Существуют два метода фрезерования наружной резьбы: 1) дисковой фрезой; 2) гребенчатой (групповой) фрезой.
Nbsp;
ВОРОНЕЖСКИЙ ГОСУДАРСТВЕННЫЙ ТЕХНИЧЕСКИЙ УНИВЕСИТЕТ
КАФЕДРА «АВТОМАТИЗИРОВАННОЕ ОБОРУДОВАНИЕ МАШИНОСТРОИТЕЛЬНЫХ ПРЕДПРИЯТИЙ»
РЕФЕРАТ
Тема: Способы получения резьбовых поверхностей
Выполнил студент
Группы РС-081
Беляев Р.И.
Научный руководитель –
Доц. Кондратьев В.А.
Оценка ______________________
______________________________
Г.
Г. Воронеж
2011
СОДЕРЖАНИЕ
Стр.
Введение
Нарезание резьбы резцами.........................................................................5
Нарезание резьбы плашками и метчиками..............................................5
3. Накатывание резьбы...................................................................................8
Фрезерование резьбы...............................................................................10
Шлифование точной резьбы....................................................................11
Список использованной литературы...........................................................13
Введение.
Резьба — равномерно расположенные выступы или впадины постоянного сечения, образованные на боковой цилиндрической или конической поверхности по винтовой линии с постоянным шагом. Является основным элементом резьбового соединения, винтовой передачи и червяка зубчато-винтовой передачи.
Существуют основные параметры резьбы и единиц измерения:
|
|
Метрическая резьба — с шагом и основными параметрами резьбы в долях метра.
Дюймовая резьба — все параметры резьбы выражены в дюймах (чаще всего обозначается двойным штрихом, ставящимся сразу за числовым значением, например, 3" = 3 дюйма), шаг резьбы в долях дюйма (дюйм = 2,54 см). Для трубной дюймовой резьбы размер в дюймах характеризует условно просвет в трубе, а наружный диаметр, на самом деле, существенно больше.
Метрическая и дюймовая резьба применяется в резьбовых соединениях и винтовых передачах.
Модульная резьба — шаг резьбы измеряется модулем (m). Чтобы получить размер в миллиметрах достаточно модуль умножить на число пи (π).
Питчевая резьба — шаг резьбы измеряется в питчах (p"). Для получения числового значения (в дюймах) достаточно число пи (π) разделить на питч.
Модульная и питчевая резьба применяется при нарезании червяка червячной передачи. Профиль витка модульного червяка может иметь вид архимедовой спирали, эвольвенты окружности, удлинённой или укороченной эвольвенты и трапеции.
Шаг (P) — расстояние между одноимёнными боковыми сторонами профиля, измеряется в долях метра, в долях дюйма или числом ниток на дюйм — это знаменатель обыкновенной дроби, числитель которой является дюймом. Выражается натуральным числом (например; 28, 19, 14, 11)
|
|
Наружный диаметр (D, d) — диаметр цилиндра, описанного вокруг вершин наружной (d) или впадин внутренней резьбы (D).
Средний диаметр (D2, d2), диаметр цилиндра, образующая которого пересекает профиль резьбы таким образом, что её отрезки, образованные при пересечении с канавкой, равны половине номинального шага резьбы.
Внутренний диаметр (D1, d1), диаметр цилиндра, вписанного во впадины наружной (d1) или вершины внутренней резьбы (D1).
Ход (Ph) величина относительного перемещения исходной средней точки по винтовой линии резьбы на угол 360°.
Различают несколько типов резьб: метрическая(M), метрическая коническая(MK), цилиндрическая(MJ), трубная цилиндрическая(G), трубная коническая(R), круглая для санитарно-технической арматуры(Кр), трапецеидальная(Tr), упорная(S) и т.д.
Основные методы создания резьбы следующие: 1 — нарезание резьбовыми резцами или резьбовыми гребенками; 2 — нарезание плашками, резьбонарезными головками и метчиками; 3 — накатывание при помощи плоских или круглых накатных плашек; 4 — фрезерование с помощью специальных резьбовых фрез; 5 — шлифование абразивными кругами.
|
|
Нарезание резьбы резцами.
С помощью резьбовых резцов и гребенок на токарно-винторезных станках нарезают резьбу как наружную, так и внутреннюю (внутренняя резьба, начиная с диаметра 12 мм и выше).
Способ нарезания резьбы резцами характеризуется относительно невысокой производительностью, поэтому в настоящее время он применяется в основном в мелкосерийном и индивидуальном производстве, а также при создании точных винтов, калибров, ходовых винтов и т. д.
Достоинством этого способа является простота режущего инструмента и сравнительно высокая точность получаемой резьбы. Схематически он заключается в следующем (рис.1): при одновременном вращательном движении детали, на которой нарезается резьба, и поступательном движении резца (на токарном станке — II) последний снимает (вырезает) часть поверхности детали в виде винтовой линии (I).
Рисунок 1. (Нарезание резьбы резцами)
2. Нарезание резьбы плашками и метчиками.
На рис.2 показаны плашки, которые по своим конструктивным особенностям делятся на круглые — I и II (лерки) и раздвижные — III (клупповые).
Круглые плашки, имеющие применение на монтажных, заготовительных и других работах, предназначены для нарезания наружной резьбы диаметром до 52 мм в один проход. Для более крупной резьбы применяют плашки особой конструкции, которые фактически служат лишь для зачистки резьбы после предварительной нарезки ее другими инструментами.
|
|
Раздвижные плашки состоят из двух половин, вставляющихся в клупп и постепенно сближающихся в процессе резания.
Рисунок 2,3. (Нарезание резьбы плашками)
При нарезании резьбы на металлорежущих станках (II) плашка устанавливается и закрепляется в специальном патроне или приспособлении (рис.3). Деталь подается в калибрующую часть вращающейся плашки. Внутреннюю крепежную резьбу в подавляющем большинстве случаев нарезают метчиками.
Метчик (рис.4) представляет собой стальной стержень с резьбой, разделенный продольными прямыми или винтовыми канавками, образующими режущие кромки. Эти же канавки служат для выхода стружки. По способу применения метчики разделяются на ручные и машинные.
Рисунок 4. (Мечник)
Последовательность получения резьбы в глухих отверстиях такова (рис.5): вначале высверливают гнездо, куда в дальнейшем будет завернута шпилька или винт. Резьбу нарезают комплектом из двух или трех метчиков (малого, среднего и нормального, чистового) в зависимости от размера резьбы.
В настоящее время широко применяются машинные мечники, для нарезания резьбы на станке за один проход.
Рисунок 5.(Получения резьбы в глухих отверстиях)
Для метрической резьбы с крупным шагом и дюймовой резьбы комплект состоит из трех метчиков, для метрической резьбы с мелким шагом и трубной резьбы — из двух.
Накатывание резьбы.
Основной промышленный метод изготовления резьбы в настоящее время — накатка на специальных резьбонакатных станках. В этом случае при большой производительности обеспечивается получение высокого качества изделия (формы, размеров и шероховатости поверхности).
Получение резьбы накатыванием осуществляется копированием профиля накатного инструмента путем его вдавливания в металл заготовки. На токарных, токарно-револьверных станках и станках-автоматах накатывают резьбы диаметром 5-25 мм одним роликом (рис.6). Резьбу накатывают при вращении заготовки в патроне или цанге и при поступательном перемещении суппорта станка вместе с накатником 3, в который вмонтирован накатной ролик 2. При этом необходимо следить за величиной деформации заготовки под действием односторонней радиальной силы. Накатывание резьбы диаметром до 50 мм происходит в более благоприятных условиях при применении резьбонакатных головок (рис.7) с тремя и более роликами.
Рисунок 6. Рисунок 7.
(Накатка резьбы одним роликом) (Резьбонакатные головки)
Головки могут быть самораскрывающимися и нераскрывающимися. Ролики выполняют с кольцевой и винтовой резьбой. Ролики с кольцевой резьбой устанавливают в головке под углом подъема винтовой линии накатываемой резьбы и смещают один относительно другого на 1/z шага, где z - число роликов в комплекте. Ролики с винтовой резьбой устанавливают параллельно оси заготовки. Резьбонакатные головки по принципу работы не отличаются от резьбонарезных головок. Накатывание резьбы производится, как правило, при самозатягивании головки, поэтому осевая подача инструмента на заготовку необходима только в начальный период, пока ролики не захватят заготовку. При накатывании поверхность резьбы получается уплотненной и без микронеровностей, характерных для обработки резанием, что повышает прочность резьбы. Резьбы можно накатывать на деталях из различных материалов. Материал считается пригодным для накатывания резьбы, если его относительное удлинение d>12%. При накатывании резьб рекомендуется применять в качестве смазочно-охлаждающей жидкости эмульсию или масло.
Для получения резьбы методом пластической деформации на внутренней поверхности применяют раскатники (рис.8). Раскатник имеет заборную часть с конической резьбой длиной L1=3P для глухих и L=(10-20)Р для сквозных отверстий. Калибрующая часть выполнена с цилиндрической резьбой длиной L2=(5-8)Р. По всей рабочей части раскатника выполняется огранка r=0,2-0,6 мм для уменьшения сил трения при обработке резьбы. В процессе работы раскатник вращается относительно детали при принудительной подаче вдоль оси.
Рисунок 8. (Раскатник)
Фрезерование резьбы.
Существуют два метода фрезерования наружной резьбы: 1) дисковой фрезой; 2) гребенчатой (групповой) фрезой.
В первом случае на медленно вращающейся обрабатываемой детали резьба нарезается дисковой фрезой, поставленной к оси вращения детали под углом, равным углу наклона нитки резьбы. Фреза, профиль зуба которой соответствует профилю резьбы, также вращается и подается вдоль оси обрабатываемой детали на величину шага резьбы на один оборот детали (рис.9, а). Полное число оборотов нарезаемой детали равно числу ниток резьбы, умноженному на число заходов. Обработку производят на резьбо-фрезерных станках для длинных резьб.
Дата добавления: 2018-05-02; просмотров: 466; Мы поможем в написании вашей работы! |
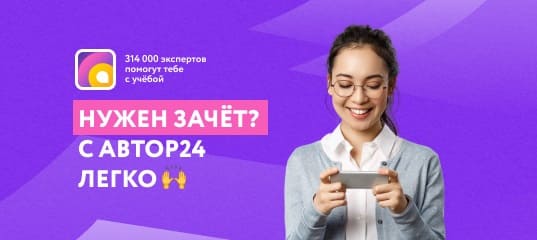
Мы поможем в написании ваших работ!