менять направление движения. Совокупная траектория атома, таким образом, представляет ломаную линию.
Практическое значение имеет проекция этой траектории на нормаль к поверхности. Проекция эта является случайной величиной. Ее можно характеризовать некоторой средней длиной пробега атомов примеси и средне квадратическим отклонением. Подбирая пластины с определенным углом среза кристаллической решетки полупроводника, можно формировать необходимую глубину р-n перехода.
Схема установки для ионного внедрения примесей
1 -источник ионов;
2,3 -фокусирующая система;
4 - магнитный массепаратор;
5 - отклоняющие пластины;
6 - система сканирования;
7 - вакуумный затвор;
8 - устройство контроля ионного пучка; 9 - контейнер с пластинами; 10-система подогрева пластин; 11 - приемная камера.
Источник ионов включает катод, анод, систему подогрева. Ионизация атомов примеси проходит либо в ВЧ – либо в дуговом разряде (500В и 5А). Исходными материалами для ионов фосфора служит кристаллообразный фосфор. Из источника ионов, они извлекаются источником отрицательного напряжения (25кВ) и попадают в массепаратор. Там ионные пучки ускоряются и разделяются по массе. Пучок корректируется по направлению с помощью отклоняющих пластин (5). Конструкция приемной камеры позволяет выполнять сканирование пластин. Контейнер (9) рассчитан на несколько съемных кассет, он может вращаться и двигаться поступательно Это позволяет загружать и обрабатывать одновременно до 36 пластин. Специальное устройство поддерживает постоянно угол между плоскостью пластин и направленнем пучка. Рабочий вакуум 10-4-10-6 мм.рт.ст.. Перед выгрузкой пластин и разгрузкой новых рабочая область отсекается вакуумным затвором (7).
|
|
Достоинства ионного легирования:
1. Возможность легирования Si и других полупроводников в разных количествах вплоть до предела растворимости.
2. Получение разного профиля распределения примесей, причем без высокотемпературной разгонки (скрытые слои с повышенной концентрацией).
3. Процесс быстрый (продолжительность несколько минут).
4. Высокая точность глубины залегания примесей (до 0,002мкм).
5. Высокая воспроизводимость результатов.
6. Возможность на одной установке выполнять комплекс операций (легирование, металлизация).
7. Низкотемпературная пассивация Si при Т=100 - 500ºС такими атомами как О2, N2 позволяет получать диэлектрики SiO2, Si3N4.
|
|
8. Отсутствие бокового внедрения.
Недостатки:
1. Глубоко легированные области сложно воспроизводить.
2. Затруднена обработка пластин большого диаметра, т.к. происходит расфокусировка пучка при его больших отклонениях .
3. Сложность оборудования: необходим высокий вакуум; высокое напряжение; сложные приспособления.
Тема 13
- получение электропроводящего покрытия с пленкой SiO2
требования к проводящему слою:
1) Сопротивление слоя должно быть меньше или равно 0,04 Ома те при толщине 1 мкм удельное сопротивление должно быть меньше или равно 0,04 мкОм*м
2) Материал должен выдерживать плотность тока I = (1 -3) * 105 А/cm2
3) Материал не должен образовывать хим соединений с кремнием
4) Должна быть хорошая адгезия к кремнию
5) Материал должен выдерживать много кратные циклические изменения температуры.
Наиболее полно этим требованиям отвечает алюминий марки А99
Удельное сопротивление (ро) = 0.0028 мkOm*m.вввв.dddd.
Он обладает высокой адгецией к кремнию, благодаря способности к окислению. После фотолитографии проводят вжигание алюминия при температуре 550 градусов цельсия в теч 5 – 10 минут.
|
|
Цель вжигания – обеспечить прочное сцепление алюминия с кремнием в контактных окнах.sdfsdf.
Температура плавления 550 градусов это температура эфтектики в сплаве алюминия в те вжигание без образования жидкой фазы при этом алюминий восстанавливает кремний из окисла. В результате образуется хороший Омический (не выпрямляющий) эффект. Если концентрация примеси менее 5*1017 1/см2 то за счет разности работы выхода электронов из кремния и алюминия образуется пространственный заряд и потенциальный барьер (барьер шотки)
Что обычно выполняется совместно с эмиттерной N+ областью. База в области контакта дополнительно легируется при вжигании его за счет диффузии алюминия. Пластичность алюминия способствует удерживанию внутренних напряжений в пленке возникающей изза большой разноси ТКЛР Al и Cr
AL – обладает высокой технологичность, пленки AL получают в вакуумным испарением из резистивных испарителей. Температура пленки 200- 400 скорость осаждения 10-15 нм в секунду. При нагреве через границу раздела Алюм кремний через контактные окна происходит взаимная диффузия АЛ и КР причем кремль в АЛ диффундирует быстрее. Это приводит к эррозии поверхности кремния и ухудшение контакта пленки с подложкой.
Чтобы избежать этого в алюминий предварительно вводят два атомных процента кремния. Кроме АЛ используется сплавы металлы – вольфрат молибден золото титан платина.
Периферийные контакты.
Являются составной частью рисунка меж соединений их получают одновременно. Они служат для присоединения проводящих перемычек между ГИМС и внешними выводами корпуса.
Размеры и расположение контактных площадок определяется расположением выводов корпуса и технологическими требованиями.
Обычно их выполняют квадратными достаточными для обеспечения качественного контакта с перемычкой.
Способы создания объемных выводов на кристалле.
Фотолитография для вскрытия окон диаметром 0.07 мм с расположением на периферийными контактными площадками.
Вакуумная металлизация последовательно в металле толщина относительно и меди толщиной 0.3 мм.
4тый этап – фотолитография для маскирования фоторезистом всей поверхности кроме открытых.
5тый – гальваническое наращивание меди толщина 35мкм а затем поверх наносят серебро 2-4 мкм.
Содержащее в олове серебро препятствует растворению гальванического серебра образовавшаяся высота выводов доходит до 5-15 мкм
Основной недостаток – разновысокость выступов.
Особенности формирования структуры балочных выводов.
Балочные выводы являются более технологичными они выступают за пределы кристалла. При совмещении перевернутого кристалла появляется возможность визуального контроля. Структуру балочный выводов обычно составляют алюм – титан – молибден – золото. В начале как обычно получают Ал меж соединения. Потом наносят силициум Ололо толщиной 5-6мкм в котором формируют окна на участке будущих балочных выводов, далее последовательно напыляют титан(1 десятая микрометра) молибден (0.2 мкм) и золото(0.15 мкм) затем получают маску из фоторезиста с окнами для балочных выводов и выполняют гальваническое наращивание золота до 10 – 15мкм.
А рабочую поверхность покрывают временным технологическим …
В результате получают след структуру:
Рисунок Б – внешний вывод кристаллов.
Недостатком ИМС с балочными выводами является относительно низкий коэф использования пластины и пониженная механическая прочность выводов.
Сухой метод получения объемный выводов
-это получение объемных выводов путем сварки золотых шариков в стык.В результате нагрева золотой проволоки в конце получается шарик после сварки проволока сразу отрезается у основания шарика.
Достоинства – высокая адгерия производительность
Недостаток – разновысокость.
Дата добавления: 2018-05-12; просмотров: 1697; Мы поможем в написании вашей работы! |
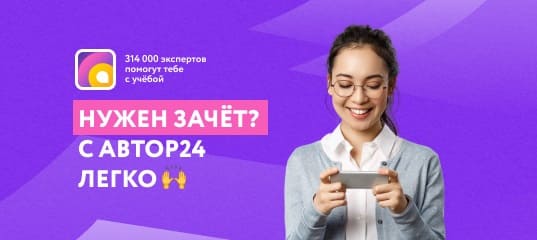
Мы поможем в написании ваших работ!