Контроль качества и методы испытания
5.1 Газлифтное оборудование подвергают испытаниям на предприятии-изготовителе и функциональным испытаниям в промысловых лабораториях перед вводом в эксплуатацию.
Скважинные камеры
Скважинные камеры подвергают:
- контролю сварных соединений;
- контролю твердости;
- контролю зазоров;
- механическим испытаниям;
- гидравлическим испытаниям.
5.2.1 Методы контроля сварных соединений
5.2.1.1 Контроль сварных соединений включает:
- визуальный и измерительный контроль;
- радиографию (РГ);
- ультразвуковую дефектоскопию (УЗД);
- цветной (капиллярный) (ЦД) или магнитопорошковый метод контроля (МПД);
- измерение твердости;
- механические испытания сварных образцов.
5.2.1.2 Контроль РГ или УЗД проводят после сварки и термообработки. Контролю ЦД по ГОСТ 18442 или МПД по ГОСТ 21105 подвергают сварные соединения после окончания работы со сварными швами либо после механической обработки.
5.2.1.3 Визуальный контроль проводят в соответствии с ГОСТ 3242. Перед контролем сварные швы и прилегающую в ним поверхность основного металла шириной не менее 20 мм по обе стороны шва очищают от шлака, брызг металла, окалины и других загрязнений.
В сварных соединениях не допускаются трещины, непровары, подрезы, незаплавленные кратеры. Размеры сварных швов должны соответствовать ГОСТ 5264 и ГОСТ 16037. Визуальному и измерительному контролю подвергают все сварные соединения.
5.2.1.4 Радиографический контроль сварных соединений проводят согласно ГОСТ 7512.
|
|
5.2.1.5 Ультразвуковую дефектоскопию проводят согласно ГОСТ 14782.
5.2.1.6 При контроле ЦД и МПД наличие протяженных и неодиночных дефектов является браковочным признаком.
5.2.1.7 Механическим испытаниям подвергают образцы, изготовленные из контрольных сварных стыков.
5.2.1.8 Каждый сварщик должен сварить контрольные пробы в объеме не менее 1 % общего числа сваренных им однотипных производственных стыков, но не менее одного стыка.
5.2.1.9 Из контрольных стыков изготовляют образцы на растяжение (не менее двух), статический (не менее двух) и ударный (не менее трех) изгиб.
5.2.1.10 Определяют следующие механические свойства сварных соединений:
- предел прочности;
- угол загиба, … °;
- ударную вязкость, KCU, (Шарпи) по шву и зоне термического влияния (ЗТВ).
5.2.1.11 В поперечном сечении образцов сварных швов проверяют твердость по металлу шва, ЗТВ и основному металлу.
При толщине металла менее 13 мм проводят по четыре измерения твердости в указанных участках сварного соединения.
5.2.2 Методы контроля твердости
5.2.2.1 Твердость поверхности готовых изделий контролируют в соответствии с ГОСТ 9012, ГОСТ 9013.
Критерии твердости принимают в соответствии со спецификацией изготовителя.
|
|
Испытания проводят на базовых образцах, число которых должно быть не менее 5 % общего числа изготовленных изделий, но не менее одного изделия.
Если испытуемые образцы по твердости не соответствуют контрольным значениям хотя бы по одной скважинной камере, то испытывают 100 % продукции. Не соответствующие нормативной документации изделия бракуют, ремонтируют и подвергают повторным испытаниям в соответствии с методом неразрушающего контроля (НРК).
5.2.3 Контроль зазоров
Каждую скважинную камеру контролируют оправкой калибровочного стержня длиной не менее 1070 мм и наружным диаметром - в соответствии со спецификацией калиброванных оправок для труб.
5.2.4 Механические испытания
Каждую скважинную камеру испытывают на собираемость с устанавливаемым газлифтным клапаном на стенде (рисунок 1). Газлифтный клапан устанавливают в скважинную камеру и извлекают из нее с помощью стандартных приспособлений канатной техники. Нагрузку при извлечении газлифтного клапана измеряют по индикатору массы.
5.2.5 Гидравлические испытания
5.2.5.1 Гидравлическим испытаниям подвергают все скважинные камеры после установки в них глухих пробок.
|
|
Скважинную камеру устанавливают в стенд (рисунок 2).
К камере прилагают гидравлическое давление, равное полуторократному расчетному давлению, но не менее 35,0 МПа.
Скважинную камеру нагружают и выдерживают под давлением не менее 3 мин. Затем давление снижают до нуля. Течь и отпотевание не допускаются.
5.2.5.2 Измерительное и испытательное оборудование
5.2.5.2.1 Параметры измерительного и испытательного оборудования должны быть: диаметр приборной шкалы манометра - не менее 100 мм, точность манометра ±2 % шкалы.
Трансформаторы давления, самописцы должны быть тарированы с точностью ±0,5 шкалы прибора. Допускается использовать калиброванные системы трансформаторов давления.
5.2.5.2.2 Для контроля присоединительной резьбы используют калибры в соответствии с документацией предприятия-изготовителя труб.
Оборудование, необходимое для измерения резьбы по API, калибруют в соответствии с [2].
5.2.6 Испытание скважинной камеры под нагрузкой.
5.2.6.1 Испытания проводят на стенде (рисунок 3).
1 - скважинная камера; 2 - мачта; 3 - направляющая; 4 - комплект стандартных приспособлений; 5 - лебедка; 6 - индикатор массы
Рисунок 1 - Стенд для испытания скважинной камеры на собираемость
1 - скважинная камера; 2 - пробка; 3 - переводник со штуцерами; 4 - трубопроводы с запорной арматурой; 5 - манометр
|
|
Рисунок 2 - Стенд для гидравлического испытания скважинной камеры
1 - скважинная камера; 2 - силовая рама; 3 - гидроцилиндр; 4 - обвязка гидроцилиндра; 5 - проушина
Рисунок 3 - Стенд для испытания скважинной камеры под нагрузкой
5.2.6.2 Скважинную камеру устанавливают в стенд. Гидроцилиндром создают растягивающую нагрузку, равную допускаемой нагрузке на страгивание для присоединительной резьбы скважинной камеры. Нагрузку контролируют по показаниям манометра.
Газлифтные клапаны
5.3.1 Газлифтные клапаны подвергают испытаниям на:
- герметичность;
- прочность;
- работоспособность.
5.3.2 Измерительное и испытательное оборудование
5.3.2.1 Диаметр манометров, используемых в испытательных стендах для нагружения газлифтных клапанов гидравлическим давлением, должен быть не менее 216 мм.
Точность манометра должна быть не ниже 0,25 % полной шкалы.
5.3.2.2 Показатели манометров, используемых на камере давления, должны быть точностью не ниже 5 % полной шкалы.
5.3.2.3 Минимальная погрешность преобразователей (трансформаторов) давления должна быть такой же, как и у манометров.
5.3.3 Испытание на прочность и герметичность
5.3.3.1 Испытаниям на прочность и герметичность подвергают основные элементы газлифтного клапана: сильфонную камеру, основной и обратный клапаны.
5.3.3.1.1 Прочность и герметичность сильфонной камеры газлифтного клапана проверяют на стенде (рисунок 4).
Газлифтный клапан устанавливают на стенд, сильфонную камеру медленно заполняют азотом под давлением 0,7 - 1,0 МПа до касания клапана с седлом, после чего давление доводят до 12,5+035 МПа. Давление выдерживают в течение 15 мин. Падение давления не допускается. В случае негерметичности сильфонную камеру заменяют и испытания повторяют.
1 - камера давления; 2 - газлифтный клапан; 3 - пульт управления; 4 - баллон с газом; 5 - баллон с воздухом
Рисунок 4 - Стенд для гидравлических испытаний сильфонной камеры
5.3.3.1.2 Герметичность обратного клапана газлифтного клапана проверяют на стенде (рисунок 5).
Газлифтный клапан с незаряженной сильфонной камерой устанавливают на стенд, постепенно повышают давление воздуха от 1,0 до 5,0; 10,0; 15,0; 21,0 МПа с выдержкой 5 мин на каждом значении давления.
При негерметичности обратного клапана в любом интервале давлений газлифтный клапан снимают со стенда, устраняют повреждения обратного клапана и повторяют испытания.
5.3.3.1.3 Проверка на герметичность основного клапана
Газлифтный клапан с заряженной азотом до давления 5,0 МПа сильфонной камерой устанавливают на стенд (рисунок 5), постепенно повышают давление воздуха в камере давления от 1,0 до 2,0; 3,0; 4,0; 5,0 МПа с выдержкой 5 мин на каждом значении давления.
При негерметичности основного клапана при любом из значений давления газлифтный клапан извлекают из стенда, устраняют повреждения основного клапана и повторяют испытания.
5.3.3.1.4 Испытание газлифтного клапана на работоспособность
Газлифтный клапан с заряженной азотом до давления 5,0 МПа сильфонной камерой устанавливают на стенд (рисунок 5), плавно повышают давление воздуха в камере давления до 6,0 МПа. Давление открытия клапана Р вычисляют по формуле
Ротк = Рр.отк ± (0,05 - 0,1) МПа,
где Ротк - фактическое давление открытия клапана;
Рр.отк - расчетное давление открытия клапана.
1 - камера давления; 2 - газлифтный клапан; 3 - пульт управления, 4 - воздушный ресивер
Рисунок 5 - Стенд для испытания газлифтного клапана на работоспособность
5.3.4 Протокол испытаний изготовителя должен содержать:
- результаты проверочных расчетов;
- техническое описание, технический паспорт изготовителя, перечень использованных материалов, перечень проверочных испытаний газлифтного оборудования и их результаты, дату испытания оборудования.
5.3.5 Протоколы должны храниться не менее пяти лет со дня изготовления оборудования с указанием типа, модели, типоразмера, заводского номера газлифтного оборудования.
Дата добавления: 2018-05-12; просмотров: 429; Мы поможем в написании вашей работы! |
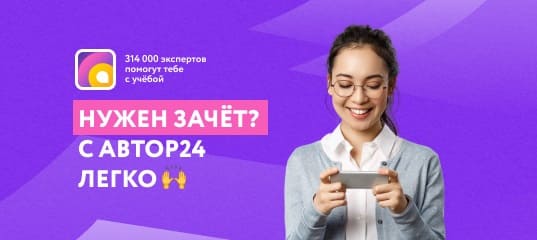
Мы поможем в написании ваших работ!