Реакторы каталитического риформинга
Реакционные аппараты
На глубину конверсии сырья в значительной степени оказывает влияние газодинамический режим контактирования сырья с катализатором, осуществляемый в реакторах различных типов.
В реакторах с движущимся слоем шарикового катализатора катализ, массо- и теплообмен осуществляют фильтрацией прямотоком в режиме, близком к идеальному вытеснению. К недостаткам реакторов этого типа следует отнести:
— катализ проводят на поверхности крупнозернистого катализатора
— при прямотоке, в отличие от противотока, завершающую стадию крекинга осуществляют на поверхности закоксованного катализатора после потери им первоначальной активности;
— большое время контакта в реакторах этого типа приводит к ухудшению селективности крекинга в результате интенсивного протекания вторичных реакций.
В реакторах с псевдоожиженным (кипящим) слоем микросферического катализатора катализ, тепло- и массообмен осуществляют при идеальном перемешивании реактантов с катализатором в режиме, характерном для безградиентных реакторов (т. е. дифференциального типа). Как наиболее значимые достоинства реакторов этого типа следует отметить:
— высокую их удельную производительность;
— легкость транспортирования микросферического катализатора и регулирования технологического режима;
— осуществление каталитического процесса в области, близкой к чисто кинетической;
|
|
— отсутствие байпасных участков и градиента температуры в кипящем слое и некоторые другие.
Из недостатков реакторов с кипящим слоем можно указать следующие:
— неравномерность времени пребывания сырья в зоне реакции
Реакторы каталитического крекинга перечисленных выше двух типов в последние годы постепенно вытесняются более совершенными типами — прямоточными реакторами с восходящим потоком газокатализаторной смеси (лифт-реактор). Дополнительного улучшения выходных показателей крекинга (т. е.глубины конверсии и качества продуктов) на современных зарубежных установках каталитического крекинга достигают:
—применением современных высококачественных катализаторов;
— переходом на лифт-реакторы без форсированного псевдоожиженного слоя, но заканчивающиеся разделительными циклонами;
— переходом на многоточечный ввод сырья в лифт-реактор и др.
Регенераторы предназначены для непрерывной регенерации закоксованного катализатора путем выжига кокса кислородом воздуха при температуре 650…750 °С. На установках с движущимся слоем катализатора регенерацию шарикового катализатора проводят в многосекционном аппарате, снабженном для снятия избытка тепла водяными змеевиками, соединенными с котлом-утилизатором.
|
|
Реакторы установок каталитического крекинга
Процесс каталитического крекинга основан на применении катализаторов, ускоряющих реакции; он протекает при температуре 450…500 °С и давлении 0,05…0,15 МПа. Сырьем являются керосиновые и соляровые дистилляты и остаточные продукты (мазут и др.). Процесс предназначен для получения высокооктановых бензинов, газов и газойля.
В настоящее время на нефтеперерабатывающих заводах применяют два типа установок каталитического крекинга:
— установки, на которых процесс химического превращения (крекинг сырья) и регенерации катализатора осуществляется в сплошном слое катализатора (катализатор шариковый);
— установки, на которых те же процессы происходят в псевдоожиженном, или кипящем, слое катализатора (катализатор порошкообразный).
На установках с циркулирующим катализатором процесс протекает в аппаратах шахтного типа, через которые непрерывным потоком сверху вниз движутся шарики
катализатора диаметром 3…5 мм. В прямоточных реакторах катализатор и сырье контактируют, двигаясь прямотоком. Реакторный блок каждой установки состоит из реактора, регенератора и системы транспорта катализатора.
|
|
Наибольшее распространение получают установки с порошкообразным или микросферическим катализатором. Реакторные блоки каталитических процессов с движущимся катализатором, включающие реактор, регенератор и систему транспорта катализатора, по взаимному расположению аппаратов и схемам циркуляции катализатора подразделяются на установки с одно- и двукратным подъемом катализатора.
Для схем с однократным подъемом катализатора используются два варианта – реактор располагают над регенератором или регенератор над реактором. При прочих равных условиях схемы с однократным подъемом катализатора отличаются большей высотой установки. Так, для установки каталитического крекинга с гранулированным катализатором высота реакторного блока при двукратном подъеме составляет60…70, а при однократном 80…100 м.
Реакторы каталитического риформинга
Реактор представляет собой цилиндрический вертикальный сосуд с шаровыми днищами. При 525 °С и 2…4 МПа водород способствует развитию водородной коррозии металла, вызывающей его трещиныи вздутия. Поэтому и для теплоизоляции изнутри металлическую стенку реактора защищают футеровкой из торкрет-бетона. Кроме того, внутри реактора устанавливают стальной перфорированный стакан, между стенкой которого и стенкой аппарата имеется газовый слой. Для изготовления корпуса и днища реактора применяют сталь марки 09Г2ДТ со специальной закалкой поверхности аппарата или сталь 12ХМ. Внутренняя арматура реактора и присоединительные фасонные патрубки изготовлены из легированных сталей.
|
|
Реакторы блока гидроочистки и риформинга имеют верхний штуцер для ввода и нижний
для вывода продуктов. В остальных реакторах риформинга штуцеры для ввода сырья и вывода продукта находятся вверху аппарата. Катализатор загружают в аппараты через верхний штуцер и выгружают через нижний. Каждый аппарат оборудован штуцерами для выхода паров при эжектировании системыво время регенерации катализатора. Из-за большого перепада давления(1,3…1,5 МПа) в реакторах с аксиальным движением потока, в последнее время стали применять реакторы с радиальным движением газо-сырьевого потока (реакционная смесь движется в реакторе через слой катализатора в радиальном направлении, а катализатор — вертикально) (рис. 8.19). Реакторы такого типа характеризуются малым гидравлическим сопротивлением (< 0,8 МПа). Даже при большом отношении высоты к диаметру можно обеспечить равномерное распределение катализатора при минимуме внутренних устройств, так что истирание катализатора очень мало.
Дата добавления: 2018-05-12; просмотров: 1243; Мы поможем в написании вашей работы! |
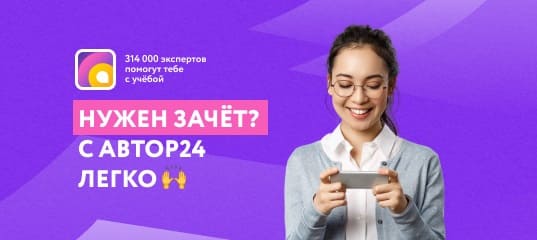
Мы поможем в написании ваших работ!