Свойства газонаполненных полимерных материалов
Материалы | Объёмная масса, кг/м3 | σв при сжатии, МПа | Водопоглощение за1 сутки, % | Теплостойкость Т °С | Структура | Горючесть |
Пенополивинил-хлориды | 100–220 | 0,5–1,5 | 0,2–0,3 | 60 | Равномерно замкнутая, пористая | Не горит при вынесении из пламени |
Пенополистиролы ПС–1, ПС–4 | 50–220 | 0,2–3,0 | 0,3 | 60 | То же | Горит |
Пенофенопласты | 190–230 | 1.0 | 0,3 | 120–150 | То же | Не горит при вынесении из пламени |
Пенополиуретаны | 40–60 | 0,3–3,0 | 0,5–1,0 | 100–130 | Закрытая, пористая | То же |
Пеноэпоксидопласты | 100–120 | 0,8–3,0 | – | 100–160 | Замкнутая | Горит |
Приложение 1.3
Режимы горячего прессования пластмасс
Пластмасса | Удельное давление Руд, МПа | Температура формиро- вания, Т°С | Время выдержки, tm, мин | Усадка при формовании, % |
Фенопласты с порошковыми наполнителями: | ||||
Новолачные и др. 01–040–02 | 15,0–45,0 | 170–200 | 0,05–0,7 | 0,4–0,8 |
Резольные и др. 32–330–02 | 15,0–40,0 | 180–200 | 0,1–0,7 | 0,4–0,8 |
На фенолоанилиноформальдегидных смолах: | ||||
СП1–342, СП 3–342–02 и др. | 15,0–40,0 | 180–200 | 1,2–1,6 | 0,4–0,9 |
На резольных фенолоформальдегидных смолах, модифицированных полиамидами К–114–35 и др. | 30,0–40,0 | 155–165 | 1,2–1,6 | 0,4–0,7 |
На новолачных фенолформальдегидных смолах, модифицированных поливинилхлоридом: фенолиты Bxl–090–34 и др. | 30,0–50,0 | 150–170 | 0,35–0,47 | 0,4–0,8 |
Прессматериалы на кремниеворганических смолах: | ||||
КМК–9 (асбест, кварцевая мука и др.) | 30,0–35,0 | 150–160 | 1–1,5 | 1,5 |
КМК–218, КМК–218л, КПЖ–9 (асбест и др. добавки) | 30,0 | 160±5 | 1–1,5 | 1,0 |
КФ–9 (кремниево-органическая смола, модифицированная фторопластом–4 с наполнителями) | 30,0 | 160–165 | 1–1,5 | 0,8–1,2 |
Пресс-поршки на мочевино - и меламиноформальдегидных смолах: | ||||
Аминопласт Al, A2 | 30,0±5,0 | 135–150 | 1–1,5 | 0,7 |
Мелалит (аминопласт Б) | 40,0±5,0 | 160+5 | 1,0 | 0,8 |
Аминопласт Г | 50,0±5,0 | 170±10 | 2,0 | – |
Аминопласт Д и Е | 30,0–50,0 | 150+5 | 1–2 | 0,4–0,7 |
Термопластические прессматериалы: | ||||
Полиакриловые пресс-поршки Л–1 | 15,0 | 130–140 | 1,5–2 | 0,1–0,6 |
Нитроцеллюлозный этрон | 20,0±5,0 | 125+5 | 1,5–2 | – |
Фторопласт–3 | 20,0–30,0 | 230–280 | 2,5–3,5 | – |
Фторопласт–4 ОП | 30,0–50,0 | 270–290 | – | – |
Фторопласт 42П и 42В | 20,0–30,0 | 220–230 | – | – |
Пресс-крошка: | ||||
Текстолитовая на фенолоформальдегидной смоле | 60,0–120 | 160+5 | 2 | 0,2–1,0 |
Древесная на резольной фенолформальдегидной смоле (ДПК) | 40,0–60,0 | 140–150 | 1,5–3 | – |
Волокниты: | ||||
Волокнит на хлопковой целлюлозе и фенолформаль–дегидных смолах: | ||||
Тормозной асбоволокнит К–6 | 30,0–60,0 | 165–180 | 0,3–0,5 | 0,3–0,6 |
Фрикционные пресс материалы К–Ф–3, К–Ф–ЗМ, К–Ф–ЗГ | 45,0±5,0 | 175+5 | 1,5 | 0,1–0,2 |
Стекловолокнит АГ–4В | 45,0+50 | 185±5 | 1–1,5 | 0,3–0,6 |
Стекловолокнит ДСВ | 35,0+5,0 | 155+5 | 1,5–2,0 | – |
Стекловолокнит ГСП | 15,0–30,0 | 140–180 | 1,5–2,0 | – |
Стекловолокнит ДВПМ–1П | 35,0+5,0 | 155±5 | 2–3 | |
Стекловолокнит на кремниеворганической смоле | 35,0 | 190±10 | 3–7 | 0,13–0,22 |
Пресс материалы со слоистым наполнителем: | ||||
Хлопчатобумажная ткань и бумага, пропитанные резольными смолами (текстолит, гетинакс, декоративный пластик) | 8,0–12,0 | 140–170 | 5 | – |
Стеклоткани, пропитанные резольными смолами (стеклотекстиль) | 2,0–5,0 | 160–180 | 4 –5 | – |
Древесный шпон, пропитанный резольными фенолоформальдегидными смолами (древеснослоистыйпластик ДСП) | 10,0–15,0 | 140–170 | 4–6 | – |
|
|
|
|
ИЗУЧЕНИЕ УСТРОЙСТВА И РАБОТЫ ИСТОЧНИКОВ ПИТАНИЯ СВАРОЧНОЙ ДУГИ
Цель работы
Изучить сущность и основные способы дуговой сварки; сущность, строение и статическую характеристику дуги; требования, предъявляемые к источникам питания сварочной дуги; устройство и принцип работы сварочных трансформаторов, генераторов и выпрямителя.
|
|
Задание
2.2.1. Изучить по учебникам сущность, способы дуговой сварки, физическую сущность, строение и статическую характеристику дуги.
2.2.2. Уяснить каким требованиям должны удовлетворять источники питания сварочной дуги.
2.2.3. Ознакомиться в лаборатории с устройством и регулировкой сварочных трансформаторов, научиться рисовать их электрические схемы.
2.2.4. Определить режим работы, при котором трансформатор работает не перегреваясь.
2.2.5. Ознакомиться в лаборатории с устройством и регулировкой сварочных преобразователей и генераторов постоянного тока. Научиться рисовать их электрические схемы.
2.2.6. Ознакомиться с приспособлениями для сварки.
2.2.7. Изучить по приложениям 2.1 – 2.4 технические характеристики различных источников питания сварочной дуги.
2.2.8. Составить отчет.
Оборудование рабочего места
Демонстрационные сварочные трансформаторы: СТШ–250, СТН–450, ТС–300, преобразователь ПСО–300, ПС–500; плакаты с электрическими схемами, действующие посты с трансформаторами ТС–500, оборудованные амперметрами, вольтметрами, электросчетчиками и приспособлениями для сварки.
План выполнения работы
|
|
2.4.1. Дома предварительно изучить теоретическую часть по конспектам и учебникам. Подготовить отчет с электрическими схемами устройств и таблицей 1.1.
2.4.2. Ознакомиться на рабочих местах с конструкциями, с устройством, маркировкой источников сварочного тока, с принципом их работы, с регулировкой и за счет чего получается крутопадающая характеристика. Обозначить на электрических схемах трансформаторов и генераторов марки и позиции.
2.4.3. Ознакомиться с требованиями безопасности на каждом посту у учебного мастера. Включить источник переменного (постоянного) сварочного тока в сеть, проверить напряжение холостого хода, при заданной дуге зафиксировать напряжение дуги и ток сварки, проверить регулировку. Данные занести в таблице 2.1. По ним построить вольтамперные характеристики источников и дуги.
2.4.4. По заданию преподавателя рассчитать режим работы источника и сделать вывод.
Справочные данные
Сваркой называется процесс получения неразъемных соединений металлических изделий за счет межатомных сил и межмолекулярных сил сцепления. Для этого путем нагрева сближают атомы соединяемых металлов на расстояние а = 0,2...0,9 нм параметра элементарной кристаллической решетки. Если нагрев осуществляют при помощи электрической дуги, то такая сварка называется дуговой.
Дуговая сварка (рис. 2.1) впервые была применена в России в 1882 году изобретателем Н.Н. Бенардосом, который использовал дугу, открытую
В.В. Петровым в 1802 году. Для сварки использовался угольный или графитовый электрод и постоянный ток прямой полярности: (–) на электроде, (+) на детали. Присадочный материал и флюс в сварочную цепь не включены, поэтому дуга оказывала прямое действие на основной металл и косвенное – на присадочный. В 1888 году Н.Г. Славянов предложил способ дуговой сварки металлическим электродом.
Сварочная дуга– мощный электрический разряд в газах между проводниками, сопровождающийся выделением значительного количества тепла и света (рисунок 2.2 а).
Для питания сварочной дуги применяют специальные источники тока. На рисунках 2.4, 2.6, 2.7 показаны схемы однопостовых трансформаторов, генераторов и выпрямителя для ручной дуговой сварки с описанием устройства и принципом работы.
Источники сварочного тока должны отвечать следующим требованиям:
1. Быть безопасными, т.е. иметь небольшое напряжение холостого хода (Uxx), но достаточное для легкого зажигания дуги –Uд = 30...35В для источников постоянного тока, Uд = 50...55 В для переменного тока. Обычно Uxx = (2...3)·Uд или Uxx = 60...80В, а отсюда Uд = Uxx/2...3.
2. Иметь крутопадающую внешнюю характеристику, когда напряжение уменьшается с увеличением сварочного тока (рис. 2.2.г).
3. Обеспечивать устойчивое горение дуги, т.е. создавать хорошие динамические свойства дуги чтобы за 0,05 секунды восстановить напряжение от короткого замыкания (U= 0) до значения Uд = 18–20 В, точка 2 на рисунке 2.8 обычно1,2 ≤ Iкз/Iсв ≤ 2.
4. Обеспечивать регулировку сварочного тока в широком диапазоне значений.
Режим работы сварочного оборудования оценивается продолжительностью включения ПВ % и продолжительностью нагрузки ПН % для всех значений, указанных в паспорте сварочного оборудования.
ПВ % определяется как:
где N –время работы сварочного оборудования под нагрузкой, мин;
Р –время паузы, мин.
При оценке ПВ % во время паузы сварочное оборудование отключается от сети.
ПН % определяется как:
где Т–время работы сварочного оборудования на холостом ходу, мин.
При оценке ПН во время холостого хода сварочное оборудование не отключается от питающей сети.
Рекомендуемый цикл нагрузки сварочного оборудования рассчитывается на номинальную относительную продолжительность нагрузки (ПН) при заданном полном времени цикла сварки (например, 5 или 10 мин). При номинальной нагрузке, указанной в паспорте, сварочное оборудование не должно перегреваться при указанном в паспорте ПН, например, при ПН 60 % и заданном полном времени цикла 10 мин сварочное оборудование должно находиться под нагрузкой 6 мин, в режиме холостого хода – 4мин.
а) б) в)
Рисунок 2.1 – Схемы основных видов дуговой сварки
а – по способу Н.Н. Бенардоса(неплавящимся электродом); б – по способу
Н.Г. Славянова (плавящимся электродом в обмазке); в – комбинированная сварка трехфазной дугой, применяется для автоматической сварки;1 – электрод, 2 – флюс, 3 – свариваемые детали, 4 – присадочный материал; 5 – дуга
|
![]() ![]() | |
Рисунок 2.2 – Устройство и характеристики электрической дуги: а –схема дуги; б – зависимость напряжения дуги (Uд) от величины дугового промежутка (lд). 1 – анодная область, 2 – столб дуги, 3 – катодная область,в–сварочная дуга, горящая между неплавящимися электродами и ее тепловые характеристики: Q– количество тепла; T1– температура при угольных электродах; Т2– температура при металлических электродах, г – вольт-амперная характеристика (ВАХ) сварочной дуги: I– падающая,II– пологая (жесткая), III– возрастающая характеристики дуги
| ||
![]() | Рисунок 2.3 – Статическая характеристика сварочной дуги Uд = f ( Iсв) где Uд– напряжение на дуге, В; Uk– падение напряжения на катоде; Uc – падение напряжения в столбе дуги; Ua– падение напряжения на аноде; Iсв– ток дуги (сварки), А; Uд = Uk+ Uc + Ua.
| |
Сварочные трансформаторы(Рисунок 2.4).
а | б | в |
Рисунок 2.4 – Схемы однопостовых трансформаторов:
а – с магнитным шунтом (марка СТШ–250);
б – со встроенной реактивной обмоткой (марка СТН –300);
в – с подвижной вторичной обмоткой (марка ТС–300, 500)
Трансформаторы содержат: пластинчатый стальной сердечник 1, первичную обмотку (изолированный провод малого сечения) 2, вторичную обмотку (изолированный провод большого сечения) 3, винтовой механизм перемещения 4, магнитный шунт 5, реактивную обмотку (аналогична вторичной, но намотана навстречу) 6.
Принцип работы трансформаторов следующий. При подаче переменного напряжения сети на первичную обмотку 2 в сердечнике 1 создается переменный магнитный поток Ф, который пересекая витки вторичной обмотки 3 наводит в ней электродвижущую силу (Э.Д.С.) используемую для сварки.
Магнитный шунт 5 (трансформаторы СТШ и СТН) делит поток Ф на Ф1 протекающий в нем и Ф2, протекающий через вторичную обмотку.
В СТШ при увеличении воздушного зазора (сопротивления потоку Ф1) винтовым механизмом перемещения 4 поток Ф1 уменьшается, тогда увеличиваются Ф2 и вместе с ним ток сварки. В СТН поток Ф также делится магнитным шунтом 5 на потоки Ф1 и Ф2, регулируемые величиной воздушного зазора. Чем больше зазор тем меньше Ф1, тем меньше ток в реактивной обмотке 6, тем больше Ф2 и сварочный ток. Такой способ регулировки необходим для обеспечения нелинейности при регулировке сварочного тока.
В трансформаторе ТС регулировка осуществляется за счет взаимодействия сил электромагнитного сцепления неподвижных и подвижных обмоток (катушек). При наибольшем удалении взаимодействие слабое, поэтому ток сварки минимальный.
Дата добавления: 2018-05-12; просмотров: 347; Мы поможем в написании вашей работы! |
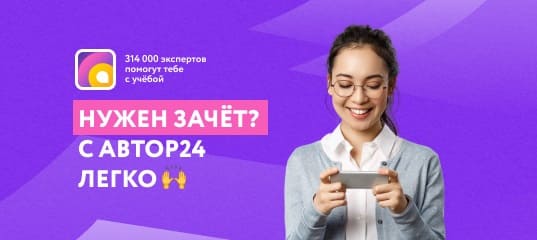
Мы поможем в написании ваших работ!