Структура технологических операций.
Технологическая операция — законченная часть технологического процесса, выполняемая непрерывно на одном рабочем месте, над одним или несколькими
одновременно обрабатываемыми или собираемыми изделиями, одним или несколькими рабочими. Условие непрерывности операции означает выполнение работы без перехода к обработке другого изделия.
Установка — часть технологической операции, выполняемая при неизменном закреплении обрабатываемой заготовки или собираемой сборочной единицы.
Позиция — отдельное фиксированное положение, занимаемое неизменно закрепленной обрабатываемой заготовкой или собираемой сборочной единицей совместно с приспособлением относительно инструмента либо неподвижной части оборудования, при выполнении определенной части операции.
Технологический переход — законченная часть технологической операции, выполняемая одними и теми же средствами технологического оснащения при постоянных технологических режимах и установке.
Вспомогательный переход — законченная часть технологической операции, состоящая из действий человека и (или) оборудования, которые не сопровождаются изменением свойств предметов труда, но необходимы для выполнения технологического перехода (закрепление заготовки, смена инструмента и др.).
Рабочий ход — законченная часть технологического перехода, состоящая из однократного перемещения инструмента относительно заготовки, сопровождаемого изменением формы, размеров, качества поверхности и свойств заготовки (шлифование одной поверхности за 5-6 ходов).
|
|
Вспомогательный ход — законченная часть технологического перехода, состоящая из однократного перемещения инструмента относительно заготовки, необходимого для подготовки рабочего хода.
Прием — законченная совокупность действий человека, применяемых при выполнении перехода или его части и объединенных одним целевым назначением.
Установление технологического маршрута последовательности обработки.
При установлении общей последовательности обработки сначала обрабатывают
поверхности, принятые за технологические базы. Затем обрабатывают остальные
поверхности в последовательности, обратной степени их точности.
Изложенный принцип построения маршрута, однако, не во всех случаях
обязателен. При жесткой заготовке и малых размерах обрабатываемых
поверхностей окончательную обработку отдельных элементов можно выполнять и
в начале маршрута. Данный принцип, кроме того, в известной степени
противоречит принципу концентрации обработки, когда в одной операции можно
совместить переходы черновой и чистовой обработок.
|
|
Последовательность операций также может измениться, если деталь
обрабатывается по типовому или групповому процессу.
Составление технологического маршрута обработки детали предшествует
оформлению технологического процесса на картах и ведется в черновой
тетради, с последующим изложением в пояснительной записке (для курсовых
проектов).
При разработке двух или нескольких вариантов маршрутов (изготовление
детали из разных заготовок, на разном оборудовании и т.п.) выбирается
наиболее экономичный в данных производственных условиях. Если его
определить затруднительно, то проводится соответствующий экономический
расчет. В маршрут включаются все операции.
30. Выбор видов обработки.
31. Выбор оборудования.
Установление режимов резания.
Режимы резания определяются глубиной резания t, подачей S, скоростью резания V. При назначении элементов резания учитывается характер обработки, тип и размеры инструмента, материал его режущей части, материал и соотношение заготовки, тип и состояние оборудования.
Значение t,S,V влияет на точность качества получаемой поверхности, производительность и себестоимость обработки.
|
|
При черновой обработке назначают максимальную t, равную припуску при обработке или большей его части. При чистовой – в зависимости от требований точности размеров и параметров, характеризующих качество поверхностного слоя.
Подача должна быть установлена максимально допустимой. При черновой обработке она ограничивается прочностью и жесткостью элементов технологической системы станка, а при чистовой – и отделочной точностью и шероховатостью обрабатываемой поверхности, определенная по расчетом или по нормативам подача должна соответствовать паспортным данным станка.
Скорость резания зависит от выбранной глубины резания, подаче, качества и марке обрабатываемого материала, геометрических параметров режущей части инструмента.
Скорость резания рассчитывается по установленной для каждого вида обработки эмпирическим формулам, которые имеют общий вид
Значение коэффициента характеризуют условия обработки, t и S, и показатели степени, содержащиеся в этих формулах так же как и период стойкости T
инструмента, применяемые для данного вида обработки приведены в таблицах для каждого вида обработки в справочнике технолога машиностроителя.
Дата добавления: 2018-05-12; просмотров: 373; Мы поможем в написании вашей работы! |
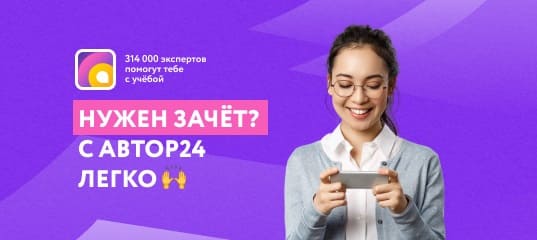
Мы поможем в написании ваших работ!