Механическая обработка заготовок
Окончательное формирование параметров лопаток первой ступени
турбины осуществляется на втором этапе обработки заготовок. Получен-
ная в литейном производстве исходная монокристаллическая заготовка
после контроля выходных параметров поступает на участок механической
обработки, где выполняется входной контроль параметров исходной заго-
товки. Он предусматривает проверку сопроводительных документов и
оценку качества поверхностей и материала заготовок на основании согла-
сованных технических требований к заготовительному производству и
соответствия заготовки установленным эталонным образцам.
Тщательной проверке подвергаются технологические базовые уста-
новочные поверхности 6–10 (см. рис. 3.5), которые формируют «ось»
исходной заготовки и обеспечивают качество дальнейшей обработки
заготовок в механическом производстве.
Процесс механической обработки можно условно разделить на три
основные части:
1) операции №10–80 – обеспечивается формирование профиля замка
лопатки и его положение относительно пера;
2) операции № 85–305 – выполняется основная механическая обра-
ботка рабочих поверхностей лопаток;
3) операции №310–500 – осуществляются доводочные и отделочные
процессы окончательного формирования качественных показателей
поверхностей лопаток.
86
План механической обработки исходной монокристаллической заго-
|
|
товки имеет следующую последовательность;
Первая часть содержит следующие операции.
№10. Заготовка (отливка).
№15. Входной контроль.
№20. Предварительное шлифование торца замка.
№25. Шлифование клина замка.
№30. Электрохимическое шлифование (ЭХШ) выходной кромки ло-
патки.
№35-60. Предварительная обработка свободных поверхностей ЭХШ.
№65. Окончательное шлифование профиля елочного замка лопатки.
№70. Окончательное шлифование торца замка лопатки.
№75. Шлифование выходного торца замка лопатки.
№80. Шлифование входного торца (Т) замка лопатки.
Вторая часть содержит следующие операции.
№85-100. Предварительное шлифование стыковых поверхностей
верхней бандажной полки и нижней замковой полки.
№105-130. Шлифование базовых поверхностей на верхней бандаж-
ной полке.
№135-140. Шлифование фасок и стыковых поверхностей под пла-
стину.
№145. Зенкерование выемки под заглушку.
№150-160. Абразивно-полировальнная обработка (АПО) радиусов
на замке, уступов на бандажной полке, трактовой поверхности замка и
бандажа и других поверхностей.
№165-180. Очистка, промывка и контроль лопатки перед пайкой.
№185-190. Комплектование и пайка заглушки.
№195-200. АПО входной и выходной кромок пера лопатки.
|
|
№205-210. Электроэрозионная обработка (ЭЭО) выборок, отверстий
и пера лопатки.
№215-225. Зенкерование фасок в отверстиях и промывка внутренней
полости лопатки.
№230-245. Абразивно-жидкостная обработка (АЖО) отверстий и
выходной кромки.
№250-265. ЭХШ полки замка и контактных поверхностей бандаж-
ных полок.
№270-285. Гидроабразивная обработка (ГАО) внутренней полости и
АПО полок замка.
87
№290-305. Промывка и контроль перед нанесением термо-
защитного покрытия.
Третья часть содержит следующие операции.
№310. Алитирование внутренней полости и отверстий.
№315-330. Глянцевание профиля хвостовика, промывка перед кон-
тролем.
№335. Люминесцентный (ЛЮМ) контроль.
№340-350. АЖО круговая, виброшлифование, АПО под покрытие.
№355. Контроль.
№340. Создание термозащитного покрытия.
№345-350. Круговая АЖО, промывка и заливка внутренней полости
парафином.
№355-390. Обработка рабочих поверхностей лопатки микро шари-
ками.
№395-415. Промывка горячей водой и шлифование контактных по-
верхностей бандажных полок.
№420-435. Окончательное шлифование стыковых поверхностей
бандажных полок.
№440-450. АПО пазов на торце замка и контура полок.
№455-460. ЛЮМ-контроль, слесарная доводка лопатки.
|
|
№465-470. Сборка и сварка ТЭС заглушки.
№475. Рентгеноконтроль.
№480-490. Промывка, контроль.
№495-500. Упаковка и отправка на сборку.
В этом процессе можно выделить отдельные операции, на которых
формируются окончательно качественные показатели детали. Тщатель-
ность выполнения операций и подготовка к выполнению этих операций
является залогом качества продукции.
Первая часть технологического процесса механической обра-
ботки заготовок заключается в предварительном формировании ос-
новных поверхностей лопаток шлифованием. Предварительные опера-
ции обеспечивают снятие основного припуска и напуска, полученного
в исходной заготовке, и создают равномерное расположение слоя ме-
талла для последующих операций по окончательному формированию
профиля елочного замка лопатки.
88
Рис. 3.10. Схема первой части механической обработки лопатки
Первой ступени турбины
89
|
Последовательность обработки основных поверхностей замковой
части лопатки и формирование окончательного профиля замка лопатки
представлена в графическом виде на рис. 3.10. При этом важнейшей
задачей является обеспечение точности расположения замка лопатки
|
|
относительно пера. Параметры точности расположения пера лопатки
относительно технологических баз, полученные в процессе отливки
исходной заготовки, необходимо сохранить, а также обеспечить совпа-
дение оси замка с осью технологических баз исходной заготовки. Эта
задача выполнима только шлифованием замковой части лопатки. Перо
лопатки не должно подвергаться механической обработке со значи-
тельным съемом металла, так как профиль пера лопаток на этом этапе
уже соответствует окончательному.
Первая механическая операция № 20 выполняется на плоскошлифо-
вальном станке. Заготовка базируется по основным технологическим
поверхностям 6-10. Эти поверхности создают ориентирование в техно-
логической системе относительно развернутой призмы (угол призмы
ϕ). Крепление заготовки направлено к центру призмы (точка 0). Такая
установка создает минимальные погрешности при ориентировании и
обеспечивает надежное закрепление заготовки в технологической сис-
теме. Операция проводится при обильном охлаждении зоны обработки
содовым раствором №8 на плоскошлифовальном станке (модели 372Б)
при следующих режимах обработки: скорости резания v=30 м/с; скоро-
сти детали vдет =10 м/мин; продольной подаче t=0,05 мм/дв. ход. Шли-
фовальный круг имеет прямоугольную форму ПП350×40×127. Состав
круга 24А40СТ1К обеспечивает съем значительного припуска и создает
шероховатость поверхности не ниже Rz=40 мкм.
Контроль геометрических параметров (размер а1= 98,42±0,2 мм) вы-
полняется на специальном контрольно-измерительном приборе. Допуск
на расположение обрабатываемой поверхности относительно базы вы-
полняется в пределах 0,3…0,4 мм для различных типоразмеров лопа-
ток. Операционный размер а1 задается относительно базовой техноло-
гической поверхности 6, которая расположена в трактовой части пера
лопатки. Такое базирование заготовки принято с целью обеспечения
минимально возможного смещения обрабатываемой поверхности отно-
сительно профиля пера лопатки.
Назначение данной операции заключается в съеме основного при-
пуска и напуска в наиболее сложном месте перехода исходной заготов-
ки в литниковую систему. В этом месте при изготовлении исходной
заготовки происходит наиболее интенсивный процесс литья и выхода
90
литейных газов. В связи с напряженными условиями при литье и с це-
лью создания высокого качества материала у замка лопатки в данной
зоне формируют значительный припуск, который в отдельных случаях
достигает более 3 мм. После его снятия создается равномерный слой
металла для последующей окончательной обработки торца лопатки и
удаления дефектного слоя, полученного в процессе отливки исходной
заготовки.
На операции №25 производится предварительная, последовательная
обработка клина замка лопатки. На этой операции также используются
технологические базовые поверхности 6–10, которые обеспечивают
точное ориентирование в технологической системе и надежное закреп-
ление заготовки в призме специального станочного приспособления.
Целью данной операции является снятие основного припуска по клину
замка, который может достигать 2,5 мм и равномерного распределения
слоя металла для последующей обработки замка.
Эта операция проводится в два этапа. На первом этапе формируется
поверхность клина замка со стороны корыта и обеспечивается размер
а3. Затем производится шлифование поверхности клина замка со сторо-
ны спинки и обеспечивается размер а2. Угловое параметры á1=15° и
á2=30° достигаются за счет расположения заготовки в технологической
системе и правке образующих поверхностей шлифовальных кругов.
Положение клина замка в осевом направлении (ось Z) создается бла-
годаря ориентированию его относительно базовой поверхности 6 и вы-
полнению операционного размера а2 (90±0,1 мм). Допуски на операци-
онные размеры, обеспечивающие профиль клина, задаются в пределах
0,15…0,2 мм (для различных типоразмеров лопаток).
При назначении номинальных размеров операционных размеров
создается равномерность припуска на последующую операцию (№65)
по глубинному шлифованию профиля замка лопатки. Операция №25
поводится на плоскошлифовальном станке (мод. 372Б) при следующих
режимах обработки: скорости резания v=30 м/с; скорости детали
vдет =10 м/мин.; продольной подаче t=0,05 мм/дв. ход. Процесс шлифо-
вания осуществляется при обильном охлаждении зоны обработки содо-
вым раствором №8. Шлифовальный круг имеет прямоугольную форму
ПП350×40×127, состав круга 24А40СТ1К. Шероховатость обрабаты-
ваемой поверхности не ниже Rz =40 мкм.
Обработка выходной кромки пера лопатки (операция №30) выпол-
няется методом электрохимического шлифования при следующих ре-
жимах: напряжение U = 0,01в; v = 30 м/сек.; продольной подачи Sм =
91
1,5…2 мм/мин. Снятие дефектного слоя после литья с тонких стенок
выходной кромки лопатки выполняется на электроалмазном шлифо-
вальном станке. Малая подача заготовки при шлифовании обеспечива-
ет обработку без возникновения прижогов.
Следующие операции – подготовка заготовки к проведению оконча-
тельной обработки профиля замка лопатки.
На операции №65 (рис. 3.11) формируется окончательный профиль
замка лопатки методом глубинного шлифования. При глубинном шли-
фовании до значений t = 10…15 мм длина дуги контакта заметно уве-
личивается. С ростом дуги контакта инструмент-заготовка повышаются
нагрузки в технологической системе, поэтому для глубинного шлифо-
вания создаются специальные высокопроизводительные станки. Они
отличаются числом (один или два) шлифовальных многониточных кру-
гов и расположением их осей [22, 23].
Станки для глубинного шлифования имеют: приборы для правки
многониточных шлифовальных кругов, редуктор для уменьшения час-
тоты вращения шлифовального кругов и регулируемый ускоренный
подвод и отвод кругов.
Режимы глубинного шлифования замков лопаток елочного типа при
скорости круга v=27 м/c приведены в табл.3.7
Таблица 3.7. – Режимы глубинного шлифования замков лопаток
Елочного типа
Скорость стола,
Глубина
Глубина
Температура
мм/мин
шлифования t, мм правки, мм
шлифования С°
50
100
100
1,97
1,07
0,05
–
0,2
0,2
1000*
780*
750*
Станки-полуавтоматы (ЛШ–233) предназначенные для двухсторон-
него глубинного шлифования профильных поверхностей замков лопа-
ток ГТД с непрерывной правкой шлифовальных кругов алмазными ро-
ликами (рис. 3.11), позволяют обеспечивать высокие показатели каче-
ства поверхностей замка. Непрерывная правка шлифовальных кругов и
оптимальные режимы обработки на окончательном этапе формирова-
ния профиля замка лопатки обеспечивают точное копирование формы
профилей этих инструментов. Расположение верхнего контура профиля
(поверхность М), относительно нижнего контура профиля (поверхность
N), заданные операционным размером аМN= 0±0,01 мм, обеспечивается
92
Рис.3.11. Схема глубинного шлифования профиля замка лопатки
первой ступени турбины:
1 – стол; 2 – станина станка; 3 – механизм непрерывной правки
нижнего круга; 4 – нижняя каретка; 5 – нижняя шлифовальная бабка;
6 – направляющие колонны; 7 – верхняя каретка; 8 – колонна; 9 – механизм
непрерывной правки; 10 – верхняя шлифовальная бабка
93
|
по первой технологической схеме [11]. Остаточное поле рассеивания
погрешности, зависящие от метода обработки ùо практически равно
нулю. Суммарное поле рассеивания погрешности также близко к нулю:
ùàMN = ùà0М + ùà0N ≅ 0 ≤ ТаMN ≤ 0,02 мм.
Расположение замка лопатки относительно трактовой части профиля
пера лопатки в направлении оси Z на этой операции выполняется с высо-
кой точностью. Ориентирование заготовки в технологической системе
осуществляется по поверхности 6 , которая находится в подполочном
пространстве лопатки. Размер ау, определяющий установку заготовки и
поле рассеивания этого размера в направлении оси Z, весьма мал.
После выполнения операции №65 профиль елочного замка лопатки
соответствует заданным значениям чертежа детали. Комплекс конст-
рукторских поверхностей, который выполнен на операции №65, обес-
печивает ориентирование лопатки в диске турбины в направлении ко-
ординатных осей Y и Z. На этой операции формируется базовая плос-
кость лопатки (см. рис. 3.2 и рис. 3.10). Относительно этой плоскости и
оси замка (оси детали) задаются и обеспечиваются все основные эле-
менты лопатки. В связи с этим качественное выполнение операции
№65 является весьма важным. Точность установки на этой операции
непосредственно влияет на возможное суммарное смещение ÄÓсм про-
филя лопатки относительно замка (см. рис. 3.8). На этой операции дос-
тигается шероховатость поверхности профиля замка Ra ≤ 2,5 мкм. Зона
шлифования обильно охлаждается смазочно-охлаждающей жидкостью
АКВОЛ-2.
Контроль геометрических параметров профиля осуществляется на
специальных контрольно-измерительных приборах, настройка которых
производится по эталонам. Периодически качество лопаток и кон-
трольно-измерительной оснастки проверяют в метрологических лабо-
раториях.
При окончательном шлифовании торцевой поверхности замка (опе-
рации №70) базирование заготовки на этой операции выполняется от-
носительно профиля елочного замка. Операционный размер а8 (см. рис.
3.10) обеспечивает непосредственную связь обрабатываемой поверхно-
сти с базовой плоскостью лопатки.
На операции №75 производится чистовое шлифование торца замка
лопатки со стороны входной кромки пера. На этой операции формиру-
ются окончательные параметры конструкторской поверхности лопатки,
которая ориентирует ее в диске турбины по направлению оси X. Бази-
94
рование заготовки в направлении оси X по входной кромке пера лопат-
ки минимальное смещение этого профиля относительно конструктор-
ской базы.
Операция №80 - окончательная обработка торца замка лопатки со
стороны выходной кромки пера лопатки. Операции №70, 75, 80 выпол-
няются на плоскошлифовальных станках типа ПШ – 232.
В комплексе операций первой части технологического процесса ме-
ханической обработки лопаток формируется важный качественный по-
казатель, который определят точность расположения профиля пера от-
носительно замковой части. Этот показатель характеризует качество
проходных сечений лопаточного венца и существенно влияет на КПД
турбины, вибрационное состояние роторной части двигателя и другие
качественные показатели ГТД.
На основании представленного технологического процесса произве-
дем анализ выполнения качественного показателя лопатки по располо-
жению профиля пера относительно замка полученной из исходной мо-
нокристаллической заготовки в первой части механической обработки
лопатки.
Результаты анализа размерных связей при формировании профиля
пера лопатки относительно технологических базовых поверхностей
6-10 приведены в табл. 3.8. Дальнейшая механическая обработка ис-
ходной безприпусковой заготовки на следующем этапе вносит допол-
нительное смещение замка лопатки относительно принятых технологи-
ческих баз и соответственно относительно пера лопатки.
Для анализа суммарного смещения профиля пера лопатки, относи-
тельно оси замка лопатки рассмотрим размерные связи, учитывающие
эти изменения.
В соответствии с комплексной схемой и учетом изменений, про-
шедших на операции №65, положение образующих поверхностей отно-
сительно фактической оси лопатки получает дополнительное смеще-
ние, которое определяется погрешностью выполнения размера а7.
Для размера К2 суммарное поле рассеивания
ù Ê 2 = ∑ ùi = ù Ë îð + ù Ë 10 + ù Ë 5 + ù Ë 0 + ù Ë 3 +
+ ù Ë 7 + ù Ë 12 + 0,5ùà7 + ùà6 ≤ ÒÊ 2 ≤ 0,4 ìì,
где 0,5 ùа 7 и ùа 6 – поля рассеивания погрешностей смещения, полу-
ченные на операции №65.
Принимая известные значения полей рассеивания для операционных
размеров, имеем
95
ù К 2 = 0 + 0,15 + 0,1 + 0 + 0,1 + 0,05 + 0,08 + 0,05 + 0,05 = 0,58 мм.
Таблица 3.8. Основные значения параметров качества изготовления
Лопаток
Заданные конструктор-
ские размеры лопатки
Изменение точности в процессе изготовления
Для исходной заготовки Механическая обработка
Размер
К2
С2
К3
К4
Допуск
0,4
0,4
0,55
0,55
ù
0,48
0,48
1
0,46
Верω
0,326
0,326
0,82
0,276
К
0,816
0,816
1,6
0,5
ù
0,58
0,58
Верω
0,412
0,412
К
1,03
1,03
1,6
0,5
Л1
0,1
0,54
0,340
-
Для размера С2 суммарное поле рассеивания:
ùÑ2 = ∑ ùi = ù Ë îð + ù Ë 10 + ù Ë 5 + ù Ë 0 + ù Ë 4 +
+ ù Ë 6 + ù Ë 11 + 0,5ùà7 + ùà6 ≤ ÒÑ2 ≤ 0,4 ìì .
Принимая известные значения полей рассеивания, в соответствии с
технологическим процессом имеем:
ùС 2 = 0 + 0,15 + 0,1 + 0 + 0,1 + 0,05 + 0,08 + 0,05 + 0,05 = 0,58 мм.
Наиболее вероятные значения анализируемых параметров опреде-
ляются по формуле (3.1):
Для определения наиболее вероятного поля рассеивания размера К2,
определяющего положение контура пера лопатки со стороны корыта
относительно оси замка (координаты XдYд) используем предельную
арифметическую сумму полей составляющих звеньев ùÊ 2 = 0,58 мм.
Так как m = 7; ì = 0,3; d = 0,1, ùmax/ωmin = 0,15/0,05 = 3; p = 0,027%, в
соответствии с прил. 1, К = 0,71.
Тогда Вер ù К 2 = К ù К 2 = 0,61⋅0,58 = 0,4118 мм.
Для вероятного поля рассеивания Вер ùС 2 , размера С2, определяю-
щего положение контура пера лопатки со стороны спинки относитель-
но оси замка (координаты XдYд) и расчетного значения ùС 2 = 0,58 мм
определим вероятностную характеристику размера.
96
Так как m = 7; ì = 0,3; d = 0,15/0,05 = 3; p = 0,027%, в соответствии с
прил. 1, то К = 0,61.
Тогда Вер ùС 2 = К ùС 2 = 0,61⋅0,58 = 0,4118 мм.
Для оценки состояния совместного производства изготовления мо-
нокристаллической отливки и первого этапа механической обработки
профиля пера лопатки методом глубинного шлифования определим
коэффициенты точности процесса в соответствии с методикой [10] и
представим основные значения параметров качества изготовления ло-
паток в табл. 3.8.
Таким образом, по результатам анализа геометрической точности
основных параметров при изготовлении лопаток (табл. 3.8) можно сде-
лать вывод: размеры К2 и С2 определяющие положение корыта и спин-
ки относительно конструкторских базовых поверхностей выполняются
с коэффициентом точности, близким к единице. Это условие требует
постоянного контроля и поддержания технологической оснастки в ка-
чественном рабочем состоянии. Вероятность выхода геометрических
параметров за пределы допустимых значений весьма высокая.
С целью улучшения качественных показателей необходимо наме-
тить конструкторско-технологические мероприятия по совершенство-
ванию процесса обработки и необходимости снижения коэффициента
точности.
Коэффициент точности для размера К3 является чрезвычайно высо-
ким и появление брака по утонению стенки у пера лопатки значитель-
ное. Для снижения вероятного поля рассеивания этого параметра также
необходимо разработать мероприятия по совершенствованию техноло-
гического процесса. Эти мероприятия должны в первую очередь усо-
вершенствовать технологический процесс изготовления керамических
стержней (см. поле рассеивания размера Л1 и результаты статистиче-
ских исследований) и разработать устройства, позволяющие улучшить
ориентирование стержня в литейной форме.
Необходимо отметить, что эта задача сложная и требует значитель-
ных качественных изменений в технологическом процессе.
Коэффициент точности для размера К4 выполняется в пределах эко-
номической целесообразности и обеспечивает стабильное формирова-
ние заданных конструкторских требований.
97
Дата добавления: 2018-05-12; просмотров: 1480; Мы поможем в написании вашей работы! |
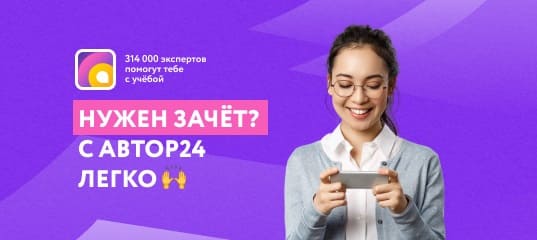
Мы поможем в написании ваших работ!